摘 要: 与传统气氛渗碳相比,高温真空渗碳在提高渗碳效率、产品质量和节约能源方面均表现出明显优势.本文分析了12Cr2Ni4A钢的奥氏体晶粒长大行为、扩散系数及奥氏体饱和碳质量分数等关键参数的影响,结合真空低压脉冲渗碳工艺原理,对高温真空低压脉冲渗碳工艺进行实验验证.结果表明:实验钢在930,950,980 ℃渗碳温度下,渗碳层的硬度梯度曲线和碳质量分数梯度曲线的实测值与预期值吻合较好.此外,随着渗碳温度的升高,碳的扩散系数和奥氏体饱和碳质量分数增加,高温真空渗碳可显著提高渗碳速率,温度每提高10 ℃约使渗碳效率提高14%~17%.
关 键 词: 12Cr2Ni4A钢;真空低压脉冲渗碳;高温渗碳;渗层深度;碳质量分数
传统可控气氛渗碳常用的渗碳温度为930 ℃,当零件需要进行深层渗碳时,工艺时间较长,渗碳效率不高,造成极大的能源浪费[1-3].提高渗碳温度可以显著提高碳原子在金属内部的扩散系数,加快扩散速率.同时,渗碳温度提高后,奥氏体饱和碳质量分数值增大,脉冲渗碳工艺中的wH(金属表面碳质量分数的高值)可以取较大的值,提高了渗碳过程中的碳质量分数梯度,即增大了扩散驱动力,因此,高温渗碳可以大幅度减少渗碳时间,提高生产效率[4].
以12Cr2Ni4A钢生产的零部件,通过渗碳+淬火+回火工艺,可以获得硬度较大且耐磨的表面层和强韧性匹配良好的心部.工件主要用作高负荷、交变应力下工作的各种齿轮、蜗轮、蜗杆、主轴等机械结构件[5].因此,常需要深层渗碳处理,传统的气氛渗碳工艺需要很长的时间,能源和资源浪费严重,同时得到的渗层均匀性较差,表面碳化物的形成难以控制,废品率较高.真空渗碳以其无内氧化、可深盲孔渗碳、可高温渗碳等工艺优势,能够有效解决气氛渗碳面临的问题[6].美国提出的2020热处理计划中特别指出要开发新一代真空高温渗碳工艺和高温渗碳钢材料[1].Yang等积极开发新一代高温渗碳钢,旨在利用高温真空渗碳大幅度提高生产效率[7].日本大同特殊钢公司通过在钢中添加Nb,A1,Ti,V 等合金化元素,实现细化晶粒,有效缩短渗碳时间,大大降低了齿轮渗碳钢的生产成本[8].舒颖等提出了饱和渗碳碳化物移动的碳传递扩散模型,并在实验和计算的基础上开发了真空渗碳工艺模拟软件[9].但是,高温真空渗碳的研究仍存在较多盲点,真空渗碳工艺关键过程参数的缺乏制约着渗碳工艺的制定.
因此,本文结合乙炔脉冲低压真空渗碳的工艺原理,基于菲克扩散定律,得到在不同温度下指定渗层深度和表面碳质量分数的真空渗碳脉冲工艺参数,并以此进行多组渗碳实验,进而对高温真空低压脉冲渗碳工艺进行实验验证.通过对渗碳层的硬度梯度曲线和碳质量分数梯度曲线的测定,对比分析工艺控制的可靠性,验证了实验钢高温真空渗碳的可行性及其高效性.
1 实验材料和实验方法
1.1 实验材料
本文以12Cr2Ni4A钢作为实验材料,下文简称实验钢.利用光谱仪检测获得实验钢的主要化学成分(质量分数,%)为:C 0.12,Si 0.24,Mn 0.41,Cr 1.59,Ni 3.84,P 0.006 9,S 0.004 3,其余为Fe.
1.2 高温奥氏体晶粒长大行为
真空渗碳可以实现较高温度下的渗碳,但长时间渗碳时,组织中的晶粒会由于温度过高发生异常长大,严重恶化工件的使用性能.因此,制定渗碳工艺前需要对材料的奥氏体晶粒在不同温度和不同保温时间下的长大行为进行研究,以确定安全的渗碳温度[10-11].
将12Cr2Ni4A钢试样置于真空炉中,随炉升温至保温温度,保温一定时间后,出炉油淬.淬火后的试样进行金相制备,腐蚀后得到晶界明显的组织,进行晶粒度测定.保温温度分别为850,930,950,1 000,1 050,1 150 ℃;保温时间分别为1,2,4 h,共进行18次实验.图1给出了不同温度、不同保温时间后奥氏体晶粒尺寸的变化情况.由图1可知,当温度超过一定值时,晶粒迅速长大,在保温时间1 h内,保温温度在1 050 ℃以下时晶粒不长大,在1 150 ℃以上时晶粒异常长大;在保温时间2,4 h内,保温温度在1 000 ℃以下时晶粒不长大,超过1 050 ℃后晶粒异常长大.由此可知,对于12Cr2Ni4A钢,当渗碳温度低于1 000 ℃时,渗碳时间在4 h以内,晶粒不会出现异常长大,因此可以进行渗碳.
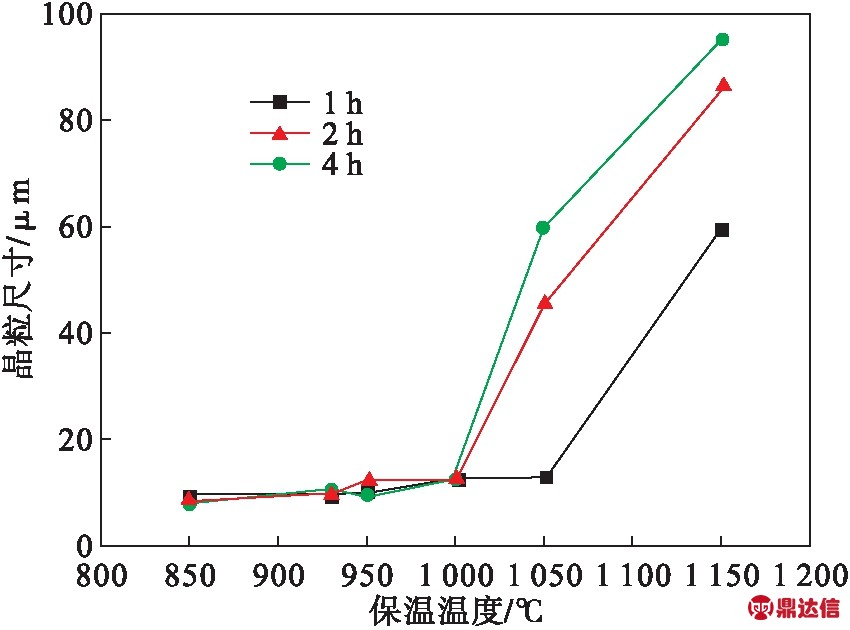
图1 保温温度和保温时间对奥氏体晶粒的影响
Fig.1 Effects of holding temperature and holding time on austenite grain
1.3 真空低压渗碳实验方案
为了验证真空低压渗碳工艺参数及渗碳控制模型的可靠性,设计了6组不同渗层要求的渗碳工艺实验.具体渗碳实验及渗层要求如下:
1) 渗碳温度分别为930,950,980 ℃.对于实验钢,传统的可控气氛渗碳工艺中常用的渗碳温度为930 ℃,作为真空渗碳工艺的参考,选取该温度渗碳作为渗碳效率比较的基准;为了研究真空高温渗碳的可行性及高效性,并结合奥氏体晶粒度测试结果,渗碳安全温度控制在1 000 ℃以下,故选取950,980 ℃进行真空高温渗碳实验.
2) 有效渗层深度分别为0.8,1.2 mm.在实际生产中,实验钢作为重型齿轮件、轴件设计时的渗层深度约为1 mm左右,故选择此深度作为预期渗层深度.
3) 渗层表面碳质量分数为0.8%.渗碳原始碳质量分数w0 为0.116%.相比930 ℃时奥氏体饱和碳质量分数为1.1%,950 ℃时奥氏体饱和碳质量分数为1.15%,980 ℃时奥氏体饱和碳质量分数为1.26%,0.8%的表面碳质量分数处于未饱和值以下,室温下得到的渗层表面组织无晶界碳化物,不影响渗层性能;相比实验钢原始碳质量分数0.116%,两者(表面碳质量分数与原始碳质量分数)差值较大,在渗层检测时可得到明显的浓度梯度,便于实验分析.
1.4 扩散系数
大量研究表明,合金元素的种类及含量也会影响扩散系数[12-13].考虑合金元素影响的扩散系数表达形式见式(1)[14].表1为其中各元素对扩散系数的影响系数.
表1 各元素对扩散系数的影响系数
Table 1 Effects of various elements on diffusion coefficient

D(T,w合金,w碳)=(0.146-0.036w碳(1-0.075wCr)+
(1)
其中:D为扩散系数,cm2/s;w碳为碳原子的质量分数;w合金为合金元素的质量分数;k1,k2是影响系数.
实验钢的合金元素主要是Cr,Ni,Mn,Si,采用上述经验模型计算扩散系数,得到930,950,980 ℃下扩散系数、扩散激活能、频率因子随碳质量分数的变化如图2所示.由图可知,实验钢的扩散激活能和频率因子随着碳质量分数的升高线性变化,扩散系数随着碳质量分数和温度的升高呈指数形式增大.

图2 实验钢的扩散系数
Fig.2 Diffusion coefficient of experimental steel
1.5 奥氏体饱和碳质量分数
渗碳时,需要对材料的表面碳质量分数进行控制.在渗碳温度下,当表面碳质量分数过高时,在奥氏体化组织中,晶界析出碳化物,在表面形成的碳化物层会影响该位置的扩散系数,在随后的淬火中,保留在室温渗层表面的组织中,影响渗层的硬度及其其他性能.表面碳质量分数的控制采用饱和值调整法.脉冲渗碳过程中,在渗碳段,表面碳通量不为0,表面碳质量分数从wL升高到wH;在扩散段,表面碳通量为0,表面碳质量分数从wH降低到wL,在该过程中,组织处于完全奥氏体化状态,并防止碳化物的出现.随着温度的升高,奥氏体饱和碳质量分数升高.因此在高温进行脉冲渗碳扩散过程中,可以适当增加强渗时间;同时由于温度升高,碳的扩散系数增加,可基于此优化渗扩比(渗碳扩散时间比例).
在工艺制定时,需要得到渗碳材料的奥氏体饱和碳质量分数值.当材料的合金元素种类较多时,需要进行多元相图的计算,本实验采用热力学软件Thermo-Calc获得实验钢在平衡状态下,计算得到930 ,950和980 ℃对应的奥氏体饱和碳质量分数值分别为1.1%,1.15%和1.26%.随着温度的升高,奥氏体饱和碳质量分数亦随之增加,渗层碳质量分数梯度增加,加速了碳原子的扩散.
1.6 真空低压渗碳工艺制定
本实验采用基于饱和值调整法的乙炔脉冲渗碳原理[15-17],具体的工艺过程如下.
1) 进料并抽真空:试样表面进行清洗,去除油渍污物,进料后炉膛抽真空.
2) 升温:试样随炉升温至渗碳温度,由于实验试样体积较小,不必采用分段加热的方式,到达设定温度后保温一段时间,直至试样心表均完全达到渗碳温度.
3) 渗碳脉冲工艺:脉冲分为渗碳和扩散两种,渗碳时,向炉膛内快速充入高纯乙炔气体,调节至稳定压力300 Pa,持续一段时间,炉膛内发生乙炔的分解、吸附、渗入,使得试样表面碳质量分数升高至wH时,进行快速抽气,进入扩散脉冲,充入氮气,调节炉内气压至70 Pa,此时仅发生碳原子由试样表面到心部的扩散;直至表面碳质量分数降低至wL时,快速抽气后充入乙炔,执行下一个渗碳脉冲,直到渗层中的碳质量分数梯度达到工艺预期.其中,渗碳和扩散的各脉冲时间由模型计算得到.
4) 淬火冷却:渗碳结束后,快速降温至淬火温度850 ℃,保温10 min后,出炉进行真空油淬.基于渗碳模型工艺软件[18],可得到渗碳脉冲工艺中各渗碳和扩散脉冲时间.由前述可知,模型计算需要表面碳通量、扩散系数、wH,wL值,其他工艺参数间接地影响模型参数,从而影响计算结果.渗碳实验各参数如表2所示.
表2 模型参数和实验条件
Table 2 Model parameters and experimental conditions

由上述参数计算得到6组真空渗碳工艺的渗碳脉冲如图3所示.其中,横轴为渗碳时间,s;纵轴为炉内气体压力,Pa.按照上述脉冲工艺进行实验,得到6种条件下的真空渗碳层,淬火冷却后对渗层进行硬度检测和组织观察.
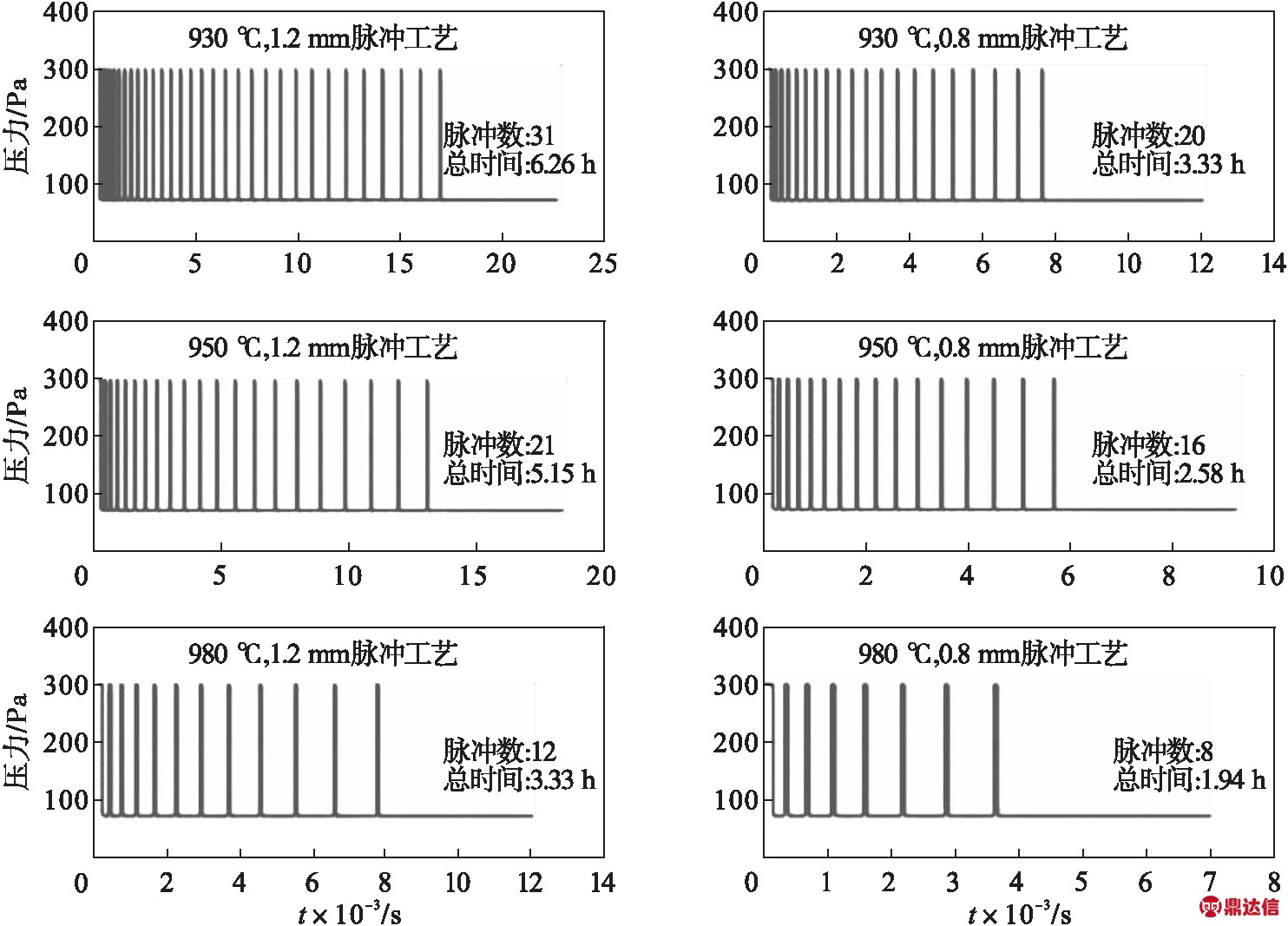
图3 真空脉冲渗碳工艺
Fig.3 Vacuum pulse carburizing process
2 结果与讨论
2.1 渗层碳质量分数梯度曲线
淬火快速冷却时,马氏体转变温度仅与渗碳层的碳质量分数有关,而与淬火温度及冷速无关.每隔相同渗层深度,记录马氏体转变区域与未转变区域的分界线,得到该分界线到表面的距离,同时记录该时刻的温度,将温度转变为对应的碳质量分数,即为该位置的碳质量分数[19].对6组渗碳实验的马氏体转变结果进行整理,得到的碳质量分数梯度曲线如图4所示.6组渗碳实验中,渗碳后的渗层各位置碳质量分数的实测值与预期值相差较小,体现了工艺控制模型的可靠性.对于实验钢,有效硬化层深度处的硬度为550 HV,其对应的碳质量分数约为0.34%.
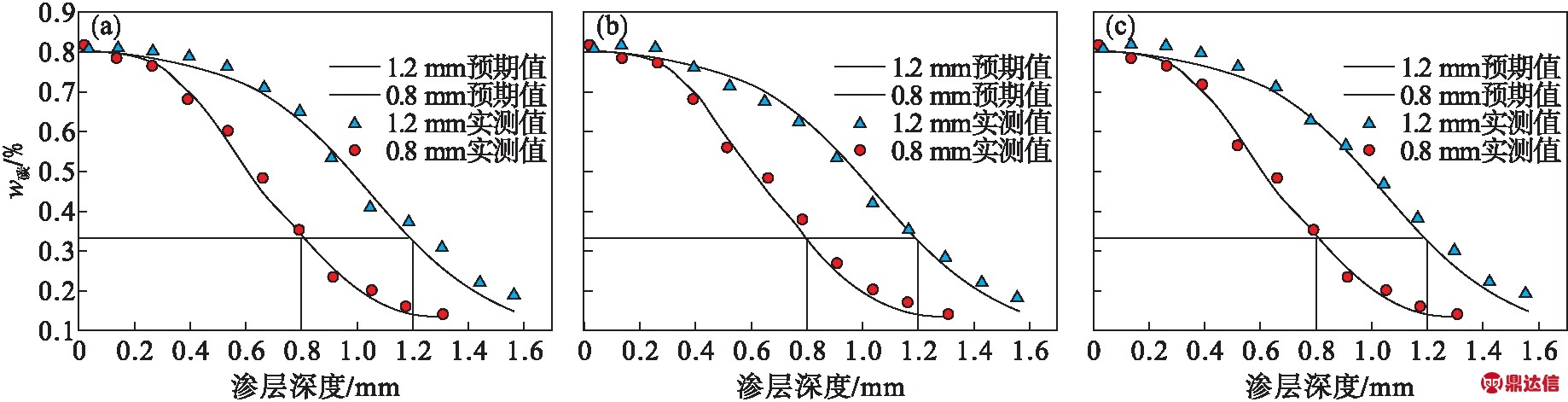
图4 渗层的碳质量分数梯度曲线
Fig.4 Carbon concentration gradient curves of the carburized layer
(a)—930 ℃; (b)—950 ℃; (c)—980 ℃.
2.2 渗碳结果对比与分析
利用维氏硬度计测定,得到渗层的微观硬度曲线如图5所示.将550 HV对应的位置视为有效渗层深度,渗层硬度从表面先增大后逐渐减小直至心部硬度保持不变.同一渗碳温度下得到0.8和1.2 mm的渗层,实测的硬度值与预期值相差较小,渗层较深时,硬度梯度曲线向右移动,在0.8 mm渗层中,硬度最大值位于渗层的0.45 mm处,在1.2 mm的渗层中,硬度最大值位于渗层的0.65 mm处;按照渗碳方案中的要求,在不同温度下获得相同渗层深度的渗碳层,实验结果显示,获得的渗层实际硬度梯度曲线与预期的硬度梯度曲线相差不大.总体来看,由真空渗碳实验得到的渗层硬度梯度曲线与模型计算得到的预期值相符.

图5 渗层微观硬度梯度曲线
Fig.5 Microhardness gradient curves of the carburized layer
(a)—930 ℃; (b)—950 ℃; (c)—980 ℃.
2.3 实验钢的高温真空渗碳效率对比分析
传统可控气氛渗碳常用的渗碳温度为930 ℃,在深层渗碳时,工艺时间较长,渗碳效率较低,造成资源和能源的浪费.然而,提高渗碳温度可以显著提高碳原子在金属内部的扩散系数,加快扩散速率,进而提高碳原子的扩散,缩短渗碳时间[20].同时,提高渗碳温度后,实验钢的奥氏体饱和碳质量分数值增大,所以脉冲渗碳工艺中的wH值可以选取相对较高的值,这又进一步提高了渗碳过程中的碳质量分数梯度,增大了碳原子的扩散驱动力,因此,高温渗碳可以大幅度减少渗碳时间,有效提高渗碳生产的效率[21].
对于实验钢,当渗碳温度低于1 000 ℃,渗碳时间在4 h以内,晶粒不会出现异常长大,可以进行渗碳.同时真空渗碳装备为冷壁式炉体结构,长时间的高温工作对装备的负担较小.本文设计的4组真空高温渗碳实验,在渗碳温度950,980 ℃下,分别得到0.8,1.2 mm两种渗层深度的渗碳层,与常规的930 ℃的渗碳脉冲工艺对比如表3所示.表中的渗碳效率是指提高渗碳温度后,相同生产时间下,可完成的渗碳生产工作.计算可知,提高渗碳温度后,总脉冲数减少,渗碳时间减少,每提高10 ℃约可使渗碳效率提高14%~17%.
表3 真空渗碳实验的脉冲工艺对比
Table 3 Comparison of pulse process in vacuum carburizing experiments

3 结 论
1) 本文得到了在930,950,980 ℃下,实验钢的扩散系数随碳质量分数的变化情况、具体的数值以及奥氏体饱和碳质量分数值.
2) 随着温度升高,碳的扩散系数和奥氏体饱和碳质量分数增加,是高温渗碳提高渗碳效率的必要条件.
3) 实验钢的真空高温渗碳可显著提高渗碳速率,温度每提高10 ℃约可使渗碳效率提高14%~17%.