摘 要:采用计算流体动力学(CFD)方法,对气液固三相旋流分离器的初始模型进行数值模拟,分析其内部流场分布,得出倒锥结构具有促进分离效果的作用。通过固定分离器的主直径与高度、入口尺寸、底流口直径、侧向出口尺寸、排液孔数量、排液孔尺寸、排液孔中心高度、溢流管直径、溢流管长度以及旋流腔长度,改变倒锥结构中的内锥直径与内锥高度,对模型进行优化,得到内锥直径为38mm、内锥高度为110mm时,三相旋流分离器的分离效果较好。
关键词:数值模拟 三相分离 结构优化 旋流分离器
目前,我国的许多油田都已经进入高含水期开采阶段,对新型高效分离设备的需求迫在眉睫。气液固三相旋流分离器作为一种新型的分离器,能够在同一时间实现脱气和除砂功能,成为近年来研究的重点。国内外许多学者对三相旋流分离器有一定的研究,并取得显著的成果[1-6]。但三相旋流分离器在实际应用中,其结构仍需进一步优化,分离效果有待进一步提高。计算流体动力学(Computational Fluid Dynamics,简称CFD)方法在三相旋流分离器中的应用,一方面可大大降低实验成本,节约人力物力;另一方面可深入分析其内部流场,进行机理分析,为结构优化提供理论依据。本文采用CFD方法,对三相旋流分离器的初始模型进行数值模拟分析,得到倒锥结构具有促进分离的作用,进而改变倒锥结构中的内锥直径与内锥高度,比较在不同参数条件下三相分离器的分离效果,得到优化模型。
1 初始模型的确立
由于改变三相旋流分离器结构会直接影响它的脱气效率、除砂效率以及压力损失,所以先给定初始模型的结构参数,再通过改变倒锥结构的内锥直径和内锥高度,确定分离器的优化结构。初始模型的结构参数为:三相旋流分离器的主直径为52mm,高度为238mm,两个入口尺寸为12mm×18mm,底流口直径为9mm,侧向出口尺寸为5mm×8mm,排液孔数量为8个,内锥直径为38mm,内锥高度为101mm,排液孔中心高度为58mm,旋流腔长度为80mm,溢流管直径为18mm,溢流管伸入长度为18mm。构建三相旋流分离器的三维模型。由于模型的结构相对复杂,网格都采用Txe/Hybrid的网格类型,网格图如图1所示。该模型设置的边界条件为:(1)两个入口均使用速度入口Velocity-inlet;(2)三个出口(溢流口,底流口,侧向出口)均使用自由出流Outflow;(3)壁面使用无滑移边界Wall。
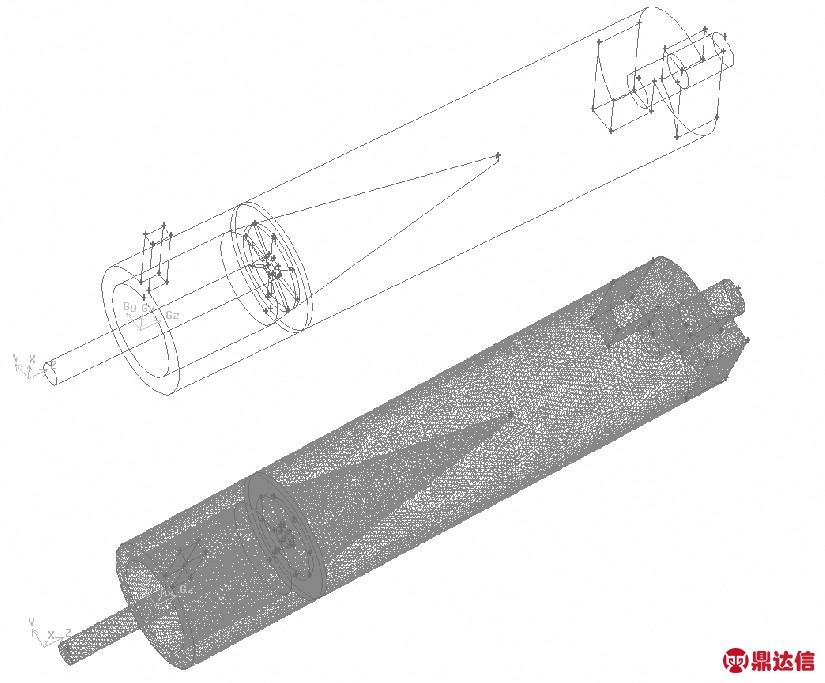
图1 三相旋流分离器的结构示意图和网格图
2 数值模拟及后处理分析
Fluent求解器选择“基于压力法的求解器”,压力速度耦合采用“SIMPLE算法”。湍流模型选择“k-ε模型”。压强差值格式选择“PRESTO!格式”,该格式主要用于高旋流、压力急剧变化流以及剧烈弯曲的区域。
对三相旋流分离器初始模型纵截面的三相旋流分离器初始模型纵截面的固相、液相和气相分布进行模拟,如图2所示。
图2a是三相旋流分离器初始模型纵截面的固相分布云图,从该图中可发现,在整个旋流器内部的柱面壁,固体基本附在内壁表面,这是由于固相、液相以及气相有较大密度差,再结合离心力的作用,固体到达壁面;底流口处固相的浓度很少,固液分离效果良好;在侧向出口附近,固相浓度高。在旋流分离器的溢流管内、溢流口附近以及倒锥结构的顶部,气相浓度非常高。在顶部形成一个气旋,说明倒锥的结构对分离效果有一定的影响;在底流口的出口处,气相浓度相对较低,但是整根底流管内部仍然存在部分气体;在侧向出口附近,气相浓度很低,说明分离效果较好。
图2c为三相旋流分离器初始模型纵截面的压力云图,从该图中可以看出,压力的分布具有一定规律,在旋流分离器内部压力沿轴向降低,在底流口处降至最低。然而在溢流口处因为有气体的充入,压力有所升高;同时可以观察出,压力沿着旋流分离器径向方向,从器壁到中心轴是降低的。这说明在旋流器内部存在轴向的压力梯度和径向的压力梯度,这样的压力梯度有助于气体的排出,提高分离效率。
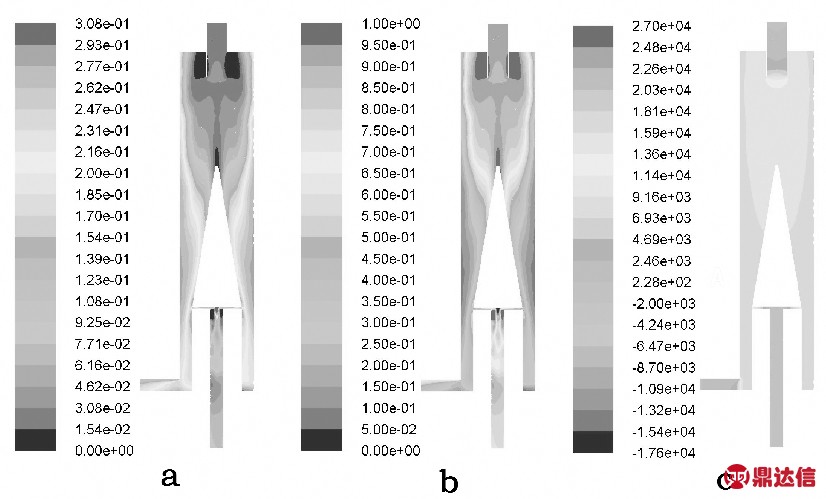
图2 初始模型纵截面,a.固相分布云图;b.气相分布云图;c.面压力云图
3 三相旋流分离器内锥结构的优化
根据初始模型气、液、固浓度云图以及压力云图的分析,发现旋流分离器的内锥结构对分离效果具有一定影响,能够有效地促进混合相的分离,对于已经分离的气体有向上举升的作用,而且对气体的及时排出有极大的促进作用。本文着重研究内锥直径和内锥高度对旋流分离器分离效果的影响。为了更充分的了解分离器内部流场的流动状况,在分离器内部,选择截面Ⅰ和截面Ⅱ进行分析。截面Ⅰ表示距离分离器顶部48mm的横截面,截面Ⅱ表示距离分离器底部28mm的横截面。
3.1 内锥直径对分离效果的影响
保持其它结构参数和操作参数不变,改变内锥直径来观察分析旋流分离器的分离效果。如图3所示,对比不同直径的三相旋流分离器在截面Ⅱ处的气相分布云图,可以观察到不同的内锥直径对三相旋流分离器的分离效果不同,从图中可以观察到速度在径向上有明显的梯度变化。切向速度直接影响旋流器分离器中产生的离心力,这是使三相分离的重要条件,切向速度的增大可改善分离效果,但切向速度过大,反而会造成粒子的破碎,不利于分离。直径为42mm的分离器切向速度过小,直径为30mm的分离器切向速度过大,38mm的三相旋流分离器的结构设计较合理。因此,切向速度值不宜过大或过小。
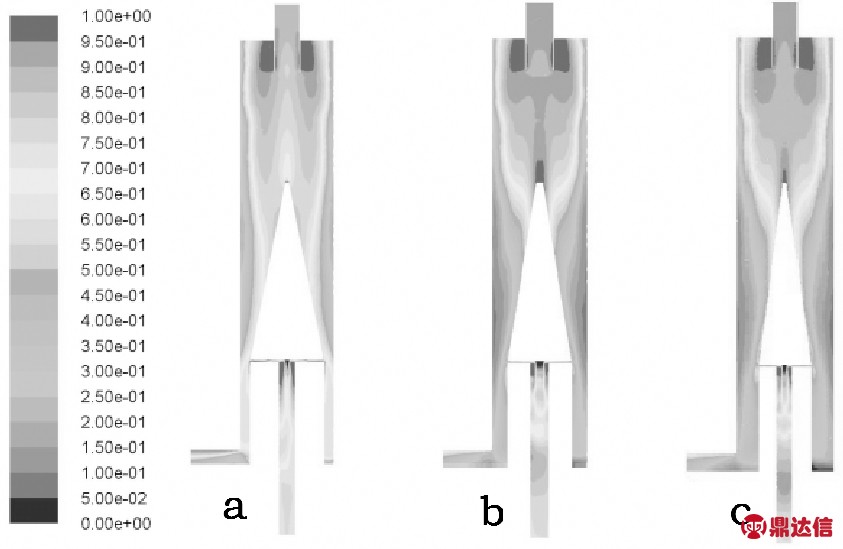
图3 截面Ⅱ处不同内锥直径的气相分布对比云图,内锥直径依次为a.42mm,b.38mm,c.30mm
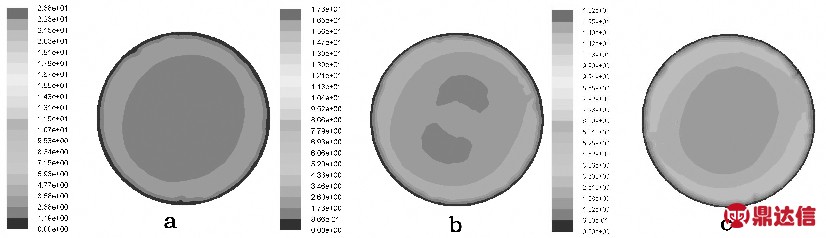
图4 截面Ⅱ处不同内锥直径的气相向速度对比云图和分布对比云图,内锥直径为a.42mm,b.38mm,c.30mm
3.2 内锥高度对分离效果的影响
本文所给的初始模型的内锥高度是101mm,保持其它结构参数和操作参数不变,改变内锥高度来观察分析旋流分离器的分离效果。如图4所示,对比不同内锥高度的三相旋流分离器在截面Ⅰ处的速度云图。对比速度云图可以看出,内锥越高,速度越大,但是在高度为118mm时,速度反而变小。通过上述对截面Ⅱ处气相分布和对截面Ⅰ切向速度的对比,得出当内锥高度径为110mm时,三相旋流分离器的结构设计较为合理。
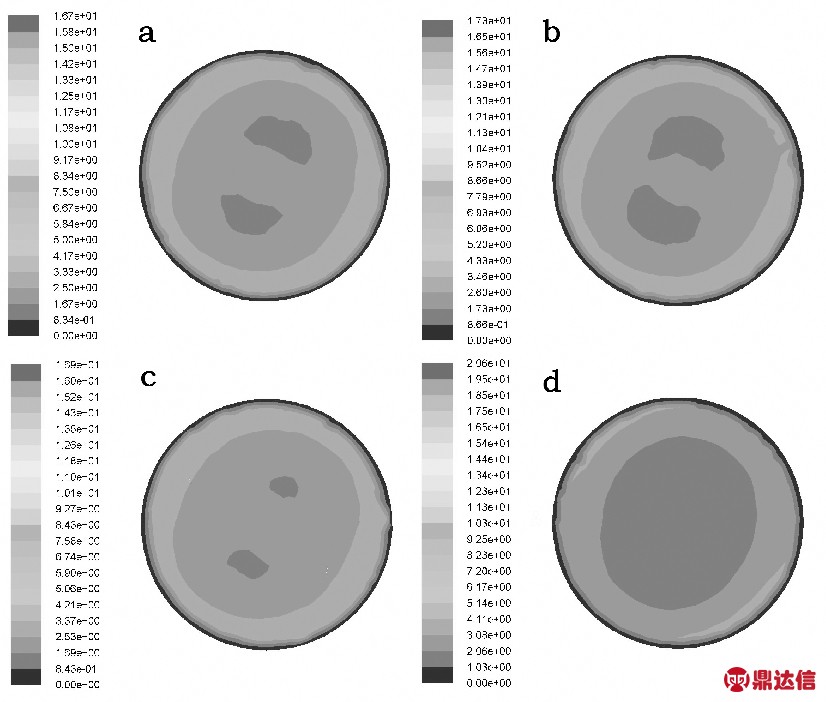
图5 截面Ⅰ处不同内锥高度的切向速度对比云图,内锥高度为a.101mm,b.110mm,c.30mm,d.118mm
3.3 优化模型的确立
通过分析对比,发现当内锥直径为38mm、内锥高度为110mm时,三相旋流分离器的分离效果较好,此时三相旋流分离器的设计较为合理。下面将优化模型和初始模型进行对比。
很显然,从图6可以看出,初始模型和优化模型的气相基本上都从溢流口流出,侧向出口基本没有气相。同时,可以看出气相浓度沿着径向向外的方向不断减小,但是优化模型的溢流口气相浓度比初始模型大。所以优化模型能够更好的分离气相和液相。
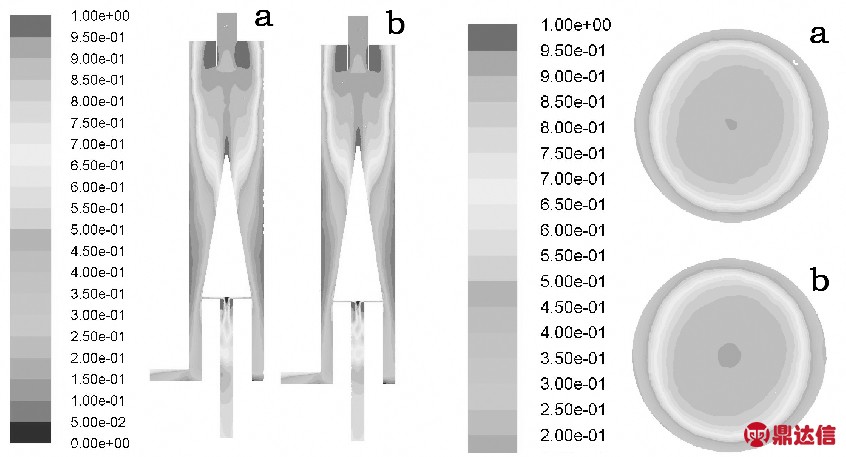
图6 纵/横截面气相分布对比云图a.优化前,b.优化后
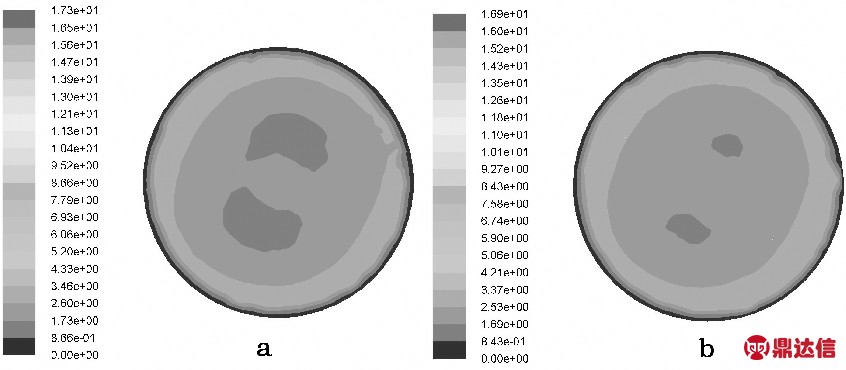
图7 纵/横截面Ⅰ的气相速度云图a.优化前,b.优化后
如图7所示,对比优化前和优化后的截面Ⅰ的气相速度云图,发现优化模型相比于初始模型的速度更大,再利用倒锥结构的举升作用,使得三相分离的几率更大,三相分离效果更好。
4 结论
本文研究三相旋流分离器内锥直径和内锥高度对分离效率的影响后得出以下结论:
(1)三相旋流分离器的内锥直径不是越大越好,我们应该根据不同的内锥直径对旋流分离器分离效果的影响来设计结构,通过分析可得出,内锥直径为38mm时,三相旋流分离器的设计较为合理。
(2)通过分析不同内锥高度对旋流分离器分离效果的影响,可以得出三相旋流分离器的内锥高度不是越高越好,对于本结构模型而言,内锥高度为110mm时,三相旋流分离器的分离效果较好。