摘 要 本文是分析工业铝型材厂设计考虑的内容,即工业铝型材厂工艺设计,产品方案及产量,工艺流程和工艺参数的确定,铝型材厂主要工艺设备选择和总图布置的几个方面的探讨,给出了一个现代的工业铝型材厂设计新思路。
关 键 词 工业铝型材;工艺设计;设计研究
铝合金以及其加工材料具有质轻、耐蚀、强度高、易加工、表面美观等优点,被广泛应用于机械、交通运输、建筑、印刷、包装等各个行业而广泛取代普钢和不锈钢等材料。近年来,随着国内经济的持续高速发展和人民生活水平的不断提高,国内工业铝材深加工相关产品的需求也在逐年提高,特别是在我国加入世贸组织以后,随着全球经济一体化的进程,各种加工制造业正在加速向我国转移,中国成为世界加工中心的地位正在逐渐形成,对各种高质量加工原材料的需求为铝加工产业带来了新的发展机遇。工业铝型材产品对尺寸公差、性能、材质等有高要求,其生产难度大,技术要求高,利润较建筑铝型材高,特别是扁宽薄壁复杂的大型工业铝型材。随着铝加工行业不断地发展壮大,生产工业铝型材企业受到投资者青睐。
工业铝型材厂的设计,应综合国内外的工艺技术和设备成熟性、先进性、节能性、环保性及经济性等方面,并结合国家经济建设、社会发展和企业自身发展的需要,使企业能为用户生产质轻、高强度、耐蚀、优质的合格的工业铝型材产品。同时生产产品、规模和设备必须符合《产业结构调整指导目录(2011 年本)》《铝行业准入条件》等国家产业政策,节能、节水、环境保护方面必须符合《有色金属加工企业产品能耗指标》《铝工业发展循环经济环境保护导则》和其他国家有关规定。因此,工业铝型材厂的设计是在工业铝型材企业发展历程中的一个重要组成部分,特别是在铝型材深加工产业的日益高速发展变化,不断提高产品质量、技术和设备,工业铝型材厂的设计是非常重要的。
1 工业铝型材厂工艺设计
工业铝型材厂设计主要是工业铝型材挤压生产车间的挤压生产线设计。按该设计开展其他辅助车间和设施设计。工艺设计将直接影响到生产和工艺技术的合理性,与施工成本和生产质量、成本,劳动环境,机械化程度,能源消耗,环境污染有密切的关系,也影响到其他设计如电力,水,天然气,油,建筑,结构等的基本数据。因此,工艺设计在整个工业铝型材厂设计中起着重要的作用。国内目前工业铝型材厂设计主要是在国内外相关技术资料、设计手册和生产经验为工艺参数的基础,而一个优秀设计必需根据企业的实际情况,结合不断变化市场对产品要求,不断更新的先进生产技术和设计理念,铝型材厂设计适应这种不断变化和发展的要求以达到设计最高境界。该设计应是系统的,完整的,科学的,合理的,客观而符合市场规律的,使企业始终处于铝型材加工行业的龙头地位。
2 确定产品方案及产量
工业铝型材产品应具有良好的经济效益、社会需求市场容量、产品变化的适应性,能够形成地方产业特色或支柱,有成熟可靠工艺技术技撑,有新功能,有资源优势、能源优势,以及先进性如:世界上已经批量生产,但可填补国内空白的产品;国内已经批量生产,但可填补本地区空白;虽然已经生产,但可改善现有产品不合理的结构;减少进口或外地进货,缓解本地区的货源紧张。随着市场需求的不断变化,将导致在产品品种的变化,因此它需要有多个产品方案。通过盈亏平衡分析法、线性规划法及供给理论确定产品的产量,并应结合原辅材料供应及综合利用、动力、供水、劳动定员、设备能力、能耗、水耗和环境要求等条件综合因素计算确定。
3 主要产品的工艺流程及工艺参数的确定
3.1 生产流程
熔铸车间的主要任务是为挤压工部生产合格的铝合金圆锭,主要生产环节有熔炼、精炼、细化晶粒、过滤、铸造等。
挤压车间应设置多条不同生产线,分别安装在各挤压车间内,挤压车间采用流水作业生产方式,圆锭加热、挤压、牵引、张力矫直和定尺锯切等工作都在生产线连续进行,利于提高生产率和成品率,减轻工人劳动强度,并在生产线上对产品监测抽检,以保证产品质量要求。同时要考虑企业具体条件,优化工艺最短流程布置,在不影响产品质量的前提下实现最合理的生产过程。
3.2 工艺参数
根据产品规格、形状及性能要求;原材料合金成份、性能;设备生产能力;燃料种类;模具材料等,确定熔铸参数包括:烘炉、熔炼、精炼及除气温度、时间;铸造温度、速度、水压参数。挤压参数包括:坯料及挤压工艺参数设计:确定坯料直径和长度,挤压摩擦系数、速度,工具预热温度等;挤压工具设计:确定挤压垫直径和厚度,挤压筒外径和长度,挤压模角、定径带长度、直径、出口直径和长度,入口圆角半径、模子外圆直径等。
3.3 工艺流程框图
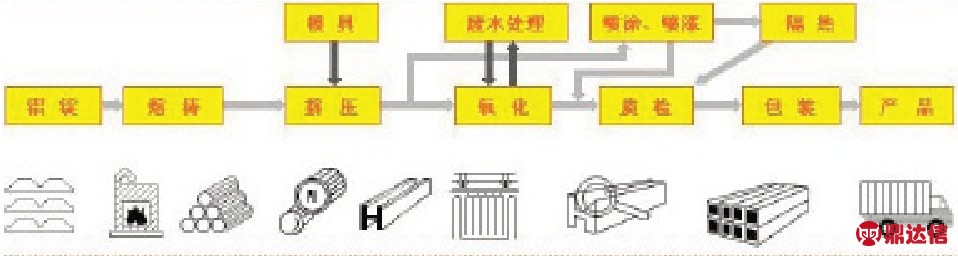
4 主要工艺设备的选择
工业铝型材厂的主要设备挤压生产线,为确保铝型材产品的质量,高生产率,轻劳动强度,挤压生产线应按全自动的主辅机配套齐全的高速连续的流水作业线。即自动完成从铝锭加热、挤压、在线淬火、锯切、冷却、矫直拉扭、定尺锯切、时效处理等工序。包括:加热坯锭的加热设备、挤压型材的挤压机及其辅助装置、挤出型材直接淬火处理的水、风淬火装置(在线淬火)、挤压型材过程中的切头去尾及中部切断的热切锯、防止型材挤出后出现弯曲扭拧和多根型材之间相互碰撞的牵引机、型材的承托辊道、以及纵向输送的移料装置、型材的冷却和横向输送的冷床、型材进行张力矫直和扭拧校正的矫直机、拉伸后的型材储存和向定尺装置横向输送型材的储料台、型材的定尺锯切装置(包括锯前辊道、锯、定尺装置和检查台等)、型材锯切后的自动装筐的集载装置、型材的时效热处理的时效炉、挤压模具的加热的预热炉等。生产线的配置形式:铝型材生产线的配置和工艺流程从坯锭加热,挤压直到型材时效的工艺。这种配置方式缩短长度,配置合理紧凑,从而保证了挤压生产线前后各工序的紧密衔接。有利于实现生产全过程的连续作业和自动控制,即工艺过程数据库用语控制系统:计算机辅助挤压屏幕启动、机器的控制通过输入相应的产品参数、现行工艺过程状态的图形显示、液压装置的图形显示、辅机运动的图形显示、使用一些屏幕的液压系统图形显示、所有系统报警和错误信息的显示和屏幕启动。控制挤压机的数据:炉温、锭坯温度、挤压力、挤压轴前进速度、锭坯长度、残料长度、挤压筒温度、锭坯出炉到挤压开始的辅助时间(锭坯运送与供锭时间)等。
5 总图布置
5.1 布置原则
充分利用现有场地自然条件,结合地形地势条件,满足生产工艺流程的要求;尽量使各生产车间之间的物料输送线路短捷,减少动力消耗;平面布置合理紧凑,管理方便,节约用地,尽量减少建设投资;利用风向,减少气体、粉尘等相互干扰;留有足够的通道宽度和企业发展用地,并满足运输、防火、防爆、安全、卫生、环保、绿化和设置管线等规范要求。
5.2 总平面布置
将生产区和生活服务区独立划分,相互协调发展且不相互影响。设计将原料仓库、熔炼铸造车间、中间产品仓库、挤压车间、半成品仓库、热处理车间、包装车间、成品仓库等集中布置,形成一个独立、封闭的生产系统,既节省用地,又使工艺流程短捷。在生产系统周围布置相应的机修车间、五金仓库、油罐区、模具车间、高位水池等生产辅助设施,以便尽量缩短与其服务对象之间的距离。变电站靠近厂区挤压、热处理车间布置,靠近外部供电电源进线为止,方便外部进线;且靠近用电负荷较大的车间布置,可以以最短的距离通到最大电负荷点,达到最大程度节能的目的。油罐区由于其性质的特殊性,将其作为一个独立的区域与周围其他厂房保留出安全距离。道路沿厂区边缘环形布置,且各功能分区呈环状布置,以满足运输消防、防爆、安全、卫生、环保、绿化和设置管线等要求。并同时在熔铸、挤压、热处理车间预留适当空间便于企业发展产品和设备升级。
6 结论
工业铝型材厂的产品方案及产量,工艺流程和工艺参数的确定,铝型材厂主要工艺设备选择和总图布置方面设计根据企业的实际情况,结合不断变化市场对产品要求,不断更新的先进生产技术和设计理念有着重大意义。