摘要:通过理论分析与三维数值模拟研究了实际运行工况下单钩波形板分离器内二次携带机理。采用Realizable k-ε湍流模型对波形板内气相流场进行数值模拟,利用离散相模型结合涡交互模型对水滴运动进行计算,根据壁面水膜运动方程求解水膜的速度与厚度分布;依据理论分析,对可能形成二次水滴的4种方式进行判定。结果表明:波形板内发生气体动力造成的水滴破碎与水滴撞击水膜产生飞溅的可能性较低,但较冷态工况的可能性高;水膜主要集中在波形板的前两级,随入口蒸汽速度或湿度的增加,水膜增厚并向下游移动;将水膜剥落和水膜分离的判别式进行统一,并证实波形板二次携带主要由水膜的剥落和分离造成,且相较水膜剥落,钩峰处的水膜分离更易发生。
关键词:波形板分离器;二次携带;水滴;水膜分离;水膜剥落
波形板分离器能高效地分离出气(汽)流中的水滴,在核电蒸汽发生器内汽水分离[1]和油气分离[2]等工程中起着重要作用。在波形板分离器中,汽流沿着Z形通道流动,具有较高惯性的水滴难以及时随汽流变向而撞击板壁,并在壁面积聚,当水量较大时,将在壁面形成水膜,最后在重力驱动下流出[3]。
当汽流速度超过临界破膜速度时,随汽流速度的增加,汽水分离效率反而急剧下降,其主要原因即是二次携带[4],因此明确二次携带的机理就成为进一步提高波形板分离性能的关键。单钩波形板作为波形板分离器的一种,其临界破膜速度较高,获得广泛应用和关注。然而,近年来学者对波形板的研究多集中于分离性能和结构优化[5-7],且以二维冷态工况下计算分析为主,较少考虑实际运行条件下二次携带的影响;虽有部分学者对波形板分离器内冷态工况下水膜流动和破裂现象进行理论和试验研究[8-9],但在理论和结构上均存在较多简化。
目前CFD技术在波形板性能预测和流动分析方面具有诸多优势,而且由于水膜流动方向与汽流流动方向相垂直,加之水滴运动使得流场具有强烈的三维三相特征。因此,本文采用三维多相数值模拟研究单钩波形板分离器内二次携带机理。
1 二次携带机理
二次携带通常由二次水滴造成。通过对水滴和水膜运动进行分析,本文认为波形板内二次水滴的来源至少有4种(图1):1) 气体动力造成水滴破碎;2) 水滴撞击水膜产生飞溅;3) 汽流剪切造成水膜剥落;4) 水膜在转角产生分离。文献[1,5]均只考虑了1~3种情况,文献[1]认为第2种情况是产生二次细小水滴的主要因素,而文献[5]认为二次水滴主要来自第2、3种情况。实际上,水膜在转角的分离对二次水滴产生有着重要影响[10]。这4种情况耦合在一起,相互影响,如水滴碰撞水膜产生冠状波将增强水膜表面不稳定性,进而促进水膜剥落,但为简化起见,本文分别进行讨论。
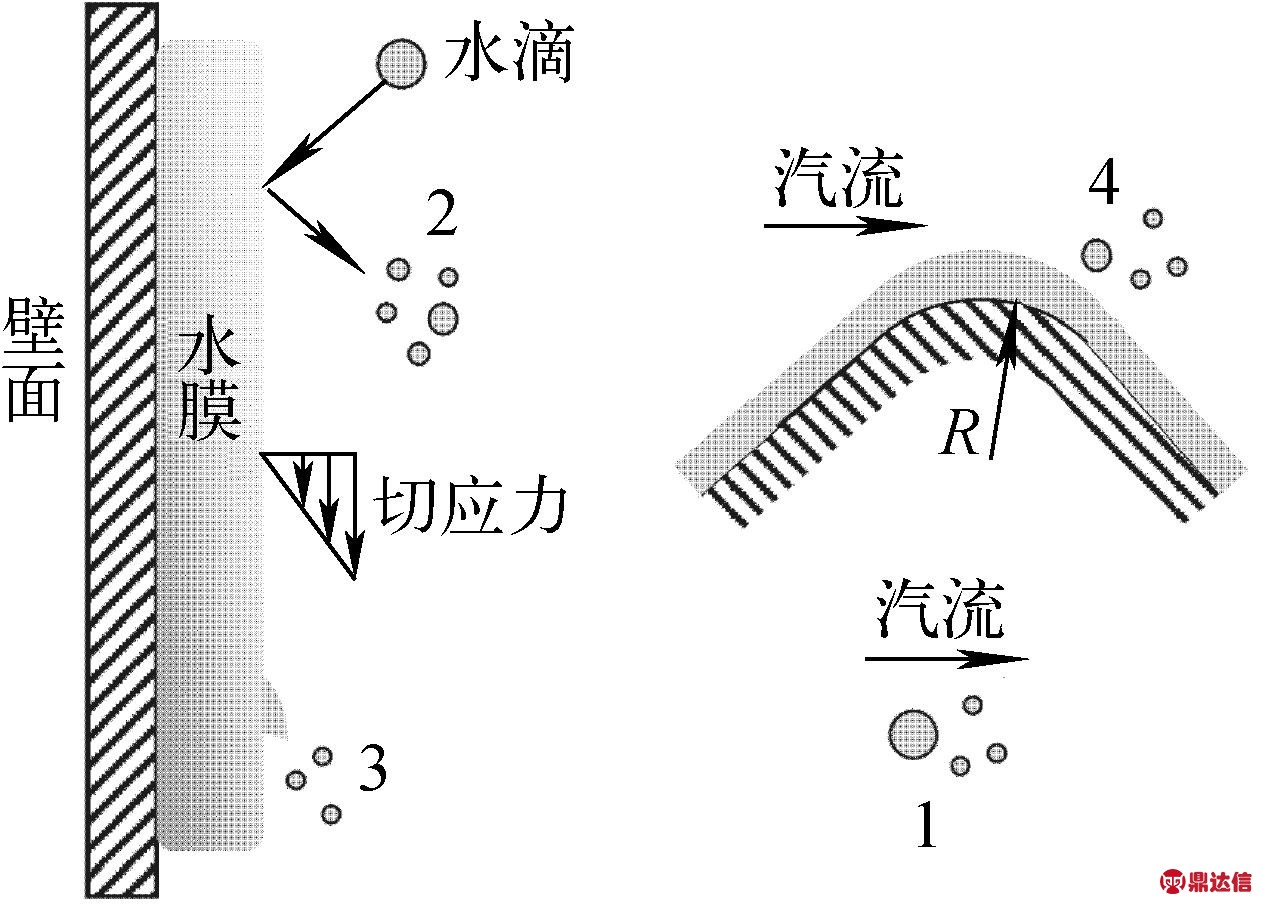
图1 二次水滴产生机理
Fig.1 Formation mechanism of secondary droplet
对于第1种情况,气体动力造成的水滴破碎可根据水滴Weber数Wed[1]判断:

(1)
式中:ρs为蒸汽密度,kg/m3;us和uw分别为蒸汽和水滴速度,m/s;σ为水滴表面张力,N/m;Dw为水滴直径,m。当Wed>13时,汽流中的水滴将破碎。
对于第2种情况,水滴与水膜碰撞过程可产生4种结果[11]:粘附、反弹、铺展和飞溅,所需水滴能量依次升高,判断准则[11]为:粘附,Wew<5;反弹,5<Wew<10;铺展,10<Wew<C;飞溅,C<Wew。其中:水滴Weber数,ρw为水的密度(kg/m3);
f3/4,单个水滴撞击频率f=uwn/Dw,uwn为水滴碰壁法向速度(m/s),μw为水的动力黏度(N·s/m2)。
粘附和铺展是水膜的成因,仅当飞溅发生时才有二次水滴产生,即需Wew/C>1。对Wew/C进行变换并假设uwn=uw得到:
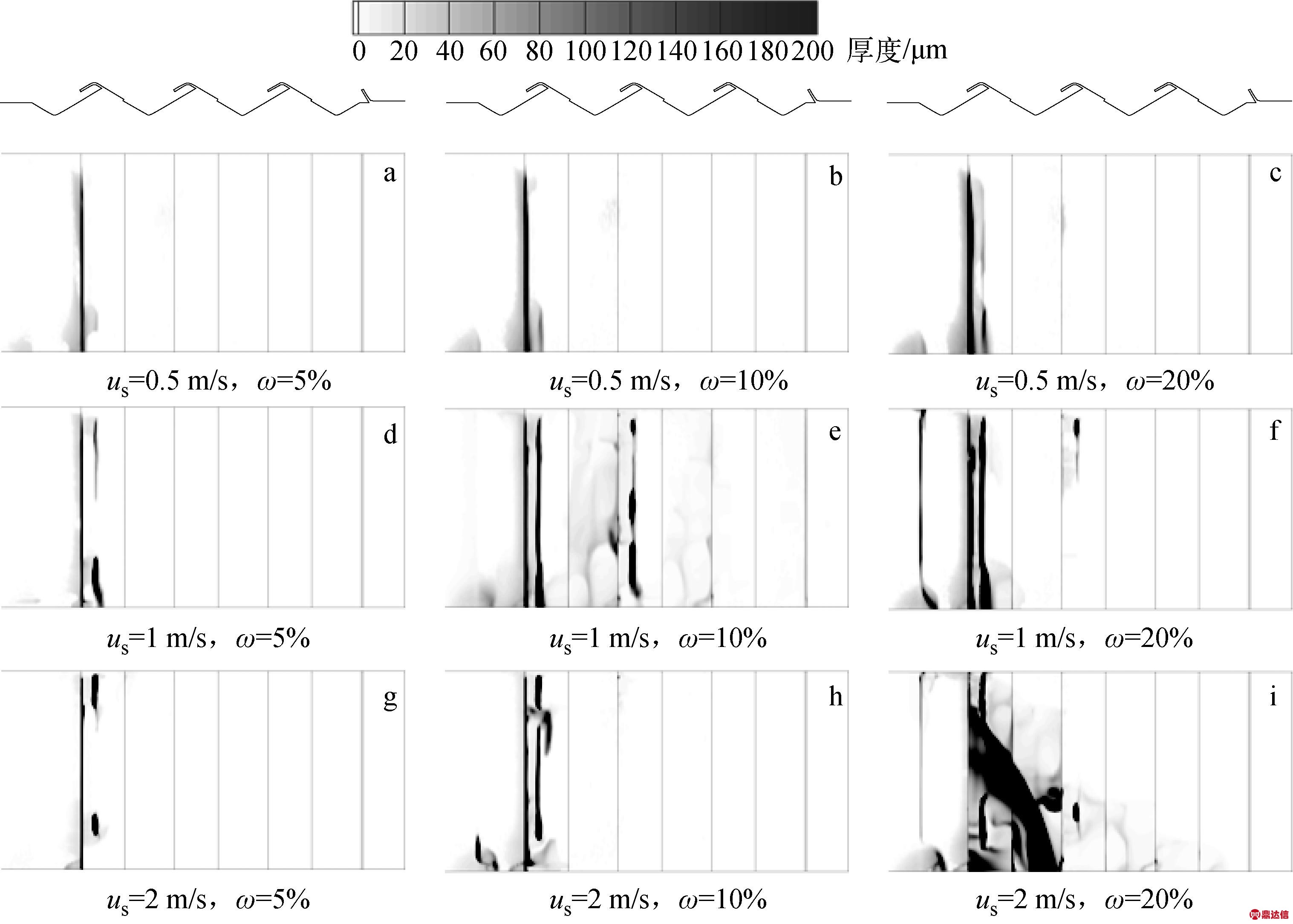

(2)
从表2可以看出,机载合成孔径雷达常规聚束工作模式针对远近不同的作用距离对雷达的分辨率及成像带宽要求相同,对于定点聚束方式而言,其方位向测绘带宽Ls=R·θ,与作用距离有关系,作用距离越近方位向测绘带宽越小,通常在最小作用距离要求处无法满足方位向测绘带宽的要求,即为解决上述问题通常在工程设计时采用定点聚束与滑动聚束相结合的聚束SAR工作方式,在远距满足方位测绘带宽的情况下使用定点聚束,在近定点聚束无法满足方位测绘带宽时,采用滑动聚束的方式以拓展方位向测绘带宽。
对于第3种情况,当气相和水膜间存在较高的切应力,水膜表面将产生Kelvin-Helmholtz波,最终将水滴从水膜表面剥落。Nakao等[1]认为水膜剥落破碎可根据水膜Weber数Wef判定:

(3)
其中:c为波速,m/s;h为水膜厚度,m。但为计算方便常以水膜表面汽流速度us替代us-c,即。当Wef>1.5时,水膜将剥落破碎,该式需先确定h和us。
对于第4种情况,具有较高惯性的水膜流过转角时,在离心力与表面张力的作用下,可能发生水膜分离[10]。Azzopardi等[3]在文献[10]的基础上得到了临界膜厚hc表达式:
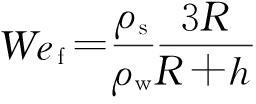
(4)
式中,R为转角曲率半径,m。当膜厚h>hc时,水膜将脱离。将切应力代入式(4)得:
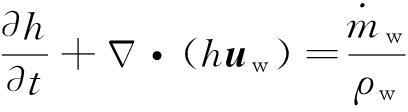
(5)
该式亦需先确定h和us,式(5)可变为:
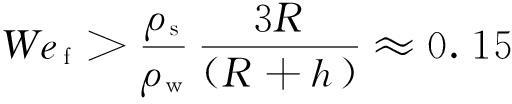
(6)
即钩峰处Wef>0.15时将发生水膜分离。至此,水膜剥落和分离均可采用Wef进行判断。式(3)和(6)均需先确定水膜厚度h和蒸汽速度us,因此下文将通过数值计算获得这些参数。
2 数值计算方案
2.1 气相流动计算
图2示出了波形板计算域,其横截面尺寸与文献[5]中单钩波形板结构尺寸相同。适当延长出口段以确保计算的稳定性。采用结构化网格划分计算域,节点数由1 600 000增加至3 100 000以满足气相流场计算的网格无关性。
为尽量接近真实工况,根据核电厂实际运行参数[1]进行计算。波形板内部流动可认为是定常不可压缩恒温流动,控制方程为雷诺平均Navier-Stocks方程和质量守恒方程。湍流模型采用在模拟研究[5-6]中表现较好的Realizable k-ε模型;采用标准壁面函数求解近壁区;采用商用软件ANSYS FLUENT 14.0进行求解。
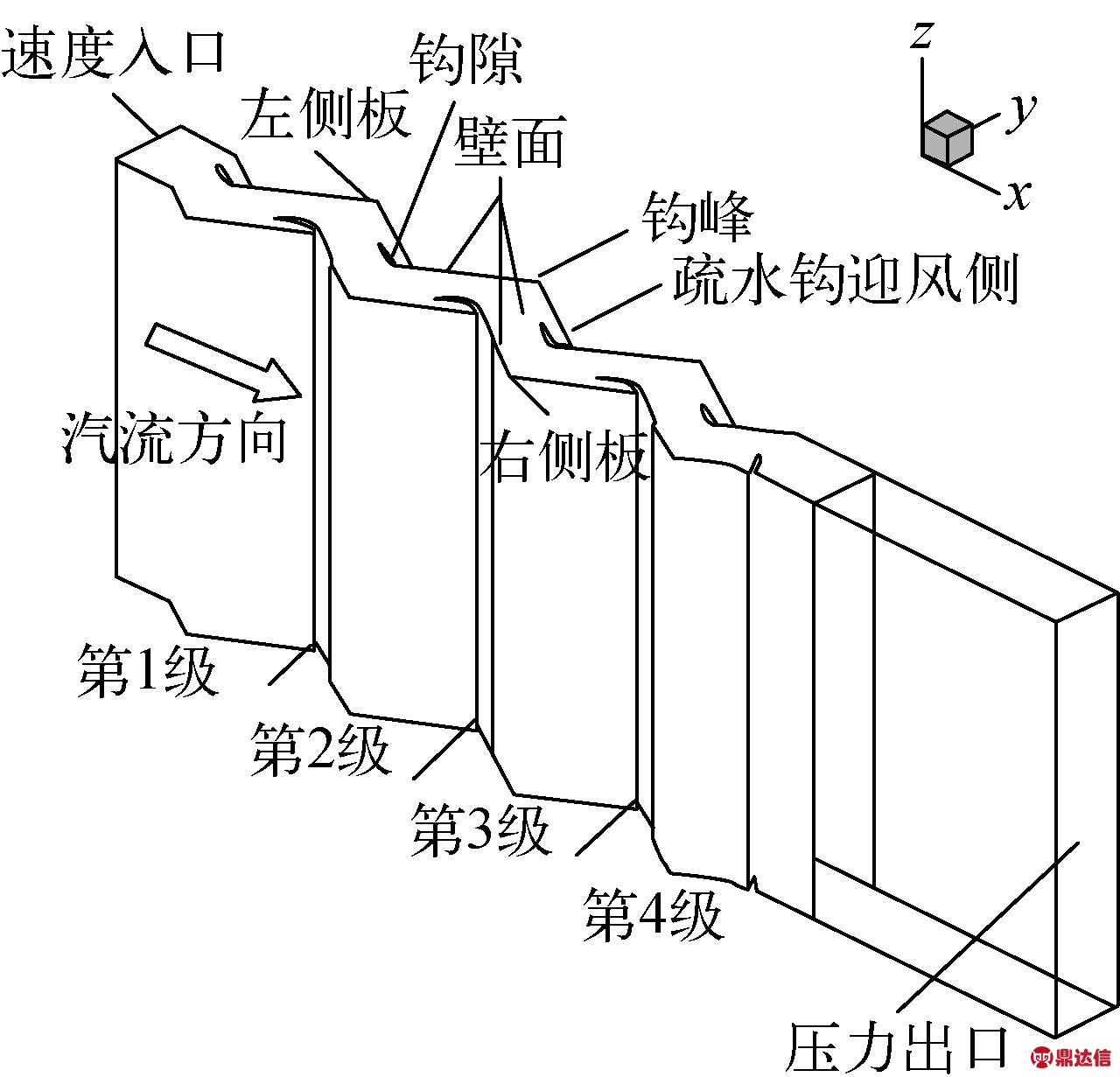
图2 计算域和边界设置
Fig.2 Calculation zone and boundary condition
进口为速度边界,分别取0.5、1和2 m/s;根据Kutateladze数Ku可求得实际运行参数[1]下的临界蒸汽流速usc,当Ku取较高值3.5时,usc=1.9 m/s。所选us=2 m/s可能发生破膜现象。湿度ω取5%、10%和20%;出口为压力边界;实际运行中,波形板底部通过特殊设计使水膜能流出而蒸汽不能,因此底部对水膜设为出口,对蒸汽则设为滑移壁面;波形板顶部和两侧均为无滑移壁面。采用二阶迎风格式进行空间离散,SIMPLE算法用于求解压力与速度的耦合。各工况以残差低于10-4且进、出口流量误差低于0.5%作为收敛标准。
2.2 水滴运动计算
1) 运动轨迹计算
当前入口湿度下,波形板内水分体积分数远小于10%,水滴运动采用离散相模型(DPM)计算[5-6],并在计算中考虑较为重要的虚拟质量力和压力梯度力。
波形板入口水滴粒径分布亦采用Rosin-Rammler分布[4],粒径范围为10~600 μm,平均直径为224 μm[6]。湍流扩散对直径为1~50 μm的水滴运动影响较大[4],本文采用涡交互模型[12]予以考虑,并采用随机涡特征周期来更为真实地反映湍流的随机性。
2) 二次水滴
在本文计算工况下对式(1)以us代替us-uw并取最大蒸汽速度2 m/s和最大粒径600 μm,得到Wed-max=5.1<13,表明在所选热态工况下,水滴不会因气体动力而破碎,与文献[1,5]分析一致。但相较冷态工况下的0.01[1]和0.368[5],该值高出1~2个数量级,表明热态工况较冷态工况更可能发生。
由式(2)可见,,在本文计算工况下以us代替uw并取最大蒸汽速度2 m/s和最大粒径600 μm,得到Wew/C=0.3<1。因此,在所选热态工况下不会发生飞溅,但仍高于冷态工况[5]下的0.16,表明热态工况较冷态工况更可能发生飞溅。
由于忽略了水滴碰壁角度使得水滴撞击频率f偏大,导致计算所得的Wew/C偏小,但本文即使在最大蒸汽速度2 m/s下的CFD计算结果仍显示水滴飞溅产生的水滴数为0,因此在其余工况计算中不再考虑水滴飞溅。
综上所述,发生气体动力作用导致水滴碎裂和水滴撞击水膜产生的飞溅的可能性较低,波形板二次携带将主要由水膜的剥落和分离造成。
2.3 壁面水膜控制方程
壁面水膜的控制方程如下。
质量守恒方程:
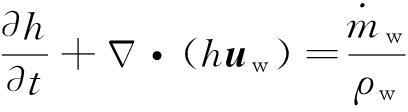
(7)
动量守恒方程:

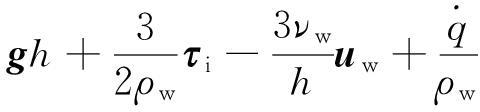
(8)
式中w为来自DPM模型的单位面积质量源项;
h)。式(8)左边分别为瞬时项和对流项,右边第1项包括气相压力ps、重力产生的压力ph和表面张力产生的压力pσ;第2项表示重力g在平行于水膜方向的影响;第3项表示气相-水膜间黏性切应力τi的作用;第4项表示水膜中的黏性力,νw为水的运动黏度;第5项中
表示来自DPM模型的水滴沉积和分离。通过与DPM模型耦合,得到水滴在壁面积聚形成水膜的过程;通过与气相耦合,获得气相对水膜的影响。
时间步长取10-5 s,瞬时项计算采用二阶隐式,空间离散采用二阶迎风格式,最大Courant数小于0.2。对壁面水膜平均厚度进行监测,当该值平稳时,认为达到收敛。每工况在处理器型号为Intel(R)Core(TM)i7-4790(CPU @3.6GHz 3.6GHz)的计算机上需72~168 h,蒸汽速度越高或湿度越大,计算时间则越长。
3 结果与分析
3.1 水膜厚度分布
图3、4示出不同入口us和ω下的壁面水膜厚度h分布。水膜主要集中在波形板的前两级,表明分离作用主要由前两级实现;图3i和图4i显示随us或ω的增加,水膜增厚并在相间剪切力作用下向下游移动,使后两级开始发挥作用,与文献[1]所得结论一致,一定程度上验证了计算的合理性。
在波形板前两级的疏水钩板上,水膜主要分布在钩板的迎风侧、钩峰和钩隙内,并呈股状下流。汽流在钩峰处发生转向,而水滴惯性较大,较易沉积在钩峰,使在较高入口湿度下钩峰处水膜较厚。随us或ω的增加,迎风侧水膜下端增厚,在汽流剪切力作用下产生横向流动,在迎风侧和钩峰之间逐渐出现“短接”现象,使钩峰局部水膜厚度较高,并逐渐增多和扩大;在us=2 m/s时,图3i显示左侧板第2级疏水钩迎风侧和钩峰水膜均被撕破,图4h显示右侧板第1个疏水钩钩峰水膜被撕破,图4i显示当湿度达到20%时,水膜难以维持垂直流动,出现了较大面积分离,并呈一定倾角沿板壁流动。
3.2 水膜破裂分析
图5、6示出不同us和ω下的Wef分布。随us或ω的增加,Wef逐渐增大,具有较高Wef的区域也逐渐扩大。根据Wef>1.5或0.15分别判断水膜剥落或钩峰处水膜分离。
us=0.5 m/s时,波形板内Wef<1.5,而钩峰处仅在ω=20%时出现Wef>0.15的区域。表明在该蒸汽速度/负荷和正常入口湿度(ω≤10%)下,波形板内不会发生水膜剥落或分离;相较水膜剥落,钩峰处水膜分离更易发生。
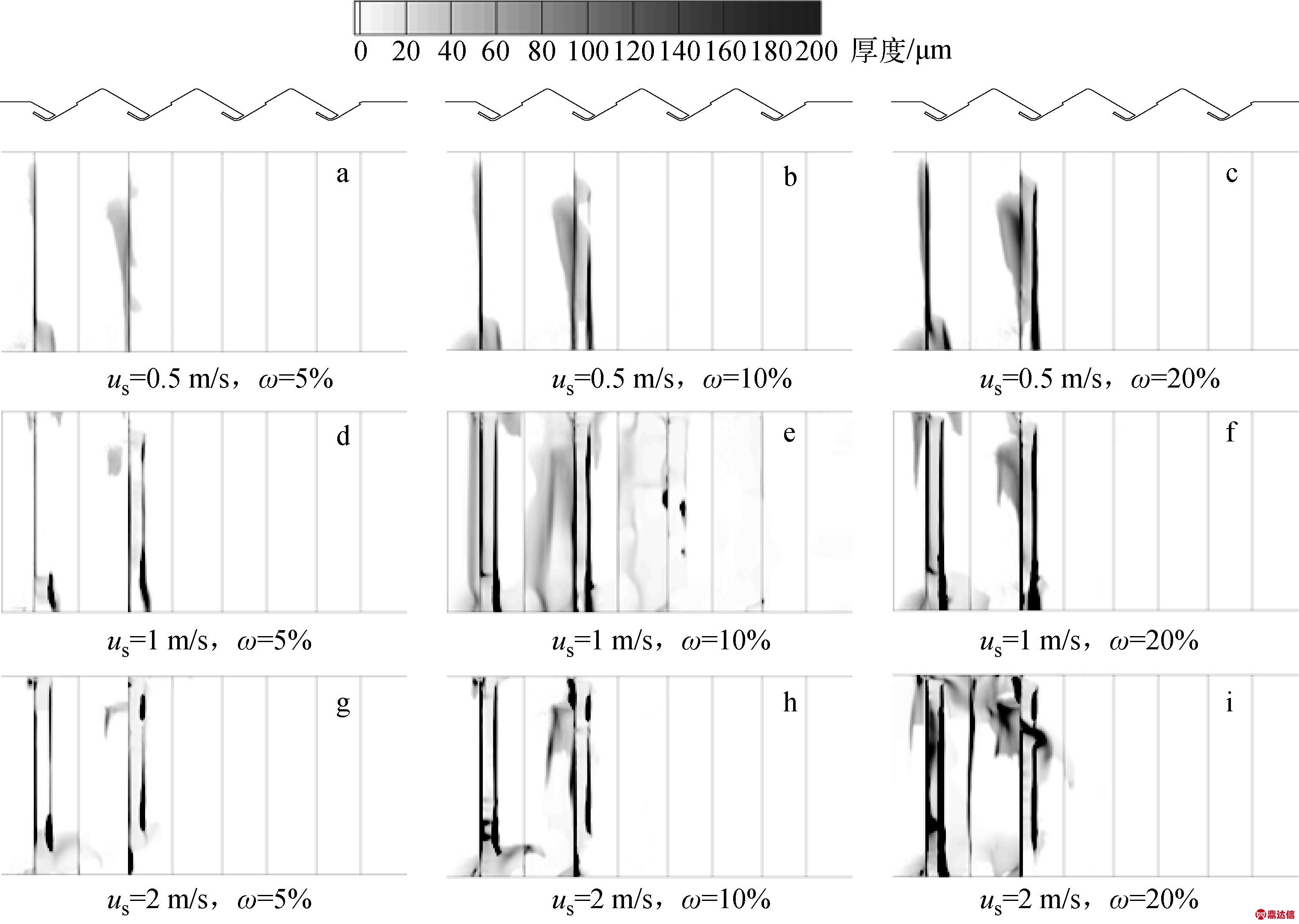
图3 左侧板水膜厚度分布
Fig.3 Water film thickness distribution on left side plate
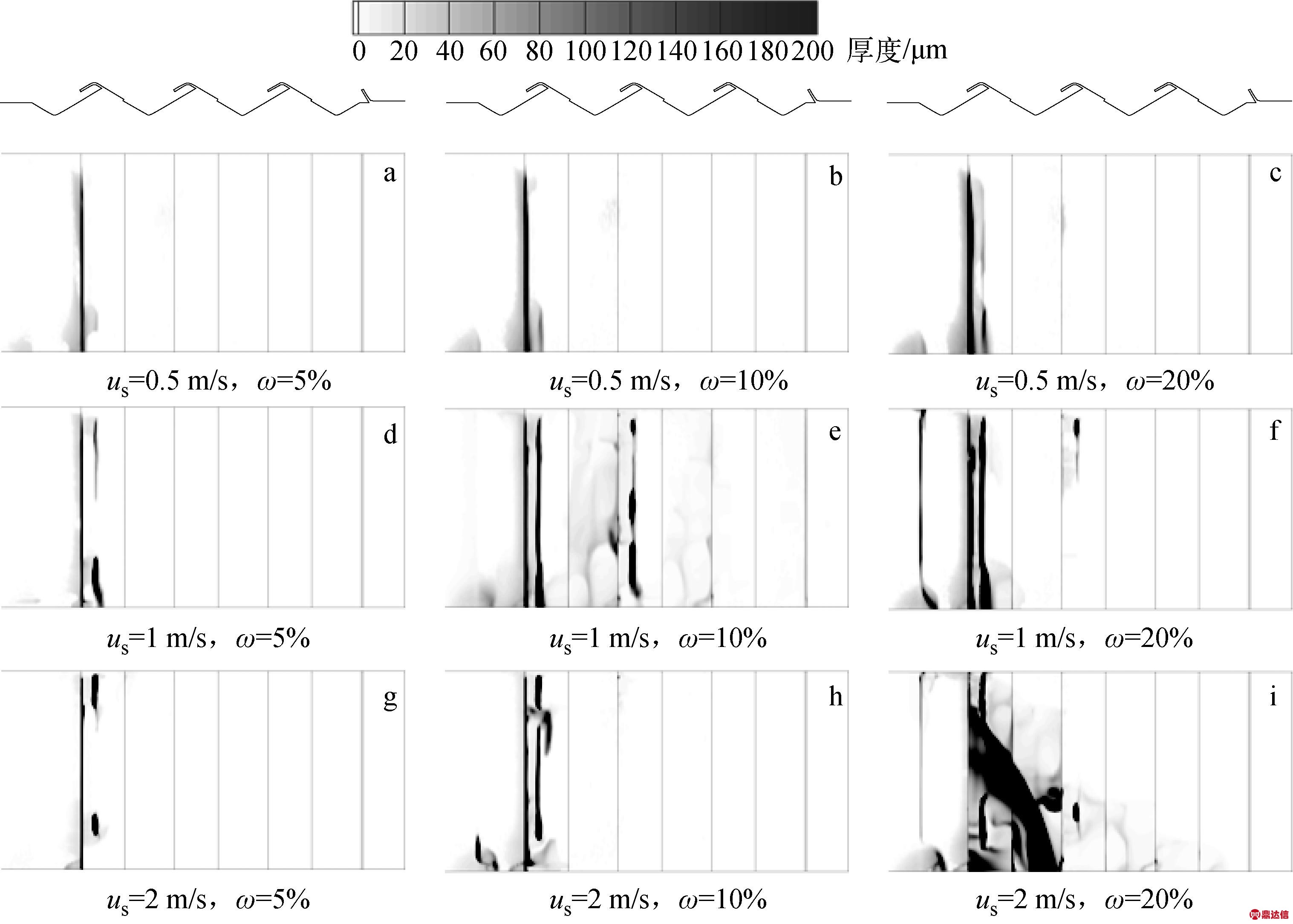
图4 右侧板水膜厚度分布
Fig.4 Water film thickness distribution on right side plate
us=1 m/s时,在各入口湿度下,仅钩峰处存在Wef>0.15或1.5的区域,且随湿度的增加逐渐扩大,表明在该蒸汽速度/负荷下,存在钩峰水膜分离现象。
us=2 m/s时,在各入口湿度下,波形板内尤其钩峰处均存在Wef>0.15或1.5的区域,且随湿度的增加逐渐扩大,表明在该蒸汽速度/负荷下,存在钩峰水膜分离和水膜剥落,并将显著影响分离性能,与Ku的预测结果一致,再次验证了计算的可靠性。当ω=20%时,水膜出现了跨级流动,导致高Wef区增大,产生较大面积的水膜剥落,且更加靠近波形板出口,进而严重影响分离性能。
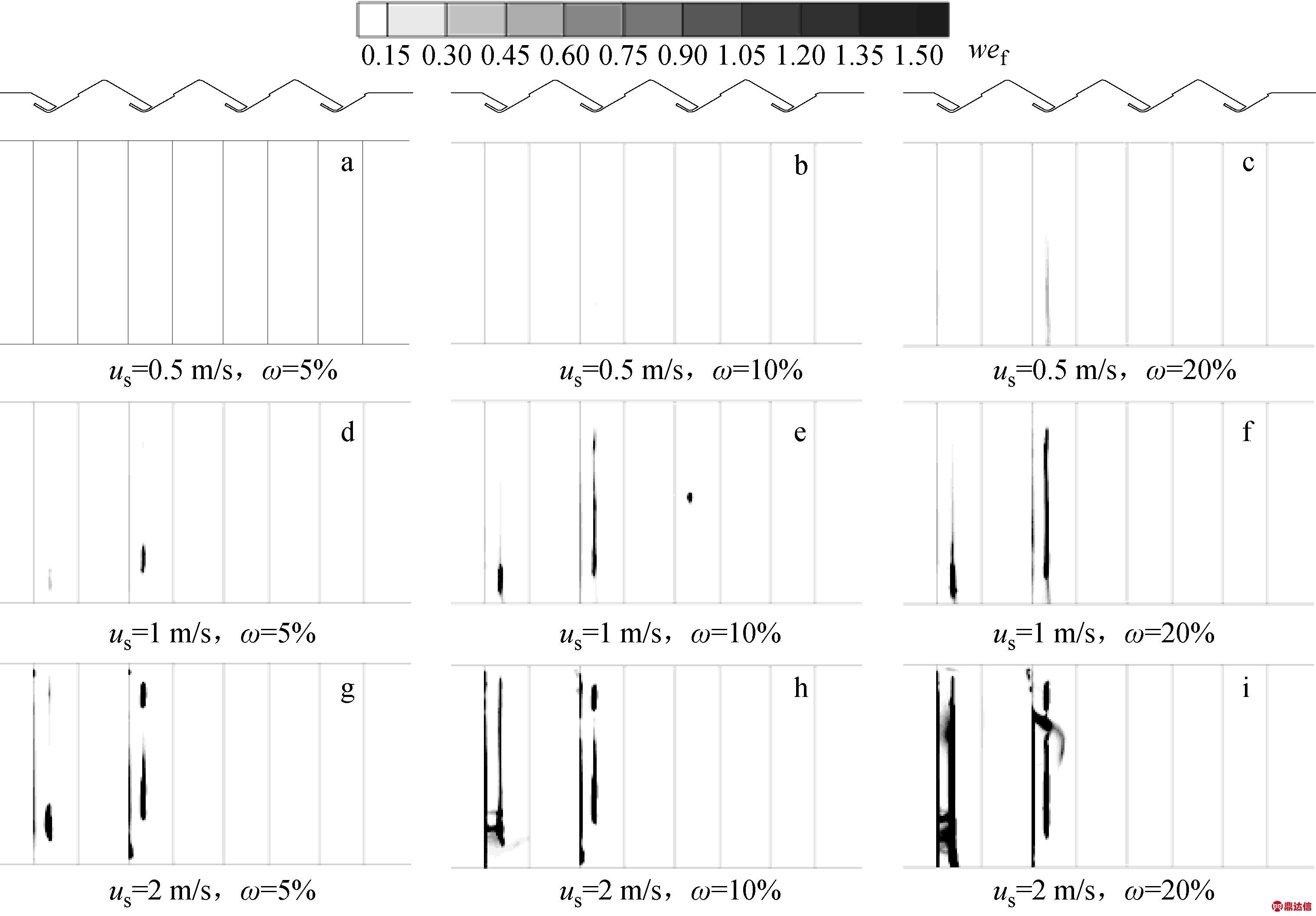
图5 左侧板Wef分布
Fig.5 Distribution of Wef on left side plate
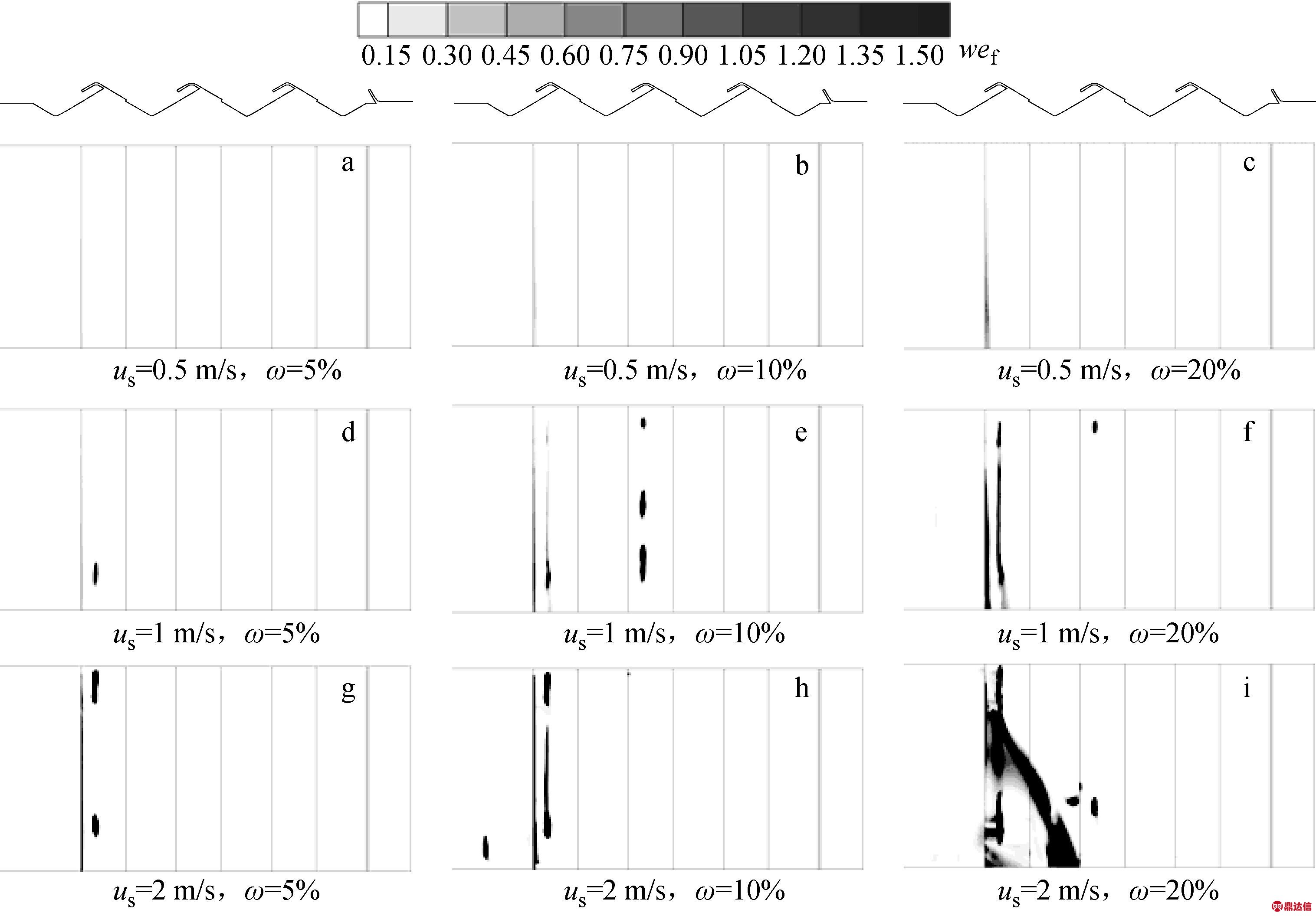
图6 右侧板Wef分布
Fig.6 Distribution of Wef on right side plate
4 结论
1) 实际运行工况下,根据相应判别式,波形板内不会发生气体动力造成的水滴破碎与水滴撞击水膜产生的飞溅,但较冷态工况下的可能性高;
2) 水膜及其运动主要集中在波形板的前两级,随着入口蒸汽速度或湿度的增加,水膜增厚并向下游移动,出现“短接”甚至跨级流动现象;
3) 将水膜分离的判别式采用Weber数来表达,从而与水膜剥落的判别式一致,并得到水膜分离的临界韦伯数表达式,在本文工况下该值取0.15;
4) 计算结果表明波形板二次携带主要由水膜的剥落和分离造成,且相较水膜剥落,钩峰处的水膜分离更易发生,在正常运行条件下(us=1 m/s,ω=10%),波形板内不会发生水膜剥落,但可能发生钩峰水膜分离。