摘 要:分析了汽车悬架球铰总成动态试验台的技术特点,阐述了其控制原理和研究路线.
关键词:汽车球铰;动态多向加载;试验台
汽车悬架球铰总成是对汽车悬架和转向机构起重要连接作用的零部件,其可靠性直接影响汽车行驶的操控性、乘坐舒适性及行使安全.因此针对球铰总成的室内台架试验在产品设计、产品质量保证体系中是非常重要的.
从实际的使用情况看,汽车悬架、转向球铰总成承受的载荷是由多方向脉动拉压、旋转、发热效应共同作用产生的复合载荷.因此设计试验台的目的是要近似模拟球铰的实际载荷工况进行二维动态试验,以使试验效果能更真实反映球铰的使用情况.
1 试验台技术特点分析
1.1 球铰的载荷分析
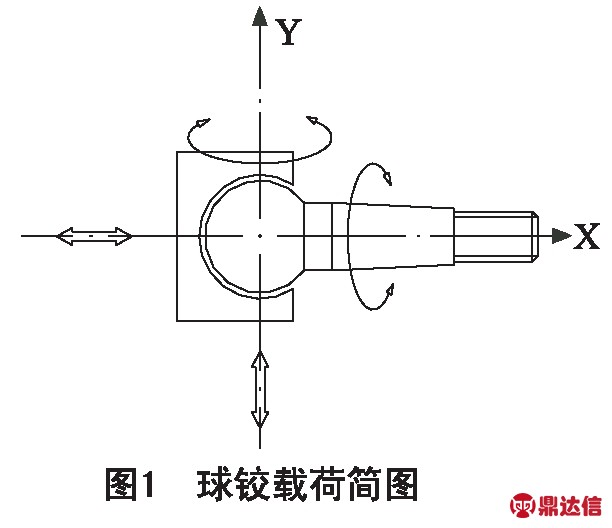
球铰在实际使用中承受的是多方向、旋转的复合载荷,情况非常复杂.通过对其载荷性质的分析,将各向载荷和旋转作用分解合成,对球铰的性能和可靠性造成影响的主要有:
a.沿轴向(X轴)、径向(Y轴)的脉动拉压作用;
b.绕X轴、Y轴的转动作用.如图1所示.
1.2 球铰试验台技术特点分析
通过对球铰的载荷分析以及各标准中球铰试验方法的研究可以看出,要完成球铰试验,试验台必须具备以下的技术特点.
a.试验台应能同时对球铰施加各项载荷,且各项载荷大小、方向、作用频率是不同的.
b.球铰试验中还要求监控球铰的球碗温度,其目的是确定试验中润滑脂是否在有效温度范围内工作.
c.各项载荷的加载机构要求能独立控制、调整.
d.根据球铰疲劳试验中载荷控制精度要求高、试验时间长以及试验样品多样性的特点,试验参数要允许根据不同的实验需要进行调整,因此试验台应由电控系统自动控制完成,并且通过电控系统应可修改调整试验参数,并能够自动存储、打印输出试验结果.
2 控制、测量技术研究
2.1 试验台总体控制形式
试验台的试验控制采用计算机控制系统,其控制软件及操作界面基于WINDOWS2003操作系统.试验人员在计算机上输入试验控制参数.开始试验后,计算机系统即自动控制试验台,实现全试验过程的自动化控制,其目的是为了提高试验过程中加载工况的稳定性和加载精度,同时大大减轻了试验人员的劳动强度.在计算机控制系统中主要研究解决的是力加载控制的精度和稳定性问题.
2.2 试验台力控制技术研究
2.2.1 力加载控制特性分析
从试验的加载特性看,在整个试验过程中控制系统需要控制油缸的加载动作,使之对球铰施加按一定波形、频率变化的载荷.而加载力的产生是油缸和球铰作用与反作用生成的,力的变化除了受油缸动作控制影响外,也和球铰、加载杆系统的反作用有关,因此影响力的变化的因素是瞬时多变的,这会造成在试验过程中任意瞬时力的不稳定性.
要在长时间的试验过程中,保持波形、频率、力值稳定的载荷工况,控制系统需要对油缸进行力反馈闭环控制,即对加载力随时进行修正才能够实现.
2.2.2 力反馈闭环控制原理
参见图2中轴向力闭环控制和径向力闭环控制的控制回路.
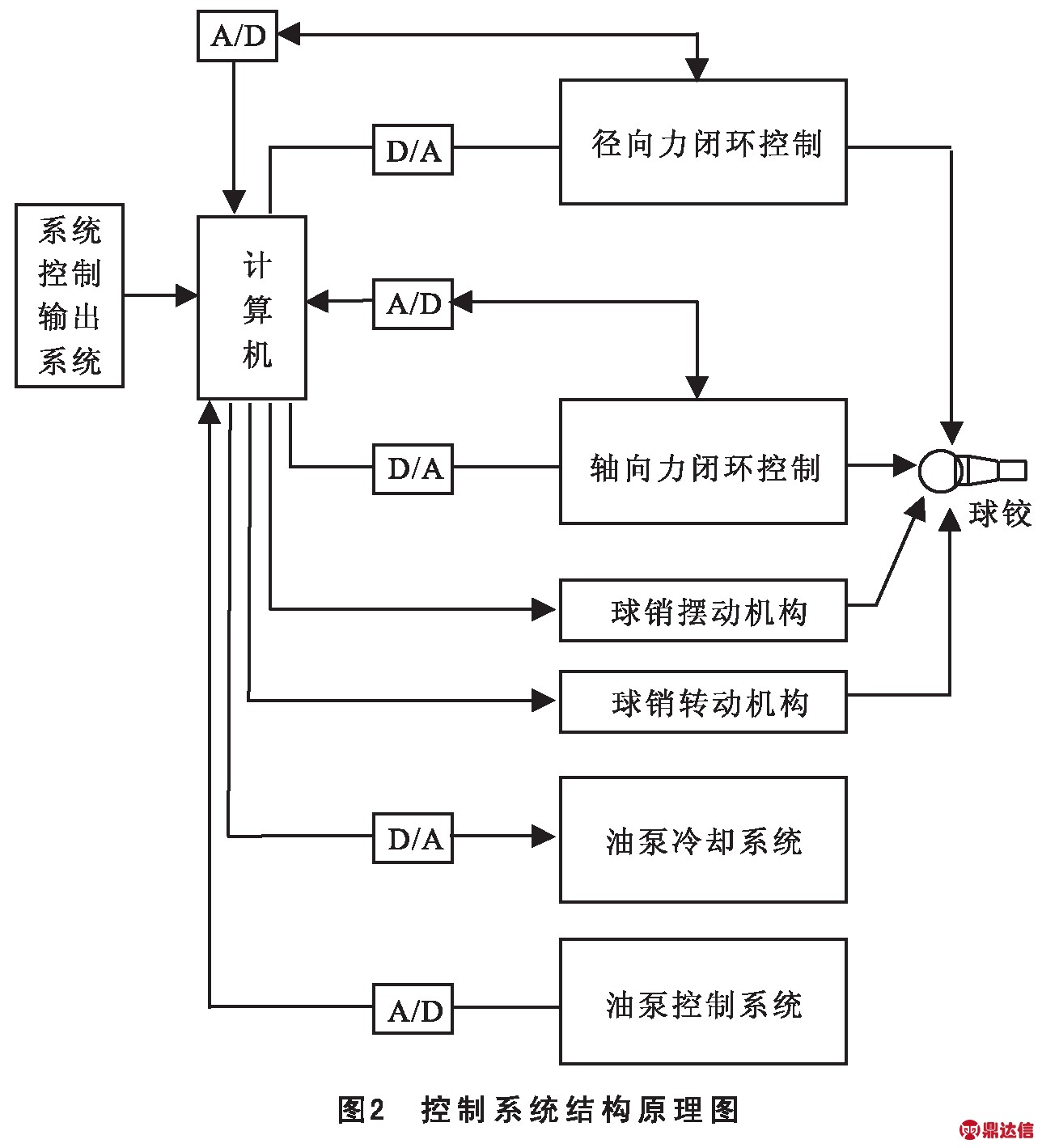
试验中计算机连续向伺服控制器发出按一定波形、频率周期变化的力加载指令信号,伺服控制按照该指令信号经伺服放大器放大驱动伺服阀工作,进而控制油缸动作,对球铰施加力载荷,该力载荷值由拉压力传感器测量.
在加载过程中,伺服控制器实时采集力传感器测得的力值,并和指令信号进行比较,当采集到的实际的加载力信号和指令信号有偏差时,伺服控制器将自动对指令信号进行修正,再经伺服放大器放大驱动伺服阀控制油缸,修正油缸的加载动作,从而使实际的加载力和试验设定的加载力一致.这一控制过程在整个试验过程中是不间断连续循环进行的,即为“力反馈闭环控制”.
3 试验台实际应用测试
对某车型(进口车国产化)的前悬下摆臂球接头总成按照产品技术要求应进行如下试验:
轴向加载 3000±5500kN 频率8Hz;
径向加载 1100±5500kN 频率8Hz;
球销转动角度 ±45° 频率1.0Hz;
球销摆动角度 ±15° 频率1.0Hz;
试验次数 100万次(按加载频率计算).
本试验台能够按上述要求进行实验.通过对CKD件及本公司产品的对比实验,公司验证设计了一种新型球接头总成,该产品通过主机厂的道路试验和技术认可,并获得了国家新型实用专利.
对通过上述台架试验的新产品进行道路试验及换装跟踪,其产品三包索赔大幅下降,降幅达90%以上,为公司开发新产品提供了有效的验证手段,降低了开发周期和开发成本,取得了明显的经济效益和社会效益.