摘要:针对真空浇注盖车的启停和控制问题,采用CU240作为控制器,结合自由功能块编程技术,通过对浇注盖车行走特性进行分析,确定盖车的启动和行走模式,实现由变频器控制真空浇注盖车运动。
关键词:变频器;自由功能块;G120
真空浇注盖车用于运输升降真空铸锭盖,某浇注车间每4台真空室配有有2个盖车。每个盖车采用1套独立的控制柜控制。笔者根据盖车的运行特性,采用基于变频器的自由功能块技术控制盖车的传动电机,以满足浇注生产对盖车的控制要求。
1 盖车结构简介及控制要求
真空浇注盖车由一个设有真空铸锭盖升降装置的钢结构车架和4组平衡轮组成,由电机和减速器驱动,电机采用变频调速精确定位。真空罐盖升降机构安装在台车顶部,采用两个液压缸通过连杆链条实现罐盖的升降。盖车两侧设有添加保温剂的料斗,料斗通过液压缸实现开闭(见图1)。
真空浇注盖车轨距8.5 m,轮距7.3 m,走行距离13 m,走行速度2~10 m/min,停车定位精度10 mm。工作时,盖车缓慢启动到达变速限位时,系统给出稳速运行信号,盖车稳速运行到接近工作位时,先在变速限位位置处减速运行,最后到达停止限位时停止。借助行程开关实现盖车慢起动、稳速运行、减速停车三段控制功能,确保设备平稳运动和高精度定位。
提升真空盖时,电气系统发出提升信号,液压缸活塞杆外伸,推动摇臂旋转带动链条提升真空盖,当真空盖提升700 mm时,限位开关发出到位信号,液压缸停止;在放下真空盖时,电气系统给出下降信号,真空盖下降700 mm,限位开关给出到位信号,液压缸停止。通过加料斗向真空室内添加保温剂时,电气系统发出信号,液压缸活塞杆回收,打开扇形门,加入保温剂;关闭扇形门时,电气发出信号,液压缸活塞杆外伸,关闭扇形门。
2 控制系统
考虑到盖车控制点数较少,设计时采用G120变频器控制行走电机,将行走限位信号接入变频器,采用内部控制逻辑管理电机的启停和行走。真空盖提升控制和扇形门的控制直接由继电器回路控制相关的液压阀组,在此不再介绍。
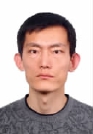
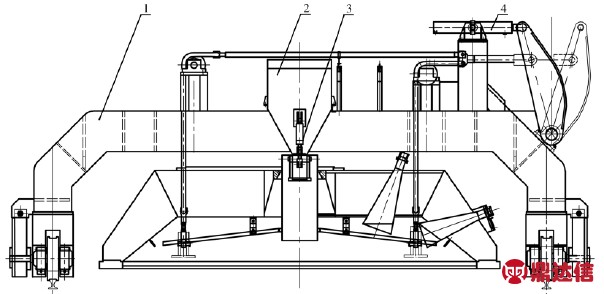
图1 真空浇注盖车设备组成示意图
1—车架;2—加料斗;3—料斗液压缸;4—盖提升液压缸。
2.1 G120变频器特点
G120是一款模块式变频器系统,主要由功率模块和控制单元构成,为方便调试和维护,还可以增加操作面板和存储卡等选件[1]。功率模块采用高性能的IGBT和先进的PWM脉宽调制技术,可以在控制单元的控制下完成对电机的多方面保护,可驱动的电机功率范围是0.37~250 kW。控制单元可以为变频器提供闭环控制功能,控制模式有多种选择,并配有ProfiBus DP和ProfiNet接口,可以与自动化系统高效整合。
变频器内的所有热损耗均通过外置的散热片散热,控制单元采用标准的自然对流散热。可以在操作面板设置参数,在起动变频器后,通过操作面板可以监视电机运行状态,获取故障和报警等重要信息。该操作面板还支持带电热插拔,由于变频器运行时不需要使用操作面板,所以也可以采用几个变频器共用1个操作面板的方案,调试时将面板装到待调试的变频器控制单元上。
2.2 主电路设计
为限制变频器的整流单元在换相时电网侧的电压降和抑制谐波,在变频器的电源侧设有进线电抗器L1。进线电抗器还可以平滑变频器的输入电流,从而延长变频器的使用寿命。
针对无线电干扰敏感的区域,应当加装进线滤波器。变频器负载侧的输出电抗器L2,用于补偿电机电缆的电容充电电流,限制电缆电容在电机绕组上的电压上升率。
盖车的2台电机分别驱动左右车轮,两侧车轮均固定在盖车本体上,机械同步,所以这2台电机用1台变频器拖动。在变频器一拖多时,需单独为每台电机配备电机断路器或热继电器进行过载保护(见图 2)。
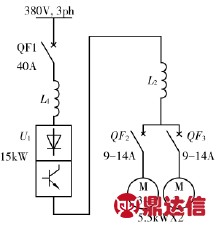
图2 盖车行走电机单线图
2.3 控制方式的选择
从控制方式上看,G120变频器具有恒压频比控制模式(V/f控制)和矢量控制方式(VC控制)。在一拖多时,由于电机参数和电气特性的差异,推荐使用V/f控制[2]。因为这种控制方式不依赖电机参数,不需要速度反馈,控制方法简单,易于实现。V/f控制目标是使电机内的磁通量Φ保持恒定。磁通量与压频比成正比,电机产生的转矩M与磁通量和电流的矢量积成比例。

为了在给定的电流下产生尽可能大的转矩,电机必须在恒定且尽可能大的磁通量下工作。
3 FFB控制逻辑
针对盖车电机的启停和变速等控制要求,若采用传统的继电器控制系统,由于需要在启动、加速、减速和停止各个速度区间切换,依次完成运动过程,且还需要设置互锁回路,控制电路复杂且难以维护。在继电器控制系统中,由于反馈接触器状态的辅助触头不能重复使用,为此还需要添加很多辅助触点,且需逐根接线,由此造成系统故障点较多,给后续调试及改造升级留下了隐患。而PLC以强大的控制功能,丰富的运算能力得到广泛应用。但是采用PLC必然增加项目的成本。因此,本系统最终采用变频器内置的FFB(Free Function Blocks,自由功能块) 控制,通过使用变频器中的数字量输入点采集限位开关信号,用FFB搭建调节电机速度的控制逻辑,特点是控制参数可以重复调用,控制回路清晰,升级方便。通过FFB中灵活的逻辑运算功能块设计,可以很好地完成各个电机速度区间的切换,并且修改非常简单,便于系统的调试、维护。
3.1 机械限位布置
在盖车上,装有4个摇臂式限位开关。限位开关采用金属外壳,结构紧凑,内部的单极转换开关具有开关重复精度高的优点,能够确保准确定位。该开关还具有高抗震性能和高防护等级。限位开关编号分别为SE1~SE4(见图3)。
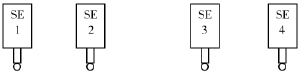
图3 盖车行走限位布置示意图
挡铁在地面固定端的左右极限处,长度400 mm。SE1和SE2间隔300 mm,SE3和SE4间隔300 mm,SE2和SE3间隔600 mm。盖车向左行走,当SE1发出信号,机构减速;当SE2发出信好时,停车。盖车向右行走,在SE4发出信号时,盖车减速;当SE3发出信号时盖车停车。
3.2 控制逻辑
在FFB中可以使用基本逻辑单元完成应用中所需的控制应用,按照盖车的控制要求,将四个限位信号接到控制单元的数字量输入端口上(见表1)。
表1 CU240E-2地址分配
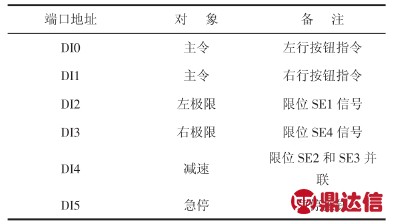
在测试完成相应信号的基础上,设计启动逻辑(见图4)。可以看出,当盖车位于左极限位置时,SE1和SE2发出信号,经与非门0后,封锁了左行命令,使盖车无法再向左移动,仅右行命令有效;而当盖车位于右极限位置时,SE3和SE4发出信号,经与非门1后,封锁了右行命令,使盖车无法再向右移动,仅左行命令有效。而当盖车不在两端极限位置时,可左右自由移动。通过调整SE1和SE4的左右极限位置,可以使盖车停止时真空盖位于真空浇注炉的正上方,即工作位置。本控制逻辑共需要5个与门和2个非门,控制单元中的逻辑门数量可以满足要求。
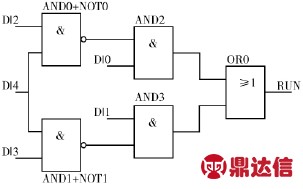
图4 自由功能块(FFB)控制逻辑示意图
经过进一步分析后发现,将两端限位开关的接线方式改为常闭型,就可以简化控制逻辑(见图5)。经过优化的控制逻辑仅需要3个与门即可满足要求。
3.3 速度设定
真空浇注盖车的设计时速为2~10 m/min,齿轮电机的额定转速为970 r/min,速比160,车轮直径Ø365 mm。依据式(2),可知允许的电机速度区间为280~1 400 r/min。考虑到盖车行走时会发生晃动,设定行走速度600 r/min,减速速度设为150 r/min,正常行走时盖车速度为4 m/min,符合设计要求。
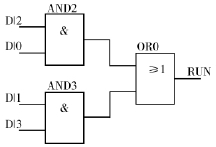
图5 自由功能块(FFB)控制逻辑简化图

式中,v—盖车速度(m/min);i—速比;D—车轮直径(m)。
通过设置变频器转速固定值,可以实现盖车减速停车(见图6)。当盖车不在减速位置时,SE2和SE3均不动作,DI4为0,DI4的反为1,此时给定速度为600 rpm;当盖车进入终端的减速位置时,SE2或SE3动作,DI4为1,DI4的反为0,此时给定速度为150 rpm,从而进入减速停车阶段。
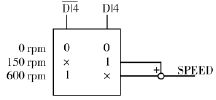
图6 盖车行走速度选择器
3.4 采样时间设定
CU240控制单元的采样时间从8 ms到256 ms,共分6档。将采样时间设置为8ms时,在触发SE1或者SE4到盖车停止的时间内最多走行0.5 mm,完全满足停车精度10 mm的控制要求。
4 结语
由变频器控制的真空浇注盖车起动及走行平稳,工作正常,满足使用要求。利用变频器控制单元内置的自由功能块编程,输入量少,控制逻辑较为简单,与PLC方案相比节省硬件费用,又可以避免用中间继电器搭建电路带来的布线复杂,不便修改等缺点,是一种值得推广的应用方案。