摘 要:悬浮颗粒的过滤方法很多种,所涉及到的过滤器也有很多,所对应的过滤机理也有很多,本文着重介绍的就是水力旋流器的过滤机理,对其生产能力的影响因素,各个部件的结构参数,评价其结构性能的重要指标等等,并通过这些来了解各个零部件的结构组成对水力旋流器的工艺影响,从而设计出满足工艺要求的水力旋流器。本文主要是通过对现在已经投入生产应用的水力旋流器进行改进,对其结构组成及其参数进行设计,其设备主要是在去除二氧化硅工艺中的应用。
关键词:水力旋流器;过滤机理;性能影响因素;结构参数的设计
1 水力旋流器结构设计的理论基础
本次设计主要采用的是第一钟方法,我们要求需要筛选的粒子直径不能大于10μm,所以我们通过对结构的组合设计出可能满足条件的旋流器,至于是否能满足相应的要求还需要通过实验进一步的验证。
2 旋流器的结构参数设计
2.1 旋流器直径
旋流器直径可以影响其生产效率等,一般来说,直径与相应的生产能力和分级粒度呈正相关,如图1 所示[2]。正常操作时,在确保其分散效果和工业生产要求的前提下,可以尽可能的选择直径比较大的旋流器,因为大直径的机器在实际操作使操作比较简单而且不容易发生旋流器的堵塞。
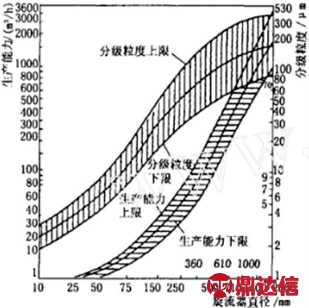
图1 旋流器的生产能力和分级粒度与直径的关系
通过以上的理论以及关系图1 可知,鉴于分级粒度的要求是10μm,所以选取直径75mm。
2.2 旋流器的开口尺寸
开口尺寸包括入口、溢流口和底流口。而这三这又有相应的关系相互制约着,进料管直径和溢流口直径影响着分割直径和压降,而底流口直径又影响着着流量比。
对进口处管口的直径的选取要求只有使流入的液体具有最大的动能一个要求,流入的液体在进口处的速率随Di 增加,动能也在加大,但是在动能达到最大之后又逐渐下降,如此一来存在最优的进料管直径。我们可知用于分离时取Di=(1/4~1/7)Dc,用于分级时取Di=(1/6~1/7) 。本设计取Di=0.25D0=0.25×75=18.75mm,取Di=18mm。
溢流管结构尺寸对于旋流器的设计来说也很重要。因为它影响了内部液体流动的结构,而且可以直接影响短路流的存在与否,以及液体流入体积的多少。本此设计创新性的将溢流管由通常采用的直管改为渐扩管。溢流液体的出口直径会大于入口直径,一般取D0 是Di 的1.25~1.50倍。本设计取D0=1.30Di=1.30×18=23.4mm,取D0=23mm。
2.3 溢流管插入深度及厚度
溢流管深入长度可以直接影响到短路流的情况,溢流管深入长度越小,旋流器分散程度就越大,但分离粒子的直径越小。深入长度H0 增加时,随壁面向下运动的小粒子被带走的可能性就会加大,降低了小粒子的分散效果,与之相反,却可以提高粗粒子的分散效果。一般溢流管插入深度H0=(0.3-1.0)Dc。本设计选取H0=0.50Dc=0.50×75=37.5mm,取H0=38mm。
溢流管壁厚度的增加,可以提高效率,并能降低能量消耗,而且还可以在一定程度下提高机器的产品水平。所以在设计分离用旋流器时可相应的增加溢流管的管壁的厚度。本设计选取溢流管壁厚为4mm。
2.4 旋流器的锥角
旋流器的锥角可以影响到分离粒子的直径大小,两者呈正相关,因此,悬浊液过滤时旋流器可以采用小于15°的较小的锥角。锥形区域的锥形角度的加大会引起能量损失增大,在其他条件都不变的情况下,生产能力的降低随之变化的就是分离粒度的加大。此次设计我们选用的是小锥角6°。
2.5 旋流器简体长度
经研究表明,柱体区域是离心沉降作用最明显的区域,所以一般情况下用于分离作用的设备的柱体长度的数值应尽可能的大,一般应在Hc=(0.2~1.5)Dc。本设计选取为Hc=1.2Dc=1.2×75mm=90.0mm。
3 结论
3.1 对砂环的影响
研究发现,螺旋器的导流板倾角为10°时,螺旋器对导流板的导流、整流才能发挥作用;将溢流管由渐扩管改为直圆管后,溢流管的出口液体静能转化为动压能,设备增大压力,能耗提高;螺旋导流板抑制液体湍动,消除了“砂环”影响,延长了液体在旋流内的完成分离流动时间,有利于细颗粒的分离。
3.2 分离性能
对影响旋流器分离性能的结构参数和操作参数进行分析,研究发现:在直筒段加入螺旋导流板的设计可以使流体按照既定方向运动,可以解决进口附近短路问题,可以制止固态离子运动。进口液体流量变大,分离器的总分离效率和粒级效率将会都变大;可是结构优化后当进口液体流量达到一定值后,分离效率就会降低,所以操作时有一个固定流量值。分离效率随着分流比与Ra 呈正相关,当Ra 大到一定值时,分离效率不再发生变化,这个值为1.0;当固体颗粒直径达到10μm 时,分级效率就不会增加那么快;当固体颗粒到20μm 时,分级效率可以到97%甚至以上。