摘 要:目的 研究真空脉冲渗碳过程中“强渗”与“扩散”脉冲分布占比对 20CrMnTi钢渗碳层晶粒粗化行为及组织性能的影响。方法 采用一种电磁感应真空变脉冲渗碳新方法,经“原脉冲”、“变强渗”、“变扩散”、“变压力”四种工艺,制备了组织致密的20CrMnTi钢渗碳层。利用SEM、EBSD、自动显微硬度仪以及XRD应力衍射仪等对渗碳层的微观形貌、晶体相变特征、硬度梯度以及表面残余应力进行了深入分析。结果 对比分析四种工艺方法,“变强渗”工艺虽使20CrMnTi钢渗碳层厚度达到1450 µm,但渗碳层中仍存在大量块状Fe3C;“变扩散”工艺使20CrMnTi钢渗碳层的Fe3C含量下降到3.88%,残余奥氏体含量下降到7.32%,厚度达到1320 µm,其中表层0~60 µm范围内,硬度提高到780 HV0.5,表面残余压应力增加到-231 MPa。故“变扩散”工艺使渗碳层组织性能最佳。结论 “变强渗”工艺增加了渗碳前期表层与内部的碳浓度差,提高了碳原子扩散驱动力,利于渗碳层生长;“变扩散”工艺在渗碳后期使碳化物进一步溶解,这利于碳原子向渗碳层内部充分扩散,降低了渗碳层的碳化物析出和残余奥氏体形成。
关键词:电磁感应;真空渗碳;变脉冲;强渗-扩散;EBSD;微观组织
20CrMnTi钢是典型的渗碳钢,通过渗碳淬火可以提高钢表层的硬度和耐磨性,且渗碳淬火后心部具有强韧性[1-3],因此被广泛应用于生产制造齿轮、齿轮轴、齿圈等重载零件[4-5]。石巨岩等[6]采用预渗碳加循环渗碳方法对20CrMnTi钢进行表面处理,发现渗碳层中形成了大量弥散分布的粒状碳化物,其表面硬度达到1057HV0.1,耐磨损性能比常规渗碳提高20%。康承飞等[7]通过液相感应渗碳技术对20CrMnTi钢进行了渗碳处理,发现渗碳层的组织主要是针状马氏体。其中,930 ℃渗碳10 min得到的渗碳层厚度为255 μm,渗碳层的最高硬度为810HV0.3。王昊杰等[8]基于真空低压渗碳炉,研究分析了不同渗碳工艺参数对20CrMnTi钢晶粒粗化行为的影响规律。结果表明,20CrMnTi钢的奥氏体晶粒长大规律符合 Beck关系式,且奥氏体晶粒随加热温度的升高呈指数形式长大,温度越高,晶粒生长指数越大。
上述文献研究表明,20CrMnTi钢渗碳层中弥散的碳化物、残余奥氏体的尺寸与分布会影响渗碳层性能。贵州大学金属材料表面处理研究室通过深入分析20CrMnTi钢渗碳动力学及渗碳控速机理[9]发现,20CrMnTi钢渗碳过程在渗碳前阶段主要受“表层吸附”控制,而在渗碳后期,由于碳原子的扩散路径增加,是以“内扩散”控速为主。但在渗碳过程中,如何控制碳含量对20CrMnTi钢晶粒粗化行为的影响尚不明确。因此,本文针对“前阶段碳势不足,后阶段扩散能力不足”的特点,提出电磁感应真空变脉冲渗碳方法,通过调整渗碳过程中“强渗”及“扩散”占比的方法,研究20CrMnTi钢渗碳层晶粒粗化行为、组织演变规律及性能。
1 实验
实验材料为 20CrMnTi钢,试样尺寸 φ15 mm×8 mm。实验前,试样经 600、800、1000、1500、2000、2500、3000号砂纸依次研磨后,采用粒度为 W0.25的抛光剂抛光,最后进行无水乙醇清洗、吹干等预处理。实验采用课题组自主研制的真空电磁感应渗碳装置[10],如图1所示。实验时,渗碳温度为 940 ℃,渗碳介质为C2H2和CH4比例为1∶5的混合气体,采用“充气强渗-真空扩散”交替型工艺[11-12],即先向装置真空管内充入一定压力的渗碳介质并保持压力,使试样进入强渗阶段,随后抽真空进入扩散阶段,交替进行8个强渗-扩散周期,随后充入1 atm的氩气,降温至880 ℃并保温10 min,之后进行油淬,经180 ℃低温回火2 h,最后取出试样。
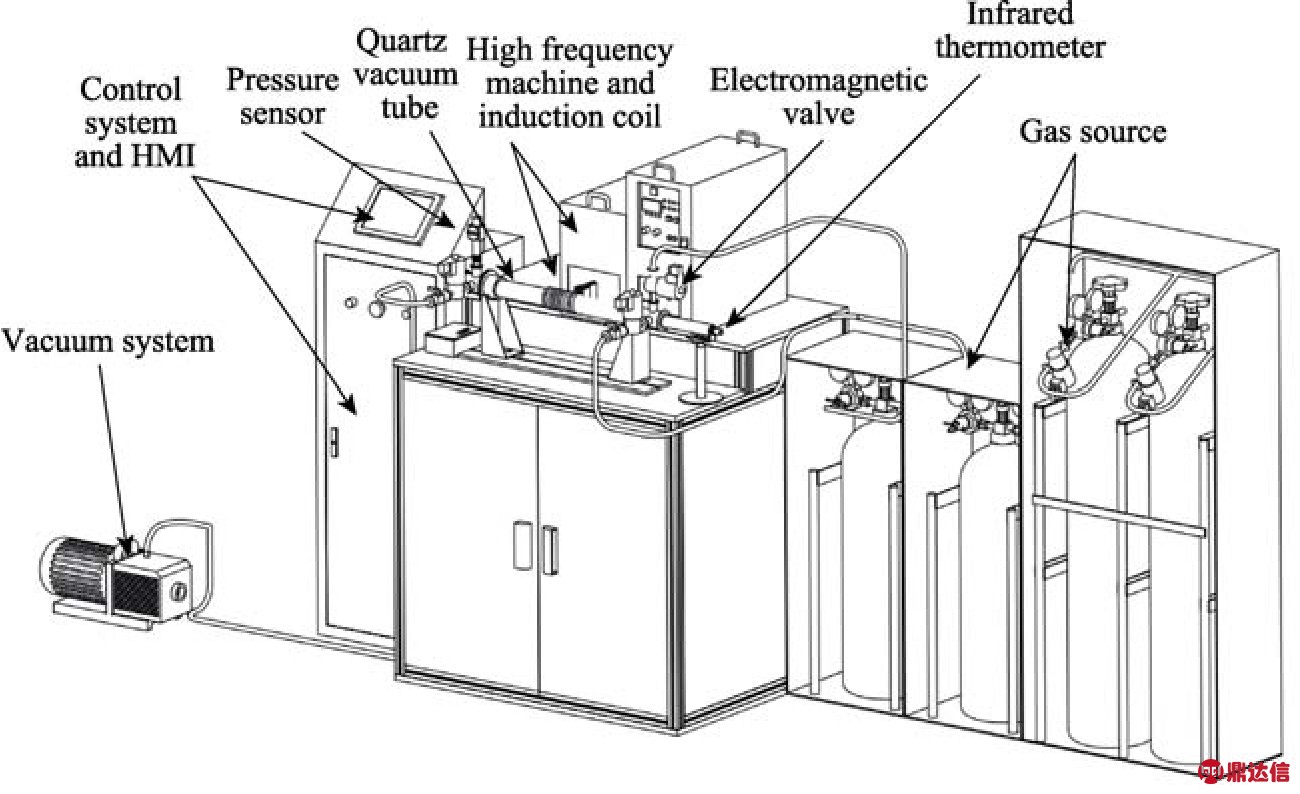
图1 电磁感应真空渗碳装置示意图
Fig.1 Schematic diagram of electromagnetic induction vacuum carburizing device
实验采用四种工艺,其强渗-扩散脉冲时间分布及渗碳压力如图2所示。工艺1:循环8个固定的脉冲,强渗压力为-70 kPa,保压强渗-真空扩散时间分配为10 min-5 min(以下称为“原脉冲”)。工艺2:循环8个强渗时间随循环次数逐步延长的变脉冲,其中保持强渗压力-70 kPa和真空扩散5 min脉冲时间不变(以下称为“变强渗”)。工艺3:循环8个真空扩散脉冲时间随循环次数逐步延长的变脉冲,其中保持强渗压力-70 kPa和强渗10 min脉冲时间不变(以下称为“变扩散”)。工艺4:循环8个强渗压力随循环次数逐步减小的变脉冲,其中保持真空强渗-保压扩散脉冲时间分配为5 min-10 min,并始终保持脉冲时间不变(以下称为“变压力”)。
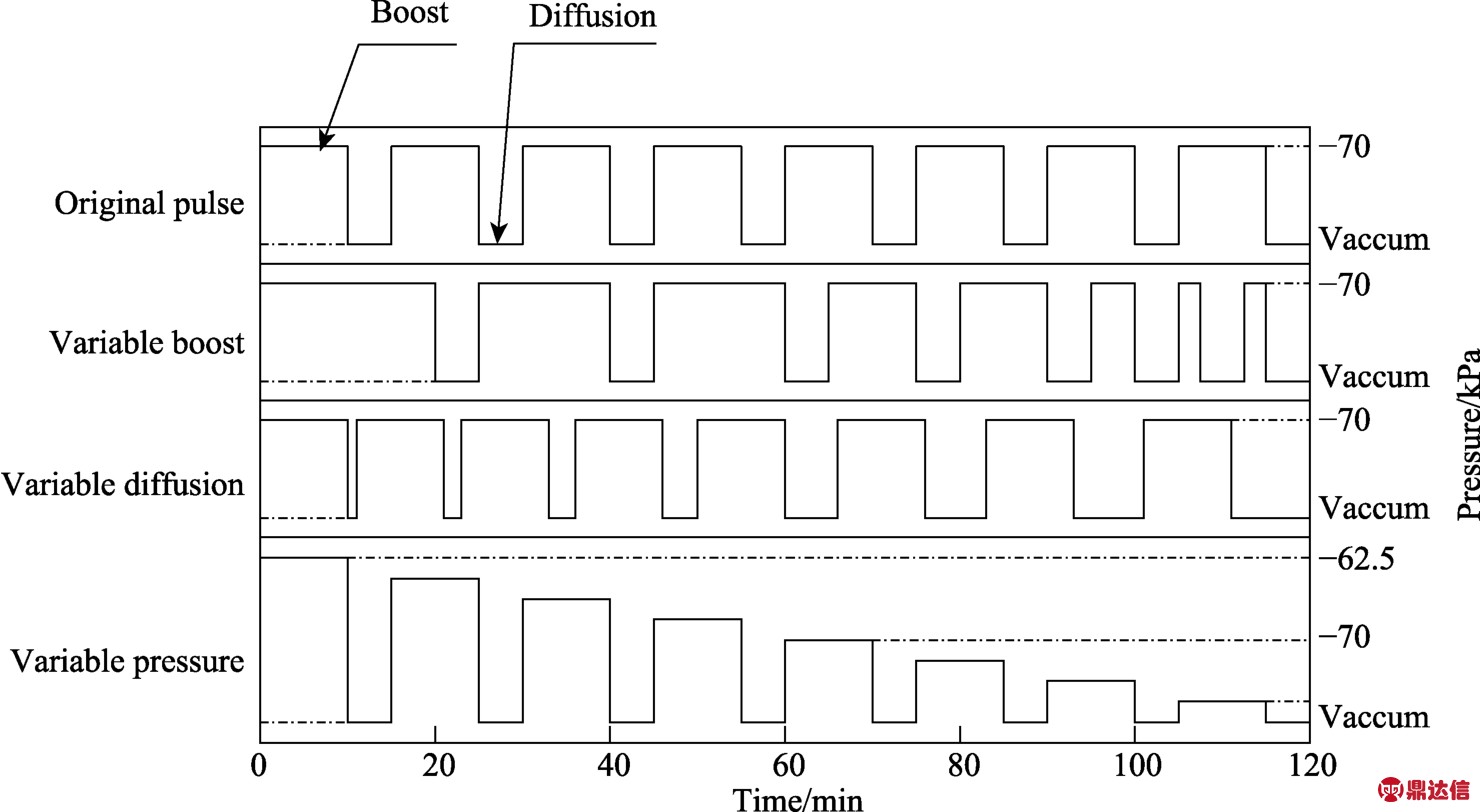
图2 强渗-扩散脉冲时间以及渗碳压力分布
Fig.2 Distribution of boost-diffusion pulse and carburizing pressure
采用场发射扫描电子显微镜(Inspect F,美国)分析试样渗碳层微观组织形貌和沿渗碳层方向的元素分布。采用X射线光电子能谱仪(EscaLab 250Xi,美国)检测渗碳试样表面碳含量。采用电子背散射衍射技术(Oxford Instruments,英国)分析试样渗碳层截面100 µm×100 µm面积区域内的残余物相含量及晶体取向。采用射线应力衍射仪(X-350A,中国)分析渗碳层表面残余应力,测试条件:靶材 CrKα,管电压40 kV,管电流40 mA。采用自动显微硬度仪(MHV-2.0,中国)对试样截面进行硬度梯度测量,其中载荷0.49 N,间距70 µm,保荷时间15 s。
2 结果及分析
2.1 渗碳层相结构及微观形貌
图3和表1分别是经四种电磁感应真空脉冲渗碳工艺处理后的渗碳层微观形貌以及试样表面碳含量。由图3可知,渗碳层组织主要为高碳马氏体、碳化物及残余奥氏体的复合组织。由于20CrMnTi钢真空脉冲渗碳后期主要是受“活性碳原子内扩散”控制,渗碳前表层聚集大量碳原子而得不到充分扩散,表层组织的奥氏体中含碳量大大增加,从而形成较大的块状碳化物和大量残余奥氏体,并随着渗碳层深度的增加,碳浓度下降,片状马氏体开始逐渐向板条状马氏体转变,而块状碳化物逐渐减小至消失,如图3a所示。由表 1可知,“变强渗”试样的表面碳含量略高于“原脉冲”,图3b表明渗碳层组织仍有大量块状碳化物存在,但块状碳化物尺寸相比图3a较小,表明尽管在渗碳前期加强碳原子的吸附渗入,能提高试样表层与内部碳浓度差,以此提高渗碳后期碳原子扩散的驱动力,但也不能完全避免块状碳化物的析出。图3c中,表层组织在奥氏体晶界中,基本无明显块状结构的碳化物形成,相应的表面碳含量仅为0.56%。其原因在于,逐步延长真空扩散渗时间,能促使表层在渗碳前期形成的碳化物进一步溶解,利于碳原子向渗碳层内部充分扩散,进而使表面碳含量下降。图3d所示的表层组织也存在大量的块状碳化物。实验时,试样表层有炭黑形成,可能原因是渗碳过程中碳势浓度过高,表层形成的炭黑阻止活性碳原子吸附、扩散,导致表面碳含量相对较低以及较少的块状碳化物析出。
2.2 渗碳层物相分布与晶体相变特征分析
为了研究经调整的吸附、扩散控速机理对渗碳层成分以及组织相变的影响,进一步分析了“原脉冲”和“变扩散”工艺处理后,试样渗碳层的物相分布和晶体相变。采用电子背散射衍射(EBSD)扫描试样渗碳层,获得的相分布和相含量如图4和表2所示。由图4的物相分布可知,20CrMnTi钢渗碳层主要为体心结构的马氏体、面心立方结构的残余奥氏体以及Fe3C化合物组成的复合组织。图4a是“原脉冲”试样渗碳层的相分布,其含有大面积的面心立方结构残余奥氏体,含量为24.52%。图4b是“变扩散”试样的物相分布,通过加强扩散过程后,渗碳层富集碳原子的扩散更充分和均匀,残余奥氏体形成量明显比前者少很多,含量仅为7.32%。少量细小均匀的残余奥氏体,对渗碳层的组织与性能有一定的益处[13-14]。由图4a、b中可知,未分解的残余奥氏体在渗碳层最表层的含量要比次表层较少,主要是由于表面脱碳、内氧化或碳化物的析出,导致奥氏体含碳量降低[15]。图4a中渗碳层最表层组织中出现不连续粗大块状的碳化物,Fe3C百分比为5.75%。与之相比,图4b中碳化物大多为细小颗粒且分布数量明显减小,Fe3C含量下降至3.88%。由此表明,“变扩散”工艺有助于减少残余奥氏体的形成以及Fe3C等碳化物的析出。
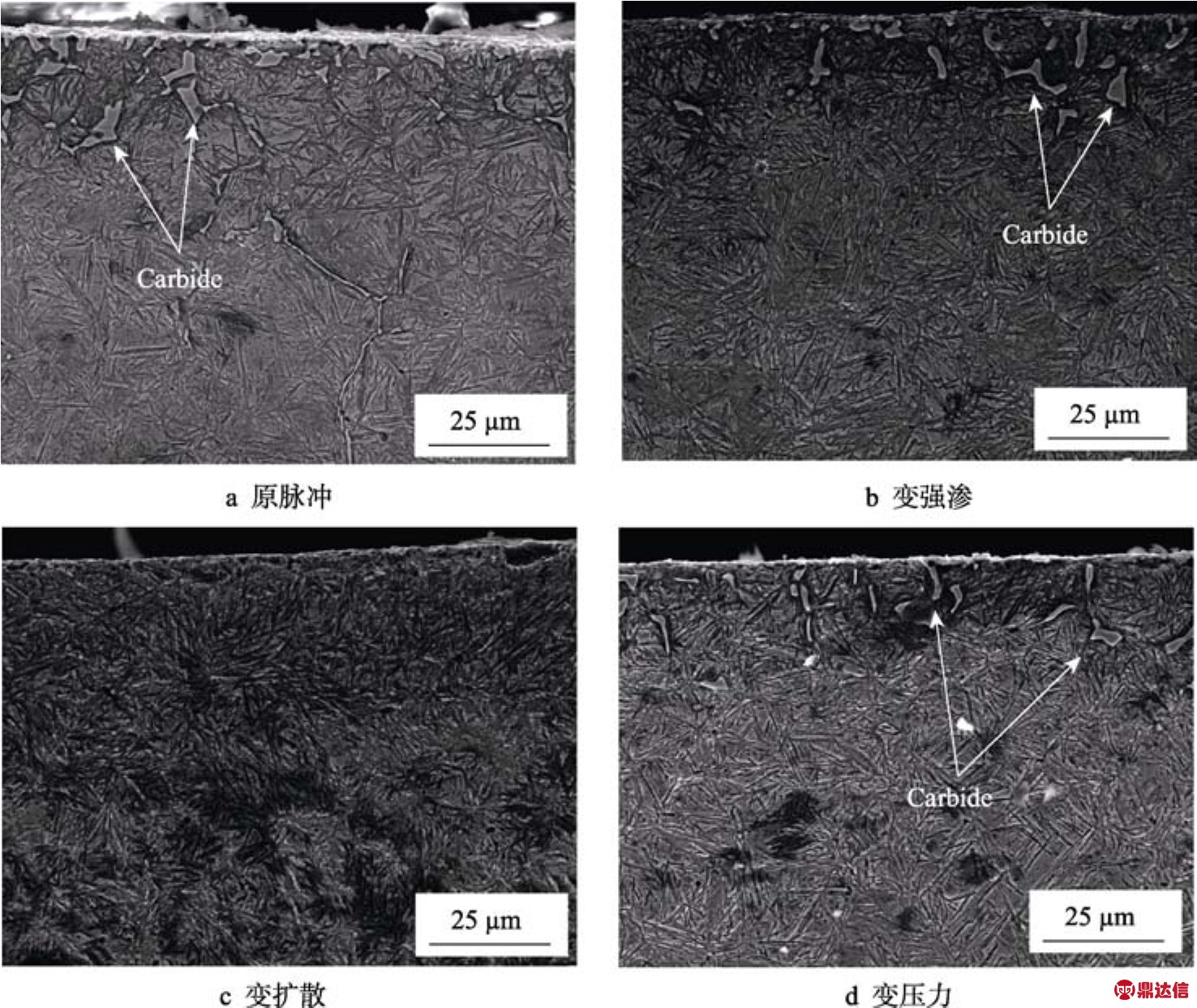
图3 不同工艺下20CrMnTi钢渗碳层微观形貌
Fig.3 metallographic structure of carburized layer of 20CrMnTi steel under different process:a)original pulse;b)variable diffusion;c)variable diffusion;d)variable diffusion
表1 不同渗碳工艺下20CrMnTi钢的表面碳含量
Tab.1 Surface carbon contents of 20CrMnTi steel under different carburizing processes
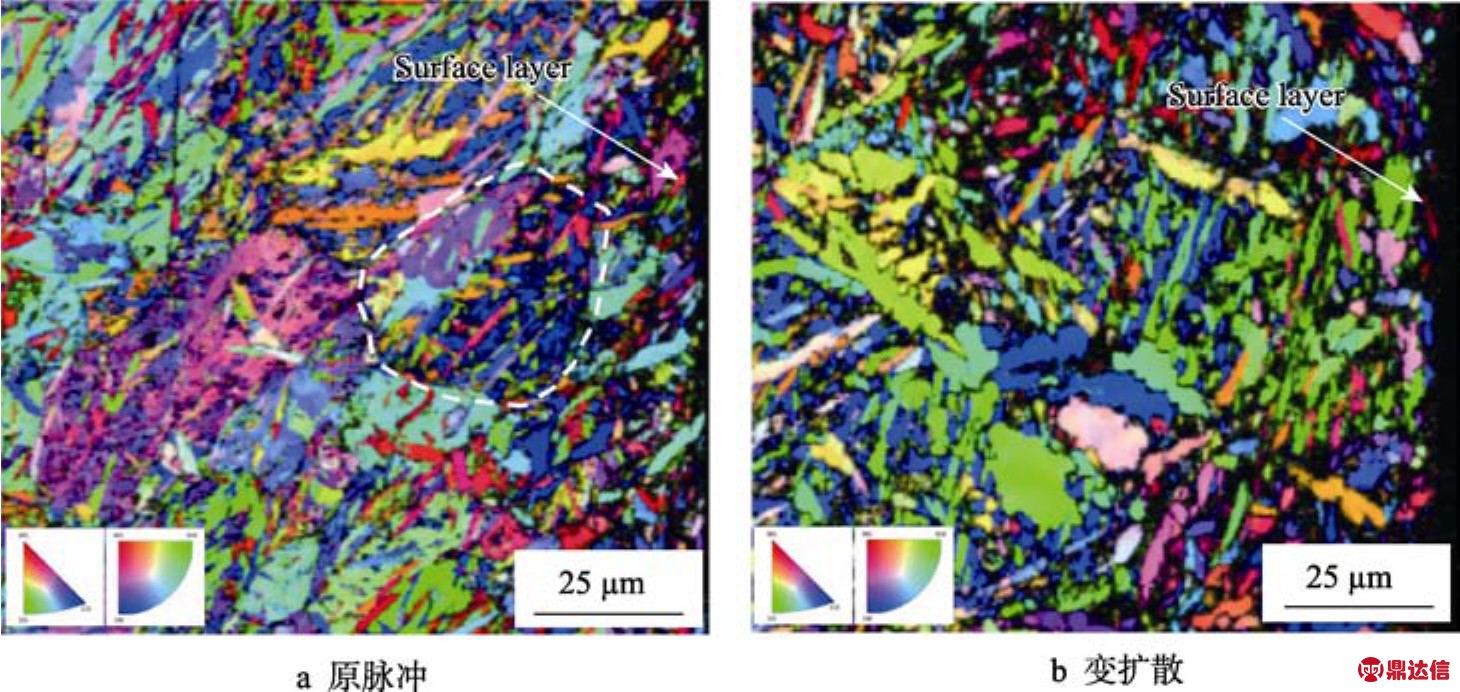
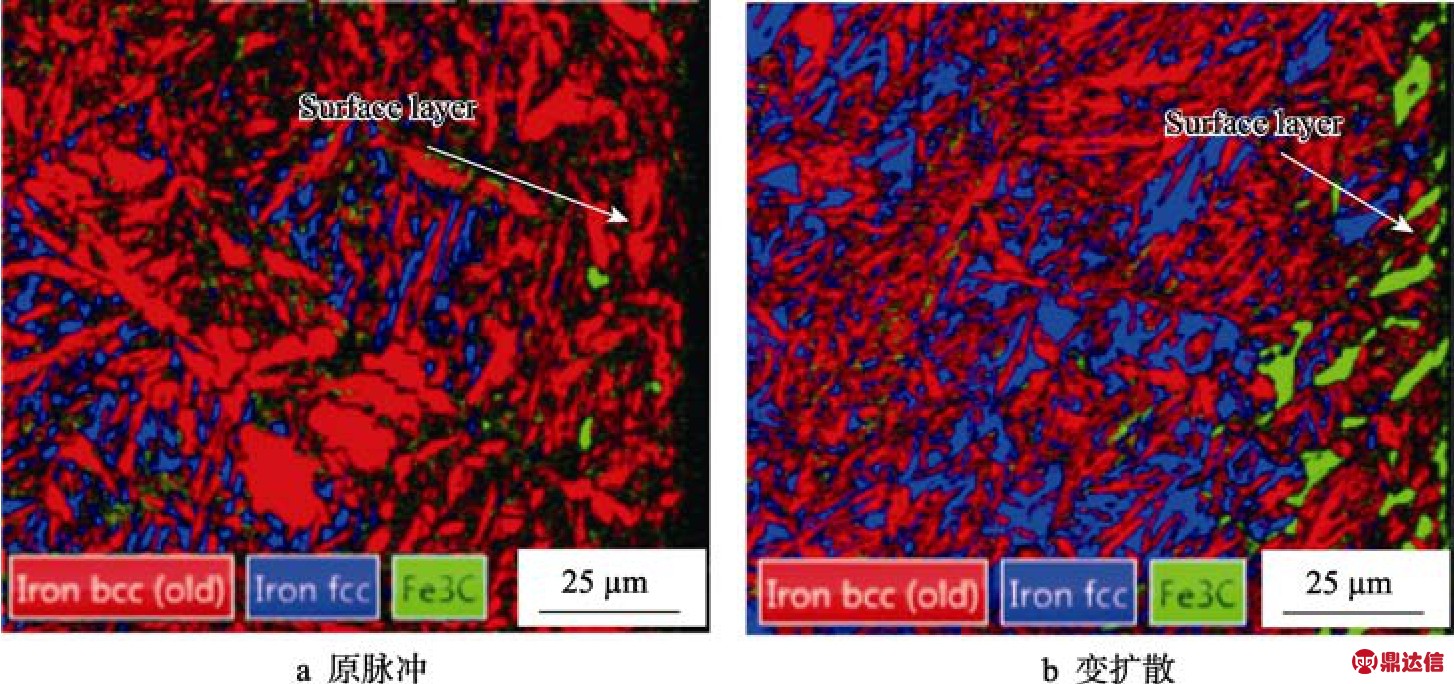
图4 渗碳层表层物相分布
Fig.4 Phase distribution of carburized layer:a)original pulse;b)variable diffusion
表2 渗碳层物相百分比
Tab.2 Phase percentage of carburized layer
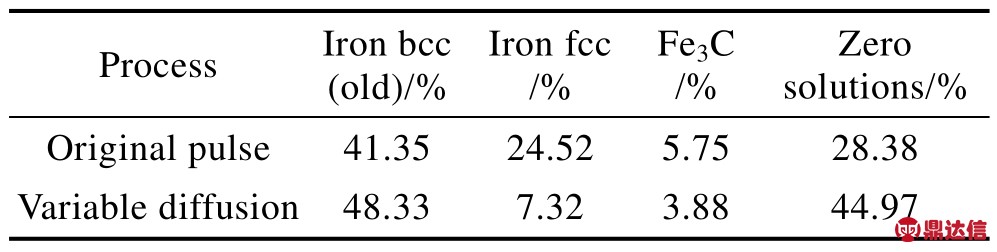
图5为采用电子背散射衍射(EBSD)对试样渗碳层扫描获得的IPF取向图。从图5a选取的白色边框标记区域可以明显辨析出,该区域为渗碳层内一个独立的原奥氏体组织,在原奥氏体晶界内约有3~5个小区域,每个区域代表原奥氏体中形成的一个马氏体域,域内的马氏体板条接近平行排列并具有相近的取向。其次,从图5a中可以看出,存在大量平行于取向介于<101>和<111>之间(粉色)的板条马氏体组织,相邻晶粒取向的变化较小。在受到外力的情况下,晶粒与晶粒之间难以协调变形,易发生断裂。表明“原脉冲”渗碳工艺获得的渗碳层具有明显的原奥氏体晶界,且马氏体组织是在原奥氏体晶粒内形成的,同时,扫描渗碳层区域内存在大量相同取向的晶粒。与之相比,由图5b中可知,整个扫描区域,晶粒的取向杂乱、分布无规律且颜色对比度高,表层为相互交替穿插的相对细小的组织,次表层为相互交替穿插的大尺寸马氏体条,无明显原奥氏体晶界。
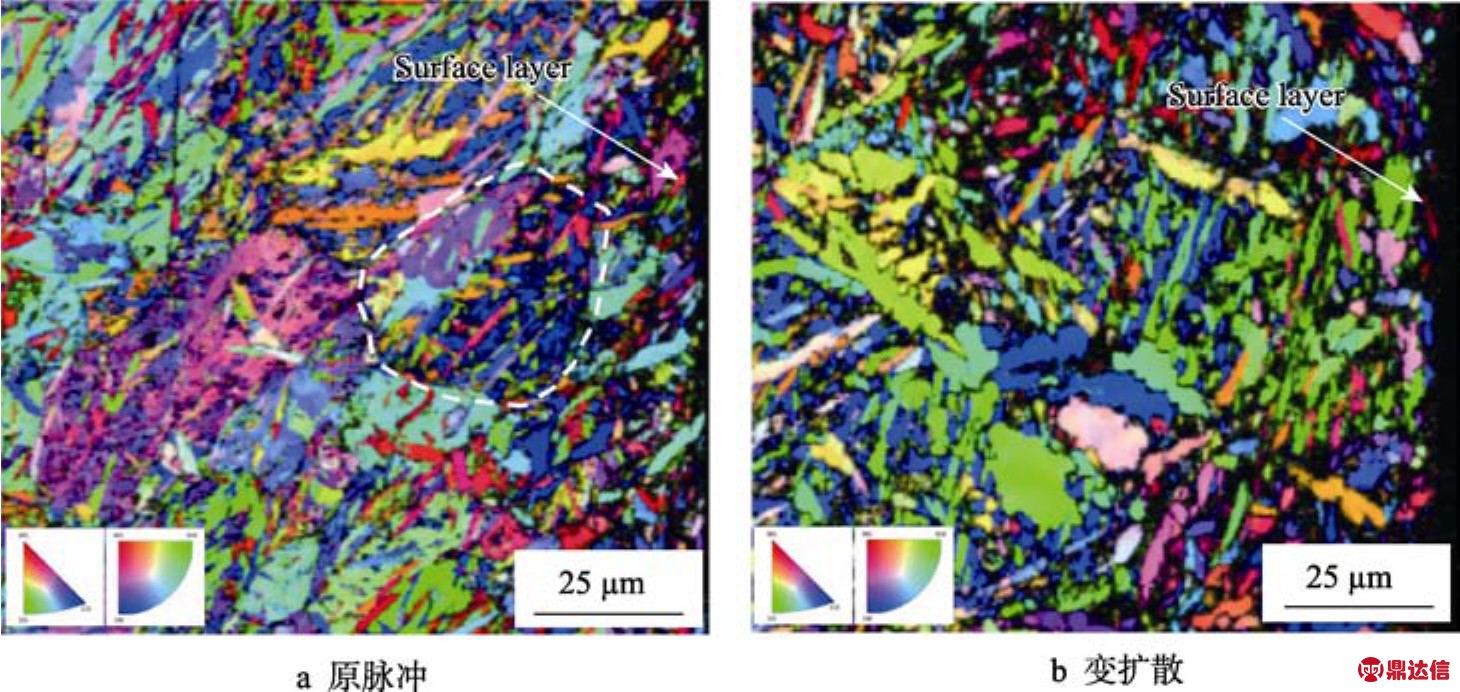
图5 渗碳层截面质量衬度图及取向图
Fig.5 Contrast and orientation figures for cross section mass of carburized layer:a)original pulse;b)variable diffusion
2.3 渗碳层硬度分布

图6 不同工艺渗碳后20CrMnTi钢截面硬度分布曲线
Fig.6 Sectional hardness distribution curves of 20CrMnTi steel under different carburizing processes
图6为20CrMnTi钢经不同电磁感应真空脉冲渗碳工艺处理后的渗碳层硬度分布曲线。由图可知,“原脉冲”工艺试样的渗碳层厚度为 1200 µm;“变强渗”工艺试样由于碳原子的充分渗入,渗碳层厚度增加至1450 µm。其次,“原脉冲”和“变强渗”工艺试样的表面硬度均在670 HV0.5左右,并随渗碳层由表及里,先小幅下降,后上升至硬度峰值。其原因为,渗碳层硬度分布主要取决于淬火后马氏体的碳含量、碳化物和残余奥氏体的含量。由图4可知,20CrMnTi钢渗碳淬火后,其表层存在大量块状碳化物和残余奥氏体分布,块状碳化物以及试样次表层比最表层含较多的残余奥氏体,从而使表层一定范围内的硬度小幅下降,而大量滑移特征的残余奥氏体导致表层0~60 µm范围内的硬度值整体偏低[16]。“变扩散”工艺试样的硬度分布与前二者的差异主要在于,表层0~60 µm范围内硬度值提高至780 HV0.5左右,未出现下降,而是小幅上升就达到硬度峰值,渗碳层厚度也增加至1320 µm。主要原因为,经过加强扩散环节的渗碳层残余奥氏体量减少,并且不连续、细小弥散分布的碳化物起到了弥散强化作用,表层0~60 µm范围内硬度值得到显著地提高;而足够的扩散周期使碳原子扩散路径延长,渗碳层厚度进一步增加。此外,“变扩散”工艺试样的表层硬度值并不是最大值,说明此工艺的强渗-扩散占比还需要进一步优化。“变压力”工艺试样的表层硬度值、硬度峰值均劣于前者,渗碳层厚度仅有1050 µm,其可能原因是,碳势过高使试样表面形成炭黑,阻碍了活性原子渗入,造成同一渗碳层深度的碳质量分数比其他工艺相对较低。
2.4 表面残余应力分析
工件经热处理在表面形成的残余压应力,可以改善工件表面的性能,使工件的抗接触疲劳性、耐磨性等得到提高[17]。为此,利用XRD应力测定仪对“原脉冲”工艺和“变扩散”工艺试样表面残余应力进行测试分析。经测试,“原脉冲”工艺试样的表面残余应力达到 33 MPa,表征为残余拉应力;“变扩散”工艺试样的表面残余应力达到-231 MPa,表征为残余压应力,较前者表面残余应力增加了 260 MPa。其可能原因是,渗碳层的表层组织分布了较多的块状碳化物和残余奥氏体,表明在奥氏体发生相变转化为体心立方马氏体的过程中,渗碳层表层组织的马氏体相变量较少,而次表层马氏体相变量较多,使得表层体积相对于次表层收缩,进而表面残余应力呈拉应力[18],如图3a所示。而对比图3c可知,经“变扩散”工艺后,渗碳层表层组织无明显碳化物和残余奥氏体,即表层组织在淬火过程中,奥氏体具有完全转变为马氏体的倾向,马氏体相变的体积膨胀效应使得表面产生了较大的残余压应力,可以提高20CrMnTi钢的疲劳性、耐磨性等[19]。