摘要 搭建适用于大电流条件下的真空接触器温升特性测量试验平台,测量并分析了真空接触器在不同电流等级下的温升特性。通过试验测量的真空接触器指定位置的温升时变曲线,讨论不同电流下真空接触器温升规律及过负载能力。利用COMSOL Multiphysics软件建立真空接触器触头及导电回路的简化三维电-热耦合分析模型,考虑了空气自然对流对散热的影响,对 800~2 500A电流条件下温升过程进行数值仿真计算,获得了真空接触器温度、焦耳发热功率分布等参数,并与试验数据进行比较,结果表明二者能较好吻合,验证了仿真模型的有效性。该研究可为大容量真空接触器的热设计提供一定参考。
关键词:真空接触器 温升试验 焦耳热 有限元分析 温度场
0 引言
真空接触器广泛应用于采矿、冶金、纺织及电力等企业的配电系统中,是完成电能转换、分配与控制功能的重要电气设备[1]。由于真空接触器的触头系统由陶瓷或玻璃密封在真空环境中,其散热方式以热传导为主,散热效率不高,所以在负载电流较高时会出现严重的发热问题。温升过高不仅危害导体机械强度,带来熔焊、疲劳及蠕变等问题,而且裸露在空气中的部分材料表面还将变得易于氧化,生成的氧化物又会增加连接位置的接触电阻进而影响真空接触器接触系统的电阻及电气性能,此外,严重发热还将增加绝缘的介质损耗,加速部件老化,影响使用寿命。根据 GB 14048.1-2006《低压开关设备和控制设备 第一部分:总则》和 GB 14048.4-2010《低压开关设备和控制设备 第 4-1部分:接触器和电动机起动器机电式接触器和电动机起动器(含电动机保护器)》中对交流接触器温升试验的相关要求[2-3],对交流接触器的发热部件规定了温升允许极限值为65K,部分企业还提出了50K等更严苛的指标要求。因此,系统测量真空接触器温升特性及准确模拟真空接触器触头系统发热的物理过程对于真空接触器向小型化、大容量方向发展具有重要意义。
近年来,电力设备的热仿真技术发展迅速。围绕着真空断路器、接触器、继电器及配电开关柜等的温升研究取得很多有益的成果。对于如真空断路器等具有散热装置的开关电器,热量主要由上下两个散热器通过自然对流和辐射的方式散出,文献[4]对影响真空断路器温升的散热表面对流换热系数、动静触头接触半径、接触点位置以及导电杆半径四种因素进行了仿真分析。文献[5]以某型号10kV/5kA真空直流断路器作为研究对象,通过热电耦合法对其进行了温度场数值模拟。短时耐受电流条件下的热稳定性是低压断路器的重要考核指标之一。文献[6]在动静触点间导电桥模型周围增加了一个传导热量的薄层解决了微小气隙中热辐射作用增长、导热效果加强的问题,利用谐波电磁场分析结合瞬态温度场,确定了焦耳热损耗及温度场分布,仿真计算了 1s短路电流周期分量有效值为 125kA正弦电流条件下触头温升分布。纽春萍、季良等建立了同时考虑主回路和电磁系统发热的接触器数值热分析模型,并分别对长期闭合工作制下额定电流为100A的交流接触器和带反馈调压系统的额定电流 160A智能接触器进行了温度场仿真[7-8],但是该研究主要针对小型空气式交流接触器,与真空接触器的触头及导电回路结构和发热机理均存在较大差异。对于继电器、开关柜等具有封闭外壳的开关设备,其内部空气流动的空间较小,因此传导散热模型被广泛采用,苏秀苹等利用ANSYS建立了12V/20A的小型直流电磁继电器热电耦合模型,考虑了电阻率等参数随温度变化,并在散热分析中计入了热传导、对流及辐射的影响,结果表明,热导率随温度变化对仿真结果的影响较小[9]。杨文英等提出了一种基于有限元仿真的电磁-热耦合建模方法,对不同环境温度和反复短时工作状态下继电器电磁机构动态特性进行了仿真分析[10]。文献[11]提出填充层法的计算模型,分析了直流12V/70A商用密封汽车继电器反复短时工作制下的瞬态热问题。周学等仿真计算了500~3 000A的短路电流条件下智能电表用磁保持继电器触头系统及导电回路的热特性及热应力引起的微小形变问题[12]。文献[13]完成了无壳和有壳下线圈恒定通电时,24V电压下型号HFV6汽车继电器温度场的仿真。李兴文等采用计算流体力学方法计算了额定电流 630A配电开关柜在自然对流、强迫对流条件下的温升分布,并与试验进行了对比,绝对误差为13K[14];此外,还计算了含通风口的开关柜在降容运行条件下的温升分布[15]。Barcikowski等研究发现微型断路器内部的对流与辐射传热过程对断路器导电回路稳态温升的影响可以忽略[16]。还有一些研究学者计算了外壳不封闭的电力设备的温升[17-18]。
目前国内外针对真空接触器温升特性,特别是在大电流条件下的真空接触器触头及导电回路整体发热过程方面的文献很少,已有的接触器温升研究也主要集中在经验公式和电磁机构部分。本文针对JRS1600A单相交流真空接触器在大电流条件下的温升特性进行了研究,通过试验和仿真总结了真空接触器的相关温升特点并结合研究结果对真空接触器的过负载能力进行了评估。首先,本文搭建了可用于 2 500A大电流条件下的真空接触器温升测量试验平台,在不同电流条件下对真空接触器的导电排、外壳等相关标准规定位置不同通电时间下的温度进行试验测量,获得了温升特性曲线,讨论了真空接触器的过负载能力。其次,为探究真空接触器触头及导电回路整体发热情况,特别是试验过程中无法测量的位置(如真空灭弧室内部触头及导电杆等)的温升特性,建立三维电-热场强耦合分析模型并采用 COMSOL多物理场耦合有限元软件对不同电流下的真空接触器的温度场、焦耳发热功率分布等参数进行仿真计算,并提取相关标准规定位置的温度数据与试验结果进行对比分析。该研究可为开发更大电流等级的真空接触器提供理论参考。
1 试验方法
1.1 试验总体方案
大电流真空接触器温升特性测量回路原理如图1所示,系统主要由主回路和控制系统两部分组成,其中系统电源采用工频交流 220V供电,经过接触器、断路器接入主变压器,主变压器电压比为77∶1。主变压器输出的电流经过可调节负载电阻流入被测接触器(型号为 JRS1600A单相交流真空接触器,额定电流为 1 600A)。试验过程中电流通过电流互感器(型号CDH10000A)测量试验过程中真空接触器电流。控制系统采用可编程延时定时循环时间继电器(型号DH48S-S)作为控制核心,通过设定其闭合与分断时间来控制电源端接触器的动作,从而实现持续通电时间的控制与工作制的选择功能。由于负载变压器输出端为3V,因此,主回路的试验电流大小主要取决于主回路中的可调节负载电阻值。试验电流分别设置为 800A、1 200A、1 600A和2 500A。主电路采用铜排与铜编织线对可调电阻、待测真空接触器和负载变压器之间连接,接触器均用黄铜螺钉螺母紧固连接,其中采用较大的黄铜垫片与弹性垫圈并涂抹导电膏以增大接触面积,减小接触电阻的影响。试验过程中通过热电偶测量真空接触器的温升特性。
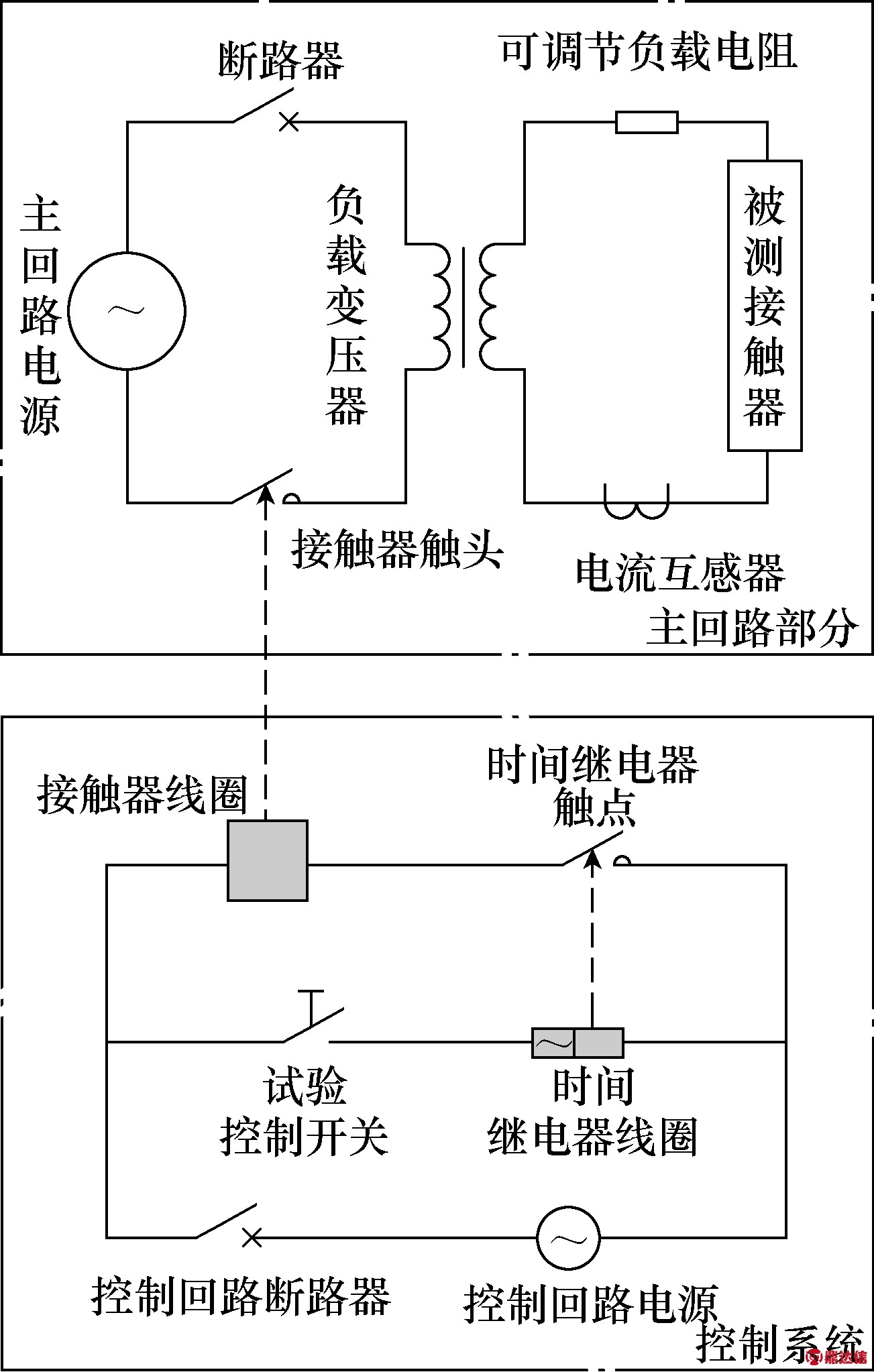
图1 实验系统原理
Fig.1 Schematic diagram of the experimental system
1.2 可调节负载电阻设计
为了确保在最高功率 9 000W 条件下温升特性试验回路的安全,本文设计了水冷可调节的负载电阻试验装置。该装置的原理如图2所示,由不锈钢管作为可调节电阻主体,通过设置接线端之间的距离以实现金属管接入电路长度(即电阻)的调节;利用在金属管内部循环流动的冷水来解决温升试验过程中发热严重的问题。
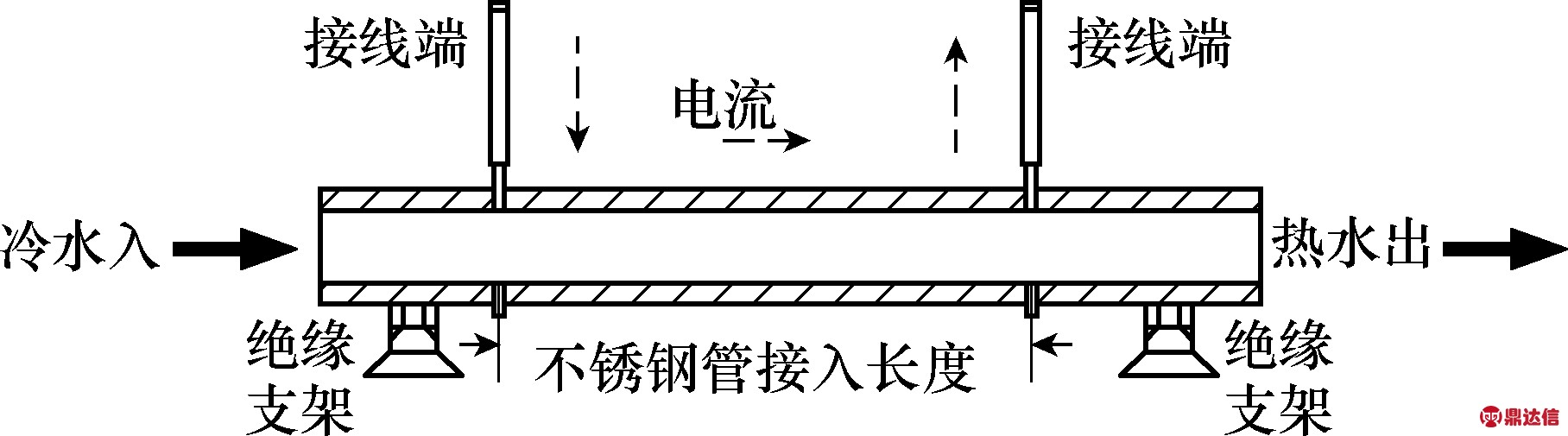
图2 水冷可调节负载电阻原理
Fig.2 Schematic diagram of variable load resistance cooled by water
该可调节负载电阻值为
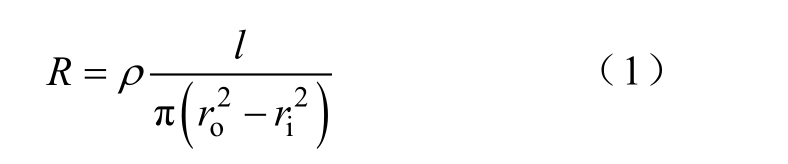
式中,ρ 为电阻率(Ω·m);l为不锈钢管接入长度(m);ro为钢管的外径(m);ri为钢管内径(m)。经计算不锈钢管长度为1m,外径为25mm,内径为21mm,以确保充足的冷却用水流量,实现可调节负载电阻的温升指标低于5K,从而避免发热造成负载电阻值波动。金属管内流出的高温水通过冷水机进行降温制冷,为了防止试验过程金属管内的水中离子、杂质参与导电影响阻值,试验采用去离子蒸馏水。金属管的接入长度与电阻、电流的对应关系见表 1。该可调节水冷负载电阻满足的指标为阻值调节范围0~5mΩ、功率0~9 000W。
表1 接入长度与电阻、电流关系
Tab.1 The relationship of length, resistance and current
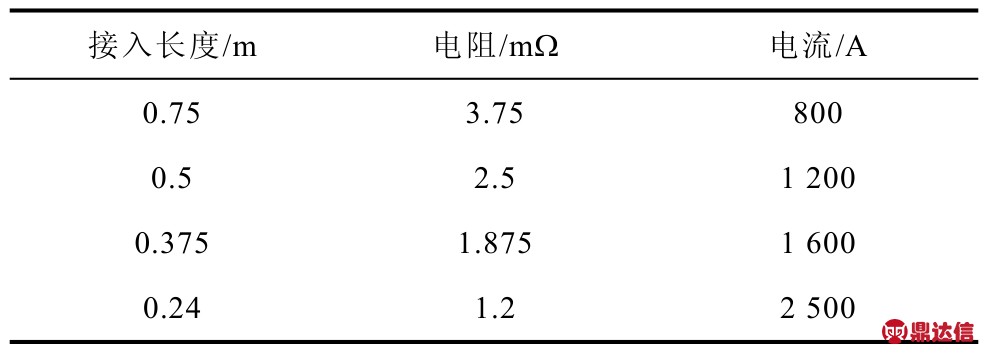
1.3 温度测量方法
根据GB 14048.1-2006和GB 14048.4-2010中对交流接触器温升试验的相关要求[17-18]。本文采用4路热电偶测温仪(型号 HT-9815)测量室内温度和待测关键位置的温度,热电偶测温仪测量范围-200~1 372℃,分辨率 0.1℃。选取温度测量点情况如下:第1路热电偶探头置于距离试验平台有一定距离的油中,以测得较为稳定的室温,避免试验过程空气温度变化与被测电器及导电回路发热之间的影响;第2、3路热电偶选取上下两个导电排进行测量,以获得对与接触器相连接的仪器设备的影响;此外,根据GB 14048.1-2006表3中的规定,接触器外壳属于已接近部件,故第4路热电偶探头置于接触器的外壳进行测量,上下导电排和真空接触器外壳温升测量位置如图3所示。热电偶探头与待测位置之间采用铝箔胶进行固定。
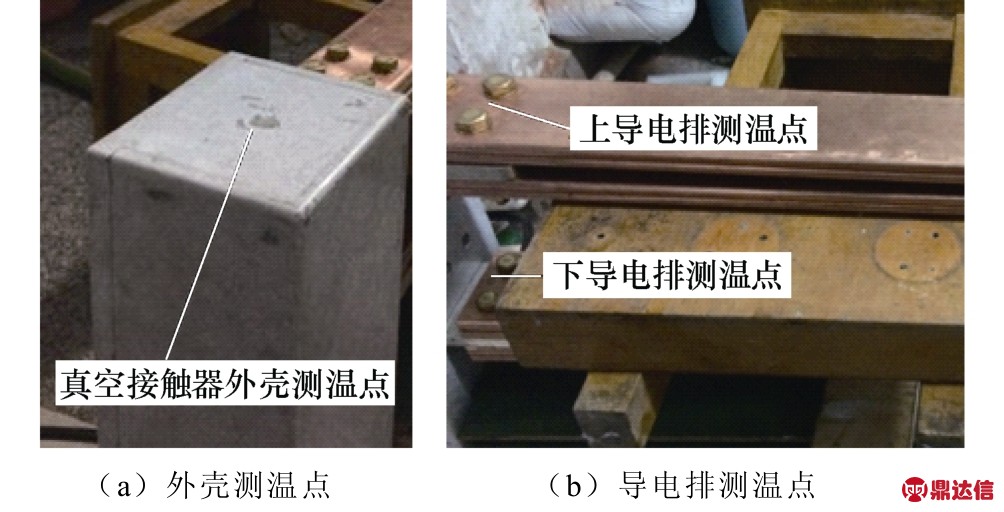
图3 温升测量点
Fig.3 Measurement point of temperature rise
2 实验结果
2.1 不同电流下时变温升情况
试验分别在电流为2 500A、1 600A、1 200A和800A的条件下,对JRS1600A单相交流真空接触器进行 180min持续通电操作,然后测量真空接触器外壳及上下导电排的温升随通电时间变化情况,如图4所示。由图4可知,3个温度测量点的温升均在 150min后达到相对稳定的状态。其中,真空接触器的下导电排温升分别为 51.2K、30.6K、13.1K和8.6K,上导电排温升分别为51.9K、33.2K、15.4K和9.7K。上下导电排的温升随时间变化呈现三次方关系,如图4a所示。在1 200A和800A电流条件下,上导电排的温升略高于下导电排的温升,原因是上导电排距离真空接触器动静触头接触位置相对更近一些,电流等级较低的条件下,触头及导电回路的温升分布还存在一定的不一致性。上下导电排的温升差异随着电流的增大逐渐缩小,由 800A条件下的1.1K缩小到2 500A条件时的0.1K,在电流为2 500A时,二者的曲线已基本重合,说明接触器的触头和导电回路的发热已经比较严重,二者的温升差异已不明显。通过对2 500A条件下的导电排不同通电时间的温升数据进行指数函数拟合处理,可以得到拟合函数为

式中,t为时间(min),温升时变曲线呈指数增长,可以求得时间常数τ =41.6,同时对其余电流条件下的温升时变数据进行拟合,求得τ 在1 600A、1 200A和800A时分别为54.5、37.6、59.8。工程上一般认为温度在 3~5倍时间常数(即(3~5)τ)时即可稳定,由于本文相关试验是在 150min后温升时变情况开始稳定,说明本文的试验数据在合理范围。
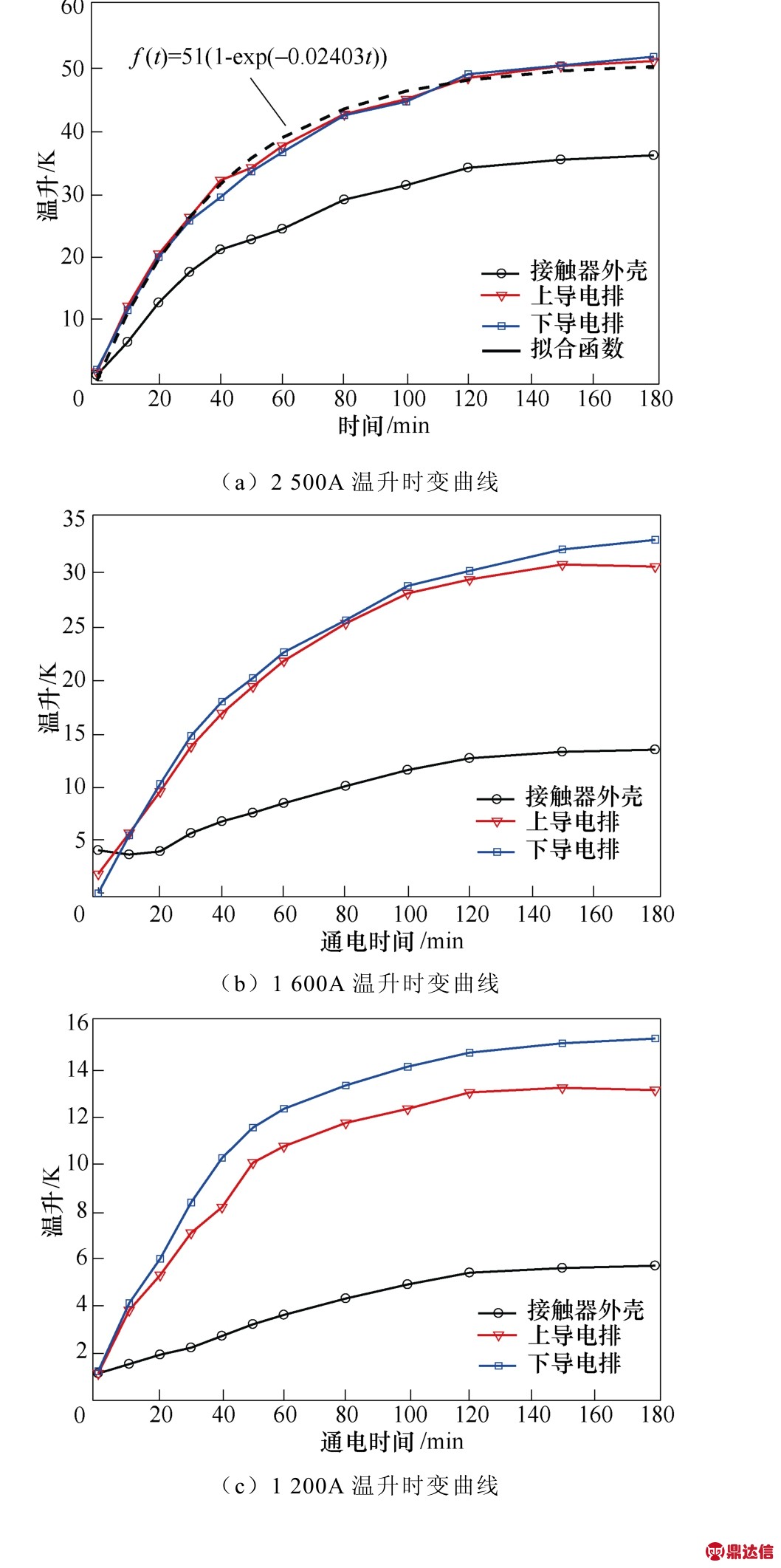
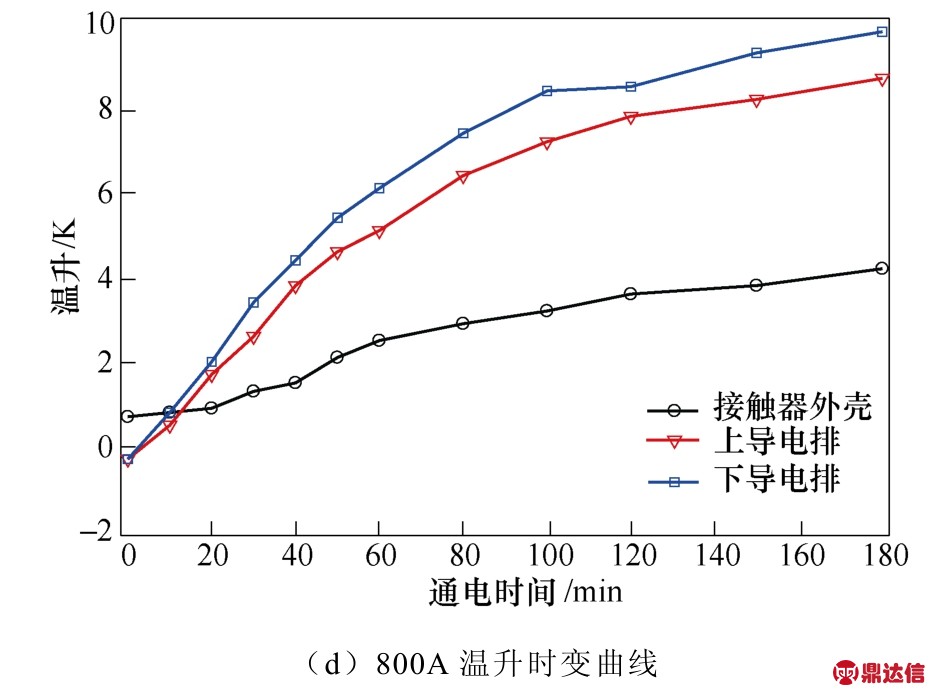
图4 不同电流下的温升时变曲线
Fig.4 Temperature rise time varying curves under different currents
此外,通电时间为 180min时,试验过程中接触器外壳温升在2 500A、1 600A、1 200A和800A条件下分别为 36.1K、13.7K、5.7K和 4.1K,随着电流的增加,外壳的绝对温升逐渐增加,其中接触器外壳的温升在电流为1 600A及以下条件时,温升变化趋势较为平缓,特别是在通电前20min基本维持在相对较低的状态。真空接触器外壳温升随时间整体呈现近似线性增加趋势,外壳温升增幅在43.9%~51.8%之间。当电流为 2 500A时,外壳的温升时变曲线与上下导电排的温升变化趋势基本一致,增幅为 62.6%。所以在面向工程实际应用的建模仿真中,如通电时间较短且电流等级较低,为节省计算时间,可以在一定条件下考虑忽略真空接触器外壳的影响。
2.2 过负载能力分析
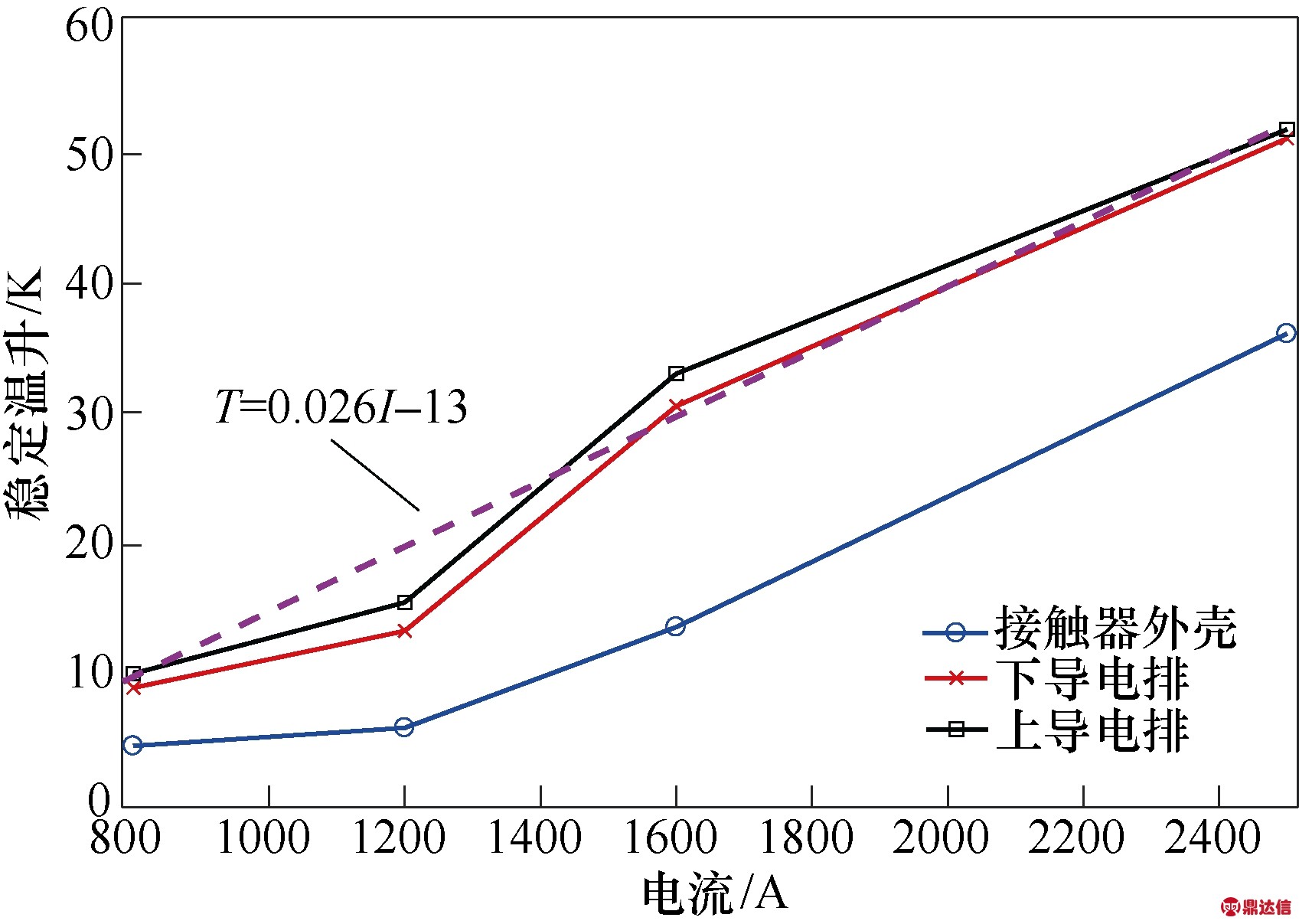
图5 不同电流下的稳定温升
Fig.5 Stable temperature rise under different currents
不同电流下t =180min时刻的稳定温升如图5所示。通过线性函数拟合不同电流下的稳定温升评估负载能力,对不同电流下的导电排稳定温升进行线性拟合,得到温升T与电流I之间的关系函数为T=0.026I -13。在GB 14048.4-2010中,对交流接触器发热部件规定了温升允许极限值,其中铜制接线端子(导电排)在不间断工作制的情况下极限允许温升为 65K,代入函数后可得该温度对应电流约为3 000A,故理论上该型号单相真空交流接触器可以在不间断工作制下超载至3 000A。说明该真空接触器在过负载能力方面还有一定提升空间。
3 仿真分析
3.1 几何模型
由于真空接触器的灭弧室属于密封真空结构,试验过程中只能对灭弧室外部的导电回路、外壳等部分进行温度测量,无法获得真空灭弧室内部的温升特性及触头、导电回路整体发热情况,因此本文对真空接触器触头系统进行电-热耦合仿真计算。真空接触器触头及导电回路结构如图6所示,其中图6a是触头系统及导电回路的三维实体,真空灭弧室内含动、静触头,剖面如图6b所示。触头为铜钨,屏蔽罩及导电回路材料均设置为铜,真空灭弧室的外壳材料设置为陶瓷。此模型的尺寸与 JRS1600A单相交流真空接触器实际产品基本相同。
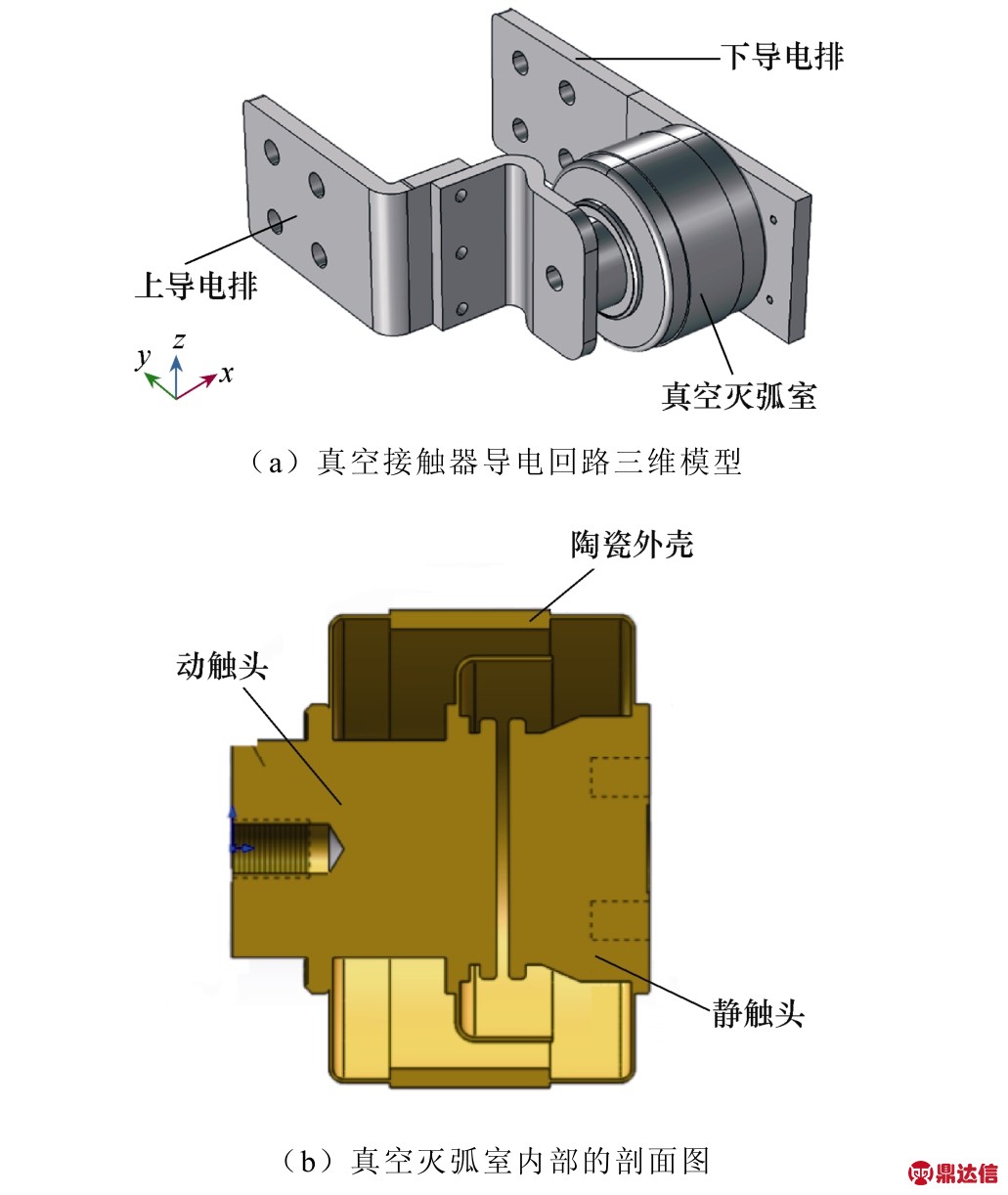
图6 真空接触器触头及导电回路结构
Fig.6 Structure diagram of contacts and main circuit for the vacuum contactor
3.2 控制方程及边界条件
真空接触器的触头系统及导电回路温度升高主要由流经导电部分的负载电流产生的焦耳热引起,温度场的分布取决于电流密度分布,所以在计算得到电流密度分布后,再通过焦耳定律就可以获得内部各处的发热功率分布。最后根据发热与散热之间的平衡关系,基于传热学理论确定求解区域的温度。该过程可以由电热耦合模型进行描述。
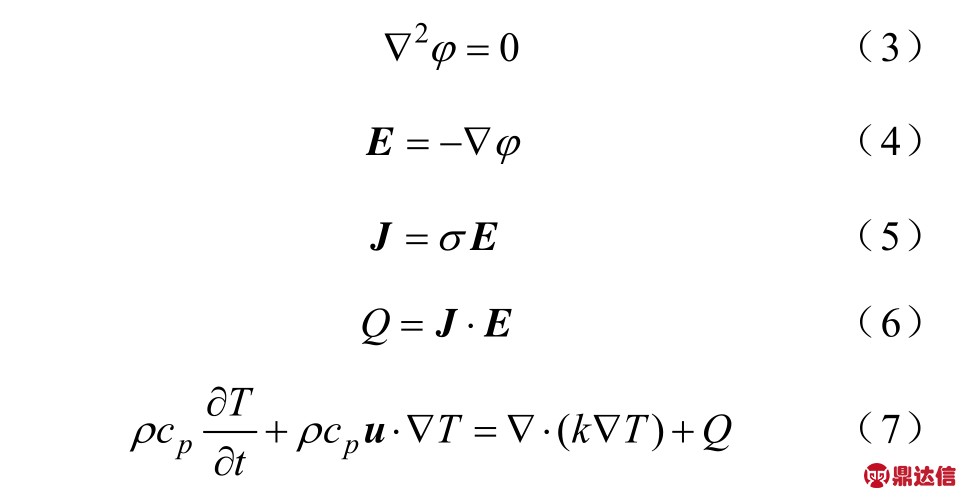
式中,φ 为电位(V);J为电流密度分布(A/m2);E为电场强度矢量(V/m);σ 为电导率(S/m);Q为焦耳热源项(W/m3);ρ 为密度(kg/m3);cp为比定压热容[J/(kg·K)];T 为温度(K);u 为速度(m/s);k 为导热率[W/(m·K)]。
本文电-热耦合仿真分析主要利用 COMSOL Multiphysics中的电流模块、固体传热模块与电磁热多物理场耦合模块。电流流出端设置为接地,即电动势为0V;电流流入端设置为第二类边界条件,将电流平均分布于输入端截面,设置为相应的电流密度,本文中的计算电流分别为 800A、1 200A、1 600A、2 500A。电流模块中设置与实验相对应的向内电流密度与接地边界条件,固体传热模块中选用对流热通量模拟接触器与空气间热量传递关系,其传热系数h设为7W/(m2·K)[2],对应试验过程中较弱对流散热的实际情形,温度场的边界设置即计算区域边界为室温300K。求解模型的网格剖分采用自由四面体网格,共剖分1 064 547个单元,求解时间设置为180min,求解步长设置为1min。
3.3 触头间接触区域处理
触头间微观区域的温度变化不是本文的研究重点,且其影响因素较多。本文采用圆柱导电桥模型模拟触头间的接触电阻和电流收缩现象,假设动静触头间的接触内表面中心只含有一个实际导电区域或者全部实际导电斑点集中在触头中心形成一个大的导电区域,将触头间的实际导电接触区域简化为位于触头表面接触面中心的一个小圆柱[2-6, 19]。等效导电半径r为
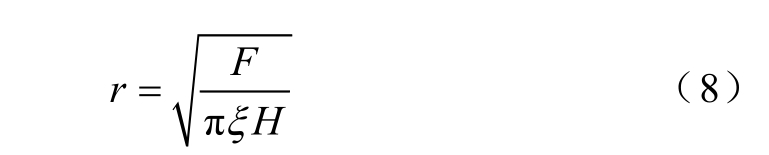
式中,F为触头间的预压力(N);ξ为与触头表面接触状况有关的修正系数,其范围在0.3~1之间;H为材料的布氏硬度(N/mm2)。经过试验测量该真空接触器触头间接触电阻为 20μΩ,触头间预压力为500N,ξ =0.45。通过式(8)计算可得,等效导电区域的半径约为2.95mm。
3.4 仿真结果分析
电流为1 600A条件下,t =180min时刻,真空接触器xy截面的温度场分布如图7所示。真空灭弧室的外壳为热导率较低的陶瓷材料,且外壳与触头之间为真空,因此开关管外壳的温度较低,而最高温度出现在触头接触区域,触头部分的温度为338K,上下导电排温升随着与触头间接触位置的距离增大而出现降低趋势,但导电排整体的温度分布基本一致,这主要是由于真空接触器的导电排尺寸较小,缺乏如真空断路器中散热器这样的散热装置。本文同时对800A、1 200A和2 500A电流条件下的时变温升情况进行了计算,发现切面温度分布与1 600A分布情况基本一致,仅最高温度不同。在不同电流、不同通电时间下,真空接触器上、下导电排与试验中一致的测温采样点的温升时变曲线如图8a和图 8b所示,仿真获得温升时变曲线的变化趋势与试验结果与图4的结果基本吻合。
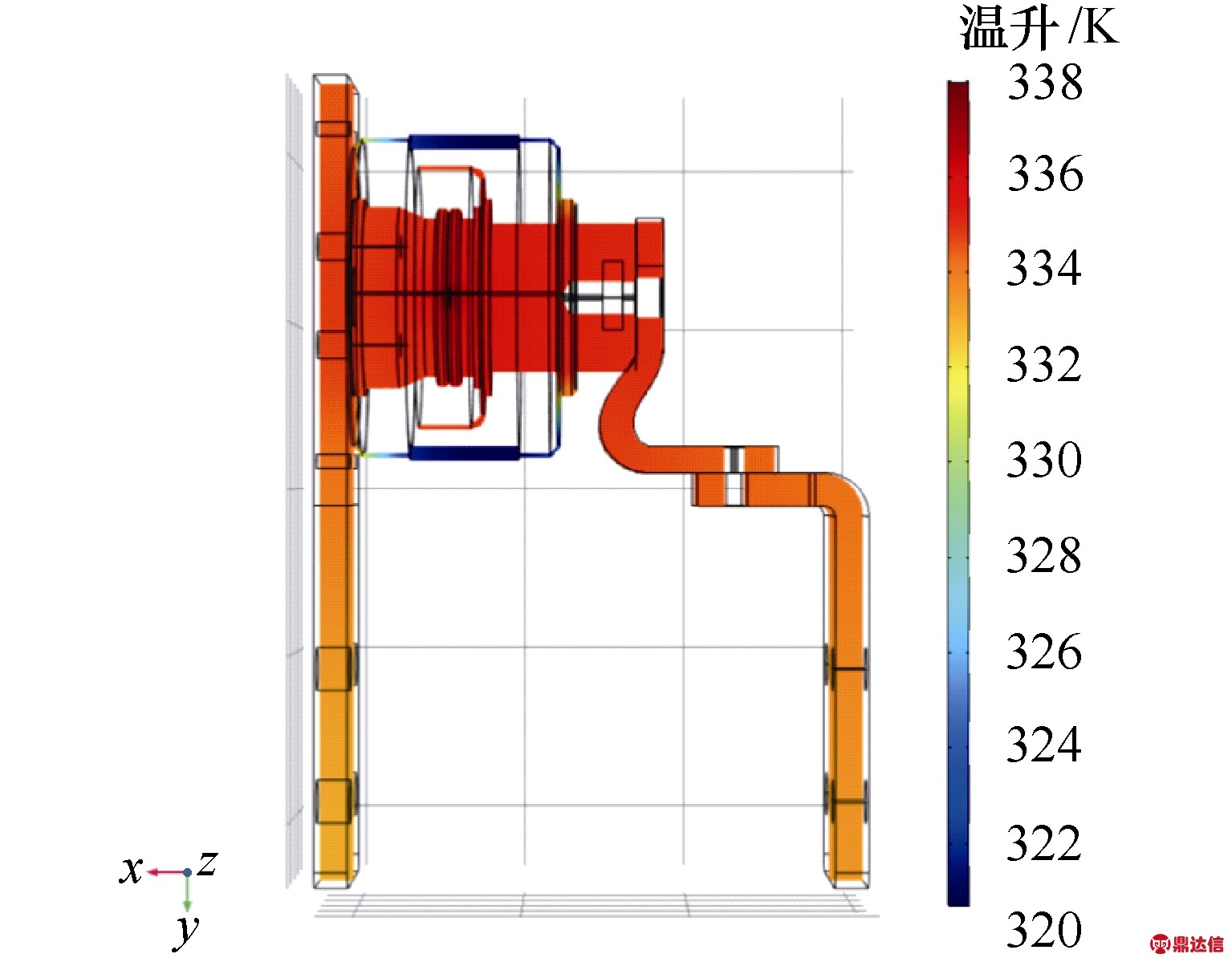
图7 温度场分布(xy截面,电流1 600A)
Fig.7 Temperature field of xy axis cross profile with 1 600A
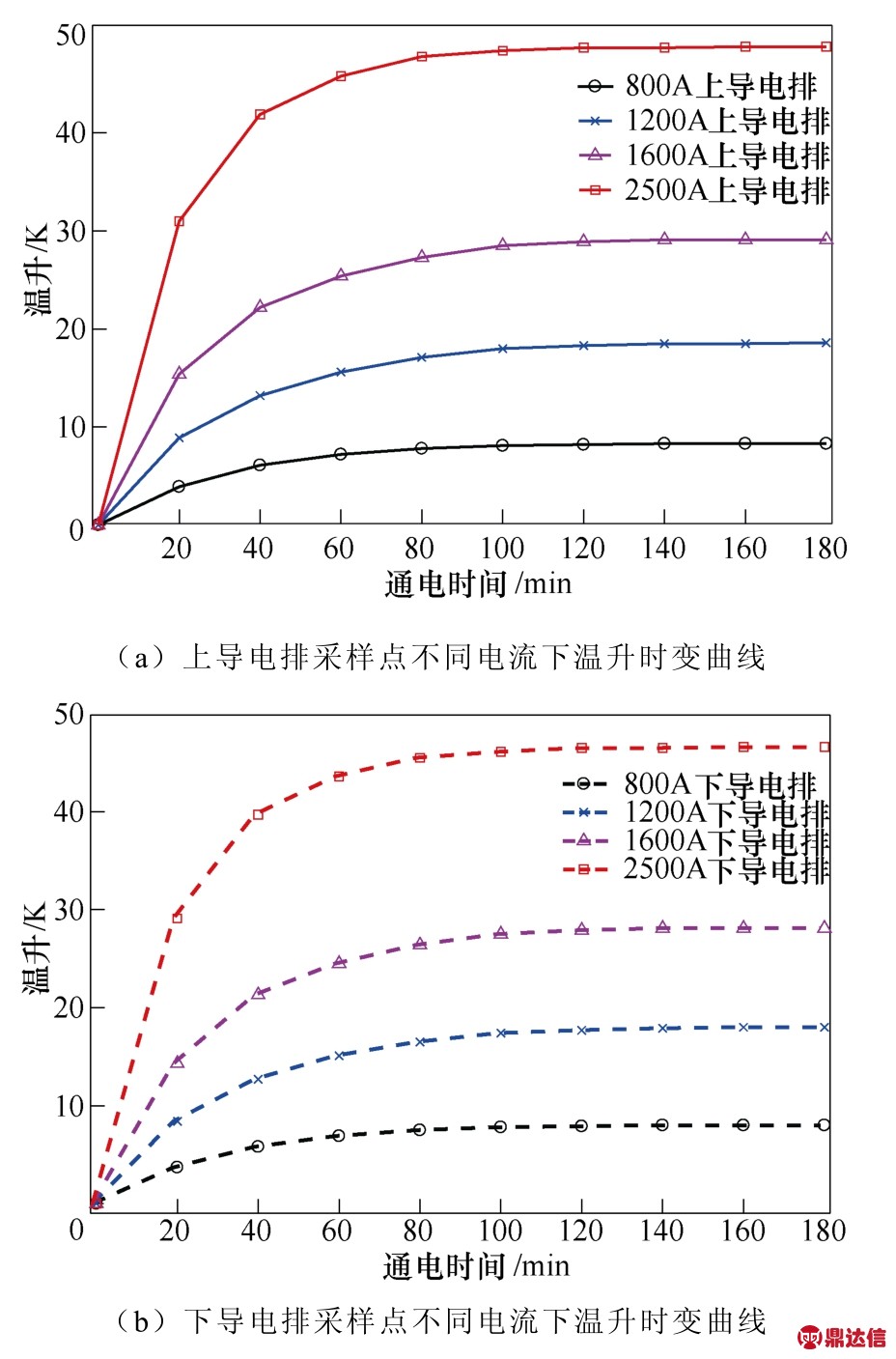
图8 不同电流条件下温升时变仿真结果
Fig.8 Calculation results of temperature rise time varying curves with different current
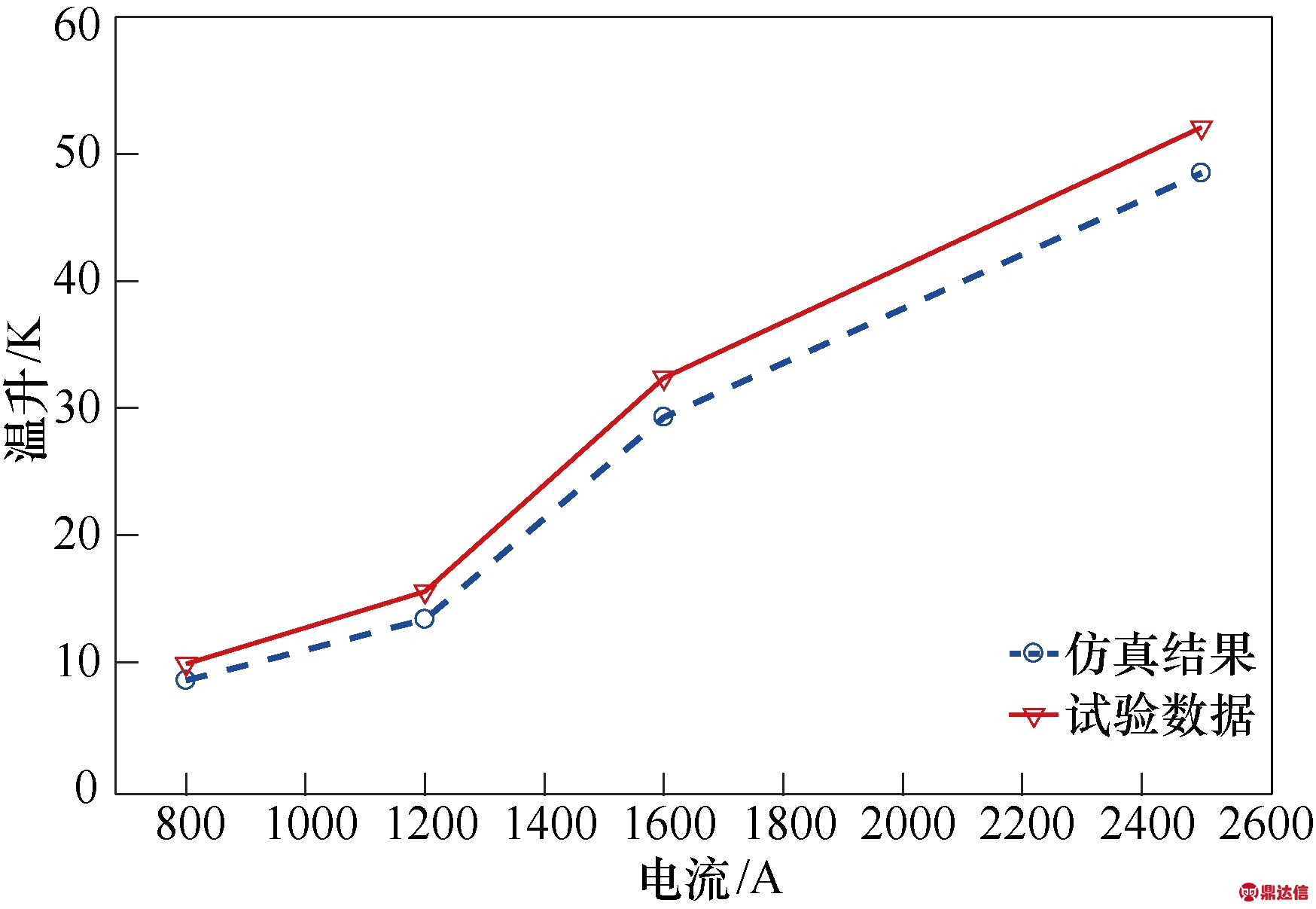
Fig.9 不同电流下温升仿真结果与试验数据的对比
Fig.9 Comparison of calculated and experiments temperature rise under different current
上导电排测温采样点的稳定温升在 t =180min时刻的仿真结果与试验数据对比如图9所示。可以看出,800A电流条件下的仿真结果与试验数据时间的绝对误差为1.3K,相对误差为13.4%;2 500A电流时,仿真则较试验低3.6K,绝对误差为2.3K,相对误差为 4.43%,随着电流等级的增大,仿真与试验之间的绝对误差略有增加,但相对误差则降低,仿真结果与试验测量的温升数据较为接近,随电流增大二者的变化趋势基本吻合,验证了本文所建立的仿真模型的有效性。初步分析,造成误差的原因一方面是本文仿真建模过程中未考虑与上下导电排连接的铜排及铜编织软连接部分,这些零部件在大电流条件下也会出现严重的发热,从而通过热传导对测温点的温度造成一定影响,因此试验过程中温度较仿真数据略高;另一方面,建模过程对真空接触器的塑料外壳及部分非金属零部件未予以考虑,且对导电排的部分细节如倒角、螺孔等进行了简化,这也会引起仿真误差。
不同电流下真空接触器 xy截面焦耳发热功率分布如图10所示,可以看出真空接触器接触系统导电回路的触头接触区域、软连接弯折部分、导电排拐角部分的导体发热功率密度相对较大,焦耳热密度最高的区域为 5×104W/m3,最低的区域为 0.5×104W/m3。随着负载电流的增大,相对较强焦耳发热功率的区域逐渐扩大。
真空接触器导电回路的弯曲部分发热相对较为严重,这是因为在弯曲部分电流线有轻微的收缩现象,从而形成了一定的收缩电阻效应,这一电流收缩的结果便是使得导电回路中的弯曲部分的实际电阻率要略大于材料的单位长度电阻。因此,在大容量真空接触器的热设计过程中,应尽量减少导电部件的弯折出现,如果不能避免,也应对弯曲部位予以重视,如在过负载条件下考虑添加散热装置或强制对流散热设备。
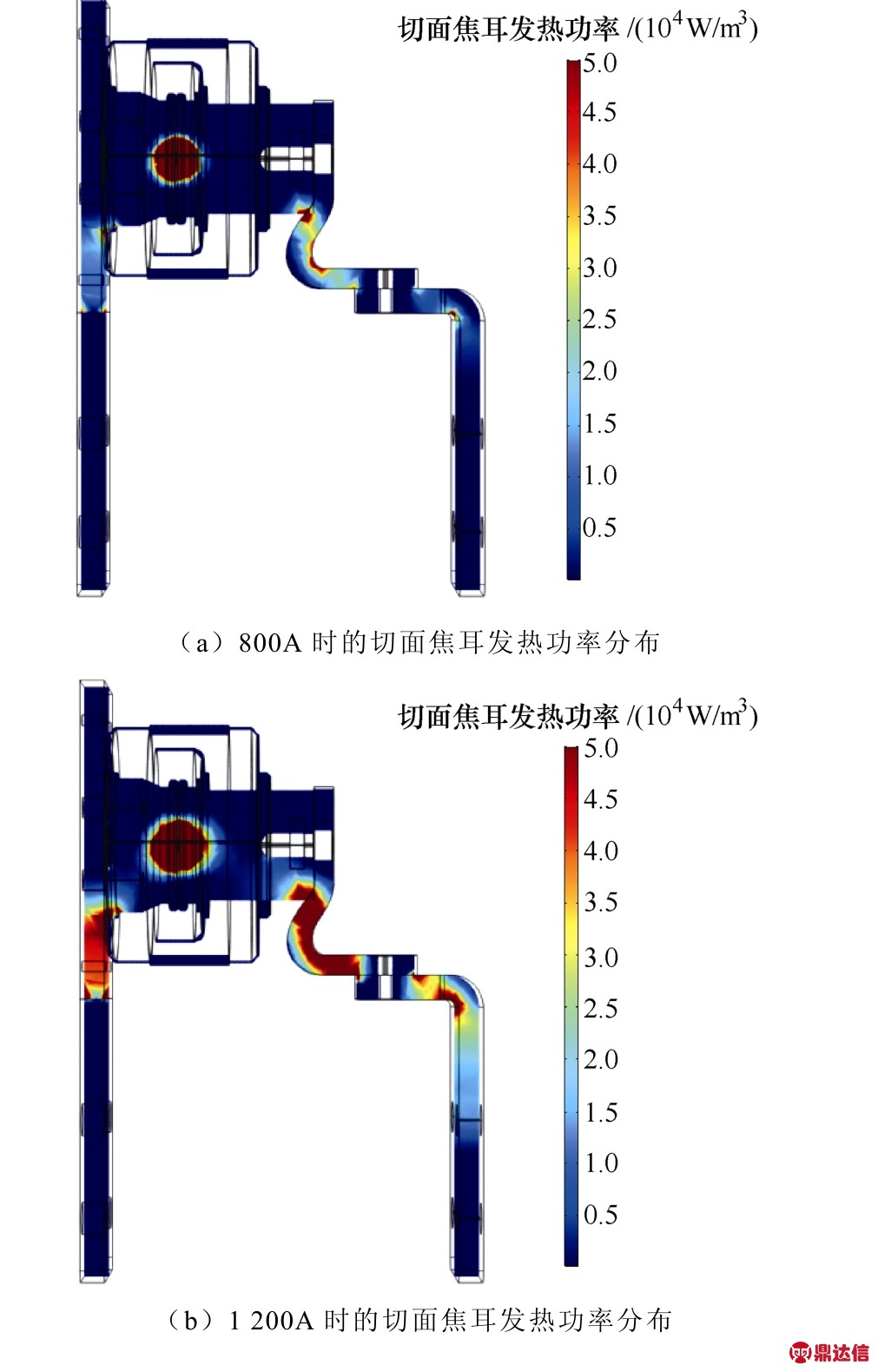
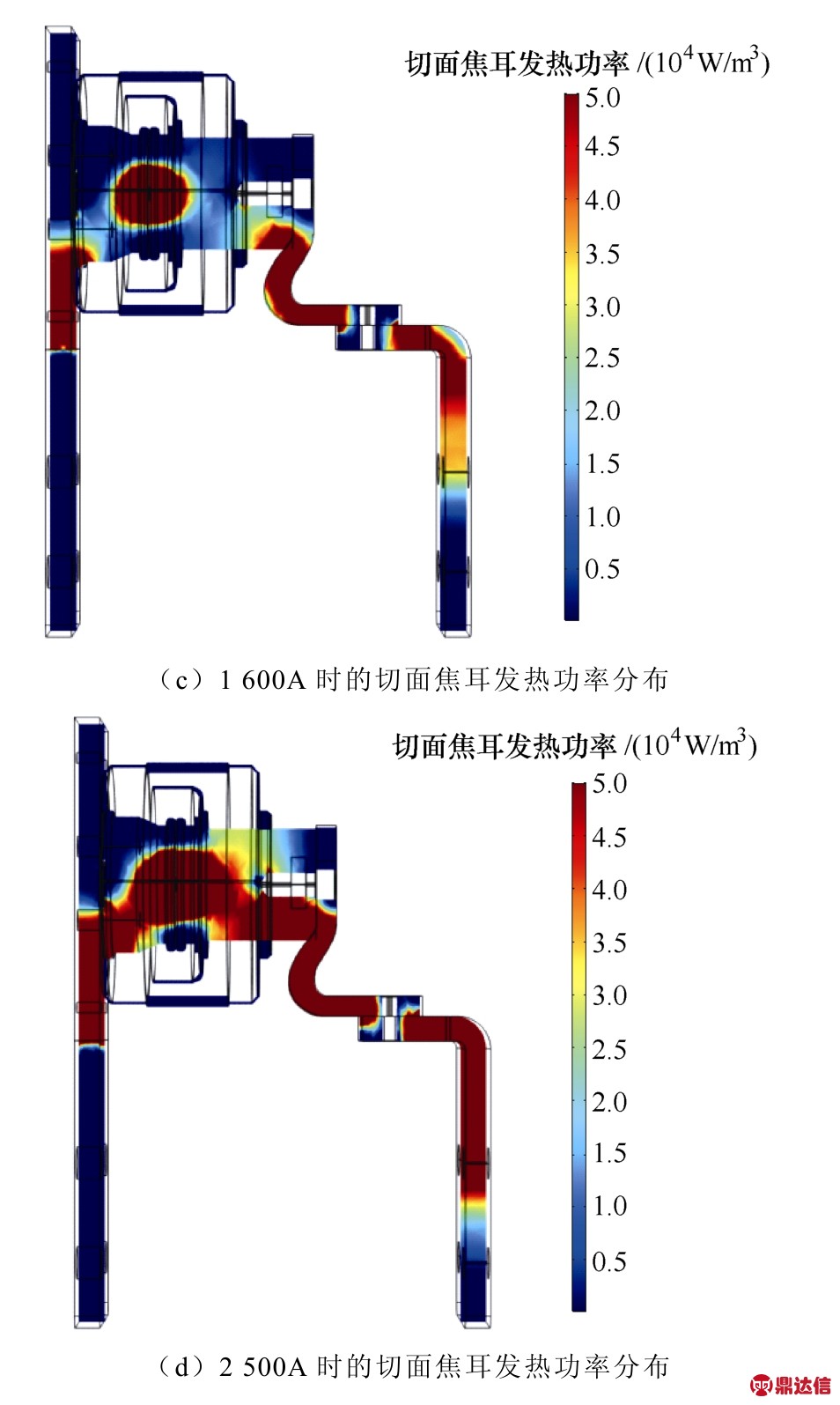
图10 不同电流下焦耳发热功率分布
Fig.10 Joule heat generation power density distribution with different current
4 结论
本文搭建了大电流条件下真空接触器温升特性测量试验平台,实验研究了不同电流下的真空接触器温升特性,仿真计算了真空接触器接触系统导电回路的温升特性参数,并与试验结果进行了对比,得到如下结论:
1)通过试验发现真空接触器外壳、上下导电排3个测温点在 2 500A/180min温升未超过极限允许温升,其中上导电排温升在1 600A及以下时均略高于下导电排温升,最大差值为 1.1K;在 2 500A时导电排的温升时变曲线基本重合,最大温升出现在上导电排测温点 51.9K;接触器外壳因温升较低在通电时间较短、电流较小的工程建模仿真中可以忽略。
2)搭建了适用于大电流条件的真空接触器温升特性测量试验平台,采用水冷可变负载电阻的设计,有效解决了 2 500kA/180min恒定负载条件下温升引起的阻值波动及潜在安全隐患,该可调节水冷负载电阻满足的指标为阻值调节范围 0~5mΩ,最大负载功率9 000W。
3)基于 COMSOL软件建立电热耦合分析模型,并对不同电流下的真空接触器触头系统的温升特性进行仿真计算,计算结果与试验数据吻合较好,最大相对温升误差为13.4%。
4)通过仿真结果发现,真空接触器触头及导电回路中的弯曲部分是焦耳发热功率密度相对较为集中的区域,因此在大容量真空接触器热设计过程中需要重点关注。