摘 要:本文系统地阐述了大型复杂压铸件自动变速箱壳体的工艺开发、模具设计、调试生产的整个过程,重点介绍了模具设计过程理论数据的分析和模具结构设计。模具三维设计及二维设计应用PTC/Creo,整套模具设计全部实现参数化,确保了工程更改的前后一致性,三维结构运用模拟装配和干涉检查,确保设计间隙,铸造工艺过程采用MAGMA进行CAE分析,不断完善优化充型和凝固过程。该模具为超大型复杂模具,采用四个对角方向定位,避免高温高压下模具受热变形引起定位不准,同时改用方导柱代替圆导柱导向,避免合模拉伤;采用水冷方式和油温加热方式控制模具温度,提高铸件质量,保证压铸生产的连续性和稳定性;对金属液末端及最后凝固的厚大部分采用局部挤压技术,降低缩孔缺陷,提高组织致密性;采用真空压铸的方式减少铸件内部气孔;同时采用复合式感应液压缸抽芯,提高生产效率。
关键词:变速箱壳体;压铸机;CAE(计算机辅助工程);局部挤压;真空压铸
变速箱壳体压铸件是压铸产品中较为复杂,技术含量较高的铸件,随着汽车轻量化的推进和模块化生产,国内外先进的汽车集团已经开始采用压铸工艺生产7速以上的变速箱壳体,甚至在跑车上应用l0速自动变速箱,变速箱压铸模具作为生产变速箱的最重要装备,其模具设计、制造水平直接影响铸件质量的提高。由于其制造难度大,国内目前只有极少数汽车厂家能够自己开发7速自动变速箱产品,本文介绍的变速箱壳体为国内开发的第一台7速自动变速箱,铸件结构如图l所示。铸件外形尺寸为:430×4l0×403 mm,铸件材料为铝合金Al-Si9Cu4,铸件毛坯重量l2.5 kg,平均壁厚大约4 mm,铸件尺寸较大,型腔比较复杂,充型困难,铸件技术要求如下:
(l)内腔密封性能要求在0.1 Mpa压力下不能泄漏;
(2)由于装配总成均为密封件,所以加工表面不允许有大于0.3 mm的气孔.
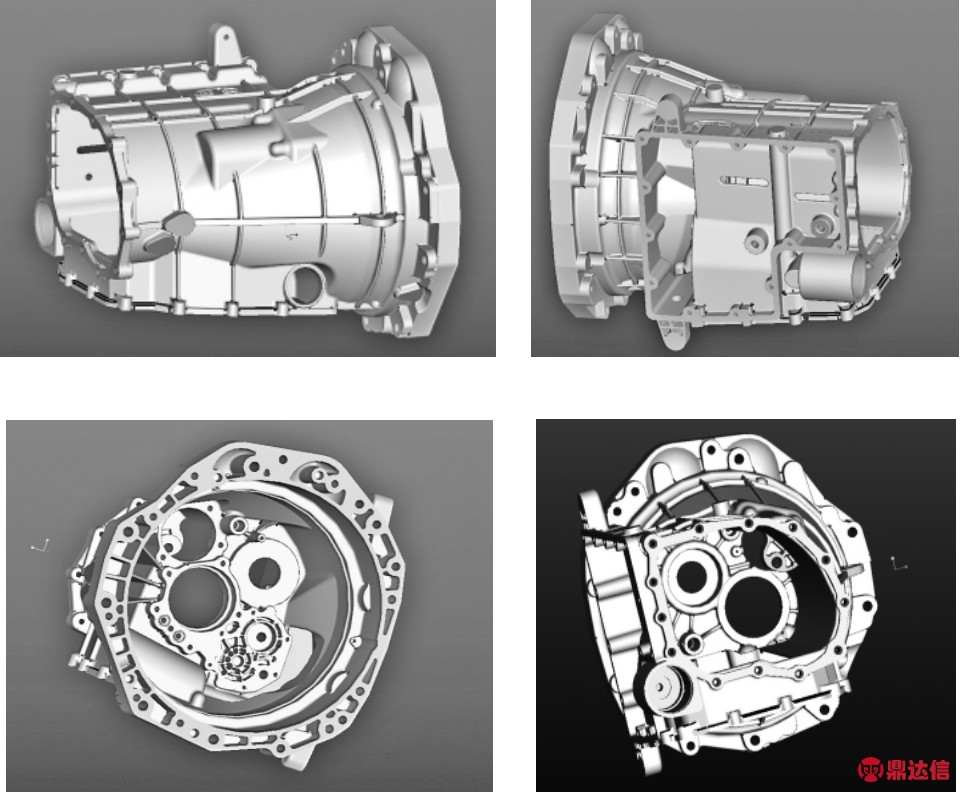
图l 7速自动变速箱壳体压铸件
l 模具方案设计
1.1 对模具结构的初步分析
根据铸件的结构与技术要求,对铸件进行工艺分析,确定主分型面,模具结构为四面侧抽芯,在下滑块的一侧布置浇道,浇道对侧及左侧设置溢流槽,工艺布置如图2所示。为保证铸件有较高的内外质量,模具内必须设置一套合理的冷却、加热通道,保证在压铸过程中处于合理的热平衡状态,必要时可以考虑采用抽真空及局部挤压技术。
1.2 压铸机的选择
1.2.1计算主胀型力
主胀型力:F主=A×p/l0
式中:F主—主胀型力,kN;
A—液态金属在分型面上的总投影面积:l 664 cm2(其中铸件l 280 cm2,另加30%浇注系统的面积);
p—压室压力,耐压薄壁件取90 MPa;
F 主=A×p=l 664×90/l0=l4 976 kN.
1.2.2 计算分胀型力
由于此模具四周形状几乎完全由侧抽滑块成型,侧面分力很大,因此分胀型力不能忽略。
F分=A芯×p×tgα/l0
式中:F分—分胀型力,kN;
A芯—铸件侧抽滑块成型处总投影面积:A右+A左+A上+A下=l000+500+800+400=2 700cm2;α-楔紧角,取l5°;
F分=A 芯×p×tgα /l0=2 700×90×tgl5°/l0=6 5ll kN.
1.2.3 压铸机所需锁模力
锁模力 F锁≥ 1.25(F主+F分)=1.25×(l4 976+6 5ll)=26 859 kN.
因此,结合生产厂家的现有设备,选用设备为布勒2 700 T卧式压铸机,机床锁模力为2 700 kN,冲头直径¢l20 mm.该设备性能优越,稳定性好,有较强的增压能力,冲头具备实时跟踪功能,适合生产该类零件。
2 浇注系统和溢流、排气系统设计
内浇口截面积Ag=G/(ρvt).
式中:G为通过内浇口的金属液质量l3 600 g;
ρ为液态铝合金密度,取2.4 g/cm3;v为填充速度取4.5 m/s;t填充时间取0.l5 s.
Ag=G/(ρvt)=l3 600/(2.4×45×0.l2)=944 mm2.
变速箱零件形状复杂,并且极其不规则,有深腔及端面法兰,非常不利于填充,而且壁厚不均,局部壁厚有2.5 mm,也有壁厚达l5 mm的厚大部位,零件近似于筒形,从产品形状、质量要求及模具结构布置方面综合考虑,选择下方滑块设计浇注系统为最佳方案,内浇道设计在外壁横筋处,为了增加内浇道的面积,利于充型,在不影响产品性能的前提下增加该筋的厚度,由原来的5mm增加到8mm.从左到右,内浇口的宽度×厚度为40mm×4.0mm、64mm×4.0 mm、60 mm×4.0 mm,60 mm×4.0 mm,30 mm×4.0 mm.在左侧、右侧、上方难于充型和最后充型的部位设计溢流槽,便于排气和充型。在排气波板上预留抽真空的位置,设计抽真空安装孔,后期调试如果需要,可以随时采用抽真空工艺,如图2所示。
经过反复计算,采用CAE铸造模拟软件多次对浇注系统及排气系统进行模拟、分析、优化,设计出最终浇注系统和溢流系统,如图3所示。
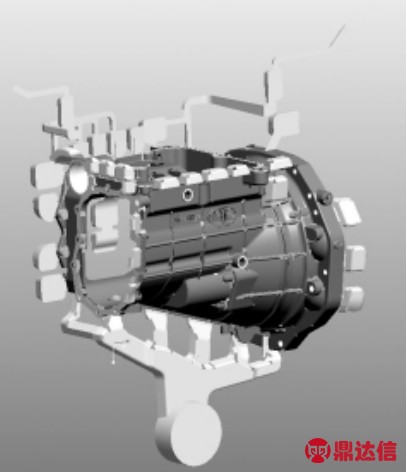
图2 压铸工艺简图
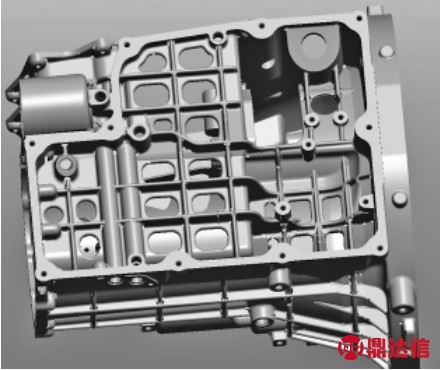
图3 优化后的工艺方案简图
3 热平衡系统设计
热平衡系统主要控制模具温度,对于大型复杂模具非常重要,如果热平衡系统设计不合理,不仅会导致铸件质量缺陷和生产节拍不匹配,严重的会导致模具变形而无法生产。通过软件热平衡模拟分析,预见型腔部分热分布情况及热疲劳部位,对设计的冷却、加热系统进行优化,确保模具在生产过程中保持良好的热平衡,提高铸件质量及模具使用寿命。
3.1 冷却系统设计
冷却系统主要设计在成型部分的衬模与镶块上,起到模具冷却的作用,控制模具在工作过程中的温度平衡,提高产品质量,保证模具连续生产,冷却系统如图4所示。图4中浅色为冷却水路,在局部深腔设计点冷。设计时,将型腔部分的冷却系统通过管路连接到模架外侧,每一个管路设计了单独控制调节流量的开关,可以根据生产的实际情况调节流量、控制模具温度,在模架外侧设计集中冷却器,所有冷却水道集中到这里与设备冷却装置连接,方便拆卸。
3.2 加热系统设计
采用模框油温加热。为提高模具使用寿命,减小模具试模时间,正式生产前需要对模具进行加热,使模具达到正常生产的温度,在模框里设计了加热油道,由设备模温机对模具进行加热,在正常压铸前模具温度达到200℃以上。这样大大减少了试模次数,提高质量,节约成本。图4、图5中深色管道为加热油路。
3.3 模具型腔部分的热平衡温度场及热疲劳模拟结果分析
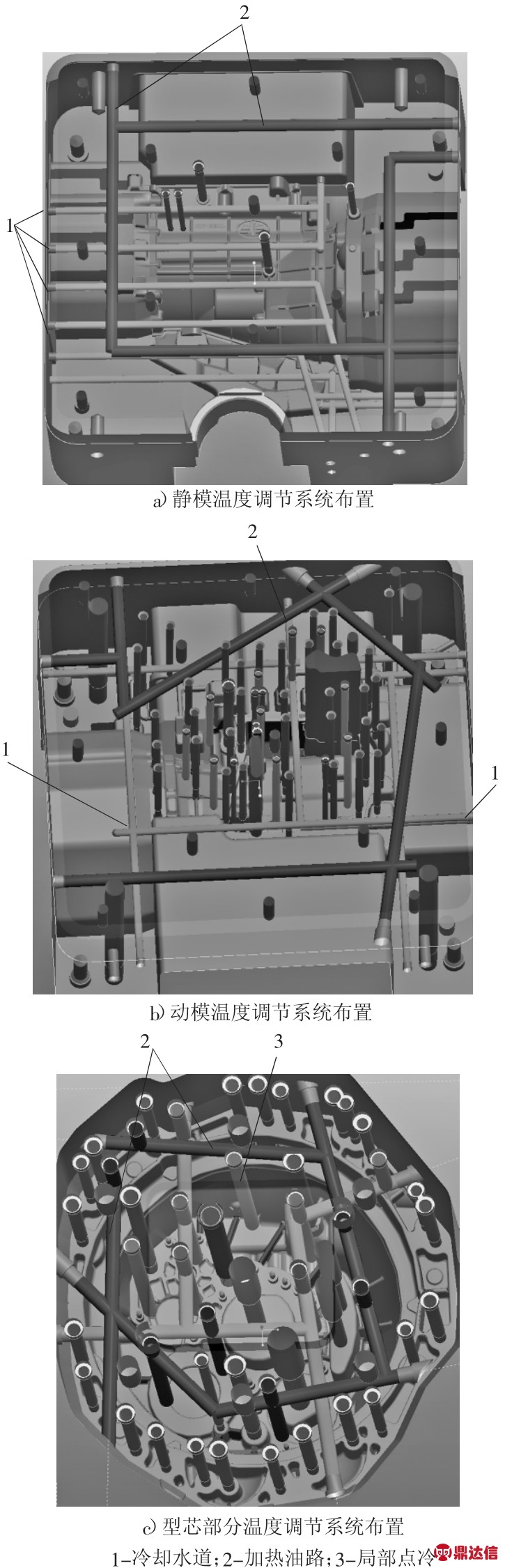
图4 热平衡系统的布置
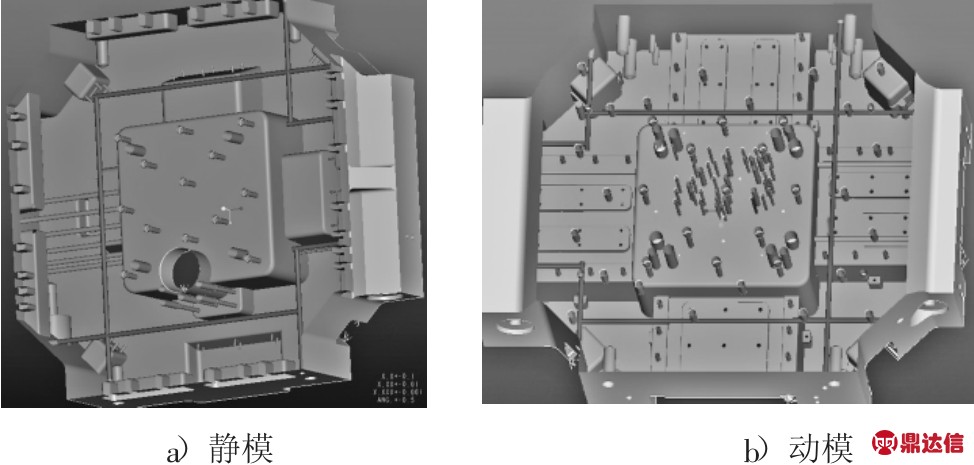
图5 加热系统的布置
用MAGMA模拟软件对模具型腔部分的热平衡温度场及热疲劳进行模拟,模拟结果如图6、图7.
由图6可以看出静衬模区域l温度偏低,区域2温度略微偏高;动衬模区域3明显较周围温度偏低;型芯l上区域4温度偏高;型芯4总体温度分布较均匀;型芯2上的区域5爪形镶块温度偏高;区域6与铸件中间部位接触,温度也偏高;区域7与铸件开口部位配合,温度偏高。
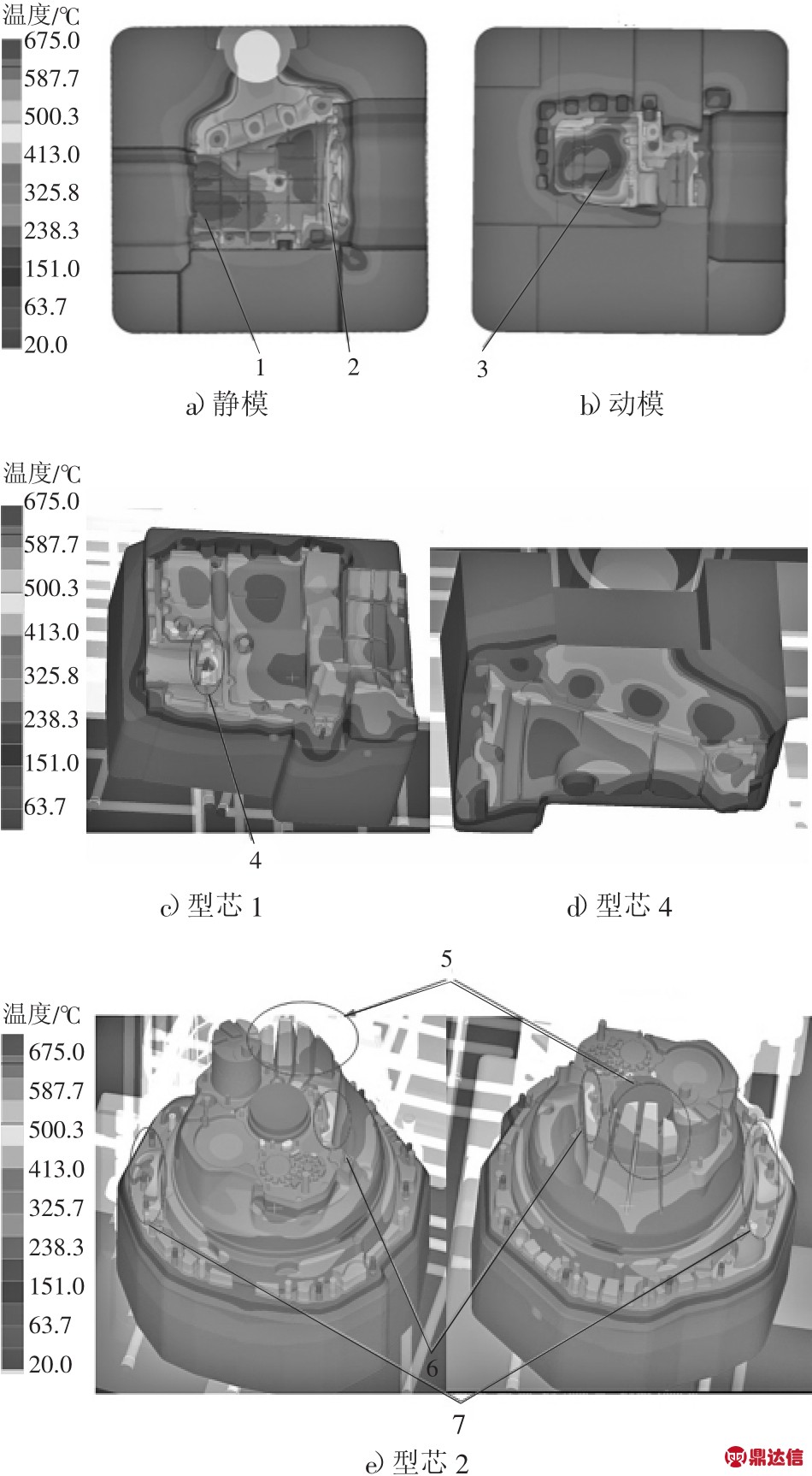
图6 模具型腔部分的热平衡温度场模拟
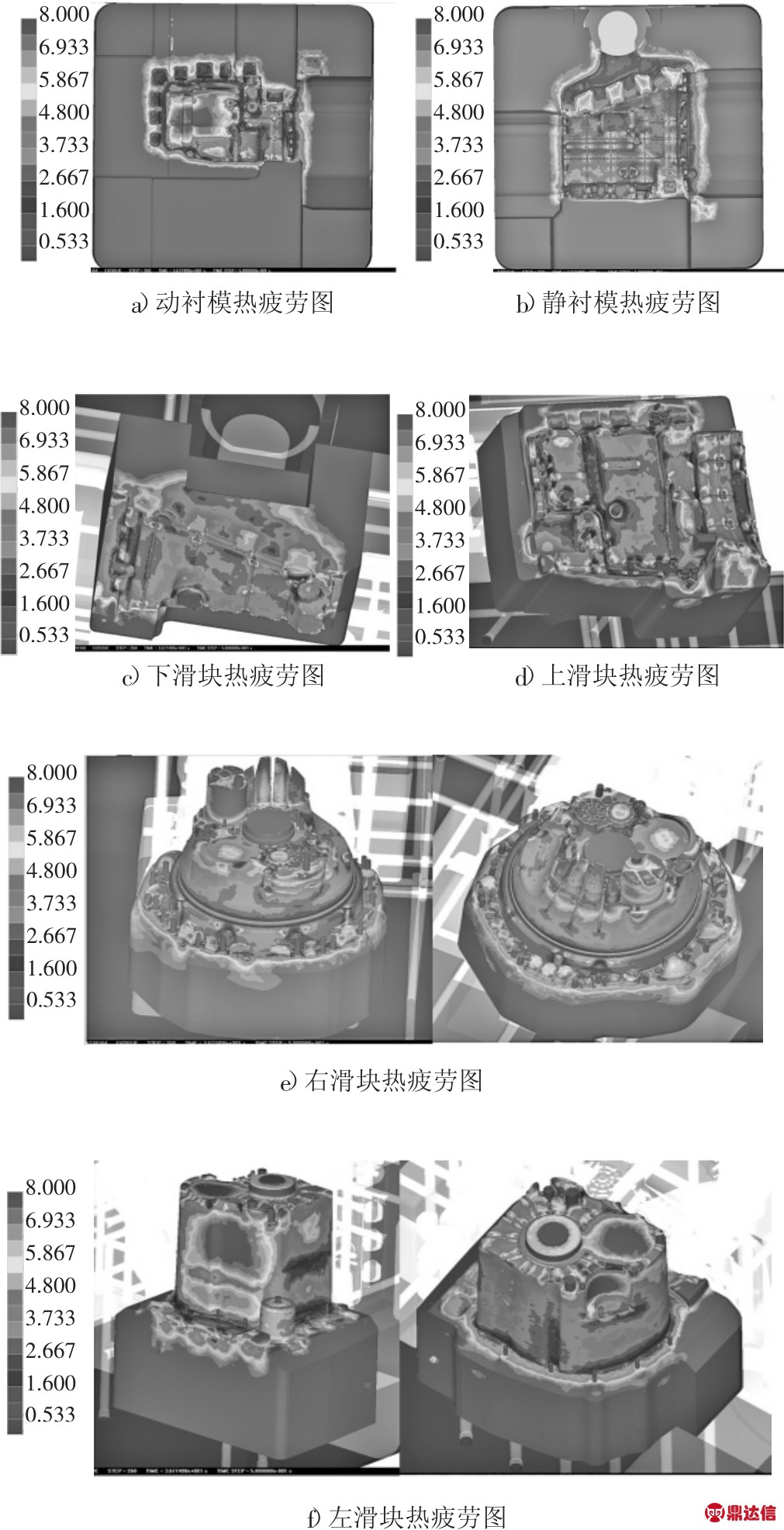
图7 模具型腔部分的热疲劳模拟
根据温度分布情况及热疲劳分布情况,在设计阶段进行优化设计,增加冷却水道和局部点冷,对热结部位及温度低的部位对冷却及加热流道进行调整,同时,根据热平衡模拟分析报告,调节压铸设备上进水温度及流量控制,既保证了正常生产的温度,也避免了局部过热导致模具寿命降低,提高了模具设计质量。
4 模具结构设计
4.1 型腔部分
型腔部分由六部分组成:动衬模,静衬模,上滑块,下滑块,左滑块,右滑块。有效配合面(封铝面)保证在l20 mm~l50 mm,滑块与动衬模滑动配合两侧做出斜度,防止拉伤,型腔凸起较高部位或易损部位做成镶块,更换方便,提高整个模具的使用寿命,见图8和图9.
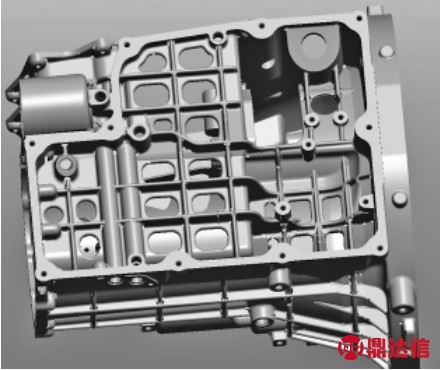
图8 右滑块局部镶块示意图
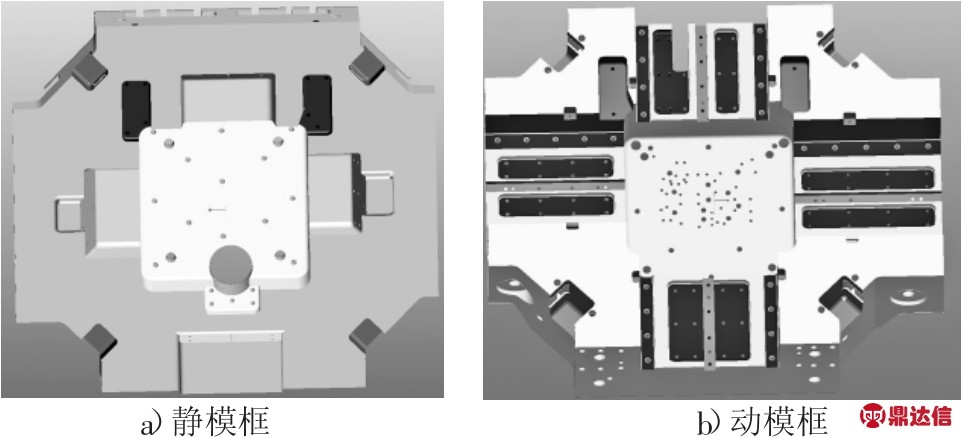
图9 衬模滑块整体位置示意图
4.2模架设计
模架一般包括动、静模框和模板,起着支承模具及连接设备的作用。针对大型模架的设计要充分考虑强度和刚性,防止模具在生产过程中受力变形失效,模架尺寸设计要满足其受力要求。静模框底面紧贴压铸机安装板,受力相对较小,厚度取l20 mm,四个滑块受力面大,闭锁面到四周距离为250 mm,确保闭锁强度。动模框要承受冲头压射力及4个滑块抽芯合模的摩擦力,受力非常大,强度及刚性要求尤为重要,设计底面厚度为l80 mm,外侧壁厚在200 mm左右,见图l0.
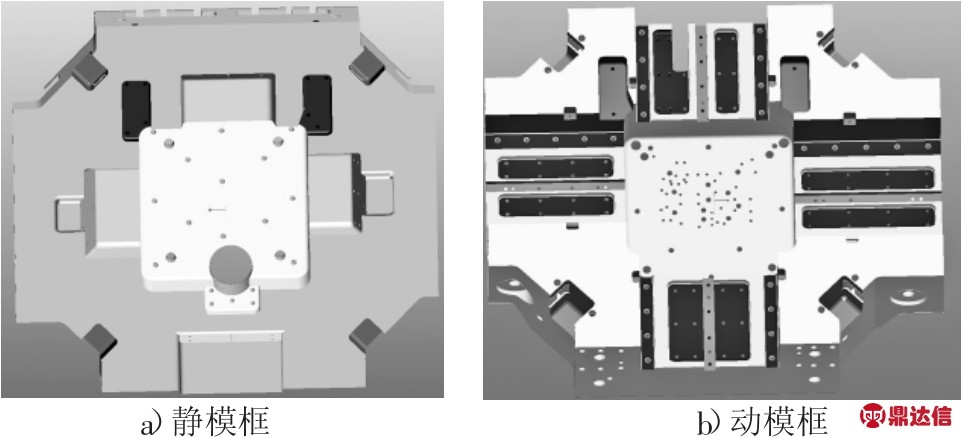
图l0 模架示意图
利用ANSYS软件对模具在压铸过程中的受力情况与变形量进行分析,分析部分结果如图ll,发现在动模底面有产生凹陷变形的趋势(图llc)),在模架支撑设计时,加大支撑面,同时在动衬模背面增加了ll个圆支柱,防止动模变形失效;在模架的四周,由于设计过于保守,出现了一些多余材料可以去除(图 lla)、b)),减小模架尺寸,可以降低模具成本。加支撑柱后经变形量分析,在最大载荷条件下模具的最大变形量为0.5 mm,满足模架在使用过程中变形量小于0.5%的设计要求。
4.3.侧抽液压缸的设计
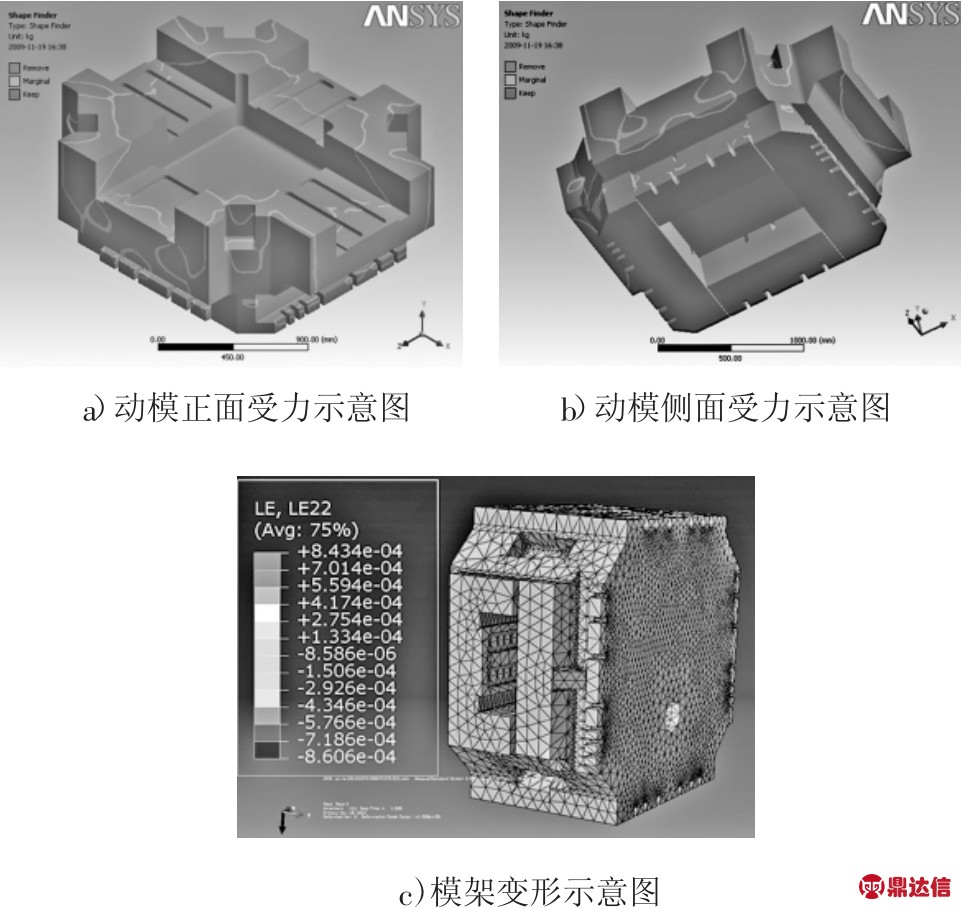
图ll 压铸生产过程受力情况与变形分析
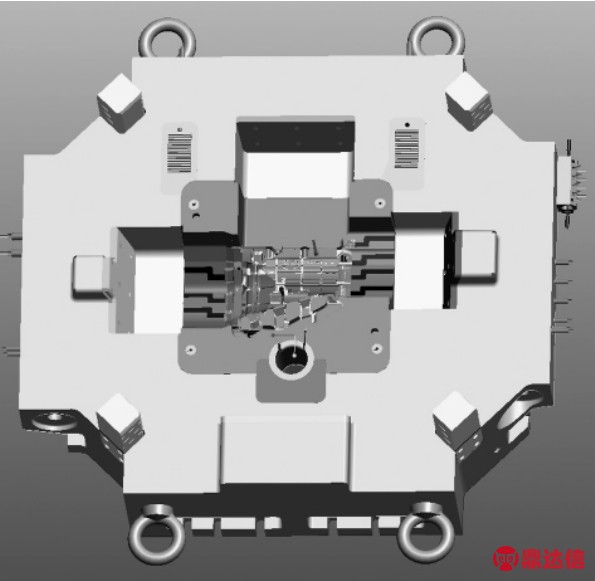
图l2 静模
上、下、左、右四个滑块及局部挤压装置采用普通液压油缸抽芯,由行程开关控制,而不是采用感应油缸,原因一是为了降低成本,同种缸径的感应油缸要比普通油缸贵l/3以上;二是便于维修,感应油缸一旦损坏,难于维修。根据滑块抽芯力的计算,确定左、右、上侧滑块抽芯液压缸直径为φ200 mm,行程分别为290 mm,350 mm,200 mm,(包括l5 mm的安全量),下侧滑块抽芯液压缸直径为φl80 mm,行程80 mm.
4.4 顶出单元设计
顶出装置由安装在顶出板上的顶针在设备顶出杆与模具复位机构带动下完成顶出制件的动作,顶出行程为l20 mm,顶出后由取件机器人抓住料柄取件,顶出单元设计有复位杆、导向柱、圆支柱及后限位等。顶针采用直径为φl2 mm的标准件,便于更换维修。
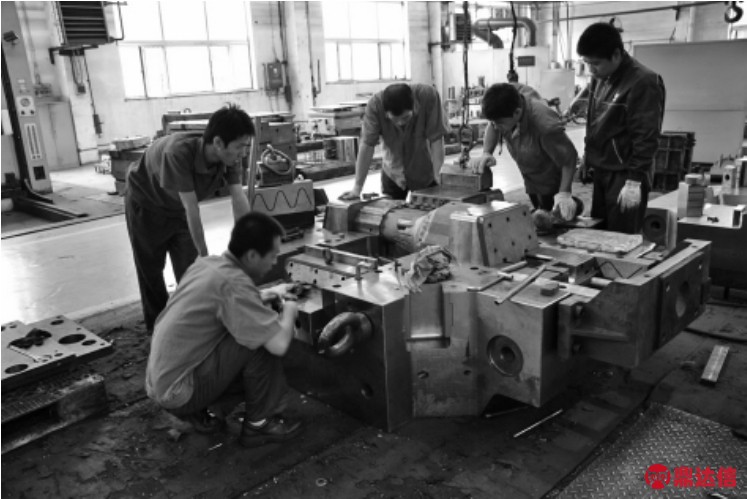
图l3 动模及滑块顶出机构

图l4 模具整体结构
4.5 模具整体结构布局
整个模具分为静模部分,动模部分,上滑块部分,下滑块部分,左滑块部分,右滑块部分,顶出部分。模具总重30 t,其中静模部分重l0 t,天车载重20 t,模具安装调试时,动、静模分开安装。天车完全能起吊,保证生产顺利进行。图l2为静模部分,图l3为动模及滑块顶出部分,图l4为整体结构。
5 模具材料及热处理
模具镶块及侧抽滑块等成型零件采用优质模具钢PHl3,采用真空淬火处理,硬度HRC42-44;型芯、推杆采用优质模具钢SKD6l,淬火硬度HRC42-44;方导柱、导板、滑道及耐磨板采用Hl3,淬火硬度HRC44-46,表面氮化处理,氮化深度0.2 mm~0.3 mm,避免压铸过程中拉伤及卡死;模板采用50#钢,调质HRC28-32,推板、推杆固定板采用45#钢,调质HRC28-32.
6 加工制造
模架尺寸非常大,单件重达l0 t~l5 t,需要专用设备方能加工,故动、静模框采用外购,型腔零件和其他部件均为自制,分为热处理前粗加工,热处理后半精加工和精加工部件加工,成型部分全部采用CNC加工,局部深腔及筋槽采用电火花加工,加工完毕经检测合格后进行装配,装配时需要研配所有配合面,确保间隙均匀,对于静止不动的配合面间隙控制在0.05 mm以内,对于滑动配合面,要充分考虑模具受热膨胀的因素,既要确保生产时不因间隙过小而拉伤,也要考虑不因间隙过大而钻铝,因此间隙控制在0.05 mm~0.1 mm,装配过程见图l5.
7 试模及结论
7.1 第一次试模
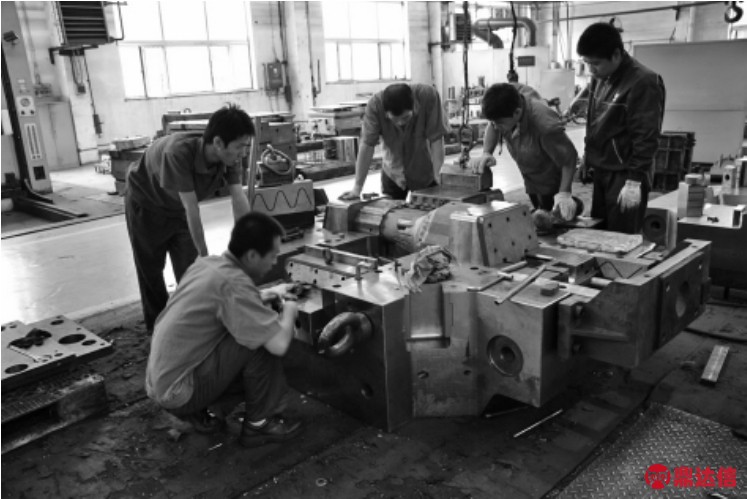
图l5 模具装配
根据模拟时的参数设置和实际生产情况,调整压铸参数,整体铸件充型顺利,表面质量比较好,没有明显缺陷,仅仅在左侧上方离浇口远端位置有轻微冷隔,提交了试加工的样件,见图l6.
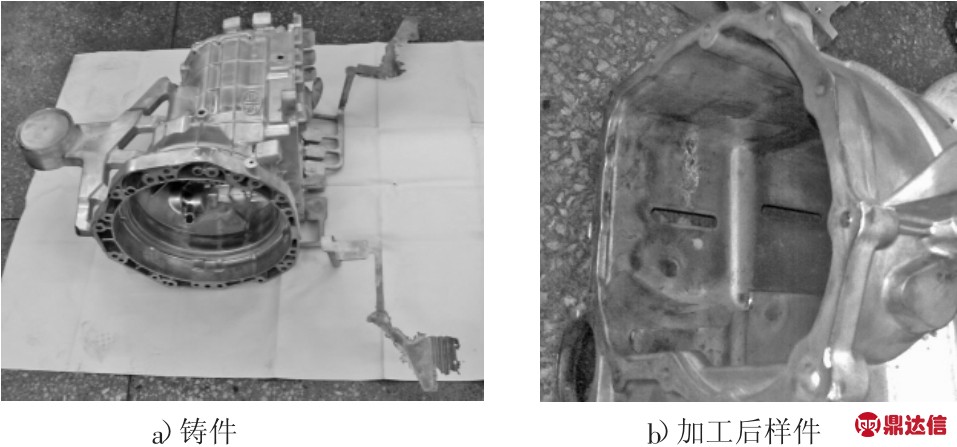
图l6 第l次试件
7.2 完善设计及第二次试模
第一次试模发现左端的冷隔,机加工发现左侧油泵孔有卷气现象,仔细分析原因,查看初始设计的模拟情况,决定加大左侧第二道浇道(图l7中l),同时在铸件左侧增加集渣包和排气道(图l7中2),铸件中间增加过桥(图l7中3).加快该区域的充型速度并且加大排气,经过重新模拟,结果该区域缺陷完全消失。
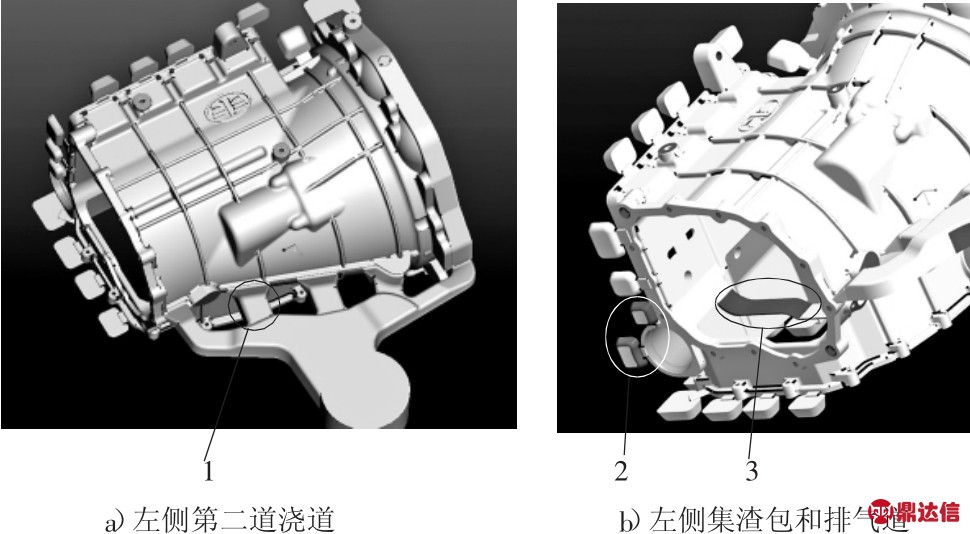
图l7 改进后工艺
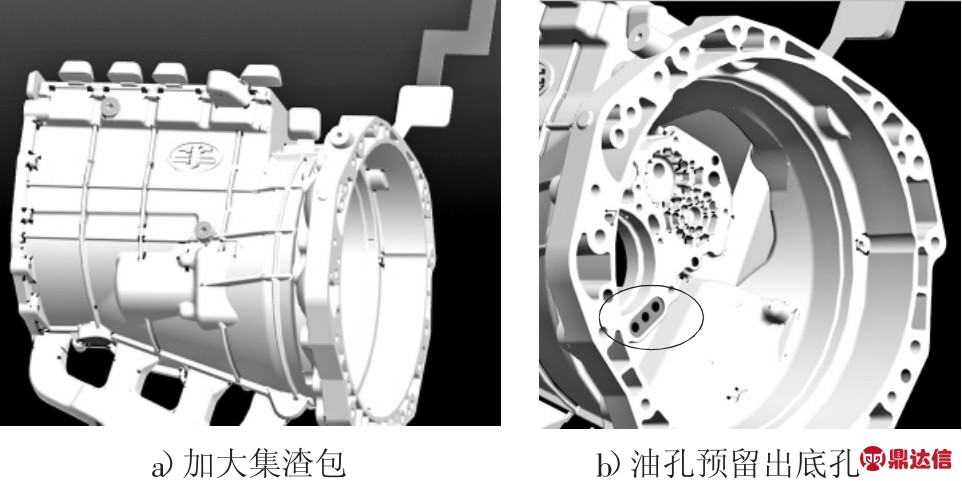
图l8 进一步改进工艺
经试模,更改后的铸件有较大改善,但是上滑块右侧筋充型不好,表面有缺陷;经过打压试验,与油底壳相通的三个油孔漏油(该孔压铸没有预留出底孔,机加工而成)。
7.3 完善设计及第三次试模
在2次试模的基础上经过分析,决定采取如下方案:右侧上方集渣包加大,开设排气(图l8a));把右侧滑块的三个油孔做出预留底孔,避免气孔和缩松(见图l8 b)).改进工艺后经试模生产出合格的制件,满足了一汽轿车的质量要求(如果采用真空压铸,产品质量会更佳,但压铸成本可能会上升)。
7.4结论
一个产品的成功开发,产品设计是基础,产品设计首先应满足产品使用特性要求,确保产品使用功能,同时也应该满足模具设计及生产工艺要求;接下来的模具设计环节要针对产品使用特性制定相关的解决方案,利用CAE手段分析模拟实际生产情况,在设计阶段把生产过程可能出现的问题及风险提前解决,减少后期生产调试周期,缩短合格产品的提交周期;在模具加工制造环节,要充分理解产品特性及模具特性,制定合理的加工方案,确保模具各种尺寸符合模具设计公差要求,从而达到产品使用特性的要求;模具调试过程是对前期产品设计、模具设计、制造的验证,把理想设计转化为实际产品的过程,理论和实际还是有一定的差别,需要通过调试,不断完善设计,摸索总结符合实际生产的参数,为将来正式生产提供依据。所以一个完整的模具设计应该从产品设计开始,一直到提供合格样件后才算完成。
8 后续完善
随着第一台自动变速箱的成功开发,后续经过不断完善,从产品和模具两个方面进行了优化,最大限度地提高产品的质量,降低了废品。8.1 产品设计优化完善
l)铸件上中间的筋加厚到l0 mm,不仅可以作为铸件与浇口的搭接,而且还提高了产品的强度,见图l9部分。
2)在铸件的内腔及外部加筋,便于合金流动,避免应力集中,如图20所示。
3)优化产品的加工工艺,将铸件中一些孔直接压铸出来,不加工,既降低了加工成本,同时也提高了毛坯质量,避免机加工废品。
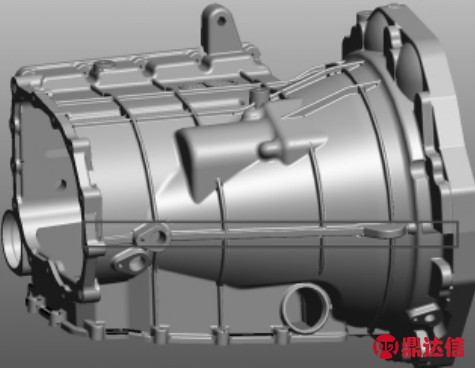
图l9 铸件设计加厚中间筋
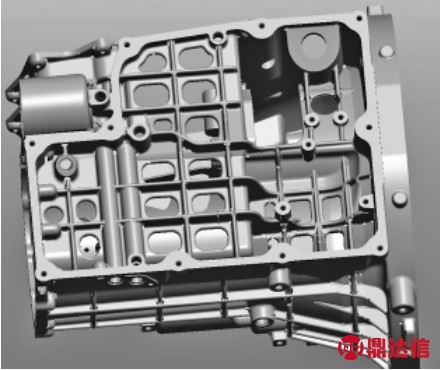
图20 铸件内腔及外部加筋结构
8.2 铸造工艺改进及模具改进。
l)浇注系统:将内浇口改为整体直冲式,见图2l,减少金属液相互冲击,避免卷气,使充型更趋于平稳。
2)优化模具结构,将浇口远端容易有缩孔的位置,设计局部挤压装置,避免缺陷,见图22.
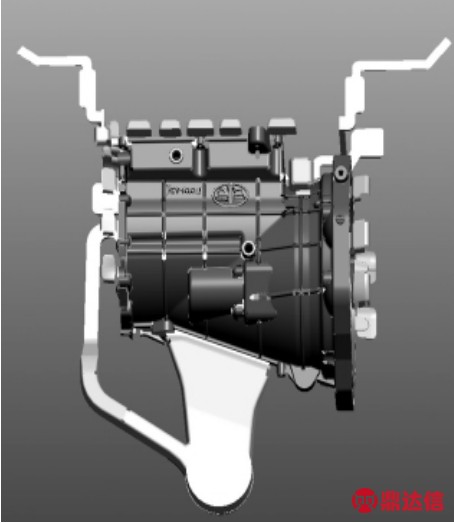
图2l 改进后的浇注系统
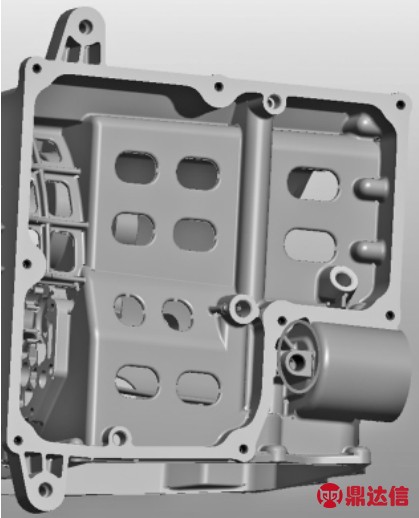
图22 局部设计挤压装置
3)优化压铸工艺,应用抽真空系统,降低产品的内部气孔。