摘 要:应用UGNX建立了平面分流组合模的几何模型,利用有限元软件 DEFORM-3D对挤压过程进行有限元模拟,研究了挤压铝合金空心型材时金属的流动情况。模拟结果表明,即便是对称性较好的铝合金窗用光企型材(有一个对称轴)模具,按照常规的设计方法也很难避免金属的流速不均问题,影响型材的成型度。对于绝大多数空心型材来说,其断面往往都是不对称的,仅依靠设计者的经验和判断设计模具是很难避免金属流速不均问题的。而采用有限元模拟的方法,则可以及时发现设计中存在的不足,并通过修改设计方案,达到满意的效果,为设计模具提供科学的依据。
关键词:平面分流组合模;铝型材;挤压;有限元模拟;工作带长度
铝材以其重量轻、比强度高、加工性能好、可焊接、耐腐蚀和美观等良好特性在现代生产生活中得到了日益广泛的应用[1],尤其是铝合金空心型材,不仅大量应用于民用建筑,而且广泛应用在现代交通运输工具方面。随着铝型材的应用范围不断扩大,其种类越来越多、结构越来越复杂,市场对产品的要求也在逐年提高,而决定型材形状、尺寸精度、表面粗糙度的关键在于挤压模具的设计。空心型材的多样化、复杂化,造成模具设计时对各分流孔的数目、面积、布置等的考虑变得更加复杂[2]。目前,挤压空心型材广泛采用平面分流组合模。由于平面分流组合模的结构复杂,挤压时金属又是在密闭的型腔中流动,因此模具设计者对挤压过程中的金属流动情况以及模具的应力、应变状况难以掌握[3]。要想得到质量合格的产品,必须尽量保证制品断面上每个质点以相同的速度流出模孔。在实际生产中,模具设计人员往往通过反复试模和修模来实现这一目的,但这种方式不利于短周期低成本的产品开发要求。为此,在铝型材挤压工艺和模具开发过程中采用成型过程有限元模拟技术,可以在制模以前就对成形过程进行计算机仿真,从而获得挤压件形状、挤压件内部各种力学场量的分布等信息,便于及时发现挤压件中可能出现的缺陷,进而实行工艺和模具设计方案的及时修改,甚至能够达到零试模的目的,这是现代化生产发展的必然趋势[4-5]。
本文针对当前铝型材生产中成模前试模次数较多、挤压成型困难的 6063空心铝型材的挤压模具为研究对象,运用 DEFORM-3D三维模拟软件对其挤压过程进行有限元模拟。通过虚拟试模分析大挤压比 (分流组合模,λ>40)复杂薄壁 (t<2mm)铝型材挤压过程中金属的流动规律、应力与应变和挤压流出速度等情况。从根本上改善过去仅凭经验法设计此类铝型材挤压模具的状态,提高铝型材生产中一次试模成功率。
1 初始模具设计
本文有限元模拟选用的 6063空心铝型材是建筑业中铝合金窗用光企型材,其截面尺寸及截面图如图1所示。型材的壁厚为 1.4mm。
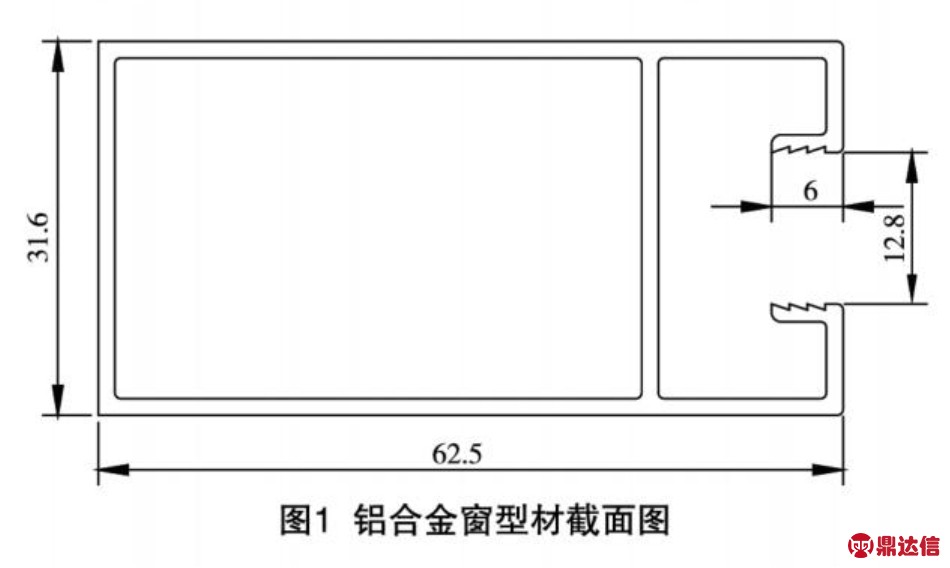
该型材采用平面分流组合模挤压成型。平面分流模一般由上模、下模、定位销、联结螺钉四部分组成。上模设有分流孔、分流桥和模芯;下模设有焊合室、模孔型腔、工作带和空刀。利用 UG NX三维造型软件对分流组合模进行实体建模,设计的模具三维视图如图 2所示。
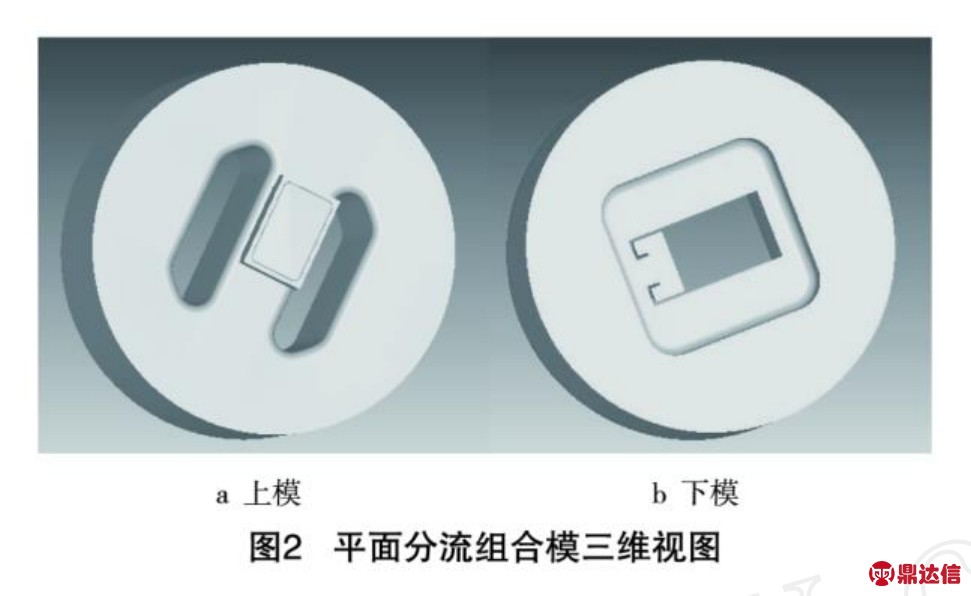
经UG建模后,以 STL格式输入到 DEFORM中,即可完成模具几何形状的输入。平面分流模的装配图如图 3所示。
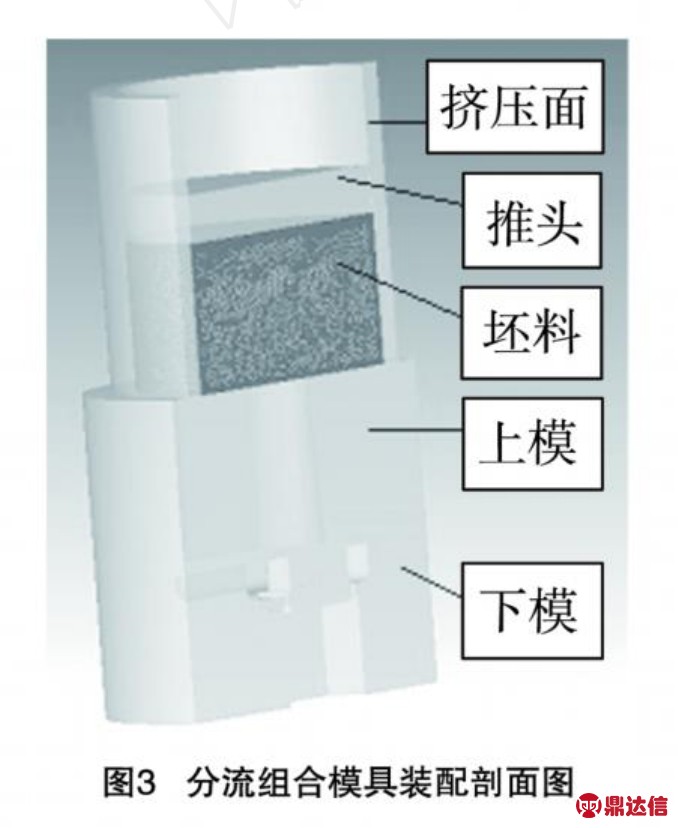
2 实验参数设置
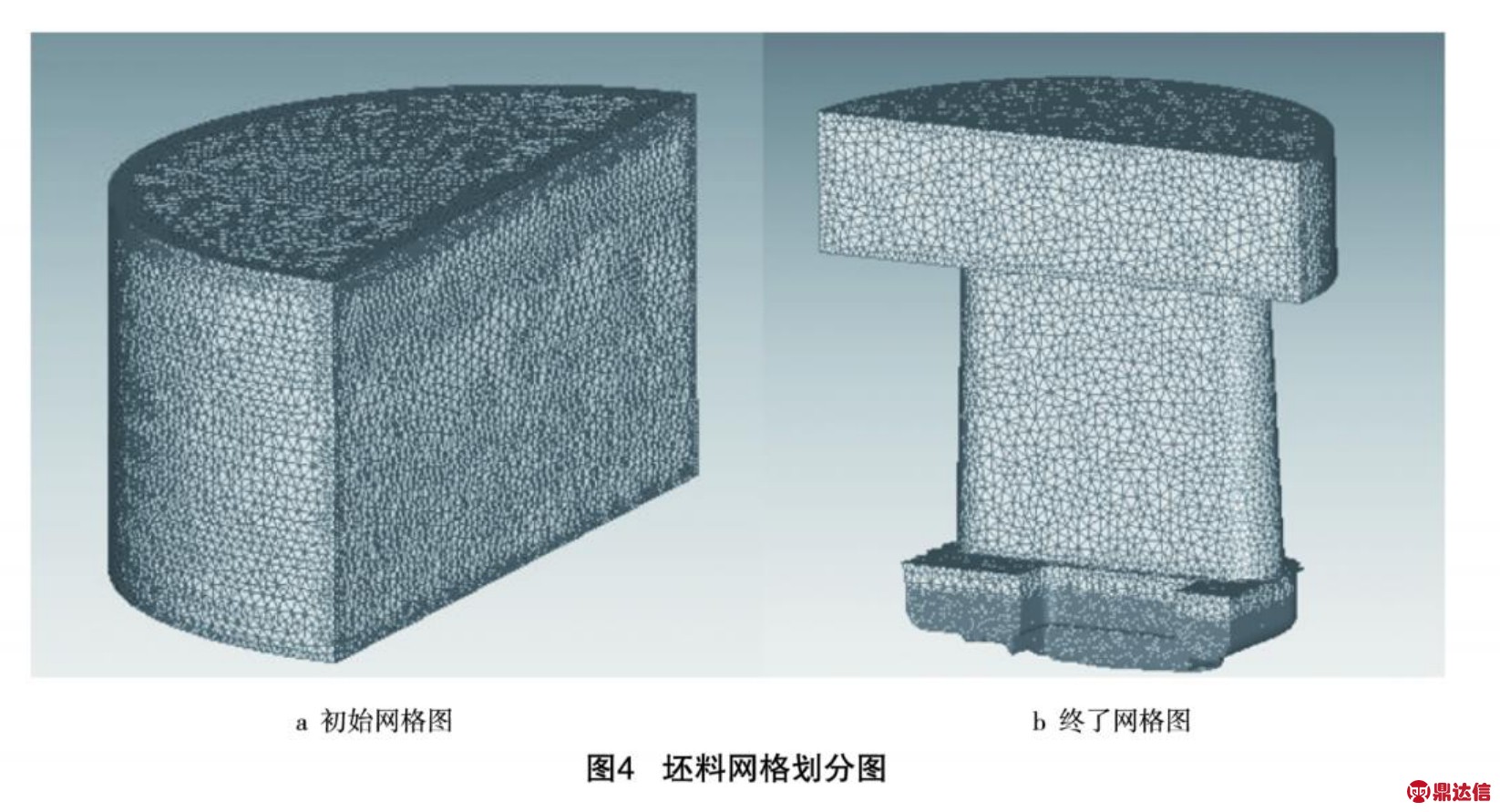
2.1 挤压参数
挤压材料:6063铝合金;挤压筒直径 125mm;初始坯料高度 60mm;挤压温度 480℃~520℃;挤压机推头速度 2mm/s;挤压分流比 K=42。摩擦因子取 0.2。
2.2 模拟参数的设定
为节约计算机内存资源和计算时间,根据模具结构和材料变形过程的对称性,采取 1/2模型进行分析。
开始挤压时,坯料部分变形比较缓慢,但下半部分金属在流出焊合室时的网格畸变程度较大,需要在坯料的下半部分进行网格细化,窗口细化比例为0.01。如图 4所示。
根据坯料有限元最小的网格边长,设定挤压的时间步长为 0.04s,当金属即将进入工作带时,将步长调整为 0.02s。
3 模拟结果与分析
3.1 初始模拟
根据上述初始设计的模具形状及参数,通过DEFORM-3D软件的有限元模拟,可得到挤压件及其各种物理场量的分布,从而检验设计的模具是否合理。理想的材料流动结果应该是在工作带出口处断面上各质点的速度均匀分布,进而获得理想的型材制品。
图 5所示为模拟过程各阶段金属流动情况。
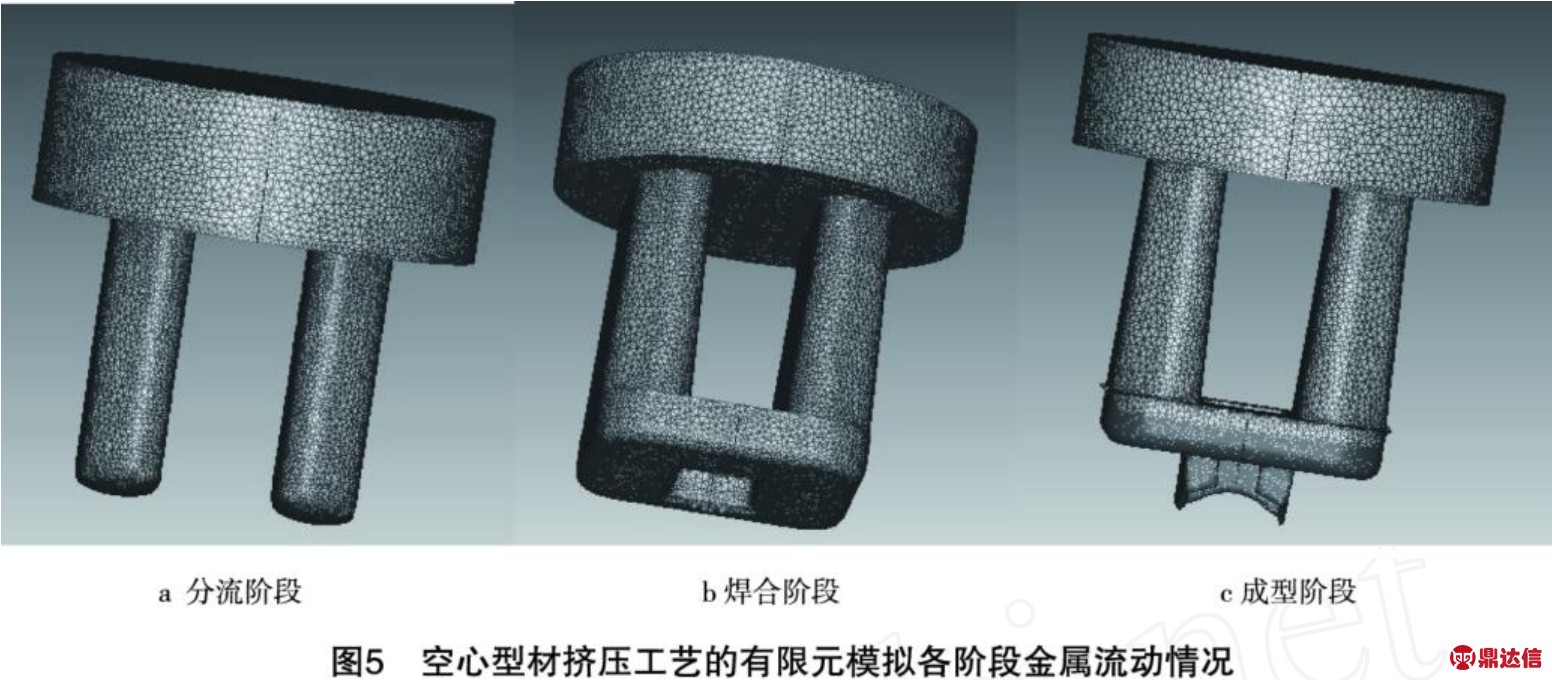
图 5c为型材流出模孔时金属的流动示意图。由图可看出,金属流出工作带时的流速不均,型材的长边一侧的金属流动速度明显大于短边一侧,出现了端面严重不平的现象,容易导致型材扭曲变形,影响型材的成型性,因此要采取措施,优化模具设计,消除缺陷。
影响金属流出工作带时流动速度的因素与金属从分流孔流入到焊合室并从工作带流出的路径有关,直接涉及到分流孔的形状尺寸和位置、焊合室的形状尺寸以及工作带的尺寸等[6]。从模拟的整个过程来看,金属在焊合室的焊合情况良好,分流孔的形状及尺寸合适,因此通过修改工作带的参数来实现优化模具设计的目的。
在分流组合模中,工作带除了决定型材的尺寸,还可以起到调整金属流速,使金属流动趋于均匀的作用。工作带的结构要素是其长度。工作带过短会导致型材的尺寸不稳定,同时也会使工作带易损,降低模具寿命;而工作带过长,则容易在其表面造成金属粘连,使制品表面出现麻面、毛刺等缺陷,影响制品质量[7]。
初始模具设计中,由于模孔全部处于分流桥的遮挡之下,因此模孔的工作带长度为相等长度。现在,为了增加型材长边的摩擦阻力,减缓此处金属流速,故增加型材长边一侧的工作带长度,并使工作带圆滑过渡到短边处,以达到金属流动均匀的目的。
3.2 优化设计后的模拟结果
经调整工作带后,对修改过的模具进行有限元模拟,由模拟结果可知,金属的流速比原来的均匀,端面没有存在严重不平的现象,得到了成型性良好的型材。图 6所示为工作带优化后焊合室的应力情况及型材的成型情况。
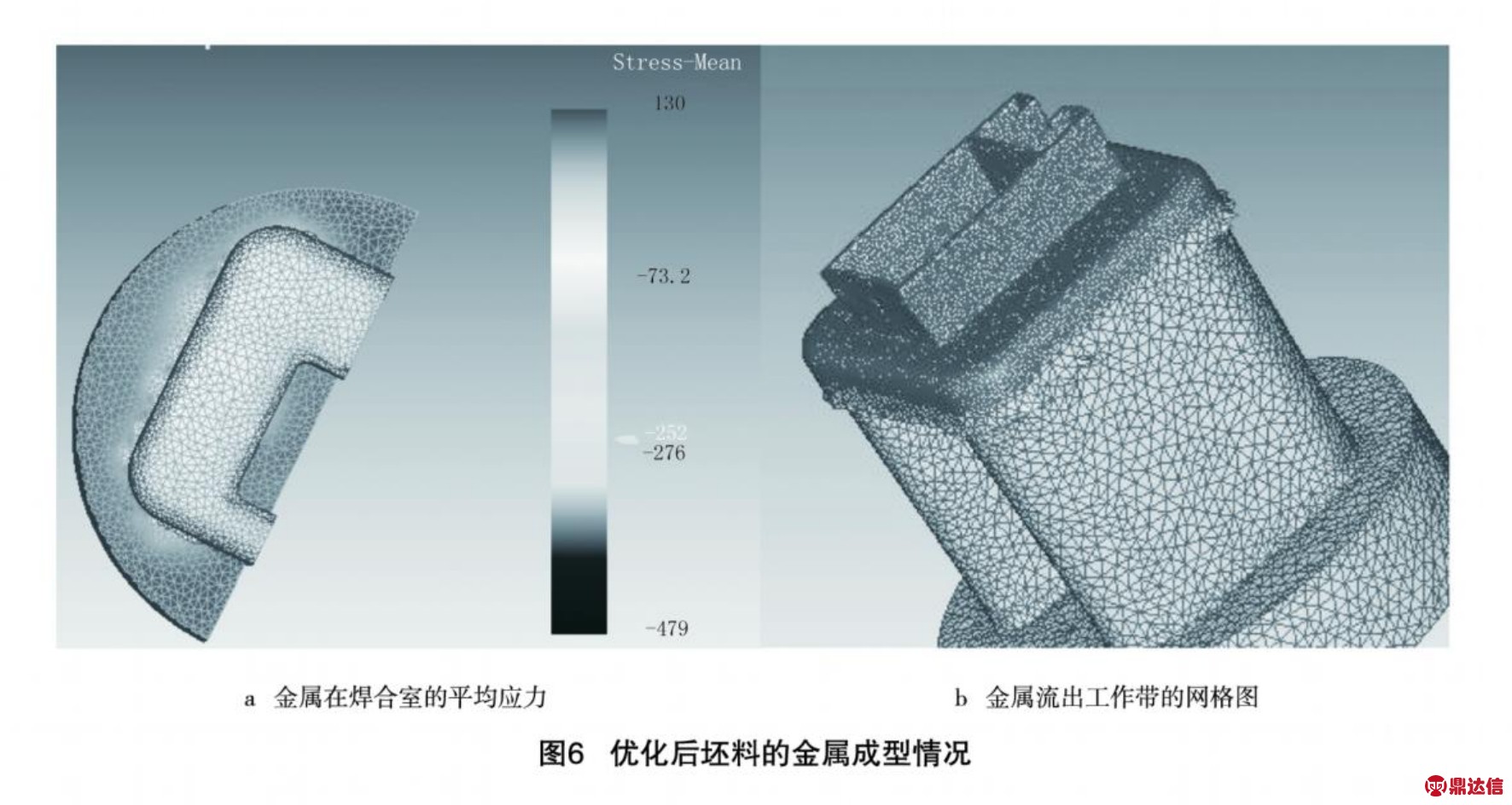
由平面分流组合模的模具结构的特殊性,可知焊合面应力分布情况关系到金属的焊合质量,直接影响到型材的质量。只有焊合面的平均应力达到一定的值,金属才能焊合,所挤出的型材质量才能符合需要。图 6a是型材在即将挤出工作带时,静水压应力的等值线图。可以清楚地看到,在金属焊合面上的平均应力在 180-220Mpa左右,超过了合金的屈服强度,可以满足焊合条件的要求。
经优化工作带后,型材的长边一侧的金属流动速度变缓,金属流动在各部位都趋于均匀化,能够保证流出工作带的金属流速均匀,如图 6b所示。
4 结论
运用 DEFORM-3D三维模拟软件对 6063空心铝型材的挤压过程进行了有限元模拟。平面分流组合模挤压过程的模拟中,如何控制几何模型数据存储的误差、有限元网格的局部细分、不同阶段的步长调整、手动划分网格等都是需要注意解决的问题。通过实验,可以从模拟结果后处理中清楚地获得挤压的应力情况,以及金属的流动规律。针对空心型材挤压件的不平衡流动缺陷,对原始模具设计采取了改进工作带不同部位的长度尺寸的措施,提高了型材的产品成型性。有效地指导挤压工艺与模具结构优化是进行有限元模拟的最终目的,从而提高了产品开发质量,缩短了模具设计的时间,节省了由于反复试模而带来的大量费用。