摘要:介绍了车辆用铝型材性能要求和一种铝型材精整实验平台。根据车辆用铝型材截面形状多种多样且较复杂的特点,通过调整型材精整实验平台矫正辊的位置及角度,就能够适应铝型材的需要,从而达到精整的目的。根据型材精整实验平台的结构特点建立矫正过程的有限元模型,并对精整过程中的型材变形进行分析,从而建立数学模型。
关键词:车辆用铝型材;实验平台;有限元模型;精整过程;数值模拟
0 引言
目前车辆用铝合金材料有十几种,其中最常用的是挤压性能和综合性能较好的6XXX(LF4)系列铝合金型材。但车辆生产企业所使用的铝型材精整设备存在精整精度不高、效率低、设备自动化程度低等问题,所以多数企业需高价从国外进口精整设备。对此本文介绍一种铝型材精整实验平台,并对精整过程中的型材变形进行分析。
1 车辆用铝型材精整实验平台
本文以车速为200km/h的动车组车体用铝合金型材6XXX(LF4)系列为例进行研究。其铝合金车体截面如图1所示。6XXX(LF4)系列铝合金型材长度为26m,主要化学成分见表1。
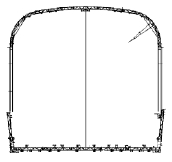
图1 铝合金车体截面
铝型材的质量主要表现在两个方面:材料的强度指标和材料的形位公差。材料的基体强度取决于淬火方式,一般来说,大型型材经过水冷淬火强度可以满足材料的强度指标,但是,对于车辆用型材而言,过于强烈的冷却会导致型材出现不希望的变形,造成产品的形位公差超差。根据长春客车厂的实践反映,目前这类型材的扭﹑拱﹑弯普遍过大,较大地影响了车辆装配精度。也就是说,需配备一台高水平的辊式矫正机在大挤压机生产线后部,用于修复型材在生产过程中不可避免的磕碰变形,以提高型材的成材率。型材精整实验平台三维框架图如图2所示。型材精整实验平台矫正过程有限元模型如图3所示。
表1 6XXX(LF4)系列铝合金型材主要化学成分(质量数) %

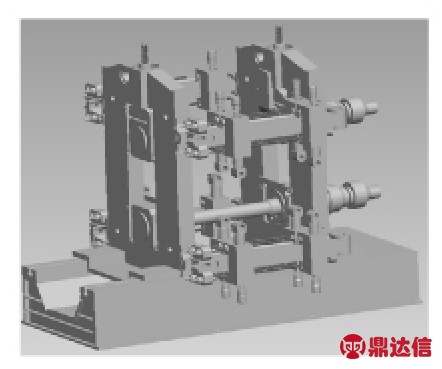
图2 型材精整实验平台三维框架图
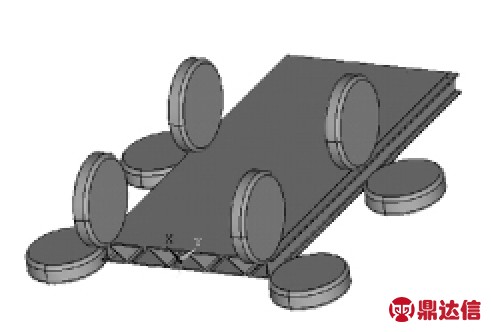
图3 型材矫正过程有限元 模型
2 建立数学模型
2.1 矫正时变形分析
在力F的作用下,梁中部产生向下的弯曲挠度δ,在力不断增大的过程中,弯曲变形随之越来越大。弯矩最大处首先由弹性变形进入塑性变形,并且塑性区逐渐扩大,形成如图4所示的塑性区;当外力撤销时,因弹性变形产生的挠度恢复,而因塑性变形而产生的弯曲挠度则保留下来。
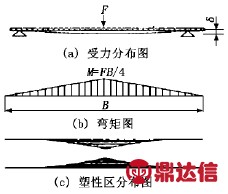
图4 横弯时的塑性区分布示意图
2.2 弹性变形挠度计算
根据图4来分析开始进入塑性变形的挠度。在图4所示的受力情况下,集中载荷处产生的最大弯矩为:

其中:F为载荷;B为梁的长度;W 为抗弯截面系数;σ为弯曲梁边部所受应力。
当梁的边部应力达到屈服极限σs时,进入塑性状态,此时受力Fs=4Wσs/B。开始塑性变形时的挠度(即回弹挠度)为:

其中:h为梁的厚度(高度);E为梁的弹性模量。
2.3 永久变形挠度计算
开始进入塑性变形后,随着力的增大,发生弹塑性变形和弯曲挠度不断增大,当外力撤除后,保留下来的变形(弯曲挠度)就是我们所需要矫正的变形。现在分析发生弹塑性变形时,总的弯曲挠度δw与残留弯曲挠度δ0的关系。
受横向集中载荷作用时,其弹塑性挠度的计算比较困难,许多文献采用近似计算法,如用大弯矩的弹性挠度代替弹塑性挠度等,对于制定矫正过程的数学模型来说,误差应尽量小,所以需要以严格的数学解析方法找出精确的计算方法。图5为平直梁受力作用下的压下挠度示意图。
图5中,ρx为任意点x处的中性层弯曲曲率半径,在弹性区lt范围内,对应F下的总挠度δw为:
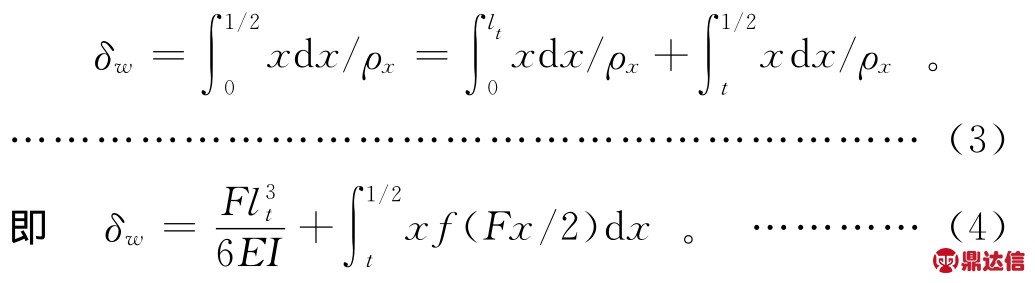
当外力解除时,相当于反向加上一个弹性弯矩,其回弹挠度这样残余挠度(永久变形)为:

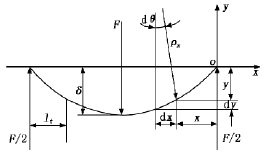
图5 力作用下的压下挠度示意图
3 结论
在精整过程中,型材先进入弹性变形,进而进入塑性变形,在精整过程中必须考虑到回弹变形和永久变形,永久变形是我们所需要矫正的变形。建立有限元模型和数学模型可为新型矫正机的优化设计研究提供理论指导。