摘 要:针对双进双出分离器分离效率低的问题,开展了数值分析、理论计算、机构优化和工程性分析等研究过程,从而建立了仿真动力学模型,获取了双进双出分离器内的流场分布、压降特性和颗粒运动形态,对分离器的结构进行了优化。研究结果表明,双进双出粗粉分离器经过结构优化改进后,分离器压降阻力大幅度降低,明显提高了制粉系统的出力、分离效率、分级效果、细度分离效果和均匀性指数。
关键词:粗粉分离器;数值模拟;优化
0 引言
粗粉分离器是煤粉火力发电厂双进双出直吹式、中间仓储式和中速磨直吹式等制粉系统中的关键设备,其分离能力将影响制粉系统寿命、耗能及燃烧炉性能。轴向粗粉分离器具有分离效率高、易于调节和循环倍率低等优点。虽然此分离器已有成功实例[1-2],但其内部流动特征有待于进一步研究,计算流体力学(CFD)模拟可以为其内部流体力学特征提供合理预测,并为其优化和放大提供了有力的理论支持[3]。以某电厂2号磨11号制粉系统中粗粉分离器优化为例,对分离器改进前进行分析,利用MFM方法和DPM方法模拟了此粗粉分离器,直观地展现CFD在轴向粗粉分离设计的作用[4-5];通过理论分析后,对现有结构进行了改进,使离心力在分离器中的作用更加明显,分离效率更高;分离器数值模拟中的欧拉-拉格朗日方法可以跟踪颗粒的运行轨迹,比较典型的包括离散元模型(DEM)和离散颗粒模型(DPM)[6-7]。为了深入研究双进双出粗粉分离器设备的分离机理,本文对双进双出粗粉分离器旳三维气固两相流的速度、压力等进行了数值模拟,得到分离器内的气体流动规律;采用离散相模型模拟了分离器内典型颗粒的运动轨迹,对分离器的结构进行了优化,并将优化前后的粗粉分离器相关特性进行比较,得出双进双出粗粉分离器的最佳结构形式,达到了提高分离效率的目的,该优化结构为同类型分离器改造提供了技术基础。
1 计算模型与数值方法
为了分析粗粉分离器性能和效果,本文将采用CFD模拟进行说明。粗粉分离器中流动结构属于气固两相,气体为空气,颗粒为煤粉,研究所用模型主要是离散颗粒方法和多流体模型,其中离散颗粒方法认为气体作为连续相,颗粒采用离散相,即Fluent离散相模型(DPM模型)。
连续性方程为
▽·(εgρgug)=0
(1)
式中:空隙率εg=1(若单相计算)。
动量方程为
▽·(εgρgug)=μeffεg[▽ug+
(▽ug)T]-εg▽p+Mg,l+ρgεgg
(2)
颗粒相采用牛顿第二定理,方程为
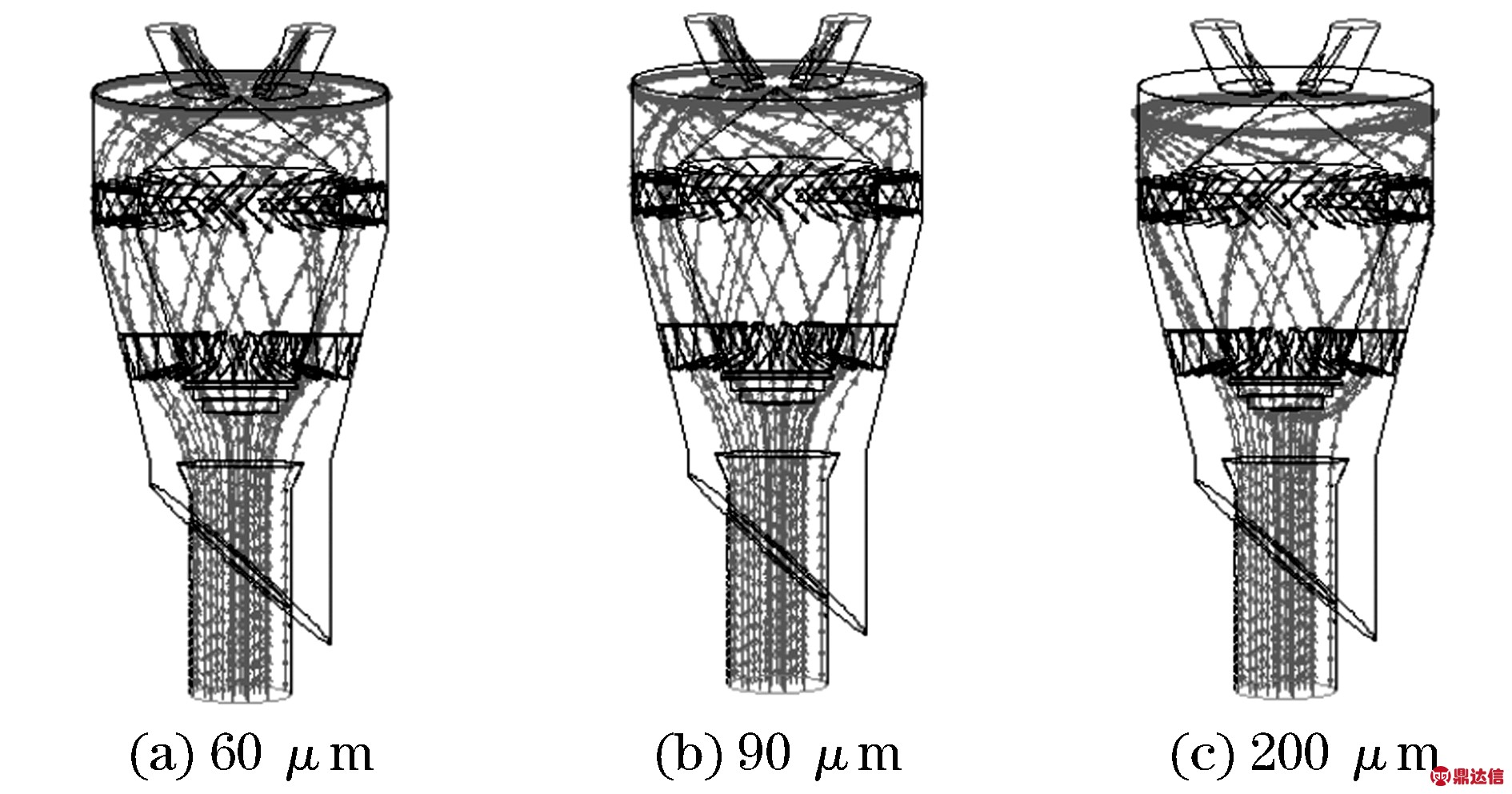
(3)
具体方程形式为

(4)

(5)

(6)
式中:p为颗粒;g为气相;为速度波动相。
τ为颗粒的弛豫时间。
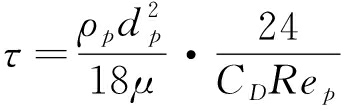
(7)
式中:Rep为颗粒的雷诺数;CD为曳力系数,为常数,由Morsi[8]和Alexander[9]针对低浓度颗粒提出。
由于颗粒体积浓度为0.000 5,低于10-3,颗粒间碰撞可以忽略。气体和颗粒间作用力主要包括曳力、升力、虚拟质量力等,其中曳力是主要的力,升力和虚拟质量力被忽略。
由于粗粉分离器内流体速度比较大且含有明显的切向速度,整个流场处于湍动状态,模型中将采用RSM湍流模型,模型形式[10]为

(8)
模型中的参数是Fluent的默认值,若采用多流体模型计算,则颗粒相应力采用颗粒动理学理论,气固间曳力采用Wen&Yu方程[11]。
计算模拟平台基于ANSYS12.1软件,采用多面体网格和四面体网格为主,网格数256万个,如图1所示。
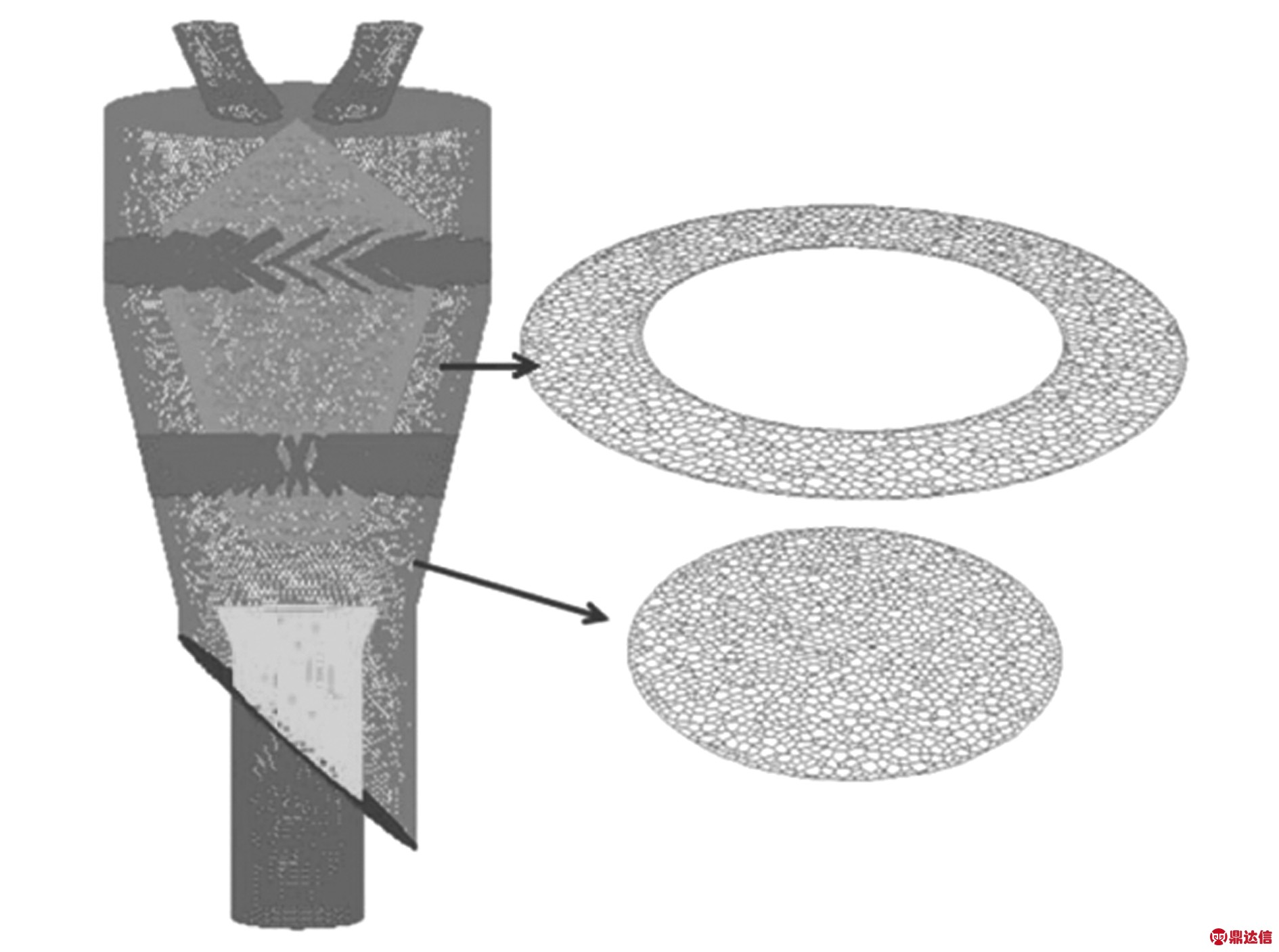
图1 模型构图及其网格划分
Fig.1 Model composition and its grid partition
边界条件:压力出口,速度入口,气体采用无滑移壁面,颗粒出口采用逃逸边界,壁面为弹性碰撞,气体稳态计算流场为初始条件,操作条件和操作物性如表1所示。
2 数值模拟计算结果与分析
2.1 优化前的分离器数值模拟结果
当上挡板开度和下挡板开度分别为30°和70°时,进口气速分别为12 m/s、16 m/s和20 m/s的整个流场静压分布如图2所示。从图2可以看出,不同位置静压分布的高低值基本保持一致,静压最大值出现在撞击锥和内外锥间隙部分, 可见撞击锥导致了压力增加现象。因为内外锥间隙内速度较高,所以压降也相应增加,顶盖附近压降出现了边沿大中间逐渐变小的情况,主要原因是由上挡板引起较大的切向速度和径向速度。其中图2(a)表明内外锥间和撞击锥的压力达到了1 710 Pa,整个流场的压降值约为1 492 Pa,出口管顶部和下部压降为700 Pa 左右,这说明出口带来的压降所占的比重比较大,这主要是缩颈造成的,说明出口的设计对压降阻力影响很大。
表1 物性和操作参数
Table 1 Physical properties and operating parameters

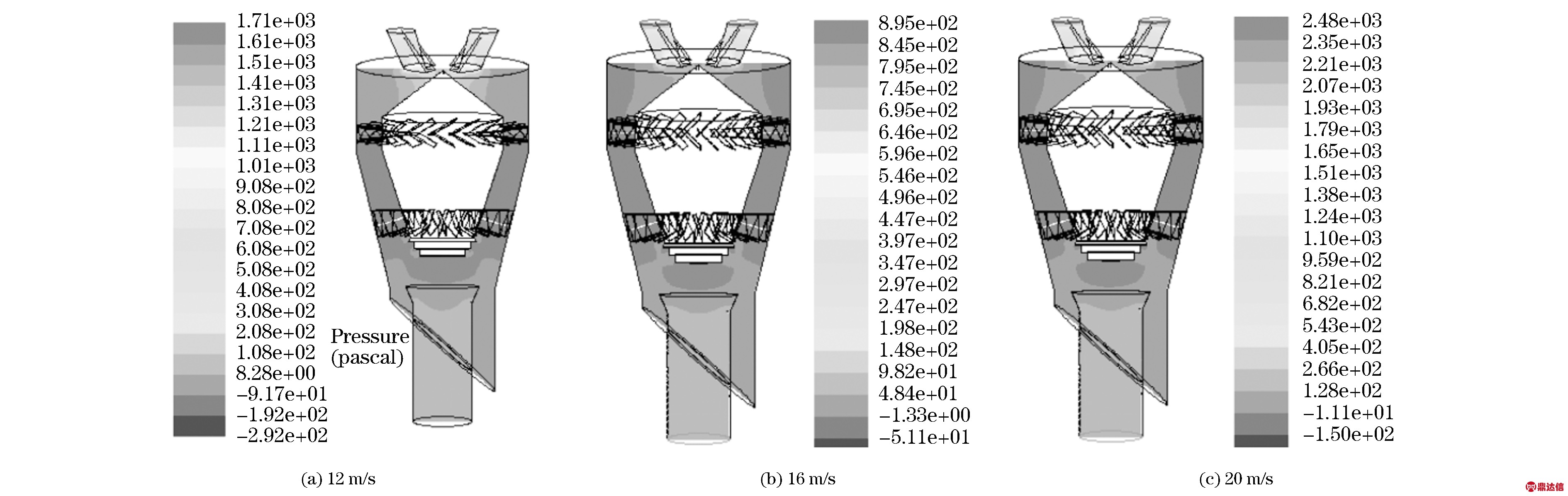
图2 整个流场的静压分布
Fig.2 Static pressure distribution of whole flow field
气体速度变化情况如图3所示。从图3可以看出,速度不同时的流型是相同的,不同的是速度值。气体速度下不同粒径颗粒的流线如图3所示。
从图3(a)可以看出,随着粒径的增加分离器出口数量减少,到达200 μm时,颗粒基本上不再从分离器出口逃逸,说明气速越低,出口煤粉细度越小。从图3(b)可以看出,气体速度基本按照阻力最小的情况进行分布,速度基本上跟横截面积大小成反比,速度最大值在出口处,约为34 m/s 左右,说明出口处产生的压降最大。从图3(b)切线速度的变化可以看出,上挡板下部的切线速度都很小,约为1 m/s。只有到了上挡板处才产生最高10 m/s左右的切线速度,其中切线速度呈中间高、边沿低形态,主要是上挡板开度较小(为30°)引起的,造成上部会出现颗粒聚集,当停机时会出现大量颗粒落入回粉管。从图3(c)可以看出,随着粒径的增加,分离器出口数量减少,相对于基准算例到达200 μm时,还有大量颗粒从分离器出口逃逸,说明气速越高,出口煤粉细度越大。
从图2和图3可以看出,经过进口通过轴向型粗粉分离器扩口管后,气流的形态发生了显著的改变,扩口管出口的速度值有了明显的降低,使该区域的速度流场分布较为合理,煤粉气流的导向作用得到了改善,加强了后续的撞击作用。气流经扩口管降速后继续上升,进入内外锥体间的环形通道。这时,在外锥体内壁附近气流速度较低,这有利于被离心力分离出来的颗粒沿壁面滑落到回粉管。由于进口气流能量的耗散和气流速度的扩散作用,因此气流在到达轴向挡板处时速度降至最低,压力达到最大值。而气流通过挡板后,速度则开始增大, 变化开始剧烈,在出口处气流的速度达到最大值,略大于粗粉分离器进口处的速度值。
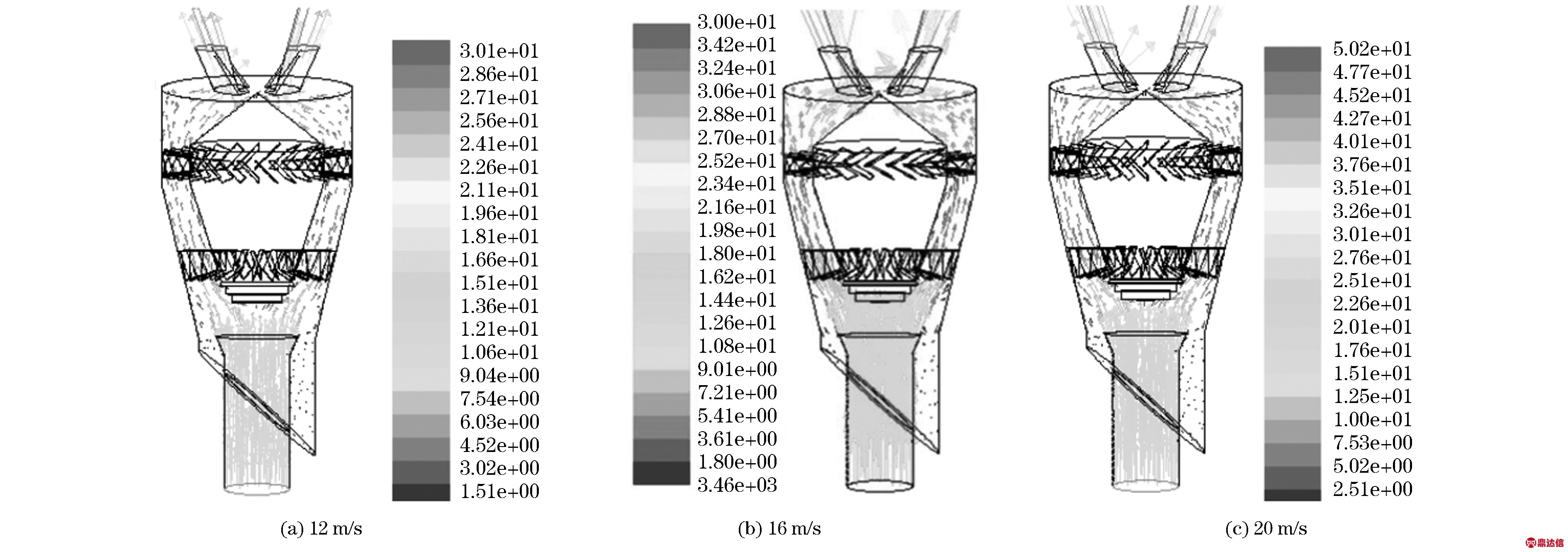
图3 气体速度下不同粒径颗粒的流线
Fig.3 Velocity and vector of gas velocity
12 m/s气速时不同粒径颗粒的流线如图4所示。从图4可以看出,随着粒径的增加,分离器出口数量减少,到达200 μm时,颗粒基本上不再从分离器出口逃逸,说明气速越低,出口煤粉细度越小。
16 m/s气速时颗粒的运动流线如图5所示,从图5可以看出,随着颗粒粒径的增加,颗粒从出口的逃逸量逐渐减少,60 μm颗粒基本从分离器出口逃逸,90 μm、200 μm的逃逸量逐渐减少,这时200 μm颗粒的逃逸量也比较大,这就造成了颗粒的细度增加,煤粉的燃烧效率降低,分离效率减小。另外,由于分离器顶盖设计问题部分颗粒在顶盖上部出现了聚集,随着颗粒粒径的增加,顶盖上部颗粒聚集越严重。
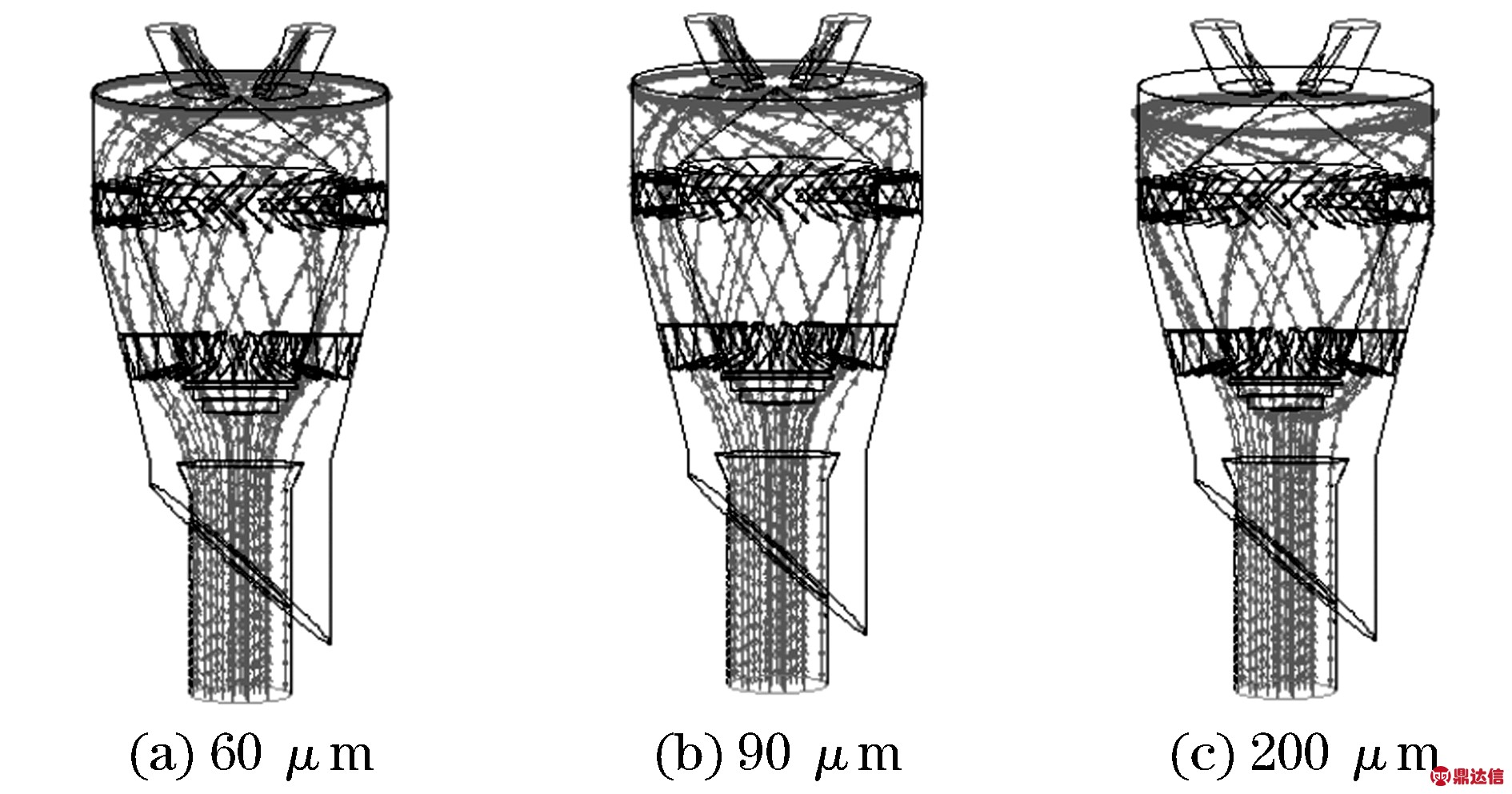
图4 入口为12 m/s时的颗粒流线
Fig.4 Particles streamlines (gas velocity is 12 m/s)
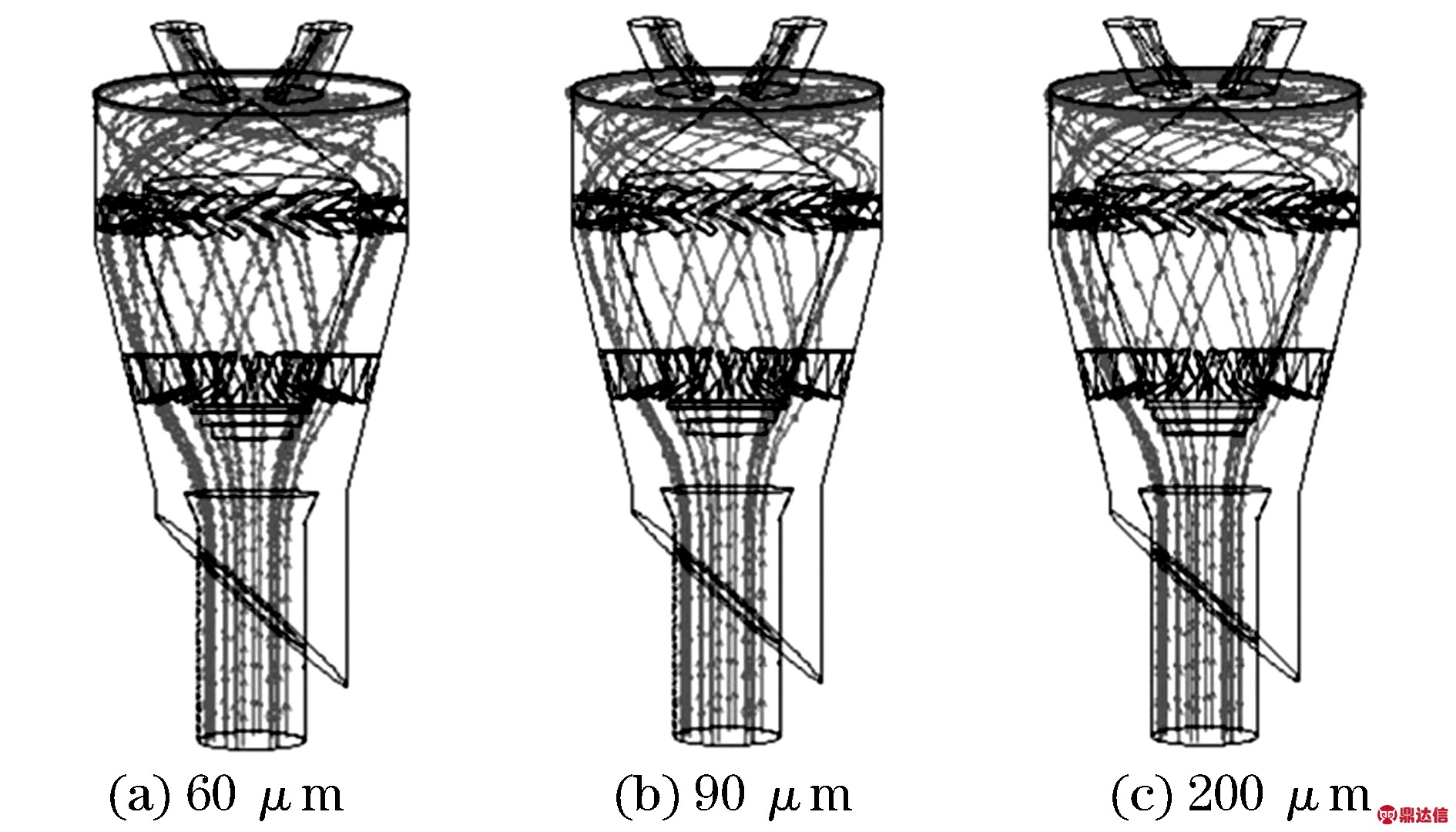
图5 入口为16 m/s时的颗粒流线
Fig.5 Particles streamlines (gas velocity is 16 m/s)
20 m/s气速时不同粒径颗粒的流线如图6所示。从图6可以看出,随着粒径的增加,分离器出口数量减少,但相对于16 m/s时而到达200 μm时,大量颗粒从分离器出口逃逸量增加明显,说明气速越高,出口煤粉细度越大。
整个流场的湍流强度分布如图7所示。从图7可以看出,较强湍流强度的位置在撞击锥和出入口处,在回粉管内湍流强度较弱,几乎可以忽略,说明回粉管气速较低。另外,在分离器顶盖处出现了湍流强度较低的情况,随着气速的增加,粗粉分离器上部的湍流强度越大,接近顶盖的低湍流强度区越小,这是形成颗粒聚集的主要原因,对改进顶盖结构是必要的。
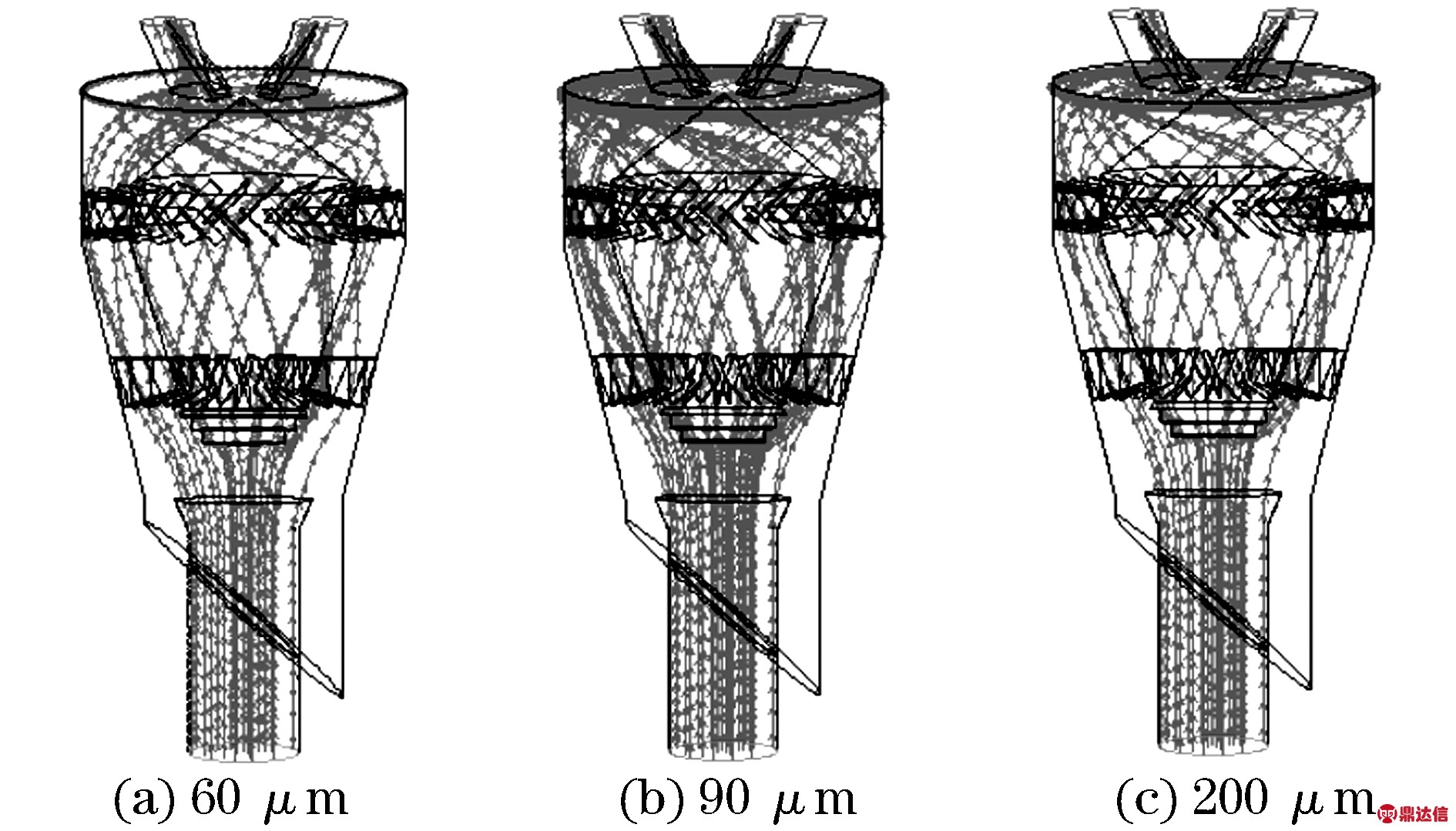
图6 入口为20 m/s时的颗粒流线
Fig.6 Particles streamlines (gas velocity is 20 m/s)
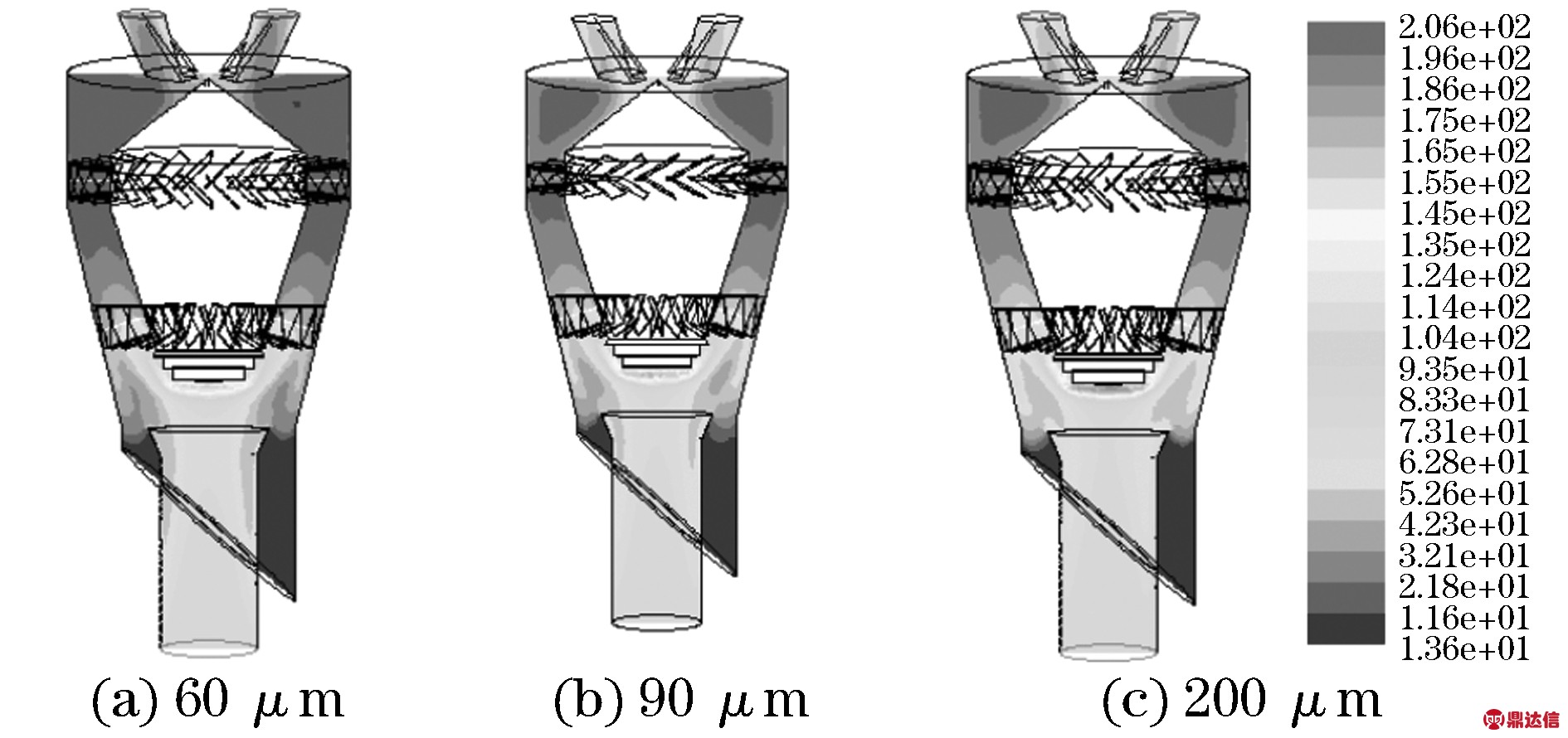
图7 湍流强度分布
Fig.7 Turbulence intensity Distribution
调节粗粉分离器,改变上下挡板开度,改变入口气速所引起的压降阻力变化的研究结果表明,随着下挡板开度的增加,压降阻力减小;随着气速的增加,压降阻力增加。保持下挡板70°不变,当上挡板开度为30°时,16 m/s 入口气速条件下压降为1 492 Pa;上挡板开度为45°和60°时,16 m/s 入口气速条件下压降分别为1 381 Pa 和1 335 Pa。而上挡板开度超过45°,压降阻力变化值减小,阻力减小出力会相应增加;当超过60°开度时,基本上压降阻力的影响非常小;若使上挡板有功效,则需调节开度至60°以下。
2.2 分离器优化及分离分析
针对某电厂粗粉分离器存在的分离和分级效率不高、细度偏大、均匀性指数不高、循环倍率较大等问题,对现有分离器进行了改进。指出了双进双出粗粉分离器轴向分离缺陷,利用切向分离的主导作用,消除撞击分离所起的作用。改进从提升管、挡板和顶盖出口等部分进行,优化后的分离器如图8所示。
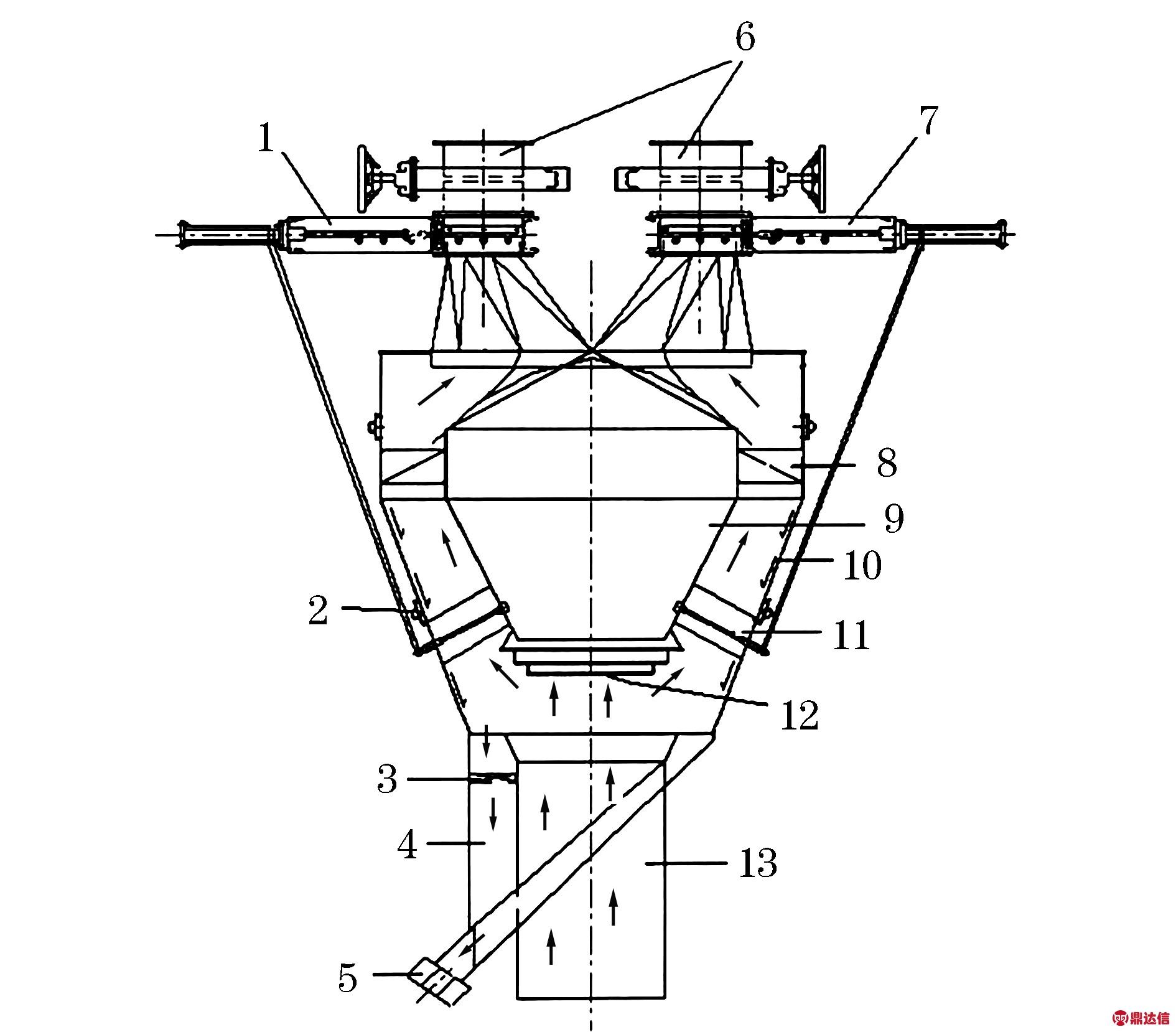
1-驱动装置;2-密封锁紧器;3-格栏栅;4-回粉筒;5-内堵塞锁气器;6-出料管;7-驱动装置;8-导向板;9-内筒体;10-外筒体;11-导流分离板;12-撞击分离板;13-进料风管
图8 优化后的分离器
Fig.8 Optimized separator
压降随轴坐标的变化如图9所示。从图9可以看出,压降随轴坐标的增加,先减小,再略微增加。然后急剧下降,三种气速下压降值分别为430 Pa、800 Pa和1 270 Pa,压降显著降低。其中,入口气速20 m/s 的压降比改进前16 m/s时还小。这表明,撞击部分产生的增压消失,出口顶盖部分颗粒聚集基本消失,较大的颗粒基本从回粉管中排出,而R90以下细颗粒基本从出口排出, 出口颗粒细度降低 ,分离效率增加。因此,新设计的粗粉分离器压降明显降低,即分离器的阻力降低,使分离器出力大幅度增加。
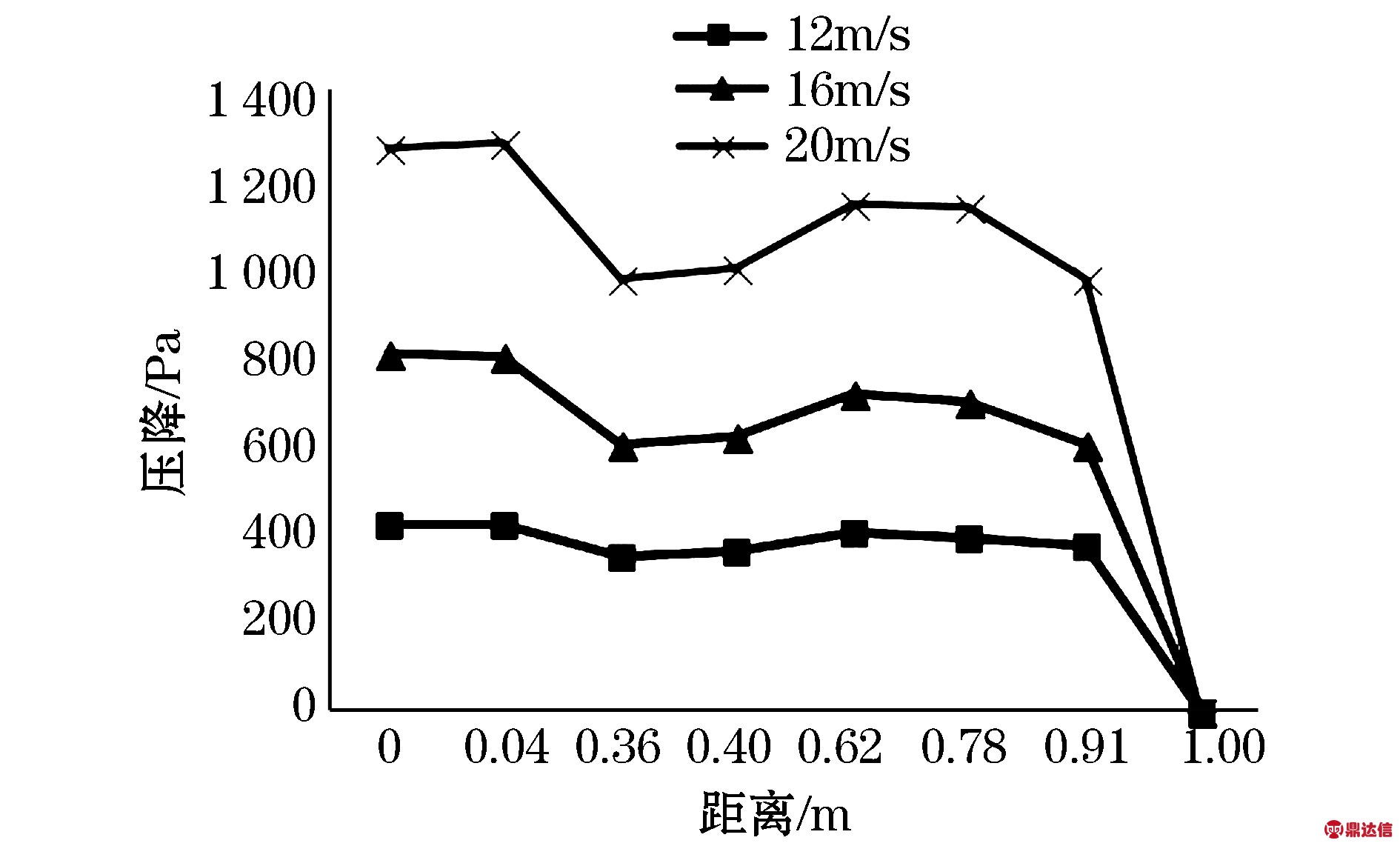
图9 压降随轴坐标的变化
Fig.9 Change of the pressure drop with the axis coordinate
3 结 语
粗粉分离器的分离性能至关重要,合理的流场有利于提高分离效率和减轻磨损,降低阻力。优化前的双进双出粗粉分离器,撞击锥处增压大,湍流强度很大,颗粒在此处聚集;分离器出口颗粒出现了堆积,易燃的煤粉容易自燃而影响安全;分离器压降很高,出力不高,煤粉细度增大。本文通过对双进双出粗粉分离器流体流速和压力分布情况进行数值模拟,得到了优化改进后的粗粉分离器,大幅度降低压降阻力,增大了制粉系统的出力;改变局部切线速度,分离和分级效果更加明显,分离效率高,煤粉细度减小,提高了均匀性指数。