摘 要:为了使冷加工精密不锈钢成品管外表面粗糙度达到产品质量要求,开发了一种精密不锈钢管外表面智能抛光设备。该设备采用自浮动磨削工艺,可处理钢管外径范围为19~114 mm,可处理钢管长度1 000~12 000 mm,抛光后表面粗糙度Ra≤0.4 μm,单边单次最大去除量为0.03 mm,抛头数量为9组,最大抛光速度为20 m/min。应用结果表明,该抛光机抛光后的产品表面质量达到了设计要求,可适用于航天、航空、医药、核电、军工等领域用精密管的表面处理加工。
关键词:精密不锈钢管;抛光设备;智能抛光
不锈钢抛光包括中间品抛光和成品抛光。中间品抛光又称粗磨,在热穿孔、退火酸洗后或冷轧、冷拔成品管工序之前进行,目的是清除热穿孔和退火酸洗工序造成的表面缺陷,改善外观质量;成品抛光又称精磨抛光,在冷轧、冷拔成品退火、酸洗工序后进行,以得到某种特定的表面质量,满足核电、石油、化工、航天、航空、医药、军工、精密仪器等领域用管材的特殊要求。
不锈钢钢管的抛光属于重要的前道工序,其抛光量除与原料质量有很大关系外,还与设备能力、工人操作水平等有关。
不锈钢管外表面自动智能抛光设备的工作流程为:输送轨道将不锈钢坯料管向前输送,当坯料管运行到修磨抛光头附近,限位开关检测到坯料管接近位置时,千叶轮抛头开始下压并进行修磨;当管坯脱离抛光头,修磨抛光头抬起。不同规格和不同修磨量,可以通过人机界面输入规格参数、抛光头正压力参数来实现自动修磨抛光。
随着产品质量的提高和升级,精密不锈钢管各道精整工序,尤其是抛光工序显得越来越重要。精密不锈钢管在每道工序后均需要进行抛光,传统的抛光方式多为人工抛光,效率低,污染严重。本研究设计的不锈钢管抛光设备及方案可实现不锈钢成品钢管自动抛光,并可根据产能分类计算,可做出基本抛光产能的匹配方案,同时还解决了环保除尘的问题。
1 自浮动磨削加工抛光机
自浮动磨削加工抛光机的结构如图1所示。该抛光机主要由上料台架、上料拨料装置、输送轨道、抛光机组、下料台架、操作间、气动系统、润滑系统、电气控制系统等组成,主要用于磨削不锈钢钢管外表面的锈迹及缺陷,使钢管外表面达到所需的表面质量要求。
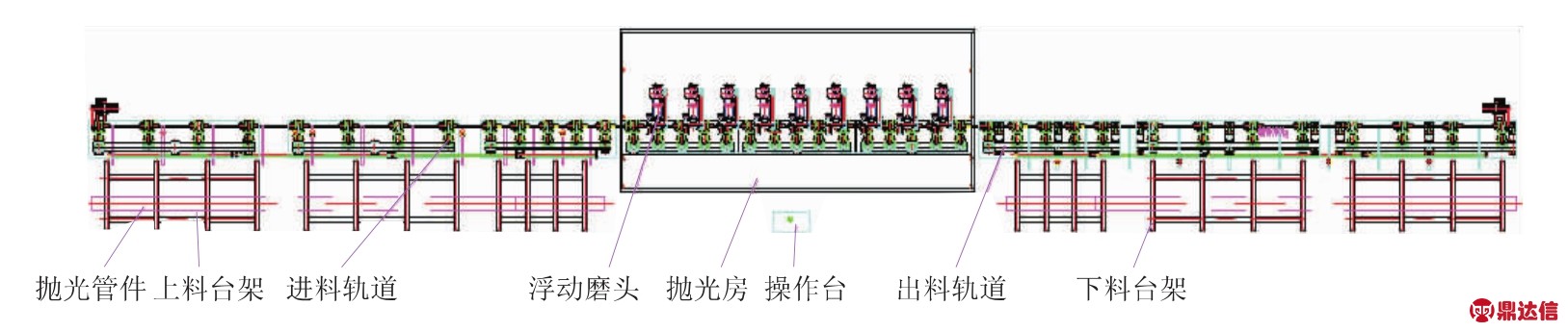
图1 单边(局部)浮动磨削加工抛光机结构示意图
1.1 主要技术参数
适用钢种:奥氏体不锈钢、 双相钢(含超级双相钢)、镍基合金。
钢管外径:19~114 mm。
钢管长度:1 000~12 000 mm。
抛光前管坯情况:硬度HB≤300,Ra≤1.6 μm,直线度≤3 mm/m。
抛光后表面粗糙度:Ra≤0.4 μm。
单边一次最大去除量:0.03 mm。
抛头数量:9组。
最大抛光速度:20 m/min。
自浮动磨削抛光机采用干抛和湿抛两种工作方式,干抛主要用于集中除尘,湿抛是指抛后水洗并吹干。抛光方式采用千叶轮,钢管状态为常温。
1.2 各设备单元结构组成及其功能
1.2.1 上料台架
上料台架实物照片如图2所示,上料台架由固定台架、链式驱动、拨料机构等组成。
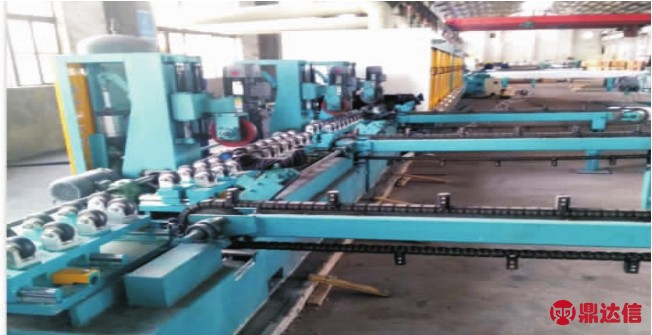
图2 上料台架实物照片
工作时,由起重机将坯料吊放在固定台架上,钢管沿台架面转动至固定台架前端的取料位置处。取料臂在电机减速器的驱动下抬起将钢管输送到轨道位置,拨料臂缓慢落下将钢管轻放于旋转托轮上,确保钢管在输送辊轮台架上顺利运行。
1.2.2 抛光机组
该装置由立柱、Y132 S2-2电动机、UCPC208带座外球面轴承、SC50x30S气缸、气缸接头、LT10-C150-24-RL1电动推杆带磁石、千叶轮抛头、修磨管坯、输送轨道托辊的组成。当坯料管在输送轨道上运行到抛光磨头附近,由检测感应开关传递信号,抛光磨头开始下压进行加工,当管坯脱离抛光磨头时,抛光磨头抬起,周而复始。同时抛光磨头加载系统由气动系统来实现,抛光磨头共由9组千叶轮组成。针对磨头砂轮机组部分,抛光磨头采用功率7.5 kW主电机。每道次单边表面磨削量为0.005~0.02 mm,主要由气压及磨头转速及输送速度进行控制。磨头转速为2 900 r/min,且变频可调,修磨后表面粗糙度Ra=0.01~0.04 μm。
根据坯料管直径大小、抛光磨头上下升降的位置可自动(或点动)调节。当抛光磨头外径减小到极限位置时,到达SC50x30S气缸同限位时,该装置发出信号,由LT10-C150-24-RL1电动推杆带磁石来调整一个单元行程,始终保持抛光磨头与管坯外表面接触,并具备一定连续性的往复修磨压力,操作人员可通过人机界面设定压力大小、管坯规格等参数来实现可控调节。磨头加载系统由气缸、ITV2050-012CL电气比例阀控制。通过气动节流阀、电气比例阀、EHTV-G1/4液压管式双向节流阀调节用气量,实现气缸压力的大小可调,从而实现磨削量的适当增加。气动系统主要由气源、阀架、中间管线及执行元件等部分组成。气源来自于车间主压缩空气管线,阀架主要包括气动三联件、电磁阀、气动比例阀、消声器等元件。抛光磨头架实物照片如图3所示,抛光机组结构如图4所示。
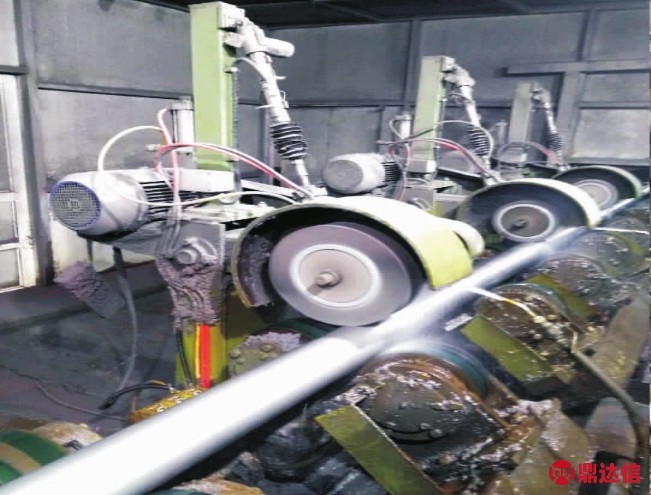
图3 抛光磨头架实物照片
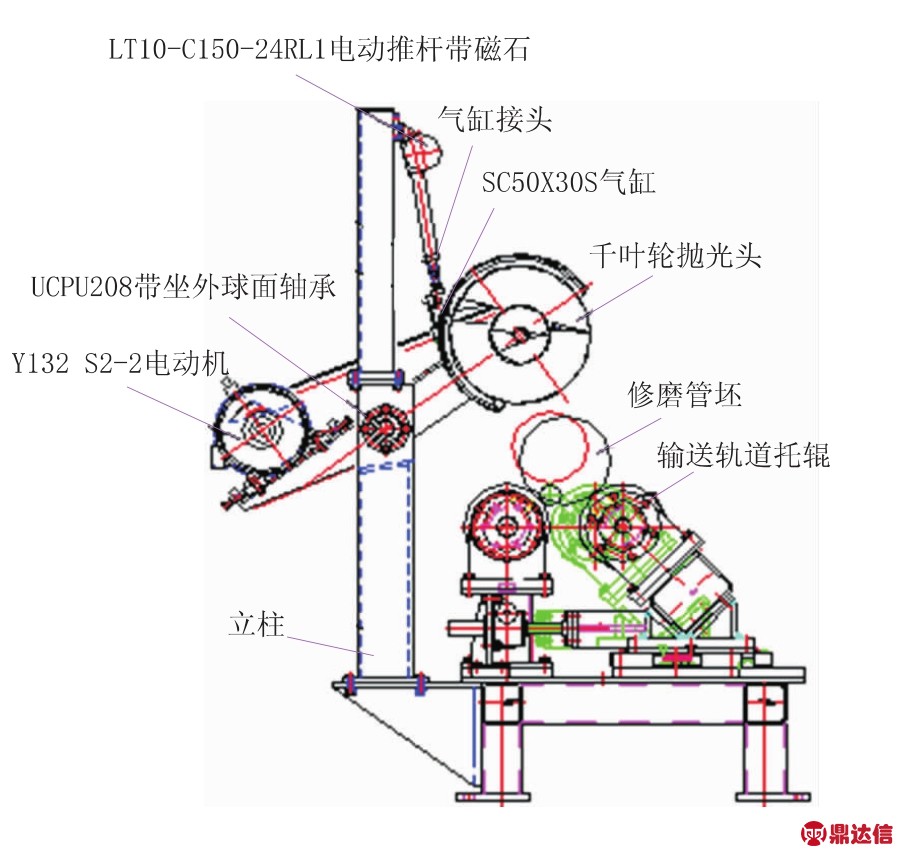
图4 抛光机组结构示意图
1.2.3 下料台架
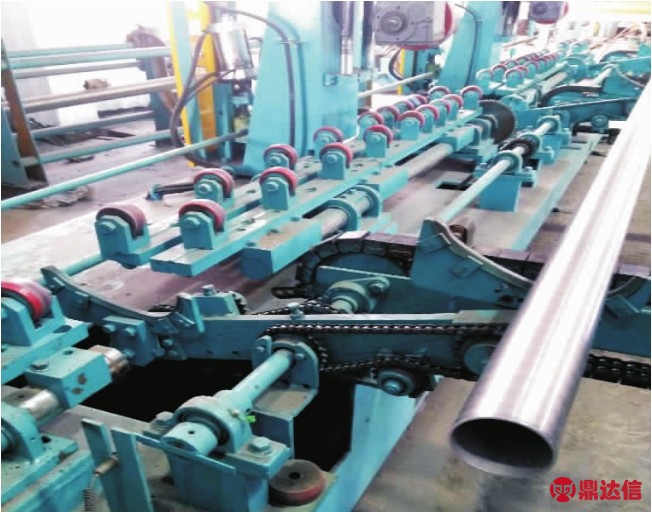
图5 下料台架实物照片
下料台架实物如图5所示,由固定台架、拨料机构、回转臂拨料机构等组成。下料台架整体长度约10 000 mm,宽约2 100 mm。
1.2.4 抛光室
抛光室起安全防护和除尘隔音作用,抛光室一侧设计有观察窗口及检修门,供维护、维修使用。
1.2.5 除尘装置
除尘装置由除尘器及除尘管道组成。一个放散管,带安全爬梯,管道设计有电动蝶阀。电机功率为30 kW(带变频器)。除尘也可通过湿式方法进行(干式、湿式两用)。
1.2.6 电控系统部分
自动控制系统由PLC、HMI、远程I/O、检测元件等组成;完成时序控制、闭环控制、联锁、故障和警报检测、信号检测及通讯等功能。PLC柜内装设西门子S7300系列PLC及其输入输出模块等装置,可以实现对全过程的自动控制及与其他设备的衔接。操作台采用人性化设计,舒适方便,配有操作开关。变频调速系统控制变频器起动、停止、保护及调速。MCC系统控制各电动机的起动、停止以及保护,并提供控制电源。检测传感器等监测系统提供设备自动化需要的各种检测信号。
整体过程控制采用西门子S7300系列,并带EEPROM存储卡,采用PC编程。采用PROFIBUSDP工业现场总线将HMI、PLC、远程I/O、调速装置及检测设备连接起来,两者之间通过PROFIBUS-DP网络连接,工控机DP口与PLC相连,使整个系统组成一个有机的整体。
PLC基本功能为:
(1)抛光机设备现场操作台面板上各设有选择开关,可根据需要选择“手动”或“自动”。
(2)当选择“手动”时,各设备之间无联锁功能,此功能仅作为调试或检修用。
(3)正常生产时自动控制,以减少人工操作;当选择“自动”时,各设备之间联锁。按下“自动启动”按钮时,各单元设备按一定间隔时间分别启动;同样,按下“自动停止”按钮时,各单元设备按一定间隔时间顺序停止运行。
(4)按下单体设备任何一处的 “紧停”按钮,该设备立即转入停止状态,而不再是顺序停机。当人身及设备或人员安全受到严重威胁时才使用该功能。
(5)如设备出现故障,操作箱面板上的故障指示器就会发出声、光报警,同时,代表该设备相应的故障指示灯亮,工控机上也有相应的故障文字提示,便于检查和维修。
电气控制系统包括:修磨机及上下料辅机。自动控制系统由PLC、检测元件等组成,主要完成时序控制、 闭环控制、联锁、故障和警报检测、信号检测等功能。
钢管抛光机HMI操作站负责工艺过程及设备管理的监控。包括设备、工艺参数的设定、生产过程中各设备状态和电气参数的动态显示及工艺参数的人工调整。电气设备的一般功能性及方式性操作。故障报警与记录等。钢管抛光线主要工控机界面包括工艺主界面、设备功能界面、手动操作界面、操作说明、故障报警界面等。
2 实际运用
采用自浮动磨削加工抛光机对某规格不锈钢坯料管进行抛光,抛光后的实物照片如图6所示。由图6可见,抛光加工后的产品管外表面光滑,可满足生产要求。
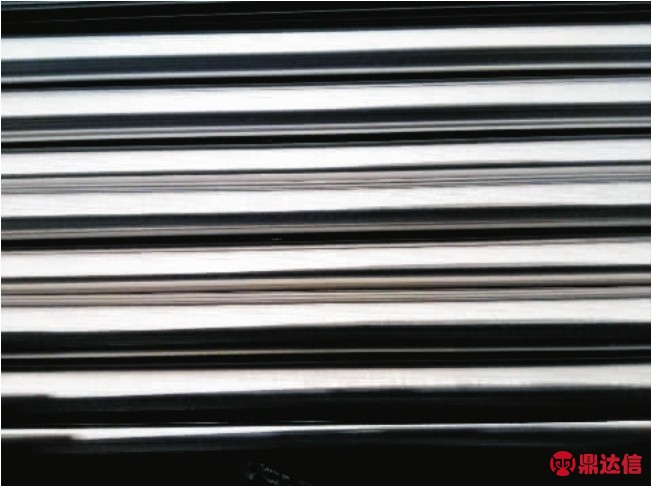
图6 抛光后的实物照片
3 结束语
对于坯料管通过金属断面成型机(轧机)或拉拔机冷加工的成品管,由于管坯外表面粗糙度达不到产品质量要求,特别是有高精密度要求的产品,需通过表面抛光来达到产品特性要求。本研究提供了一种实现上述目的的技术解决方案,为抛光磨头自动加工装置。
作为优选,高速抛光磨头组合体可由高强度主轴系统、皮带变速系统、高速轴承等组成,且电机皮带张紧可调(电机座可调);磨头加载系统可由气缸、气动比例阀控制。通过气动比例阀调节用气量,实现气缸压力的大小可调,从而实现磨削量的适当增减。同时,还可采用EHTV-G1/4液压管式双向节流阀和气液转换器,确保抛光磨头运行平稳;采用LT10-C150-24-RL1电动推杆带磁石自动调节抛光磨头的向下行程。