摘 要:针对目前变压器铁芯手工叠装生产效率低下、质量参差不齐的问题,设计了一套硅钢片自动叠片装置进行铁芯的生产。该装置选用可移动的基座、采用圆柱坐标系的运动模式、步进电机带动同步带和丝杠直线滑台的驱动方式、吸盘真空吸取的抓取方式,利用工控计算机结合运动控制卡的方式对叠片过程进行控制。并提出了检测叠片效果的方式和多型号开发的模式,能够带来良好的社会效益和经济效益。
关键词:变压器 自动叠片 取件机械手 料仓布置 安全保障系统
0 引言
变压器行业是一个传统的行业[1],变压器铁芯作为变压器的核心部分,它的质量直接影响到变压器的技术性能、经济指标和运行的安全可靠,因此,它的制造技术改良和质量控制十分重要。由于变压器铁芯叠装制造工艺的特殊性,现有的铁芯制造几乎都采用手工叠装硅钢片的方式生产。以一台10kV小型变压器为例,铁芯叠片工序由两人操作,操作工在叠片过程中, 均靠经验和肉眼观察来保持叠装精度,生产效率低下,产品质量参差不齐[2]。人工铁芯叠装的弊端在自动化生产飞速发展的今天逐步显现,成为制约变压器产业发展的障碍[3]。同时,国内外也没有专门针对变压器铁芯叠装的设备,只有加拿大MTM公司有类似设备,但不是完整的自动叠片机器人。
针对上述问题,本研究设计出一套以步进电机作为动力驱动,采用嵌入式单片机控制,利用自动取件器械手进行变压器铁芯叠装的自动叠片装置(以下简称叠片装置),并对其进行结构优化,经过一系列振动测试与试验,验证所设计的装置能够达到实际生产的精度要求。
1 叠片装置整体设计
叠片装置的设计思路是通过吸取—位移—放置等功能,在不损伤硅钢片的情况下,实现将不同规格的硅钢片快速而准确地放置在指定位置上,从而高效地完成铁芯的装叠。
本叠片机主要包括取件机械手、硅钢片料仓夹具、堆叠工装座及传送滚筒、机架、控制系统及控制柜几大部分。除电控柜外的整体装置的三维模型(图1),制作实物(图2)。叠片装置的中央位置为堆叠工装座,用于固定待堆叠的铁芯。堆叠工装座固定在可随滚筒移动的平台上,传送滚筒将堆叠完毕的铁芯传送出中心位置。铁芯两侧布置有两个取件机械手,用于吸取、堆叠硅钢片。取件机械手固定在可平移旋转的基座上,由气缸推动,共四个工位。取件机械手的四周放置不同的料仓,料仓夹具用于存放待吸取的硅钢片。所有电器控制系统布置在控制柜内,并安装有工控计算机用于操作工人操作。
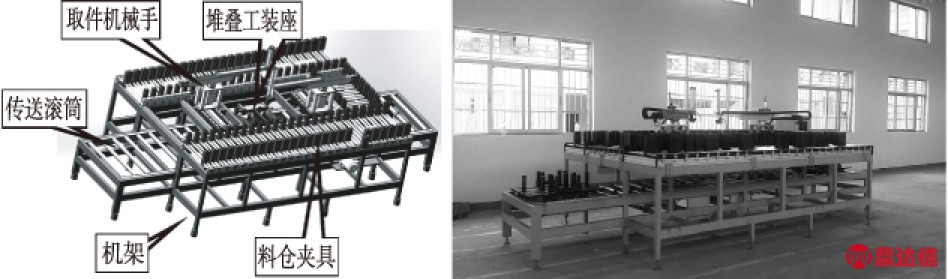
图1 叠片装置整体结构三维示意图 图2 叠片装置整体结构实物图
叠片装置整体工作流程图如图3所示。开启电源后,按照要求放入部件和堆叠工装板,操作工人向料仓加入相应的硅钢片,启动机器,取件机械手回原点,输送链滚筒把堆叠工装座送入中央的堆叠工位,升降机把堆叠工装座举升到位,机械手按照预先设定好的程序顺序堆叠硅钢片,一个产品堆叠完成,机械手回原点停止工作,升降机返回,输送滚筒送出已完成的产品,并把新的堆叠工装座送入中央的堆叠工位。以此循环,直到人工停机。
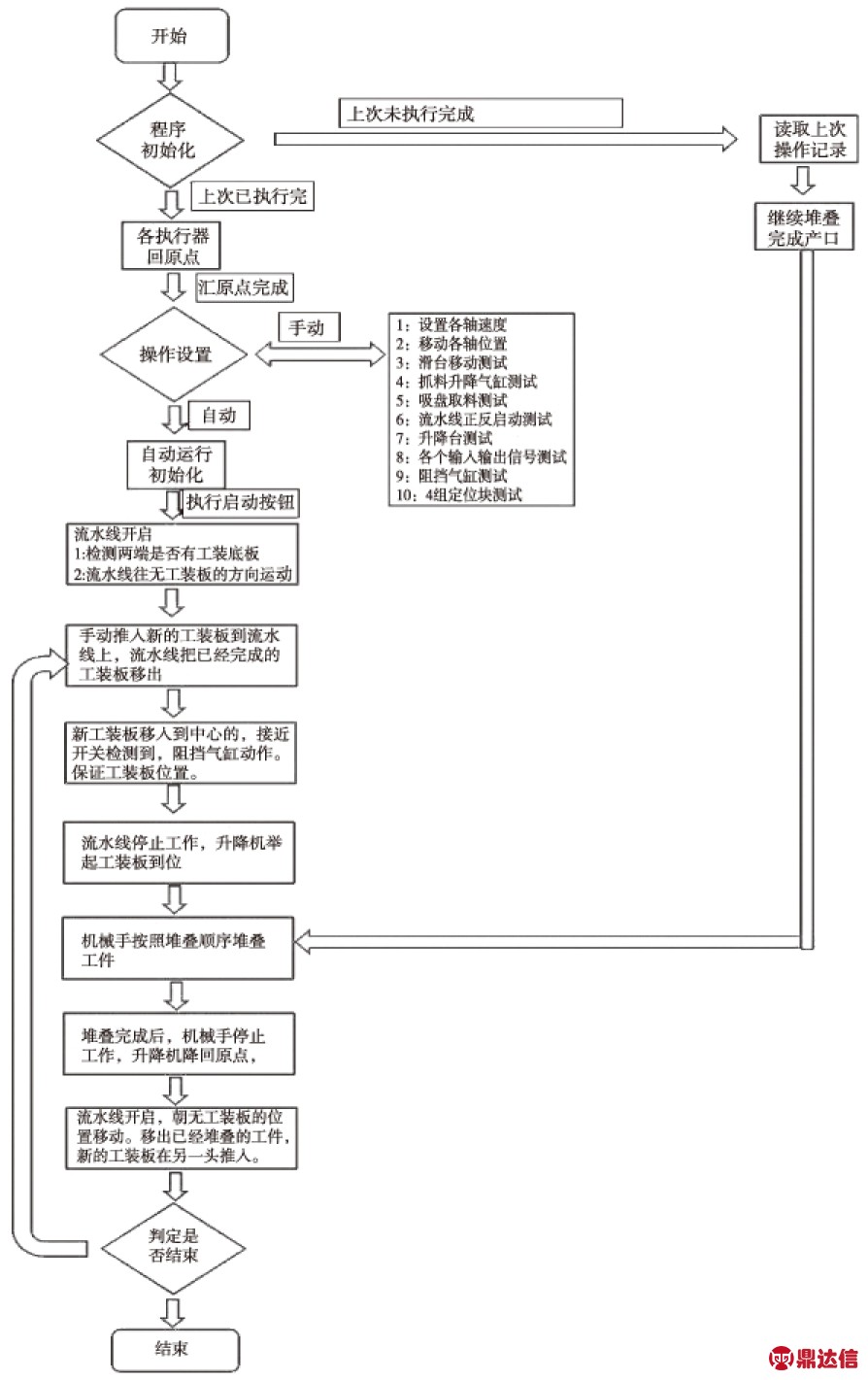
图3 叠片装置叠片工作流程图
下面将分别就取件机械手、运动构件设计、硅钢片料仓布置方式、运动控制系统和安全保障系统四部分对叠片装置进行详细介绍。
2 取件机械手及运动构件设计
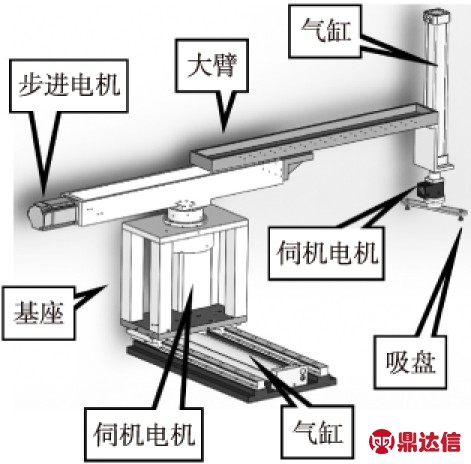
图4 取件机械手的结构示意图
取件机械手的结构示意图如图4所示。取件机械手布置在铁芯的两侧,共4个工位。机械手基座本身可以旋转,由伺服电机驱动;基座还可在导轨上实现平移,由气缸驱动;机械大臂可以伸长缩短,由步进电机及丝杠驱动;吸盘轴可以上升下降,由气缸驱动;吸盘轴可以旋转,由伺服电机驱动。
作为整个叠片装置的核心部分,取件机械手设计及其运动必须保证较高的运动速度,同时运动的偏差和硅钢片的放置精度也要保证。因此为保证平稳性和高效率,设计主要从取件机械手的运动模式、动力驱动方式以及取件方式着手。
1)运动模式
运动模式主要有直角坐标、圆柱坐标、极坐标与关节式。结合变压器铁芯硅钢片料仓的摆放位置、利用机械手进行叠片的整体布局与机械手的功能要求,圆柱坐标机械手的构造简单,定位精度也比较高。
2)动力驱动方式
对于不同位置动力驱动的需求,应采取不同的驱动模式方式,以求在做到保证精度的同时尽可能提高运行速度并减少成本。对于机械臂两点式的运动,采用气缸驱动的方式;对于机械臂的旋转运动,采用伺服电机驱动旋转的方式;对于机械手的伸长和缩短,采用步进电机配合丝杠的方式进行运动。
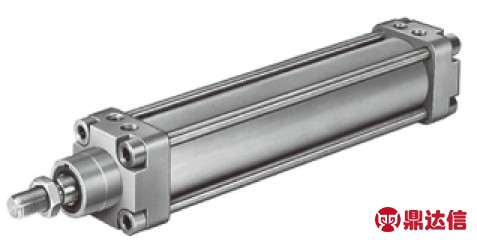
图5 气缸结构示意图
两点式的运动,除了两个目标点外,没有中间点位置,因此采用气缸驱动。一方面气缸驱动产生的动力较大,另一方面在满足精度的同时成本较低,易于控制。仅采用开关量控制,使相应部件仅能停留在两个特定的位置。如图5所示。
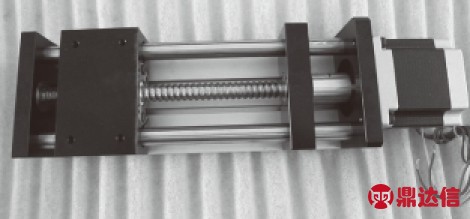
图6 步进电机及丝杠
对于长度方向上的运动,即机械手的伸长缩短,采用步进电机配合丝杠的方式。步进电机可以实现开环控制,即通过驱动器信号输入端输入的脉冲数量和频率实现步进电机的角度和速度控制,无需反馈信号,适用于短距离频繁动作。具有速度快(10~600 mm/s),精度高(±0.5 mm),控制简单,成本低等特点,各项指标均适合本自动叠片机的工作需要,如图6所示[4]。而丝杠具有摩擦阻力小、传动效率高、运动平稳、反应迅速等优点,满足叠片工艺在精度上的要求[5-6]。
对于机械臂的旋转运动,采用伺服电机驱动。伺服电机可使控制速度,位置精度非常准确,可以将电压信号转化为转矩和转速以驱动控制对象。伺服电机转子转速受输入信号控制,并能快速反应,在自动控制系统中,用作执行元件,且具有机电时间常数小、线性度高、始动电压等特性,可把所收到的电信号转换成电动机轴上的角位移或角速度输出。
3)取件方式
气缸—活塞杆运动机构实现了机械手z方向上的运动,再利用吸取机构和电感式接近开关通过真空吸取式取件。硅钢片由于其表面光滑平整,质量较小且分步均匀,采用真空吸取式的抓取方式可有效保证抓取的可靠性和准确性,力度可控,还可保护硅钢片外表面绝缘层,防止被破坏。如图7所示。
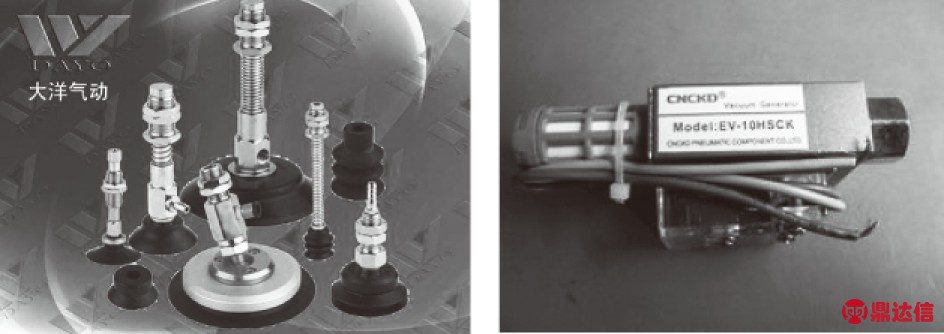
图7 真空吸盘及发生器
吸取机构由真空吸盘、抽气管和真空发生器组成。当电磁阀打开时,压缩空气就会进入真空发生器的喷管,通过喷管高速喷射压缩空气在喷管出口处形成射流,从而产生卷吸流动,进而使吸附腔内的压力低于大气压,形成一定真空度[7],于是吸盘便可以以真空吸取的方式抓取硅钢片。
电感式接近开关的工作原理是当金属物体靠近振荡器的交变磁场时,振荡将发生衰减甚至停振,这一变化被放大电路处理后成为开关信号,用以驱动逻辑电路[8],从而实现非接触式检测。电感式接近开关响应频率高,抗干扰性能好,广泛用于工业控制中[9]。当吸盘与硅钢片刚接触时产生的电信号将作为运动控制系统的输入参数,用来控制吸盘抽气阀门的开启。
3 硅钢片料仓布置方式
硅钢片料仓的布置将会影响到机械手的取件的效率,对整个生产过程有很大的影响。因此,必须对料仓的布置进行合理的排列,使得整体取件和移动的时间最小,生产效率最高。
为保证生产效率并防止两个机械手互相干涉,以一个取件的同时另一个叠放的方式循环。不同硅钢片料仓位置的设定以数量较多的片型放置在离机械手取料距离较近的位置(就近原则)为准则。以型号为S11-M-250/10的铁芯为例,该铁芯共8级,第1级轭端厚度为188 mm,而第8级厚度仅为16 mm,因此第1级硅钢片放置在距中央堆叠工位最近的料仓,而第8级硅钢片则放置在距中央堆叠工位较远的位置。其料仓布置如图8所示。
当检测到某一料仓硅钢片储量低于下限值时,系统将自动发出警报,提示操作工人加料,机械手自动暂停取片。待加料完成后,操作工人重新启动机械手,叠片生产继续进行。
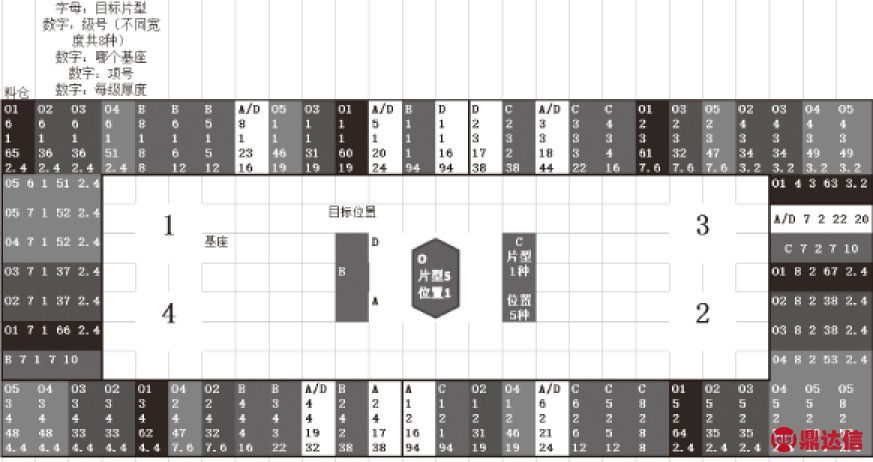
图8 S11-M-250/10硅钢片料仓布置示意图
为保证叠装精度以及取料的可靠性和准确性,采用模具夹具定位与传感器定位相结合的方式,以保证定位的效果。
叠装前,利用专用夹具即特制的料仓来确定放置硅钢片的初始位置,这些特制的料仓可调整形状以适应不同料号的硅钢片。叠装时,采用相应的传感器来监测机械手是否运动到了正确的叠放位置,并将监测结果反馈给单片机控制系统,再由控制系统发出下一步运动的指令给机械手,以保证硅钢片的叠装精度。图9为特殊设计的可调料仓。
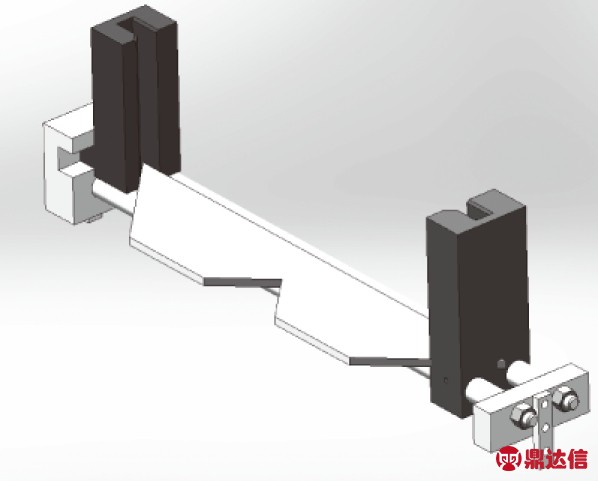
图9 可调料仓示意图
4 运动控制系统
运动控制系统是整个叠片装置的大脑,它控制整个机器人的运动,包括基座的移动,机械手的伸缩和抓取,并对反馈的数据作出逻辑判断。同时必须具备运算能力强大,操作步骤简单,用户界面友好等特点。依据上诉要求,该叠片装置的运动控制系统采用工控计算机结合运动控制卡的方式(PC-base)。
工控计算机采用window操作系统,带有可触控的液晶显示屏。此外,该操作系统内还带有用C++语言编写的可执行文件(.exe),作为计算机控制程序,通用性强,操作工人学习成本低,使用方便。工控计算机控制界面如图10所示。
运动控制卡通过改变发出脉冲的频率来控制电机的运行速度,通过改变发出脉冲的数量来控制电机的运行位置,它的脉冲输出模式包括脉冲/方向、脉冲/脉冲两种方式。一种以太网8轴运动控制卡如图11所示。
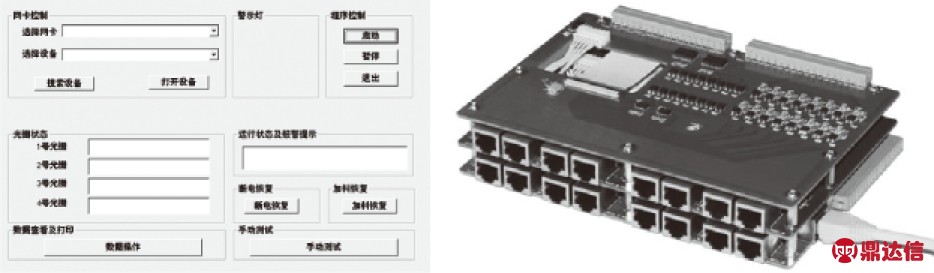
图10 工控计算机控制界面 图11 以太网8轴运动控制卡
5 安全保障系统
叠片装置生产依靠机械手自动吸取叠放硅钢片实现,但机械手的高速移动可能会伤到未按照操作规范而靠近的操作工人,因此必须有相应的安全措施来保障操作工人的人身安全。
在叠片装置的四周设立安全光栅,若有物体或人体进入光栅范围并被检测到,则自动叠片机就会立即停止工作,机械手运动构件立即锁死,并发出警报,保证不会伤到靠近的人员或触及靠近的物体。只有将报警消除,并解锁机械手运动部件,才能再次进行生产。双重安全保障系统可以有效防止人员伤亡和机器损坏,也能防止因不规范操作直接消除报警可能带来的安全隐患。安全光栅如图12所示,其布置形式如图13所示。
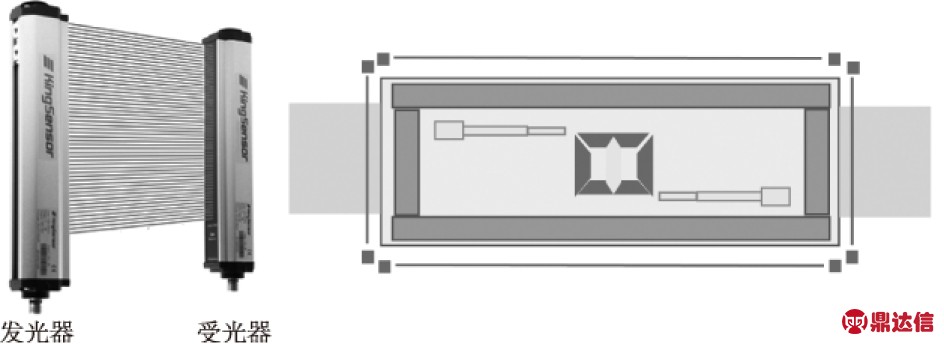
图12 安全光栅 图13 安全光栅的布置形式
6 自动叠片机试验
在专门的实验室内对叠片装置进行组装试验。通过购买材料组装样机,同时对运动过程分析处理,按照相应标准进行系列试验,获取试验数据以对样机结构进行初步评价和进一步修改和优化。
6.1 可靠性试验
对已组装好的样机进行工作测试。使其进行24小时不间断的连续工作,测试其工作的稳定性,不同部件之间的相互干涉情况以及测试机械手与料仓之间的匹配联系关系,并记录相关数据,以便于后续进行大数据分析,作为初步评价的依据,并找出初始设计的不足,为进一步修改和优化做准备。
6.2 生产精度试验
在样机进行不间断工作后,用相应的测量工具对叠好的变压器铁芯进行测量。测量不同位置,不同角度的叠装误差,利用统计和大数据的方法求出叠片装置的平均生产精度,叠片的方差、最值,以评判叠片装置的叠装效果,为后续的改进优化提供源数据支持。
7 总结
本文从改变变压器铁芯手动叠装这一现状出发,设计了一套高效的硅钢片铁芯自动叠片装置。
叠片装置采用圆柱坐标系的运动模式、伺服电机、步进电机与气缸配合的动力驱动方式和真空吸取式的取件方式,配套相关料仓、运动控制系统和安全保障系统,使得该叠片装置具备了实际生产能力,能够在保证叠装精度的同时提高生产效率。在样机组装完成后,按照相应标准进行可靠性和生产精度试验。对叠片装置的研究提升了我国相关行业的技术水平和竞争力,也带来良好的社会效益。但存在的一些不足还有待进一步改进和完善。