摘要:介绍了高速列车用铝型材的精整过程,运用Ansys有限元分析软件,建立该铝型材精整过程的有限元模型,分析了铝型材精整过程中的应力、应变、压下位移等的变化规律。当t=6 s时,应力值开始达到铝型材的屈服极限σs,之后开始进入塑性变形;当t>12 s时,应力超过了铝型材的强度极限,压下行程大于10 mm,型材发生破坏性的塑性变形。该研究为优化异型截面型材的精整工艺提供了理论参考。
关键词:异形截面型材精整机;精整压下行程;高铁车辆用铝型材
0 前言
精整是指金属塑性加工后,为满足用户对产品在表面质量、尺寸、外形和某些性能方面的最终要求而进行的一道重要工序。主要包括火焰清理、热加工后的冷却、卷取、切断、矫直、缺陷的物理检测等方面。精整机是完成此工序之一的重要设备。在当前的精整技术和设备的研究中,大部分集中在钢板,对铝型材特别是异型截面的高铁车辆用铝型材的精整研究还比较少。与普通的钢板不同,轨道交通用铝合金特种型材,生产难度大,技术要求高,其不但要求大型(均有10余米长,甚至30 m)、大断面、整体、薄壁、扁宽、断面形状复杂、壁厚差大,而且对力学性能、焊接性能、抗腐蚀性、尺寸精度和质量要求都特别高[1]。异型截面铝型材经过挤压-拉伸矫直之后,还存在表面缺陷、斑点及扭曲变形,这就需要对其进行精整加工,以达到产品的质量要求。
长期以来,精整工艺的实施多由工人凭经验和估计精整压下行程,反复测量和试验,这种方法不仅效率低,劳动强度高,而且不易保证精度。在使用异型截面铝型材精整机对型材进行精整加工的过程中,对精整压下行程的设定要求较高,否则会达不到消除型材表面缺陷,实现精整的目的,同时还会在精整辊与型材接触的表面出现凹陷变形,严重影响了铝型材的精整质量,甚至产生废品。因此,有必要对高速列车用铝型材的弹塑性回弹进行预测,分析精整压下行程铝型材的精整质量的影响,为异形截面型材精整机的工艺参数的优化提供理论参考。该套系统是轨道车辆如地铁、轻轨、高速列车等车体生产线上必不可少的关键设备。
1 异型截面铝型材精整机组的组成与结构
如图1所示,型材精整机组主要由左右机架、底座、驱动装置、精整装置、压下装置以及电气控制装置等部分组成。其中驱动装置主要包括由上、下两个驱动辊,铝型材在压力的作用下被夹持在两个驱动辊之间,在其接触处产生摩擦力,并依靠此摩擦力来运送铝型材,从而实现铝型材的匀速运动。精整装置主要是由八个精整辊组成的,其中入口侧4个,出口侧4个,每个精整辊均安装有分度装置,可以实现任何角度的旋转,能够满足多种异型截面和表面质量的精整。所有的精整辊、驱动辊均是由尼龙材料制成的,可以有效地避免辊子在铝型材上产生刮痕,保护铝型材的表面质量。
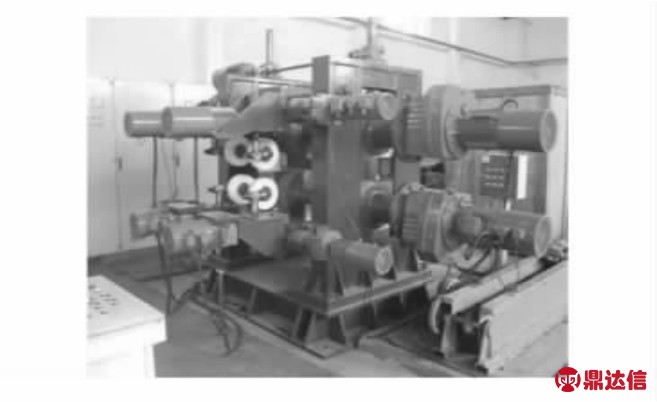
图1 型材精整机组图
Fig.1Picture of finishing unit
2 高速列车用铝型材的基本参数
高速列车用铝型材的种类繁多,但是所用的型材都具有断面尺寸大、形状复杂、壁厚相差悬殊、宽厚比大、长度一般在10 m以上,而且形位公差和尺寸精度要求都很高。本文主要选用空心的6005A铝型材做分析研究,其截面的三维结构如图2所示。基本性能参数及化学成分见表1、2。
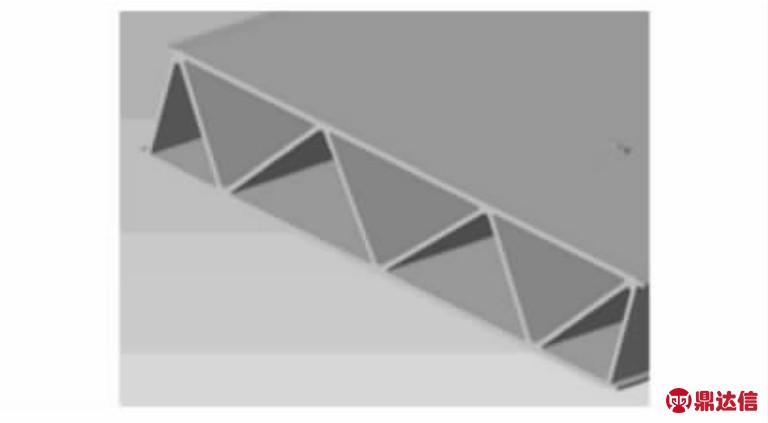
图2 6005A铝合金三维结构图
Fig.2Three-dimensional structure of 6005A alloy
表1 6005A基本性能参数
Tab.16005A performance parameters
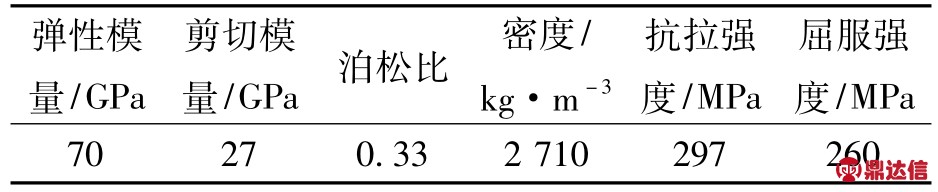
表2 6005A铝合金的主要化学成分
Tab.2Main chemical composition of 6005A alloy%

3 铝型材精整的Ansys分析
铝型材的精整是通过对弯曲的型材施加一定的载荷(力或者精整压下行程),使工件产生弹塑性变形,然后卸载回弹的过程[2]。因为高铁车辆用铝型材经过挤压、拉伸矫直之后的表面缺陷、残余的弯曲变形程度不同,所以本文选择表面平直的铝型材进行实体建模[3]。选取的6005A铝型材的尺寸规格:截面尺寸330 mm×55 mm,长度为2 000 mm。采用大型有限元分析软件,对高铁车辆用铝型材进行精整压下行程的Ansys非线性结构分析。
针对车辆用铝型材的宽厚比值较大及精整时压弯量相对较小的特点,为了简化计算,本文进行以下假设:忽略材料沿带宽方向的变形对弯曲变形的影响;忽略铝型材精整速度对屈服强度的影响;忽略铝型材厚度方向的变形对弯曲的影响;忽略精整过程中摩擦对材料变形的影响[4]。忽略精整过程中精整辊和铝型材的接触点位置对精整的影响。
3.1 单元的定义
采用三维实体单元solid164进行精整模拟,solid164单元是一种8节点实体单元,被用于三维的显示结构实体,节点具有X、Y、Z方向的平移、速度和加速度的自由度[5]。该单元没有实常数,但该单元具有塑性、蠕变、膨胀、应力强化、大变形和大应变能力,且有利于沙漏控制的积分缩减。
3.2 材料属性的定义
铝型材定义为变形体,上下四个精整辊均定义为刚体,其中下部分四个精整辊的所有的旋转、平动自由度均被约束。上部分的四个精整辊除了沿Z方向平动自由度(RUBZ)不加约束之外,其余的五个自由度均被约束。分别输入材料的密度、弹性模量、泊松比等参数。其中铝型材的材料属性参数见表2,尼龙的弹性模量E=28 GPa,μ=0.4。
3.3 铝型材精整模型
在建立模型的时候,为了简化模型,减少网格的数量和计算时间。将所有的辊子都定义为刚体,这样只需给出辊子的外轮廓模型即可,不需要具体的形状结构,并且将铝型材长度取为2 m,实际铝型材的长度一般为7~10 m。由于铝型材的截面形状比较复杂,模型建好之后,选用智能划分,可以缩短网格划分的时间。在ProE上建立好的铝型材精整模型如图3所示。
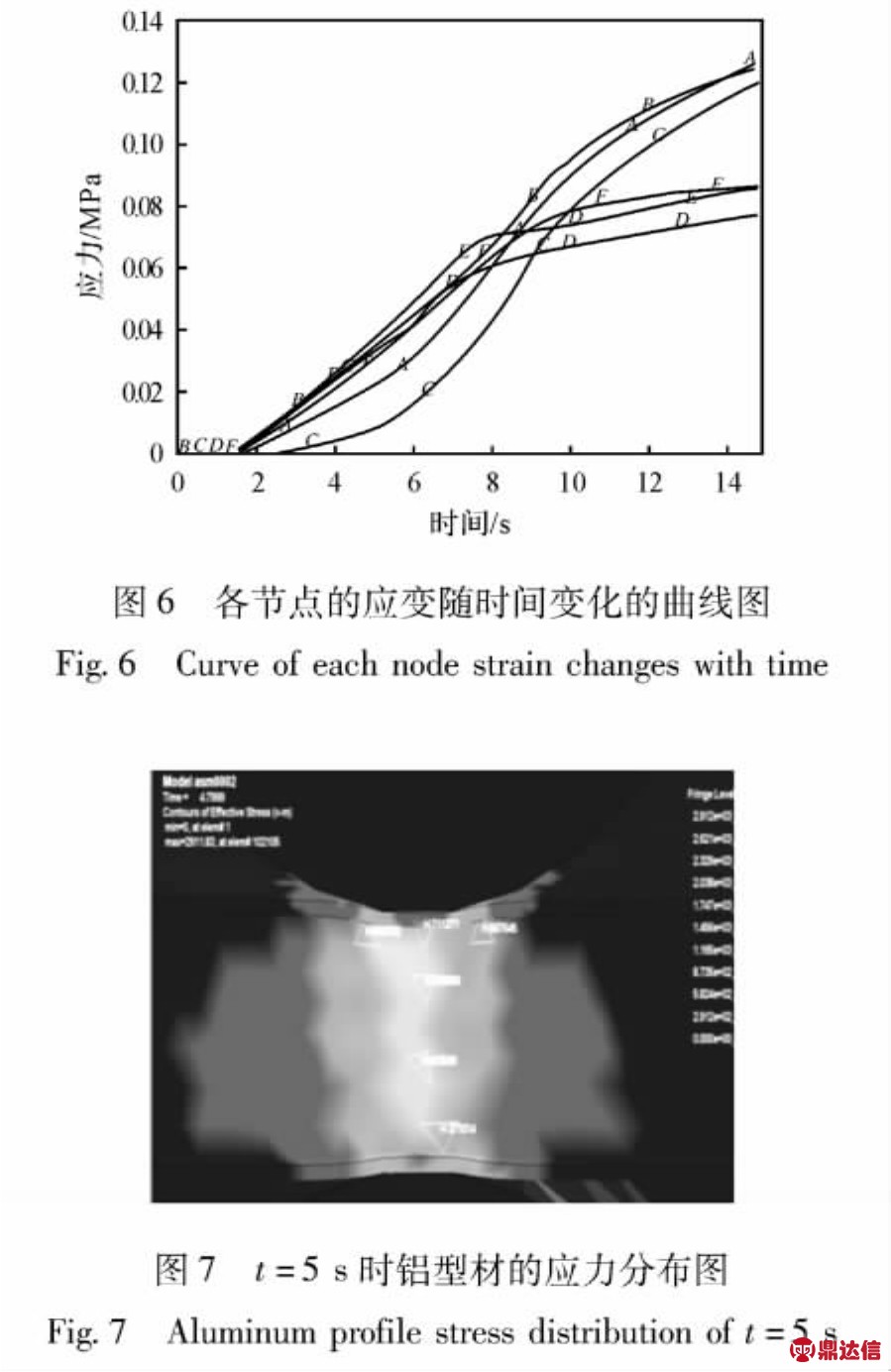
图3 铝型材精整模型
Fig.3Aluminum profile finishing model
3.4 设定精整参数
由于将精整辊设置为刚性体,所以只能将载荷加到PART号上,而且载荷类型为速度和转速。由于型材精整机所精整的铝型材的品种具有一定的范围,精整速度应相应进行调整,根据产品的规格,给上部分四个精整辊施加一个匀速向下的速度v=1 mm/s[6]。在实际的精整过程中,铝型材运行的速度比较小,为了简化模型,忽略铝型材的进给速度,即将其视为静止的。
3.5 模拟精整的结果分析
图4、图5、图6分别为模拟精整过程中,精整辊与铝型材接触的最大变形区域处的部分节点单元在Z方向的压下行程、应力和应变随时间变化的曲线图。其中B表示的精整辊与铝型材接触位置处的节点单元,A、C为铝型材变形区域最大挠度之间的两节点单元的曲线。D、E、F分别为变形区域在纵向上选取的三个节点单元的曲线。比较这六条曲线可以看出,变形处的铝型材内部的所有节点随位置的不同,其压下行程、应力和应变值也不一样,但是其形状都基本上相似,都符合铝型材在精整过程中的变化规律。
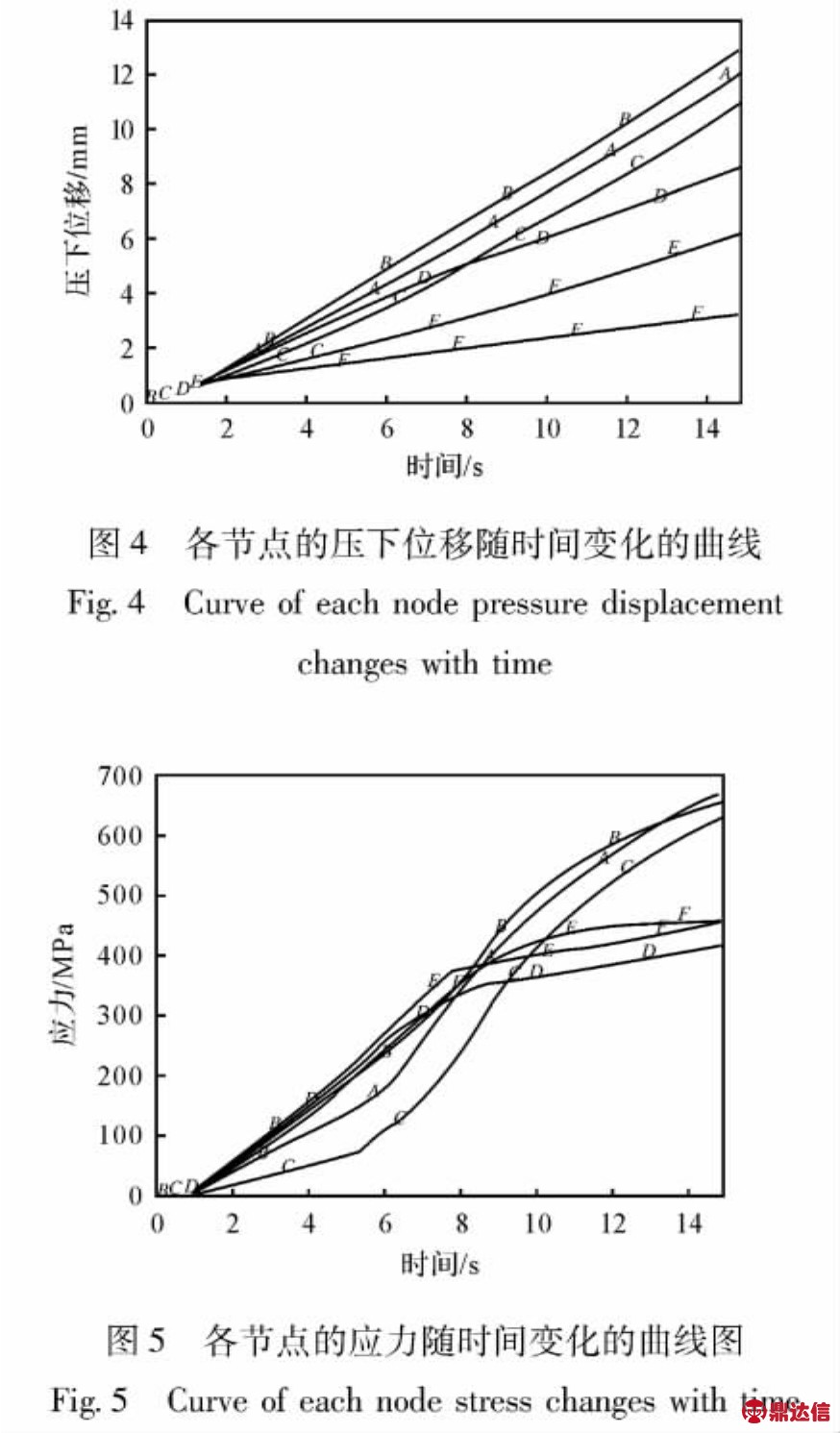
在精整辊以一定的压下速度往下压铝型板材时,随着精整行程的进行,残余应力不断变大,当t=6 s时,应力值开始达到铝型材的屈服极限,之后渐渐超过屈服极限,开始进入塑性变形,如图7所示。
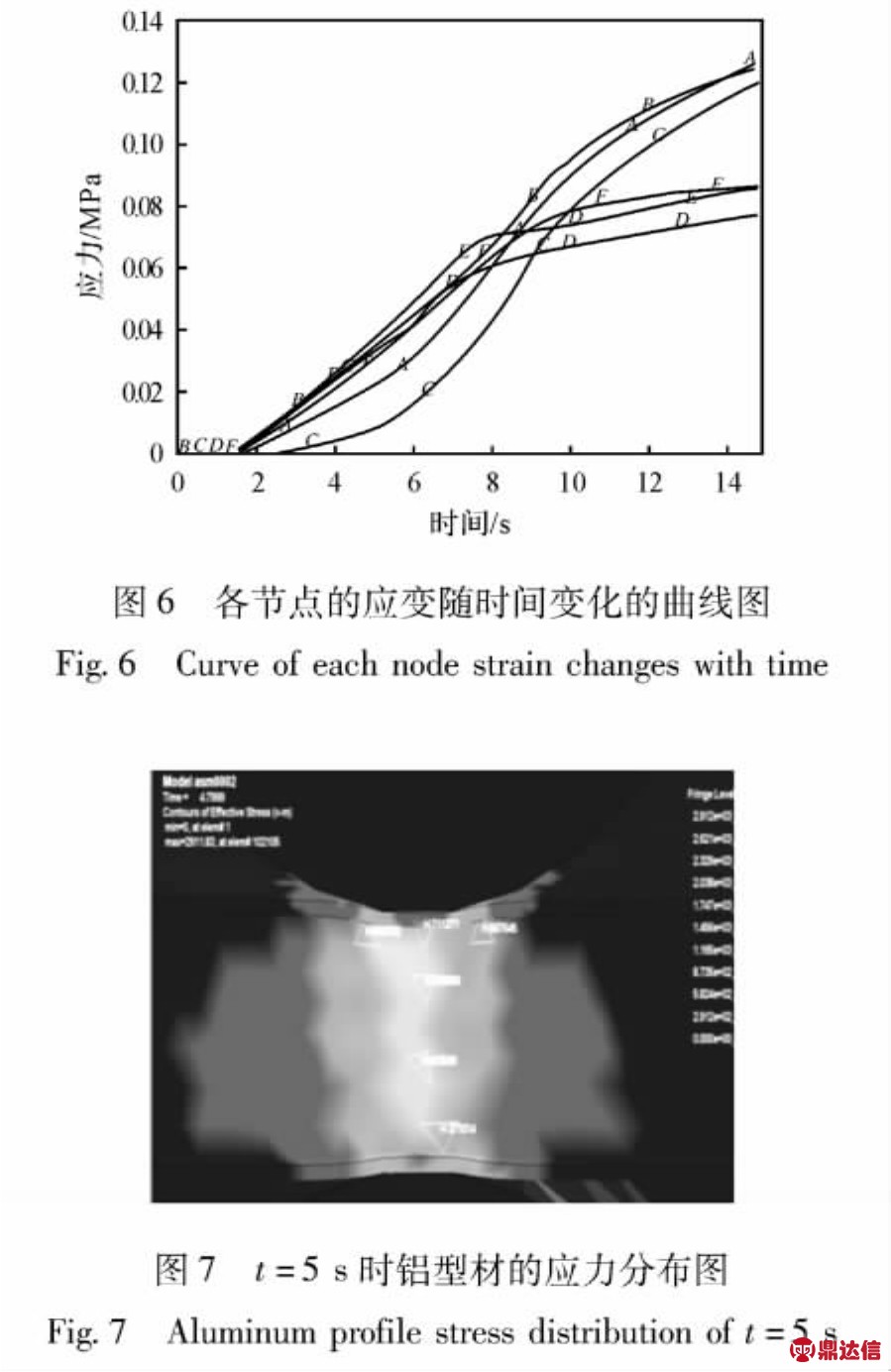
随着塑性变形的逐渐变大,伴随着精整过程和加工硬化,达到铝型材的强度极限后,开始发生破坏性的塑形变形。当t>12 s之后,应力值超过400 MPa,已经超过了铝型材的强度极限,压下行程大于10 mm,已经远远超过精整的理论值,此时型材已经发生破坏性的塑性变形,型材已逐渐被压坏,上表面、侧面以及内肋板都出现永久性凹坑与突凸变形,变成废品,如图8所示。

图8 铝型材破坏之后的截面图
Fig.8Aluminum profile section after damaged
4 结束语
本文通过运用大型分析软件ANSYS对高速列车用6005A铝型材的表面精整过程进行了动态模拟,得出了压下行程、应力和应变随精整时间的变化的曲线图。通过分析曲线图。可以得到铝型材的精整加工过程中的压下行程与铝型材表面的精整质量的关系,为铝型材的精整加工提供了最佳的工艺参数参考,减少了由于人为失误而导致工件的破坏与报废。