摘要:燃气轮机进气系统配置或运行维护不当,会引起燃气轮机运行效率和出力降低甚至故障。为此首先通过介绍典型的进气过滤系统结构,分别从过滤器的过滤机理、滤材特性、滤芯型式、过滤性能评价等方面系统阐述进气系统的工作原理,分析过滤器性能对燃气轮机运行的影响;继而根据不同进气环境的特点,提出设计选型原则和运行维护措施建议,即合理配置进气过滤系统须综合考虑进气环境、滤芯性能及布置方法,并考虑后期运行维护工作的经济便捷性。最后结合实际工程案例表明:利用所提的设计原则和运行维护经验进行进气过滤系统改造后,过滤器进气压差增长速度较之前明显降低,运行效率和出力升高,堵塞问题得到初步解决。
关键词: 燃气轮机;进气;过滤器;设计选型;运行维护
燃气轮机发电机组具有发电效率高、污染物排放低、建造周期短、占地面积小、耗水量少和运行调节灵活等特点。目前,燃气轮机电站的发电量约占全球总发电量的23.1%[1],最先进的H(J)等级的机组单机容量大于500 MW,联合循环效率大于63%[2]。燃气轮机是精密的高速旋转机械,燃烧及做功过程需消耗大量的空气,若所吸入的空气中携带过多的灰尘(粒径在1~100 μm范围内)或有大颗粒杂质(粒径大于等于1 mm),就会影响燃气轮机性能和安全运行。首先,灰尘会逐渐附着在压气机叶片上形成污垢,致使压气机的效率、流量、压比等指标降低,极端情况下还会引发压气机失速喘振或振动故障[3-4];其次,大的颗粒物会对压气机叶片和透平叶片产生擦伤和侵蚀,造成叶片寿命缩短或损坏,影响机组的性能和可靠性[5-6]。尽管进气过滤系统占联合循环电站总投资的比例并不高,但进气系统导致的燃气轮机故障时有发生,且进气空间的限制致使后续维修改造极其困难,因而得到广泛关注。目前有些文献在燃气轮机进气系统引发的故障和进气滤网更换周期优化方面做了研究,但文章多数都是针对某一具体问题展开讨论,对问题产生的机理和根源,即进气过滤的原理和进气系统的方案设计,以及在运行维护过程中如何避免或减少问题的产生尚未有系统性分析和总结。基于此,本文解构了国内外燃气轮机厂商主流机组的进气过滤系统所采用的典型配置方案,分析阐述了进气过滤的机理和关键技术,介绍了通用的过滤器选型和评价标准,最后通过案例分析总结了进气过滤系统的工程设计和运行维护实践经验,为燃气轮机进气系统配置和运行维护提供参考。
1 进气过滤系统的结构
进气系统整体上是一个大的封闭空间,一般由过滤段、消音段、进气通道和进气室组成,典型的进气装置结构如图1所示。
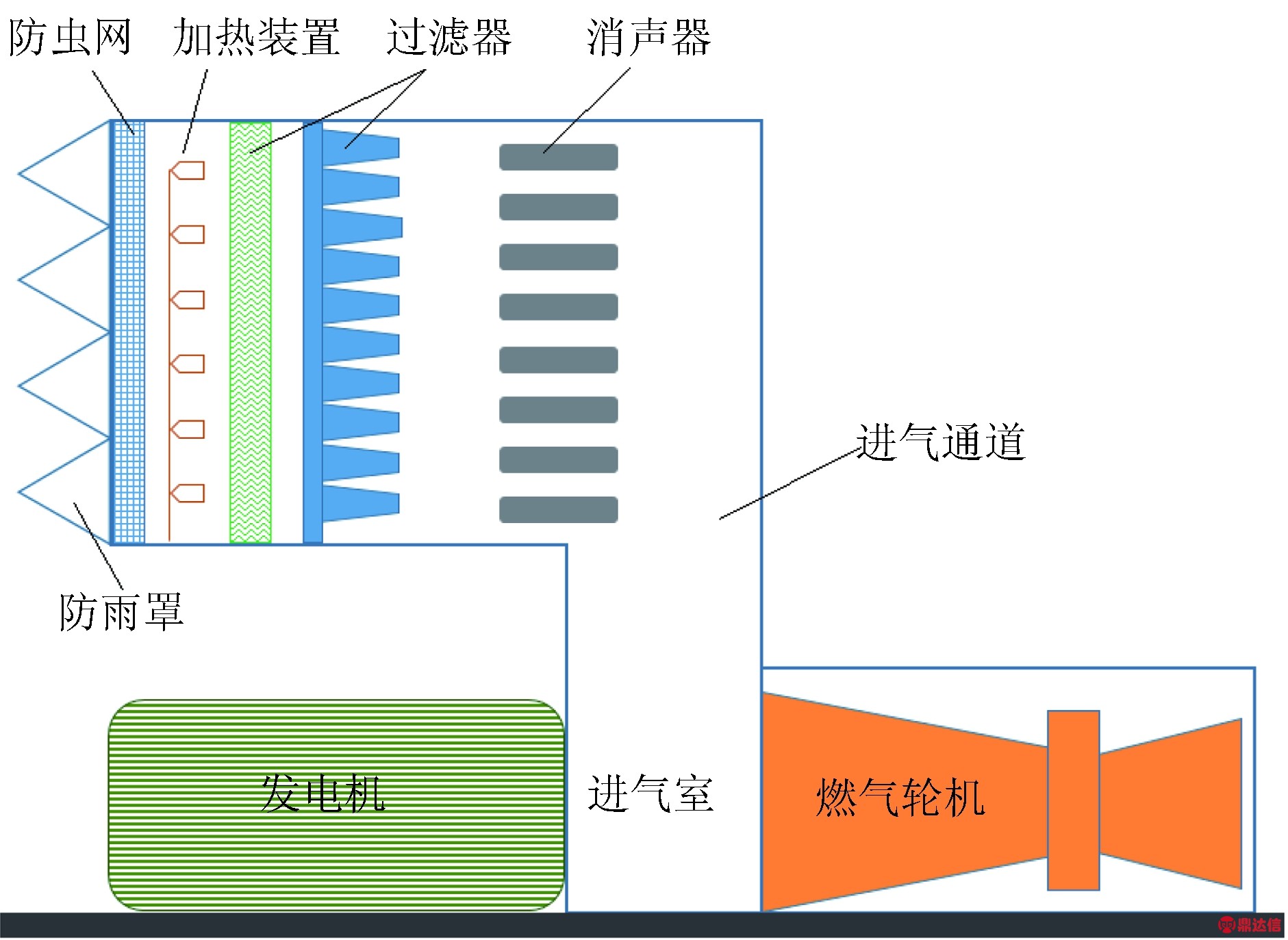
图1 进气过滤系统结构
Fig.1 Structure of air inlet filtration system
空气由过滤段前端的进气防雨罩吸入,之后经防虫网再进入到过滤段。在潮湿多雨地区,为防止空气携带大量的水汽进入过滤器,通常会在防雨罩上同时设置水滴分离器和聚结过滤器。空气通过一级或多级过滤器,过滤掉其中绝大多数的微粒,保护压气机叶片不被磨损、腐蚀和结垢。除湿和过滤可单独布置,也可综合布置。在寒冷地区,通常还须在过滤段前加装空气加热装置,以防止水汽结冰覆盖住过滤器影响进气流量。加热装置的热量来自压气机中间抽气,热空气通过喷嘴喷射到过滤器前的整个进气空间。消声段布置在过滤器与进气弯道之间,消声器按类别区分主要有阻性消声器、抗性消声器以及阻抗复合型消声器[7]。阻性消声器主要特点是对听觉上较为刺耳的高频噪音有突出的消声作用,因而进气系统通常采用阻性消声器。消声器之后的进气通道包含进气弯道、直管段、膨胀节和挡板门等部件,对过滤后的空气进行导流和整流。膨胀节位于挡板门之前,进气系统与压气机之间的振动是通过织物膨胀节吸收的。挡板门位于压气机锥形进气室上游的直管段上,由电动执行机构驱动,当燃气轮机停机时,关闭挡板门以防止湿空气进入压气机,同时保证停机时干燥系统能对燃气轮机通流部分的空气进行有效的干燥。
2 进气过滤的机理及型式
2.1 过滤的机理
考虑到燃气轮机的地理位置、周边的生产活动和气候季节性变化等因素,进气系统吸入的空气可能含有的介质包括固体颗粒、气体和液体,如昆虫、花粉(絮)、海盐、水汽、灰尘、沙子、工厂排气、含有石油和燃料蒸汽的废气、颗粒以及化学品和各种工业副产品等。
空气中的微粒一直在作布朗运动,微粒与过滤纤维间还存在范德华力和表面静电相互作用。根据空气中微粒分散度、物理化学特性和带电状况,过滤器可归纳为5种基本过滤机制:惯性碰撞、拦截效应、扩散、筛除和静电效应[8]。惯性碰撞是指气流沿过滤纤维绕流时,大而重的微粒(粒径大于 1 μm)因惯性直线运动脱离流线,直接撞击并附着在过滤纤维上。拦截是指中等大小的微粒(粒径在0.5~1.0 μm之间)在气流中沿流线运动接触到过滤纤维并被截留。扩散是指粒径在0.5 μm以下的微粒做布朗运动而撞击到过滤纤维并被捕获的过程。筛除是指过滤纤维之间的空隙小于颗粒本身,导致微粒流经时被捕获和夹持。静电效应是指粒径在0.01~1.00 μm范围的带电微粒在流经静电纺丝纤维时在静电的作用下被吸附。过滤器所采用的过滤机理取决于介质通过的速度、纤维大小、介质的堆积密度、颗粒大小和静电电荷,在单一过滤器中通常综合运用了各种过滤机理。
2.2 过滤器的滤材和型式
滤纸是过滤器的核心,滤纸特性直接关系到过滤系统的性能,过滤材质已从全植物纤维滤纸、非植物纤维复合滤纸、全非植物纤维滤纸发展到了纳米纤维复合滤纸[9]。为满足性能、加工和使用寿命需要,滤纸除了要有一定的耐湿性、耐腐蚀性、耐热性等,还要满足耐破度、弯曲挺度、厚度、透气度和孔径等指标要求。滤芯内部滤纸的褶皱方法对过滤器的结构阻力有影响,也是一项关键技术[10]。例如针对纤维和易结块颗粒,较宽的褶皱间距其脉冲清洗效率更高。国内外过滤产品的差距主要体现在滤材和阻力特性这两方面。近年来以静电纺丝纳米纤维膜覆由纤维素、聚酯和聚酰胺组成的粗纤维基材的过滤材料成为研究热点。利用静电纺丝法制得的纳米纤维膜具有表面积大、纤维直径小(0.2~0.3 μm)、孔隙率高、多孔互连结构等特点,在微粒捕捉方面优势明显,因而静电纺丝过滤器具有良好的过滤性能[11]。
为了满足不同运行环境、检修维护间隔和空气洁净度的要求,生产商开发了多种不同类型的过滤器。粗过滤器通常放置在聚结过滤器之后,以清除空气中较大的颗粒杂质(粒径在2~10 μm范围内),该类型过滤器一般由粗合成纤维滤纸嵌入在一次性的矩形框架结构中,为了增大容尘量和减小过滤压力损失,粗过滤器通常做成滤袋的形式以增大过滤面积。中、高效过滤器在多级组合式过滤系统中布置在粗过滤器之后,目的是为了清除粗过滤器无法过滤掉的亚微米级颗粒杂质,这些细小杂质可能会引起叶片腐蚀、结垢和冷却通道堵塞。根据EN 1822-1:2009,高效过滤器可分为EPA、HEPA和ULPA 3个等级,最低过滤效率分别为85.0%、99.95%和99.999 5% [12]。
过滤器可以做成不同的型式:矩形板式、圆柱筒式和袋式。按照过滤器是否可重复利用的标准,可将其分为静态过滤器和自清洁过滤器。对于静态过滤器,当它积累到一定容尘量或过滤压力损失后就需要对其进行更换,以便进气系统重新恢复过滤能力。静态过滤器一般使用矩形框褶皱或W型无隔板玻璃纤维滤纸,采用深层过滤方式,粉尘颗粒会渗透并累积到滤料基底深处,堵住气流通路。自清洁过滤器通常做成圆筒状,滤纸密集折叠绕筒环布一圈,滤筒内外以金属网将滤纸固定。为消除传统滤纸中灰尘粒子被截留在滤材孔隙里难以反吹清除的问题,自清洁过滤器一般采用纳米纤维复合滤纸,该滤纸将灰尘粒子捕集在滤材表面,减少粒子向滤材深处穿透,这种表面过滤的特性使得捕集的灰尘粒子在脉冲反吹的过程中更容易脱除。当过滤器的压力损失达到某一阈值,利用从滤筒由内向外反吹脉冲压缩空气,清除滤纸表面积累的容尘,使得过滤器重新恢复一定的压力损失,滤芯可多次重复利用。
3 过滤器的性能评价及选型
3.1 过滤器的性能指标
过滤器的评价需考虑多方面因素,在工业应用中主要考虑以下几个性能指标:迎面风速、压力损失、容尘量、过滤效率。
a) 迎面风速。过滤器的分级都是基于额定风量或试验风量确定的,风量等于过滤器迎面风速乘以过滤器迎风面积。迎面风速高,大颗粒惯性过滤效应增强;迎面风速低,微小颗粒扩散过滤效应增强。过滤器压力损失与迎面风速的平方成正比,因此迎面风速不宜过高,一般不超过3 m/s。
b) 压力损失。空气通过过滤器的杂乱纤维后会有一定的压力损失,其与过滤效率成正相关性。当进气压力损失增大时,过滤器后的进气压力和密度均降低,空气质量流量减小,为维持燃气轮机出力和排气温度平稳,压气机的压比就要增大,须消耗更多压缩功,因而会降低燃气轮机的效率。
c) 容尘量。在额定风量下,随着过滤器不断地捕集灰尘颗粒,慢慢地会达到“满尘”状态,这时它的压力损失会达到一个设定值。根据过滤材质的不同,过滤器的容尘有2种形式:一种是微粒逐渐地嵌入到滤纸纤维层中间去;另一种是微粒大部分积聚在滤纸纤维表面,只有很少一部分能够穿透到纤维层中。容尘量越大,过滤器更换的频次越低。
d) 过滤效率。过滤效率η是一个广义的概念,微粒重量、体积或粒子数Xout与进入过滤器的原始量Xin和过滤效率η的关系为
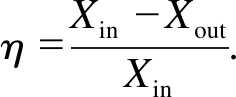
(1)
过滤效率可以用几种方式来表达:最大效率、最小效率和全生命周期平均效率。有些过滤器在初始使用阶段对微小颗粒的过滤作用非常弱,但是随着过滤纤维捕获了一些颗粒,反而逐渐能捕集之前无法捕获的微小颗粒了,这样它的平均效率是要高于初始效率的。过滤效率也随颗粒大小而变化,通常对小颗粒的过滤效率较低,对大颗粒的过滤效率较高;因此,在讨论过滤效率时须与规定的粒度范围和流速相关联。目前国内外比较通行的通风用空气过滤器标准的分级和对比关系参见文献[13]。
通常在选择过滤器产品时,除以上指标外,还需考虑过滤器的耐用性、维修更换的便捷性和较低的操作限制,以便实现灵活的运行调整和较低的运行维护支出。
3.2 过滤器性能对燃气轮机运行的影响
过滤器对燃气轮机运行的影响可概括为3个方面:热效率、出力和运行安全。
过滤器能够保护通流部分,如果空气洁净度不够会导致压气机叶片磨损和结垢,使压气机的气动性能偏离流体设计工况,引起通流效率和喘振裕度的下降。结垢的严重程度及结垢部位与颗粒物大小有直接关系,沉积速率与颗粒物初始浓度和表面粗糙度等成正比[14]。文献[15]研究发现结垢对压气机压比影响最大,效率次之,质量流量最小。
粗过滤器的压差在其前90%寿命周期增长平缓,之后开始快速增长;精过滤器的压差在总压差中占比较大,但在运行周期内一般上升幅度很小。过滤器的压差通过压差变送器将信号传送到控制系统,当压差到达某一设定值时,机组需降负荷运行;压差进一步增长到极端情况设定值后需立即停机处理。正常情况下过滤器的总压力损失一般在300~1 000 Pa范围内,对于简单循环,进气压力损失每增加250 Pa,出力将会降低0.4%,热耗增加0.1%[2];但在此范围内压力损失对联合循环机组热耗和出力的影响并不明显[16]。IGIE、ELSAWY和杨小军等研究发现联合循环机组配置高效的过滤系统比配置低效的过滤系统性能更好,尽管高效的过滤系统压力损失更大[17-19]。
若因过滤器压差过大导致非计划停机,机组轴系和叶片寿命会因燃气轮机启停次数的增加而受影响。此外,灰尘在压气机上产生磨损或结垢,会改变压气机的气动特性甚至引发振动故障,灰粒在热通道上沉积还会引起叶片热腐蚀。含金属无机盐的微粒在燃烧过程中与硫和氧发生反应,这些无机盐燃烧产物会沉积在燃烧室衬套、喷嘴、涡轮叶片和过渡件上,导致这些部件上具有保护作用的氧化膜的氧化速度数倍加快,并有可能堵塞透平叶片冷却空气孔而使叶片局部过热被烧损[20-21]。
3.3 过滤器的设计选型
不同环境下过滤器的配置型式不同,运行维护的要求也不同。按照不同气候条件和现场环境,可把进气环境进行分类,结果见表1。
如果选择了错误的过滤系统则可能导致更频繁的过滤器更换、更高的入口压力损失、计划外停机或燃气轮机故障,以及相关的成本或盈利损失。在过滤器的设计选型阶段,需要考虑气候条件和主要颗粒物,总结起来有以下一些选型原则和经验:①在多雨雪地区应选择防雨罩,同时为了防止进气携带水汽较多,还应配置聚结过滤器和水滴分离器;②在多昆虫或多悬浮杂物环境应选择防虫网;③在严寒地区应设置加热装置,防止进气系统结冰堵塞;④在干燥多沙尘地区,宜选用自清洁过滤器,减少过滤器更换频率,若机组需配置进气冷却装置保证出力,则应考虑设聚结过滤器或水滴分离器;⑤在沿海或海洋环境应着重考虑增强配置除湿装置,适当增加在线水洗频次以防止盐分沉积;⑥在多细尘工业区或空气相对湿度较大环境,宜选择静态过滤器,防止细尘在过滤器内板结;⑦若过滤效果不理想,在满足进气压力损失的条件下可增加过滤器级数,一般不多于3级。进气系统的主要配置部件如图2所示。
在进行不同进气系统设计方案的对比分析时,可采用过滤器全寿命周期成本分析方法[22],对设备的购置成本和废弃成本进行综合的测算与比较,考虑价格变化因素后分别折成一个净现值(net present value,NPV),各净现值相加得到一个进气系统的总净现值fNPV,total,该值最低者为最优方案。
fNPV,n=C.
(2)

(3)
式(2)、(3)中:C为年运行维护成本;i为折现率;e为价格增长率;N为运营的年数,j=1,2,…,N;Cb为购置成本;Cd为废弃成本;fNPV,n为第n年运行维护成本的净现值。
表1 燃气轮机进气环境分类
Tab.1 Classification of inlet air conditions

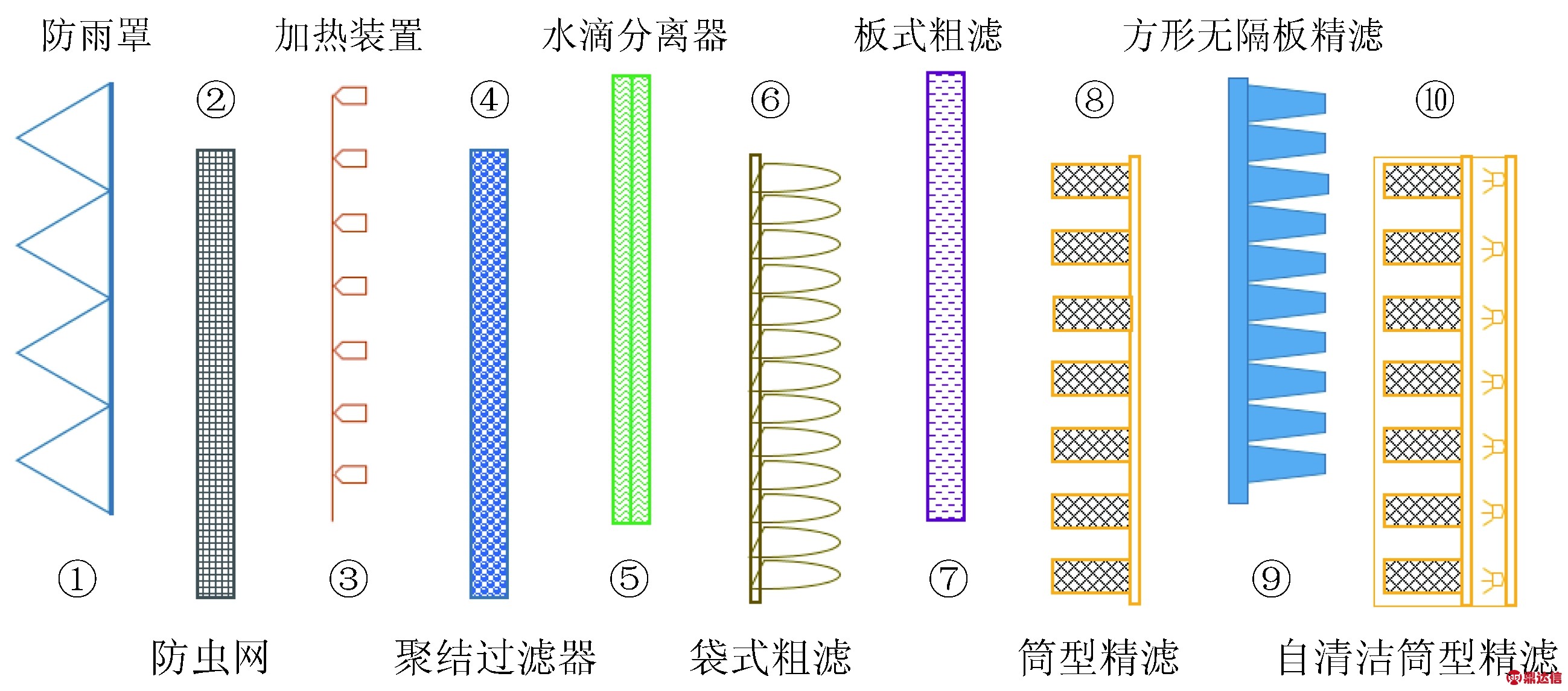
图2 进气过滤系统部件
Fig.2 Air inlet filtration system components
3.4 过滤器的运行维护
系统选型设计对过滤器运行效果的影响最为关键,但是良好的进气系统运行维护工作也同样需要引起重视。标准化的进气系统运行维护规范目前尚未建立,国内电厂大都根据自身情况在摸索如何与本体检修结合起来,例如小修前进行检测评估是否更换滤芯,定期对进气压差进行检查记录,并根据压差变化趋势预判滤芯寿命或其他评估决定更换哪一级。对于低位布置的燃气轮机进气系统,需要在进气口的周围保持干净,以免粗过滤器负荷过重。对于配置自清洁过滤器的进气系统,要充分利用机组停机的时机进行过滤器清理反吹,此时进气系统空气停滞不存在滤网二次吸附的影响,灰尘收集系统可将反吹掉的灰尘充分排出进气系统,增强反吹清洁效果。若当地有飞絮时节,要注意及时清理防虫网上积累的飞絮,以免堵塞进气。在某些空气湿度相对较大且粉尘较多的时期,为了防止灰尘聚结,可以优化进气加热系统和反吹系统的控制逻辑,增加投入使用频率,降低空气相对湿度以减轻过滤器内灰尘结垢情况,延长滤芯寿命[23]。当采取措施提升了过滤器的过滤等级后,压气机通流部分的洁净度会大大改善,基荷机组可以适当减少在线水洗的频次。过滤器拆卸检修期间,人工吹扫过滤器时要防止损坏滤芯,尤其注意滤芯内部不要受颗粒物沾污,保证燃气轮机安全运行。所有滤筒必须同时更换,如果混用新旧滤芯,气流会自动通过阻力最小的路径并绕新滤筒循环,这会迫使压气机将粉尘颗粒吸入新滤材的深处,导致这些沉积粉尘最终无法通过脉冲清灰进行清理,而且这些滤筒容尘会很快饱和,最终需要比原计划提前更换。
3.5 案例介绍
以本文第一作者在2017年工作中所参与的工程总承包项目——格鲁吉亚某燃气联合循环电站为例。该GE-6FA.03燃气轮机在进气过滤器选型设计时,因未考虑到附近水泥厂粉尘飘散的影响,设计参数Dust Level基准值为0,即认为当地空气较干净,因而选择了板式粗过滤器(G4)和脉冲反吹的自清洁筒式过滤器(F9)的简单组合配置。该机组在枯水期承担基本负荷,在正常运行仅4个多月后,过滤器进出口压差就从350 Pa上升至1 500 Pa,触发了进气系统设置的报警阈值,机组被迫停机检修。运行维护人员在检修过滤器时发现,自清洁筒式过滤器已被大面积的粉尘结块所堵塞,反吹也无法清除,因而导致过滤器压差急剧上升。事后分析认为原因如下:由于当地空气全年平均相对湿度较高(68%),冬季11月至次年2月的相对湿度最大值可达95%以上,而过滤器入口也未配置水滴分离器,因此在过滤器内存在很多水汽;其次,水泥厂飘散输送来的无机污染物黏性粉尘较多,由于粗滤过滤不充分,无机污染物黏性粉尘在精滤筒内吸收水汽而聚结,反吹系统无法清除,导致过滤器堵塞。在解决方案上曾考虑过将该自清洁过滤器更换为静态精滤,但由于静态精滤无法在线更换,故空气质量较差时会导致频繁停机更换,影响电站运行的经济性。综合考虑后对该电站采取的措施为:加装水滴分离器,粗滤改装为无隔板(M6)玻璃纤维过滤器,更换新的滤筒,并加大了进气加热系统的反吹时间和频次,以降低水汽含量和减少粉尘集聚,延长滤筒更换周期,减少因进气系统性能劣化导致的发电效率损失、停机损失和过滤部件频繁更换的运行维护损失。工程总承包项目中进气系统通常是在燃气轮机厂商的供货范围内,该项目美国通用电气公司给出的改造变更报价为36万欧元。改造后运行的8个多月时间内,进气压差由初始值380 Pa缓慢上升至700 Pa左右,运行效果较之前大有改善。
4 结束语
燃气轮机进气过滤系统的配置选型需要综合考虑当地气象条件、现场空气环境和运行维护经济便捷等因素,过滤效果主要取决于进气系统的过滤级数和滤材特性。当前采用静电纺丝工艺生产的纳米纤维复合滤纸能够满足进气高效净化、延长滤芯寿命并显著节约成本的要求,但仍需解决效率和压力损失的矛盾,提高静电纺丝纳米纤维滤材的容尘性能。对不易引起过滤器积垢板结的进气环境,选择自清洁过滤器相比于静态过滤器有助于减少滤芯更换次数,降低更换成本和人工成本的同时缩短停机时间。了解进气过滤系统的功能结构和过滤机理,总结运行维护经验,有助于工程技术人员更好地设计进气过滤系统,从源头上保障机组安全稳定运行并降低后期运行维护成本。