摘 要: 提出了基于模拟退火算法的阻尼孔组合优化方案,实现了多孔式液压缓冲器的优化设计。根据缓冲器缓冲过程中的受力状态和孔口流量特性,建立了多孔式缓冲器缓冲过程的动态数学模型;以阻尼孔直径、阻尼孔间距和阻尼孔数量为优化变量,基于缓冲器动态数学模型与模拟退火算法,建立了阻尼孔组合优化求解模型;根据该优化模型对阻尼孔的3个优化变量进行了组合优化,并将优化前后的数据输入到多孔式液压缓冲器的AMESim仿真模型中进行验证。仿真结果表明:同最初方案相比,组合优化后的液压缓冲器的内腔最高压力降低了12%,缓冲行程缩短了6.7%,缓冲过程更加平缓。
关键词: 液压缓冲器;阻尼孔优化;模拟退火算法;特性分析
引言
多孔式液压缓冲器是利用油液流经阻尼孔产生阻力来消耗冲击能量,由于其吸能密度大,缓冲性能稳定,得到越来越广泛的应用[1-2]。液压缓冲器的性能取决于内部阻尼孔设计、油液黏度、活塞面积等本身的设计参数,以及初压力、加工公差以及工作条件等其他参数[3-7],其中,液压缓冲器的阻尼孔孔径与排布方式是影响缓冲效果的关键因素[8]。
田文健[9]首次系统的推导缓冲器数学模型并探讨了阻尼孔的设计方法;张翠霞等[10]对比分析了混合介质缓冲器不同参数下的动力学特性;汪云峰等[11]对缓冲器主要结构参数进行了优化研究,阳雄和孙爽[12-13]分别以粒子群算法和遗传算法算法对阻尼孔进行了优化设计;Duym和Raymond等[14-16]研究了液压缓冲器的热传导规律,提出一种以热传导为基础的新建模思路;王成文和吴林倩[17-18]通过Fluent软件对缓冲器进行了优化设计。
多孔式液压缓冲器的阻尼孔直径、阻尼孔间距和阻尼孔数量决定了其工作特性;针对阻尼孔的优化设计,未见以阻尼孔直径、阻尼孔间距和阻尼孔数量为优化变量进行组合式优化。本研究提出基于模拟退火算法的阻尼孔组合式优化方案并对优化结果进行了模拟验证,为阻尼孔的优化设计提供了理论指导和模型参考。
1 数学模型的建立
1.1 前提假设
前期作者提出的多孔式液压缓冲器[19]的结构简图如图1所示,由于运动部件多,装配关系、组成结构复杂,工作性能受外界因素影响大,为简化分析,在保证仿真结果真实有效的情况下对部分因素做如下假设[17]:
(1) 在流体力学中,单次工作时间和油液流动时间不超过1 min即可认为是绝热过程。而液压缓冲器的单次工作时间一般低于5 s,且工作频率不高,所以假定液压缓冲器工作过程为绝热过程;
(2) 液压缓冲器尺寸相对较小,工作油液的的重力势能远远小于其动能与压力能,故忽略其重力势能;
(3) 活塞与内缸,复位活塞、内缸和外缸之间公差选择合理,根据流体动力学理论,运动副建立起的油膜压力足以实现密封,另外,运动副之间配有密封圈等密封装置,因此假定运动副之间的泄漏量为0;
(4) 缓冲过程中缓冲器工作腔,尤其高压腔内的压力很大,并不断变化,且油液温度也不断变化,由此引起的系统刚性结构的弹性变形极为复杂,因此,忽略压力及温度引起的系统结构件的弹性变形。
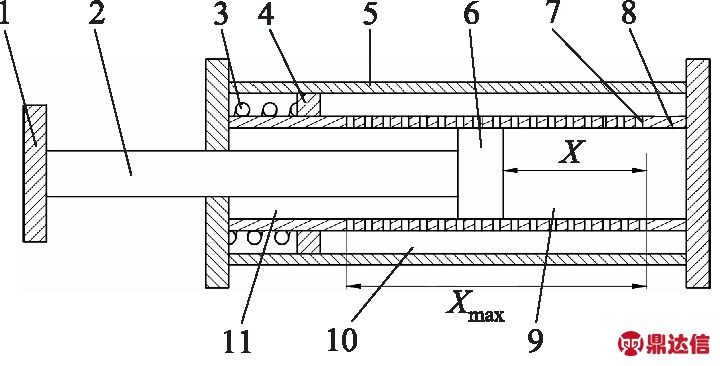
1.撞头 2.活塞杆 3.复位弹簧 4.复位活塞 5.外缸 6.活塞
7.阻尼孔 8.内缸 9.无杆腔腔 10.复位腔 11.有杆腔
图1 液压缓冲器结构简图
1.2 活塞受力分析
根据1.1假设,液压缓冲器撞头与活塞杆作为整体进行考虑,液压缓冲器竖直放置,冲击物从高处向下冲击,其受力状态如图2所示,根据牛顿第二定律,得活塞受力平衡方程:

(1)
式中, m —— 运动物体质量
g —— 重力加速度,9.8 m/s2
p2 —— 有杆腔压力
p1 —— 无杆腔压力(或复位腔压力,复位腔与有杆腔互通,其压力值一样)
A1 —— 活塞横截面积
A2 —— 活塞杆横截面积
Ff —— 活塞对于内缸的摩擦力
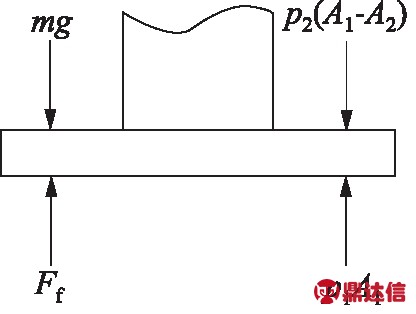
图2 活塞受力分析图
1.3 节流口流量方程
本设计中的阻尼孔为薄壁短孔,根据液压流体力学,薄壁短孔的流量方程[20]为:
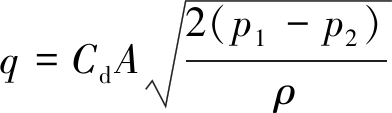
(2)
式中, q —— 薄壁短孔的流量
A —— 阻尼孔总面积
Cd —— 流量系数
ρ —— 油液密度
1.4 流量连续性方程
在缓冲时间Δt中,高压腔即无杆腔油液的体积变化主要来自:
(1) 自阻尼孔流出的油液体积(忽略泄漏): qΔt
(2) 油液被压缩的体积:
(3) 活塞位移占用的体积: A1x
故高压腔的油液连续性方程为:
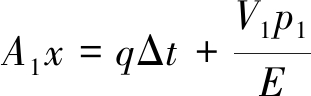
(3)
式中, V1 —— 缓冲过程中被压缩油液的体积,
V1=(S0-x)A1
E —— 油液弹性模量
S0 —— 液压缓冲器总行程
x —— 活塞位移
低压腔即有杆腔和复位腔(复位腔与有杆腔互通,其压力值一样),有杆腔油液体积变化主要来自活塞杆与活塞位移占用的体积:(A1-A2)x,复位腔油液体积变化主要来自于复位活塞位移占用的体积:A3y。
由于p1远大于p2,油液体积弹性模量很大,因此忽略低压腔油液压缩体积,无杆腔流出的油液体积等于复位腔和有杆腔流入油液体积,则连续性方程为:
A1x=(A1-A2)x+A3y
(4)
式中, A3 —— 复位活塞横截面积
y —— 复位活塞位移
1.5 复位活塞受力分析
复位活塞上侧受弹簧力,下侧受复位腔液压力,其受力状态如图3所示,根据牛顿第二定律,得复位活塞受力平衡方程:
ky=p2A3
(5)
式中, k为复位弹簧刚度。
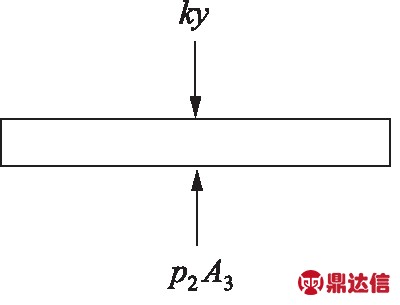
图3 复位活塞受力分析图
综上所述,经过方程式化简组合,得状态方程组为:
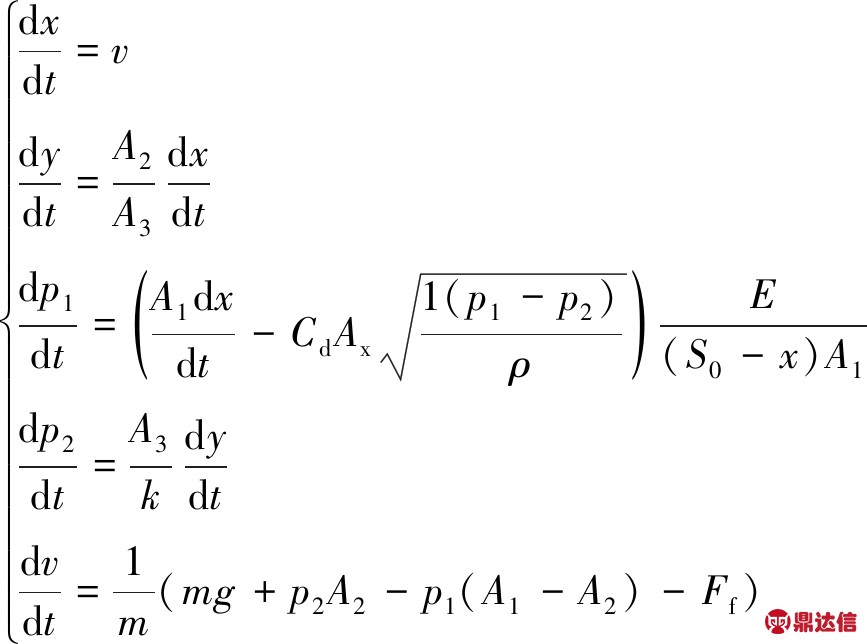
(6)
2 阻尼孔的优化
本设计的模型参数见表1。
表1 数值模型参数表
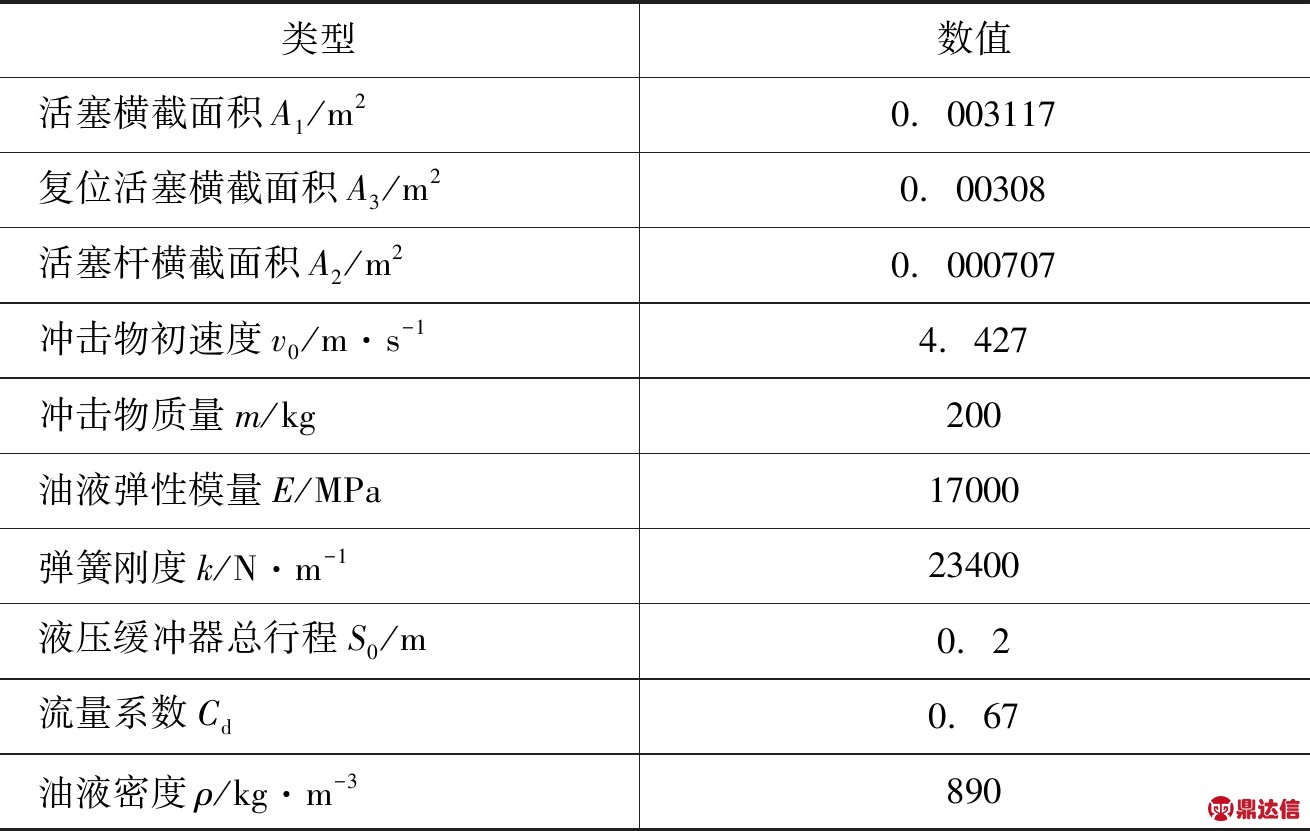
2.1 优化变量的确定
本设计将阻尼孔直径、阻尼孔数量、阻尼孔间距作为优化变量,由于本缓冲器的类型为多孔式液压缓冲器,其阻尼孔离散分布在缓冲器的内缸缸壁内,所以采用优化组合的方式进行优化,表2位优化变量取值,图4为内缸阻尼孔分布示意图。
表2 优化变量取值
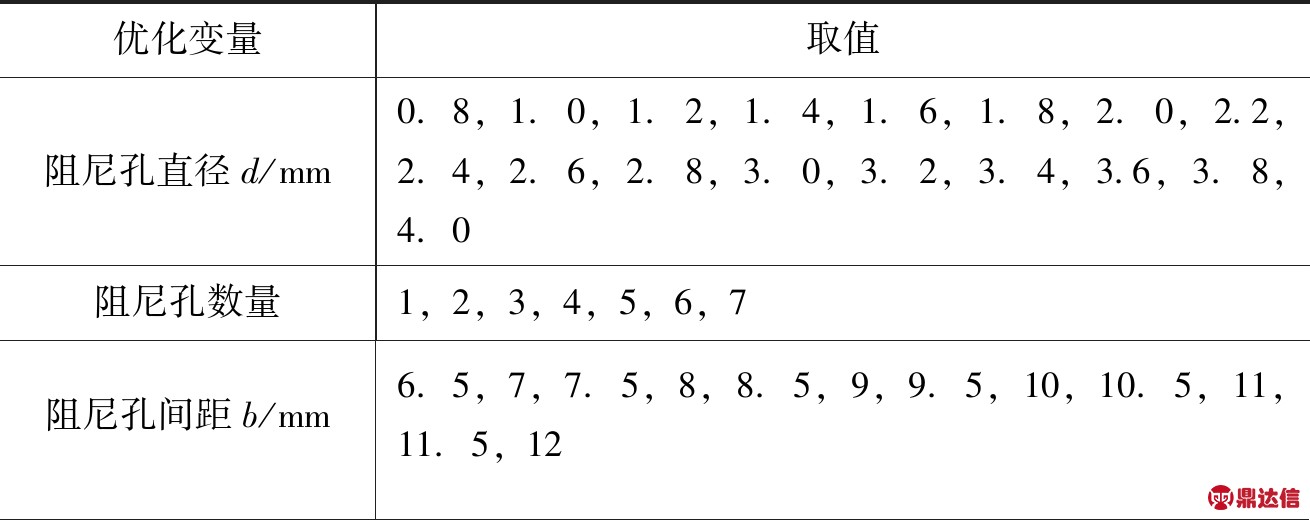
2.2 目标函数的确定
在给定能量下,缓冲器在最大缓冲行程内峰值缓冲力最小。因此,选定给定吸收能量时峰值缓冲力最小为优化目标,即选定缓冲器缓冲效率最大为优化目标。本研究提出的优化目标函数为:
Minc=Fmax-FN
(7)
式中, c为缓冲器实际最高缓冲力与理想最高缓冲力之差,如图4所示。 Fmax为缓冲器实际最高缓冲力; FN为理想缓冲力。
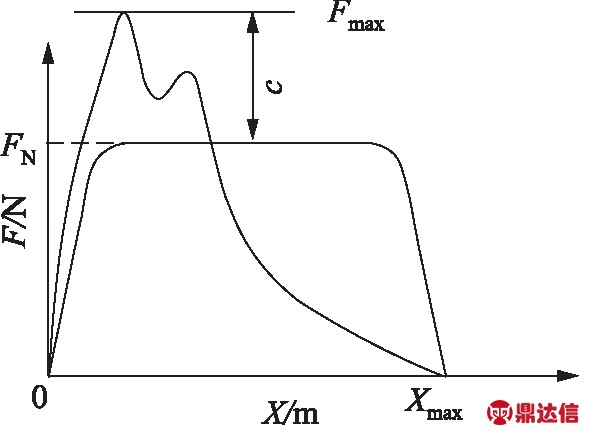
图4 优化目标示意图
2.3 约束条件
通过对液压缓冲器性能需求可知,工作状态较优的缓冲器,其工作状态平稳、平均缓冲力小、缓冲位移适中的基础上,达到较好的缓冲效果。由于液压缓冲器缓冲位移、复位弹簧位移和缓冲时间都必须满足一定要求,因此,以缓冲位移、复位弹簧位移和缓冲时间最大值作为约束条件,即:
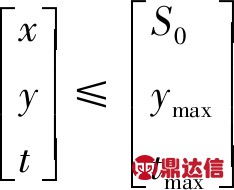
(8)
式中, ymax —— 复位活塞最大位移
tmax —— 缓冲器最大工作时间
2.4 优化求解及优化结果
由于液压缓冲器阻尼孔离散分布在缓冲器的内缸缸壁内,需要采用优化组合的方式进行优化,故选用优化组合中最为经典的算法-模拟退火算法。
液压缓冲器状态方程式(6)是一组常系数非线性微分方程组,采用四阶龙格库塔求解,根据表1数值模型参数可以得出液压缓冲器高压腔、低压腔、活塞速度、活塞位移和缓冲力曲线,使用MATLAB软件编制求解程序,优化结果如表3所示。
3 基于AMESim的仿真分析
AMESim软件提供了用于机械、液压、气动、热、电和磁的系统建模仿真及动力学分析的平台, 用户可以在一个平台上建立复杂的多学科领域系统的模型,并在此基础上进行仿真计算和深入的分析。按照图1所示的简化模型,本研究将液压缓冲器等效为如图5所示的AMESim模型。根据前面已知条件设置仿真参数,并且将优化前后阻尼孔参数输入模型中,运行AMESim软件,其仿真结果如图5~图11所示。
表3 优化结果
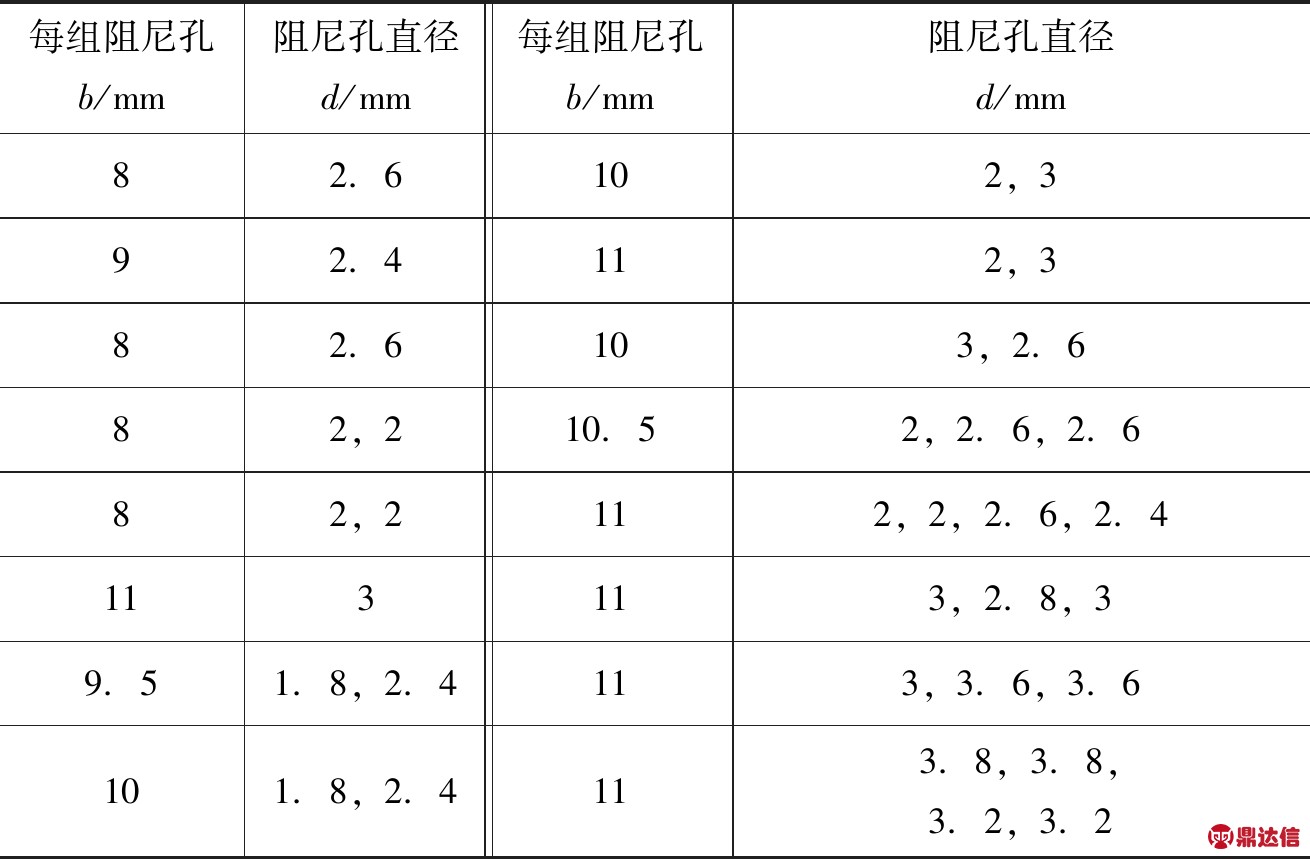
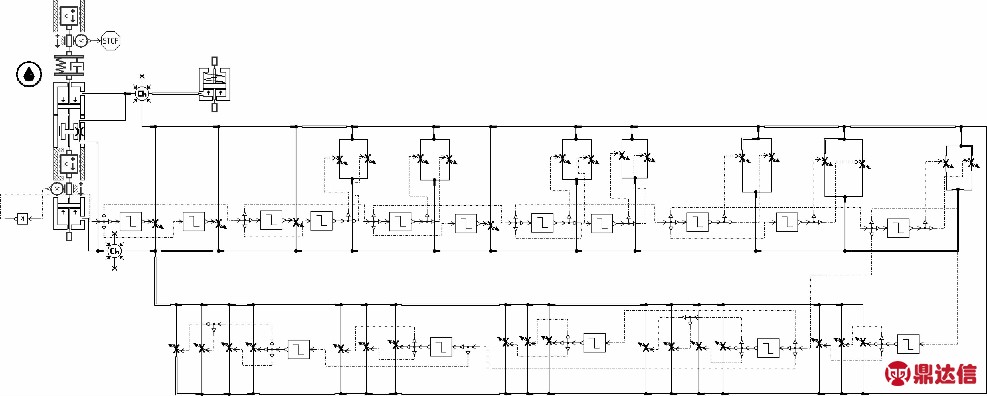
图5 液压缓冲器AMESim仿真模型
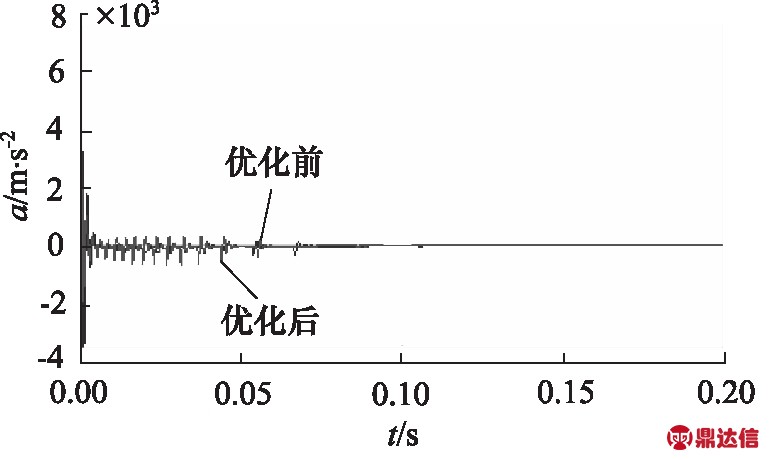
图6 优化前后缓冲加速度对比曲线
从图6可以看出,优化前冲击物在缓冲过程的初始阶段,加速度在正负值之间波动,这是由于冲击物撞击缓冲器撞头后震动产生的,而且优化前加速度的峰值大于的优化后加速度峰值,从而导致优化前缓冲器的缓冲力大于优化后缓冲力,从图10也印证了这一点;在缓冲起始阶段,高压腔压力很高,压力能转化为油液动能,因此通过阻尼孔的油液速度很快,导致部分区域油液压力降低,甚至低于大气压力,如图7所示。
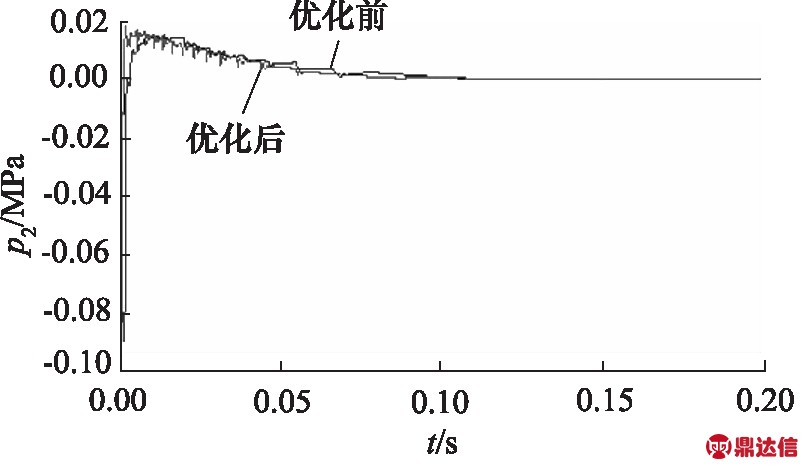
图7 优化前后缓冲低压腔压力对比曲线
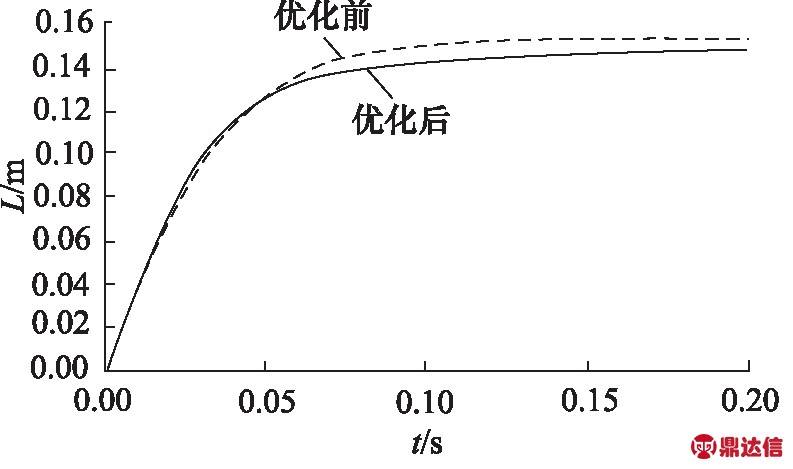
图8 优化前后缓冲行程对比曲线
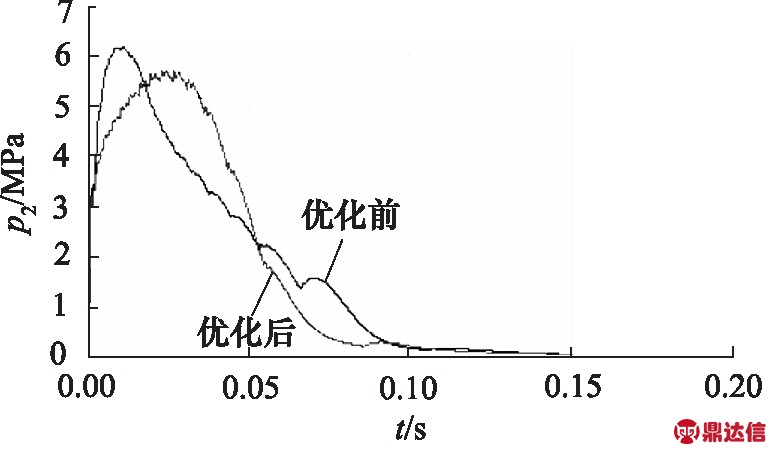
图9 优化前后高压腔压力对比曲线
从图9可以看出,缓冲起始阶段,冲击物与缓冲器撞头接触瞬间,高压腔压力迅速上升,优化前缓冲器高压腔上升到6.2 MPa,优化后缓冲器高压腔最高压力降为5.6 MPa,高压腔最高压力降低了10%且高压腔压力变化更加平稳;与此同时,如图8、图10、图11所示,缓冲器产生的缓冲力也很大,使冲击物速度急速下降,但由于冲击物速度较大,因此,冲击物位移增加很快;如图7所示,缓冲器在缓冲过程的初始阶段优化前缓冲力达到了19.3 kN,优化后降为17 kN,降低了12%,较优化前缓冲力变化更加均匀;如图11所示,经过模拟退火算法优化,液压缓冲器的缓冲总行程略微减少,较优化前缓冲行程减少约0.01m,缩短了6.7%;如图9~图11所示,由于多孔式液压缓冲器的阻尼孔是非连续性分布,导致其压力和缓冲器曲线存在轻微波动,也验证了仿真模型的正确性。
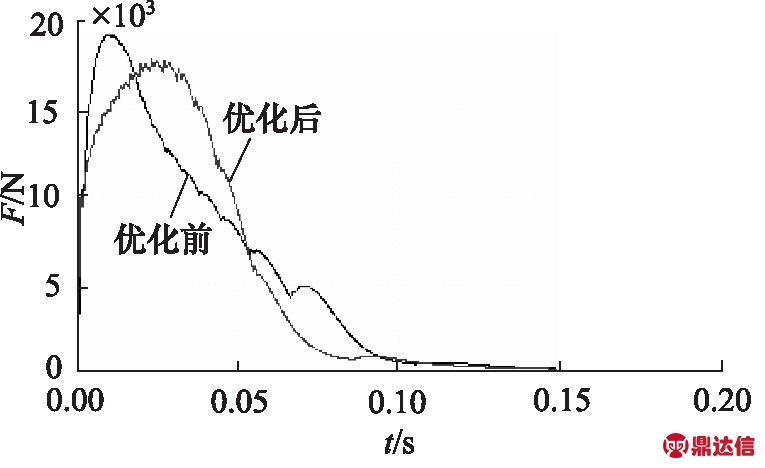
图10 优化前后缓冲力对比曲线
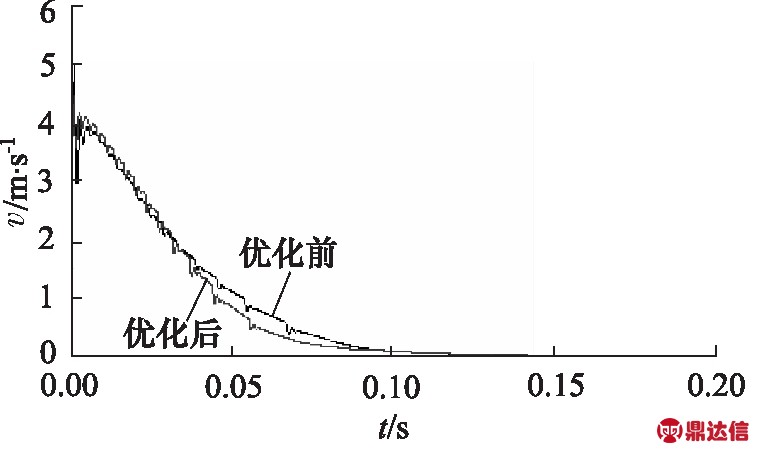
图11 优化前后冲击物速度对比曲线
4 结论
现有的研究虽然有人对缓冲器的阻尼孔进行过优化设计,但均没有以阻尼孔直径、阻尼孔间距和阻尼孔数量为优化变量进行组合式优化,提出基于模拟退火算法的阻尼孔优化方案并对优化结果进行了模拟验证。
在现有工况下,根据该方案优化后的缓冲器的高压腔最高压力降低10%,最高缓冲力降低12%,缓冲行程缩短6.7%,有效的提高了缓冲性能。
仿真结果为阻尼孔的优化设计提供了理论指导和模型参考,下一步研究要通过样机来验证仿真模型及优化结果的有效性。