摘要:本文将主要介绍在我国应用的动静态旋转分离器的技术发展。
关键词:中速磨煤机;动静态旋转分离器;技术发展
1 动静态旋转分离器的选择及其优点
在中速磨煤机直吹式制粉系统中,中速磨煤机的分离器是否选用动静态旋转分离器,主要取决于锅炉燃烧要求的煤粉细度R90。通常情况下,原煤的煤粉细度R90主要与原煤的干燥无灰基挥发分Vdaf有关,即R90=0.5nVdaf;
式中:Vdaf为煤粉在90μm筛孔筛子筛上余量占煤粉总量的百分比%;
n为煤粉的均匀性系数,一般情况下,配离心式静态分离器时,n=1.0~1.1,配旋转动态分离器时,n=1.1~1.2;
Vdaf为原煤的干燥无灰基挥发分,%;
当锅炉燃烧要求的煤粉细度R90小于12%,建议选用动静态旋转分离器。由于动静态旋转分离器含有静叶轮和旋转叶轮两级对煤粉的细度分离,不仅能提供较细的煤粉,同时由于动静态旋转分离器的旋转叶轮由于自身的旋转,可提供较强的气流旋转力度,在动态分离器出口的煤粉均匀分配比较好,煤粉均匀性指数较高,可以有效改善锅炉炉膛的燃烧,从而提高锅炉的燃烧效率。
动静态旋转分离器仅需通过调整变频器的频率,从而使变频电机得到不同的输出转速,进而调整旋转叶轮的转速,从而可以得到不同细度要求的煤粉。因此,动静态旋转分离器对煤粉细度的调整更加方便,仅可通过改变变频器的参数即可实现,也不像静态分离器那样,需要人员爬上静态分离器的顶部,通过人力调整叶片操纵装置而改变静态分离器的叶片的角度,从而实现对煤粉的细度调整。
采用静叶轮和旋转叶轮的动静态旋转分离器,提高了一次热风对煤粉的携带能力,提高了分离器对煤粉的分离效率,减少了合格的煤粉被降落至碾磨区域重新碾磨,降低了磨煤机内部煤粉的循环倍率。因此,通常情况下在煤粉细度R90<25%时,动静态旋转分离器有助于提高磨煤机的出力。
因此,正是由于动静态分离器的应用有诸多的好处,在燃煤火力发电机组中得到了较为广泛的应用,特别是我国国内的大部分1000MW级燃煤火力发电机组,选用的原煤均不是褐煤,因此一般都要求选用动静态分离器,以提高锅炉的燃烧效率。
动静态旋转分离器在我国的应用先后经历了两代技术,第一代是采用变频电机、通过齿轮传动方式的动静态旋转分离器,第二代是采用变频电机、皮带传动方式的动静态旋转分离器。
2 第一代采用齿轮传动方式的动静态旋转分离器
第一代采用齿轮传动方式的动静态旋转分离器,其主要结构见图1,包括驱动部分、分配器、分离器壳体、静叶片、旋转叶片等部分组成,其中驱动装置中包括变频电机、驱动座(分别包括上部驱动座和下部驱动座)、小齿轮、大齿轮、旋转轴架、防尘密封圈、落煤管和齿轮油组成。
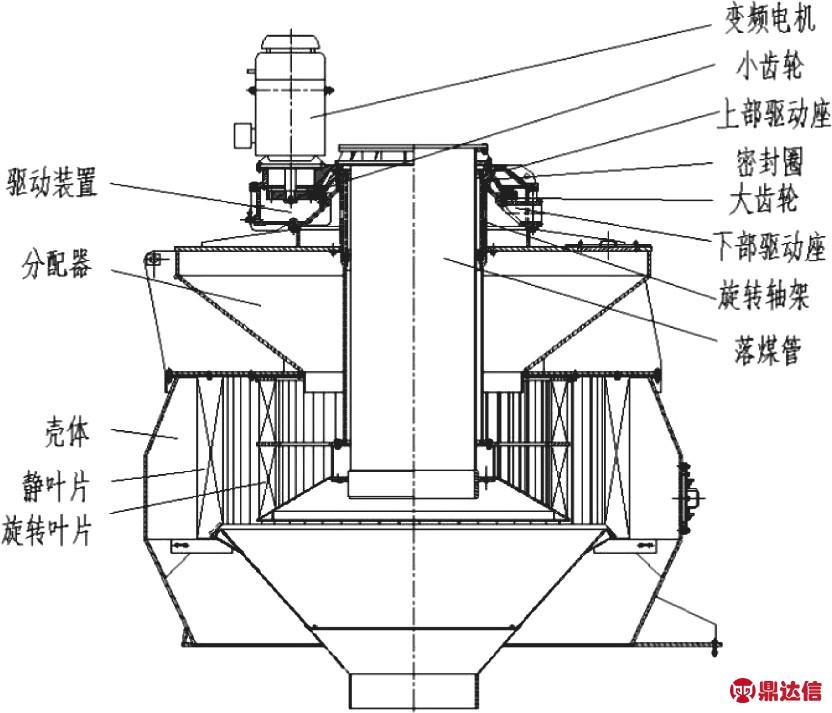
图1 第一代动静态分离器结构图
齿轮传动是机械传动中应用最广泛的一种传动方式,具有齿轮传动平稳,传动比精确,结构紧凑、传动效率高、寿命长,工作可靠等方面的优点。但也有制造和安装精度要求较高,价格昂贵,精度低时,振动和噪声较大,不宜用于轴间距离大的传动。
从结构上看,采用齿轮传动方式的动静态旋转分离器是由变频电机带动小齿轮、大齿轮旋转,大齿轮带动旋转轴架旋转,进而带动旋转叶片旋转,再通过变频电机的变频调速最终实现分离器旋转叶片转速的调整。第一代齿轮传动的动静态分离器首先通过一对直径大小不等的啮合的齿轮来首次实现输出转速的降低的。在动静态分离器的第一代产品中应用的齿轮传动方式突出体现了传动比精确、结构紧凑、工作效率高、寿命长、工作可靠等齿轮传动的优点。因此第一代动静态分离器自诞生以来,齿轮传动方式被人们接受并认可,第一代动静态分离器也得到了广泛的应用。
从生产制造上看,由于第一代的动静态旋转分离器采用齿轮传动方式,其结构组成中含有驱动座,且上部驱动座和下部驱动座均为铸造件,而且需要一对直径大小不一的齿轮,因此在生产制造中所需的成本较高。同时,为了防止驱动装置中的轴承所在区域进入煤粉,驱动装置中的旋转轴架上下两面各含有一套结构近似VD形橡胶密封圈的防尘密封圈,在轴向方向产生形变,旋转轴架的上下两个部件驱动座均为不旋转部件,因此在分离器运行的过程中增加了旋转叶片转动的阻力,使得旋转叶片被驱动非常困难,需要的变频电机的功率也较大,以避免变频电机出现过载现象。
因此,第一代的动静态旋转分离器的设备本体重量较重、旋转叶轮转动的阻尼力也较大,设备成本也较高,在应用了一段时间后,人们开始探索其他传动方式的动静态分离器的技术。
3 第二代采用皮带传动方式的动静态旋转分离器
在机械设计中,皮带传动也是应用较为广泛的一种传动方式。皮带传动的优点有结构简单,传动平稳无噪声、能缓冲、吸振,过载时带将会在带轮上打滑,可防止薄弱零部件损坏,起到安全保护作用。正是由于皮带传动的诸多优点,因此,设计师开发了皮带传动的第二代动静态旋转分离器。
第二代采用皮带传动方式的动静态旋转分离器主要结构见图2,包括驱动部分、分配器、分离器壳体、静叶片、旋转叶片等部分组成,与第一代齿轮传动方式的动静态旋转分离器的不同是,第二代皮带转动方式的动静态旋转分离器的驱动装置中包括变频电机、皮带、大皮带轮、小皮带轮、轴承座I和轴承座II、深沟球轴承、防尘密封圈、密封环和落煤管等组成,取消了驱动座,降低了驱动装置的重量,同时将VD形橡胶密封圈的防尘密封圈改为唇形密封圈,极大地降低了密封圈的旋转阻力,使旋转叶片轻松实现了旋转。
从结构上看,第二代采用皮带传动方式的动静态旋转分离器,是由变频电机带动小皮带轮、大皮带轮转动,进而带动轴承座I以带动旋转叶片的转动,再通过变频电机的变频调速最终实现分离器旋转叶片转速的调整,再通过变频电机的变频调速最终实现分离器旋转叶片转速的调整。
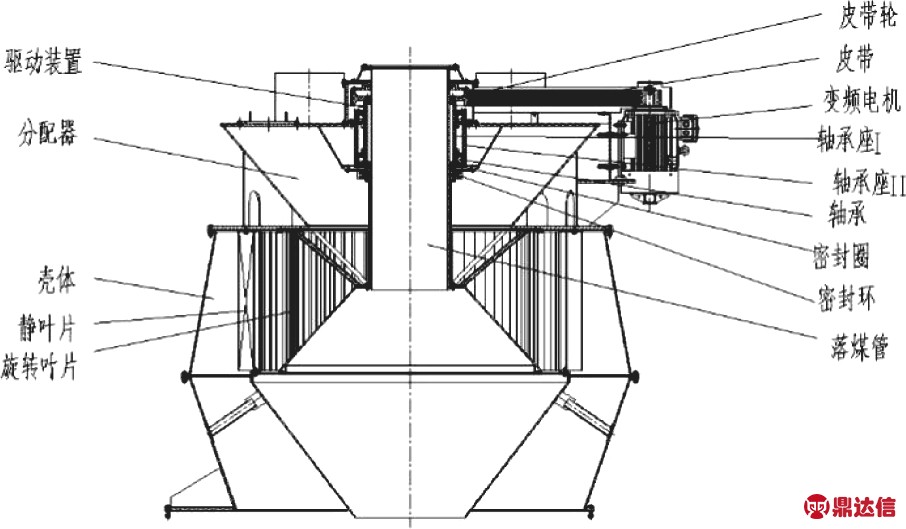
图2 第二代动静态分离器结构图
从生产制造上看,由于第二代的动静态旋转分离器采用皮带传动方式,其驱动结构得到了简化,生产制造也更加容易实现,降低了生产制造成本,同时,取消了相对尺寸和重量较大的驱动座,节省了恒产制造成本,设备安装更加容易,检修维护更加方便,避免了第一代齿轮传动的动静态旋转分离器易漏齿轮油的弊端,其润滑系统采用脂润滑系统,根据设计的流量定时将油脂注入到轴承的部位即可。
目前,国外部分动静态分离器制造厂家已经采用了皮带传动的传动方式,替代了齿轮传动的方式。中国电建集团长春发电设备有限公司作为国内专业设计、生产制造MPS-HPII型中速磨煤机的唯一厂家,MPS-HP-II型中速磨煤机是MPS型中速磨煤机的最新、技术最先进的产品,该公司在几年前就已经自主研发了采用皮带传动方式的第二代动静态旋转分离器,并随着MPS-HP-II型中速磨煤机产品广泛应用于国内外的燃煤火力发电厂、钢铁冶炼厂和化工厂等行业,为用户提供了技术先进、性能优良、安全可靠的MPS-HP-II型中速磨煤机及第二代动静态旋转分离器产品。
为了提高磨煤机的煤粉均匀性系数,进而提高锅炉的燃烧效率,虽然燃用褐煤项目要求的煤粉细度较大,一般要求的煤粉细度R90为30%~35%,但已经有部分的褐煤项目的用户选用了动静态旋转分离器,可见动静态旋转分离器的应用已经被进一步的推广。
4 结论
动静态旋转分离器作为中速磨煤机的重要组成部分,动静态旋转分离器的优点已经在实际应用中得到了验证,并被广大设计院、用户所认可。同样,作为专业设计、生产制造MPS-HP-II型中速磨煤机的厂家,中国电建集团长春发电设备有限公司也一直在动静态旋转分离器产品的应用中进一步改进其结构,使其结构更合理、设备性能更加优良,为提高我国中速磨煤机产品的技术水平而努力。