摘 要:为了提高空调系统中旋流油分离器的分离效率、降低压力损失,本文对其结构参数进行了优化设计,通过流体仿真研究了油分离器内部各参数对分离效率和压力损失的影响,得到最佳的参数尺寸比例,并据此制作了一款新型油分离器,安装在空调系统中进行实验测试。实验结果表明:新型油分离器在回油工况(最低制冷剂流速)下分离效率由95.5%提高到99.0%,名义制冷工况下分离效率由97.3%提高到99.6%;名义制冷工况下压力损失由55.2 kPa降低至23.1 kPa;同时获得了油滴颗粒的分布函数。
关键词:分离性能;流体仿真;旋流分离器
空调油分离器一般分为滤网式、填料式、离心式(旋流式)和洗涤式。无论采用何种形式的油分离器,需要以分离效率和压力损失来评价。分离效率不高,导致润滑油循环量上升,当循环量为3%和5%时,蒸发器制冷量的衰减约为5%和10%[1]。一般情况下,系统中带油率每提高1%,循环性能系数COP衰减约2.5%[2-4]。分离效率不高引发压缩机缺油甚至可能导致抱轴、烧毁等恶性现象[5]。油分离器的压力损失会导致排气压力上升,压比加大,COP下降[6]。
目前国内外对空调油分离器的研究多集中在过滤式油分离器上,如左世海等[7]研究过滤式油分离器的过滤结构及滤芯布置,申浩等[8]研究过滤式油分离器过滤网目数对分离效率的影响。在旋流油分离器方面,李进杨[9]研究螺旋式旋流油分离器的工作原理和应用方案,吕家明等[10]通过流体仿真减小了气液分离器的容积,罗毅等[11]通过流体仿真认为进气管、筒体直径和进气碰撞结构对油分离器性能影响较大。空调油分离器入口处油滴颗粒直径分布、内部流场规律研究和常规油分离器结构具体尺寸比例优化涉及的较少。
本文以空调旋流油分离器为研究对象,采用CFD方法对其内部流场进行模拟,并根据内部流场规律提出一种新型油分离器结构及几何尺寸关系,通过实验验证其性能。并利用实验数据校核入口油滴颗粒直径分布函数参数β。
1 油分离器优化设计
1.1 旋流油分离器原理
常规旋流油分离器结构大多如图1所示,包括气态制冷剂出口管、油气混合物入口管、回油管、筒体、内筒体等。
当油气混合物进入分离器后,受油分离器壁面约束,由直线运动转为圆周运动,旋转气体绝大部分沿轴向下做螺旋运动,即外漩涡。这时密度大的被甩向分离器壁面,通过与壁面的一次次碰撞,动量损失完,并随着气体的外漩涡落入排油口被分离出来。
外漩涡使得周边气体压力升高,在筒体中心形成低压区,当气体到达筒体下部某一位置时,向中心集中,以相同的旋转方向向上做螺旋运动,即内漩涡。部分未被分离的油也和气体一起排出去。
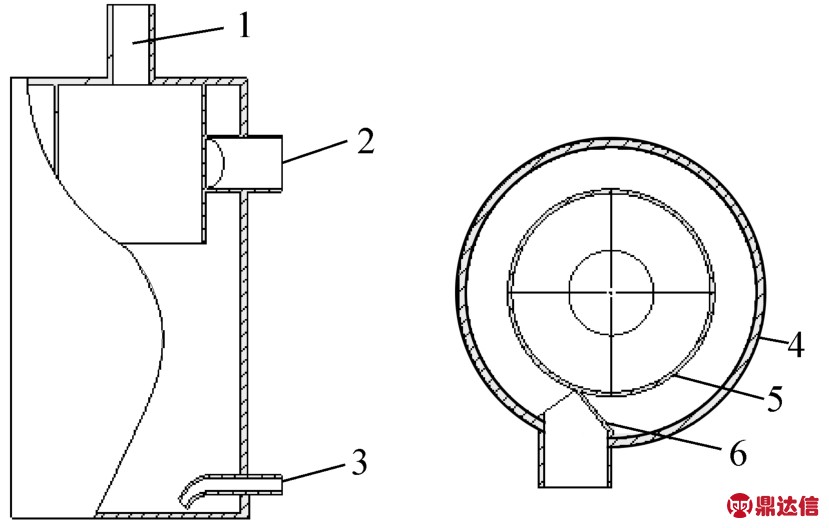
图1 常规油分离器结构
Fig.1 The structure of conventional oil separator
1气态制冷剂出口;2油气混合物入口管;3回油管;4筒体;5内筒体;6挡板
1.2 常规油分离器结构
如图1所示,常规油分离器结构是“矮胖”型,分离器内油气混合物速度小。当油气混合物入口流速低于5 m/s或颗粒直径小于1×10-5m时,分离效率不高,不利于压缩机的长期稳定运行。
常规油分离器入口通过挡板来加速和保证运动轨迹。由于气体与挡板碰撞,损失较大。当油气混合物流速大于18 m/s时,油分离器的压力损失达到60 kPa以上,使空调COP明显下降。
1.3 油分离器的优化设计
为了提高油分离器分离效率,降低压力损失,设计如图2所示的油分离器结构。
1)在入口管2处采用异径接头加速,替代挡板加速,消除碰撞挡板的压力损失;取消入口管深入到筒体内部分,避免伸入段影响混合物运动轨迹。
2)减小筒体直径,增加混合物的流速;筒体长度加大,使油气混合物能够充分进行螺旋运动,油气能充分分离。
3)在油分离器下半部分增加锥部6,对进入到油分离器底部的油分离器再次加速,提高小颗粒的分离效率,尤其是低流速下的情况。
2 仿真计算
为了对图2的结构的油分离器的参数进行优化,对其进行理论分析和流体仿真计算。早在1978年,柳绮年等[12]对分离器内部的三维流场分布进行测量。近些年来,越来越多的人利用流体仿真手段来研究气液/气固分离[13-14]。
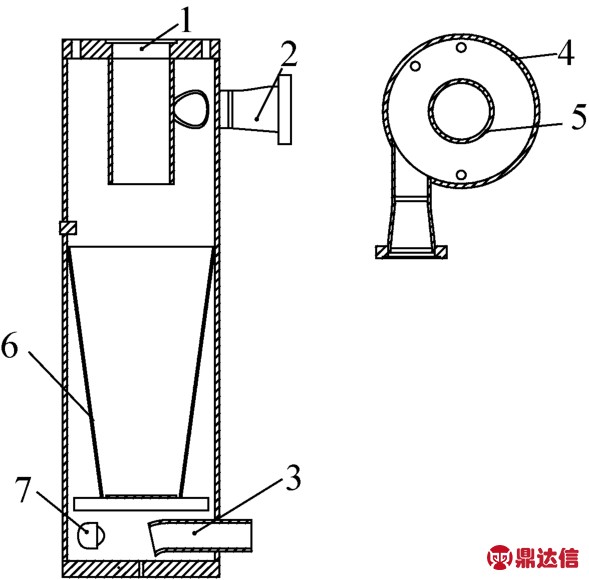
图2 新型油分离器
Fig.2 The structure of new oil separator
1气态制冷剂出口;2油气混合物入口管;3回油管;4筒体;5内筒体;6锥体;7电加热等插口
2.1 计算模型
由于油分离器内流动非常复杂,各向异性比较明显,制冷剂连续相多采用的是雷诺应力湍流模型。但是工程实践中,采用RNG k-ε湍流模型也能满足精度要求。油滴颗粒相选用DPM模型。求解方法是油滴跟随气体运动,根据受力平衡求解油滴的运动轨迹。
RNG k-ε湍流模型湍动能和耗散率方程[15]为:
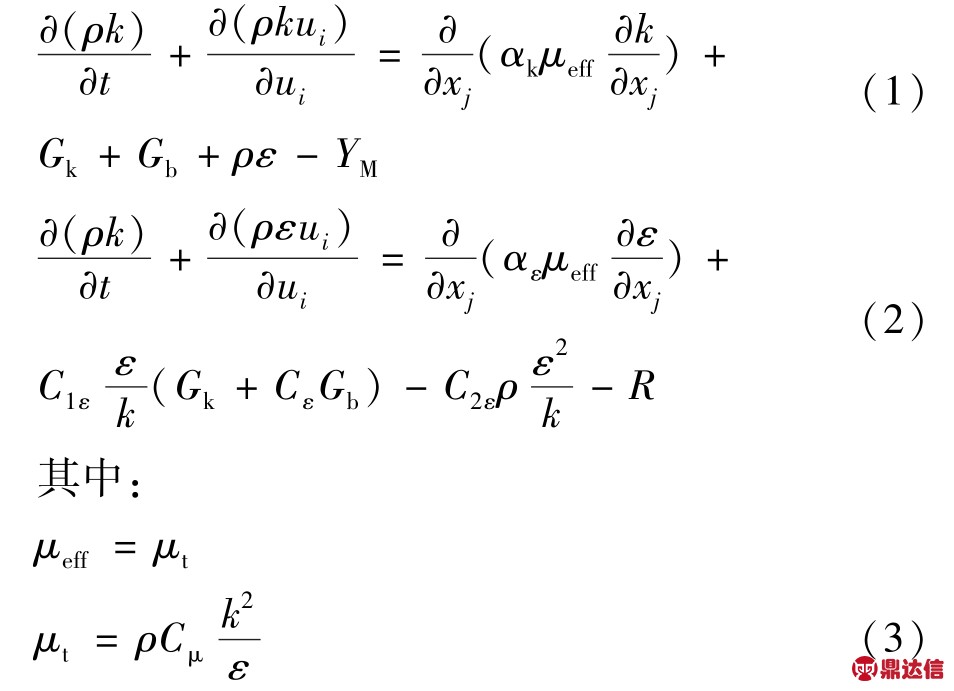
式中:Gk为由平均速度提梯度引起的湍动能;Gb为由浮力影响引起的湍动能;YM为可压缩湍流脉动膨胀对总耗散率的影响;αε、αk分别为湍动能和耗散率的有效普朗特数的倒数。
采用随机轨道的模型对油分离器内部的离散相颗粒进行追踪,在拉格朗日坐标系下,颗粒在气流中的受力方程[15]为:

式中:u为流体的相速度,m/s;up为颗粒速度,m/s;FD为拽力,N;CD为拽力系数;μ为流体的动力黏度,Pa·s;ρ为流体密度;ρp为颗粒密度,kg/m3。
2.2 边界条件
采用velocity-inlet为入口边界条件,outflow为出口边界条件。腔体内部wall的DPM类型选择为trap格式。湍流强度和水力直径湍流边界。压力速度耦合方程采用SIMLPEC方程,离散格式采用QUICK格式。
采用单螺杆压缩机HSS4223,压缩机名义排量为722 m3/h,制冷剂为R407C,排气压力为2140 kPa,排气温度为80℃,制冷剂密度为80 kg/m3,黏度为1.91 ×10-5Pa·s。润滑油为RL68H,密度为912 kg/m3。
2.2.1 制冷剂速度
计算排气口体积流量Vd,即油分离器入口体积流量,从而得到入口速度:
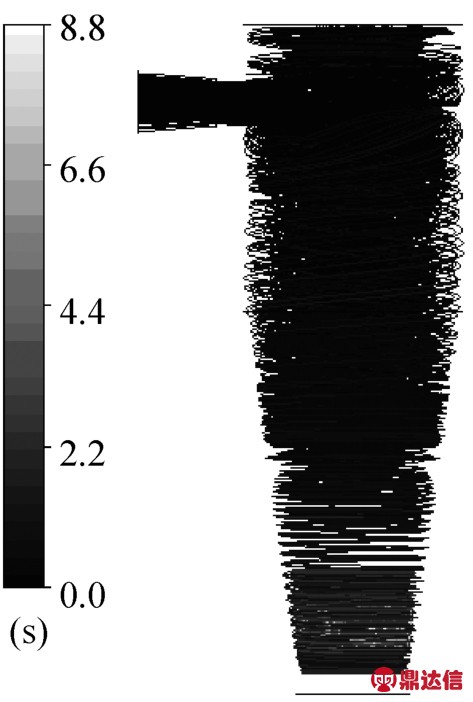
式中:Vs为吸气口理论体积流量,也是压缩机理论排气量,m3/h;η为容积效率;vs为吸气比容,m3/kg;vd为排气比容,m3/kg。
根据空调的不同的负荷,计算油分离器入口速度,其中最小流速为 3.2 m/s,名义制冷流速为9 m/s。湍流强度为10%,水力直径为0.09 m。
2.2.2 油循环量
计算油循环量的公式:

式中:C为流量系数一般为0.8~0.9;A为回油管面积,m2;ρp为润滑油密度,kg/m3;ps为吸气压力,kPa;pd为排气压力,kPa。
2.2.3 油滴颗粒分布
李红旗等[16]根据小波动理论和相似原理得到油滴的分布函数和最大直径的计算式:
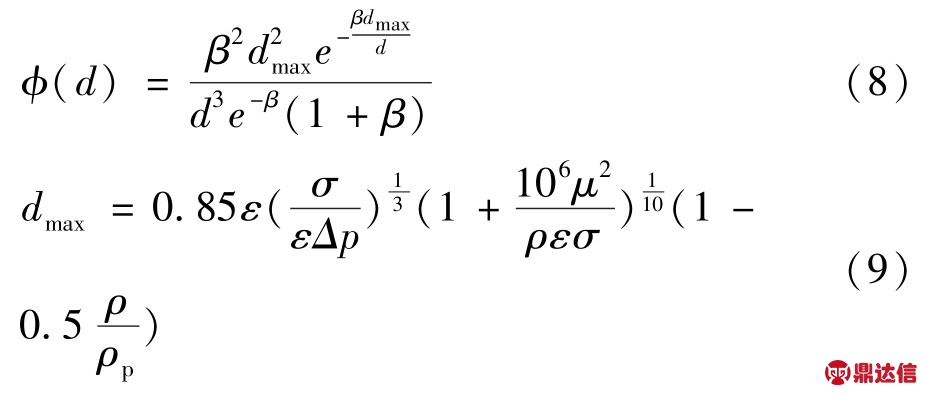
式中;φ(d)为油滴颗粒直径为d的概率;dmax为最大液滴直径,m;β为分布函数参数,由实验确定;ε为喷口处液膜厚度,m;Δp为油分离器压力损失,kPa;σ为液体的表面张力,N/m;ρ为气态制冷剂密度,kg/m3。
当油从排气管喷入油分离器,并与壁面碰撞时,油滴颗粒部分会被吸附、碰撞、反射,并且考虑到油滴颗粒与油膜厚度、表面张力和黏度有关,本文采用第二种分布函数法来描述油滴颗粒粒径分布。计算分布函数参数β时,需要根据实验数据和经验来调整。
为了简化计算,选择粒径分别为1×10-6~1× 10-5m每隔1×10-6m取一个值,2×10-5m、3× 10-5m和1×10-4m的油滴颗粒进行计算。
2.3 网格设置
将设计好的三维导入到模型处理软件DM中进行合理的切面,再导入到网格处理软件Meshing中划分网格。与入口段相连接的腔体为四面体网格,其他部分为五面体或六面体网格。网格数量为65万,网格如图3所示。
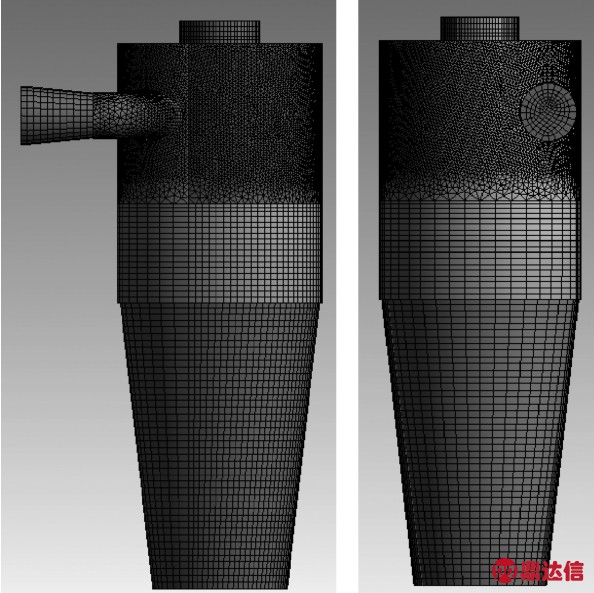
图3 油分离器网格
Fig.3 The mesh of oil separator
为了验证网格数量与计算结果之间无关联性,选取名义工况下油分离器压力损失和颗粒直径为3 ×10-6m油滴颗粒分离效率进行网格独立性验证。计算结果见表1所示,随着网格数量增加,分离效率和压力损失误差偏离很小,认为满足网格独立性要求。
表1 网格独立性验证
Tab.1 Grid independent validation
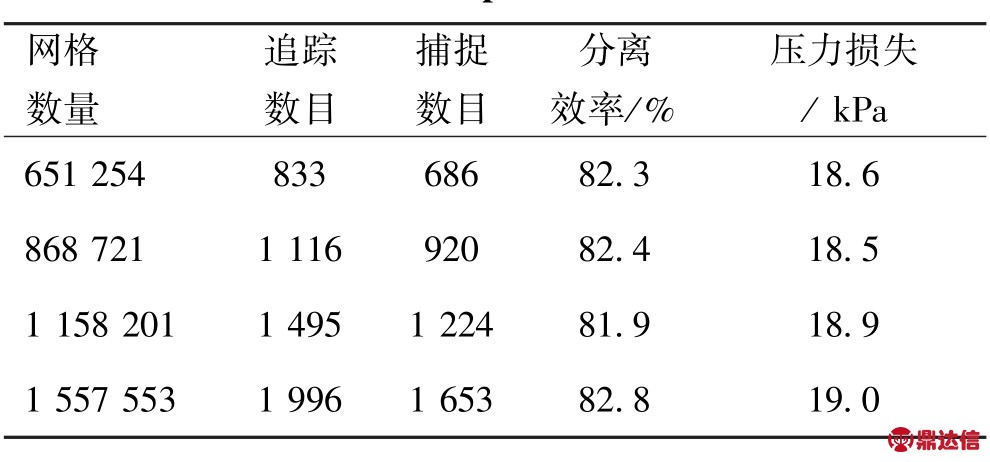
2.4 计算结果
将计算好的边界条件输入到求解器,初始化并求解。在已知入口管直径 di、出口管直径 do情况下,通过参数化设计比较不同油分离器筒体直径D、内筒体直径de、筒体长度H、锥体长度Hc以及锥体角度下最优分离效率和压力损失,得到最优结果如表2所示。
根据表2得到的规律,设计新型油分离器结构,其制冷剂运行轨迹如图4所示。从图可以看出,制冷剂流线比较流畅规则且布满整个油分离器空间,说明压力损失较小,分离时间充分。
表2 油分离器最佳尺寸比例
Tab.2 Optim um size ratio of oil separator
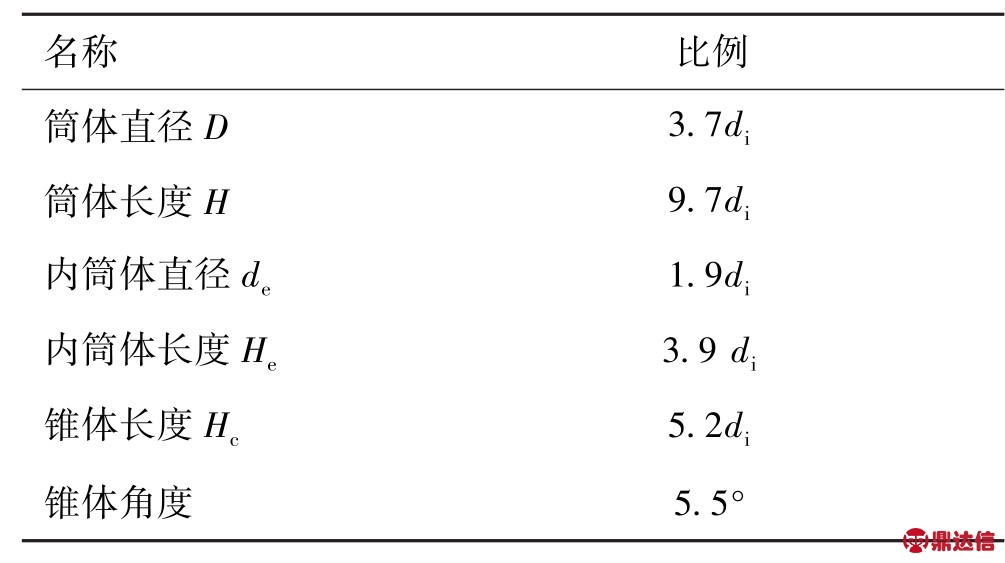
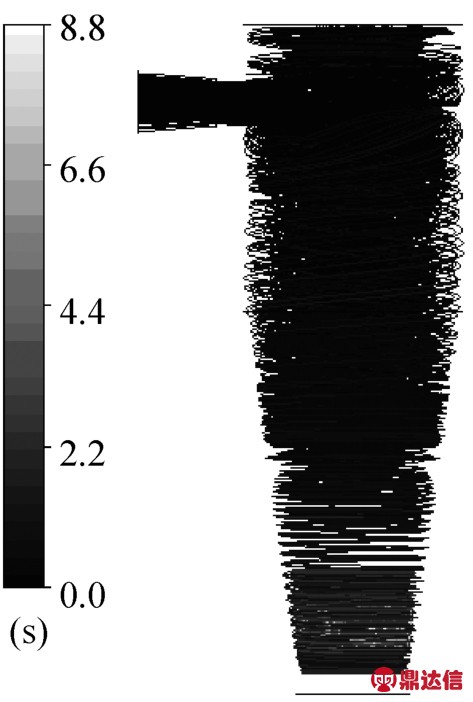
图4 制冷剂运行轨迹
Fig.4 The stream line of refrigerant
2.4.1 压力损失和速度分布
制冷剂速度为9.0 m/s时,速度和压力分布如图5所示。经过锥体的加速,最大速度达21.2 m/s。计算压力损失为18.6 kPa。
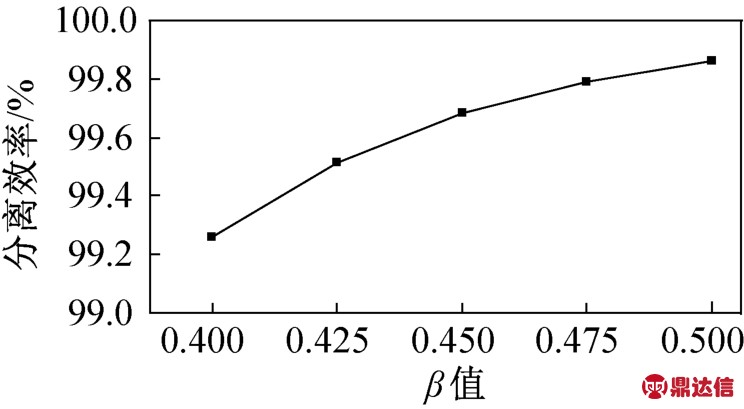
图5 速度和压力云图
Fig.5 The contours of velocity and pressure
2.4.2 油滴轨迹与停留时间
制冷剂速度为3.2 m/s时,不同直径的油滴运行轨迹如图6所示。由于直径越大,油滴越容易被分离。所以随着直径的变大,油滴会越来越早被分离出来,油滴与制冷剂的分离时间从粒径为1×10-6m的8.02 s降低到1×10-4m的0.31 s。
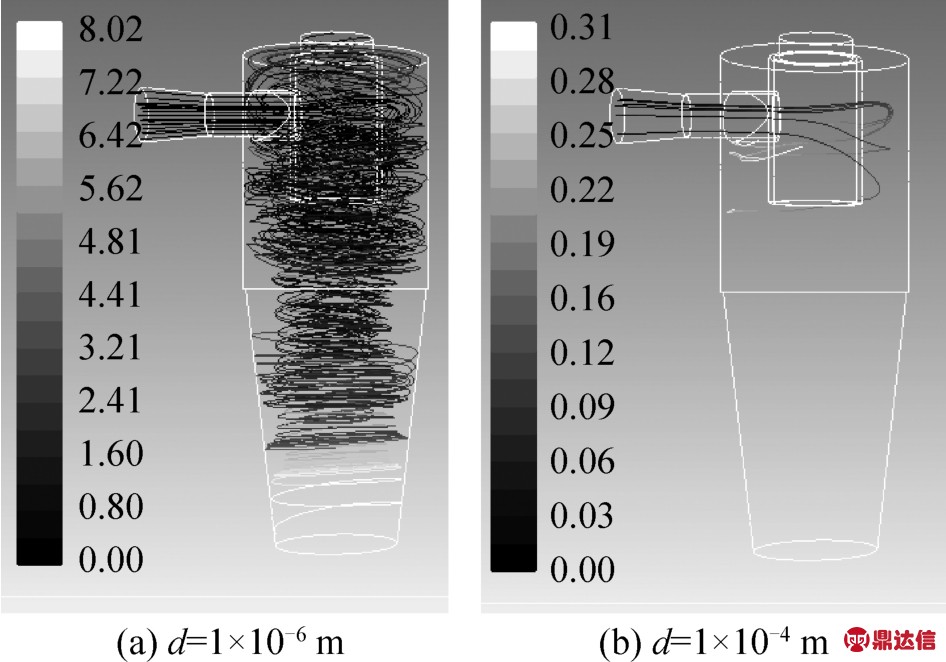
图6 不同粒径油滴颗粒轨迹与停留时间(s)
Fig.6 The path line and residence time of different diameter oil-particle(s)
2.4.3 分离效率
通过Fluent中的颗粒跟踪,可以获得总追踪颗粒数目、捕捉到的颗粒数目和逃逸的颗粒数目。不同粒径的分离效率见表3和表4所示。总的分离效率=∑单个粒径分离效率×分布函数的比例。计算得到 3.2 m/s和9 m/s的分离效率分别是98.97%和99.68%。
表3 不同粒径油滴的分离效率(入口速度3.2 m/s)
Tab.3 The separation efficiency of different diameter oil-particle(inlet velocity:3.2 m/s)
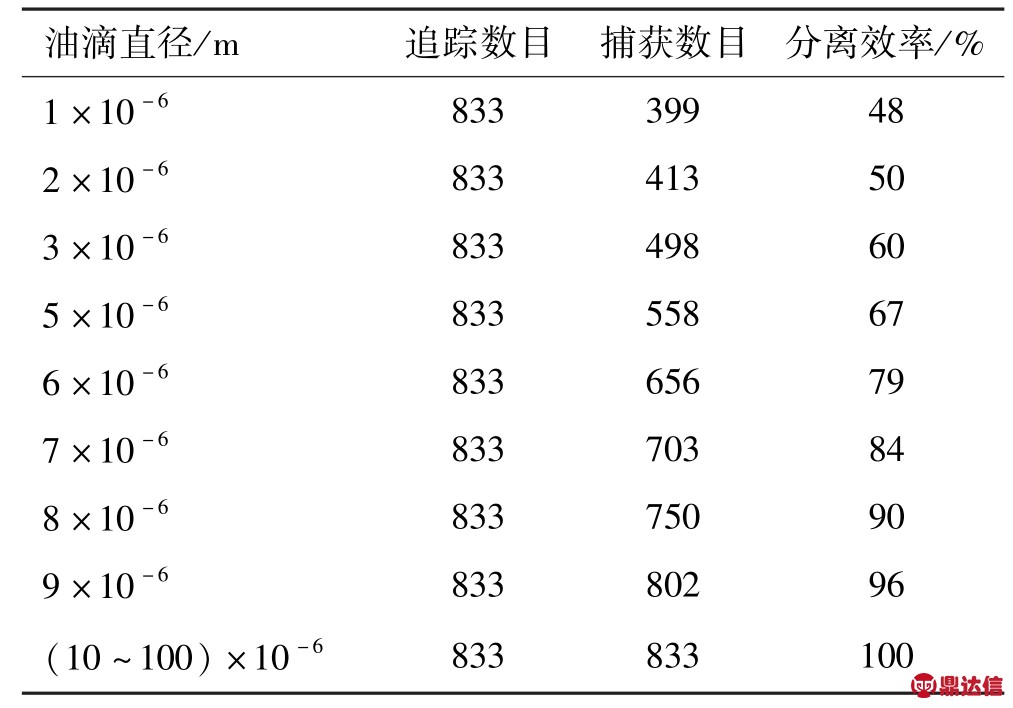
表4 不同粒径油滴的分离效率(入口速度9.0 m/s)
Tab.4 The separation efficiency of different diameter oil-particle(inlet velocity:9.0 m/s)

3 实验结果与分析
为了对优化的油分离器进行实验验证,将油分离器安装在空调系统上并进行测试。图7所示为空调系统示意图,从压缩机出来的油气混合物经过油分离器进行分离,分离出来的润滑油经过回油管道回到压缩机吸气口,制冷剂气体继续循环。
秦泗河教授曾主编《外固定与足踝重建》专著,由人民卫生出版社2015年出版。近年在足踝畸形矫正与功能重建领域又取得重大进展,引起国际学术界的关注。自中国骨科医师分会外固定与肢体重建委员会(CEFS)成立以来,主任委员秦泗河教授及其团队,已成功举办十六期外固定与肢体重建培训班,因其优良的教学品质,被学员誉为“黄埔培训班”。至今,秦泗河矫形外科已经接收了290余名培训班学员、100余名国内进修医师、8名国外进修医师,积累了丰富的教学经验,培养了一大批外固定(Ilizarov技术)与肢体重建专家。
在名义制冷工况风冷侧干球温度35℃,出水水温7℃[17]及含油量测试工况干球温度44℃,出水温度4℃工况下(25%负荷)测试油分离器的分离效率和压力损失。
3.1.1 分离效率测试方法
根据国家标准GB/T 5773—2004附录A的含油量测试方法[18],涂虬等[19]分离效率的测试方法,并结合实验室数据,得到测试步骤如下:
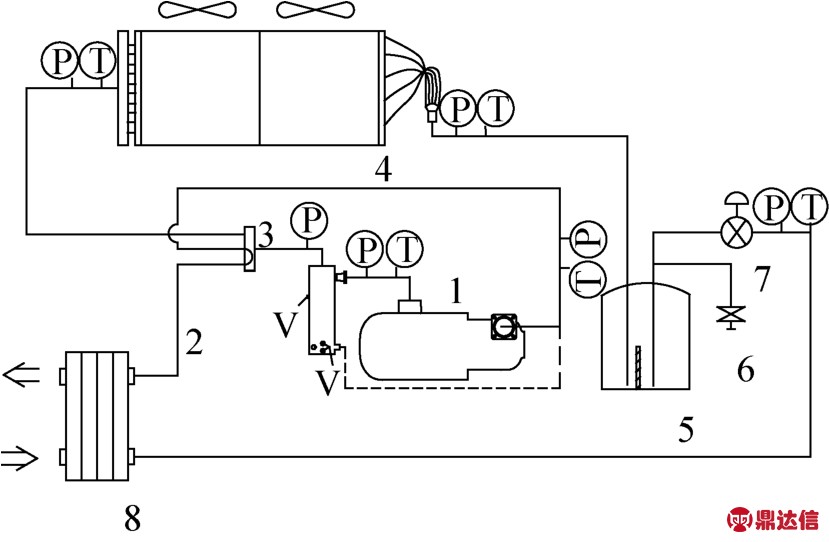
图7 空调装置示意图
Fig.7 Schematic diagram of air-conditioning
1压缩机;2油分离器;3四通阀;4冷凝器;5储液器;6油气混合物取样口;7电子膨胀阀;8蒸发器;P压力测点;T温度测点;V视油镜
1)把三个取样容器抽真空,并持续10 min,之后称重取平均值,记为g1。
2)空调系统稳定运行1 h后,每隔15 min将取样容器与制冷剂管道(储液器与电子膨胀阀之间)相连,抽取油气混合物样品,将三个取样容器称重取平均值,记为g2。
3)将容器口的密封盖拧开一个小口,让气态制冷剂缓慢放出来,同时需要确保无油被带出来。放完后,称重取平均值,记为g3。
4)油分离器效率为[1-(g3-g1-ρgV1)/(g3-g2)],其中ρg为称重时大气压和环境温度下的制冷剂密度,g/L,V1为取样容器容积,L。
3.1.2 压力测试方法
在油分离器入口和出口处增加压力取点。记录稳定运行2 h后的数据,其中压力损失Δp为入口压力p1与出口压力p2之差。
3.2 分离效率实验结果
3.2.1 分离效率测试结果
本次实验制冷剂充注量为120 kg,润滑油充注量为17 L。测试油分离器分离效率数据见表5。
表5 不同状态下取样容器的称重数据
Tab.5 Testing data of the sam pled container under different conditions
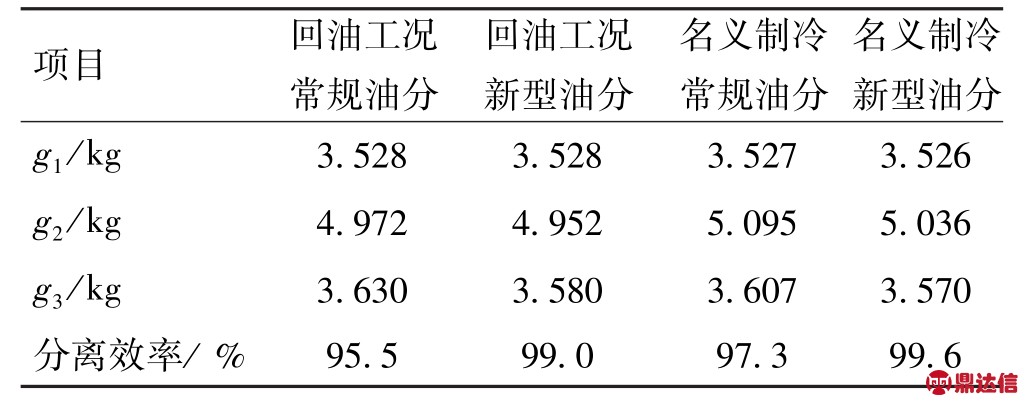
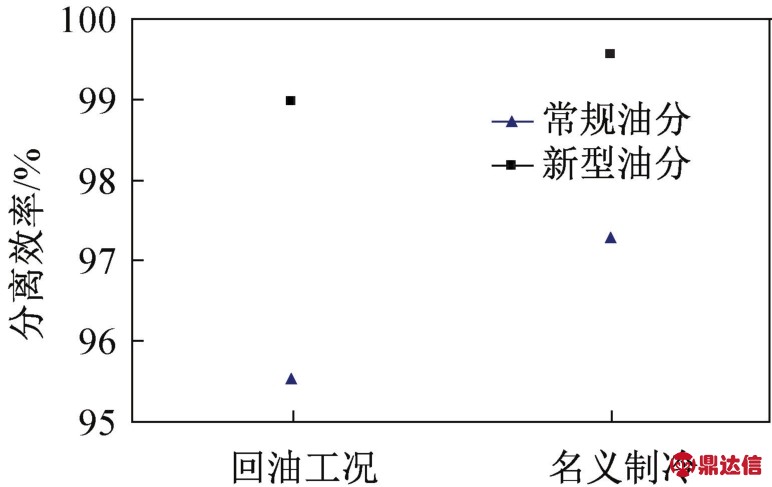
图8 不同工况下常规和新型油分离器的分离效率
Fig.8 The separation efficiency of convectional and new oil separator on different load
由表5可知,常规油分离器分离效率在名义制冷和回油工况下分别为95.5%和97.3%,新油分离器则分别提高至99.0%和99.6%,分别提高了3.5%和2.3%。
由图8可知,新型油分离器分离效率在两个工况下均要高于常规油分离器,且回油工况下,提升更加明显。
3.2.2 油滴颗粒分布函数的确定
喷口处液膜厚度ε取0.002 m,实测压力损失为23.1 Pa,润滑油表面张力σ为0.02 N/m。计算得dmax为1.33×10-4m。
通过假设不同的β值,来获得不同粒径油滴颗粒的分布概率,分离效率计算公式如下:

式中:η为总分离效率;η(d)为直径为d的分离效率,其值为Fluent中直径为d的油滴颗粒捕捉数目/追踪数目。
其中β∈[0.4~0.5]的分离效率如图9所示。根据测试数据,名义工况分离效率为99.6%,实验值与计算值的偏差见表6所示,β为0.45最接近,因此本空调系统β取值0.45。得到其颗粒分布函数曲线见图10。同样可以计算出3.2 m/s情况下 β为0.275,dmax为2.25×10-4m。
表6 实验与仿真结果比较
Tab.6 Comparison between experimental and CFD simulation


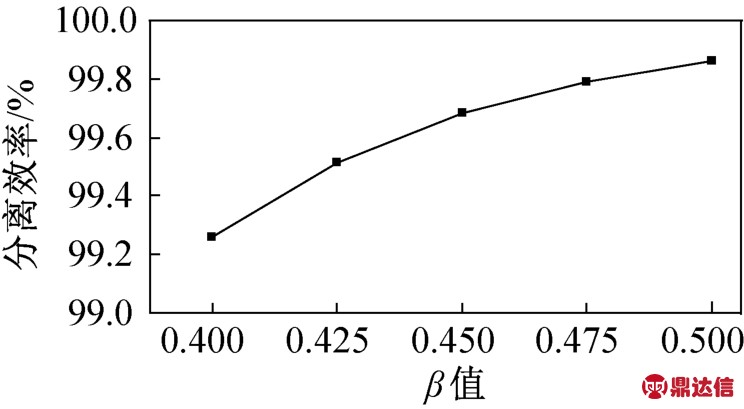
图9 不同β值下的分离效率
Fig.9 The separation efficiency with different β value
3.3 压力损失实验结果
工况稳定后开机,系统运行稳定1 h后,记录35 min内油分离器入口和出口压力平均值。得到实验结果如表7所示。由表7可知,常规油分离器压力损失在名义制冷和回油工况下分别为55.2 kPa和7.4 kPa,新油分离器则分别降低至23.1 kPa和4.2 kPa,分别降低了58.2%和43.2%。
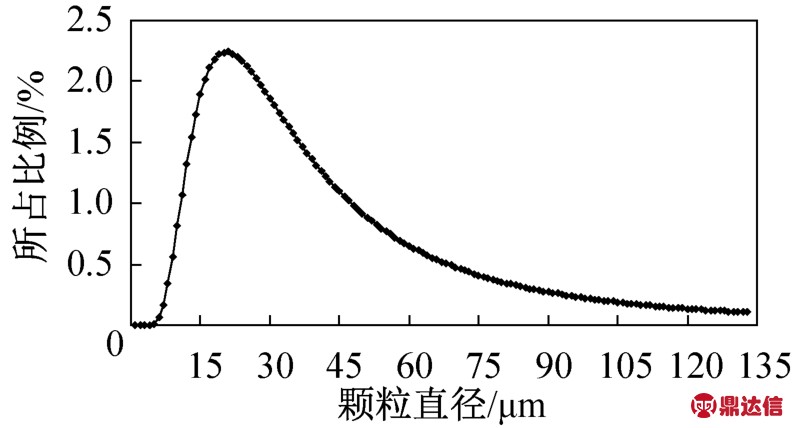
图10 油滴颗粒分布函数曲线(dmax=1.33×10-4m,β=0.45)
Fig.10 The distribution function curve of oil-particle
表7 不同负荷下常规和新型油分离器压力损失Tab.7 The pressure loss of convectional and new oil separator on different load

图11所示为不同工况下常规和新型油分离器的压力损失计算值与实验值对比。从图中可知,计算值与实验值符合较好,误差在20%以内,且实验值均大于计算值。随着速度增大,误差在增大。计算值与实验值误差产生原因是由于筒体壁面设置为trap类型,而实际运动过程中会有油滴碰撞筒体内壁产生压力损失,且速度越大,碰撞越剧烈,压力损失也更大。
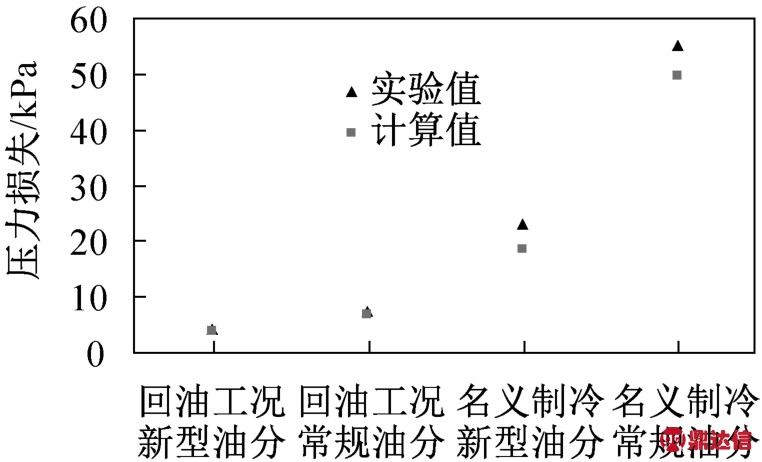
图11 不同工况下常规和新型油分离器的压力损失
Fig.11 Pressure-loss com parison between convectional and new oil separator on different load
4 结论
本文对空调旋流油分离器进行内部流场仿真,获得油滴颗粒分布函数β值确定方法,通过参数化设计获得最佳油分离器尺寸比例,并通过实验验证优化结果,得出以下结论:
1)通过实验获得本空调系统名义工况油分离器入口油滴颗粒最大直径和颗粒直径的分布函数。
2)通过流体仿真得到油分离器内部流场,获得最佳的尺寸比例名称,如筒体直径D为3.7di,筒体长度H为9.7di,内筒体直径de为1.9di等,其中di为油分离器入口管管径。
3)根据流体仿真获得内部流体规律设计出的新型高效旋流油分离器,并将油分离器安装在空调系统上测试,新型油分离器在回油工况(最低制冷剂流速)下分离效率由95.5%提高至99.0%,名义制冷工况下由97.3%提高至99.6%,名义制冷工况下压力损失由55.2 kPa降低至23.1 kPa。