摘要:针对真空注型(VC)产品质量依赖于工艺设计人员经验,造成VC装备自动化程度低、加工柔性差、产品质量难以控制等问题,基于计算机图形学和人工智能技术,建立一种面向VC工艺的质量控制模型。通过构建体素化模型,近似求解壁厚、均匀程度、体积等模具型腔几何特征参数;在此基础上,融合案例推理和神经网络推理技术,建立型腔几何特征参数与成形工艺间的关系模型,充分利用历史案例,实现初始工艺参数的智能推荐;利用基于规则的模糊逻辑推理方法,挖掘工艺设计人员经验,对试模后的产品缺陷进行智能修正。生产实例说明,基于上述思想方法和推理机制的质量控制模型有较好的推理和质量控制能力。
关键词:真空注型;产品特征;体素化;质量控制
0 引言
真空注型(vacuum casting,VC)工艺是快速模具(rapid tooling,RT)技术中应用最为广泛的工艺方法,该工艺属于聚合物反应加工范畴,由双组分液态低黏度聚酯基树脂在真空环境下快速混合后注入模具,经过交联反应和冷却固化后形成塑料产品。由于该工艺具有反应成形温度低、制造周期短、功耗少的优点[1],因此被广泛应用于航空航天、汽车、家电、医疗等行业。
VC工艺成形过程是包含化学反应、液体流动及传热传质等复杂物理化学现象的聚合物加工过程,其成形工艺参数和产品质量之间存在非线性强耦合和时变性的关系,属于典型的弱理论强经验领域[2],加工过程中常常会因工艺参数设置不当,产生气泡、欠注、飞边及翘曲等质量缺陷。目前对VC产品的成形质量控制则完全依赖于工艺设计人员的经验,通过试模来保证,因而造成了VC技术存在装备自动化程度低、加工柔性差、产品质量难以控制等问题,制约了该技术的进一步发展。
人工智能技术具有自学习、推理、判断和自适应能力,近年来随着制造业与人工智能技术的不断融合[3],该技术已在设计、制造、故障诊断等领域得到了广泛应用。罗晨等[4]基于案例推理技术建立了一种夹具设计案例特征表示的新型检索机制,采用统一建模语言和面向对象的表示方式,实现了特征信息存储的结构化和模块化,并通过搜索节点对应约束的最大相似连通子图,确定了零件的几何特征相似度,生产实例验证了该新型检索模型的有效性和实用性,缓解了夹具设计过程对个人经验的依赖程度;刘伟等[5]利用遗传神经网络算法建立了工件加工质量与效率和相关磨削工艺参数间的非线性映射关系,并基于正交试验法的分析结果对遗传神经网络算法进行了改进,实现了相关磨削工艺参数的优化,试验结果表明,该方法能够缩短氮化硅陶瓷材料球面廓形工件数控磨削工艺制定与操作的时间;曾莎莎等[6]结合神经网络算法和遗传算法的优点,提出了一种以倒传递神经网络法为基础的加工工艺参数优化方法,对薄壁件铣削加工工艺参数进行优化,试验结果表明,该方法能够有效提高产品质量与加工效率;CHEN等[7-8]结合正交试验、BP神经网络、粒子群算法和模拟退化算法,对注塑成形工艺参数进行了多目标优化,试验结果表明,所提方法不仅提高了产品的质量,而且有效地减少了产品的塑性变形;ZHAO等[9]利用Kriging模型建立了成形工艺参数与产品质量间的关系模型,并采用遗传算法求解,优化了工艺参数,减小了制品翘曲量和生产周期;时培明等[10]针对齿轮故障诊断问题,提出了一种基于深度学习、特征提取和粒子群支持向量机状态识别相结合的智能诊断方法,相比传统诊断方法,该方法摆脱了对大量信号处理知识和诊断工程经验的依赖,节省了大量时间,取得了较高的监测诊断精度。从近年的研究可以看出,越来越多的学者将制造领域的专有知识注入人工智能模型中,形成了一系列融合创新方法,成效显著。
考虑当前制造业智能化发展趋势以及VC技术在快速制造领域所发挥的作用,如何将VC领域专有知识与人工智能技术相结合,将工艺设计人员的经验运用到VC产品成形过程中,摆脱VC产品质量依赖工艺设计人员经验,是使VC从“可以成形”向“智能高效成形”转变的关键。基于此,针对VC工艺特点,本文结合计算机图形学和人工智能技术,提出一种面向VC工艺的质量控制方法,模拟工艺设计人员的经验思维,实现对产品质量的智能控制。
1 质量控制模型框架
本文融合案例推理(case-based reasoning,CBR)、神经网络推理(neural network reasoning,NNR)和模糊推理(fuzzy-based reasoning,FBR)技术,提出一种面向VC工艺的质量控制模型方法。首先,采用CBR技术模拟工艺设计人员“借鉴”的思路,从历史案例库中提取相似度较高的案例,并“借鉴”该案例的工艺方案,推测出新产品的加工工艺参数。在案例推理失败的情况下,采用NNR技术模拟操作人员“经验推理”的思路,从历史案例所蕴含的经验中“推理”出新产品的加工工艺参数,并将推荐工艺参数用于试模。根据试模的结果,采用FBR技术对产品进行缺陷修正,并将最终修正结果以及新案例信息存储至案例数据库中,以便下次使用。质量控制模型框架如图1所示。
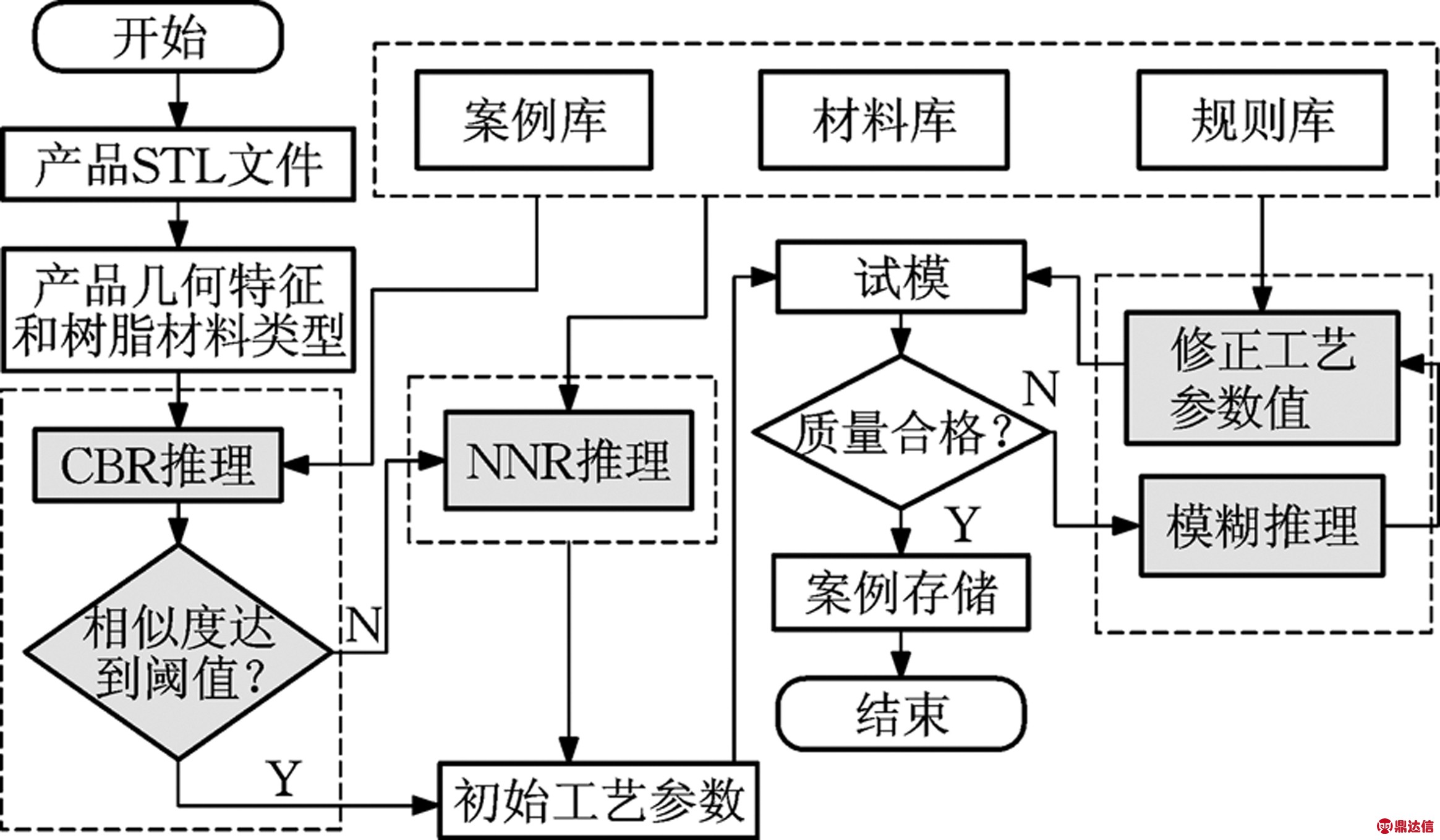
图1 质量控制模型框架
Fig.1 Architecture of quality control model
2 工艺参数推荐
2.1 产品特征获取
VC成形过程中伴随有化学反应,树脂体系会在短时间内由液态向固态转变。在前期研究中发现[11-13],在成形薄壁、结构复杂的大体积产品时,常常会在充模结束前出现提前凝胶现象(即树脂体系会由液态转变为不可逆的固态),导致流道堵塞,树脂体系不能流过流道,增加了气泡形成的几率,严重时甚至无法完成充模,造成欠注等缺陷。模具型腔的壁厚、体积、复杂程度等几何特征一定程度上决定了成形工艺参数大小。为获取模具型腔几何特征,本文以产品造型中常用的三角网格模型作为数据基础,通过构建模腔体素化模型方法,来近似求取模腔几何特征。
2.1.1 三角网格模型体素化
(1)采用 OpenMesh开发包,实现对产品STL(stereo lithography)文件的读取以及拓扑关系的建立。
(2)根据网格模型顶点坐标,建立STL模型最小包围盒,即最小边界点(xmin,ymin,zmin)和最大边界点(xmax,ymax,zmax)。
(3)沿z轴方向,采用逆向几何求交的算法[14]对STL模型进行等间距分层,分层间距为h,求取所有截面轮廓线段。
(4)对获得的截面轮廓线段沿y方向进行等间距扫描线填充,扫描间距为h,求得扫描线与截面轮廓线段交点,并以x坐标值对交点由小到大排序,进而得到一系列进出点,连接进出点得到扫描线;在此基础上,再对扫描线段沿x方向进行等间距离散化,离散间距为h,从而得到分层截面轮廓离散点阵。
(5)所有截面的离散二维点阵按分层方向上组合就构成了空间三维的均匀密度点阵。以点阵中每个点坐标(xv,yv,zv)为中心、边长为h作立方体,就构成了产品的体素化模型。采用三维数组结构形式表示,若数组内元素为0,则表示没有体素占据;若数组内元素为1,则表示有体素占据,体素单元(e,g,l)的索引计算公式如下:

(1)
某品牌电器壳体素化过程如图2所示。
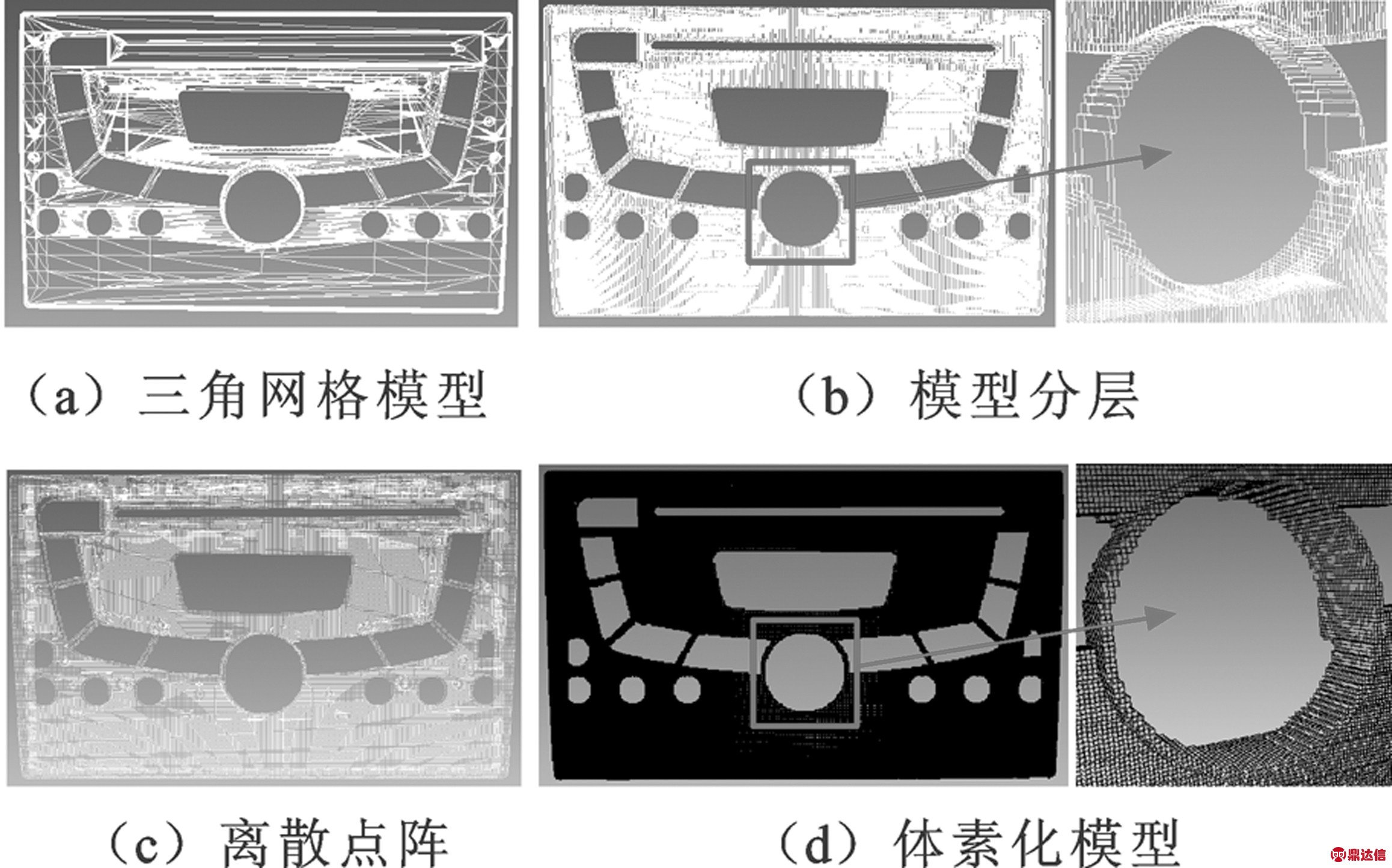
图2 体素化
Fig.2 Voxelization
2.1.2 特征获取
(1)体积。对于得到的体素化模型,其产品体积
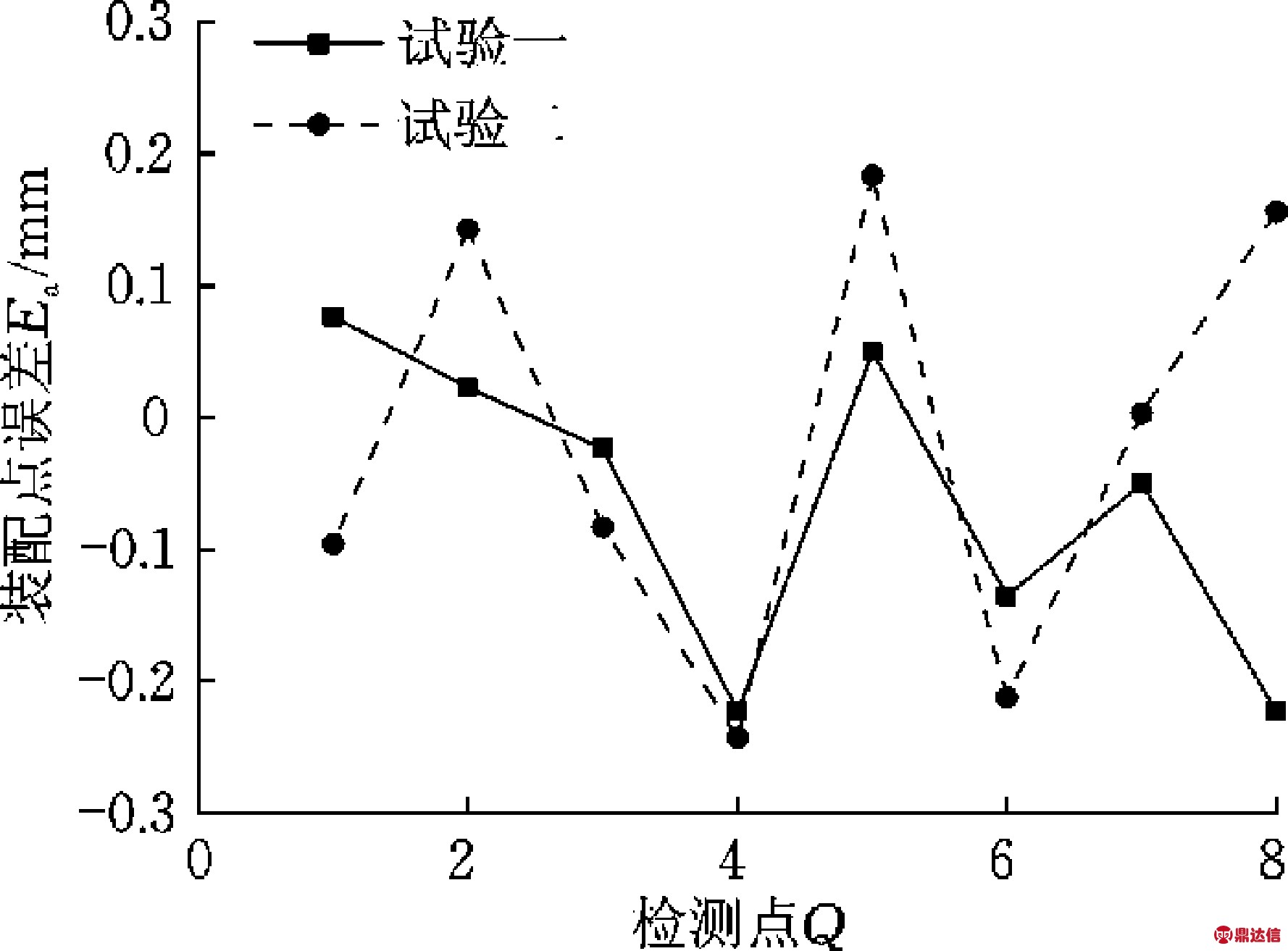
(2)
式中, vi为标记为“i” 的体素体积;nv为所有标记为“1”的体素个数。
(2)壁厚。对于产品的最小、最大壁厚,可通过欧氏距离变换计算即近似求解不同位置(层)内标记为“1”的体素中点到标记为“0”的体素中心的距离,如图3所示,其中,A1B1即以A1为中心点体素的最小欧氏距离。
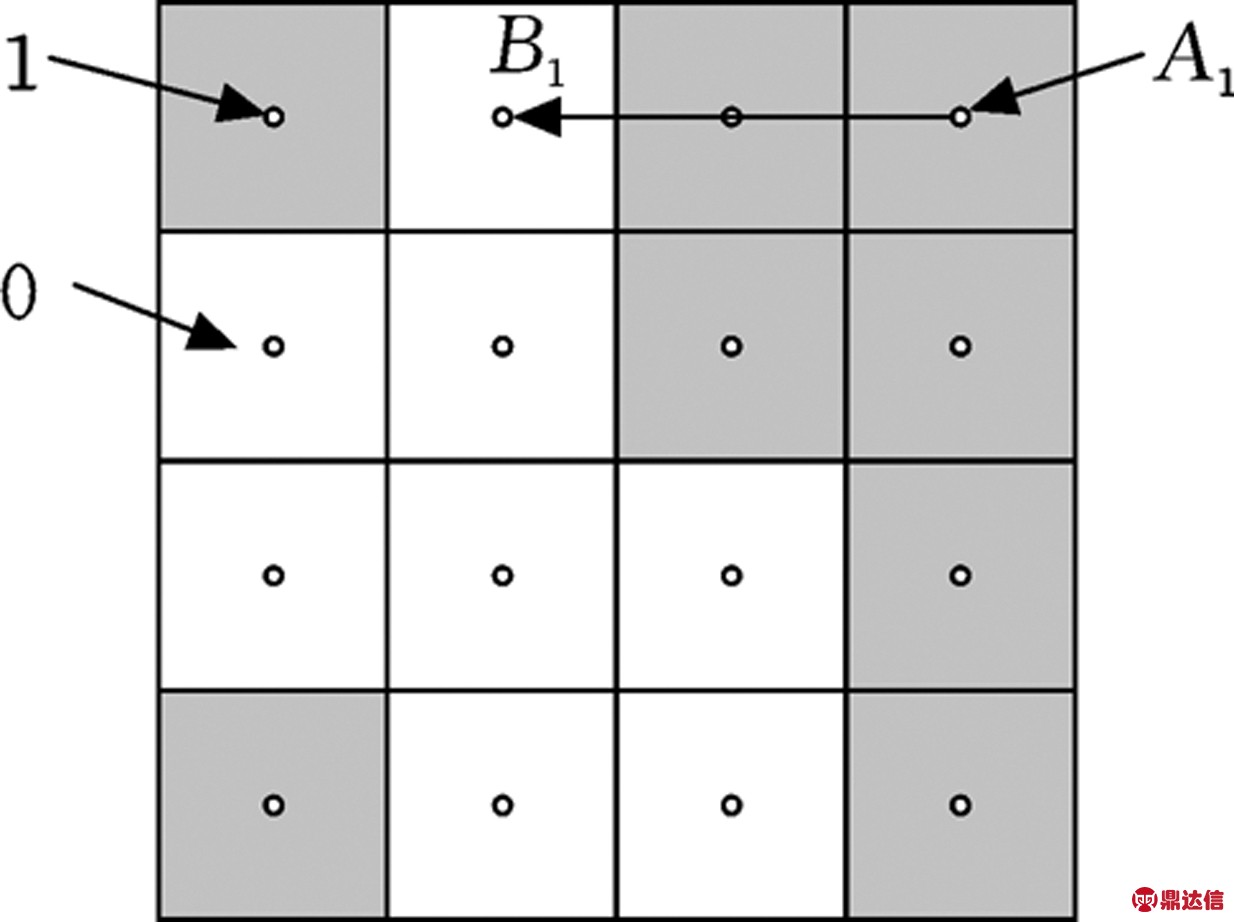
图3 模腔壁厚求解示意
Fig.3 Solution of cavity wall thickness
最大、最小壁厚dmax、dmin及第r层内第i个标记为“1”的体素中心坐标到离它最近且标记为“0”体素中心的距离计算公式如下:

(3)
0≤r≤(zmax-zmin)/hv
式中,zmax、zmin分别为产品三角网格模型z向最大边界点和最小边界点;hv为体素边长;(xvi,yvi)为第i个被标记为“1”体素中心坐标;(xvj,yvj)为第j个标记为“0”体素中心坐标。
平均壁厚davg计算公式为
davg=V/S
(4)
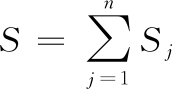
式中,S为产品表面积;Sj为产品三角网格模型中第j个三角面片的面积,可通过海伦公式计算。
壁厚均匀程度ut计算公式为
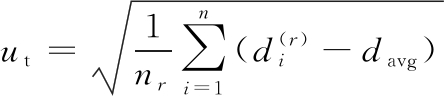
(5)
其中,nr为所分层数。由于体素化求解过程是离散逼近的过程,故存在一定误差。减小体素尺寸,会提高逼近进度,但会增加计算量,所以需合理划分体素密度。
2.1.3 复杂程度
产品复杂程度是产品结构复杂程度的表征,决定产品的注型难易程度,但产品复杂程度是一个不确定的模糊概念,一般反比于产品的平均壁厚(VC工艺可成形最小壁厚为1 mm的产品)。本文对产品结构复杂程度的描述采用0-1的复杂度来表征,并分为5个等级,用变量k表示,k∈[0,1],其计算公式为
k=λ/davg
(6)
其中,λ为比例系数,初始值为0.75,系统留有人机交互接口,后期可根据需要由设计人员设定。其对应映射关系如图4所示。
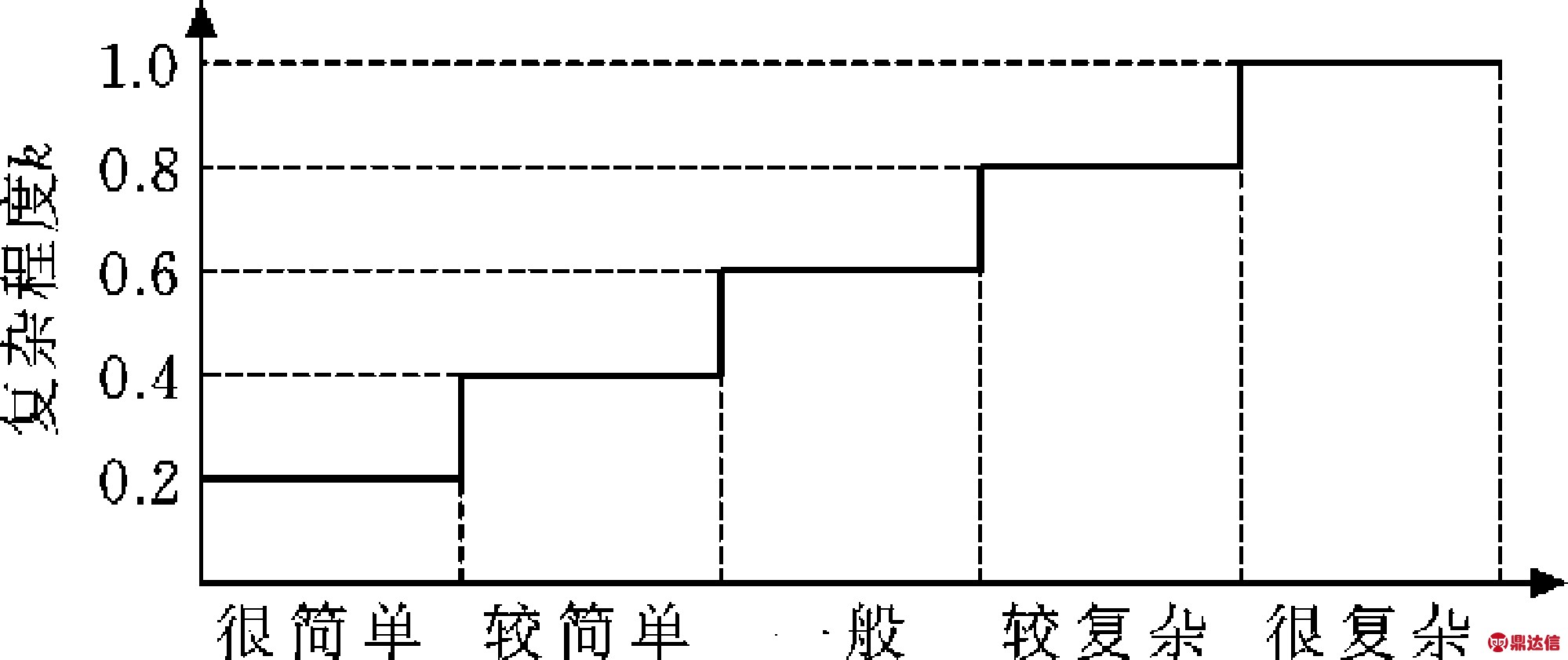
图4 产品复杂程度的函数映射关系
Fig.4 Function mapping relation of product complexity and complexity
2.2 基于CBR的工艺参数推荐
基于案例推理(CBR)的工艺参数推荐策略的核心思想是根据待解决问题的有关信息得到历史记忆中的源案例,找到相似问题的解决方法,获得新问题的解。
(1)产品案例表示。丰富的案例是CBR技术实现的基础,它蕴含了VC技术中工艺设计人员的经验,但是以何种形式来描述案例是实现CBR的前提。一个完整的案例表示应包含问题特征描述及其解决方案,由此本文从问题角度出发,将案例表示成一个有序对:
<问题描述,解描述>
在VC工艺实际生产过程中,以材料类型和产品的几何特征作为案例问题特征描述,工艺参数作为案例解决方案,并采用状态空间法对案例(case) Case进行描述。即
Case={M,D,P}
(7)
D={D1,D2,…,Di} P={P1,P2,…,Pj}
其中,M为树脂材料类型;D为型腔几何特征数据集合,i为几何特征数量;P为解决方案即工艺参数集合,j为工艺参数个数。由上文求取的壁厚、体积、复杂程度等来描述型腔几何特征、树脂材料温度、模具温度、充模压差等工艺参数[14]解决方案。
(2)案例相似度计算。案例相似度计算是案例检索的基础,是历史案例与待求解实例间相似程度的定量表征,它决定了案例推理的成败,相似度计算实质是计算当前案例与历史案例的欧氏距离[15],目标案例与历史案例的相似度
(8)
其中,为欧氏距离,表示两个案例的相似程度,
值越大,距离越大,则相似程度越小;
值越小,距离越小,则相似度越大。p*为目标案例,
是
的第i个属性值;u*为案例库中的历史案例,
是u*的第i个属性值;m为每个案例的属性个数;wi为第i个属性的局部相似度权值,初始默认权值见表1,由有经验的工艺设计人员设定,并留有人机交互接口,后期可根据需要修改。
表1 成形产品几何特征权值
Tab.1 Geometry feature weight of forming product

(3)产品案例检索和匹配。获得综合相似度后,采用最相邻近策略(nearest-neighbor strategy,NNS)进行案例检索。对于目标案例p*,若历史案例库中存在历史案例u*,对所有案例u′∈R,都有sim(p*,u*)≥sim(p*,u′)成立,则称案例u*为实例p*的最近邻居NNS,记为
NNS(p*,u*):⟺u*∈R:sim(p*,u*)≥sim(p*,u′)
(9)
相似度匹配及处理办法见表2。
表2 实例相似度匹配及处理办法
Tab.2 Similarity judgment and treatment of target case
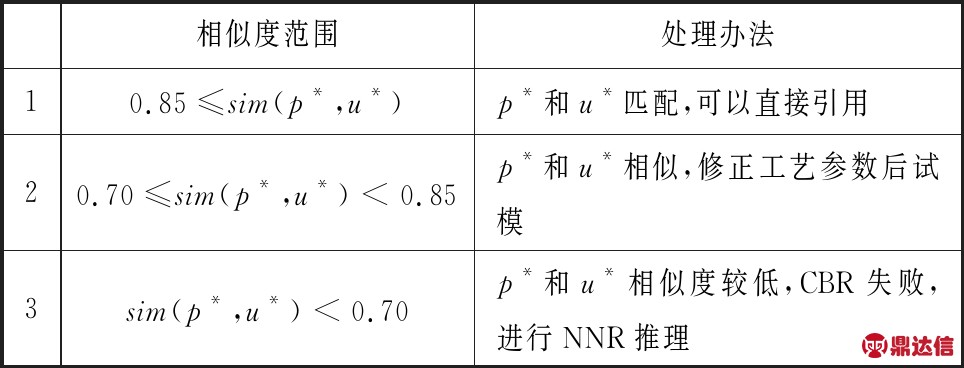
2.3 基于NNR的工艺参数推荐
CBR推荐策略的求解性能和求解效率依赖于历史案例库的覆盖范围、案例检索算法的合适性等,在许多场合下,单纯的CBR技术不足以保证系统求解问题的可行性,需要对其加以补充。神经网络推理技术技术能够以非线性映射的方式自动辨识输入输出之间的复杂关系,本文采用广义回归神经网络(generalized regression neural network,GRNN)建立产品特征与工艺参数之间的预测模型,对新产品实例初始工艺参数进行预测,相比于BP 网络,在达到相同预测效果的情况下,GRNN所需的样本仅为BP 网络的1%[16]。
GRNN是一种基于非线性回归理论的前馈式神经网络。对于输入的新产品几何特征向量xnew=(C1new,C2new,…,Cinew),其输出工艺参数预测向量
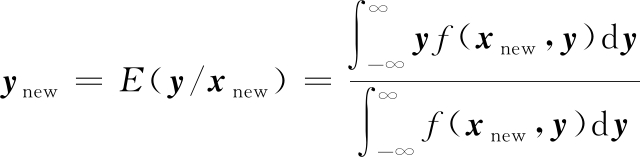
(10)
其中,y为相对于产品特征值xnew的回归,f(xnew,y)为随机变量x和随机变量y的联合概率密度函数,可应用parzen非参数估计。即

(11)
其中,n为案例库中同种材料的案例数量;q为产品特征向量xi的维数,i=1,2,…,n;σ为高斯函数的宽度系数(光滑因子);pi为神经元传递函数。将式(11)中f(xnew,y)代替式(10)中f(xnew,y),则工艺参数输出预测值
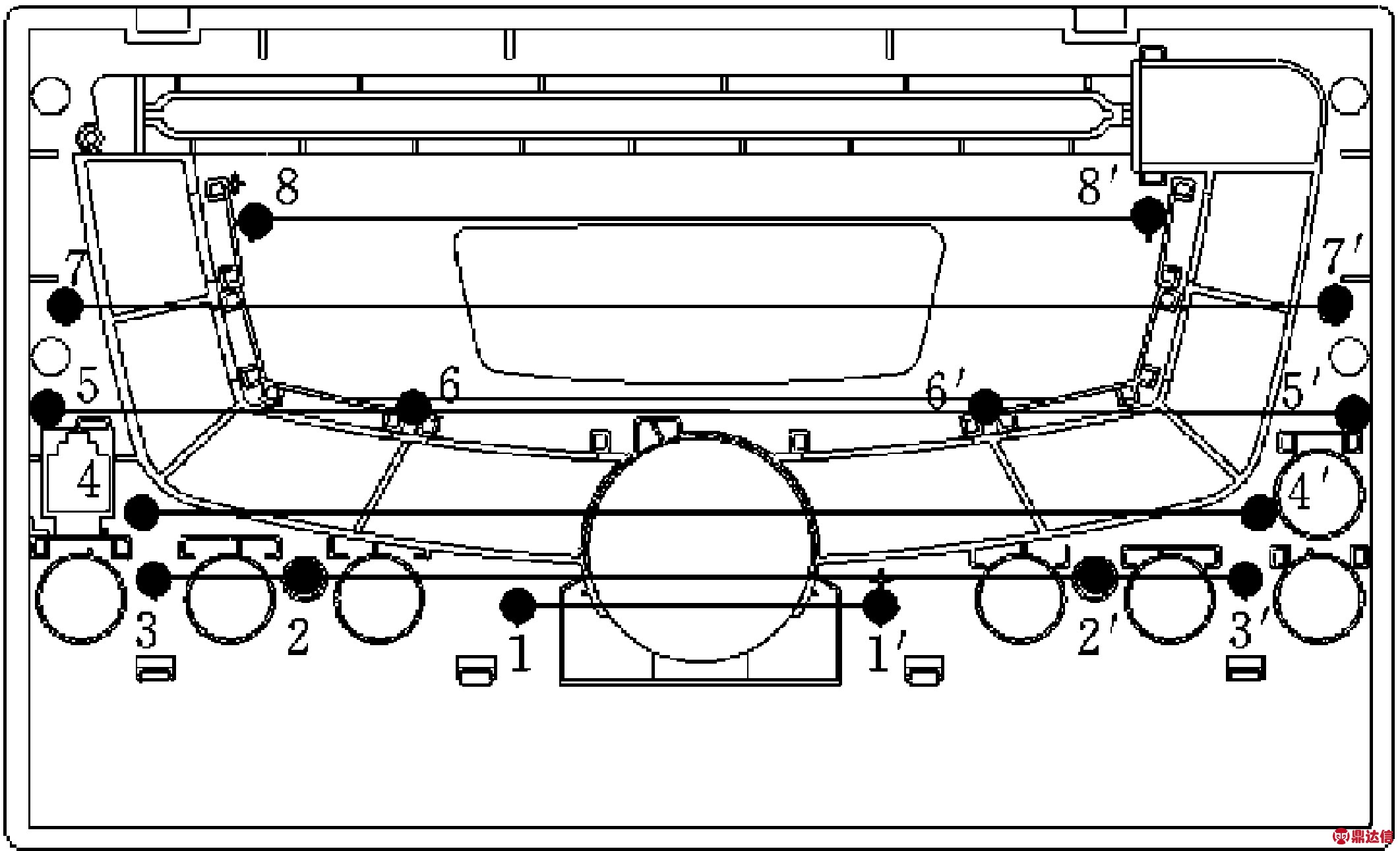
(12)
GRNN网络结构如图5所示,分别为输入层、模式层、求和层与输出层4层神经元。
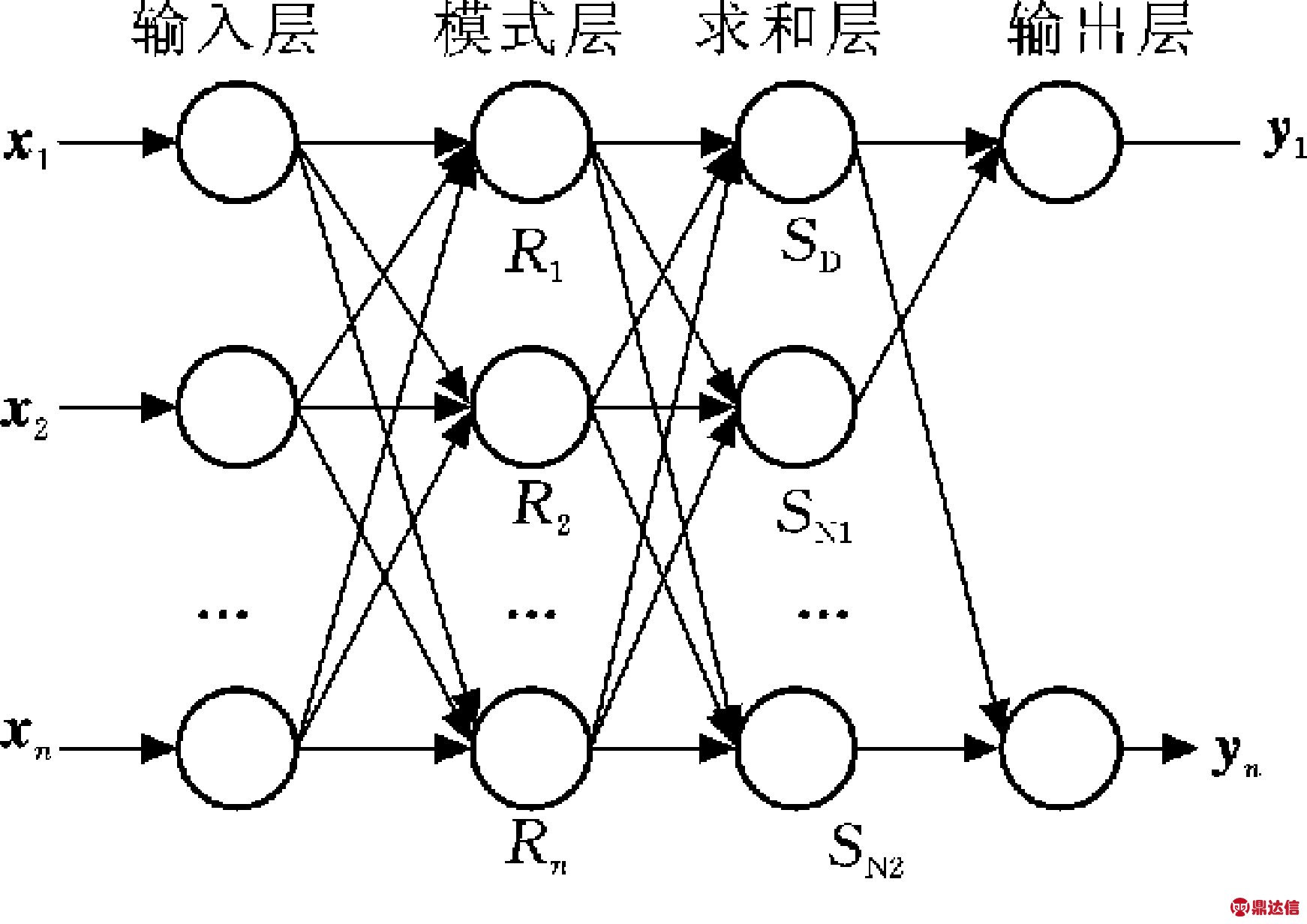
图5 GRNN结构
Fig.5 The structure of GRNN
其中,模式层的神经元数目等于输入层神经元数目,各神经元对应不同的样本,神经元传递函数为

(13)
i=1,2,…,n
求和层中使用两种类型神经元进行求和。一种类型是对所有模式层神经元的输出进行算术求和,其模式层与各神经元的连接权值为1,传递函数为

(14)
另一种类型是对所有模式层神经元进行加权求和:

(15)
输出层中的神经元数目等于学习样本中输出向量的维数,神经元 j 的输出对应估计结果为
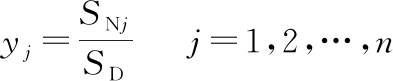
(16)
GRNN属于有导师型网络,它靠学习来逼近问题应有的模式,以案例库中PX245材料的390组数据为例,样本数据源于案例数据库中以往加工案例,选择360组数据作为网络训练样本,剩余30组作为测试样本以检验网络预测的准确性,以产品体积V、产品平均壁厚davg、壁厚均匀程度ut和产品复杂程度k作为GRNN的输入;将材料温度tm、模具温度td和充模压差pf作为GRNN的输出。根据式(11),预测值ynew为所有训练样本yi的加权平均,权值为pi。在样本一定的情况下,其连接权值便随之确定,由此光滑因子σ对GRNN的预测性能影响较大。为选取最佳的光滑因子σ,采用循环训练的方法进行寻优,令光滑因子σ以增量0.01在范围[0.1,1]内递增变化,取样本中一个样本用于检验,其余样本构建GRNN,计算检测样本的误差相对值,重复上述步骤对样本值进行估计,得到误差序列,计算误差序列的平均值:
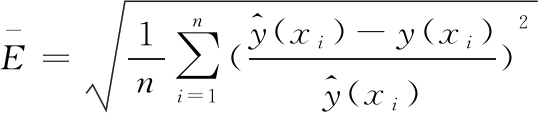
(17)
其中,分别为计算值和样本值。将式(17)计算得到的平均误差作为网络性能的评价指标,将最小误差对应的光滑因子σ用于最终GRNN的构建,如图6所示。
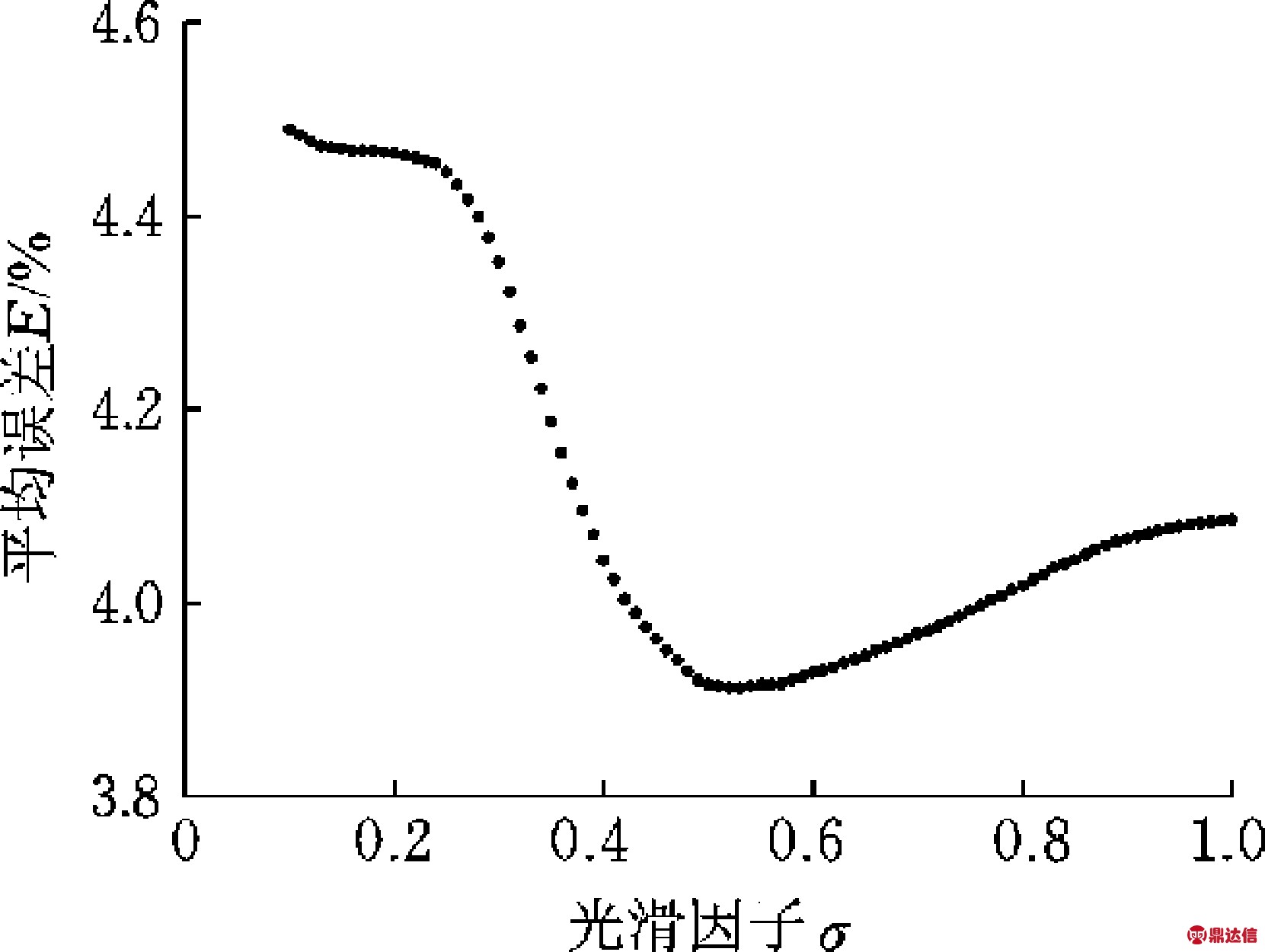
图6 平均误差
Fig.6 Average error
光滑因子σ取0.51时,对应的最小平均误差为3.92%,此时,训练数据的预测效果最好,预测结果及误差如图7~图9所示。可以看出,充模压差的误差值范围为[-570,370]Pa,模具温度和材料温度的预测误差范围为[-0.7,1.0]℃,三者误差均在较小的范围之内,精度满足要求。
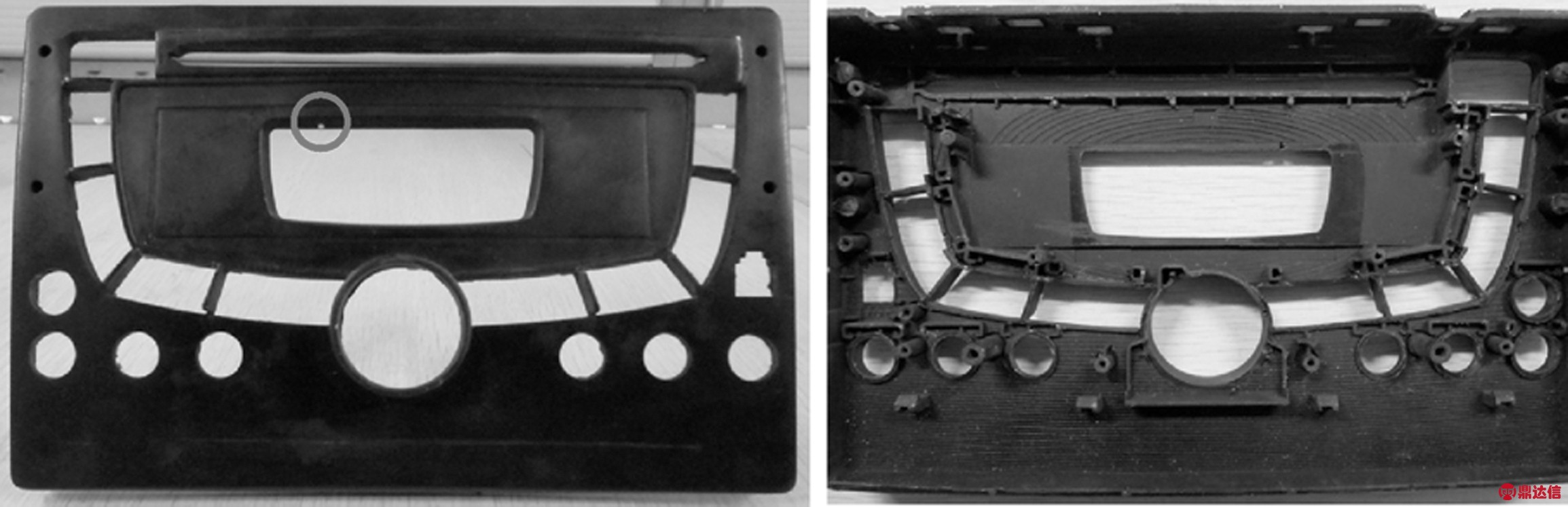
图7 材料温度预测结果及误差
Fig.7 Prediction results and errors of material temperature
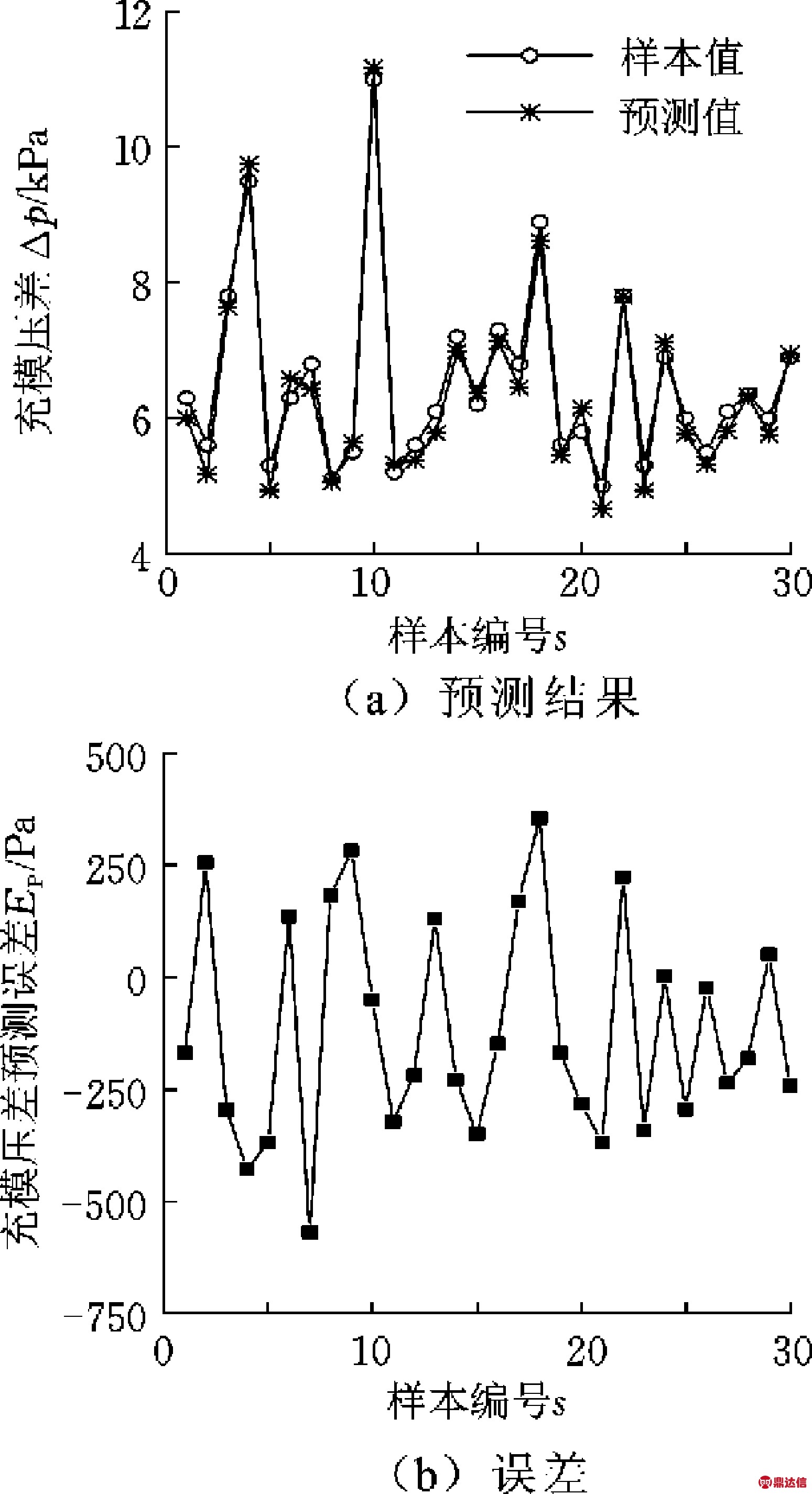
图8 充模压差预测结果及误差
Fig.8 Prediction results and errors of filling pressure difference
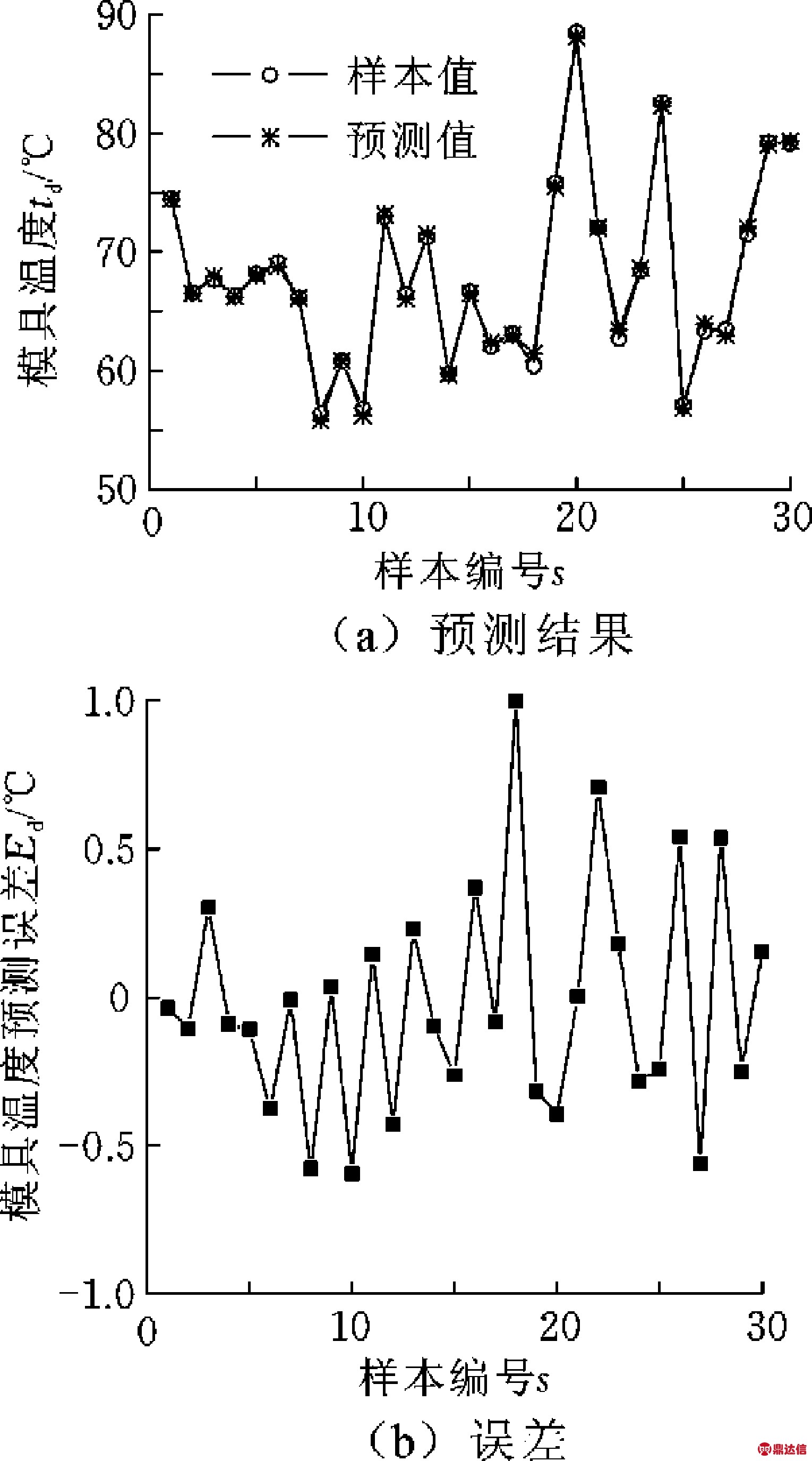
图9 模具温度预测结果及误差
Fig.9 Prediction results and errors of die temperature
3 产品缺陷修正
对于CBR和NNR推荐的初始工艺参数,在实际加工中,产品仍然可能出现质量缺陷,需要根据产品缺陷类型和程度对工艺参数进行调整,以达到改善产品质量的目的。因此,本文采用模糊推理的方法对产品进行缺陷修正。
(1)输入输出模糊集及隶属函数。试模过程中,产品可能同时存在多种缺陷,每种缺陷对应需要调整的工艺参数也不尽相同,而且工艺参数调整量还受缺陷程度和上次试模过程中该工艺参数当前值的制约。因此,将缺陷类型、缺陷程度以及工艺参数当前值作为模糊推理系统的输入,将工艺参数的调整量作为模糊推理系统的输出。
缺陷程度的输入方式采用自然语言和精确数值两种形式,其术语集合为 {轻微,中等,严重},并映射到区间[0,1];缺陷程度的模糊化则采用三角形隶属函数来设计,所建立缺陷程度的输入隶属函数曲线见图10。对于当前工艺参数输入方式,同样采用自然语言和精确数值两种形式,其术语集合为{小,较小,中,较大,大},并映射到区间[0,1] ,工艺参数当前值的模糊化则采用梯形隶属函数来设计,以充模压差为例,所建立的缺陷程度的输入隶属函数曲线见图11。
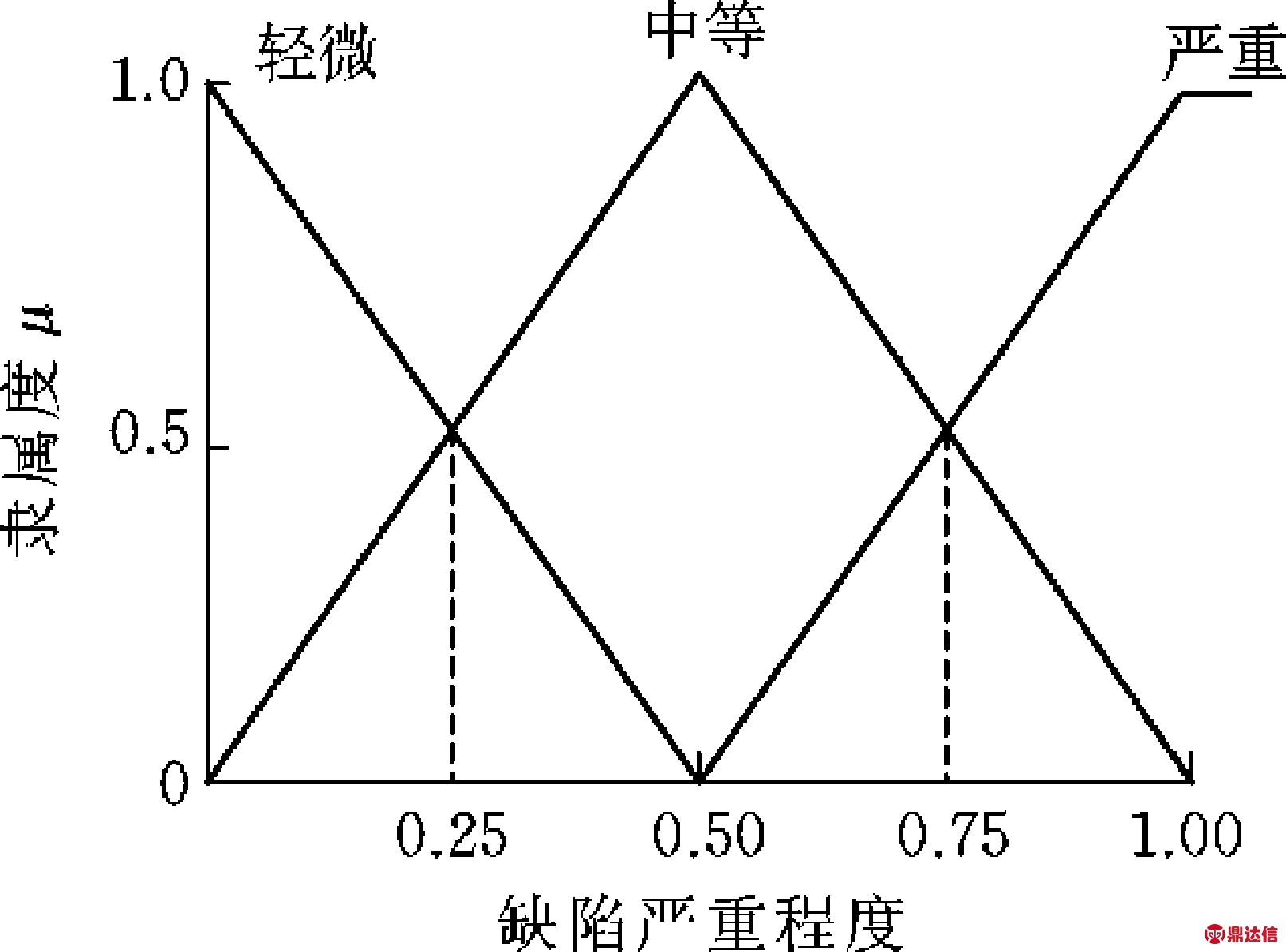
图10 缺陷程度隶属函数曲线
Fig.10 The membership function curve of degree of defect
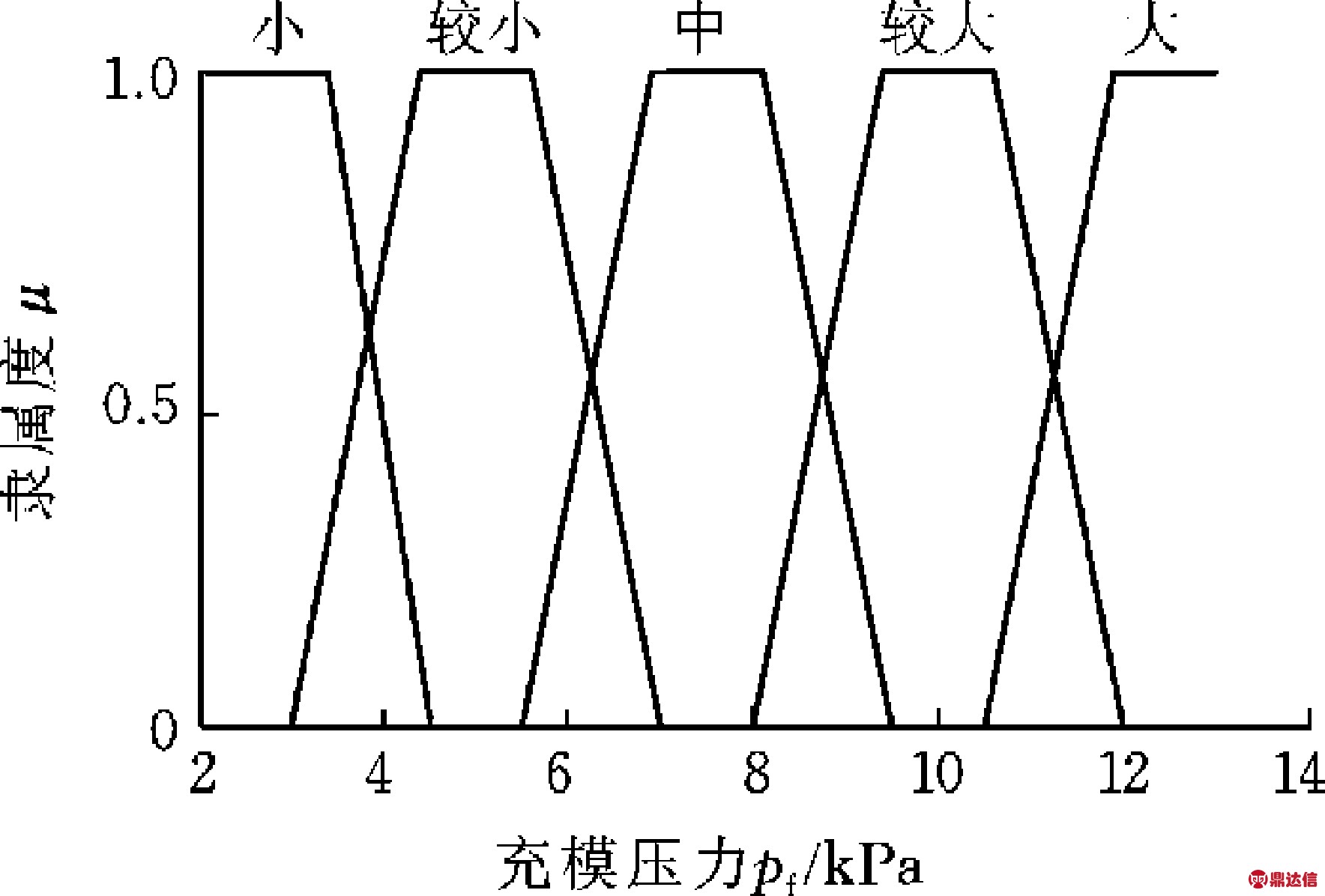
图11 充模压力隶属函数曲线
Fig.11 The membership function curve of filling cavity pressure
(2)模糊控制规则。由于模型输入变量为缺陷程度和工艺参数的当前值,故模型采用以下形式的“IF-THEN”规则:
IF x is A and y is B,THEN z is C
规则中,x为缺陷程度输入语言变量;y为工艺参数当前值输入语言变量;z为工艺参数调整量输入语言变量;A、B、C分别是论域X、Y、Z上的模糊集合。
以欠注缺陷对充模压力的调整为例,建立表3所示模糊规则表,确定工艺参数的调整量,调整量的隶属函数设计如图12所示,其他工艺参数-缺陷模糊规则表结构与表3一致。
表3 充模压力-缺陷模糊规则表
Tab.3 Fuzzy rule table of filling pressure-short
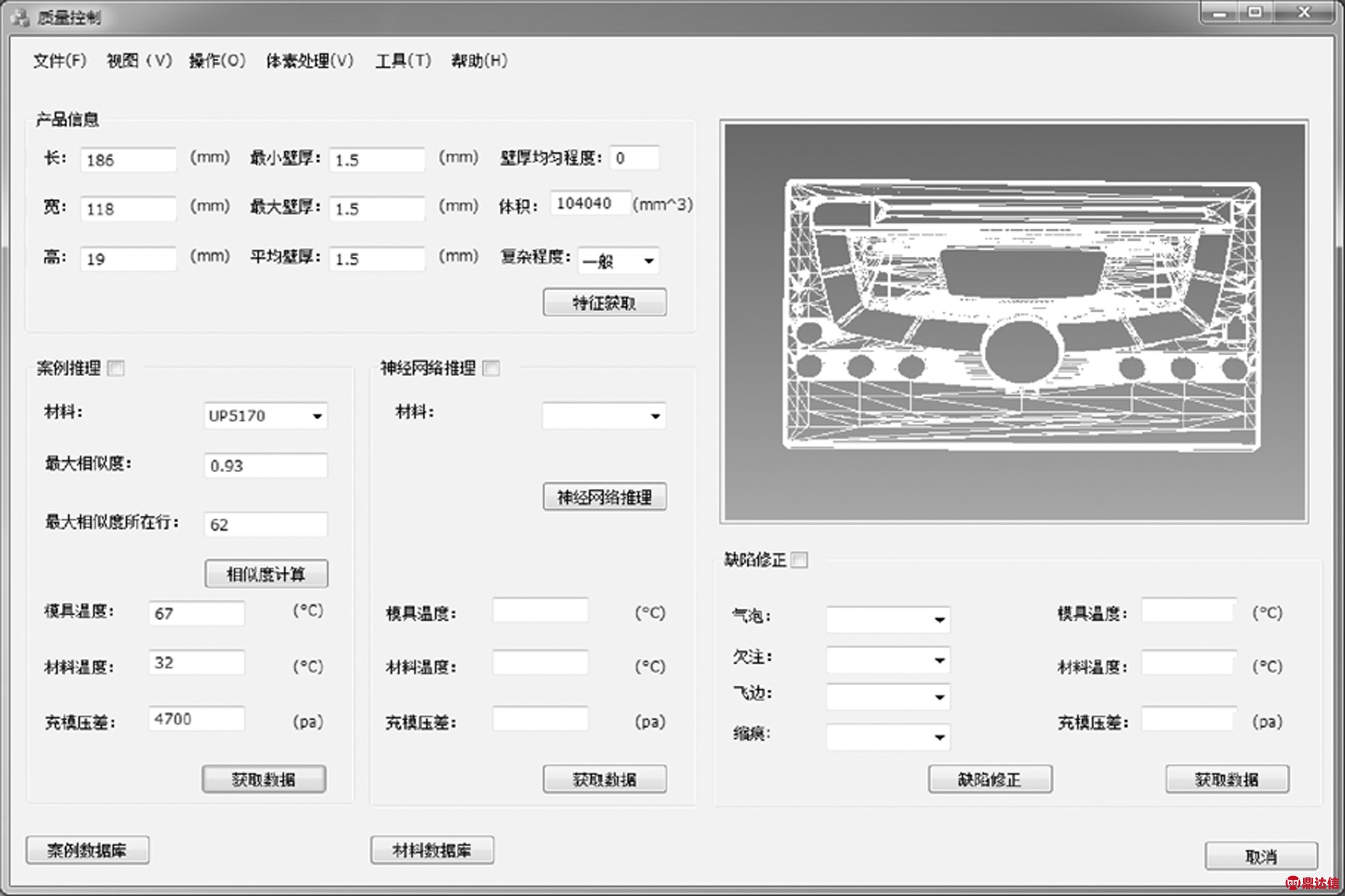
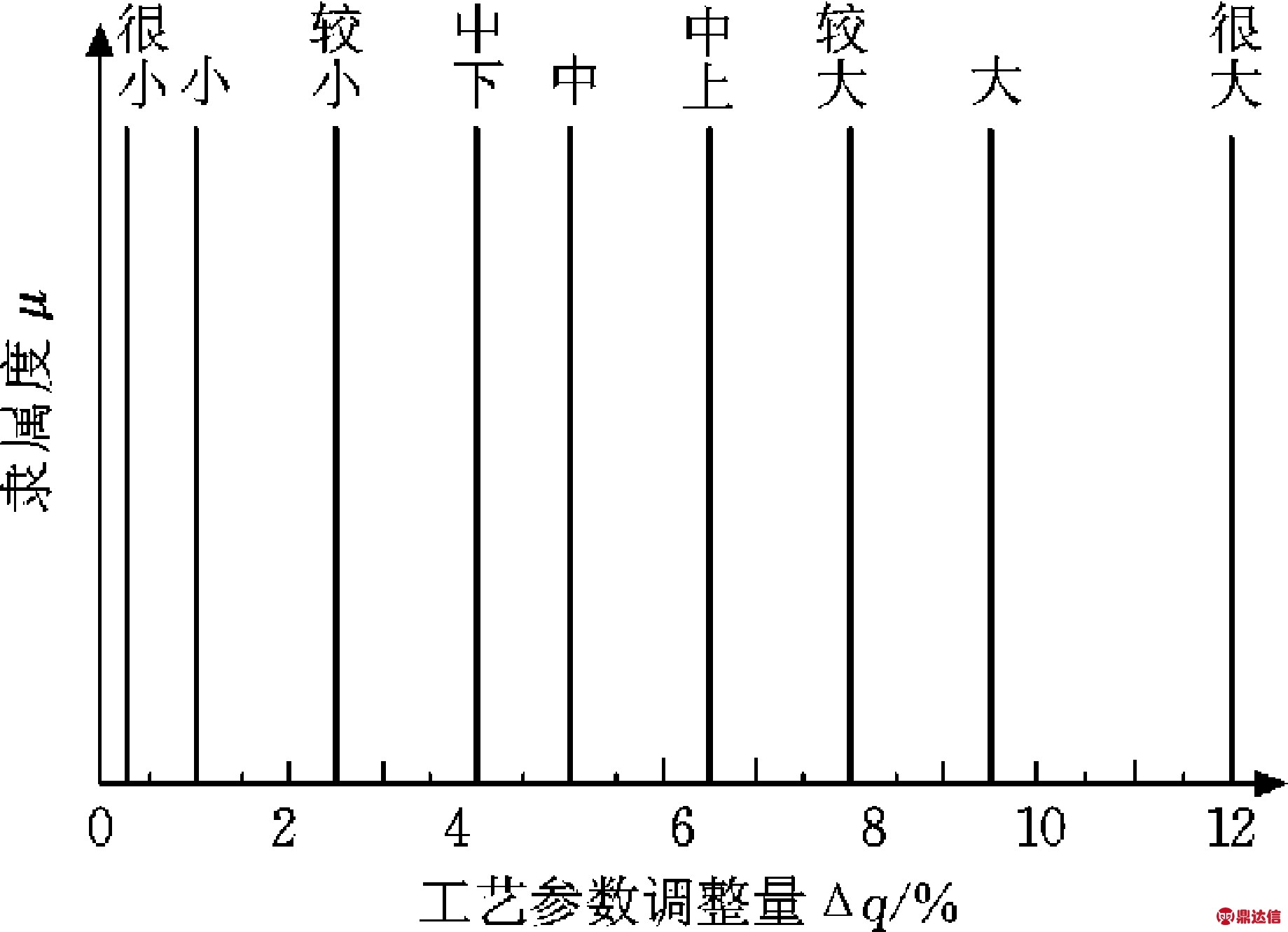
图12 工艺参数调整量隶属度函数
Fig.12 The membership function of process parameter adjustment
(3)模糊推理及反模糊化。模糊推理采用“多个前件多条规”的推理形式,选择Mamdani模糊推理法[17]作为模糊关系与模糊集合的合成运算模型,其结构如图13所示。
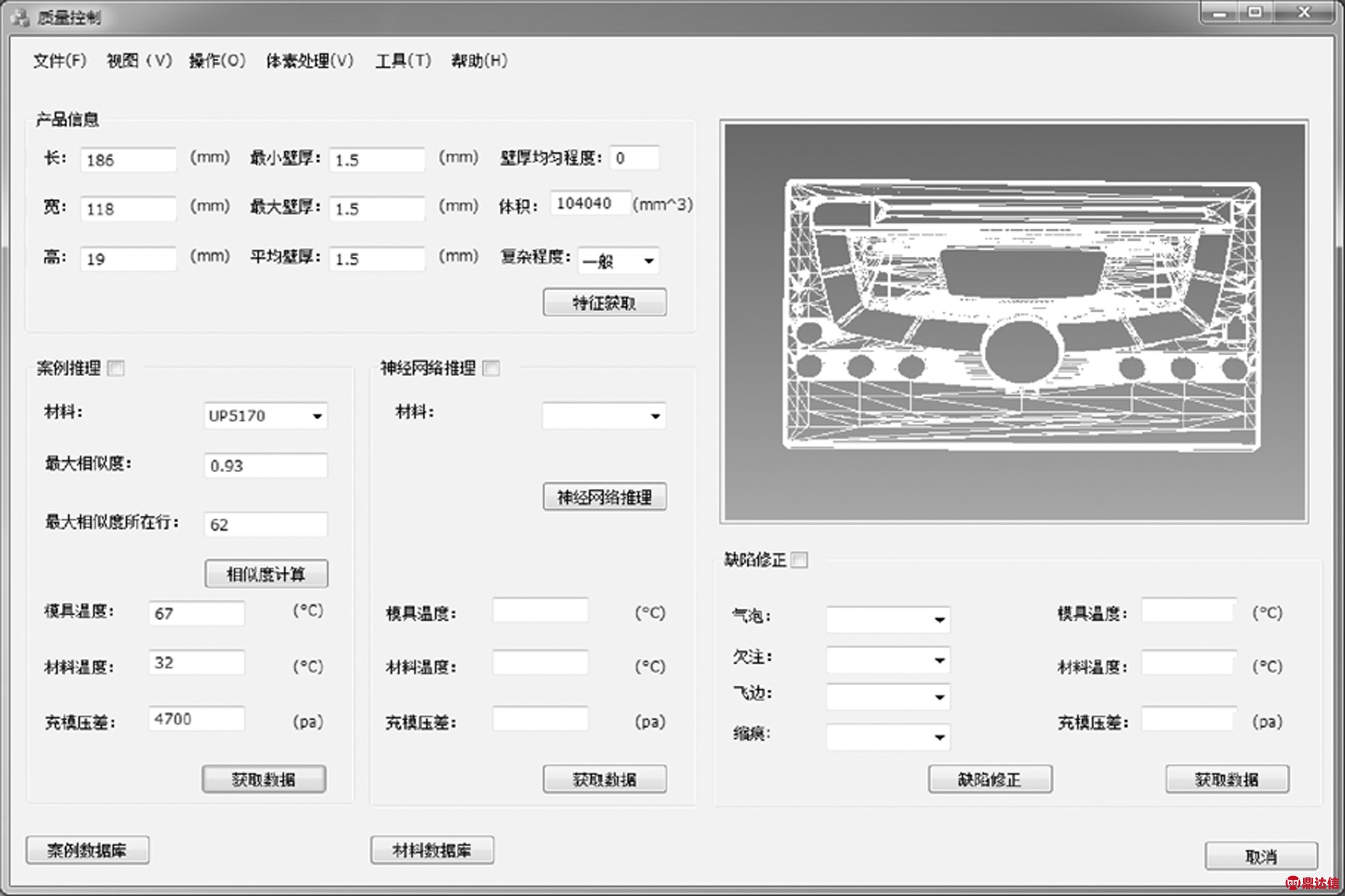
图13 模糊推理系统结构
Fig.13 Fuzzy inference system structure
A={A1,A2,…,Ar }为描述工艺缺陷程度的模糊集合;B={B1,B2,…,Br }为描述工艺参数当前值的模糊集合;z为工艺参数调整幅度精确值,C={C1,C2,…,Cr }为描述工艺参数调整幅度的模糊集合;C*为描述工艺参数最终调整幅度的模糊集合。对于精确的模型输入值x=A*,y=B*,其模糊规则见图11。
根据Mamdani模糊关系定义,多个前件多条规则的模糊推理结果可由下式求得:
(18)
μRMi(x,y,z)=μAi(x)∧μBi(y)∧μCi(z)
其中,μRMi(x,y,z)是Ai、Bi、Ci间模糊蕴含关系,i=1,2,…,r;在模糊规则i下所得到的模糊集合
=
=(wAi∧wBi)∧μCi(z)
(19)
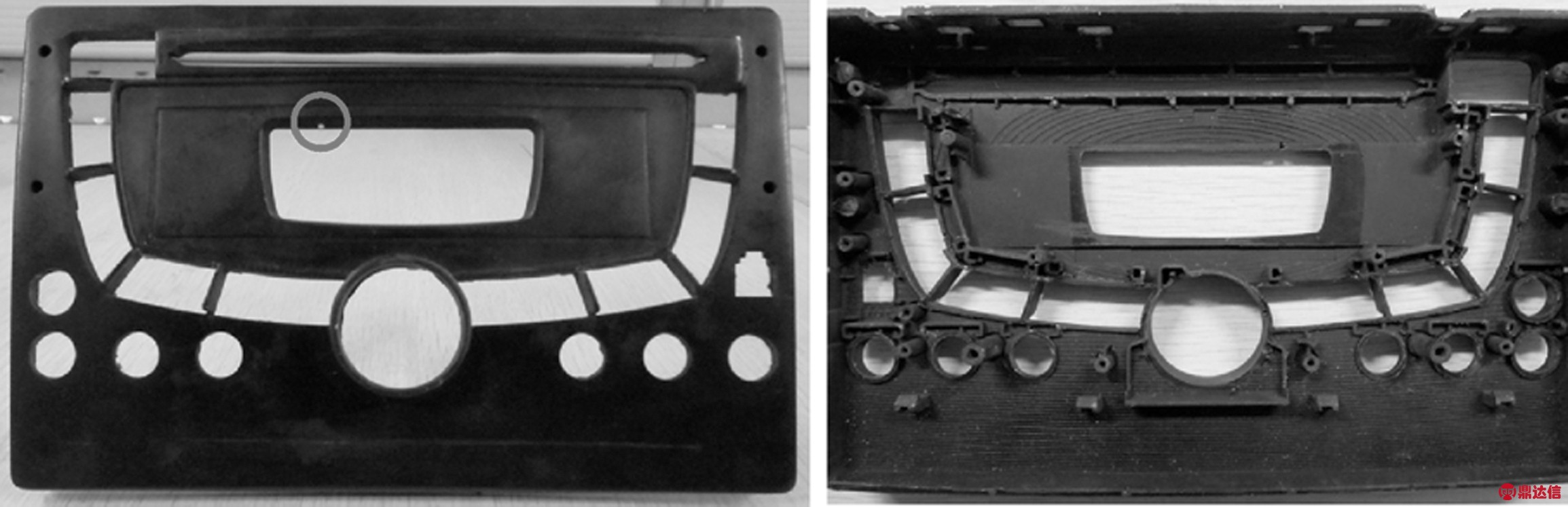
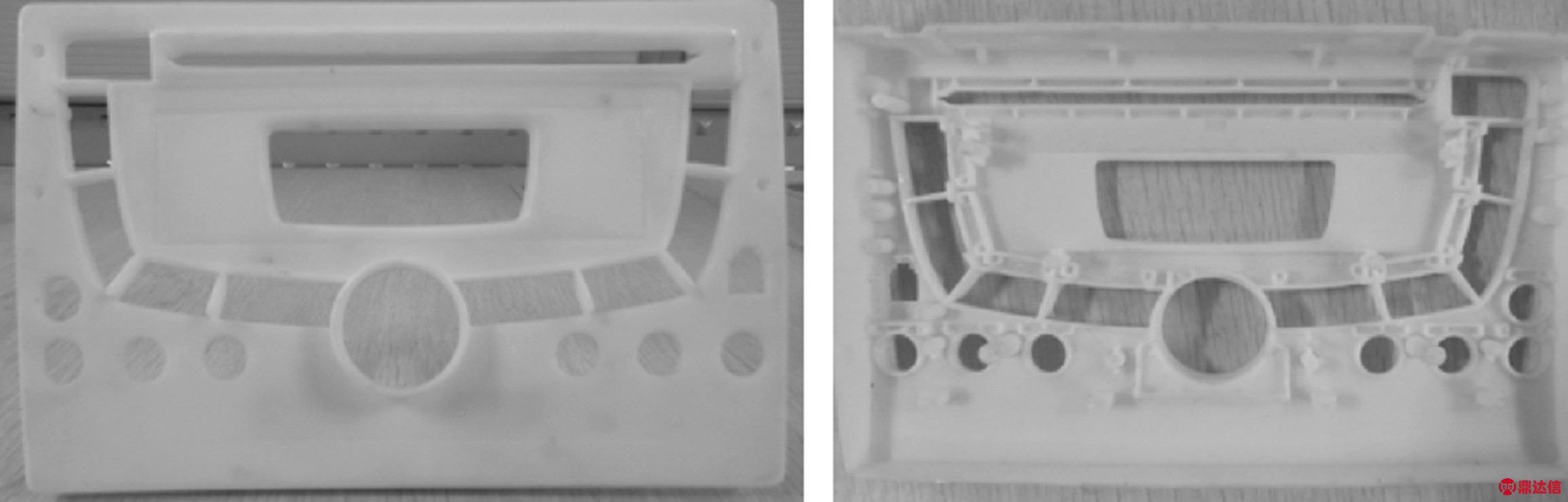
式中,wAi为A*对Ai的适配度;wBi为 B*对Bi的适配度;wAi∧wBi为模糊规则的激励强度。
对式(18)推理得到的模糊集合,采用面积重心法进行参数修正值的反模糊化处理。工艺参数修正值

(20)
式中,Z为工艺参数当前值;wi为规则的激励强度,wi=wAi∧wBi;zr为工艺参数调整值;r为触发规则个数。
4 实例验证
在WIN 7系统下,采用Visual Studio 2010集成开发环境,结合VTK可视化开发工具包,开发了VC质量控制系统,为方便处理三角网格模型,在算法实现过程中调用了OpenMesh库,所建立的质量控制系统窗口如图14所示。
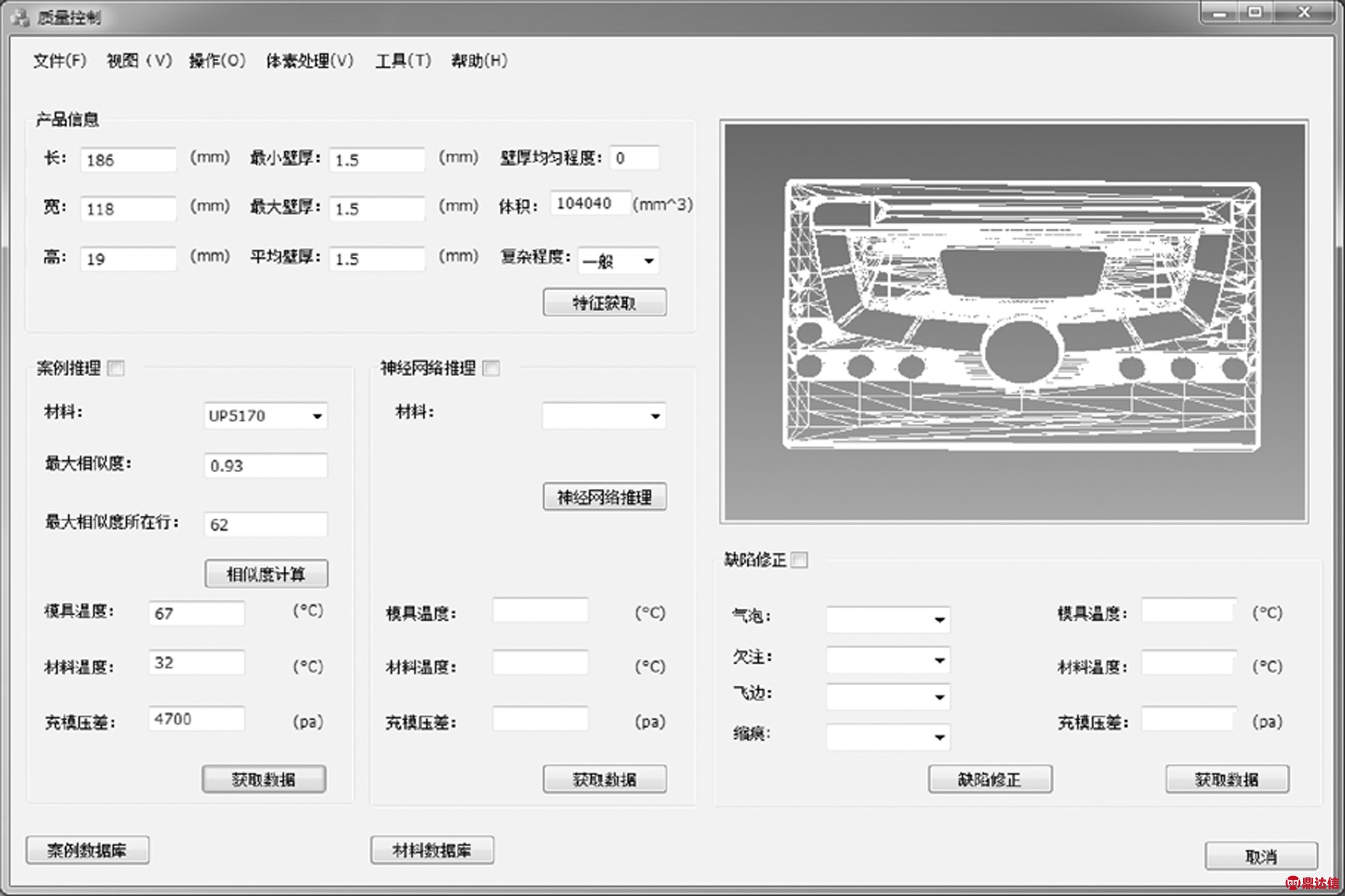
图14 质量控制系统界面
Fig.14 Interface of quality control system
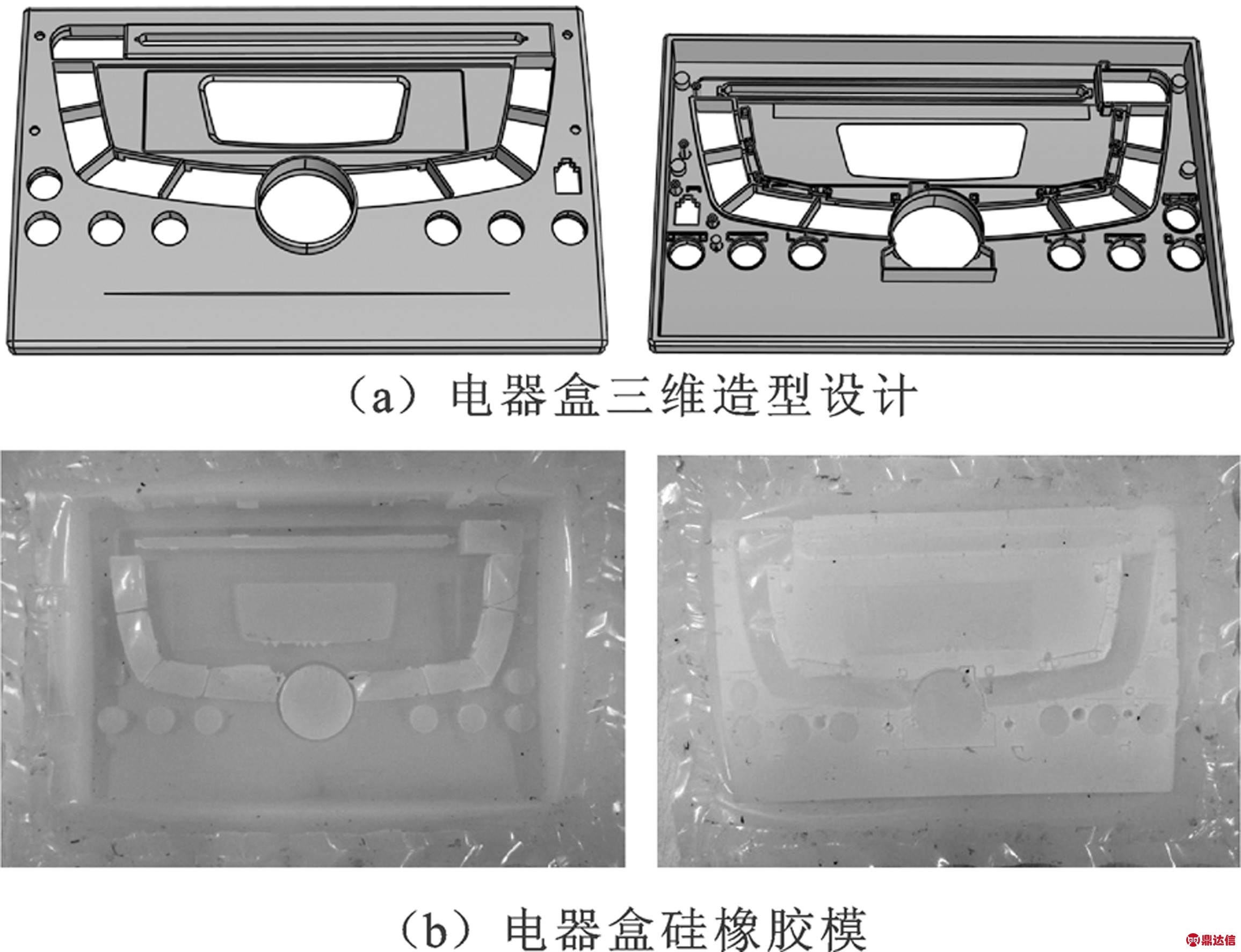
图15 电器盒
Fig.15 Electrical enclosure
为评估本文算法的可行性,采用某品牌电器盒进行试验,如图15所示;材料选取法国AXSON公司UP5170和PX223-HT树脂;试验设备采用自制数字控制VC机物理样机,如图16所示;试验要求产品特征完整,气泡少,表面质量好。
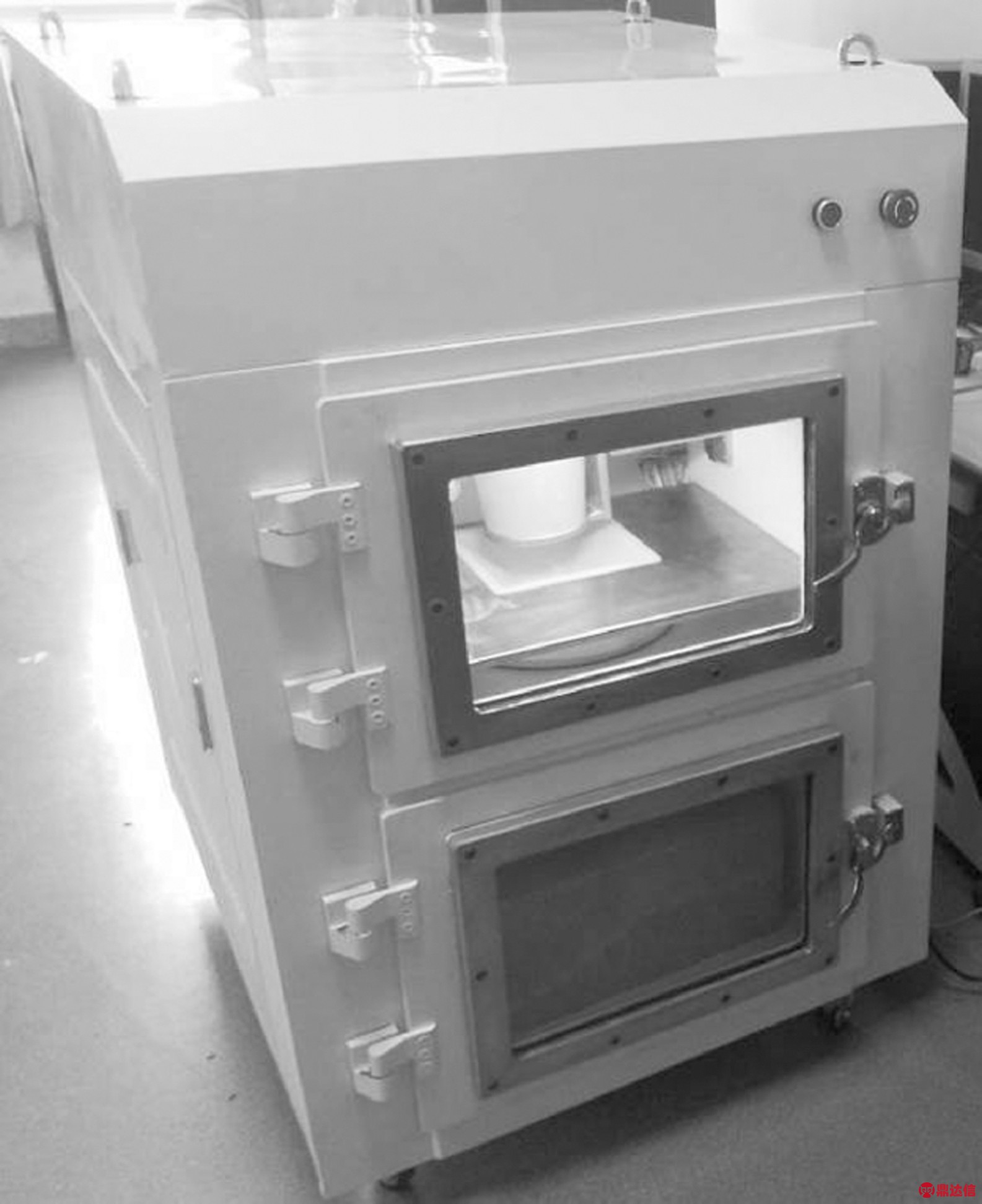
图16 数字控制VC机物理样机
Fig.16 Digital controlled physical prototype of VC machine
试验一。树脂UP5170 材料充模试验。模腔几何特征计算,获取产品特征信息,其外形尺寸为186 mm×118 mm×19 mm,体积为104 040 mm3,平均壁厚为1.5 mm,壁厚均匀。通过实例检索和匹配,其最大相似度为0.93,案例推理过程成功,初始工艺参数如下:模具温度为67 ℃,材料温度为32 ℃,充模压差为4 700 Pa。根据推荐工艺参数进行初始试模,结果如图17所示。产品充填完整,无明显飞边现象,有轻微气泡现象,但不影响产品外观。
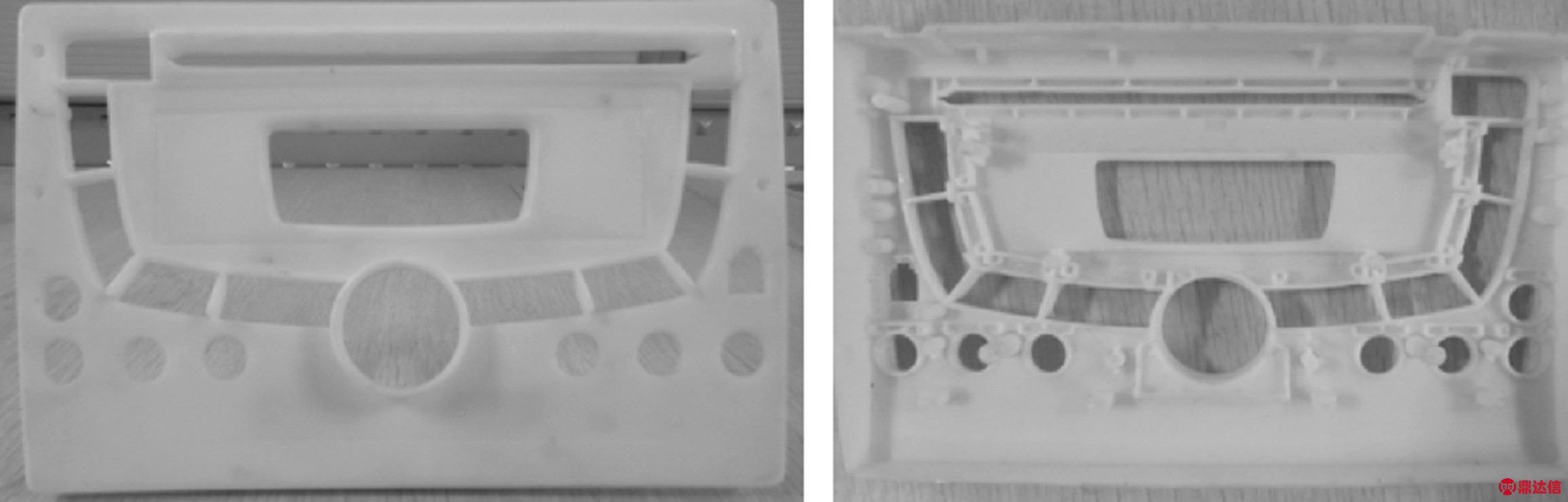
图17 产品初始试模结果(试验一)
Fig.17 Product model of initial mold test(test one)
试验二。PX223-HT材料试验。选择PX223-HT,采用CBR方法对历史案例数据库进行检索,其最大相似度为0.56,案例推理过程失败。转而使用NNR工艺参数进一步推荐初始工艺参数,推荐出的工艺参数如下:模具温度为68 ℃,材料温度为26 ℃,充模压差为4 800 Pa。根据推荐工艺参数进行初始试模,试模结果如图18所示,产品充填不完整,上表面多处存在孔洞,装配特征不完全,有轻微气泡的现象。
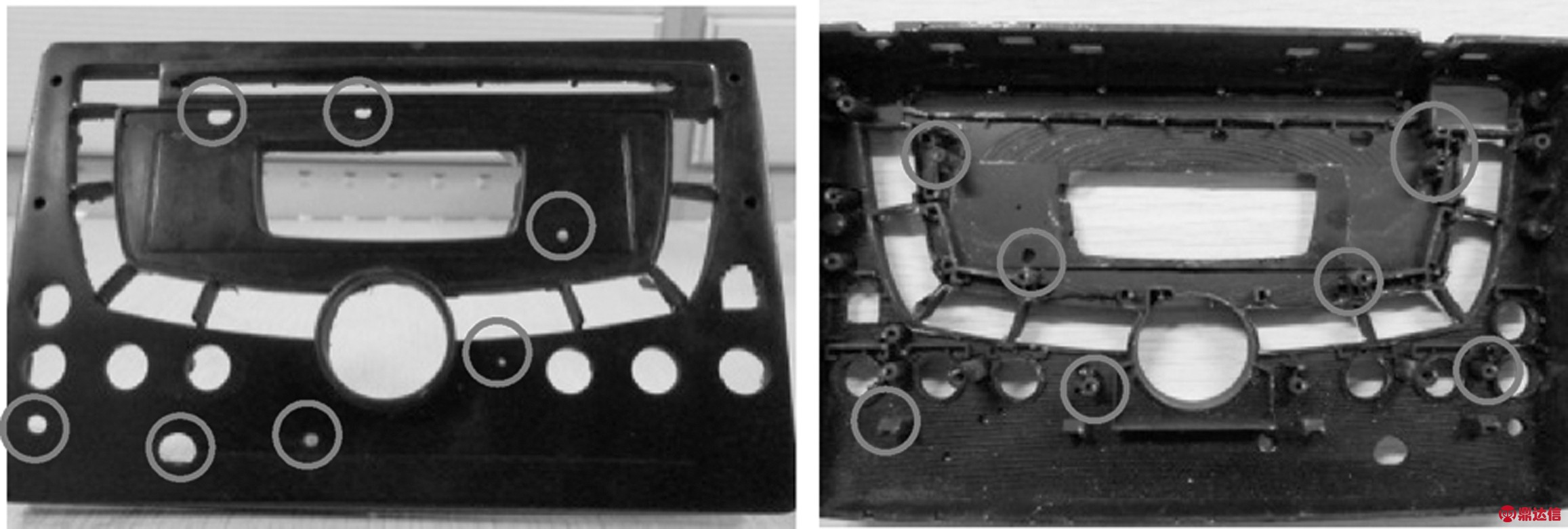
图18 产品初始试模结果(试验二)
Fig.18 Product model of initial mold test(test two)
根据第一次试模反馈的严重欠注和轻微气泡缺陷情况,使用模糊推理对产品缺陷进行第一次参数修正,修正后工艺参数如下:模具温度为71 ℃,材料温度为29 ℃,充模压差为6 200 Pa。根据修正后的工艺参数进行第二次试模。试模结果如图19所示,产品充填不完整的缺陷得到一定改善,但仍有少部分装配特征不完全。
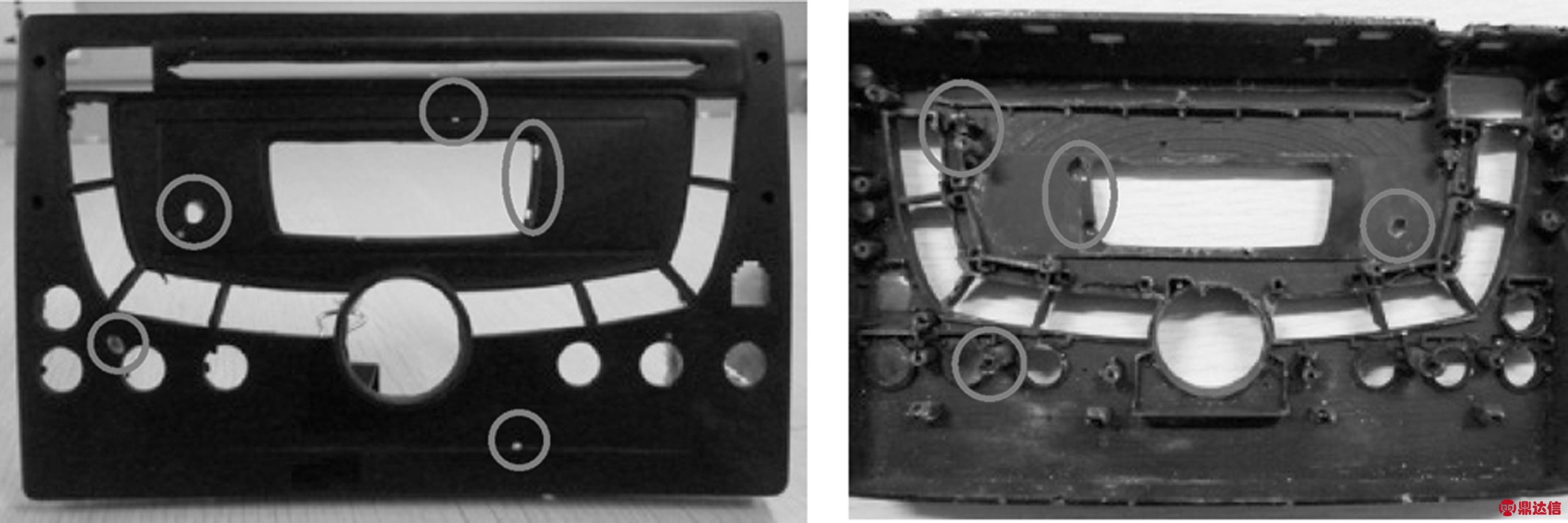
图19 第一次参数修正的试模产品
Fig.19 Test products after the first parameter modification
再次反馈缺陷类型和程度,使用模糊推理对工艺进行第二次参数修正。修正后工艺参数如下:模具温度为74 ℃,材料温度为33 ℃,充模压差为6 800 Pa,并再次进行试模,试模结果如图20所示。产品充填完整,无欠注现象,产品表面有轻微气泡缺陷,但已不影响产品外观。
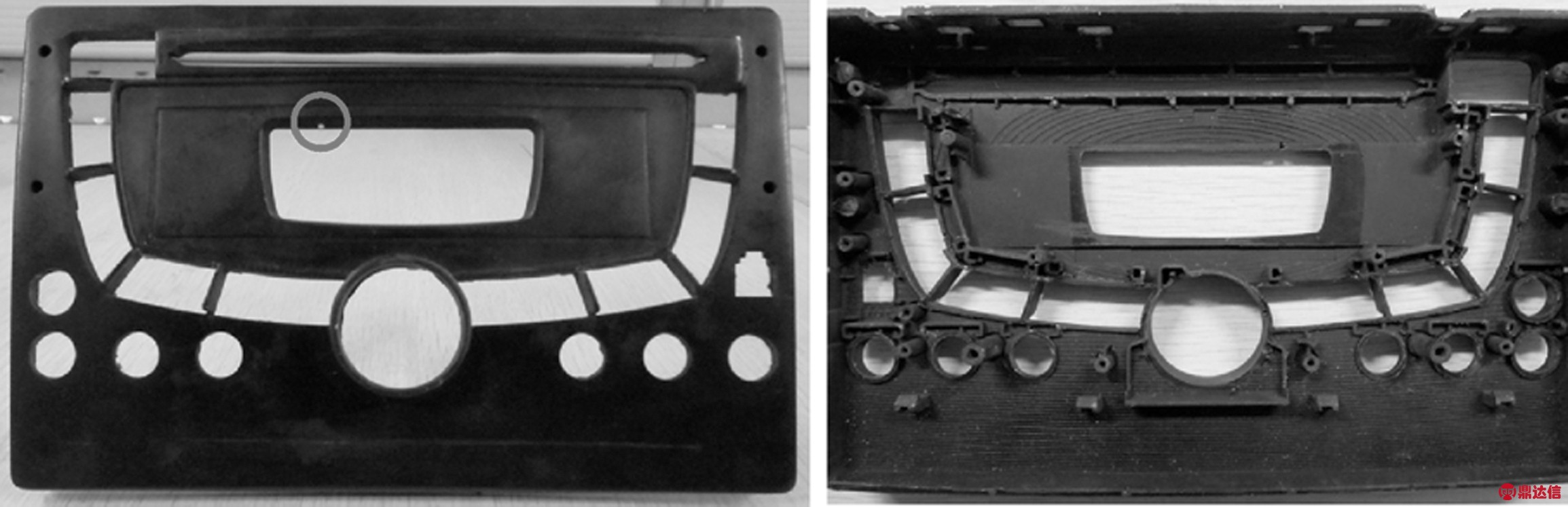
图20 第二次参数修正的试模产品
Fig.20 Test products after the second parameter modification
翘曲变形是衡量产品质量的重要指标,影响产品后期的装配,因此选取电器外壳装配部位8对配合点,如图21所示,采用三坐标测量机测量其位置坐标并计算相应对等点之间的距离,并与设计距离对比,以此间接反映产品的翘曲变形量,测量结果如图22所示,其装配点之间的最大误差在0.25 mm以内,满足产品装配要求。
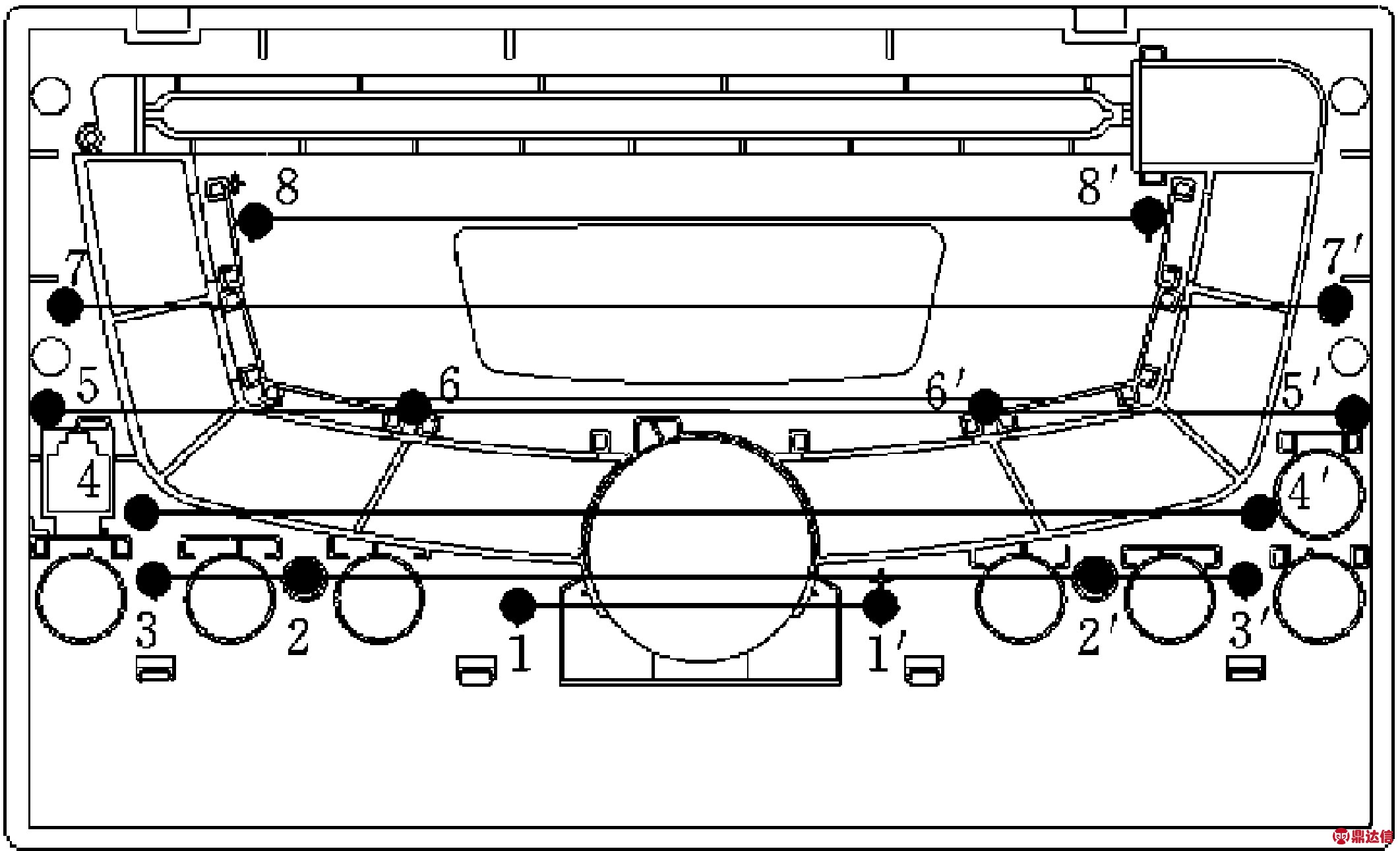
图21 装配点测量示意图
Fig.21 Schematic diagram of assembly point
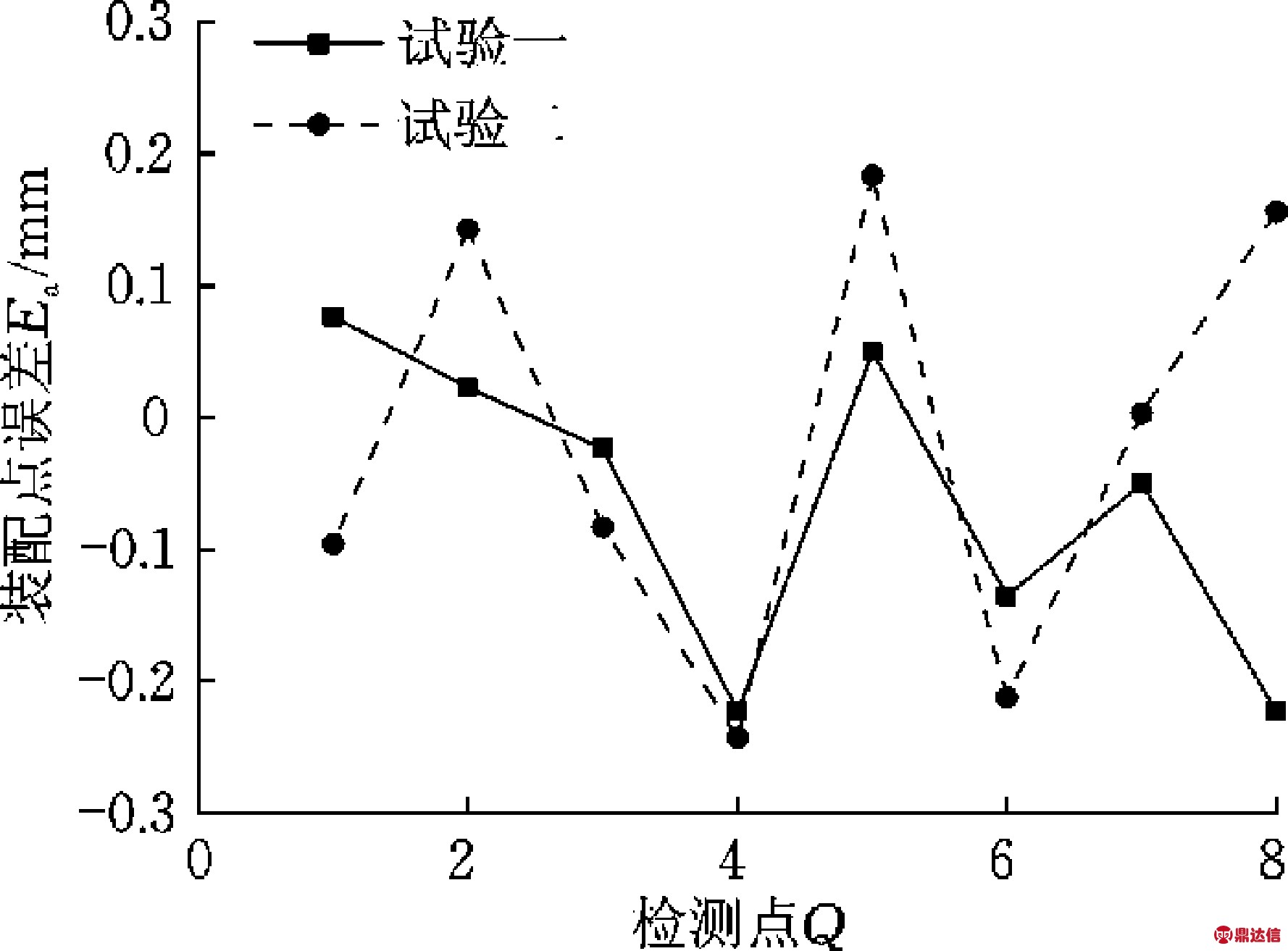
图22 装配点误差
Fig.22 Error of assembly point
由试验一及试验二可以看出,产品体积、壁厚、复杂程度以及成形材料等特征对工艺参数推荐有重要影响,实例结果证明,选择模具型腔几何特征以及材料作为问题特征描述是合理的。案例推理方法的求解性能和效率依赖于案例库的覆盖范围、案例检索的合适性,由此在案例较少的情况下,需要神经网络推理作为有效的补充。实例试验结果验证了基于神经网络推理可以在案例推理失败的情况下实现工艺参数的智能化设置,降低了对操作人员的经验要求。
5 结论
本文融合案例推理、神经网络推理和模糊推理技术,提出一种面向真空注型工艺的质量控制模型,并通过对某品牌电器盒试验,验证了该质量控制模型有较好的推理和质量控制能力,解决了VC产品质量控制主要依赖于操作人员知识和经验的问题。但随着数据量的增加,案例检索的效率会降低且神经网络的训练时间将会延长,如何在保证检索效率和网络泛化能力的前提下简化数据库还有待进一步研究。