摘 要:采用计算流体力学方法,通过不同壁面粗糙度布置,对直升机粒子分离器无叶片三维流道进行详细的模拟分析。结果表明:壁面粗糙的变化对分离效率影响较小,但会导致流道总压损失的增大。靠近流道出口壁面对流道损失的影响要比靠近进口处大,其中对主流道总压损失影响最严重的是主流道的外壁面。不同的粗糙度分布,对流场的影响也不一样;而且壁面的粗糙度对近壁面流场有影响,还会通过累积影响到远离壁面的流场。
关键词:粒子分离器 表面粗糙度 流动损失 数值模拟
直升机一般在低空作业,近地面的空气环境是比较复杂的,在恶劣的环境下运转,常常会导致分离器壁面受损,主要有昆虫、灰尘、沙粒影响导致壁面不光滑,使粗糙度变大[1,2]。实际过程中,加工精度不够也会影响分离器壁面粗糙度。
目前各国对粒子分离器已有较深入的研究。国外学者从20世纪70年代就开始了分离器的研究,Ghenaiet[3]通过数值模拟,分析了不同流量、扫气比和粒径对分离器性能的影响;还着重分析了唇口几何形状位置的影响。Jiang[4]则通过模拟,分析粒子的大小、形状以及碰撞性能等对分离器运行的影响。Barone[5—8]通过实验详细的分析了进气流量、扫气比以及粒径对流道的影响,并通过改变型线来优化粒子分离器的性能变化。国内也做了关于分离器流道优化,上海交大的高彬彬[9]将流道分为7个部分,通过自己开发的程序,对分离器的优化做了比较详细的研究,得到了两个比较理想的模型。而国内最早研究分离器的侯凌云[10,11],主要侧重于网格的划分方法上。吴恒刚[12]、董晓婷[13]分别对无叶片和有叶片的粒子分离器进行了流场模拟。叶静[14]讨论了流道内壁、流道外壁、流道进口与流路面积和分流器位置对粒子分离器性能带来的影响,并提出了一种基于两相流的流道设计理论。
关于粒子分离器表面粗糙度的研究,从公开发表的文献来看,涉及较少。但是关于流体机械表面粗糙度的研究,已有不少可供参考的资料。Khalfallah[15]、Corten和Veldkamp[16]分别针对沙尘、昆虫对大风机性能的影响做了研究。在大量的研究基础上Sagol[17]总结出三种改善粗糙度影响的方法:①提高加工精度;②在壁面添加涂层或镀层;③及时检查和维护。关于粗糙度的研究表明,流体机械表面粗糙度对其性能有不可忽视的影响。近些年来直升机发展很快,直升机将会得到迅速的普及,在能源紧张的今天,保证直升机有一个良好的工作状态,对减少能耗十分重要。所以对直升机粒子分离器粗糙度的研究就有重要的意义。
基于此,本文将采用计算力体力学(CFD)的方法,对某型直升机粒子分离器三维流场进行模拟计算,探索粗糙度对粒子分离器性能的影响。
1 数值计算
近年来,随着计算机技术的发展,高速大容量的计算机不断更新,计算效率提高,计算机成本降低。而且随着计算流体力学研究的不断深入,计算的可靠性、准确性不断提高,计算力体力学在研究流体问题中得到广泛的应用。
1.1 粗糙度模型
无论有何种因素引起的粗糙度,都可以用大小、密度、分布来表征[18]。粗糙度的大小取决于单个粗糙元素的高度或者表面上多个元素高度的平均值,因此可以用高度来定义大小;密度就和粗糙在表面上的集中程度来确定;而分布就是粗糙部分出现的位置。
由于实际的粗糙度分布情况比较复杂,计算力体力学中难以准确模拟,所以就有了等效粗糙度的概念[18,19],将表面凹凸不平的粗糙部分,看成是相同直径的球状颗粒物紧密地排列在物体表面,如图1所示。
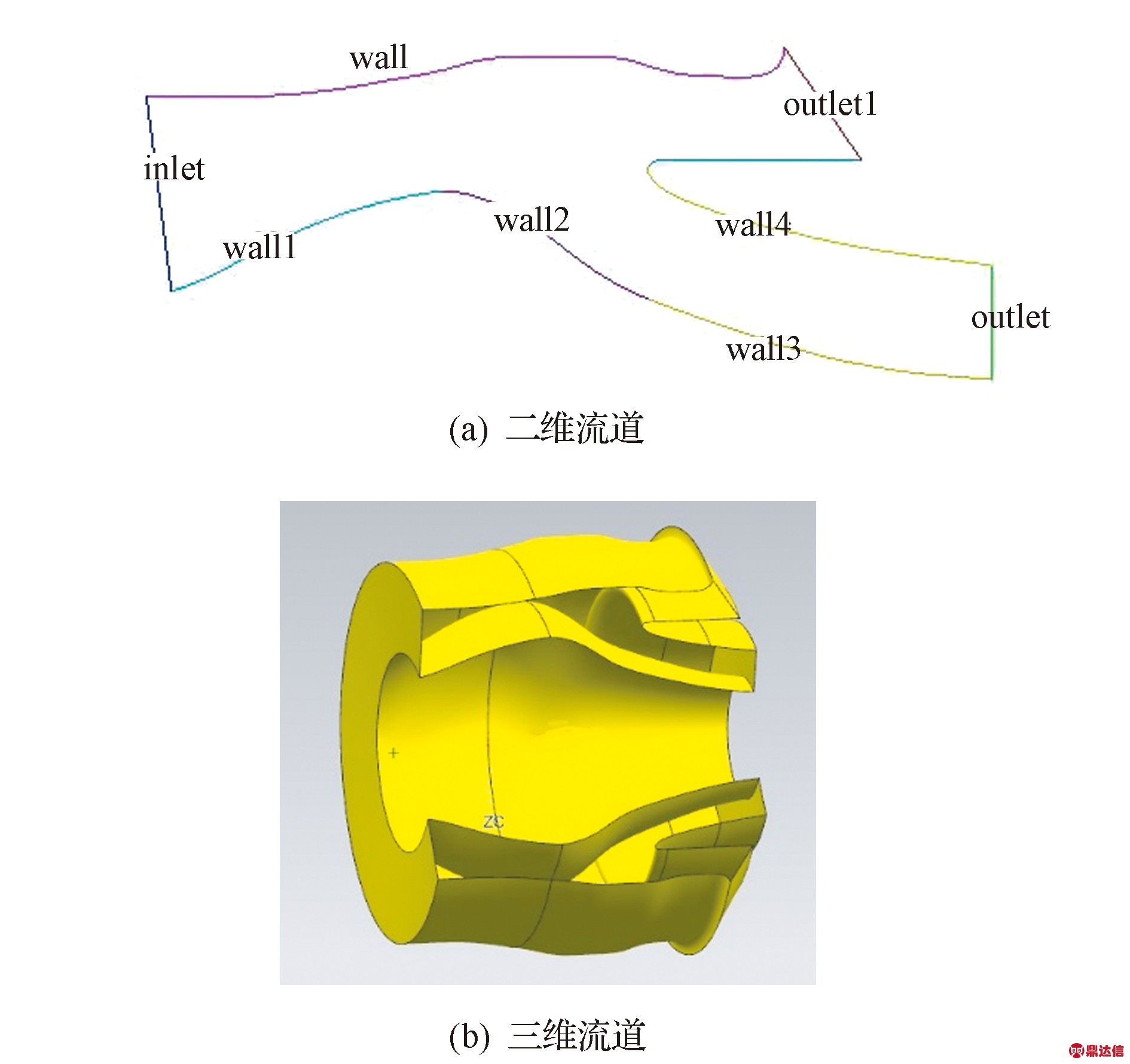
图1 等效壁面粗糙度示意
Fig.1 Diagram of equivalent wall roughness
应用上一般用无量纲粗糙度来表征粗糙度,定义为
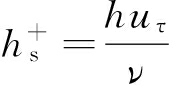
(1)
式(1)中为无量纲粗糙度,h为粗糙高度,m;uτ为壁面流体速度,m/s;υ是流体运动黏度,m2/s。Schlichtion[20]等通过研究发现,不同的对壁面的影响不同,可以分为3个层次:水力光滑壁面
过度粗糙壁面
完全粗糙壁面
由于模型采用了壁面函数,所以紧贴壁面处的网格就会影响计算的准确度。如图2所示,H为近壁面第一层网格高度,点p为第一层网格中心点,为粗糙高度。为使计算结果更准确,要求靠近壁面第一层网格高度要在壁面函数对数率的一定范围里面,即要取一个较小的值。但对于粗糙壁面,第一层网格高度应该高于粗糙高度。
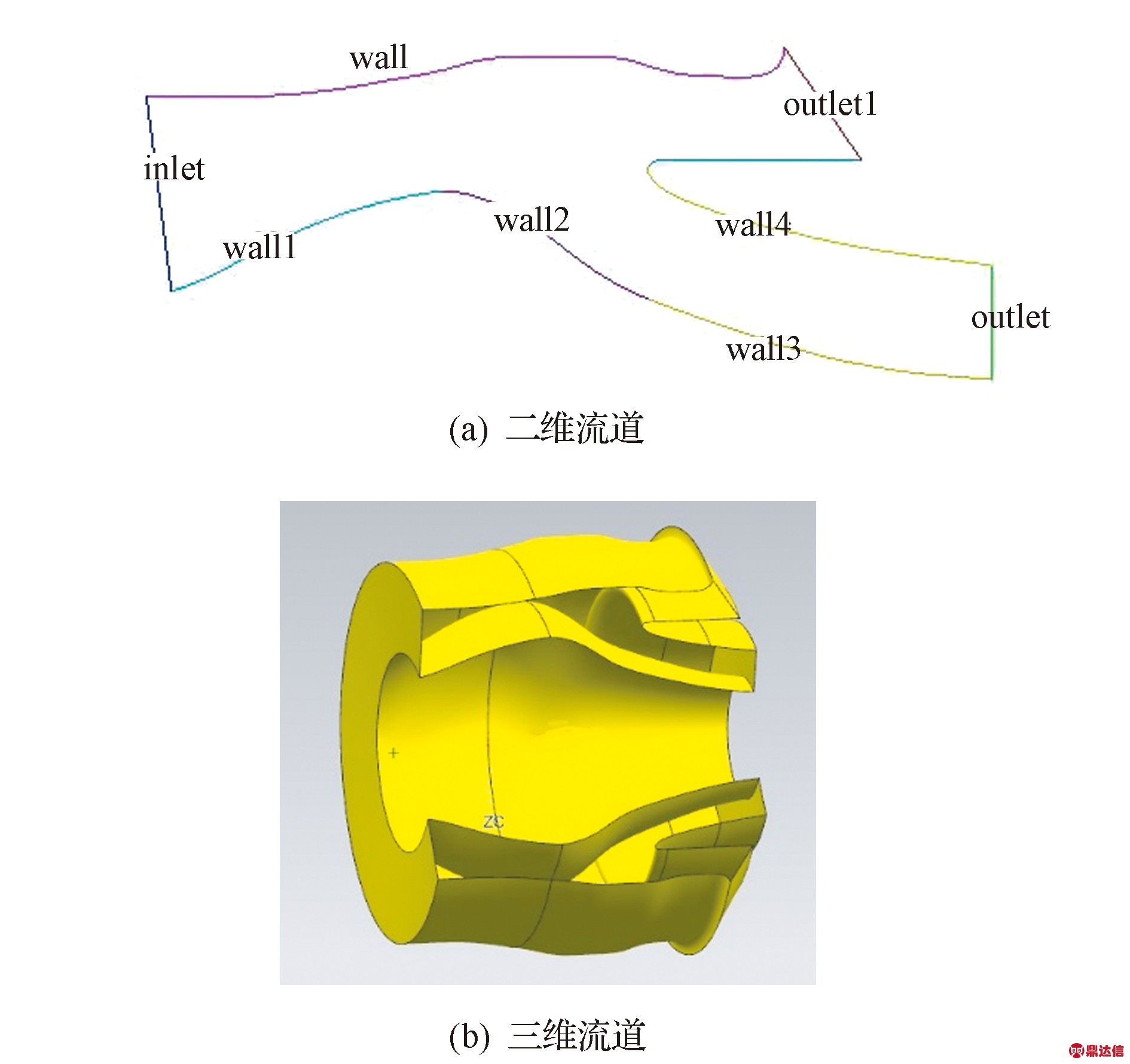
图2 近壁面网格高度和粗糙高度示意
Fig.2 Near wall roughness height and mesh height
在实际的计算中,很难同时满足这两个条件。但是杨胜华等[21]通过研究发现,不需要遵守第一层网格的中心高度要大于粗糙高度这一条件,所以在使用k-ε模型壁面函数时,优先考虑壁面y+值落入合理范围内,故本文优先考虑保证y+的合理性。
1.2 几何模型与计算条件
对粒子分离器流道进行三维模拟,图3为粒子分离器流道几何图,旋转轴是Z轴。图3(a)为二维的几何流道截面,有一个进口inlet,两个出口分别是主流出口(outlet)和清除流出口(outlet1)。为研究不同位置壁面粗糙度对分离器的影响,将流道壁面分成图3(a)所示5个部分,wall2的起点和终点分别是内壁面的最高点和唇口最前端等Z坐标处,图3(b)为三维的流道几何。
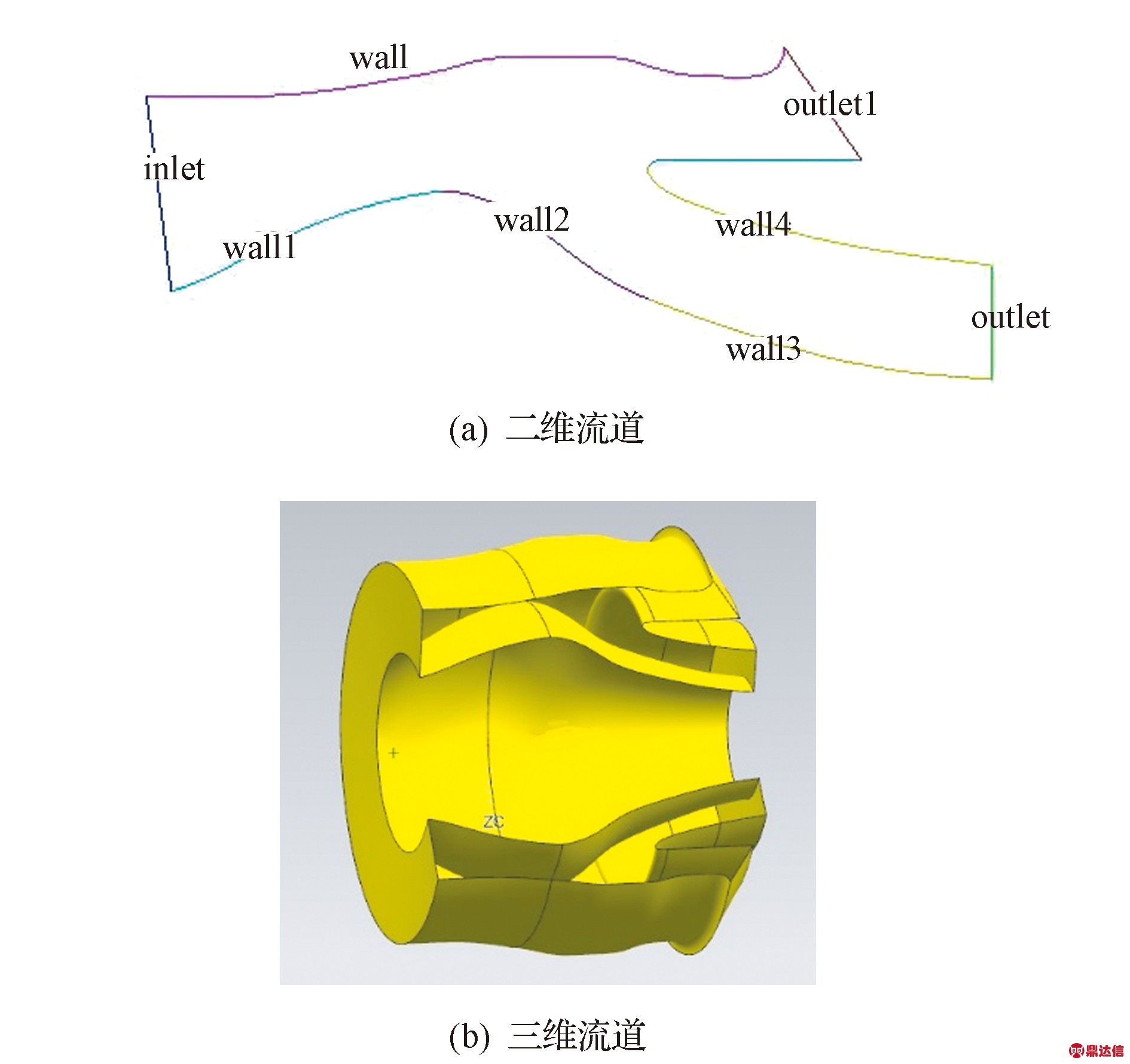
图3 粒子分离器流道几何
Fig.3 Particle separator flow path
本文所用的粒子分离器,采用ICEM划分结构网格。近壁面处网格加密,网格总量为3 930 489,壁面平均y+都小于10。
计算流体力学软件选用CFX,流体工质为空气,粒子给定粒径,进口(inlet)给的是总温总压,清除流道和主流道的出口(outlet)给定质量流量边界条件。其他部分壁面(wall)设置为无滑移壁面(no slip wall)边界,粗糙度根据具体情况来设置。
2 计算结果分析
2.1 壁面粗糙度对分离效率的影响
分离效率是粒子分离器最重要的性能指标,其定义如下:
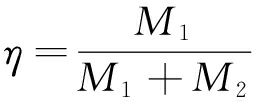
(2)
式(2)中,M1、M2分别为进入清除流道的粒子质量和进入主流道的粒子质量。分离效率的高低直接影响到发动机稳定性和飞机的飞行安全。
从流道结构来看,最有可能影响到分离效率的是内壁面的wall1和wall2两处壁面,这两个壁面处于粒子分离之前的流道内壁面,如图4所示。因此针对这两处壁面,模拟了不同粗糙度下粒子分离器的分离效率。计算结果如表1所示。
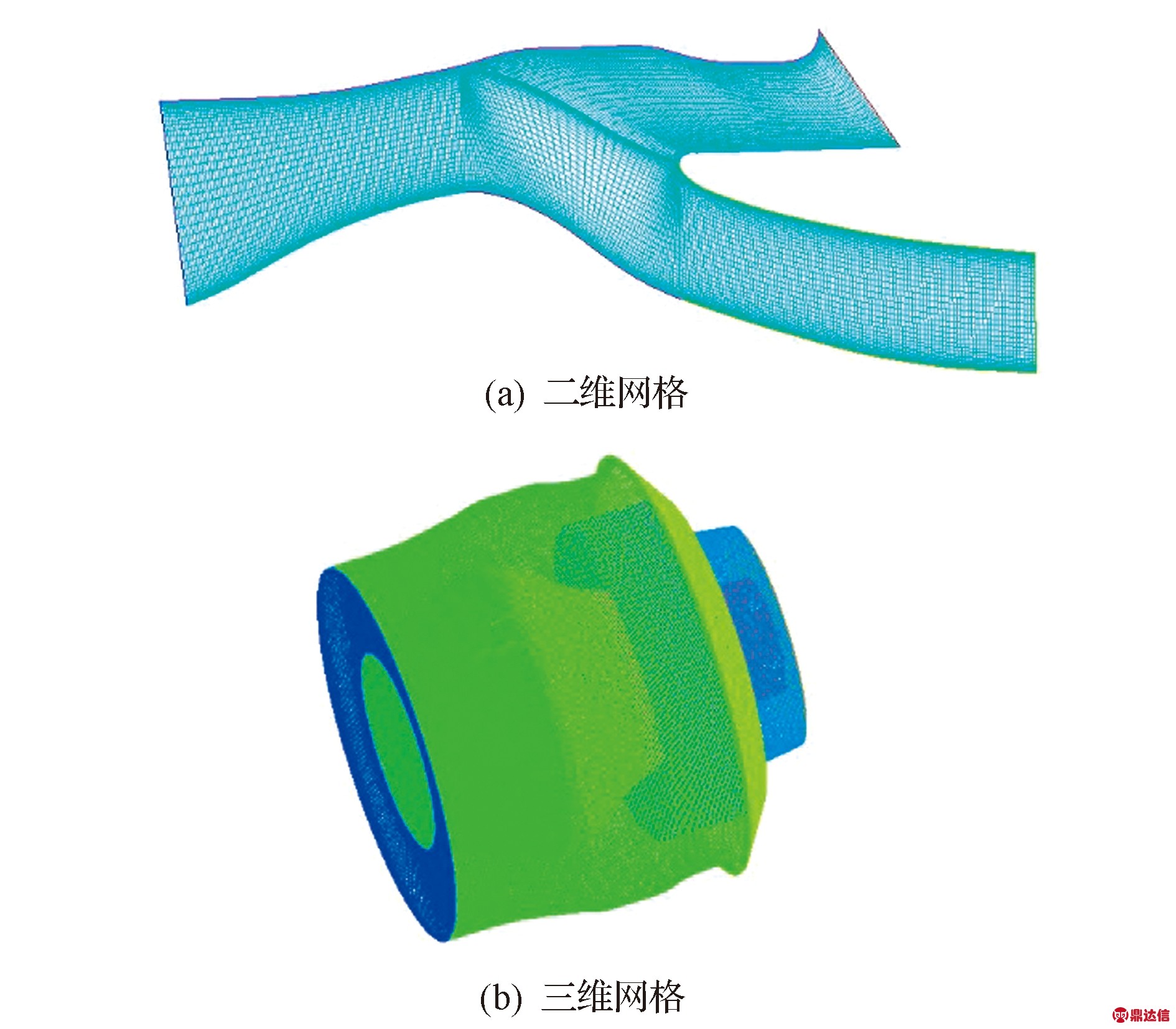
图4 流道网格划分示意
Fig.4 Flow path mesh
表1 壁面粗糙度对分离效率的影响
Table 1 Roughness effect on separation efficiency
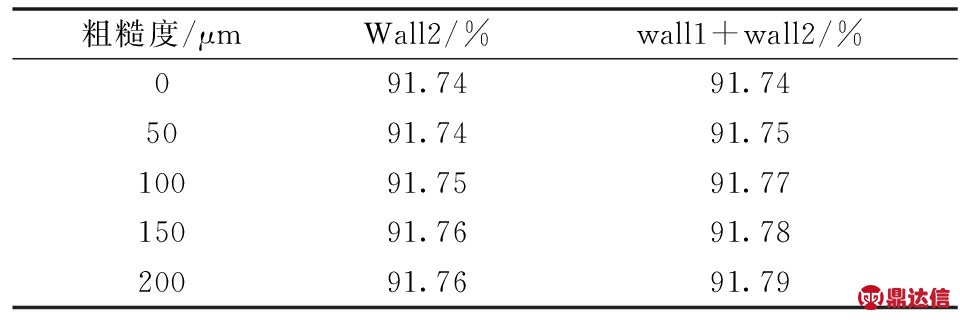
从计算结果来看,随着粗糙度的增大,分离效率略微增大。在同样粗糙度情况下,两个壁面的分离效率比单个壁面的分离效率稍大,但变化量较小,wall2壁面粗糙度从0增加到200 μm时,分离效率的相对变化量为0.025%,这种变化量在实际应用中可以忽略。因此可以认为,粗糙度对粒子分离效率无影响。
2.2 壁面粗糙度对流道气动性能影响
通过改变不同位置壁面的粗糙度,通过数值模拟得到结果,整理得到图5所示曲线,从不同壁面段粗糙度对分离器总压损失的影响曲线可以看出,对所有壁面,随着粗糙度的增加,总压损失都增大。
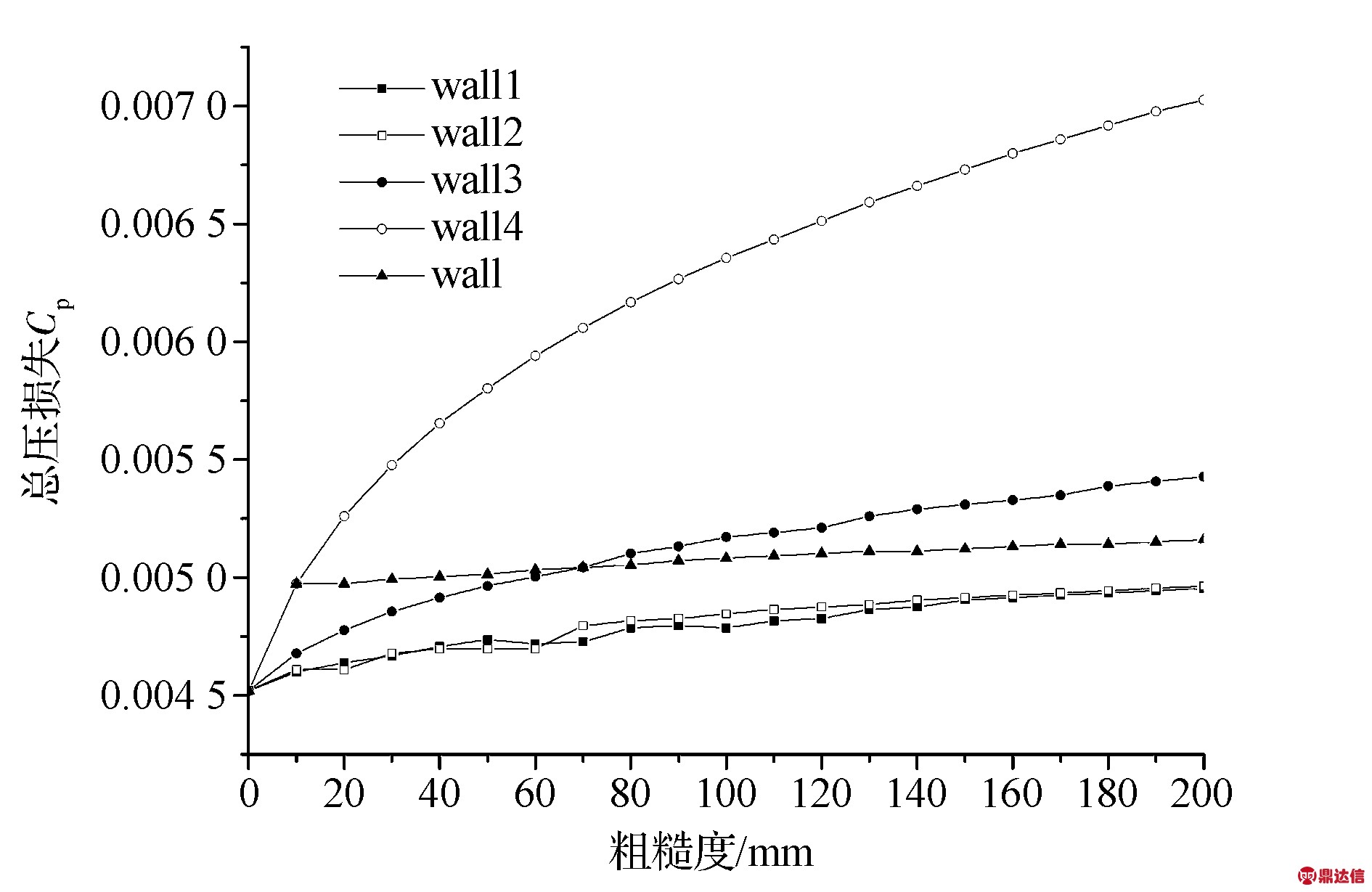
图5 粗糙度对总压损失影响
Fig.5 Effect of roughness on total pressure loss
五处不同壁面虽然都在增加,但增加的趋势和增大的幅度不尽相同。外壁面(wall)由于在整个流道中都处于外侧,因此对处于后部内侧的主流通道流动影响不大,特别是流体在唇口处分离后,外壁面不参与主流道的流场,因此虽然外壁面粗糙度增加会引起主流总压损失的增加,但是比流道其他壁面的影响要小,曲线变化很平缓。
流道内壁面前段wall1和wall2虽然是内壁面,但是由于都是在分流之前,所以变化不明显。而且就单个区域来说,wall1比wall2更远离唇口处,所以wall2的影响比wall1就更明显。但由于wall1和wall2的面积都比外壁面(wall)要小,所以在同样的粗糙高度下,外壁面的总压损失更大。
处于内壁面主流道上的wall3影响就很明显,无论是在变化趋势或是在总压损失的大小上,比外壁面及wall1、wall2都要明显。当粗糙度为0~100 μm时,wall1和wall2的总压损失变化量只有5.9%和7.6%,而wall3的变化量达到14.4%。而且在粗糙度为80 μm处,总压损失大小已经超过外壁面,之后的变化一直比外壁面更明显。
对总压损失影响最大,变化最明显的是主流道的外壁面wall4,从图5中看来不论是从变化速度或者变化量上,wall4都远超过其他几处壁面。粗糙度在0~100 μm变化时,总压损失的相对变化量达到40%之高,该壁面对流道损失的影响十分严重。
为了进一步研究各处壁面对流道的影响,在粒子分离器中截取YZ平面,然后取主流道出口的截线如图6(a)所示,进而研究这条线上的压力变化。截线位置以及压力变化曲线如图6(b)所示。横坐标为y坐标值,纵坐标是除以进口总压后的无量纲压力值。
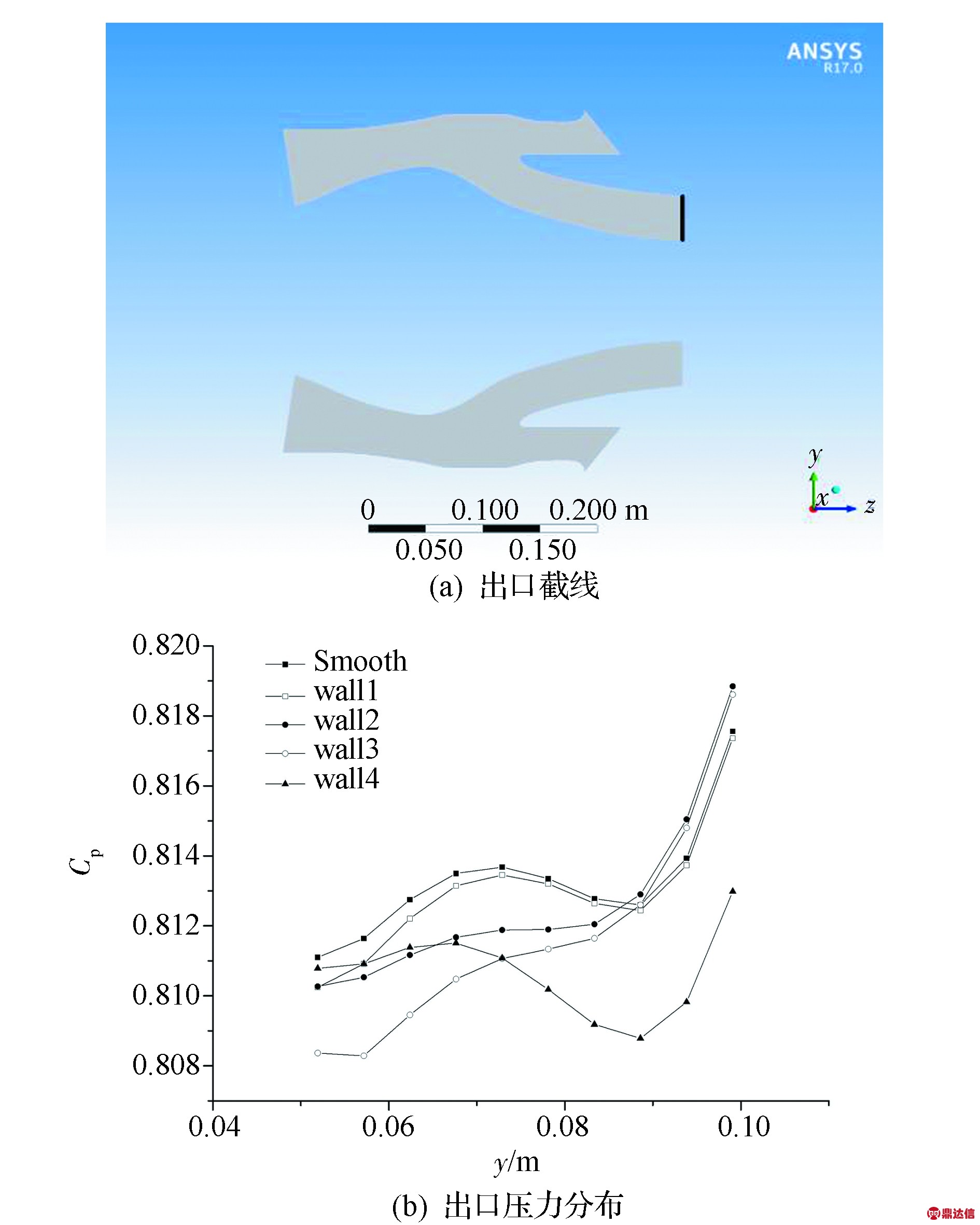
图6 主流出口压力分布
Fig.6 Mainstream outlet pressure distribution
图6中所选的是各壁面粗糙度为100 μm时的计算结果。图6(b)能进一步说明外壁(wall)和wall1、wall2对主流道的影响不是很明显,wall1基本和光滑壁面的压力分布一致,wall和wall2虽然有些偏差,但是在分布趋势上也跟光滑壁面工况很接近。但是wall3和wall4的变化就很大,wall3是内壁面,所以在y坐标值较小的地方和光滑壁面的压力分布相差较大,而处于主流道外壁面的wall4则是y坐标值较大的地方和光滑壁面压力相差大。
为了更直观的了解粗糙度的影响,将wall4壁面粗糙度为200 μm和光滑壁面的湍动能云图截取出来,如图7所示。
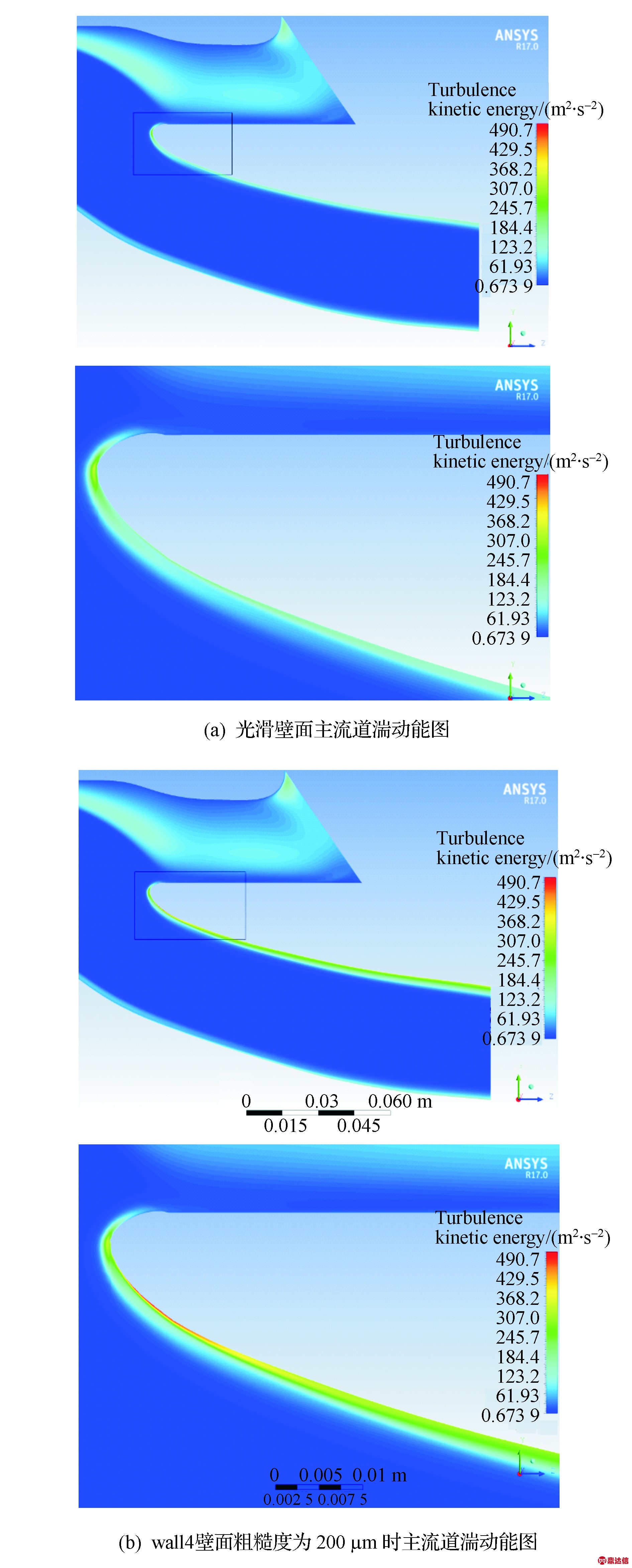
图7 主流道湍动能示意图
Fig.7 Mainstream turbulent kinetic energy
从图7(a)两幅图中可以看出,除了wall4附近的湍动能分布不一样,其他区域分布基本一致,在wall4表面附近的高湍动能区,有粗糙度的情况不仅湍动能值较高,而且从整个流道来看,高湍动能的区域也有较大差异,直观的表现粗糙度对流动损失的影响。图7(b)为图7(a)唇口处的放大,从唇口最前端开始,近壁面处的湍动能分布就开始有了差异。Wall4表面设置粗糙度后,湍动能比较高,而且高湍动能的区域也随着流动的进行逐渐扩大。而且在加了粗糙度后,紧接着唇口不远处有一段壁面附近出现了红色的高湍动能区,所以造成流动的损失较大。
2.3 粗糙分布对流道性能影响
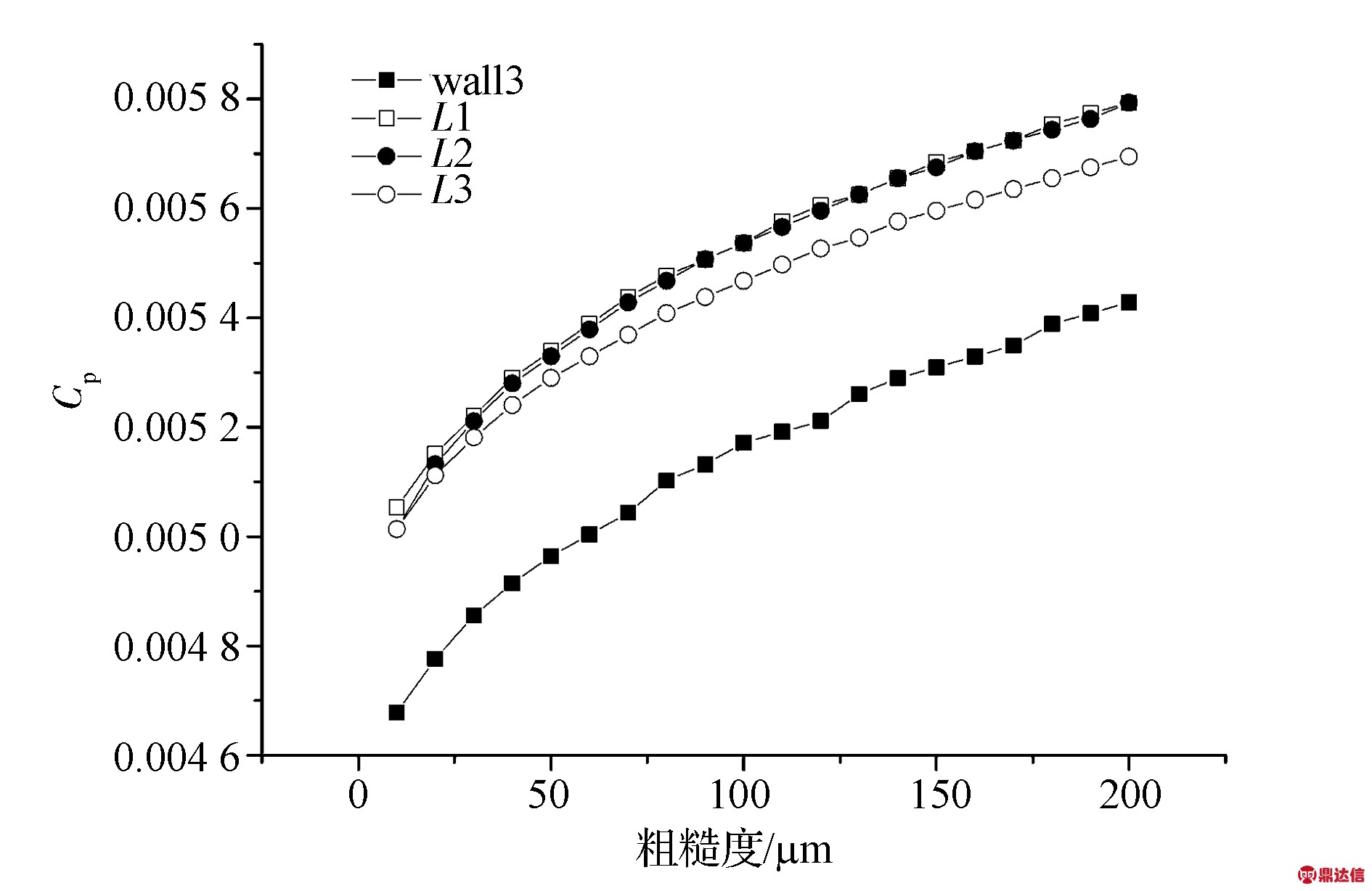
图8 粗糙度分布对流道影响
Fig.8 Roughness distribution effect on flow
为研究粗糙度分布对流道的影响,本节选取内流道作为研究对象,内流道分成三段设置粗糙度,其他壁面设为光滑壁面。通过计算得到图8所示曲线,其中L1是将整个流道内壁面都设成同一粗糙度,L2和L3则是考虑到越靠近入口,壁面磨损越厉害,所以顺着流动方向依次减小粗糙度,L2后一段壁面比前一段减小5×10-6 m,而L3则是以中间为基准,前后分别为中间高度的1.5倍和0.5倍。图8中的wall3是上节的计算结果,这里用作另三条曲线的参考。
从图8中可以看出,不论内流道上粗糙度怎么分布,总压损失都比wall3大,因为其他三条是整个内壁面都有粗糙度,而wall3曲线仅wall3处有。观察L1、L2和L3三种分布情况,以均匀粗糙度的L1为参考, L2和L3的值都是比均匀粗糙度情况下要小,L2和L3的粗糙度分布比L1更接近实际情况,所以这样的结果是比较希望看到的。究其原因,一方面是由于对主流道影响较大的壁面wall3的粗糙度减小了,另一方面是由于三块壁面粗糙度不同,导致流体在流道中的流动出现了差异,流体运动的相互作用的不同,使得压力损失有变化。
下面通过流场的几个截面压力变化情况,来分析三个不同的粗糙度分布对流场的影响。取图9所示的三条截线,观察曲线上的压力分布。图9是YZ截面上,三根截线分别是三个壁面的节点处的等Z坐标线,取这三个位置的目的在于考察三处壁面不同粗糙度对流场的具体影响。
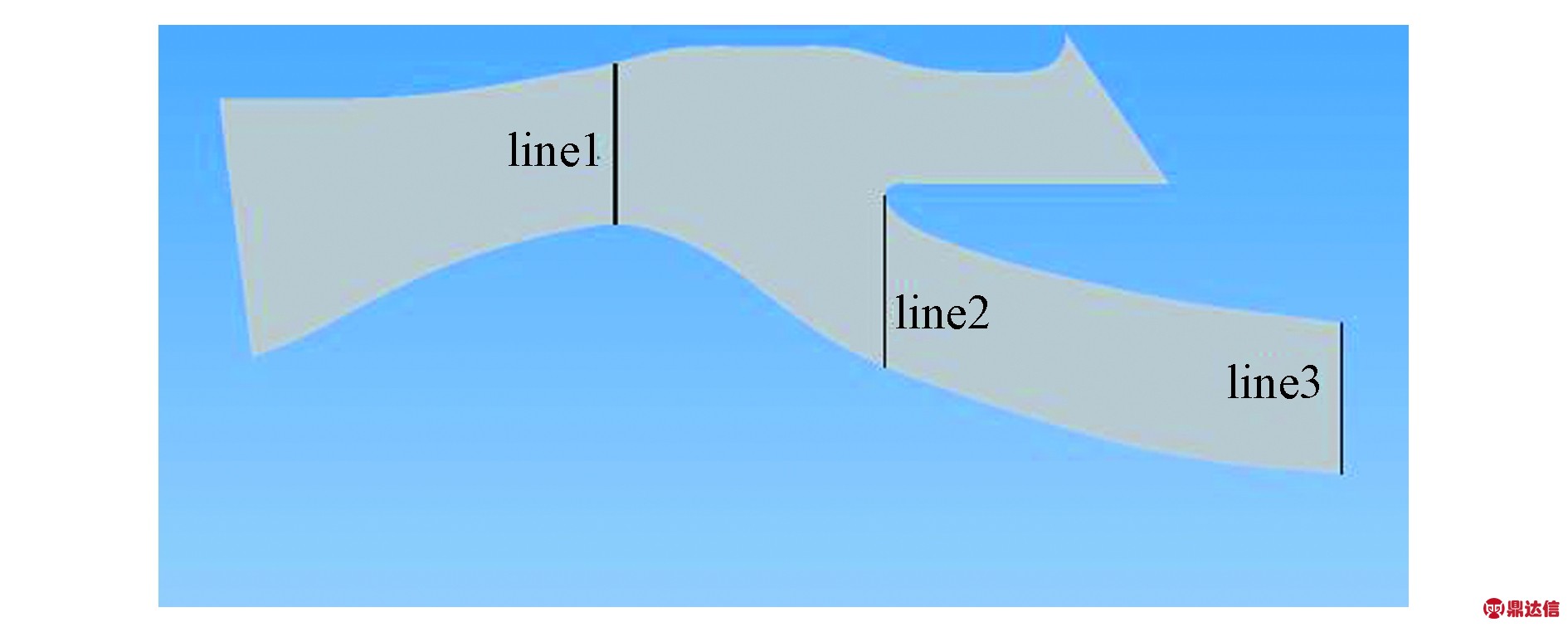
图9 流场截线示意图
Fig.9 Section line of flow field
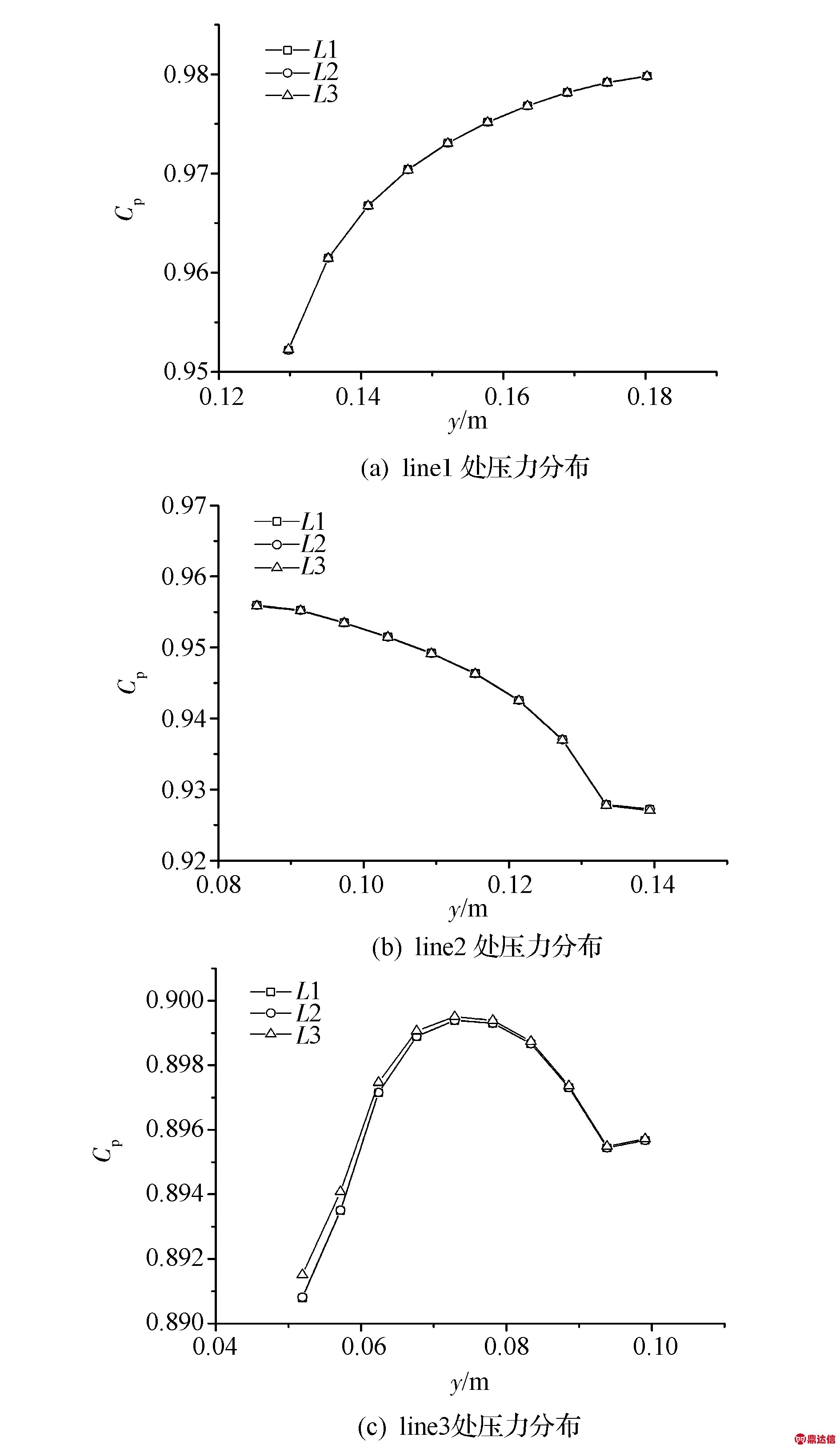
图10 截线L1、L2、L3压力分布
Fig.10 Pressure distribution on section line
三根截线上的压力分布如图10所示,在line1处三种不同的粗糙度分布情况下,压力的分布几乎一样[图10(a)],说明wall1处粗糙度的变化对流场影响十分微弱。line2处三条压力曲线也十分接近,但是在y值较大的地方,L3的压力比其他两处要小,也就是在接近唇口处压力分布有了差异,而整个wall2的粗糙度在三个工况下都是一致的,这就表明,wall1处的壁面影响在line1截面上没有立即体现出来,而是在流动过程中逐渐累积,引起了下游流场的变化。图10(c)中,L3和其他两条曲线的差异就比较明显,L3的值比其他两条线要大,在y坐标值较大处,三条曲线的值趋于一致,表明粗糙度的影响随着与壁面距离的增大而逐渐减弱。
观察后两幅图,虽然在前两段壁面上粗糙度使L3的压力降低得更多,但是流体经过wall3区后,L3的压力损失比L1和L2要小,这就说明wall段的影响效果比wall1和wall2两者的共同影响还要大。
3 结论
本文运用CFD方法,借助ANSYS CFX计算软件对某型粒子分离器的无叶片三维流道进行数值模拟,对壁面粗糙度这一影响分离器性能的因素进行研究,得到如下结论。
(1)粗糙度对粒子分离效率的影响很微弱,可以忽略不计。
(2)壁面粗糙度的增加,会导致流道上的压力损失。根据本文对流道壁面的分块来看,靠近流道入口的地方,壁面粗糙度对流道影响没有靠近出口处的影响大。完全处于主流道上的wall3和wall4,外壁面的wall4对流道影响更为明显,是整个流道上对流场影响最为严重的一块。
(3)从流道内壁面的粗糙度分布可以总结出,不同的分布方式对流道的影响各不相同,粗糙度不仅影响近壁面的流动,还会通过累积影响到远离壁面的远处流场,靠近主流道越近的壁面,粗糙度对流道损失的影响就越明显。