摘 要:旋风分离器内部流场较为复杂,属于典型的三维湍流强旋流场,具有非线性、时变性等特点,而颗粒在旋风分离器内的运动则更为复杂。应用Fluent软件来对旋风分离器内气固两相流进行数值模拟研究,以期能够更加深入、更加全面地认识旋风分离器内部流动规律,进而实现模拟与工业应用的良好结合。
关键词:旋风分离器;气固两相流;数值模拟
旋风分离器内部流场较为复杂,属于典型的三维湍流强旋流场,具有非线性、时变性等特点,而颗粒在旋风分离器内的运动则更为复杂。若想更好地提高旋风分离器的分离性能,就需要深入研究旋风分离器内气固两相流的流动情况。主要存在3种研究方法:计算流体力学法、实验法和理论分析法。早期对旋风分离器的研究基本都是理论分析法,为了能够更简便地了解旋风分离器的气固两相流情况,很多学者[1-2]都提出了各种各样的研究假设,所得出的理论研究结果与实际情况存在着一定的差异;而后又有较多的学者通过实验方法来对旋风分离器的分离机理进行研究,并将理论模型与实验数据进行拟合,进而得出了一系列的经验模型,但这些经验模型无法通用于全部类型的旋风分离器,只能对有限的问题进行解决。计算流体力学法则是近年来随着计算机技术、数值计算方法发展起来的一种研究方法,目前已经取得了较快的发展。有鉴于此,本文通过建立正确的CFD数学模型,应用Fluent软件来对旋风分离器内气固两相流进行数值模拟研究。
1 数值模拟
1.1 几何模型的建立和网格的划分
采用ANSYS DM(design model)建模,为了准确反映旋风分离器内部实际的流场情况,对几何模型未作任何简化,保持其几何尺寸与实验结构尺寸完全一致(见图1),将排尘口的中心处设置为坐标原点,沿着旋风分离器中心轴线向上的方向为z轴正方向。而数值计算的关键步骤在于网格的划分,网格划分也是流场数值模拟的前处理过程,最终计算结果的精度会直接受到网格质量的影响,若网格质量较差,还有可能会导致最终计算结果出现严重的失真现象。由于旋风分离器的进气口与圆筒体相切,且存在着较为尖锐的夹角,所以,很难对旋风分离器进行整体网格划分。所以,采用Gambit®2.4将旋风分离器分为3个子区域来进行分块网格划分,分别是锥体区域、入口和环形区域、排气管区域;每个区域都采取结构化网格,待生成网格之后就组合在一起形成整体网格,经过网格无关性验证,最终网格数为15万。
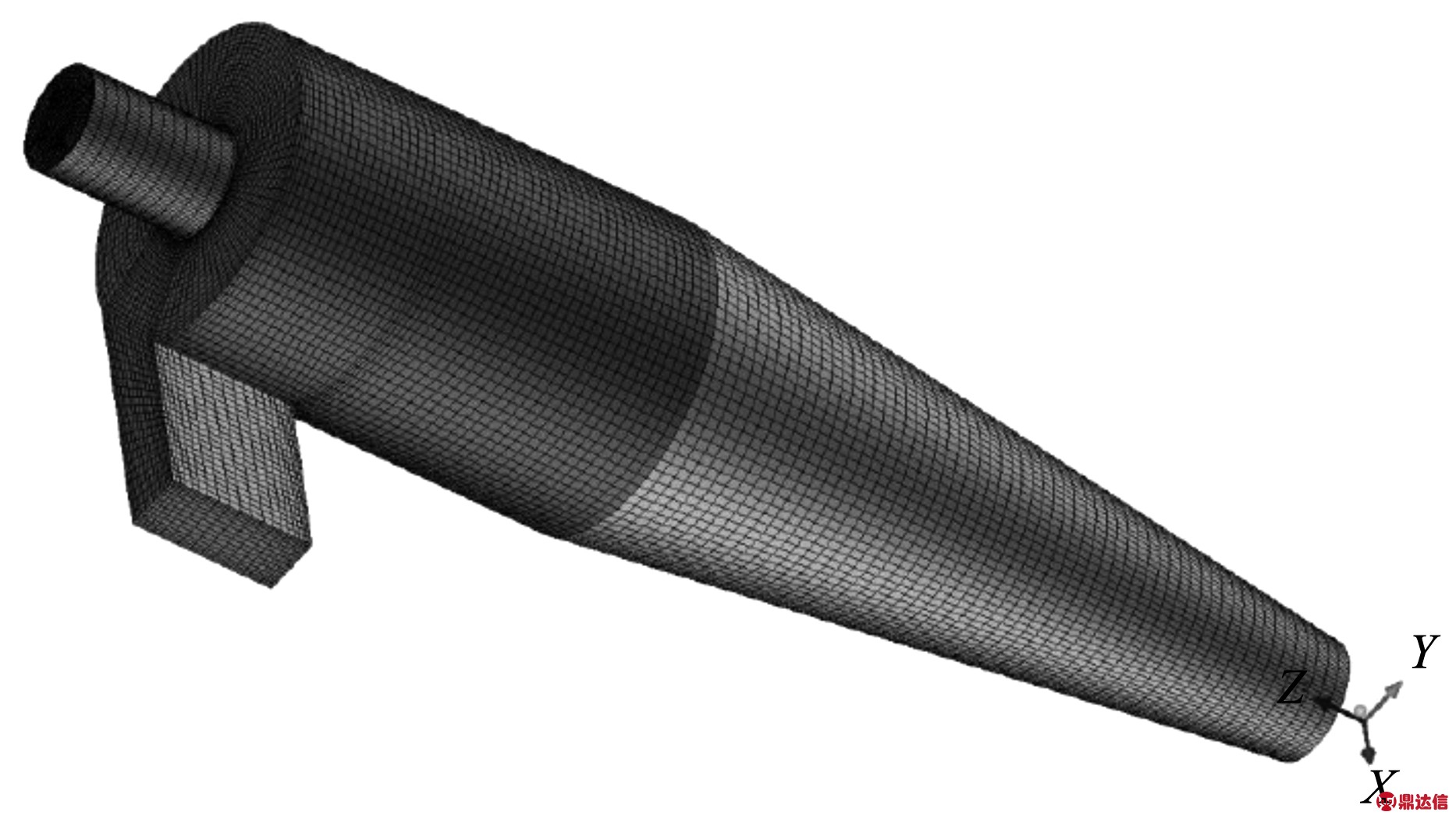
图1 旋风分离器网格划分
1.2 参数设置
1.2.1 设置材料及物性
本文在气固两相模拟时,气相所采用的介质仍然为常温空气(温度为20 ℃,密度为1.225 kg/m3,黏度为1.789 4×10-5 kg/(m·s)),与单相气相设置完全相同。颗粒相采用颗粒密度为1 450 kg/m3的颗粒,假定固体颗粒均为球形的,那么模拟时可采用均一粒径颗粒。固体颗粒的粒径分布情况可采用Rosin-Rammler分布法来模拟,Rosin-Rammler分布法将固体颗粒全部的粒径范围均分为若干个离散的尺寸组,每个尺寸组由一个组射流源中的颗粒流来代表,并且假设Yd(颗粒质量分数)与d(颗粒的粒径)之间存在着一定的指数关系:
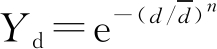
(1)
式中,n是分布指数,取是中位径,定为15 μm。
在强旋转流动的作用下,固体颗粒在旋风分离器中的流动状态较为复杂,总体上难以描述,故可从单颗粒运动轨迹入手来进行观察,而颗粒的入射位置、粒径大小不同均会造成单颗粒运动轨迹存在着较大的差异。图2为粒径6 μm的颗粒运动轨迹图,分别有9个入射位置,其中,(a)为入口部分的外侧下方位置,(b)为入口部分的外侧中心位置,(c)为入口部分的外侧上方位置,(d)为入口部分的中间下方位置,(e)为入口部分的中间中心位置,(f)为入口部分的中间上方位置,(g)为入口部分的内侧下方位置,(h)为入口部分的内侧中心位置,(i)为入口部分的内侧上方位置。
旋风分离器数学模型主要包含动量守恒方程、质量守恒方程和控制方程等,其中,控制方程为三维雷诺时均N-S方程。在选择湍流模型时,由于RSM模型较好地将流线型旋转、弯曲而造成的张力迅猛变化考虑其中,能够更好地预测复杂流动情况,故选用RSM模型作为湍流模型。
1.2.3 设置两相边界条件
1)入口处:采用平面射流源的方式来释放固体颗粒,颗粒流的初始位置即为入口面,固体颗粒均匀地从入口面入射到旋风分离器内。由于固体颗粒进入旋风分离器时就已有较佳的跟随性,所以,颗粒的入口速度与气相相同,并且气体和固体颗粒之间还存在一定的滑移速度,假定固体颗粒在运动时不存在旋转、相互碰撞的情况。
2)壁面处:设置为reflect,假定当固体颗粒运动到壁面时,就会与壁面出现弹性碰撞现象,可通过恢复系数来确定固体颗粒的动量变化。气相为无滑移,固相为半滑移。
3)颗粒相出口处:设置为trap,假定一旦有固体颗粒运动到颗粒相出口面(排尘口底部边界),那么就会出现颗粒完全捕集的现象,这种情况下就停止跟踪颗粒运动。
1.2.2 数学模型
为了保证装置运行稳定,模拟时间设为40 s,后10 s进行数据时均统计。时间步长设为0.000 3 s,每一步最大迭代次数为40次,以此保证计算的收敛。
2 结果与讨论
2.1 单颗粒运动轨迹
4)气相出口处:设置为escape,假定当固体颗粒运动到气相出口面(排气管出口),那么就认为固体颗粒已经不能再被捕集,已经完全逃逸出旋风分离器。
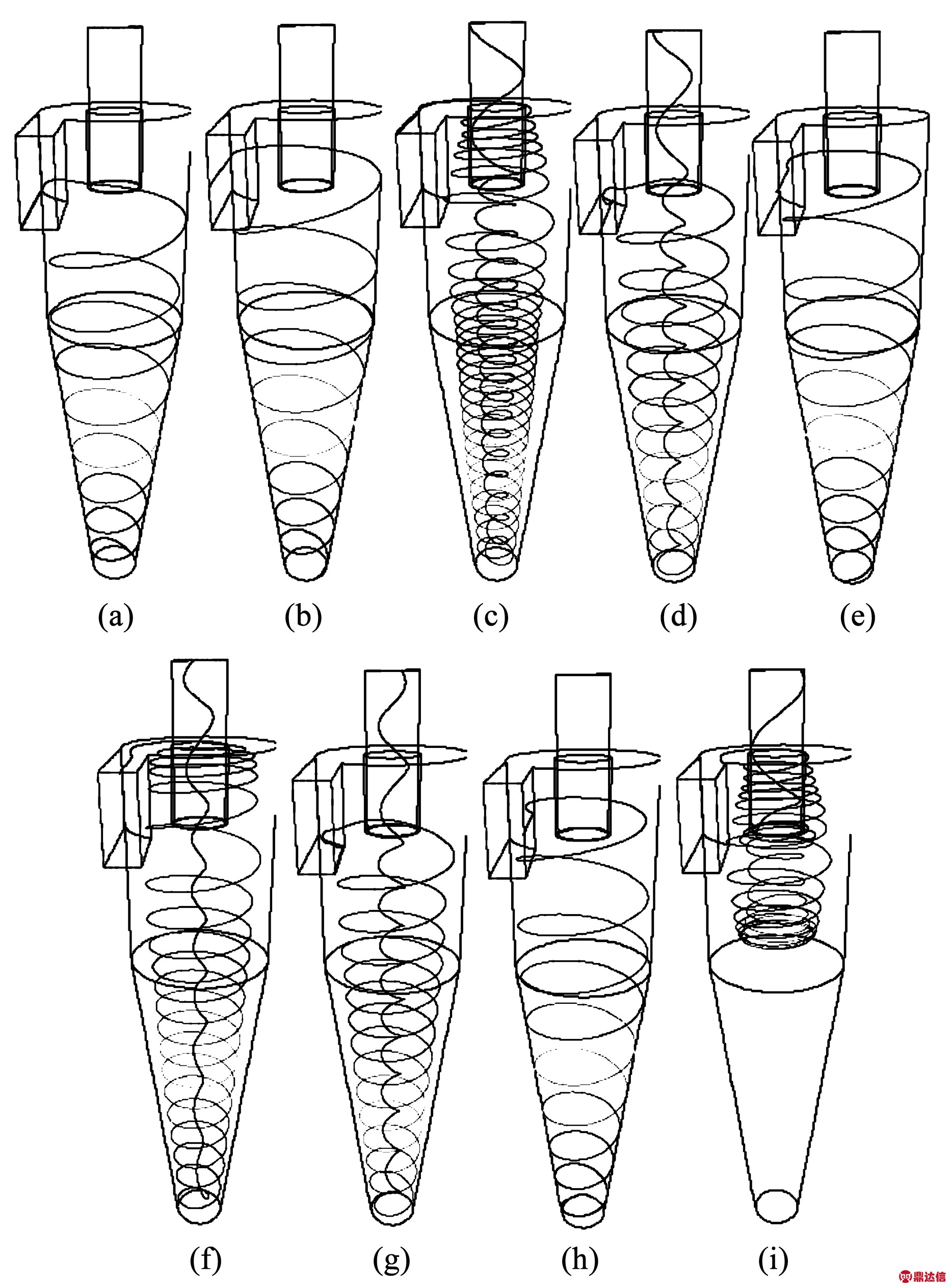
图2 粒径为6 μm的颗粒运动轨迹图
由图2可见,入射位置为(c)、(f)、(i)时均出现了固体颗粒逃逸的现象,且3个入射位置均由上方位置进入到旋风分离器内部,其中,(i)是固体颗粒在受到排气管处气流短路影响之下而出现逃逸,(c)、(f)是固体颗粒在气体的夹带之下出现逃逸,由此可见,由上方位置入射到旋风分离器内部的固体颗粒不易分离,很容易出现颗粒逃逸或者短路流的现象。入射位置为(b)、(e)、(h)时均出现了固体颗粒被捕集的现象,且3个入射位置均由中间位置进入到旋风分离器内部,由此可见,由中间位置入射到旋风分离器内部的固体颗粒易于分离。此外,入射位置为(g)、(i)时均出现了固体颗粒逃逸的现象,且2个入射位置均由入口内侧进入到旋风分离器内部;而入射位置为(a)、(b)时均出现了固体颗粒被捕集的现象,且2个入射位置均由入口外侧进入到旋风分离器内部,由此可见,与入口内侧相比,由入口外侧进入到旋风分离器内部的固体颗粒被捕集的几率更高。主要原因在于:由入口外侧进入到旋风分离器内部的固体颗粒通常会受到较大的离心力,这样一来,就很容易被抛甩到外壁面,进而实现分离。
2.2 颗粒组运动轨迹
颗粒组运动轨迹图如图3所示,其中,(a)为粒径为6 μm的颗粒组运动轨迹图,(b)为粒径为10 μm的颗粒组运动轨迹图,(c)为粒径为15 μm的颗粒组运动轨迹图,(d)为基于Rosin-Rammler分布的颗粒组运动轨迹图。由图3可知,颗粒组的分离效率、运动轨迹与粒径大小存在着密切的联系,当粒径为6 μm时,排气管有大量的固体颗粒逃逸;当粒径增大为10 μm时,经过排气管逃逸的固体颗粒数量大幅度减小;当粒径增大为15 μm时,固体颗粒基本被全部捕集。由此可见,粒径越大,越易于被捕集;粒径越小,越易于逃逸。观察图3中(d)的排气管可见,气体夹带着少量的固体颗粒,边旋转边离开旋风分离器,流出方式并非单纯的直线型,这充分说明出口气流同时具有一定的切向速度与轴向速度。
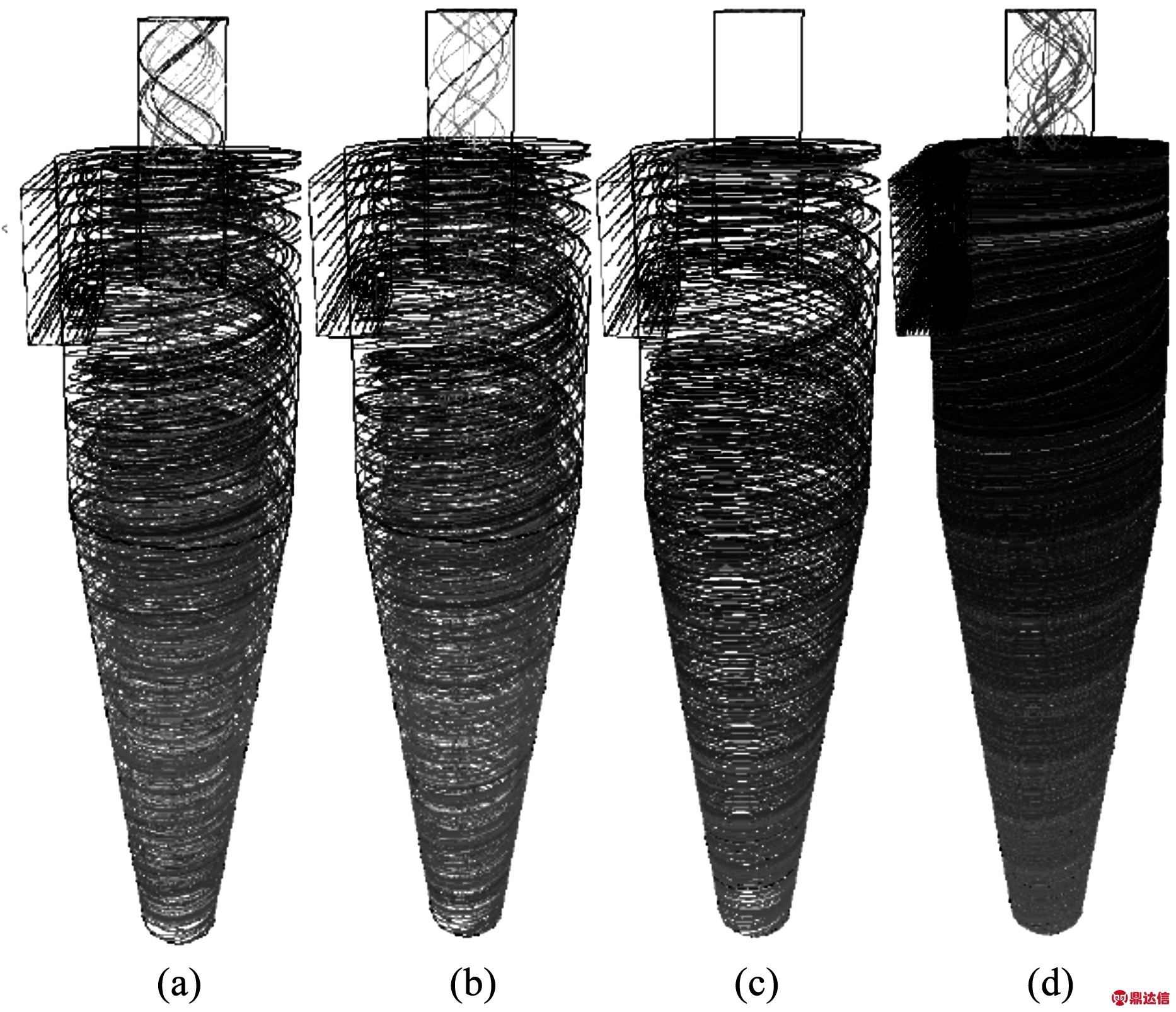
图3 颗粒组运动轨迹图
2.3 分离性能
2.3.1 颗粒粒级效率和总效率
通常而言,分离效率的计算方法有2种:1)选择逃逸的颗粒数与释放的总颗粒数的比值大小;2)选择捕集到的颗粒数与释放的总颗粒数的比值大小。本文选择第1种计算方法。分级效率是指旋风分离器对于某一粒径颗粒的分离效率;与总效率相比,分级效率能够更好地将旋风分离器的分离性能进行表明。本节从入口均匀喷射了若干个不同粒径的颗粒,以此来获得颗粒的分级效率,进而能够求得分离效率。分级效率的计算式见式2,分离效率的计算式见式3。值得注意的是,分离效率精度与从气固两相入口面释放的颗粒数存在着较大的正比关系。

(2)

(3)
式中,nie是从气相出口面逃逸的颗粒数;nif是从气固两相入口面释放的颗粒数;nic是从颗粒相出口面捕集到的颗粒数;di是颗粒粒径,单位为μm;η是分离效率。
模拟所得的颗粒粒级效率和总效率见表1,模拟得到的旋风分离器分级效率如图4所示,由图4可知,旋风分离器的分离能力随着粒径的增大而增强,若粒径<3 μm,那么分级效率较低,基本≤50%;而粒径>6 μm,则分级效率基本都>50%,粒径为15 μm及以上的分级效率为100%,可全部分离。
表1 模拟所得的颗粒粒级效率和总效率
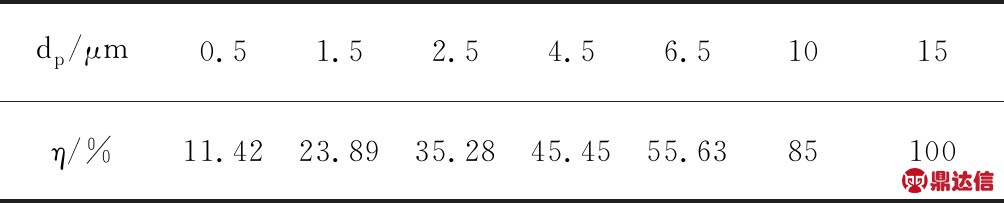
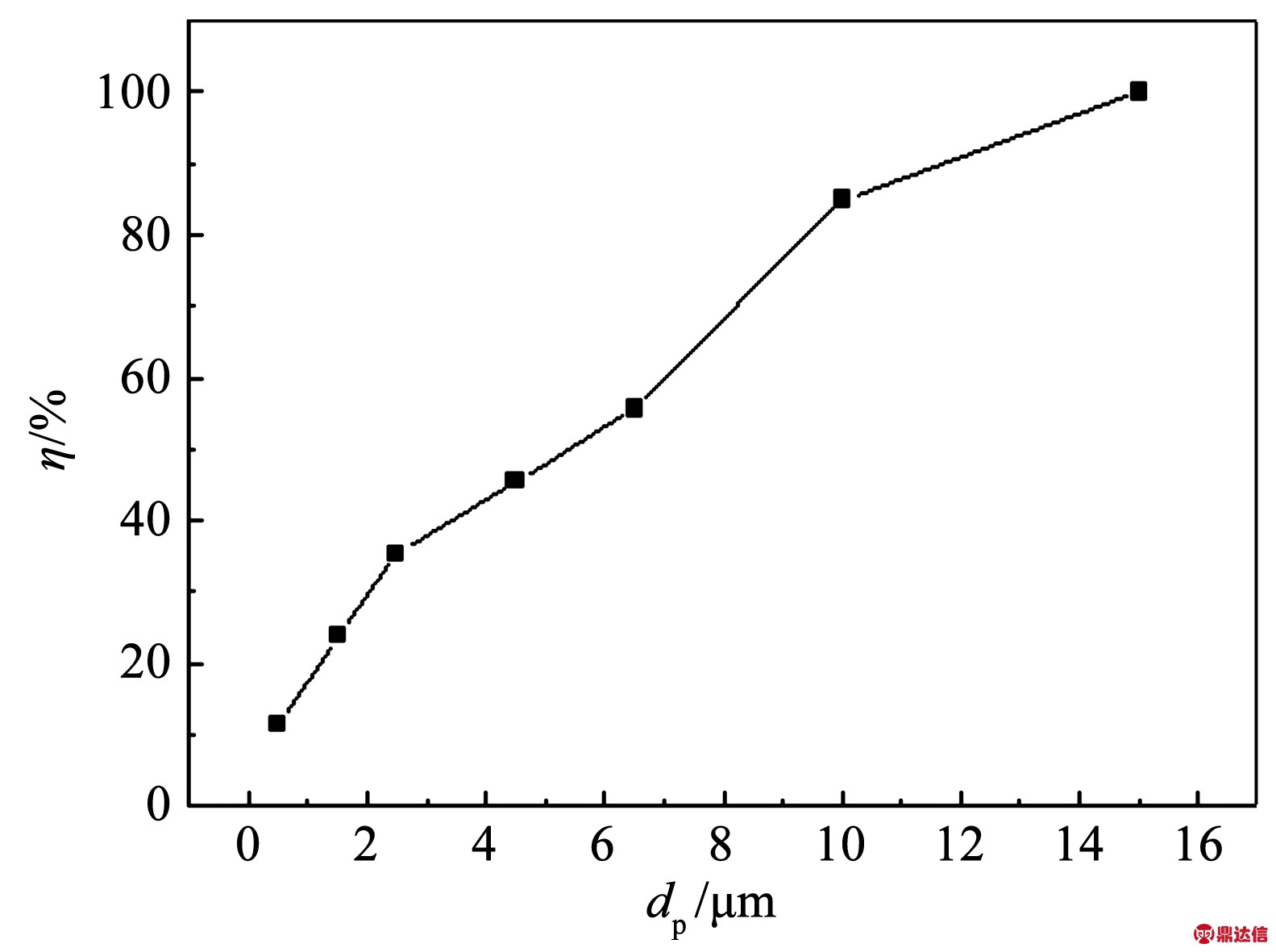
图4 模拟得到的旋风分离器分级效率
2.3.2 入射位置对分离效率的影响
为了能够分析出入射位置对分离效率的影响,本文跟踪了3 000个固体颗粒,粒径<3 μm、3~6 μm、>6 μm的颗粒组颗粒捕集统计图如图5~图7所示。与中心位置入射、上方位置入射相比,颗粒组从下方位置入射的捕捉效果更佳,但差异并不太大,并且分离效率随着粒径的增大而增大,逃逸颗粒数量日趋减少。
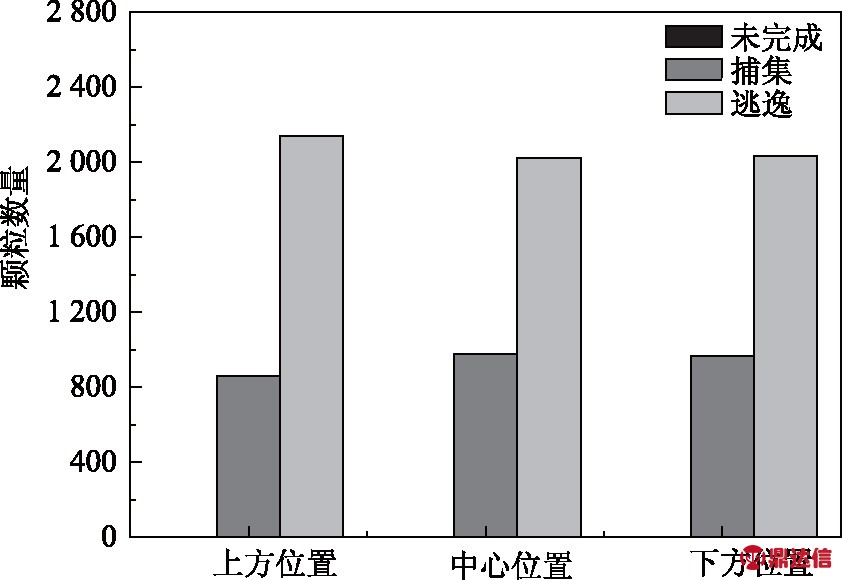
图5 粒径<3 μm的颗粒组颗粒捕集统计图
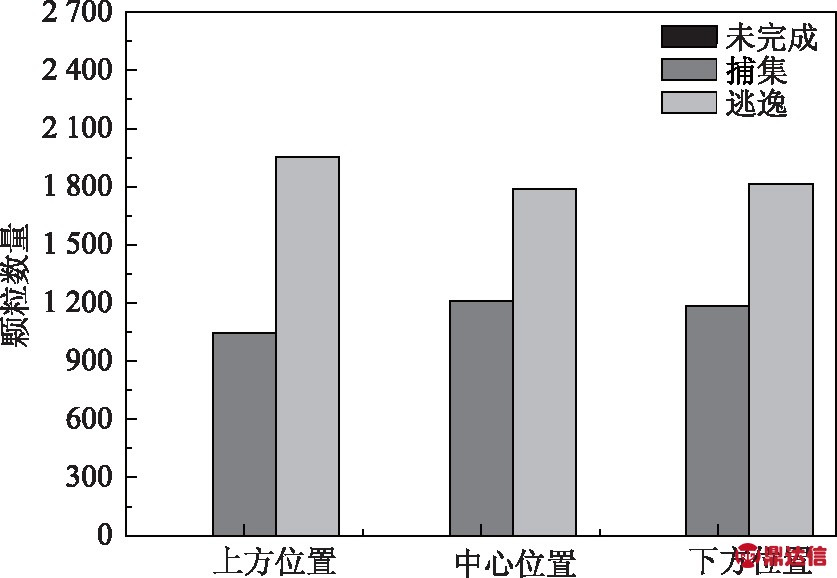
图6 粒径为3~6 μm的颗粒组颗粒捕集统计图
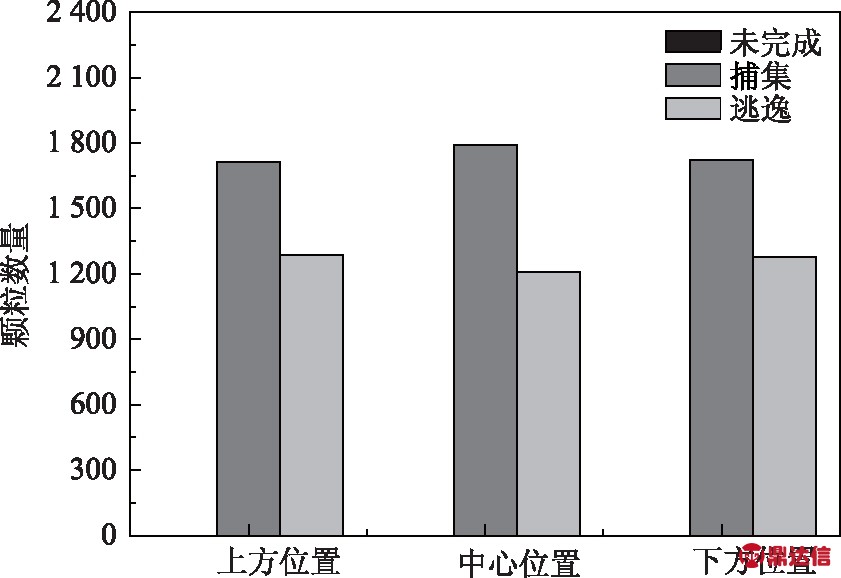
图7 粒径>6 μm的颗粒组颗粒捕集统计图
3 操作参数对分离性能的影响
3.1 入口速度
入口速度的大小表征了旋风分离器处理含尘气流的能力,入口速度越大,就表示能够处理越多的含尘气流。为了能够分析入口速度对旋风分离器分离性能的影响,本节分别选择了5个入口速度,分别是5、7.5、10、12.5和15 m/s,进气管总流量为0.05 kg/s。不同入口速度下旋风分离器的分离效率如图8所示,由图8可见,旋风分离器的分离效率随着入口速度的增加而增加,主要原因在于入口速度的增加会导致颗粒所受的离心力增加,这样一来,就会导致颗粒向外壁面抛甩速度加快,进而实现分离。由此可见,若固体颗粒的粒径适中,为了能够提高旋风分离器的分离性能,那么可将入口速度适当增大。
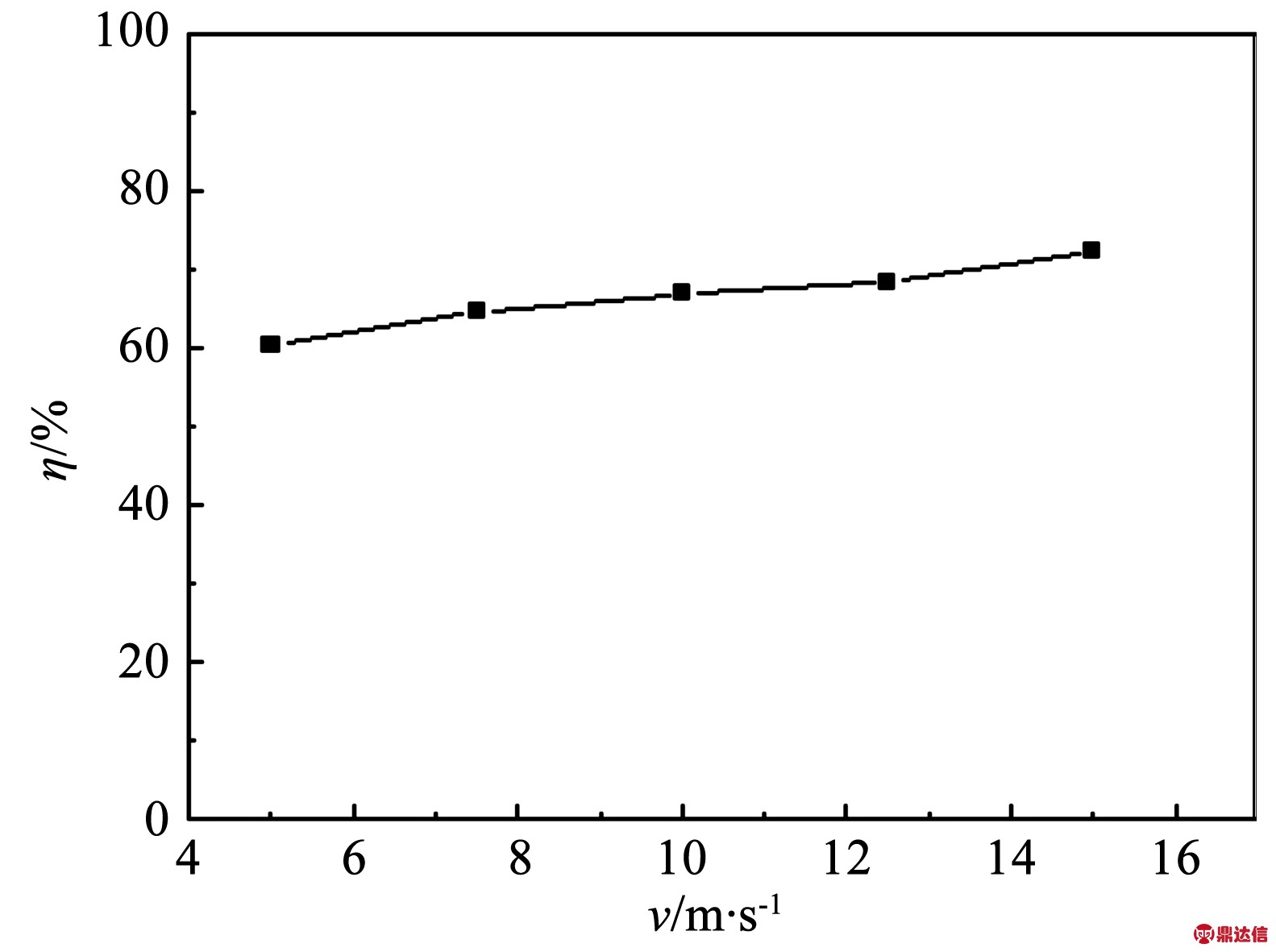
图8 不同入口速度下旋风分离器的分离效率
3.2 入口浓度
为了能够分析入口浓度对旋风分离器分离性能的影响,本节分别选择了5个入口浓度,分别是1、2、4、5和6 g/m3,进气管总流量为0.05 kg/s。不同入口浓度下旋风分离器的分离效率如图9所示,由图9可见:1)旋风分离器的分离效率随着入口浓度的增加而增加,主要原因在于,固体颗粒的浓度增加之后,就会导致其进入旋风分离器的惯性力增大,这样一来,必然会降低湍流紊乱的影响程度,促使更多的颗粒朝着排尘口位置靠近,这无疑有利于分离效率的提高。2)随着入口浓度的逐步增加,旋风分离器分离效率的增长幅度逐渐减小,即便再提高入口速度也不会使其分离效率增加太大,入口浓度达一定值之后,分离效率就基本处于停滞不变的状态,而且固体颗粒浓度过大会加剧颗粒对旋风分离器的磨损程度,并且还会增加动力消耗。由此可见,为了能够提高旋风分离器的分离性能,就需要在一个适宜的入口浓度进行分离操作。
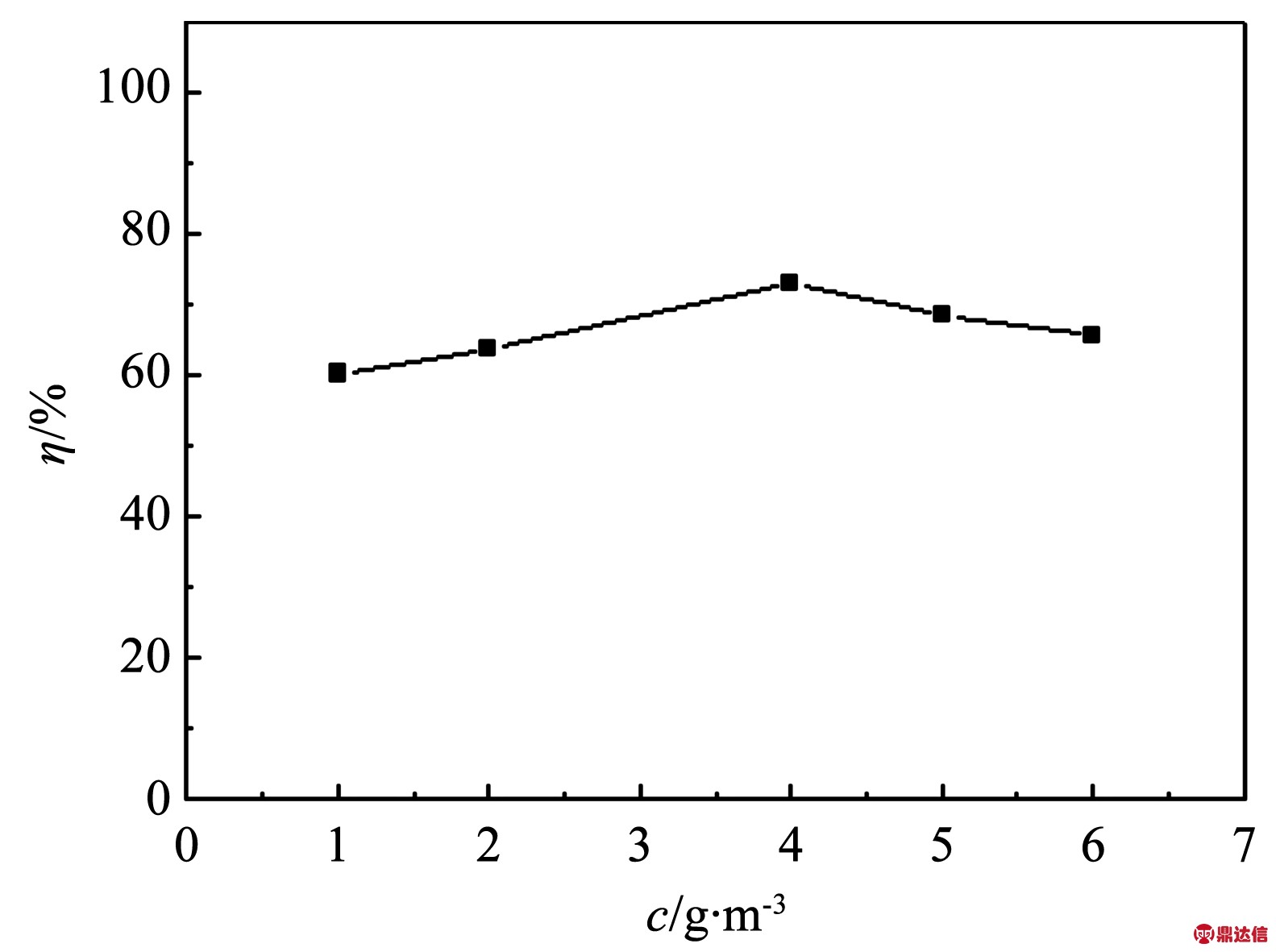
图9 不同入口浓度下旋风分离器的分离效率
4 结语
通过上述研究可以得出如下结论。
1)由上方位置入射到旋风分离器内部的固体颗粒不易分离,由中间位置入射到旋风分离器内部的固体颗粒易于分离。与入口内侧相比,由入口外侧进入到旋风分离器内部的固体颗粒被捕集的几率更高。
2)排气管有大量的固体颗粒逃逸;当粒径增大为6 μm时,经过排气管逃逸的固体颗粒数量大幅度减小;当粒径增大为15 μm时,固体颗粒基本被全部捕集。
3)若固体颗粒的粒径适中,为提高旋风分离器的分离性能,可将入口速度适当增大,且需要在一个适宜的入口浓度进行分离操作。