摘要:在蓄电池生产中,针对蓄电池盖形状及结构的特点,设计了一款电池盖的自动抓取装置,该装置采用两对齿轮齿条进行相向安装,可以实现同时抓取多个元件或长条形物料的功能。
关键词:机器人;自动抓取;蓄电池;对中;齿轮;齿条;气动;手指机构;电池盖;夹爪;气缸
0 引言
进入本世纪以来,机器人、自动化设备得到了极大的发展,广泛地应用在制造、物流运输、通讯电子等行业。在制造工厂里,这些设备往往用来完成组装、检测、加工、搬运等操作。在传统的蓄电池生产中,机器人也得到了广泛的应用,一般用于组装、包装、上下料等方面,因此与机器人配套的抓取或者吸取机构不断出现。在蓄电池行业的生产中,随着工业机器人的逐步应用,需要设计物料的自动抓取机构。另外根据蓄电池零件的形状为条状或者扁平状的特点,如电池槽、电池盖,可以设计一个专门的装置来进行蓄电池物料零件的抓取。
1 自动抓取装置的设计
1.1 自动抓取装置的工作原理
如图1所示,该自动抓取装置设计了一对相向平行移动的滑块。滑块为长条形,分别为滑块A和滑块B。将两个滑块拼装在滑道内,使其能在滑道内平滑移动,然后在两个滑块上面安装了两对齿条[1],并且在滑道内部安装对应的两个齿轮。滑道内的齿轮要分别与滑块上的齿条相啮合。当滑块A移动时,齿条带动齿轮旋转,而旋转的齿轮则驱动滑块B的齿条,使两个滑块相向移动,从而完成夹紧、松开动作[2]。在滑块的驱动源方面,可以采用气缸[3]驱动夹紧,比起常用的铰链式夹爪,驱动力要可靠些。
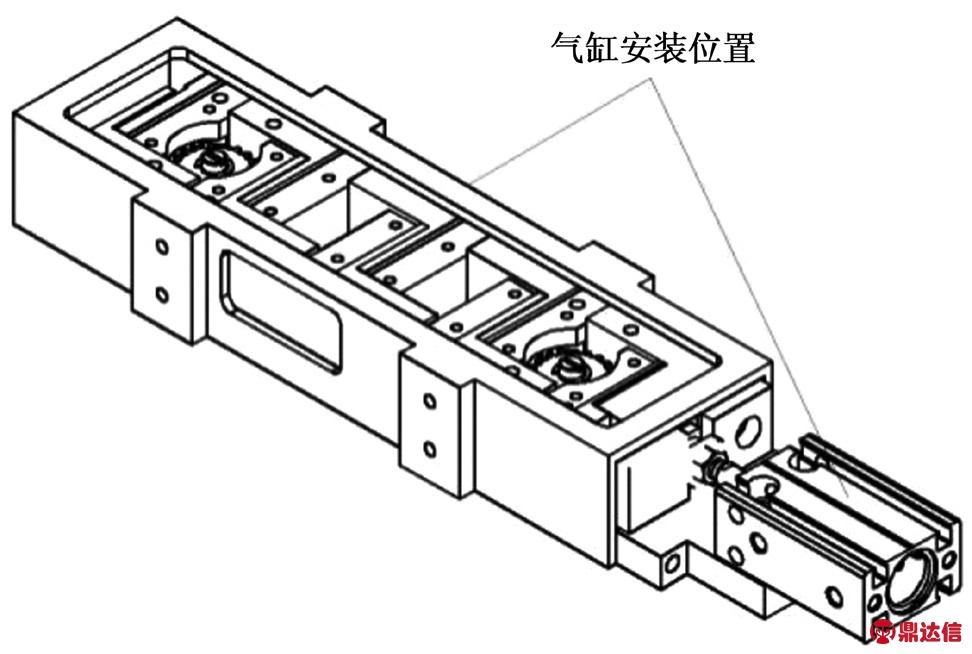
图1 原理示意图
1.2 自动抓取装置的结构
1.2.1 夹爪安装的设计
为了便于适应多个物料的抓取,自动抓取装置还设置有多对夹爪安装孔,这样就可以安装多对夹爪,实现同时抓取多个物料。例如:极板抓取中可以同时安装6~8对夹爪;抓取电极胶帽可以安装2对夹爪[4]。夹爪安装位置如图2所示。另外,如果在每个滑块的相对最远端装1对夹爪,就可以抓取扁长条形的零件,而且对中性好(采用2组精密的齿轮,而且齿条方便调整,以便消除间隙),如抓取蓄电池盖等。
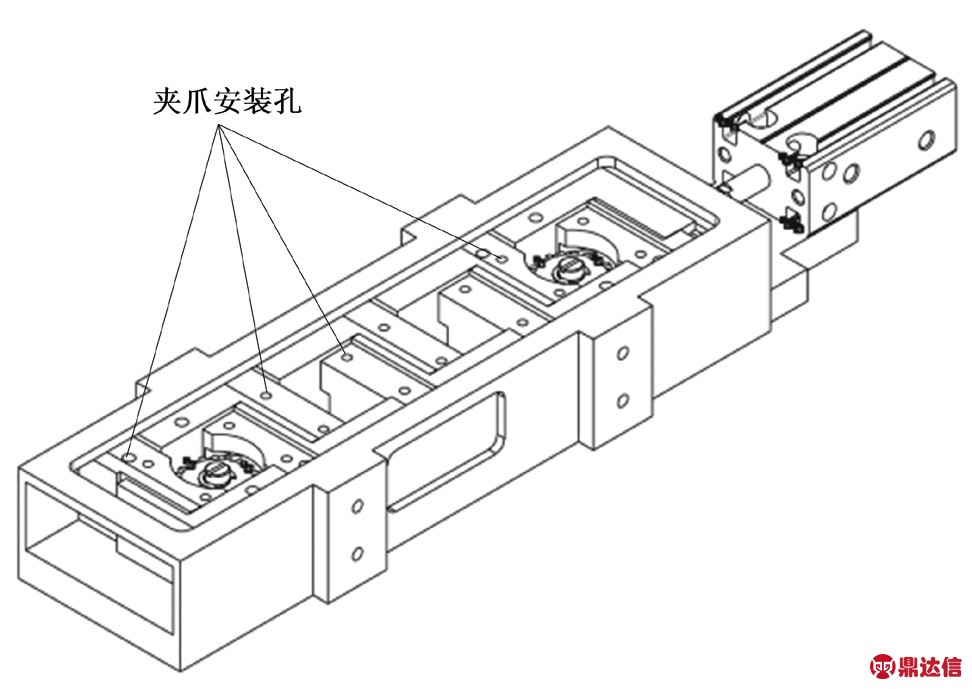
图2 夹爪安装孔示意图
1.2.1 气缸安装的设计
气缸的安装位置有两种,其中一种是沿着移动方向,另一种是在滑道的两侧,如图3所示。滑块上设计有驱动连接块的安装孔,因此可以根据空间需要灵活安装。与其相应的机构也可以安装在滑道的底面和侧面。
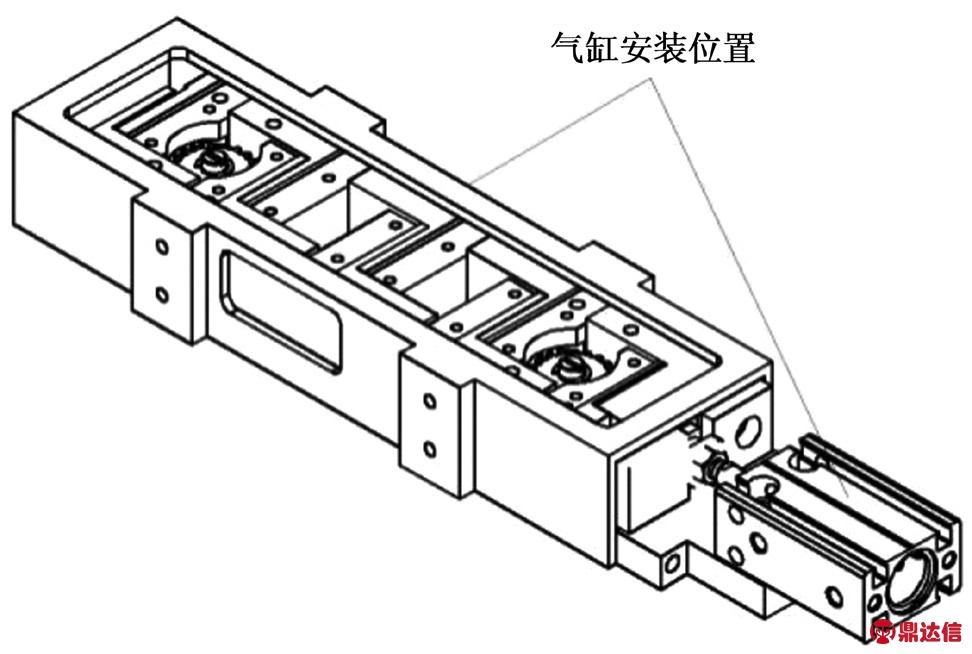
图3 气缸安装位置示意图
1.2.3 组件安装的设计
此外,该自动抓取装置在侧面和背面上设计有组装安装孔,作为“自动盒盖机械手”的整体的1个部件,在该部件安装到整体组件上时,非常方便。其中,组件安装孔位置如图4所示。侧面的安装孔和背面上的安装孔一样可以固定在机械手上,这样该手指在机器上安装灵活。另外,该自动抓取装置结构比较规则,制造工艺相对容易些。比如,滑块为长条形结构,滑道采用腔体式或者组合成腔体式。
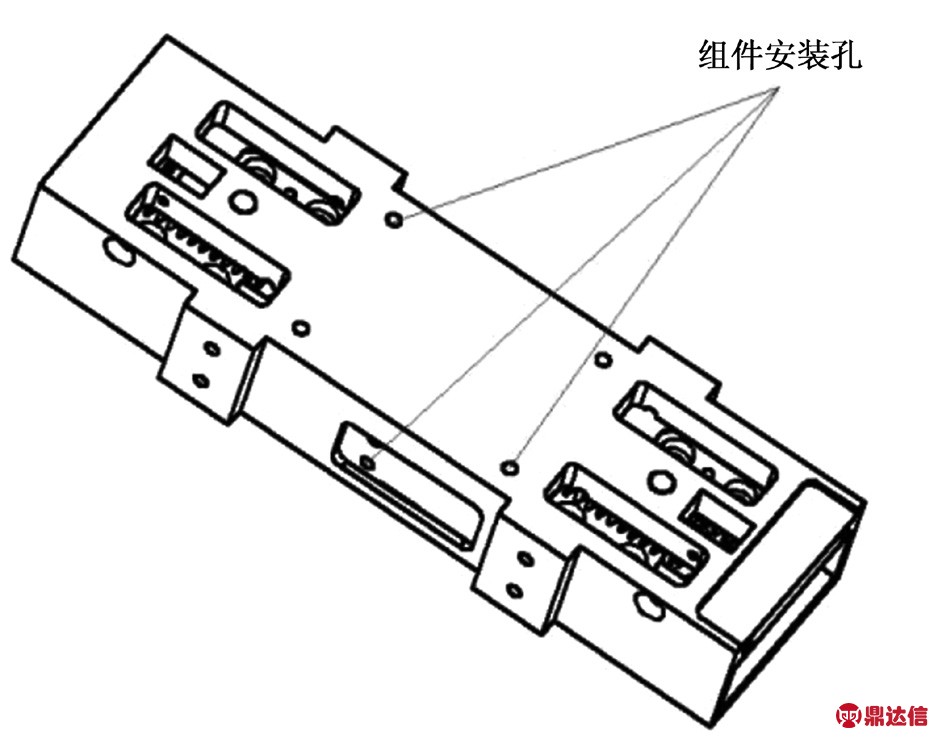
图4 组件安装孔位置示意图
1.2.4 自动抓取装置的装配设计
该自动抓取装置包含有滑道、滑块A、滑块B、驱动连接块、浮动接头、气缸安装底板、精密小齿轮(惰轮)、齿条、惰轮销、旋转衬套、卡簧、气缸等零件[5]。装配如图5所示。该机构中齿条采用模数1.0(最大可到3.0)的精密齿条。齿条材质为耐磨材料,如黄铜,或者合金钢淬火处理。该机构中共用了4条齿条,分成2组,分别安装在滑块a、b上。通过调整每队齿条的位置,可以消除运动间隙。滑块a、b的材料一般选用优质钢材如SKD11,Cr12[6]等,经加工和热处理,然后精磨[7]而成。滑动面可以开润滑脂槽。滑块上有用于安装夹爪的安装孔,而且成对出现。图中机构有4对安装孔,最多可以安装4对夹爪。滑块a、b通过齿条齿轮传动在滑道内作相对或者相向滑动。滑道的材质也是表面硬化处理过的优质钢材,一般在硬度上比滑块的高HRC1至2度。在滑道侧面可开设润滑脂孔(因负载轻图中未开)。其中滑块b通过驱动连接块和浮动接头与气缸轴浮动联接。气缸轴运动实现夹爪松开、夹紧。
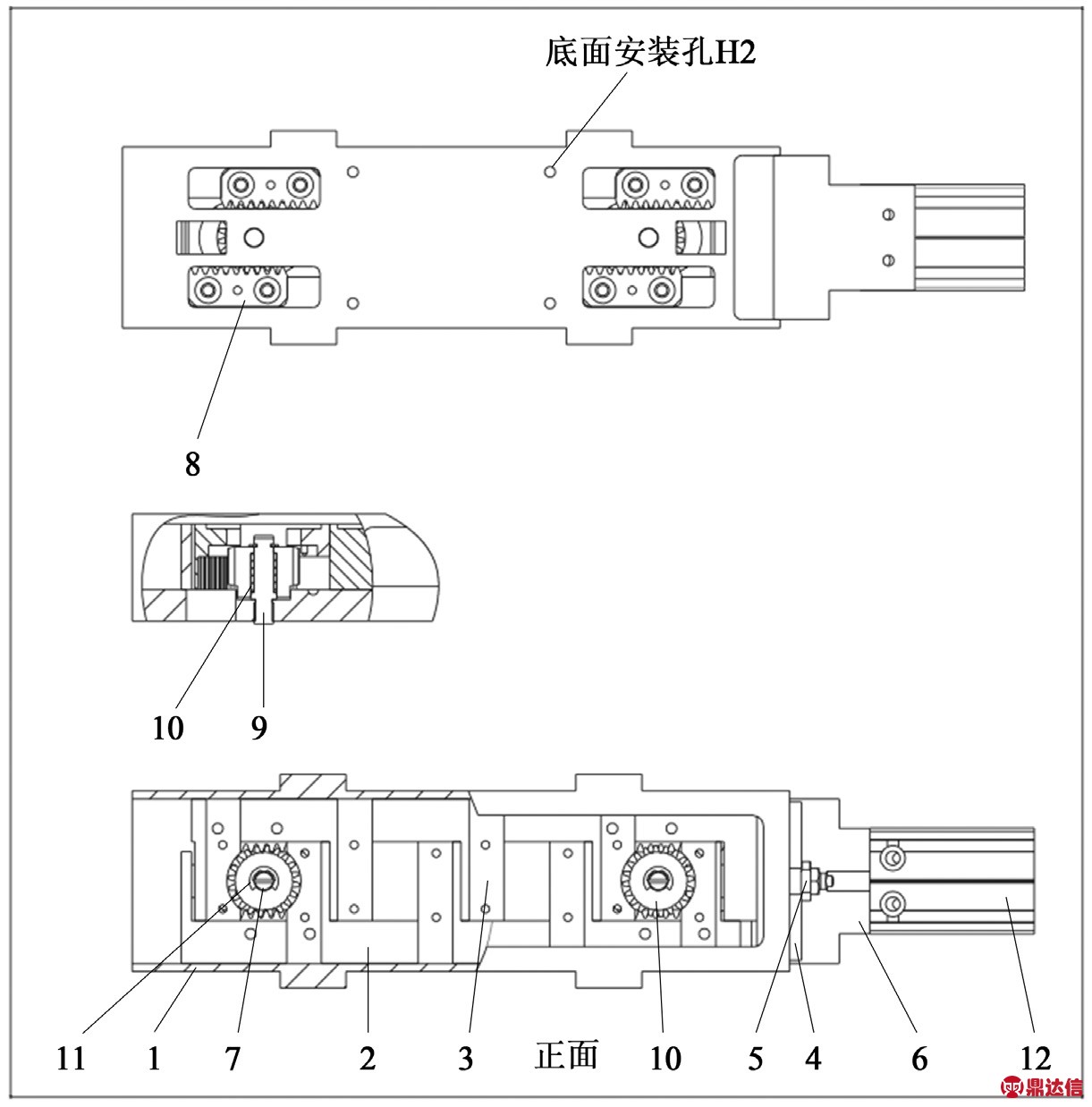
图5 自动抓取装置的装配示意图
1—滑道;2—滑块a;3—滑块b;4—驱动连接块;5—浮动接头;6—气缸安装底板(底面安装式);7—精密小齿轮(惰轮);8—齿条;9—惰轮销;10—旋转衬套;11—卡簧;12—气缸
2 结束语
自动抓取装置采用了两对齿轮齿条进行相向安装,从而带动滑块进行夹紧和松开的动作,并在滑块上设计多对夹爪安装孔,一方面可以实现同时抓取多个零件,另一方面还可以抓取长条状、扁平状的零件,比如蓄电池生产中的箱体抓取、盒盖组装,以及电极帽,极板抓取。采用自抓取装置,与工业机器人配合,实现自动抓取功能,自动精密的定位,自动稳定抓取,为企业节省了人工成本,提高了企业的生产效率。