摘 要:针对海上油气田开发后期所面临的储层压力降低、产出水不断增加、立管发生段塞等问题,分析采用水下分离器方案开发海上油气田的优势,研究水下分离器的测试技术,总结水下分离器在安装应用前需完成的试验、测试以及相应的技术要求,为打破国外垄断,实现水下分离器的国产化应用提供技术支持。
关键词:深水;油气田开发;水下分离器;测试技术;国产化
0 引 言
随着海上油气田开发水深和回接距离的不断增加,各种各样的问题逐渐涌现,如油藏压力降低、立管产生段塞和水合物等,这些都给油气田开发者带来巨大的技术挑战。解决这些问题,需要对深水开发的关键设施技术和设备,特别是水下分离器进行研究,以实现我国南海深水油气田的自主开发。在这个研究过程中,除需关注设备的设计技术外,还应关注设备在实际应用中的测试技术。
目前,世界范围内已经形成了全过程的产品质量跟踪试验测试、工业验证技术体系和配套的测试装备、技术体系,但这方面的关键技术掌握在少数先进国家、企业和公司手里,如FMC公司、GE公司等,对外实行技术垄断和封锁,而国内尚处于起步阶段,仅有宁波威瑞泰默赛多相流仪器设备有限公司研发了水下气液旋流分离器工程样机,甘肃蓝科石化高新装备股份有限公司研发了三相分离器原理样机。因此,本文对水下分离器的测试技术进行研究,为未来实现水下分离器的制造和国产化应用提供技术支持。
1 水下分离器的优势
水下分离技术是水下油气集输处理的一种新技术,对于水下生产系统的流动安全保障起着至关重要的作用。随着海上油气田开发数量的迅速增加,许多问题在已投产的海上油气田中显现出来,如海上油气田在生产后期会遇到储层压力降低、产出水不断增加的问题等。随着开发水深的不断增加,由于静水压升高,出现举升困难,立管产生段塞和水合物的概率增加、回接距离远等问题都严重影响着深海油气田的开发和采收率。深水油气田开发面临的问题如图1所示。世界范围内多采用水下分离技术解决这些问题,如:Tordis油田,其生产后期产出水不断增加,采用了SSBI系统[1](海底分离、增压和注水系统);Marimba油田[2]和Perdido油田[3],由于储层压力过低,采用了水下分离器。
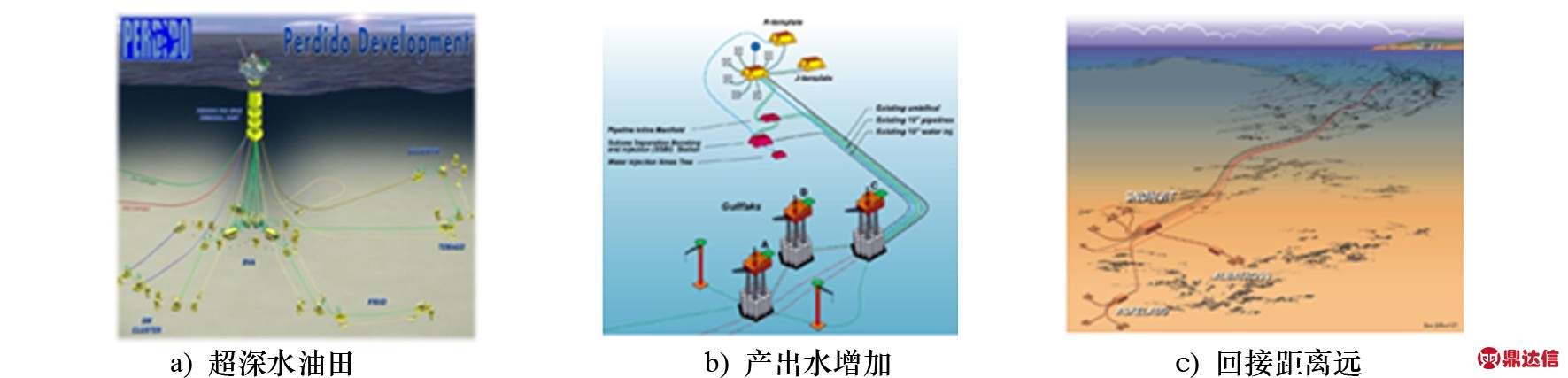
图1 深水油气田开发面临的问题
油气田开发中常遇到一些实际问题,如含水增加、药剂用量增加、立管产生段塞、水合物的概率增加,压力降低和无法自然输送等。采用水下分离器处理深水油气田开发问题具有以下几点优势:(1) 在深海进行水下分离,将装置置于海底,可以不受天气或气候影响,既减轻了海上平台的负担,又不会因为平台的状况而影响油气处理效果,可以降低投资和生产成本。(2) 在海底进行水下分离,只需举升有用的油气,可以减少管线的尺寸,从而降低油气输送过程中化学药剂的使用量。(3) 水下分离可以减小井口背压,避免产生立管段塞流,从而减少产生气蚀等设备破坏问题,降低水合物形成的概率。(4) 可以提高油气采收率,提高原油的输送能力[4],显著降低油气田开发成本。
2 水下分离器的测试类型
国外在近十几年的时间中,对水下分离器的设计及制造加工技术进行研究。水下分离器从2001年开始应用,目前,大约有20套水下分离装置成功应用于挪威、巴西和美国等国家,其中最大应用水深达2 400 m。但是国内对水下分离器的研究和设计尚处于探索阶段,还没有水下分离器的产品成品。在水下分离器产品进入实际应用之前,一般需要经过一系列的试验和测试以保证水下分离器的性能和可靠性。
通过调研相关标准和国外厂家对水下设备的试验,探索研究出水下分离器在成为工业产品前需要进行的现场测试类型。水下分离器的现场测试主要包括:材料试验、无损检测、内压试验、高压舱试验、陆地试验、水池试验和工厂验收FAT试验等。
(1) 材料试验。水下分离器在海底高压低温的环境中工作,其材料的选择要满足一定的强度和稳定性要求[5]。因此,选定水下分离器的材料后,需要对材料的力学性能(强度、硬度和塑性等)和工艺性能(铸造性能、锻压性能、焊接性能和切削加工性能等)进行测试,以满足水下分离器使用环境的要求。
(2) 无损检测。水下分离器在建造完成后,需要对整体结构进行探伤和焊缝无损检测,以保证水下分离器的整体结构没有缺陷,从而保障水下分离器单个元件和整体的材料性能和结构强度。只有无损检测合格后才可以进行水下分离器的内压强度试验。水下分离器的无损检测需要在拥有检测资质的厂家进行专门的检测。
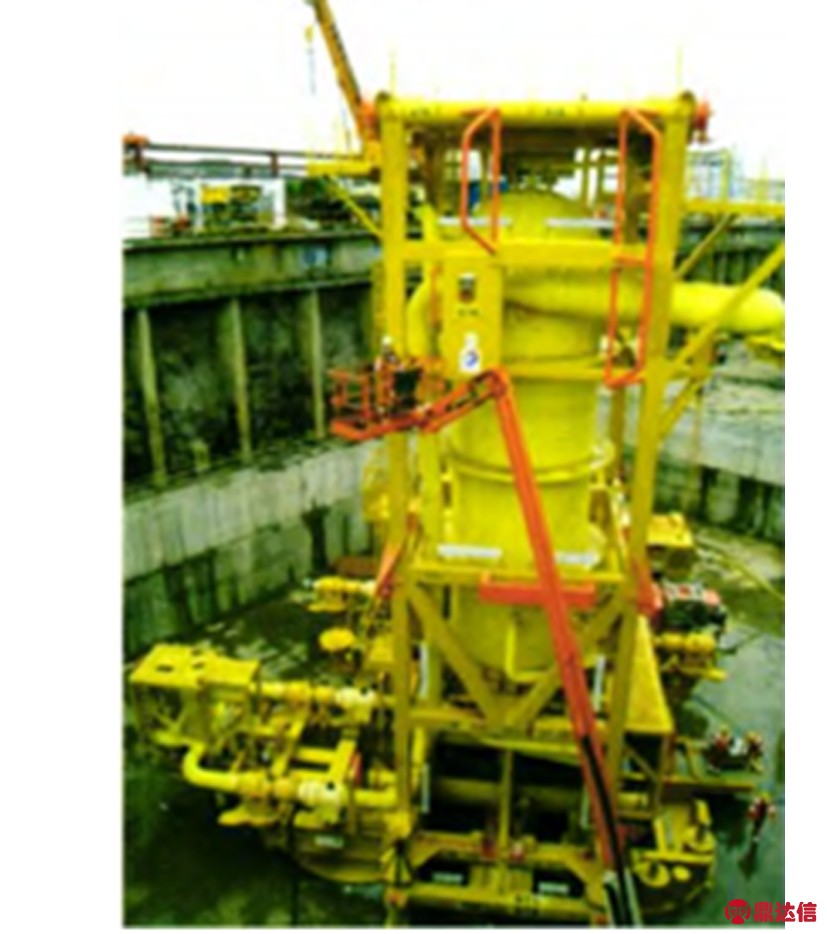
图2 FMC公司分离器的水池测试
(3) 内压试验。水下分离器用于对海底生产流体进行分离,其内部需要承受生产流体的压力和温度,因此,需要对水下分离器进行内压试验,以保证水下分离器的结构强度要求。水下分离器位于海底,为了保证其在使用过程中内部流体不发生泄漏,也需要进行内压试验和外压试验,以保证水下分离器的密封性能要求。只有内压试验合格后才可以进行水下分离器保护漆的第1次喷涂工作,此时的保护漆仅是普通的用于防止设备免受环境侵蚀、生锈的原色保护漆。
(4) 高压舱试验。为了使水下分离器能够在设计的使用水深处正常工作,还需要进行高压舱试验,以保证水下分离器在高外压作用下的结构强度、稳定性、可靠性以及密封性能要求。在高压舱试验合格后可以进行水下分离器保护漆的整体喷涂工作,此时的保护漆是按照对海洋设备的要求而特制的黄色保护漆。
(5) 陆地试验。陆地试验用于测试水下分离器的分离性能、各部分组件的可操作性能和阀门的液位控制能力。经过陆地试验的测试,可以测试、计算得出水下分离器的分离效率,测试出不同气、液流量对水下分离器分离性能的影响,寻找、总结原因和规律,从而有助于下一步改进水下分离器的设计。
(6) 水池试验。水池试验用于模拟水下分离器的使用环境、测试水下分离器在水下的各种性能(包括:分离性能、液位控制性能、组件的可操作性能和密封性能)和水下分离器的安装测试。如美国FMC公司为Pazflor项目生产制造的水下分离器,在正式投入使用前先进行了水池测试,如图2所示[6]。
(7) 工厂验收FAT试验。工厂验收FAT试验是为了确定水下分离器的各组件是否满足特定的功能和技术要求。在通过FAT试验后,需要进行系统集成SIT试验,用于水下分离器的系统性能测试和联调,以保证水下分离器在交付使用前各项性能指标均满足要求。
3 水下分离器的测试
水下分离器的现场测试类型很多,本文仅对内压试验、高压舱试验、陆地试验和水池试验作详细介绍。
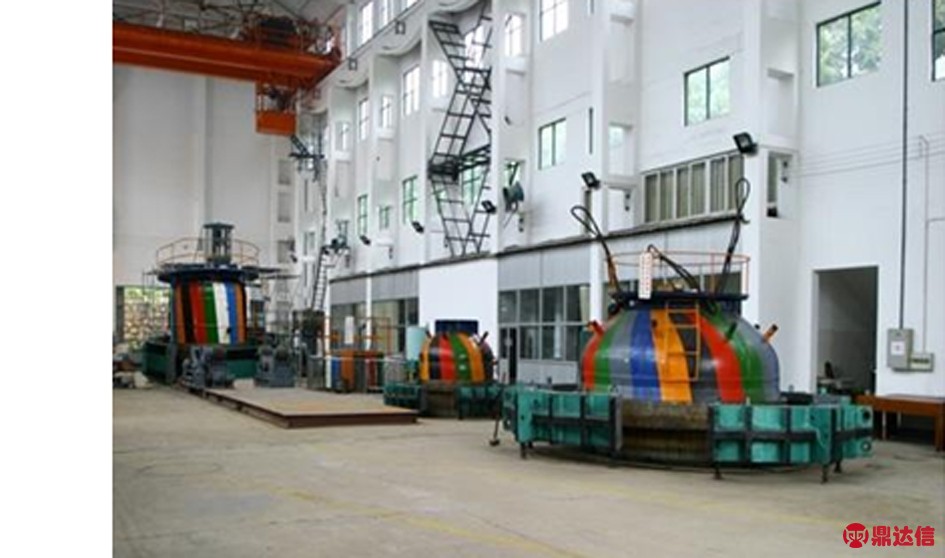
图3 高压舱测试现场
(1) 内压试验。在内压试验阶段,向水下分离器设备注水,并加载一定的压力进行保压试验,从而确定水下分离器的承压性能和密封性能。水下分离器内压试验所需要的试验设备有测试用承压帽、压力计、计时秒表、测试用软管、高压泵和测试用水收集容器(水桶)等。试验步骤为:a)使用测试用软管向水下分离器中注水。当注入水水层与水下分离器快速接头顶部的法向距离达到约5 cm时,注水停止。b) 将相应的测试用承压帽安装到水下分离器与跨接管连接的快速接头上。 c) 在测试要求的保压时间15 min内,观察压力计的数值,以检测压力是否有下降,测试用水是否有泄漏现象。d) 测试完成后,从水下分离器中排出测试用水,并使用相应的容器收集测试用水。
(2) 外压试验。在水下分离器设备制造、喷涂完成后,进行高压舱试验。在高压舱试验阶段,把水下分离器设备放入高压舱进行外压强度、形变、涂层和密封性的综合测试,如图3所示。高压舱试验可以获得水下分离器容器关键结构部位的应力应变数据,从而判断水下分离器的结构强度性能和稳定性能。高压舱试验所需要的试验设备包括:压力筒、压力表、压力传感器、数字应变仪和转换箱等。测量系统如图4所示。试验方法:对水下分离器设备进行匀时、匀速的加载和卸载。由于水下分离器在海底使用,需要根据水下分离器工作的水深确定水下分离器所需承受的外压值,并在试验中选取使用水深压力的1.5倍作为最高压力进行加载,且需在使用水深压力的1.1倍压力处保压30 min进行测试。在经过均匀加载试验和卸载试验后,水下分离器结构表面未见明显形变,且未见漏水,表明水下分离器的结构强度和密封性能良好,满足设计要求。
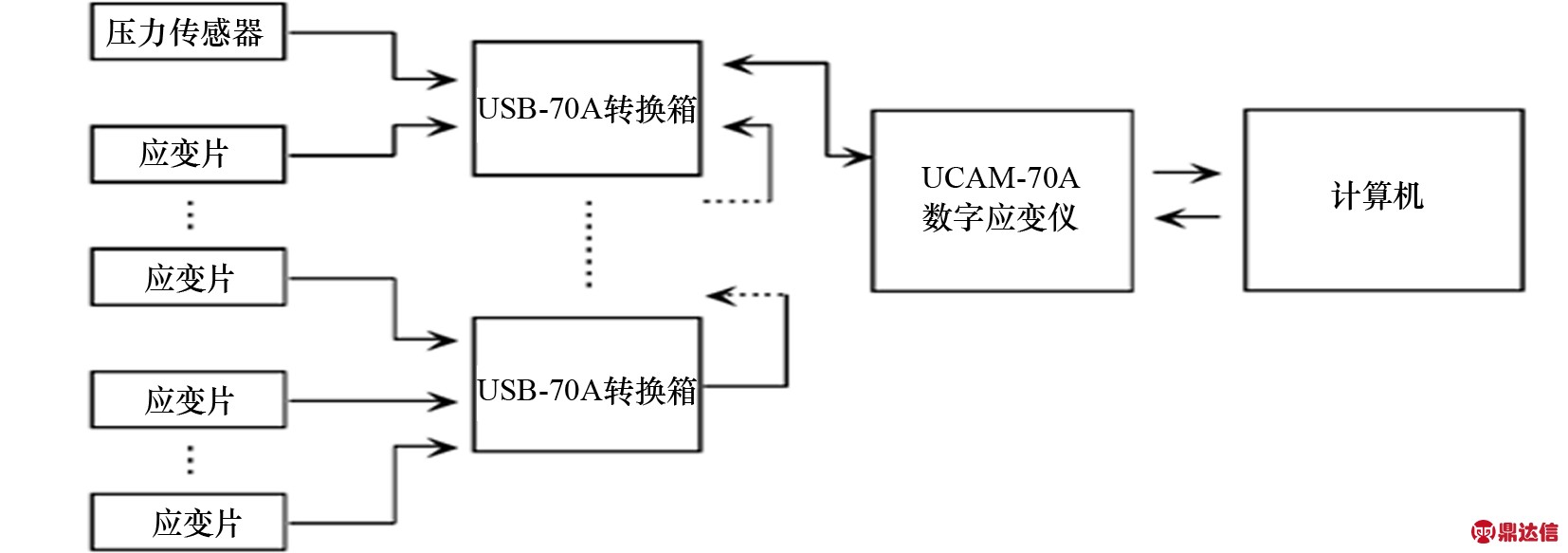
图4 测量系统框图
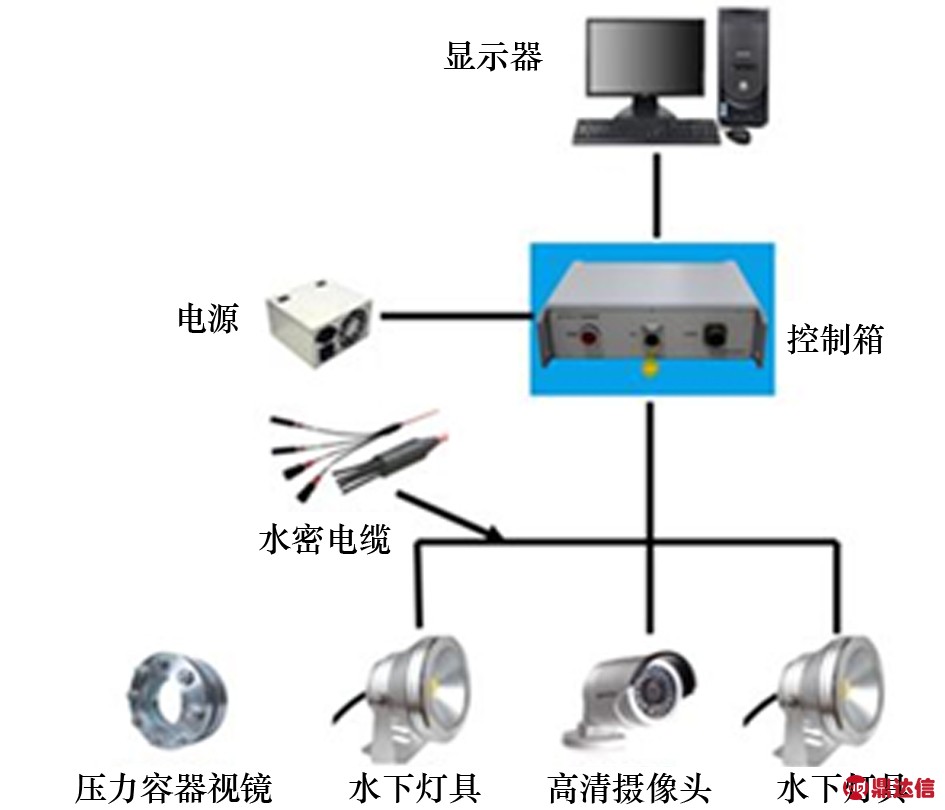
图5 监控部件
(3) 陆地试验。陆地试验的试验设备包括:测试发生回路、流量计、温度变送器和压力变送器。试验方法:混合后的空气、水进入水下分离器中,分离后的气体通过气路流量计进行计量并记录,液相通过液路流量计进行计量并记录,之后气液两相在出口处汇集进入下游流程。在试验过程中,同时检测设备的压力和温度。改变流量,分别记录气相、液相流量值。经过测试,并对数据进行分析,判断水下分离器的分离性能。
(4) 水池试验。水池试验的试验设备包括:测试发生回路、温度变送器、压力变送器、测试水池和水下监控部件。测试发生回路是模拟流体工况的发生装置,用于向水下分离器中输送流体;水下监控部件用于监测水下分离器在水池中的情况,将水池试验可视化。水下监控部件主要由高清摄像头、水下灯具和压力容器视镜等组成,如图5所示。在水池试验中需要测试水下分离器的调节阀及液压驱动单元能否正常工作、液位波动是否满足设计要求、压力波动是否满足设计要求和水下分离器的连续稳定工作时间是否满足设计要求。试验方法:(1) 混合后的空气、水进入水下分离器中,记录单相的流量、系统压力、温度,同时观察水下分离器的液位、压力、温度等参数的波动情况。(2) 改变流量,分别选择设计参数的10%,50%,75%,100%,120%等进行测试,观察、记录水下分离器的液位、压力、温度和单相流量等参数的波动情况。(3) 改变液位,观察水下分离器的压力、温度和单相流量等参数的波动情况。(4) 经过多轮测试,将测试数据进行对比分析,判断水下分离器的分离性能、液位控制性能和组件的可操作性能。
4 结 语
为了能更好地评估水下分离器设备的可靠性和稳定性,本文重点研究了水下分离器的现场测试技术,以确保水下分离器产品的质量。材料试验、无损检测、内压试验和高压舱试验是水下分离器的基础试验,为水下分离器系统的集成和后续的试验提供技术保障,陆地试验、水池试验和工厂验收FAT试验等是水下分离器的核心试验,是验证水下分离器综合性能的试验。本研究为实现水下分离器的国产化及应用提供技术支持。