摘要:采用普通点焊工艺参数进行车身骨架三层板甚至四、五层板的点焊连接,难以获得优良的焊接接头,同时还会带来高频次的飞溅、毛刺、焊穿等点焊缺陷,造成生产节拍和生产成本的浪费。同时在各大整车厂越来越多地引入热成型板后,传统的单脉冲点焊工艺参数已经难以获得飞溅少、成形好的点焊接头。针对此类包含热成型板的多层板点焊连接,采用基于BOS6000软件的点焊控制器进行多脉冲点焊工艺参数试验。经金相、BOS6000 UIR曲线、现场统计反馈等论证,采用多脉冲点焊工艺能够获得焊点可靠、飞溅率低的焊接接头。
关键词:点焊;多层板;多脉冲;BOS6000
0 前言
汽车的安全性能和车身轻量化是当今世界汽车工业发展的潮流,因此热成型板、高强度镀锌钢板的使用越来越普遍,其焊接品质备受青睐。在汽车白车身的焊接中,特别是三层/四层厚板的焊接及匹配间隙大的焊点,采用普通的焊接工艺难以获得质量优良的焊点,不仅影响生产效率,而且严重影响白车身的焊接质量。若仅增加焊接电流或焊接时间,则可能造成焊接热输入过大,导致焊点过烧、飞溅大等焊接缺陷。针对上述问题,根据生产现场情况,对部分焊点采用了多脉冲焊接的点焊优化试验,特别对厚板、三层/四层板焊接、间隙大的焊点,采用二次甚至三次通电点焊工艺,能够形成合格的焊核,避免了焊核偏移至厚板,同时能够获得形貌美观、飞溅毛刺少、焊接强度可靠等综合性能良好的焊点。国内外学者对汽车用热成型板、高强度镀锌钢板进行了大量研究,采用增加预热脉冲进行点焊能够很好地改善点焊接头的质量问题[1]。上海交通大学的唐虹[2-3]等人充分研究了多层板点焊,认为三层板焊核最初是横向扩展,然后才是纵向扩展,容易形成一定的焊核偏移。徐松等人研究热成型板点焊电流模式对点焊试样断裂点位置和中心偏析的影响,分析了焊接接头软化区中心偏析的原因[4]。本研究针对目前汽车车身常用的低碳钢和热成型钢这种差强差厚钢板的焊接存在的熔核偏移、焊点强度不合格,焊点压痕过大、焊接飞溅严重、薄板变形严重的问题,通过控制变量法设计工艺实验,利用金相分析、凿测测试等多种手段,借助BOS6000焊接控制器本身采集焊接电阻时间曲线,研究制约差强差厚钢板形成良好熔核的原因。通过设计特定的焊接工艺,使用3次脉冲电流的方法,获得熔核尺寸、位置满足要求,表面质量良好的焊点。试验在车身实际生产中对解决差强差厚钢多层板焊接的方法进行焊接稳定性验证,结果显示该焊接工艺方法能够克服焊接接头过热、焊核偏移的影响,连续焊接出尺寸合格、表面整洁、无焊接缺陷的焊点。
1 试验方法及设备
1.1 试验材料及设备
试验基于某车型车身骨架三层板的点焊连接。板材为低碳镀锌钢板和热成型板,试验材料为上海宝钢生产的普通低碳钢冷轧钢板,其中板a、c为镀锌板,牌号DC54D+Z100MB,板厚分别为0.8 mm和2mm,板b为高强度热成型板,牌号22MnB5 AS150,厚度1 mm,材料化学成分如表1所示。采用KUkA机器人自动点焊、During气伺服点焊焊枪和BOS 6000控制器。采用Cr-Zr-Cu合金电极,电极型号21-58D-8246/1,外径16 mm,焊接端面直径6 mm,电极形状如图1所示;采用蔡司Axio Imager A2m金相显微镜,威尔逊UH250万用硬度试验机。点焊工艺参数如表2所示,预压时间200 ms,维持时间200 ms。
表1 镀锌板和热成型板材料成分%

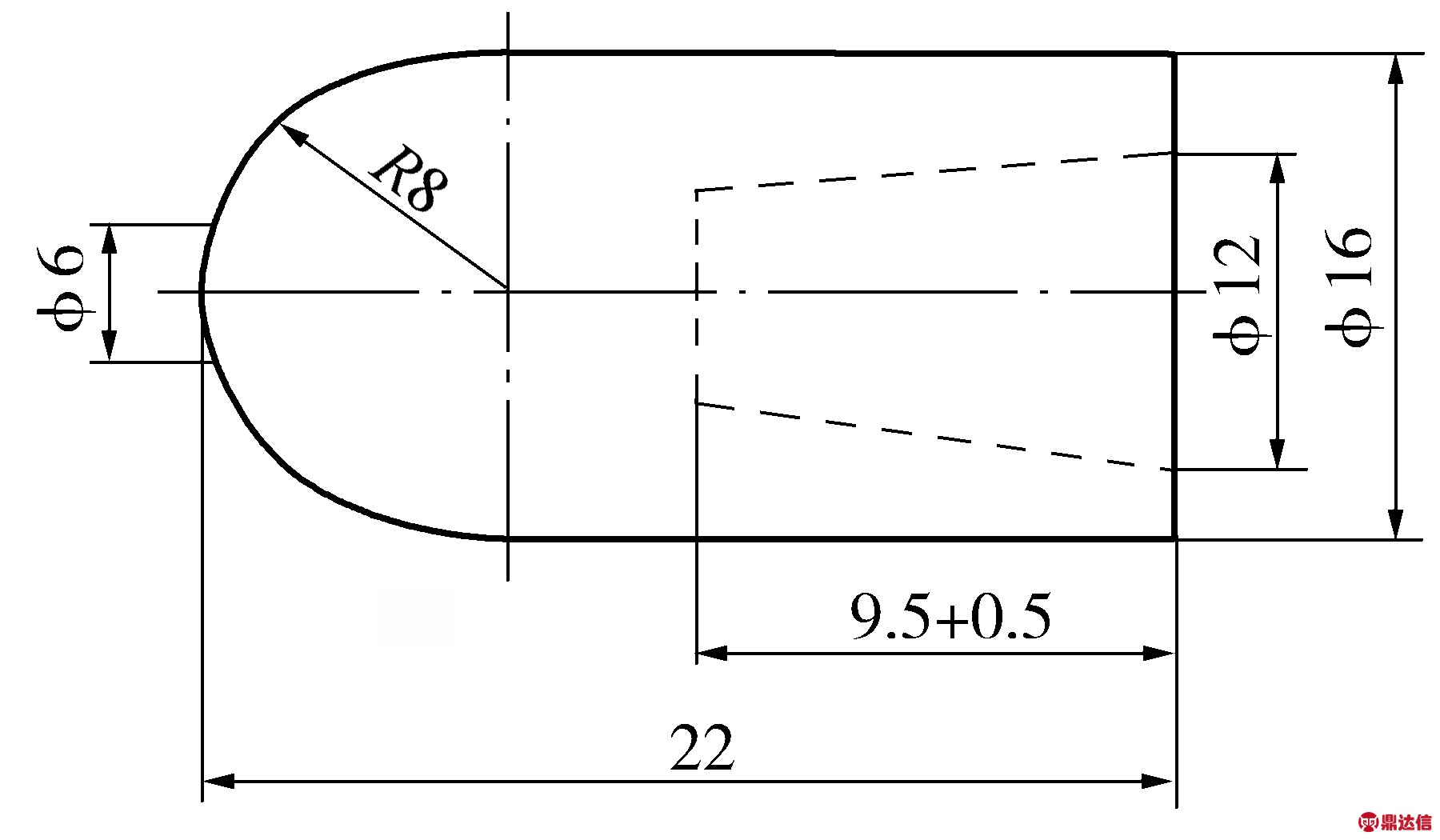
图1 电极头示意
1.2 试验方法
考虑到现场实际生产状态,在保持焊接过程热输入、预压时间、预热电流和预热时间不变的条件下,通过改变点焊脉冲次数、焊接电流和时间参数进行对比,得出最佳的焊接工艺参数见表2。
表2 点焊工艺参数
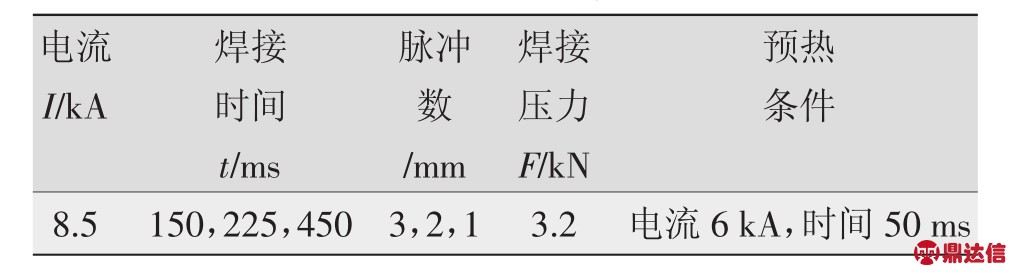
试验采用手动焊枪,选取3种生产现场使用的板材夹紧后施焊,焊接装置如图2所示。
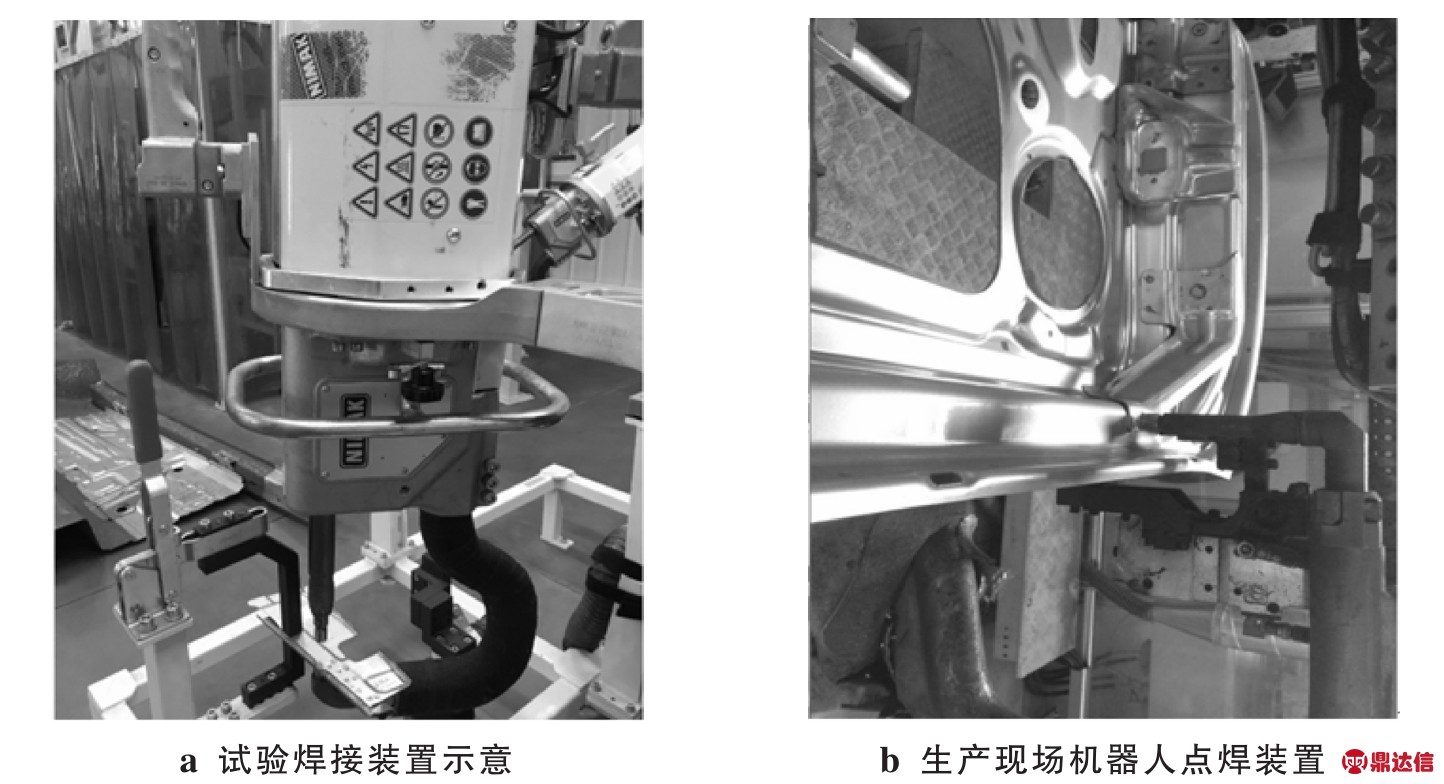
图2 多层板焊接试验设置
2 试验结果与分析
2.1 点焊表面和焊缝横截面形貌
不同脉冲条件下的焊点表面形貌和横截面形貌如图3、图4所示。
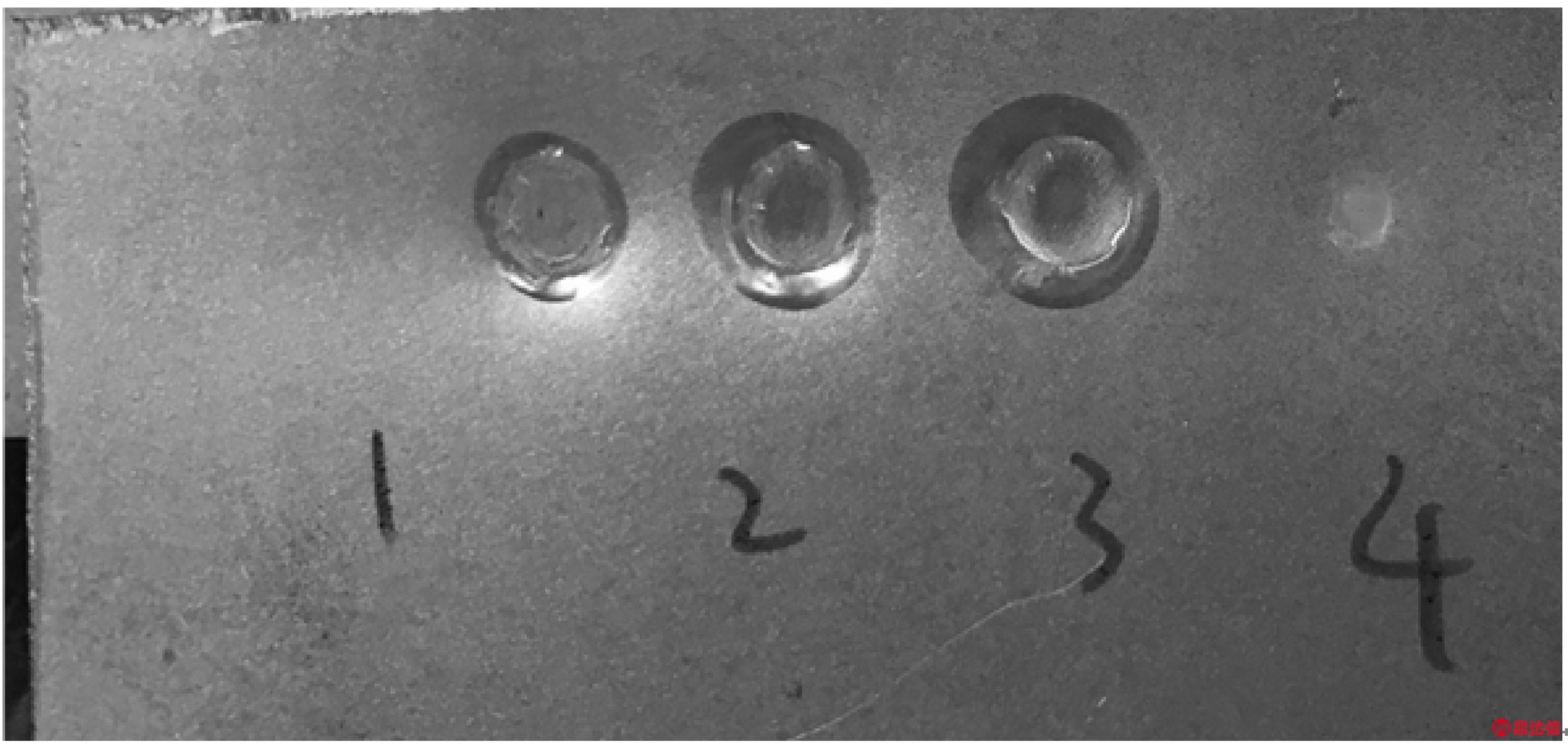
图3 多层板焊接试样焊点表面形貌
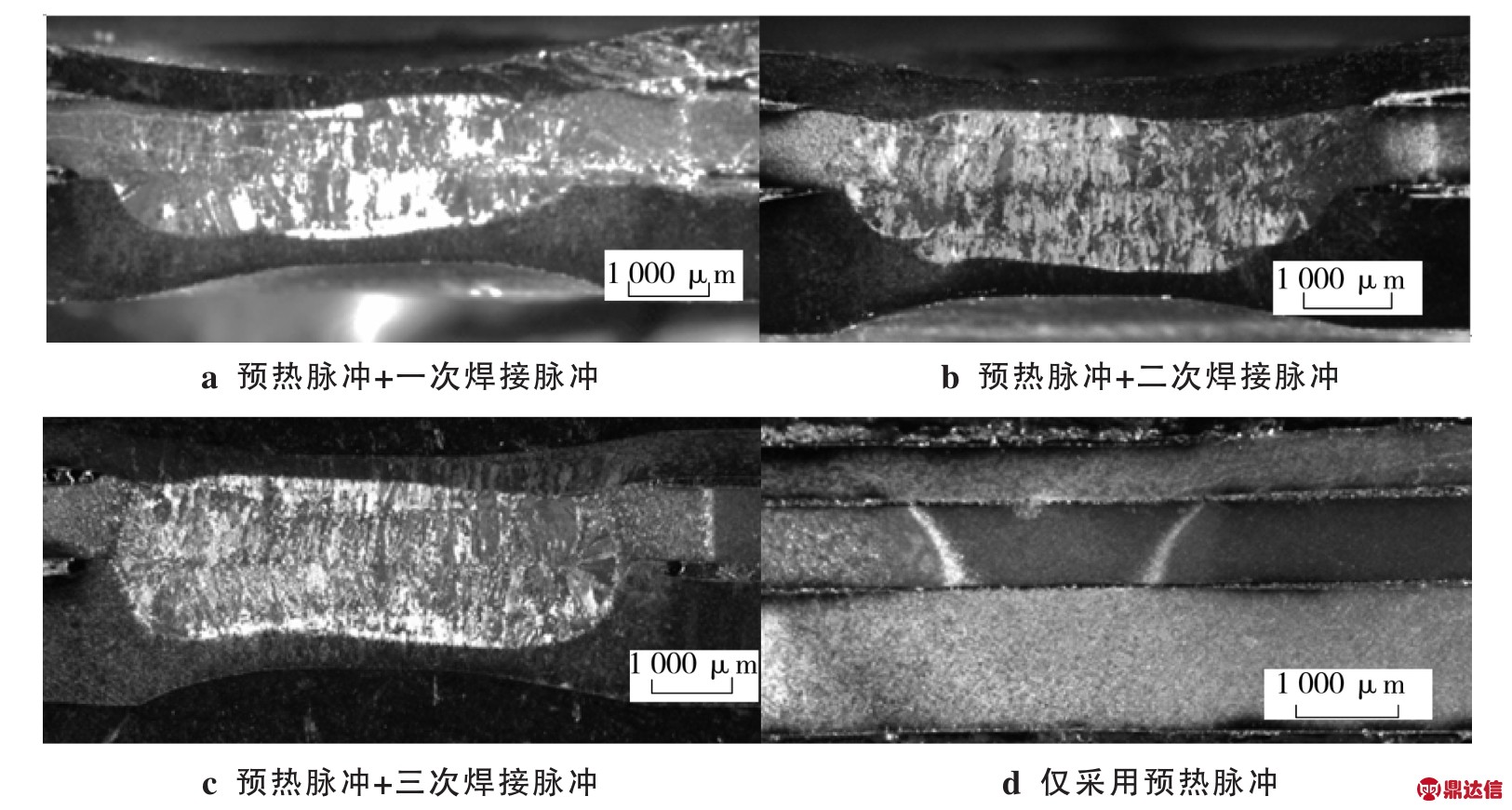
图4 多层板焊接试样横截面形貌
图3中1、2、3、4分别为采用一次脉冲、二次脉冲、三次脉冲以及仅采用预热脉冲(本试验预热脉冲不作为焊接脉冲次数)的焊点表面形貌。可以看出,随着脉冲数的增加,薄板侧焊点表面受热痕迹变得明显,说明多脉冲条件下薄板一侧的热量大于单脉冲条件,而当仅采用预热脉冲时未形成有效焊核。图4a为采用预热+一次焊接脉冲,工艺参数为50 ms/6 kA预热脉冲+450 ms/8.5 kA一次焊接,焊核已经形成,但薄板一侧焊核不足,整个焊核形状不规则,焊核在板厚方向形状过扁。图4b为采用预热+两次焊接脉冲,工艺参数为50 ms/6 kA预热脉冲+225 ms/8.5 kA两次焊接脉冲(两次焊接脉冲之间冷却时间为10 ms),与图4a相比,薄板侧的焊核熔深明显变大,焊核形貌呈较规则的椭圆形。图4c为采用预热+三次焊接脉冲,工艺参数为50ms/6 kA预热脉冲+150 ms/8.5 kA三次焊接脉冲(中间两次冷却时间均为10ms),此时薄板侧的焊核熔深更深,焊核形貌饱满均匀,呈规则的椭圆形。由上述焊核成形区别可知,在总热输入不变的前提下,增加焊接脉冲数(总热输入为:焊接电流×焊接时间,总焊接时间保持不变但将其平均分成多次焊接脉冲来完成)能够抑制焊核向厚板侧偏移同时增加焊核熔深。图4d为仅采用预热阶脉冲焊接,工艺参数为50 ms/6 kA,通过焊点横截面实验可以看出,在预热阶段三层板未形成有效连接,仅中间热成型板存在热影响区。
2.2 金相组织及硬度分析
使用显微镜观察图4c试样焊点横截面金相组织,利用万能硬度机测量焊点横截面硬度,试验结果如图5、图6所示。
镀锌板母材组织主要是铁素体(见图5d),热成型板母材的组织为细小板条马氏体组织(见图5e),这是因为热成型板工艺是在高温下塑性成型后快速冷却形成,且母材中加入B等微量元素有助于高温下的奥氏体化,通过模具控制冷却速度保证晶粒从奥氏体向马氏体转化,从而保证材料的高强度和硬度[5]。图5c为焊核与上板交界处金相组织,粗大的针状马氏体深入铁素体一侧,两种组织分界线较为明显,热影响区宽度较窄,这是因为点焊过程中加热集中且电极帽通过冷却水循环冷却,有效减小了焊接接头热影响区的大小。图5a为焊点接头处照片,焊核沿着下层板与热成型板搭接面成树枝状生长成针状马氏体组织。这是因为焊缝区最高温度Tm大于奥氏体化温度,焊接过程中发生相变时由于高温停留时间很短,只有部分铁素体发生相变,因此铁素体数量减少,马氏体数量增多,且晶粒排列杂乱;而越靠近焊核,最高温度越高,相变转化越充分,铁素体残留越少,马氏体晶粒越来越粗大,到焊核区便成为规则的板条马氏体。尤其是到焊核中心区域时,高温停留时间tm较长,冷却相对较慢,从奥氏体晶界的侧面以板条状向晶内生长成镐牙状的板条铁素体,见图5b、图5c。
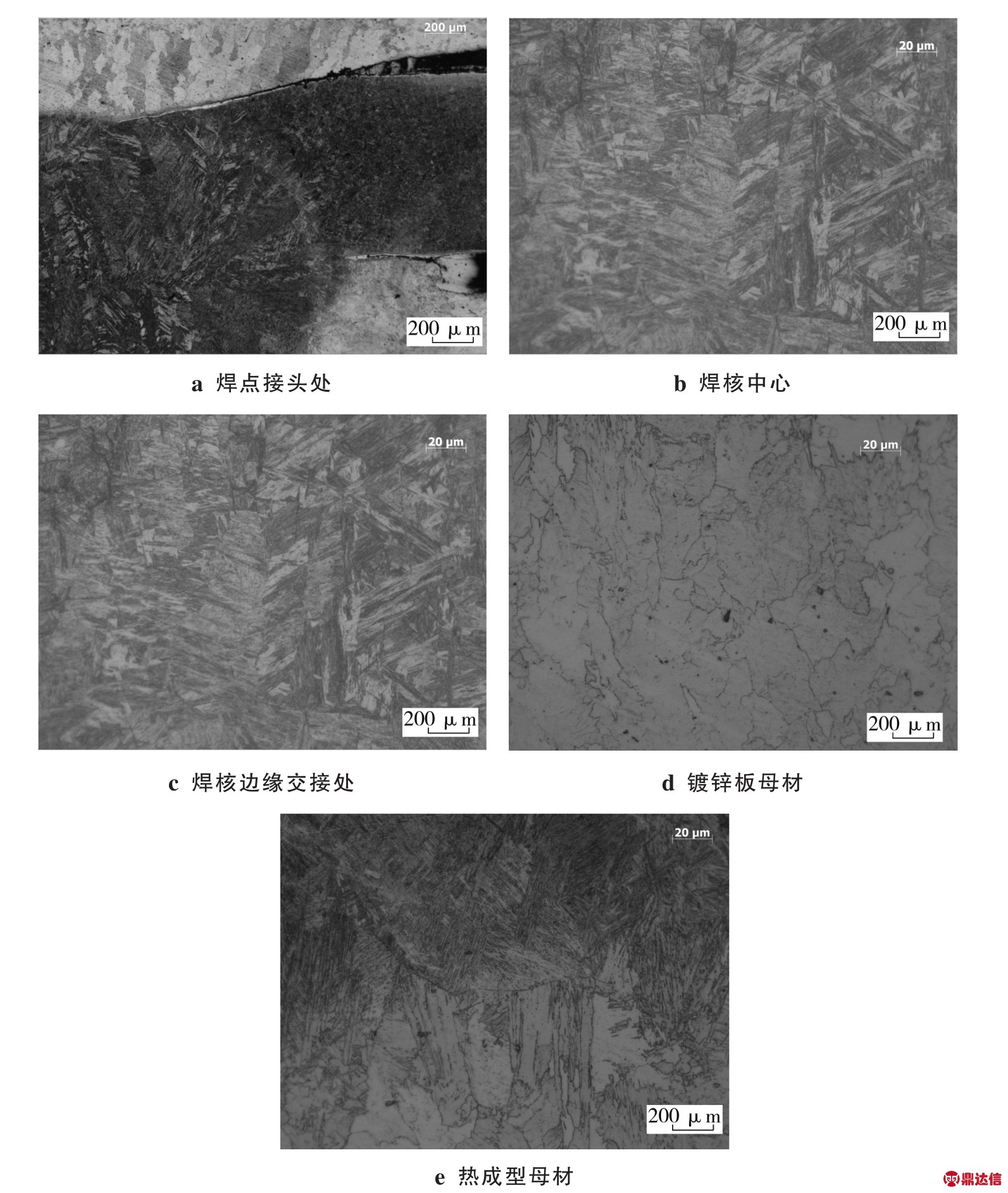
图5 焊点横截面金相照片
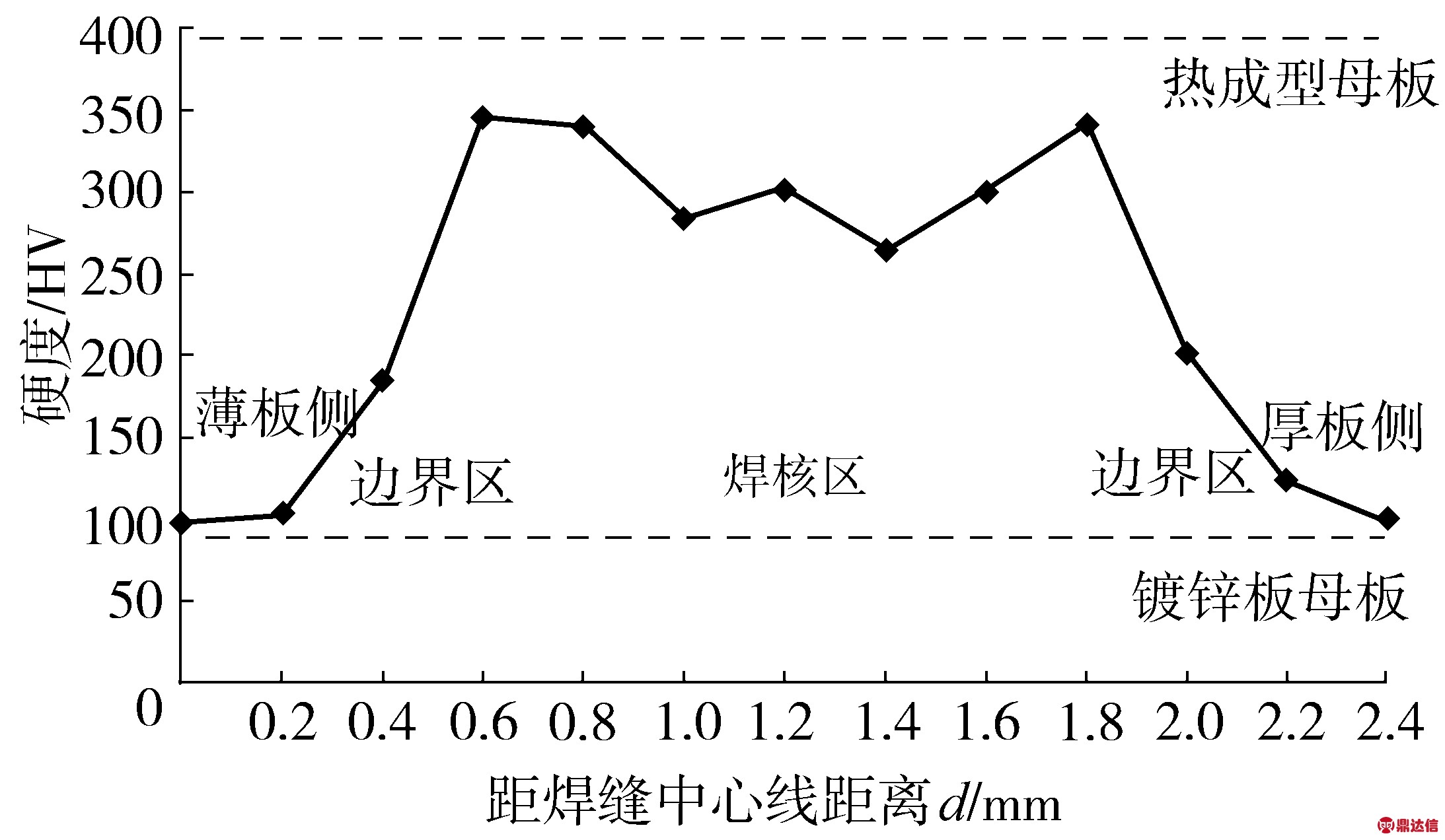
图6 显微硬度
从点焊接头横截面沿焊核中心线纵向的硬度分布(见图6)可以看出,焊点接头区横截面最高显微硬度为350HV,硬度最高点在焊核中心两侧区域,焊核区的硬度明显高于焊核交界区,而热成型板母材硬度最高,镀锌板母材显微硬度最低。焊核区越靠近焊核中心,硬度越低,显微硬度在300~350HV呈上下波动状。这是因为相对于镀锌板,点焊接头得到硬化,但相对于热成型板,由于热成型板本身组织为细小均匀的马氏体组织,硬度、强度均很高,焊接过程经过再次加热冷却后,点焊接头马氏体组织变得粗大且软化。此外整个焊核区的组织硬度差别不大,但中心区焊核硬度略低于两侧,主要原因是焊核中心区热量集中,冷却速度慢,晶粒软化程度大于焊核边缘。
2.3 多脉冲焊接实际使用结果
车身骨架焊接由于大部分都是三层板点焊连接,且包含热成型板材,采用一次焊接时需要大电流短时间硬规范来完成才能保证薄板一侧焊核直径符合要求。但通过长期金相和凿测验证发现这类点焊风险较高,薄板一侧熔核过小或没有熔合,且过大电流导致门框飞溅严重,既影响后道工艺和美观,给整车强度带来隐患,也增加了工厂监控和返修成本。因此选取总拼A柱区域三层板焊点作为实际多脉冲生产试验点,以现场跟踪飞溅效果,UIR监控的飞溅率以及金相结构作为依据判断该工艺是否起到优化作用。优化前仅采用一次焊接脉冲,焊点表面飞溅严重,照片如图7所示,需要人工100%打磨毛刺返工。优化后采用三次脉冲参数,焊点表面平整无飞溅毛刺,照片如图8所示。
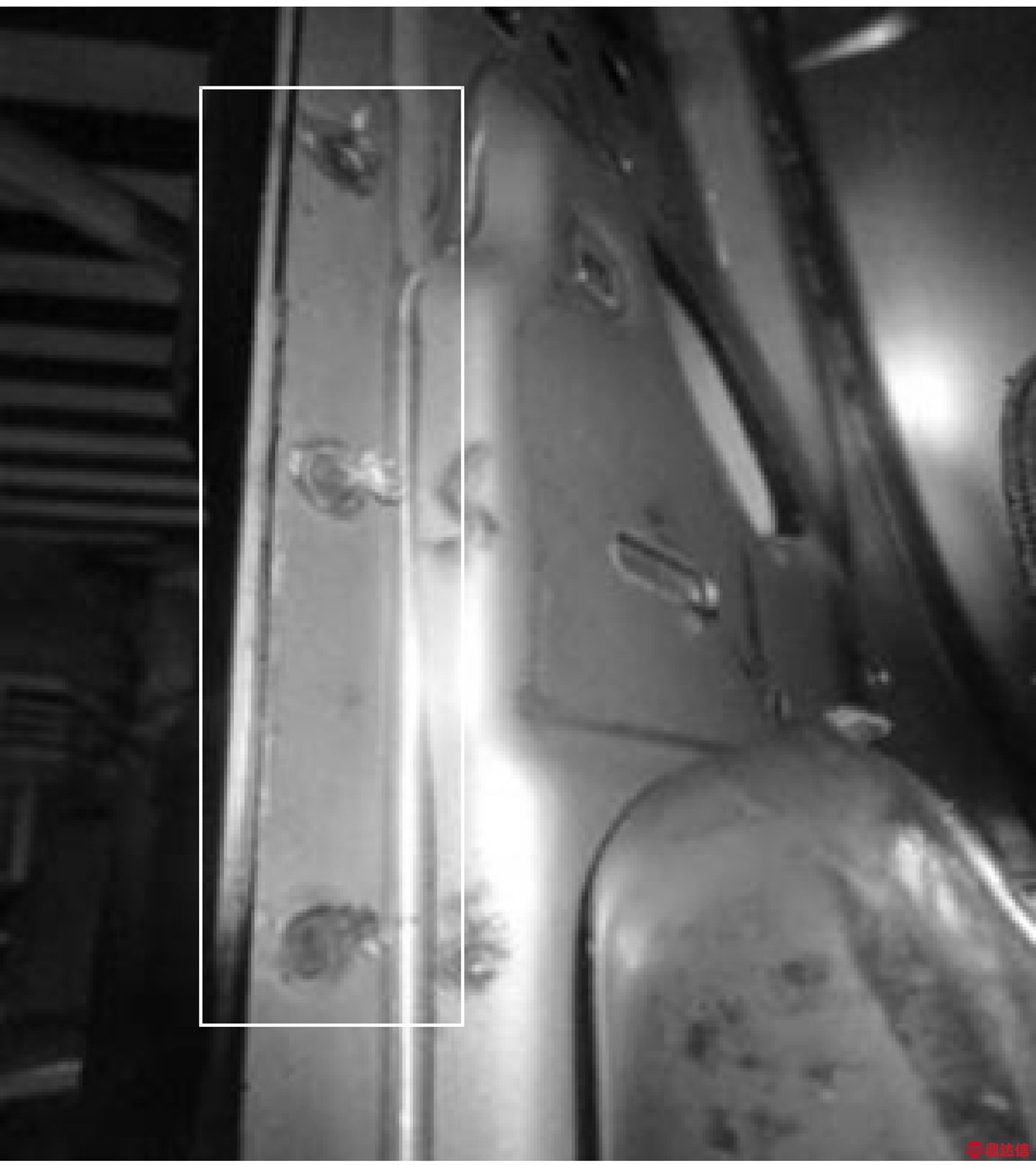
图7 采用一次焊接脉冲9.5 kA/300 ms照片
经现场跟踪统计,点焊毛刺消除,点焊飞溅率(见下文的焊缝冷却曲线)由之前的30%降至10%,极大减轻了生产线员工的劳动负荷,同时提升了生产线节拍。
2.4 UIR曲线分析
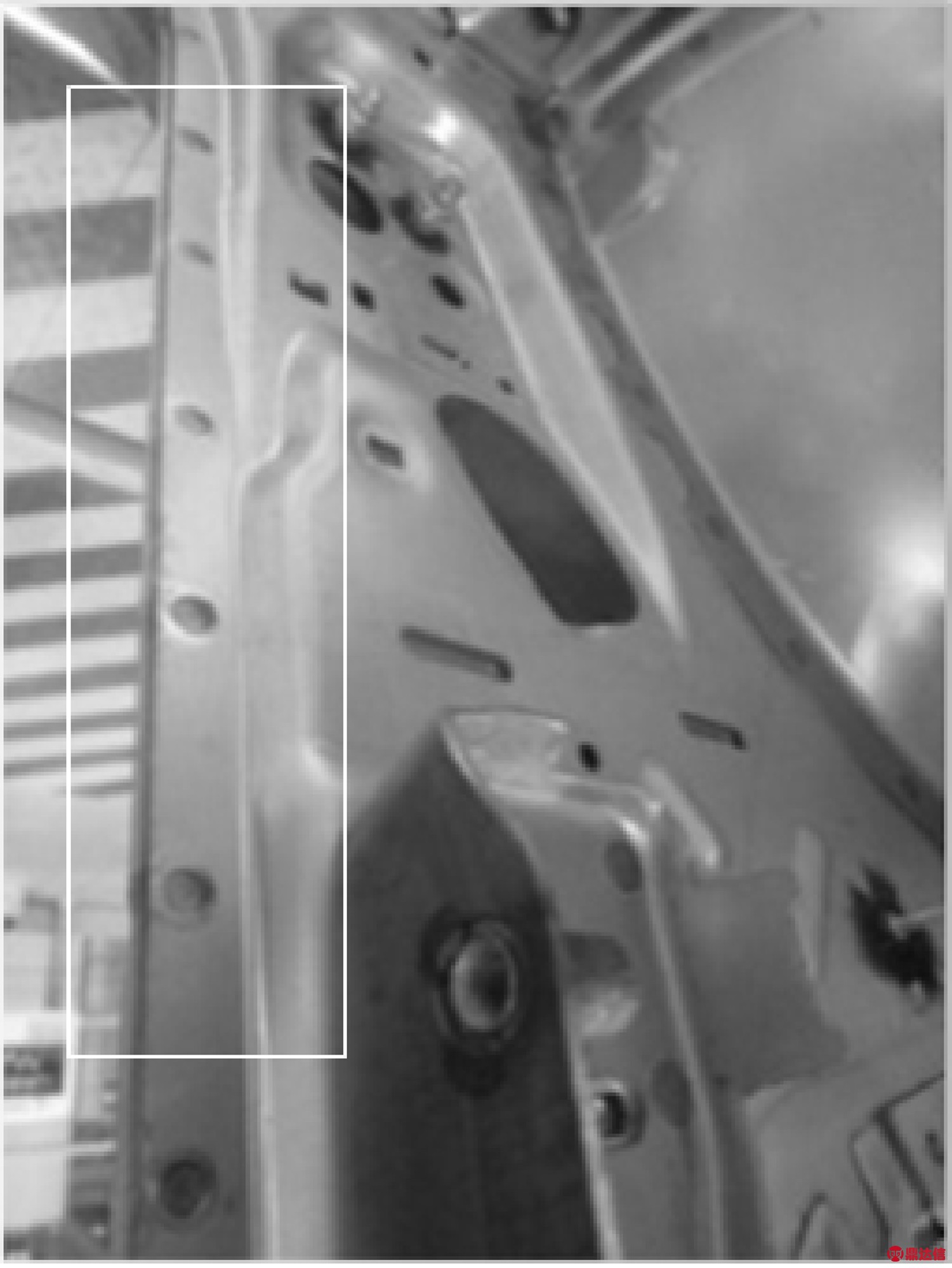
图8 采用6 kA/50 ms预热,8.5 kA/450 ms三次脉冲照片
Bos6000本身的UIR曲线具有监控焊接过程中电阻随时间变化的功能,同时该UIR曲线能够根据电阻值的陡降判断焊接过程是否产生飞溅。本次实验对单脉冲、双脉冲、三次脉冲等模式下的焊接工艺参数进行曲线对比分析,采用三次脉冲焊接时的参数设置界面如图9所示。结果发现,随着脉冲数的增加,整个焊接过程电阻值逐渐减少,焊接曲线更加平滑。当仅有一次脉冲时,在约120 ms出产生飞溅;当有两次脉冲时,约在200 ms产生飞溅但此时电阻陡降值较小,产生的飞溅小;当采用三次脉冲时则没有飞溅产生,如图10所示。这是因为多次脉冲之间存在冷却阶段(冷却时间10ms),在冷却阶段无电流作用而焊接压力保持不变,塑性环持续增大而焊核保持不变,从而有效避免了因焊核持续增大超过塑性环带来的焊接飞溅。由一次脉冲变为多次脉冲正是降低了焊核持续受热增大的速度从而降低飞溅。
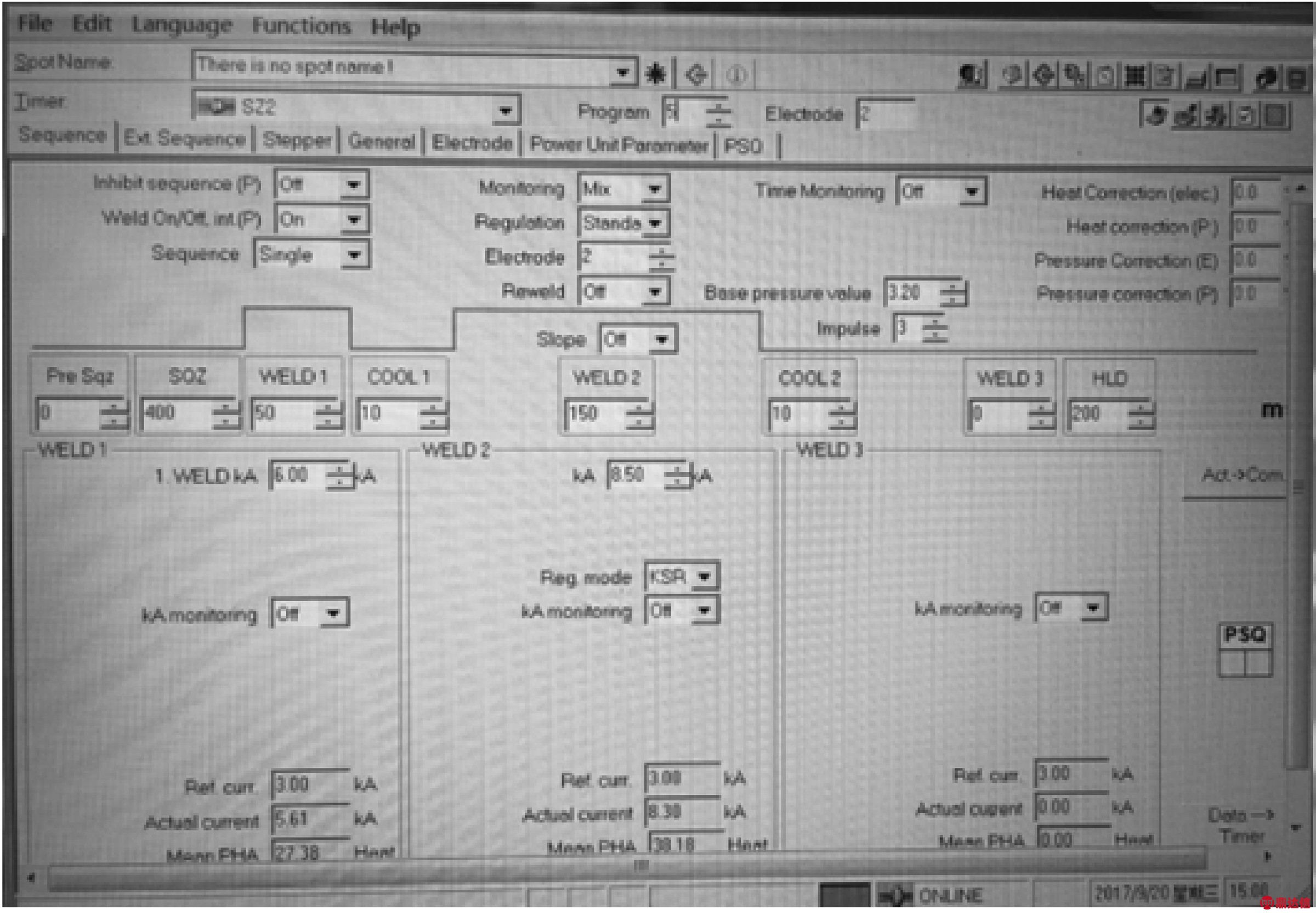
图9 采用三次焊接脉冲的参数设置界面
3 结论
(1)采用多脉冲点焊工艺可以获得无焊核偏移、焊点成形良好的点焊接头,且能够适用于实际车身制造工艺。
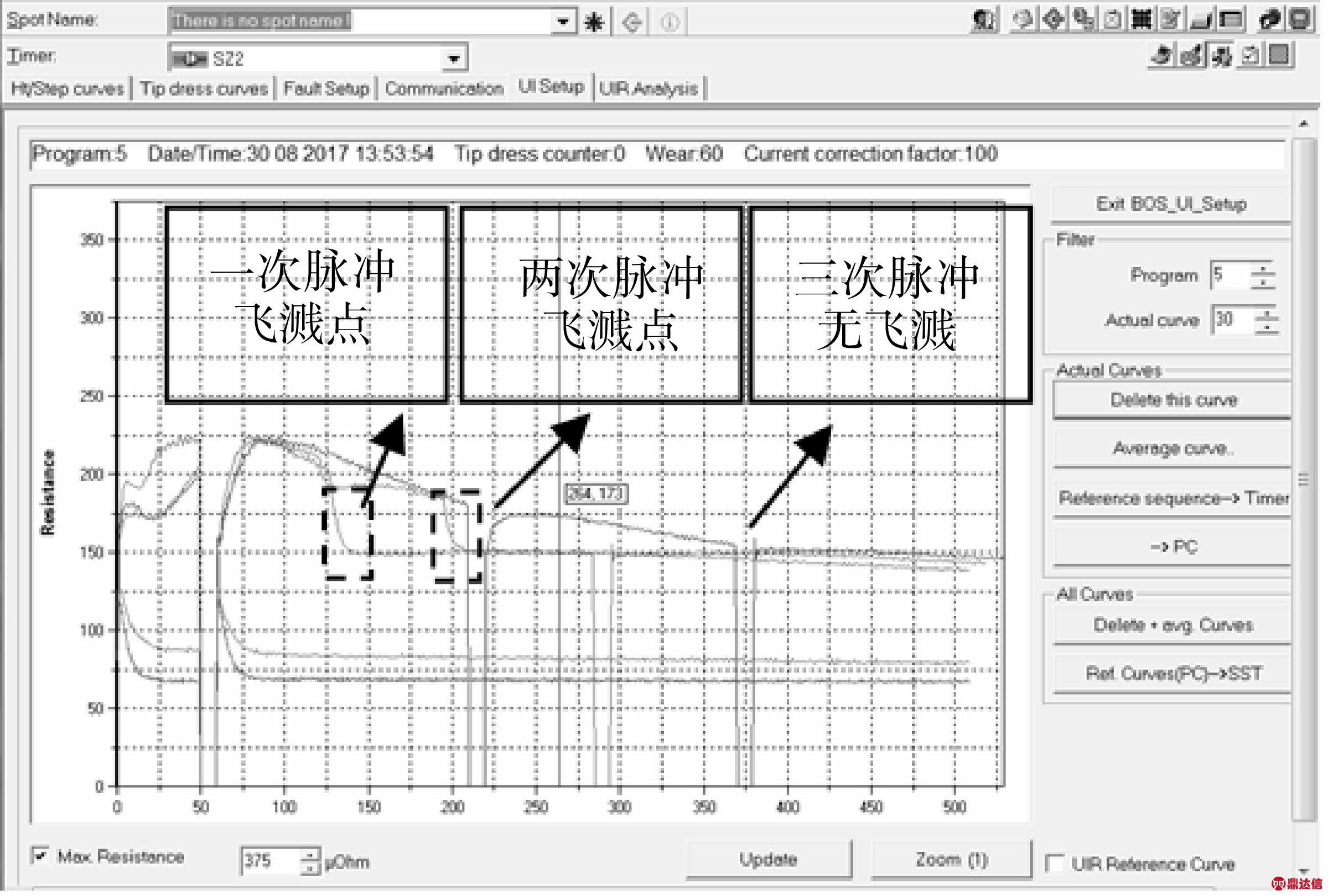
图10 Bos6000电阻随时间变化曲线
(2)包含热成型板的三层板点焊焊核硬度高于镀锌板而低于热成型板,焊核区晶粒组织为粗大马氏体组织。
(3)通过UIR曲线发现,多脉冲点焊工艺能够获得稳定的焊接过程,降低甚至消除多层板点焊飞溅。