摘 要:为探明气液分离器布液板的性能,应用k-ε模型和Discrete Phase Model(DPM)模型,对分离器内流场进行了三维数值模拟。通过比较未安装布液板和安装孔直径为16~24 mm、孔隙率为25.6 ~31.8
布液板的气液分离器内部流场的速度分布与分离效率,得到布液板的整流特性。结果表明,布液板能梳理流场,降低流速不均匀度,抑制回流,使流场分布更均匀稳定,有利于液滴的沉降分离;布液板孔直径与孔隙率均不宜过大或过小,孔直径为20 mm、孔隙率为31.8
时布液板的整流效果较好。研究成果可为气液分离器的结构设计和布液板的选型提供一定的参考。
关键词:气液分离器;整流;布液板;数值模拟;优化
0 前言
在油气田地面集输工程中,从油气井中产出的一般都是油、气、水和砂等的混合物[1-2],为了得到合格的石油和天然气,油气集输首要任务是进行气液分离,所以气液分离器是石油天然气生产运输中一种必需的设备[3-4]。但一直以来,气液分离器的设计主要靠宏观的认识和简单的经验总结,对重力式气液分离器内部流场的微观机理研究还不够成熟,理论研究始终落后于实践[5-6];同时,由于气液分离器内部整流、聚结等元件周围的流动非常复杂,对这些元件影响分离的机理更是缺乏深入研究,造成对分离器内构件的认识停留在感性阶段,对内构件的具体作用没有从流场分析的角度去研究,造成气液分离器的设计效率较低[7-8]。
研究气液分离器及其内构件的传统手段主要靠实验对比,不仅易受实验条件限制,而且研究周期长,制作样机以及实验费用高,严重制约了研究的广度和深度。近年来,多相流理论和计算机技术的快速发展极大地推动了气液分离器的理论研究,相比实验研究,数值模拟技术可以节约大量成本,极大地缩短研究周期,并且可揭示不同内构件对流场各区域的具体影响,具有重要的工程应用价值。因此,国内外学者对重力式气液分离器流场进行了模拟研究[6-16],但多采用多相流模型,该模型适用于含液量较高的气液混合物,不适于天然气生产中使用的气液分离器。因此,笔者从这种需要出发,采用适用于稀疏离散相的Discrete Phase Model(DPM)模型[17-18],研究对比了安装不同型号布液板[19]的气液分离器内流场及其性能,优化了布液板结构参数,为气液分离器的结构设计和布液板的选型提供一定的参考。
1 数值模拟
1.1 几何模型及网络划分
为使研究更符合实际应用,采用实际工程中的气液分离器原型建模,主体直径为800 mm,长度4 m,封头为标准椭圆封头,气液分离器入口处设有轴流式旋流器,出口处为折板捕雾器。为改善气液分离器流场,减小紊流,气液分离器内发展了多种内构件,布液板即为其中一种。布液板可以对流场进行重新分布,使其更加均匀,抑制漩涡和返混的产生。由于气液分离器由液位控制机构将液面控制在容器高度的一半处,故气液混合物的流动区域(即计算区域)为容器的上半部分,见图1。
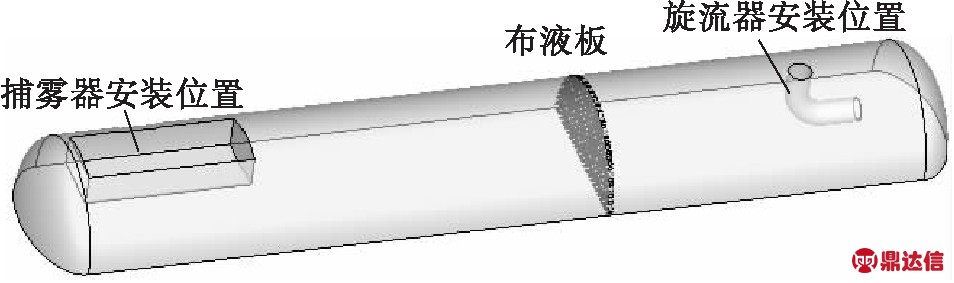
图1 计算区域示意图
布液板是一块与气液分离器等直径的圆形板,上面均匀打孔以便流体通过。对其稳流性能影响最大的参数是孔隙率(ηb)和孔直径(db,采用圆形孔)。孔隙率可由孔直径和孔间距(lb)决定。为了研究不同结构的布液板性能和影响,建立了不同结构参数的几何模型。布液板具体结构参数见表1。
表1 布液板结构参数
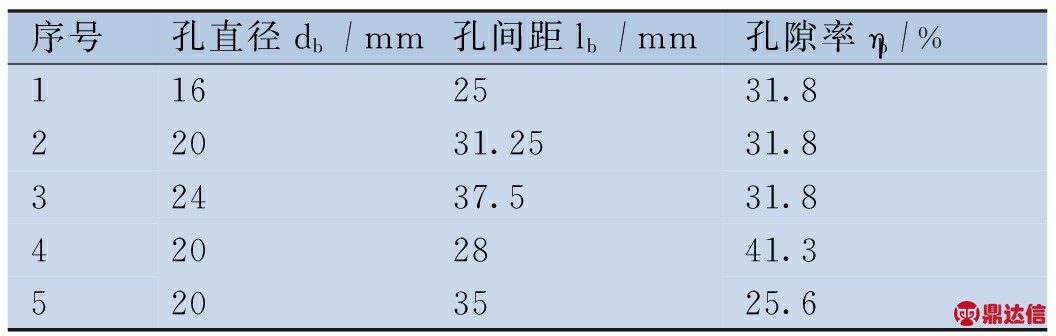
模拟的布液板分两组:一组为孔隙率相同(约31.8 )而孔直径不同,一组为孔直径相同(20 mm)而孔隙率不同。各布液板结构示意及对比见图2。
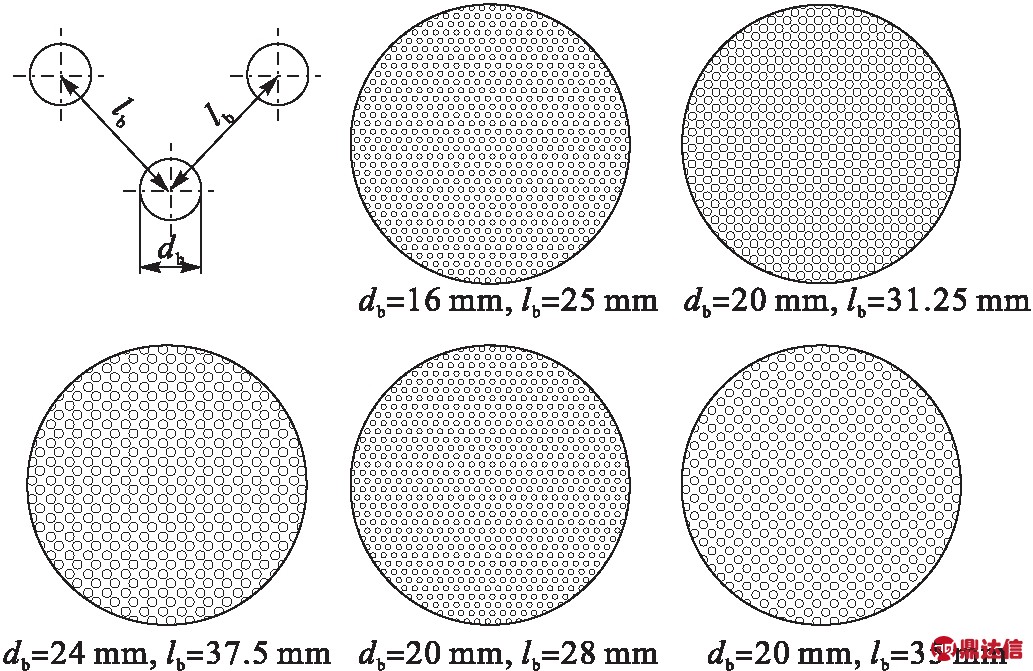
图2 布液板结构示意图
由于布液板结构较复杂,难以划分结构网格,故气液分离器的网格采用四面体非结构网格划分,在气液分离器进出口及布液板附近进行加密处理,网络单元数目在140×104左右,见图3。

图3 气液分离器网格示意图
1.2 边界条件及求解
为使结果具有对比性,采用真实参数进行模拟。该气液分离器设计压力8.5 MPa,日处理气量20×104 m3,日产液量5~100 m3。计算得出工况下天然气密度82.09 kg/m3,黏度1.32×10-5 Pa·s,由于压力变化不大,可忽略气体密度变化,采用不可压缩方法计算。入口设为速度入口,出口处为捕雾器入口,设为自由出流(outflow),气液界面处对气体而言为壁面。液滴相采用DPM模型进行处理,从入口面上均匀入射,撞击气液分离器壁面则被反弹,若达到气液交界面则认为被捕集(trap),达到出口则认为逃逸(escape)。
根据气液分离器流量计算出气流雷诺数Re=3 402,故流态仍为紊流。但是沉降段内紊流程度较轻,且不存在强旋流,采用工程上应用最广的k-ε模型可以得到满意结果[20]。采用有限体积剖分的SIMPLEC算法进行求解,差分格式选取为一阶迎风格式,压力插补格式采取标准格式。
2 模拟结果分析
2.1 孔直径的影响
为了研究相同的孔隙率情况下,不同孔直径的布液板对流场的影响,取布液板后方300 mm处(图3中b截面)的截面进行分析,其轴向速度分布见图4。
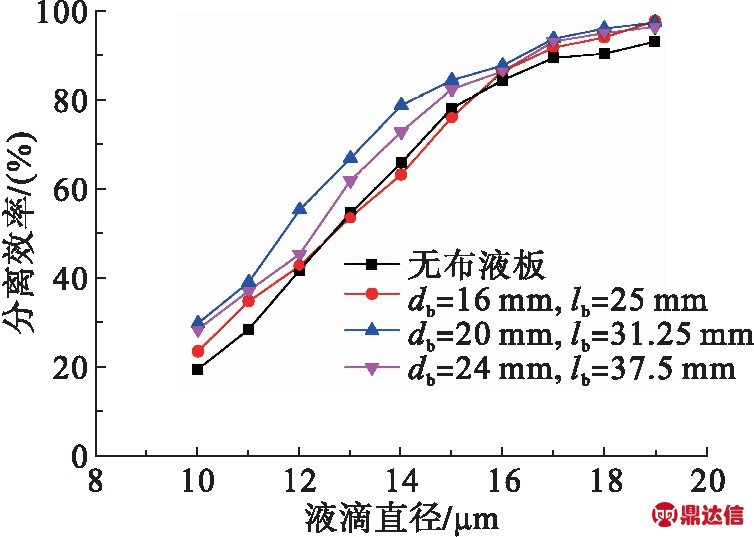
无布液板
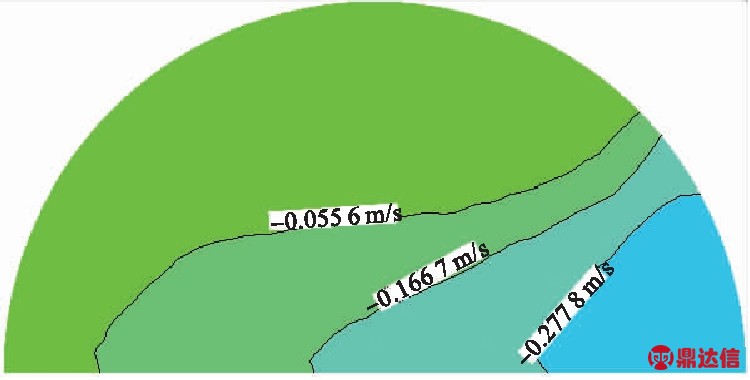
db=16 mm,ηb=31.8
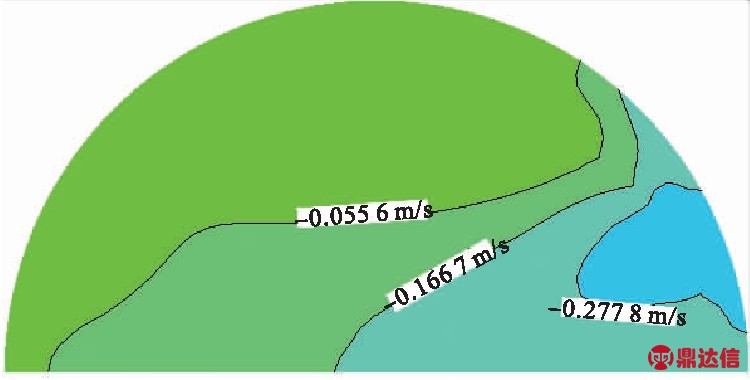
db=20 mm,ηb=31.8
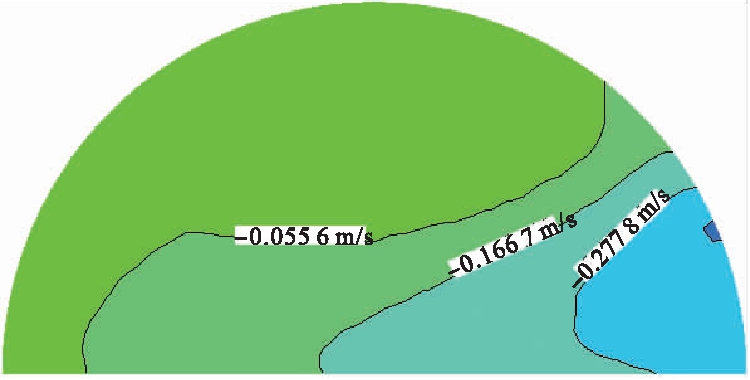
db=24 mm,ηb=31.8
图4 不同孔直径布液板b截面上速度分布
从图4可以看出,布液板对流场速度分布有明显改善作用。无布液板时等速线密集而且速度大小跨度范围更大,而安装布液板后等速线变得稀疏,说明速度梯度减小,变化更加缓慢,并且基本都消除了逆流现象,这种变化将有利于沉降分离。从横向上看,当孔隙率相同时,3种不同孔直径(16、20、24 mm)的布液板对流场梳理效果基本一致,差异较小。
为更准确地比较布液板对流场的梳理作用,现将截面上各点流速的标准差定义为速度不均匀度Su:
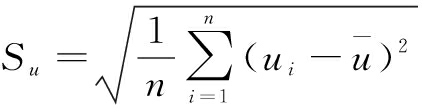
式中:ui为各点速度,m/为平均速度,m/s;Su为速度分布的均方差,即不均匀度。
Su越小,则速度分布越均匀,流场越稳定,越有利于分离。取图3 a、b、c、d截面的速度求取速度不均匀度,可得安装不同孔直径布液板后气液分离器内的速度不均匀度变化曲线,见图5。从图5可以看到,相比无布液板时的情况,布液板对速度分布有一定的梳理作用,3种孔直径布液板的速度不均匀度都小于无布液板时,特别是在布液板后面的b截面间速度不均匀度下降最为明显,c、d截面速度不均匀度也有所降低。但是,孔隙率相同的情况下,孔直径对流场影响不大,3条曲线非常接近,相对来说孔直径20 mm时速度不均匀度最低,流场梳理效果较好。
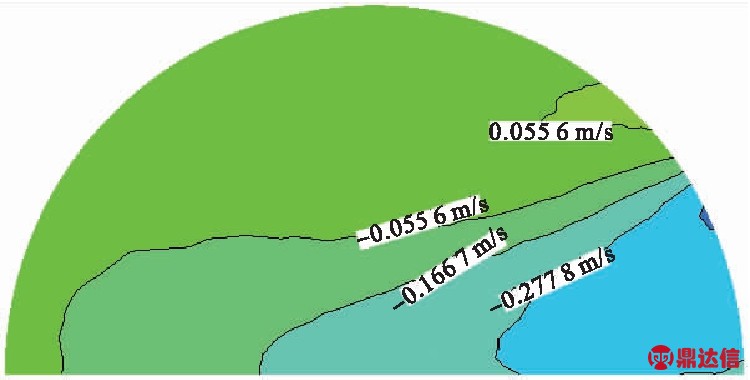
图5 不同孔直径布液板的速度不均匀度变化曲线
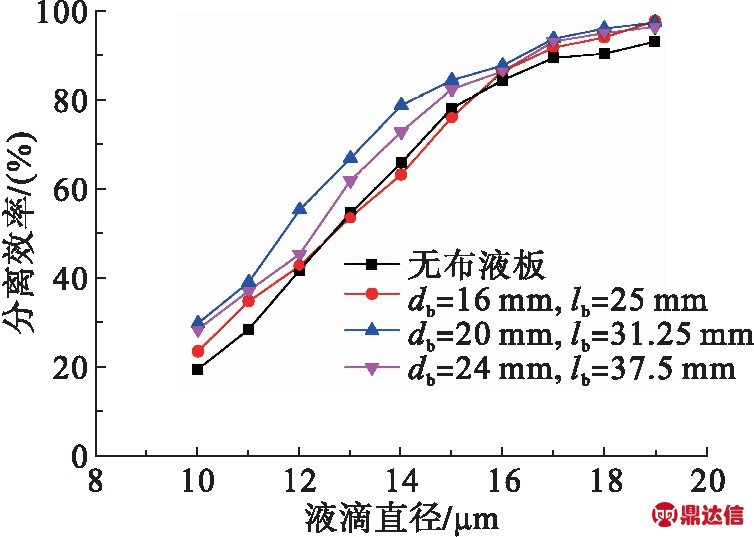
图6 不同孔直径布液板分离效率变化曲线
不同孔直径布液板分离效率见图6,由于对流场的梳理作用,布液板对分离器的分离效率有一定提升。但是3种孔直径布液板对效率的提升效果相差无几,特别是对15 μm以上的较大液滴,相对来说孔直径20 mm效率最高,故当布液板孔隙率相同时,孔直径20 mm时效果较好。
2.2 孔隙率的影响
同样的,建立包含孔直径相同而孔隙率不同布液板的气液分离器模型,求解流场后取布液板后方300 mm处(图3中b截面)的流场进行分析,其轴向速度见图7。
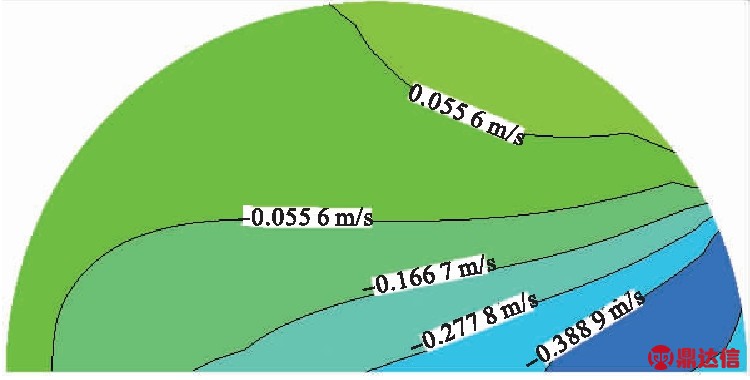
无布液板
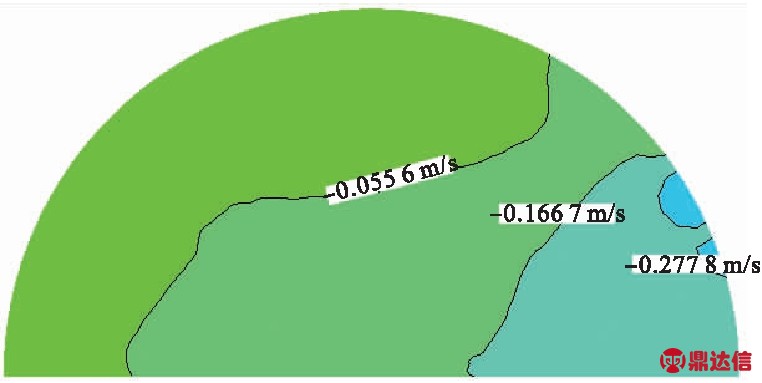
db=20 mm,ηb=41.3
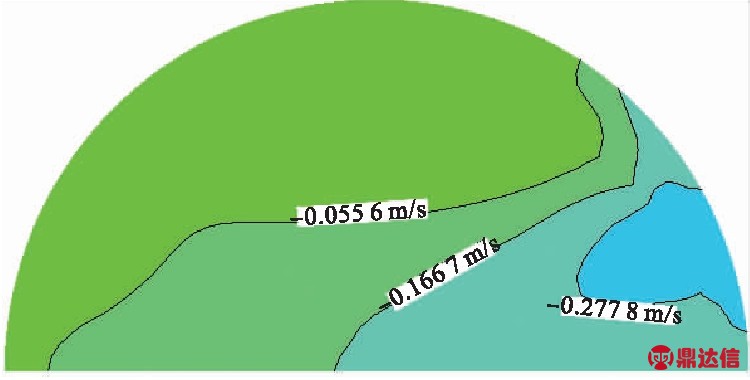
db=20 mm,ηb=31.8
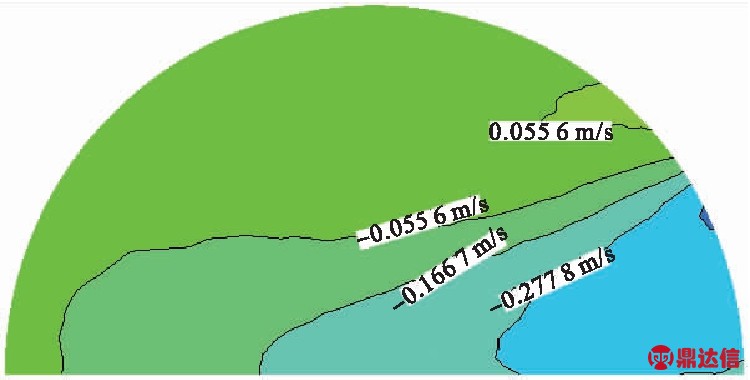
db=20 mm,ηb=25.6
图7 不同孔隙率布液板b截面上速度分布
从图7可以看到,不同孔隙率布液板对流场速度分布也有梳理作用,相对于无布液板时等速线变得更稀疏。但是可以发现,孔隙率过小对流场梳理不利,孔隙率为25.6 时等速线分布更为密集,说明其流场梳理作用明显不如孔隙率较大的布液板好。而孔隙率对速度分布的具体影响还需参考气液分离器沿程截面的速度不均匀度的变化,见图8。
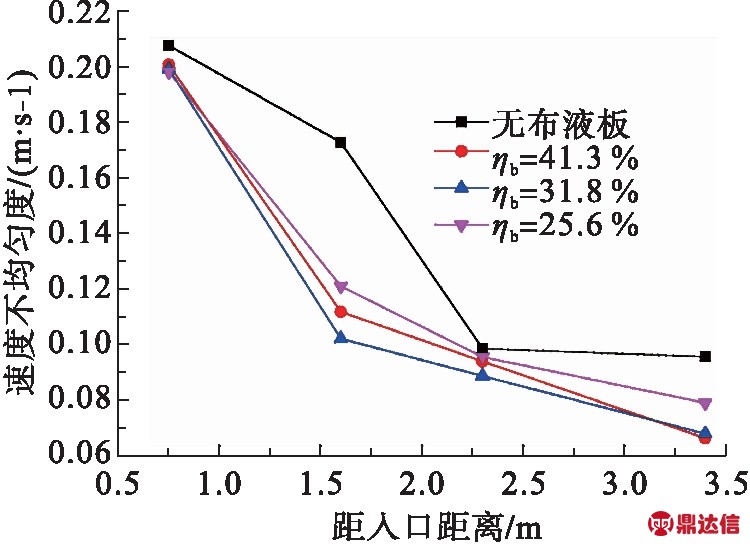
图8 不同孔隙率布液板的速度不均匀度变化曲线
从图8可以看出,不同孔隙率布液板对速度分布的紊乱都有改善,特别是在布液板后方一段距离内效果明显。但是不同孔隙率布液板效果不同,孔隙率过小或过大均不利于流场梳理,说明孔隙率存在一个最优值,此处约31.8 ,即孔直径20 mm,孔间距31.25 mm。
不同孔隙率布液板分离效率见图9,从图9可以看出,孔隙率对分离效率的影响与对速度分布的影响有相似的规律,安装了布液板后对分离效率有所提升,特别是对较小液滴提升较大;在孔直径相同时,同样存在孔隙率的最优值,过大或过小都会使分离效率下降,而在此处,保持孔隙率32 左右为佳。
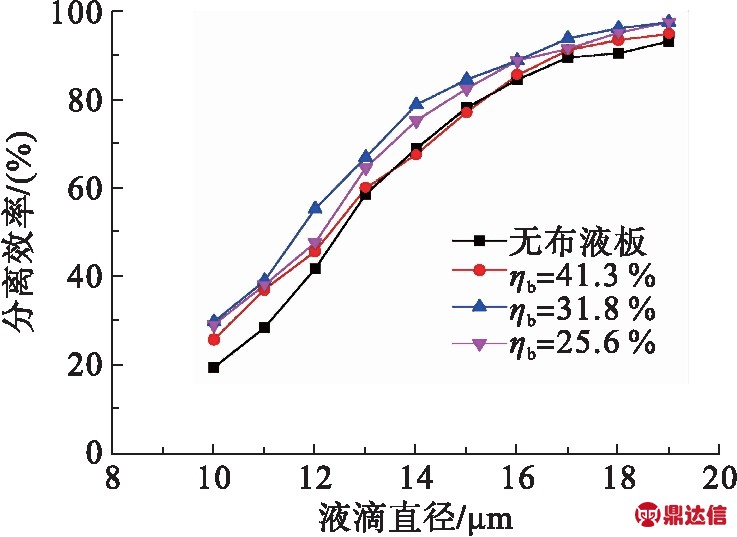
图9 不同孔隙率布液板分离效率变化曲线
3 结论
1)采用k-ε模型和DPM模型,对气液分离器安装不同结构布液板的分离流场进行模拟研究,并与无布液板的分离流场进行了对比。发现布液板能梳理流场,降低流速不均匀度,抑制回流,使流场分布更均匀稳定,有利于液滴的沉降分离。
2)布液板孔直径对流场的梳理作用有一定影响,孔径过大或者过小均不利于速度的均匀稳定,本气液分离器中安装孔直径约20 mm的布液板效果最优。
3)布液板孔隙率对流场的影响与孔直径有相同规律,孔隙率存在一个最利于分离器性能提高的最优值,本气液分离器中布液板孔隙率约31.8 时最佳。