摘 要:基于计算流体力学理论,采用控制变量法,利用流体模拟软件Fluent分别研究了分离器入口烟气流速与压力损失的关系、叶片仰角及分离器直径对分离器阻力系数的影响。发现分离器的压力损失与分离器入口烟气流速的平方成正比关系;分离器阻力系数与分离器开孔率呈二次函数关系;分离器阻力系数值与分离器直径无关,并最终得到了旋流式气液分离器压力损失计算模型。
关键词:烟囱雨 压力损失 气液分离器 数值模拟
0 引言
近年来,湿法脱硫工艺所带来的烟囱雨问题已经越来越受关注[1]。为了缓解烟囱雨问题,开始在烟囱上增设烟囱雨消除装置[2],例如:旋流式气液分离器(以下简称“分离器”),其被装设于湿法脱硫塔顶钢烟囱之内,原理是通过倾斜的叶片使高速通过它的气流发生旋转,从而使气流中夹带的大粒径烟囱雨液滴在离心力的作用下运动到烟囱内壁流下来,减少烟囱排放的烟囱雨液滴,缓解烟囱雨问题。分离器的压力损失是指分离器的进口和出口气流全压之差[3],其性能是代表分离器耗能大小的重要技术经济指标。为获得分离器的压力损失计算模型,运用Fluent 15.0数值模拟软件,对不同入口烟气流速、不同结构的分离器压力损失性能进行研究。
1 旋流式气液分离器介绍
1.1 基本结构
分离器由中心圆柱、叶片、外围筒壁组成(如图1)。外围筒壁为圆筒形,以中心圆柱为中心;叶片为平面板,略呈矩形,连接外围筒壁及中心圆柱,采用16块叶片环绕中心圆柱均匀阵列排布;中心圆柱及外围筒壁的高度根据实际应用时的叶片仰角进行调整,以刚好与叶片最上沿平齐为准。
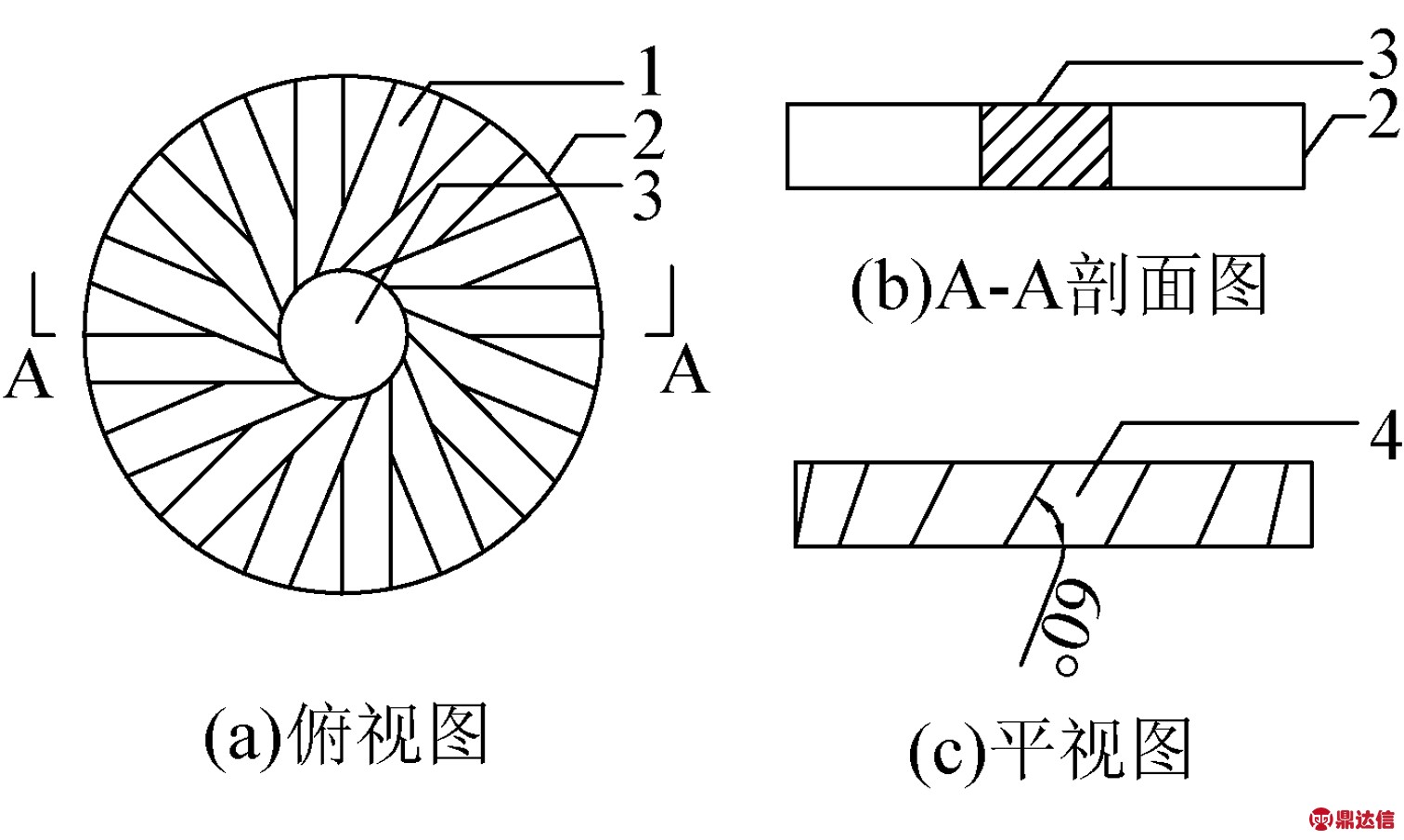
1—叶片;2—外围筒壁;3—中心圆柱;4—叶片仰角
图1 旋流式气液分离器结构示意图
1.2 主要参数及计算方法
叶片数取16片,限定:
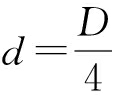
(1)
式中,d为中心圆柱直径,m;D为分离器直径,m。
外围筒壁及中心圆柱高h为:
h=esinα
(2)
式中,e为叶片宽,m,本文取e=0.65 m;α为分离器水平放置时叶片与水平面的夹角。
分离器的开孔率φ为:
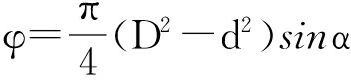
(3)
2 数值模拟实验
采用控制变量法,研究叶片仰角、分离器直径、入口烟气流速3个主要因素对分离器压力损失性能的影响。
2.1 简化与假设
建立模型时,将烟囱壁及叶片简化为不带厚度的面,忽略烟囱与分离器之间的缝隙,认为烟囱直径与分离器直径相等。为了便于求解,对烟囱内气相流场的流动气体假设为标准状态下的空气。
2.2 数学模型
采用Realizable k-ε湍流模型[4]。在近壁区内的流动,Re数较低,湍流发展并不充分,本文采用壁面函数法对近壁处的流动进行处理。
2.3 数值模拟实验流程
运用Fluent数值模拟软件进行数值模拟实验,流程依次为:建立几何模型、进行网格划分、选择湍流模型、设定边界条件、选择离散方法、设定收敛残差、迭代步数及初始化、数值计算及后处理[5-7]。
3 分离器的压力损失性能
3.1 分离器入口烟气流速的变化对分离器压力损失性能的影响
采用控制变量法,对结构一定的分离器(即直径为3.5 m且叶片仰角为60°)在不同的入口烟气流速(即10,11,12,13,14及15 m/s)下的内部流场进行数值模拟实验,得到相应条件下的分离器内部及烟囱内部的气流流场和进出口压力损失值。模拟实验结果见表1。
表1 模拟实验结果
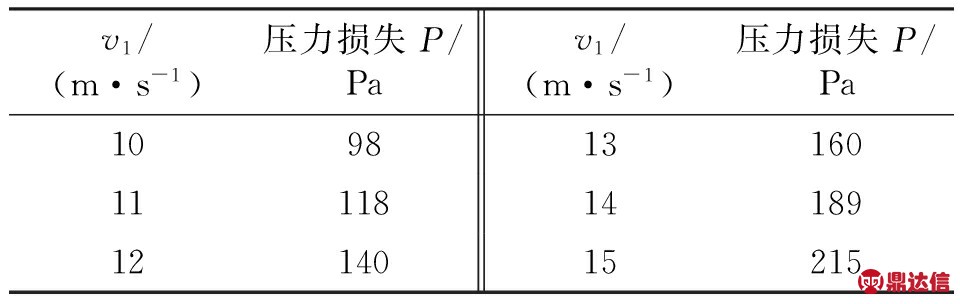
根据表1可得可以看出随着入口烟气流速平方的增大,分离器的压力损失也在不断增大,且曲线拟合程度高,R2达到了0.998 2,表明入口烟气流速的平方与分离器的压力损失呈过(0,0)点的线性关系。用数学公式可以表示为:
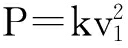
(4)
式中,k为分离器阻力系数。
3.2 分离器叶片仰角的变化对分离器阻力系数的影响
采用控制变量法,建立直径为3.5 m且不同叶片仰角(即分别为50°,60°,70°,80°)的分离器模型,并在不同的入口烟气流速(即10,11,12,13,14及15 m/s时)下的内部流场进行数值模拟,模拟实验结果见表2。
表2 模拟实验结果
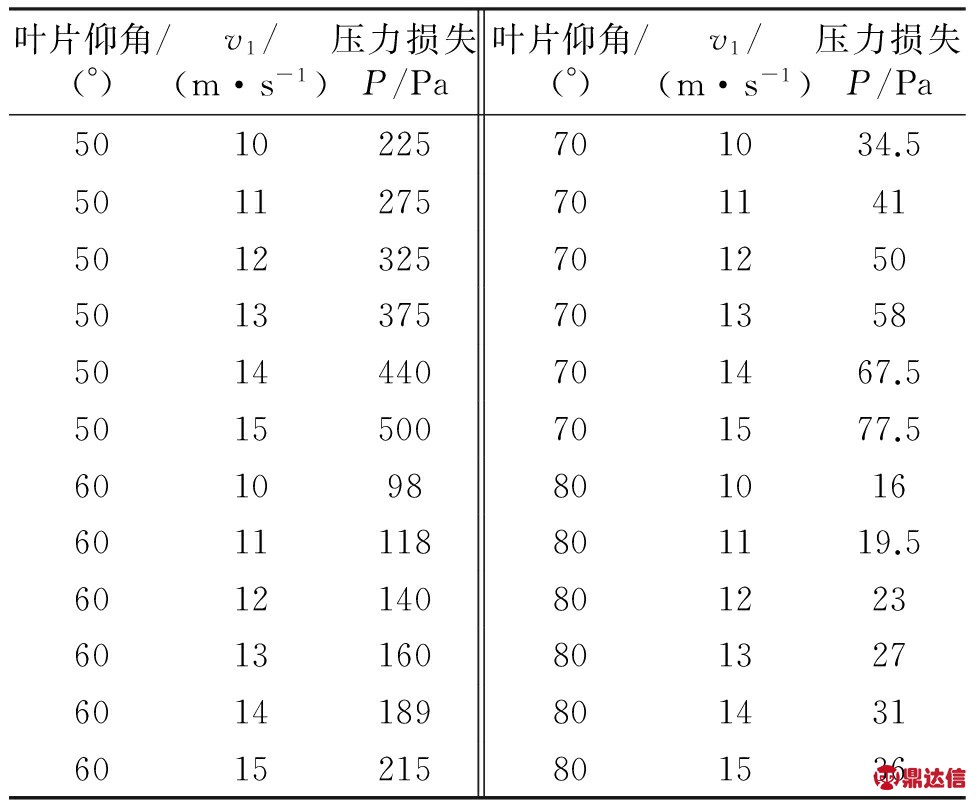
根据表2的实验结果,以入口烟气流速的平方为横坐标,压力损失为纵坐标分别作50°,60°,70°,80°叶片仰角的分离器入口烟气流速的平方压力损失P散点图并拟合曲线,得到不同仰角分离器的阻力系数值。不同叶片仰角的分离器入口烟气流速的平方与分离器压力损失关系曲线图见图2。
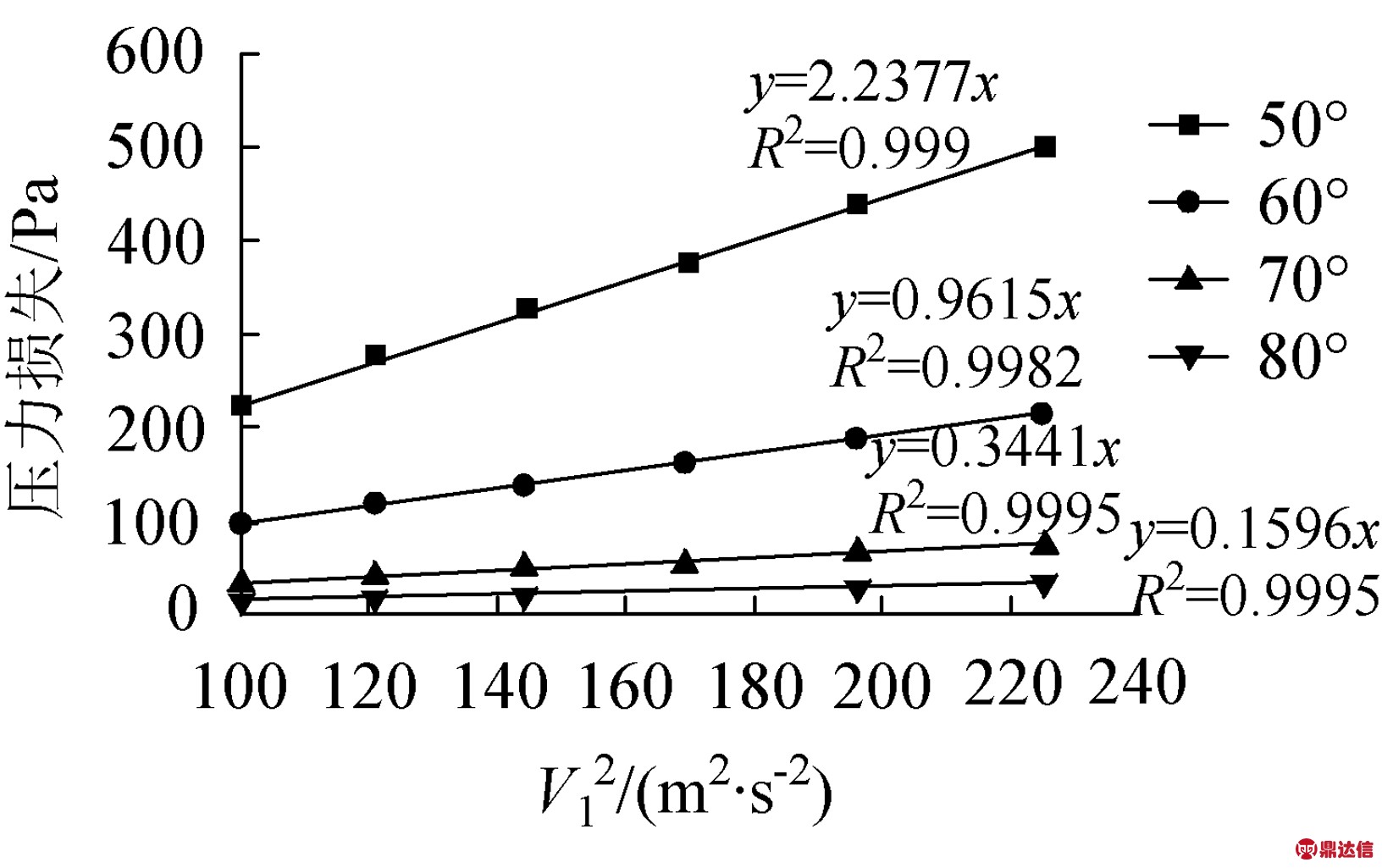
图2 不同叶片仰角的分离器入口烟气流速的平方与分离器压力损失关系曲线
图2中曲线拟合程度均较好,R2值均达0.998以上。可以看出,同一入口烟气流速下的分离器的叶片仰角越小,压力损失就越大,这是由于叶片仰角小,则使分离器的开孔率变小,增加了分离器对烟气的阻挡作用;随着入口烟气流速的增加,不同叶片仰角下的分离器的压力损失均变大,且呈线性关系,但就分离器压力损失的变大幅度而言,较小仰角的分离器的压力损失比较大仰角的分离器的压力损失变大的幅度要大。由式(4)可知,通过图2中曲线的斜率可以得出各个仰角下的分离器阻力系数值。
由于叶片仰角的改变实际上反映的是分离器开孔率大小的变化,因此为研究分离器阻力系数与分离器开孔率的关系,以开孔率为横坐标,分离器阻力系数为纵坐标作3.5 m直径分离器开孔率与分离器阻力系数关系曲线见图3。

图3 3.5 m直径分离器开孔率与阻力系数关系曲线
可以看出,由于开孔率增大,减小了分离器叶片对气流的阻挡作用,开孔率越大分离器阻力系数就越小;同时当开孔率变化时,就阻力系数的变化幅度而言,较低开孔率分离器的变化幅度要比较高开孔率分离器的变化幅度要大。由图3可得,直径3.5 m分离器的分离器阻力系数与开孔率的数学关系式为:
k=32.042φ2-62.783φ+30.801
(5)
令D=3.5,由式(1),(3),(4),(5),可得以叶片仰角及入口烟气流速表示的3.5 m直径分离器压力损失计算模型如下:

(6)
式中,α∈[50°,80°]。
综上,当结构一定时高速旋流式分离器的净压力损失与入口烟气流速平方成正比;当分离器开孔率变化时,开孔率的不同阻力系数变化幅度不同。
3.3 分离器直径的变化对分离器压力损失性能的影响
在不同的叶片仰角(分别取50°,60°,70°,75°)下建立不同直径(分别取3.5,4.5,5.5 m)的分离器模型,并在入口烟气流速为15 m/s下进行数值模拟实验,作出相应的入口烟气流速的平方-压力损失曲线,从而得到该直径下该叶片仰角下的阻力系数,再通过拟合各个直径下分离器的开孔率-阻力系数关系曲线,分析分离器直径变化对分离器阻力系数的影响,模拟实验结果见表3。
表3 模拟实验结果及阻力系数表
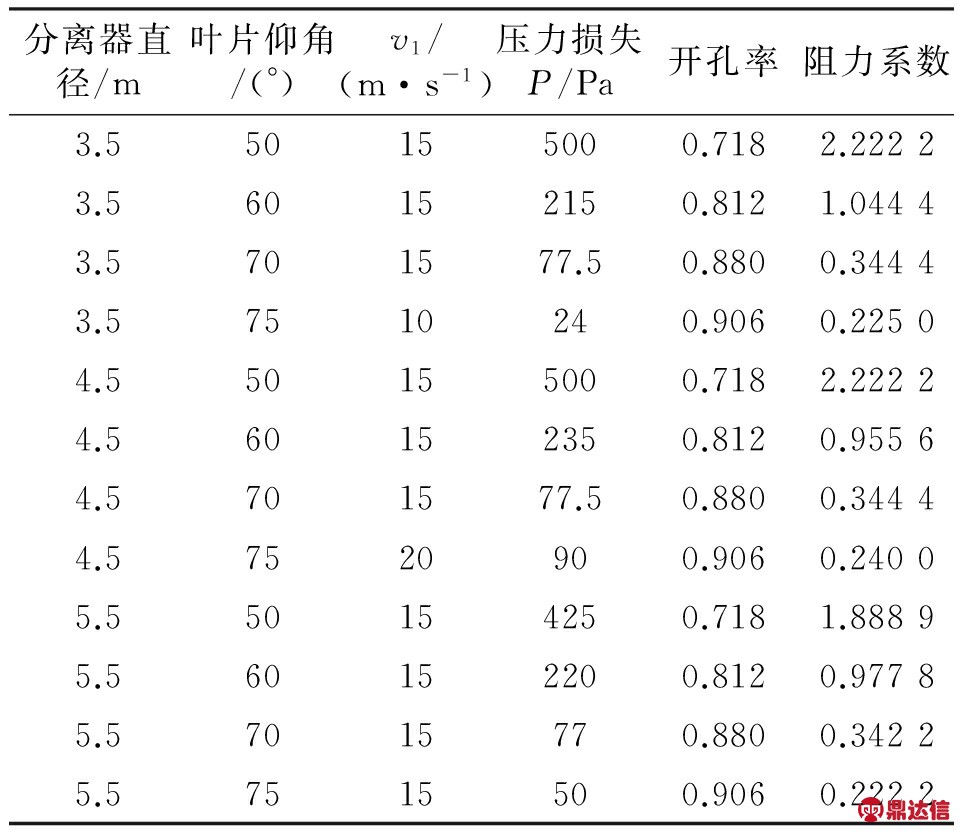
根据表3的模拟实验结果可作不同直径的分离器开孔率与分离器阻力系数关系曲线见图4。
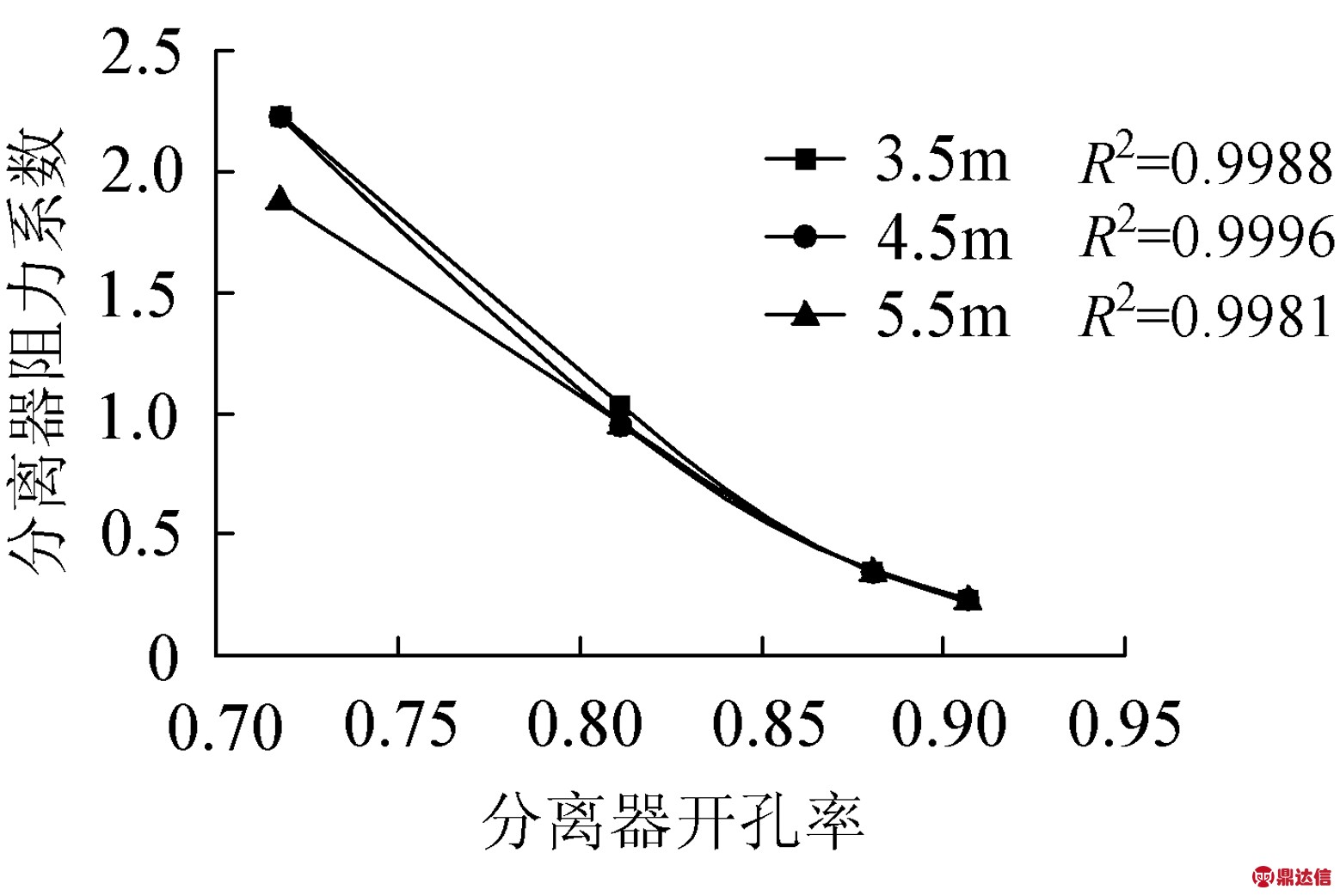
图4 不同直径的分离器开孔率与分离器阻力系数关系曲线
图4中曲线拟合程度均较好,R2均达0.998以上。不同直径分离器的开孔率-阻力系数关系曲线几乎重合在一起,也就是说,同一叶片仰角下不同分离器直径下的开孔率-分离器阻力系数曲线是同一条一元二次函数曲线。因而分离器阻力系数k与分离器直径大小无关,分离器直径的变化不会影响分离器压力损失值。这一特性与旋风除尘器的特性一样,即当除尘器结构类型相同时,几何相似地放大或缩小,压力损失基本不变[8]。因此,3.5 m直径下的压力损失计算模型对于不同直径的分离器均适用。
4 结语
本文分析了烟囱雨防治应用中的旋流式气液分离器的主要性能与其本身结构及工艺工况的关系,确定了主要影响因素;采用控制变量法,利用流体模拟软件研究了分离器入口烟气流速与压力损失的关系、叶片仰角对分离器阻力系数的影响、分离器直径对分离器阻力系数的影响。发现分离器的压力损失与入口烟气流速的平方成正比关系;分离器阻力系数与分离器开孔率呈二次函数关系;分离器直径的变化对分离器阻力系数的值没有影响。本文得到的分离器压力损失计算模型在一定程度上能为分离器应用于烟囱雨治理时的设计提供合理参考。