摘要:为探索厌氧反应器中三相分离器污泥回流缝对分离器内流场及气、液、固三相分离性能的影响,以 Eulerian多相流模型为理论框架,利用计算流体动力学(CFD)技术对厌氧反应器及三相分离器中的气、液、固三相三维流场以及分离效率进行了模拟分析,模拟中采用工程上常用的80、95、110、125、140 mm回流缝宽度。模拟结果表明:三相分离器内部的三相流速大大高于反应器的设计上升流速,其中固相平均流速相对较高;三相分离器内部液相流场以环流为主;污泥回流缝宽度对气、液流动相影响小,对固相影响则相对较大;三相分离器对固相的分离效率较高,混合液经过一层挡板的固相分离率均大于87%,而气相的分离率最低在60%;污泥回流缝宽度越宽、各单层的气、固相分离效率下降,通过三相分离器最上层沉淀区域的补充,混合液中的固相基本上能达到完全分离,而气相在回流缝宽度为95 mm左右时分离效率最高。
关键词:三相分离器 回流缝宽度 多相流 厌氧反应器 模拟
引言
环境保护领域中的厌氧技术把废水处理和能源的回收利用有机地结合在一起,特别适用于低成本污/废水的治理[1-6],在国内外有很大的应用市场和潜力[7-11]。厌氧反应器目前已发展到第3代,其中三相分离器(Three-phase separator,TS)作为厌氧反应器的关键设备[1-6],直接决定着厌氧反应器的效率。因此探索分析三相分离器内部气、液、固的运动状况以及影响因素具有重要的现实意义。鉴于三相分离器结构与工作机理的复杂性,人们对其内部固、液、气三相的实际运动理论和规律知之甚少。目前在设计上通常按照固- 液两相分离的理论进行设计[2,5-6],缺少相应的理论基础,其技术一直掌握在国外公司手中,相关的设计方法和参数鲜有报道[1-6]。国内对TS的研究起始于20世纪90年代,重点在模仿、结构改良分析和性能试验等方面[1-3,5-6],很少涉及到其内部的流场形成和规律等基础理论方面[1-6]。
污泥回流缝(亦称回流口)的确定是TS设计的一个关键问题,过大和过小均会导致TS三相分离效率降低,目前国内按照固-液两相流理论设计,要求混合液的上升流速小于污泥颗粒沉降速度[1-6],按该方法设计的回流缝宽度往往偏小,其计算值一般小于 30 mm(包括 EGSB反应器)[1-6],极易导致堵塞,与实际运行的回流缝宽度差别较大。
随着计算流体动力学(CFD)求解技术在化工反应器领域的成功应用[1-6],越来越多的研究者利用这项技术进行环境领域的反应器研究,从二沉池、澄清池的流态模拟开始[1-6],正逐步深入到带搅拌器的 CSTR类反应器流态模拟研究等方面[1-6,12-18],但目前尚未涉及反应器内的复杂结构问题。本文以国内应用广泛的欧洲专利变形三相分离器为对象,采用CFD技术,在模拟5种典型回流缝宽度下分离器内部固体颗粒、液体和气体的三维运动情况的基础上,分析回流缝宽度对三相分离器分离性能的影响。
1 模拟理论
反应器内混合液在三相分离器内部的流动为固、液和气三相的混合流动,其描述方程分为以流体为主的Eulerian-Eulerian Multiphase Model和强调颗粒运 动 的 Particle Transport(Lagrangian Particle Tracking)Model两类[13-18],由于反应器混合液中固、气颗粒和质量较小,所以模拟模型选择以连续流为基础的 Eulerian-Eulerian Multiphase Model中的Inhomogeneous Model连续流体模型[6,18]。基于单项液体流动的N- S方程,考虑各相的相互特性和相互作用关系,包括动量方程(Momentum equations)、连续性方程(Continuity equations)、相体积守恒方程(Volume conservation equations)、压 力 控 制 方 程(Pressure constraint)、总 能 量 方 程 (Total energy equation/Thermal energy equation)[19]。各方程表述如下:
动量方程

式中 α、β——流体的连续相和分散相
rα——多相流中α相所占的体积分数,%
ρα——α相的密度,kg/m3
Uα——α相的速度矢量,m/s
Uβ——β相的速度矢量,m/s
——哈密顿算子
⊗——两向量的向量积运算
pα——α相的静压强,Pa
μα——α相的动力粘度,Pa·s
Np——流体的相数
——由相之间质量传递引起的动量传递,其中符号Γ表示散度
SMa——流体外部体积力引起的动量源相
Mα——其他相对α相产生的作用力连续性方程

式中 SMSα——自定义的质量源
Γαβ——单位体积的 β相流向 α相的质量流量,kg/(m3·s)

总能量方程

式中 eα——α相的内能,J
λα——α相的热传导率,W/(m·K)
τα——α相的剪切应力,Pa
SEα——内部热源
Qα——流体内其他相向α相的传热率,W/s
——由其他相向 α相质量传递引起的热量传递速率,W/s
气泡和污泥颗粒作为分散相在流体中的运动采用颗粒模型(Particle model)来模拟,假设两种颗粒(以β表示)均为球形,在连续流体α中受到流体对其的多种作用力

式中 Mαβ——合力
——拖拽力
——浮力
——壁面润滑力
——虚质量力
——紊流扩散力
——颗粒间的碰撞力
反应器内的混合液虽流速较低,但在流经具有复杂结构的三相分离器时仍会产生紊流。本文采用应用较广的k-ε(液)和 Dispersed Phase Zero Equation(气、固)模型[13-18]:
k- ε紊流模型
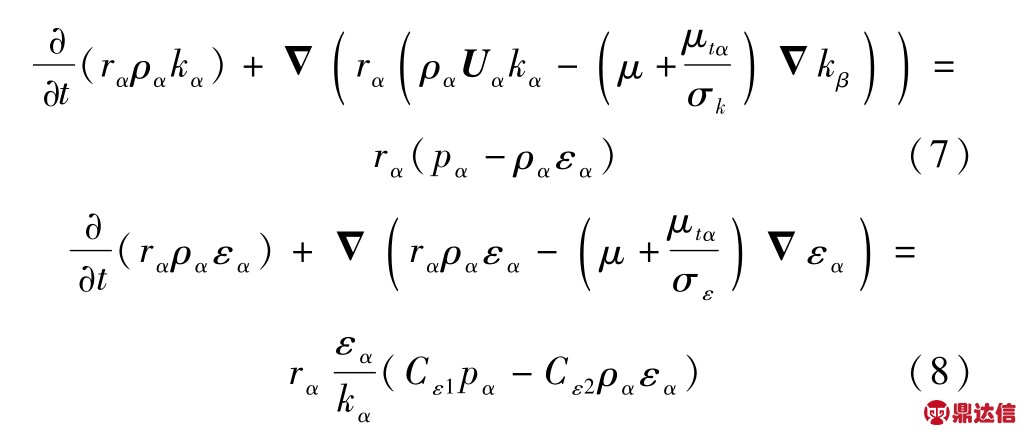
式中 k——单位质量流体的紊流动能,J/kg
ε——流体的紊流耗散率,W/m3
μtα——α相的紊流粘度,Pa·s
Cε1、Cε2——常数,分别取 1.44、1.92
Dispersed Phase Zero Equation稳流模型

式中 μt——气、固颗粒的紊流粘度,Pa·s
σ——紊流的 Prandtl数
下标d表示分散颗粒状态,c表示连续体状态。
模拟中涉及气泡和污泥颗粒的数量和尺寸,模拟开始设定一初始浓度和大小,对应工程上调试的接种量,后续气泡和污泥颗粒的数量按生成和流失确定(模拟期间没有污泥废弃),其中污泥的产生量为[20]

式中 PX,VSS——每天污泥生成量,g/d
Q——流入反应器的水量,m3/d
Y——细胞合成产量,取 0.08 g/g
kd——细胞衰减系数,取 0.03 g/(g·d)
fd——以细胞残骸存留的生物体比率,取0.15 g/g
S0——进水中的可溶 COD,g/m3
S——出水中的可溶 COD,g/m3
TSRT——污泥龄,取 50 d
Qnb VSS——进水中不可降解的 VSS,g/m3
产气按100%为CH4估算:假设与COD的比率为 0.35 L/g[20],产气的浓度分布与污泥的浓度分布一致。
2 模拟
在厌氧反应器中,应用最广的是上流式污泥床(UASB)和厌氧颗粒污泥膨胀床(EGSB)反应器[1-3,5-6]。目前国内工程上使用的三相分离器均是基于欧洲专利和荷兰Paques公司专利基础上进行的变形和改变产品,其典型结构为三层相互交错的人字形挡板,如图1所示。图1为典型 UASB厌氧反应器单元,底部为布水系统,反应器下部为生化反应部分,上部为三相分离器。假设原水均匀进入反应器,顶部出水(反应器池体超高部分略),人字形单板底部三角区域内排气(气体收集系统略)。模拟单元结构尺寸为 1 200 mm(长)×1 000 mm(宽)×5 000 mm(高)。实际结构以基本单元为基础,在长度和宽度方向上扩展,这样的选取既可综合考虑流经三相分离器固、气的浓度发展与分布,又可控制模拟模型的计算量。
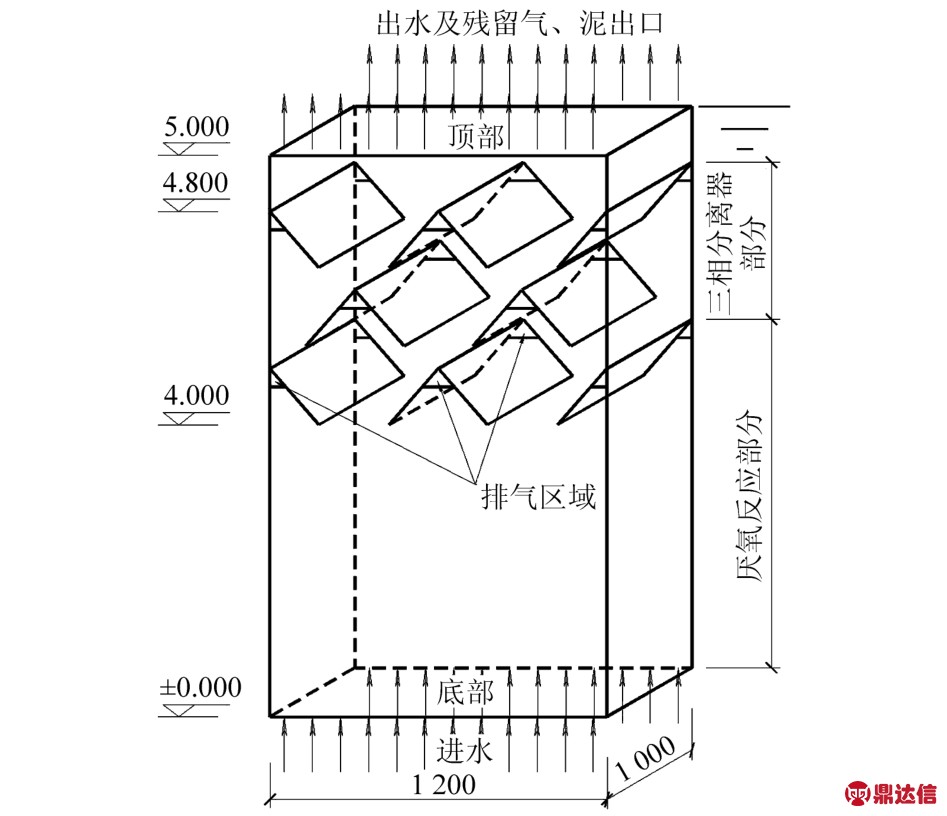
图1 厌氧反应器模拟单元
Fig.1 Schematic view of UASB unit simulation
模拟模型的网格划分采用非结构化四面体网格,三相分离器部分网格较密,最大长度35 mm,下部厌氧反应器部分较疏,最大长度100 mm,网格总数在276万~281万之间(5个几何模型),3项指标(Orthog.Angle、Exp.Factor、Aspect Ration,软件自带)的优良率分别为:78%、90%、100%。
模拟采用 Ansys CFX®14.0进行,反应器上升流速取1.0m/h,采用5个几何模型模拟5种回流缝宽度(80、95、110、125、140 mm)对三相分离器气、液、固分离效果和内部流态的影响(上下两层分离挡板的投影重叠度不变)。模拟的部分初始条件、参数取值、模型选取见表1。
3 结果及讨论
模拟计算在工作站上进行,主要结果见表2、3和图2~4,理论模拟预测值与实际现场试验结果对比见文献[12]。表2为在5种污泥回流缝宽度下,UASB反应器内部(下部)固、液、气三相的总体运动特征。从表中可以看出,实际的各相平均流速远大于设计的上升流速(1 m/h),其中液相的平均速度比设计上升流速高2个数量级,液相与气相流速接近,气相稍高于液相;5种情况下,固相的平均流速最高,为其他两相的2~3倍;污泥回流缝宽度对UASB反应器总体的三相流速影响不大,回流缝变大时,固相的平均流速升高,对气、液两相流动相来说,呈现中间高、两边低的情况;反应器中,气、液两相的流速分布不均衡,表现为其最大值比平均值高一个数量级(10倍左右),相比之下,固相流速分布较为均匀。
表3所示为5种污泥回流缝宽度下三相分离器内部的流场统计及分离效果,仍然是气相平均流速略高且与液相接近,固相平均流速最高,比气、液两相高出一个数量级。在三相分离器内部,流动相的平均速度比设计上升流速要高出2个数量级。由于分离器挡板对流动的阻碍作用,1~2层挡板之间区域的平均流速要明显高于2~3层挡板之间的区域,回流缝宽度不同,速度差异也不同,总体上表现为回流缝宽度越窄,差异越明显。
5种回流缝宽度对三相的平均流速有一定的影响,表现为对气、液流动相影响小,对固相影响大的特点。增大回流缝宽度时,固相平均流速变大,而后基本维持在某一水平上。该结构特点的分离器对固相的分离效率较高,模拟结果显示:各种回流缝宽度情况下,经过1层挡板后(到达第2层回流缝时)的固相分离率均大于87%,多为90%以上,而在相同条件下,气相的分离率最低在60%,经过两层分离器挡板后,固相分离率大于95%,气相分离率大于89%(气相的分离率与上下两层挡板之间的重叠率关系较大,本文的重叠率设定为50%)。
表1 模拟的部分初始条件、参数取值及设置
Tab.1 Som e initial cond ition,param eters and settings of sim u lation
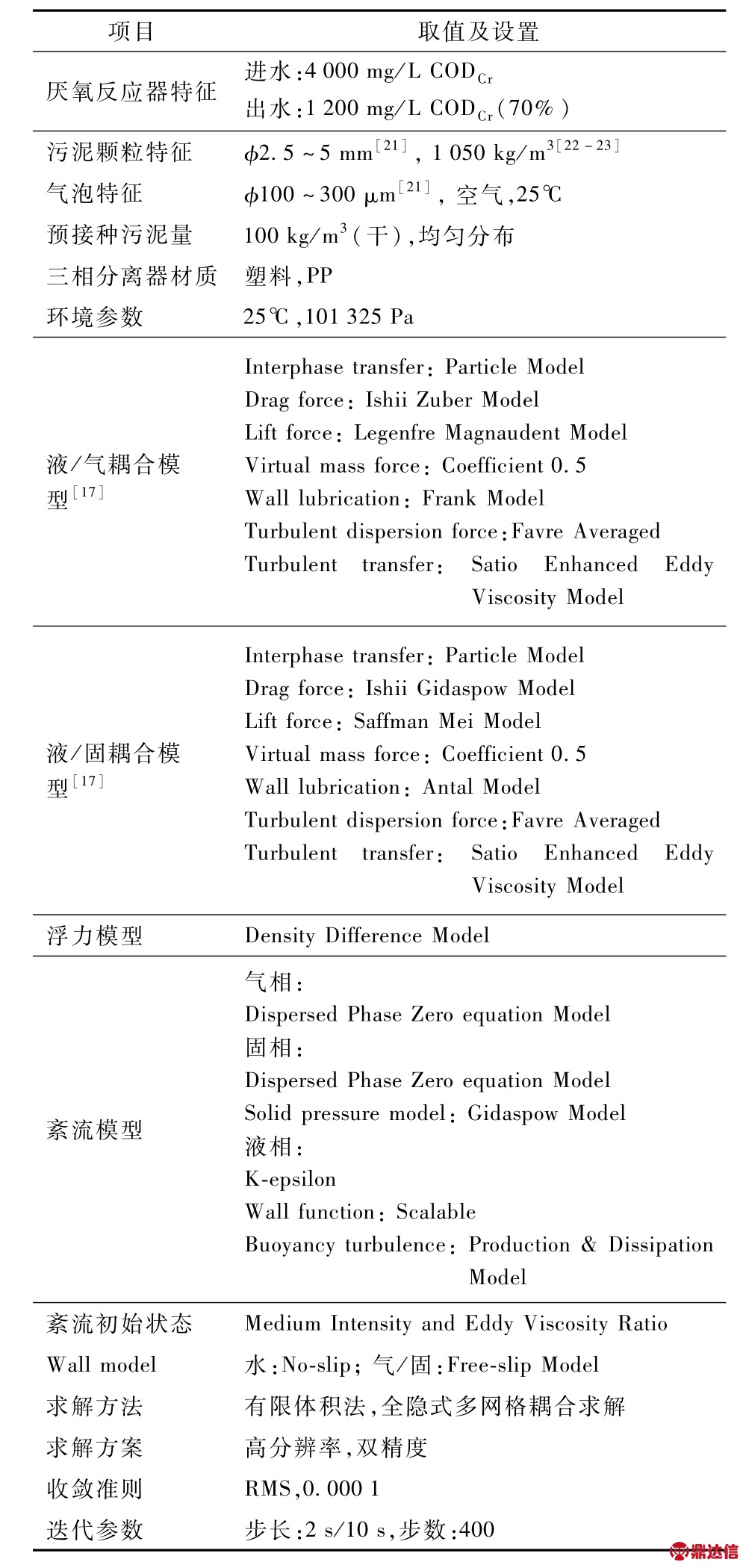
表2 一些UASB反应器模拟总体特征结果(流速)
Tab.2 General characteristic results of the UASB sim u lation m/s

注:流速数据中的“最大”表示垂直向上的速度分量。
表3 一些三相分离器内部模拟特征结果
Tab.3 Averaged internal characteristic results of the TS sim ulation
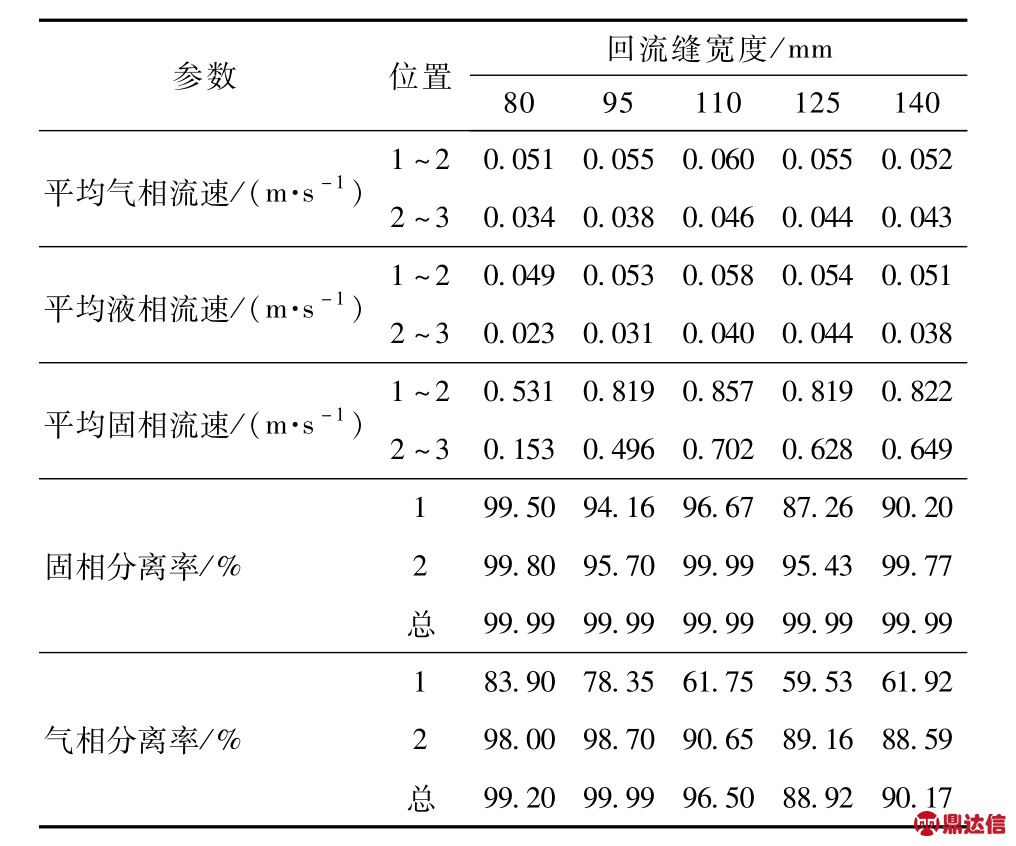
注:位置中“1~2”和“2~3”指位于三相分离器第1层和第2层挡板之间、第2层和第3层挡板之间的区域;位置中“1”、“2”和“总”指混合液经过一层分离器挡板(到达第2层回流缝时)、2层和出水界面处;气固相的分离率指其产生率被分离的质量比率,通过顶部逸出固、气相的质量流量计算。
污泥回流缝宽度对分离率的影响比较复杂,在本例的5种宽度下,总体上呈现回流缝宽度越宽、各单层的气、固相分离效率下降的情况,但对固相的影响不如对气相的影响明显。通过三相分离器最上层沉淀区域的设计补充,混合液中的固相基本上能达到完全分离,说明按固-液两相设计三相分离器回流有一定的可行性,但上层沉淀区对气相的分离作用不大。在污泥回流缝宽度在95 mm时,三相分离器表现出最高的气相分离效率,其可能的原因是:较窄的回流缝有利于气相高效分离,但会造成部分气相流速过高而逸散,而较宽的回流缝则直接允许一部分气流自由通过。
图2为气相在三相分离器(污泥回流缝宽度为95 mm)部分的运动迹线模拟情况(平面图,截面为三相分离器的中纵截面),顶部为反应器出口,下部为三相分离器。可以看到气相在三相分离器内部以上向流为主,流线比较规则和规律,其在挡板部分流速较下部有明显提高(一条流线上两个箭头之间的距离对应流速的大小),并紊流加剧,绝大部分气相在两层挡板顶部的气相收集排出区域溢出,极少部分高速气体越过挡板随反应器出水溢出而损失。由此可见,分离器在设计时通过优化下部两层气相收集以及排空结构可获得更好的气相分离效果。
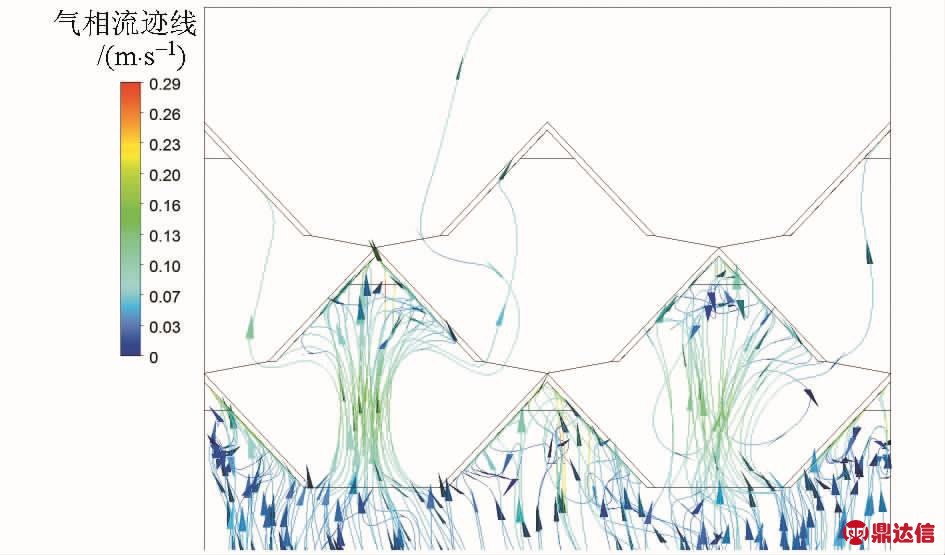
图2 三相分离器部分的气相流迹线模拟(回流缝宽度95 mm,中纵截面)
Fig.2 Gas velocity stream line simulation of TS
图3所示为液相在三相分离器部分的运动迹线模拟情况,与气相相比,流动以紊流为主,特别是在角形挡板下部的区域,呈现十分明显且剧烈的环流运动,液相在三相分离器内的运动混乱、不规律,虽然强烈的环流和紊乱有利于减少死区的存在,但与推流反应器中设计流场相去甚远,需要进一步深入研究。1~2层挡板之间的环流十分明显,而且在气相捕集区域出现较高的气流速度,另外,在三相分离器上部出水区域也出现不规则的紊流现象。流体的紊乱现象是三相之间以及相与挡板之间相互作用的结果,如果在三相分离器底部设置稳流栅,在反应器出水结构上加以调整和改变,则可进一步稳定和规则三相分离器内部的流动。
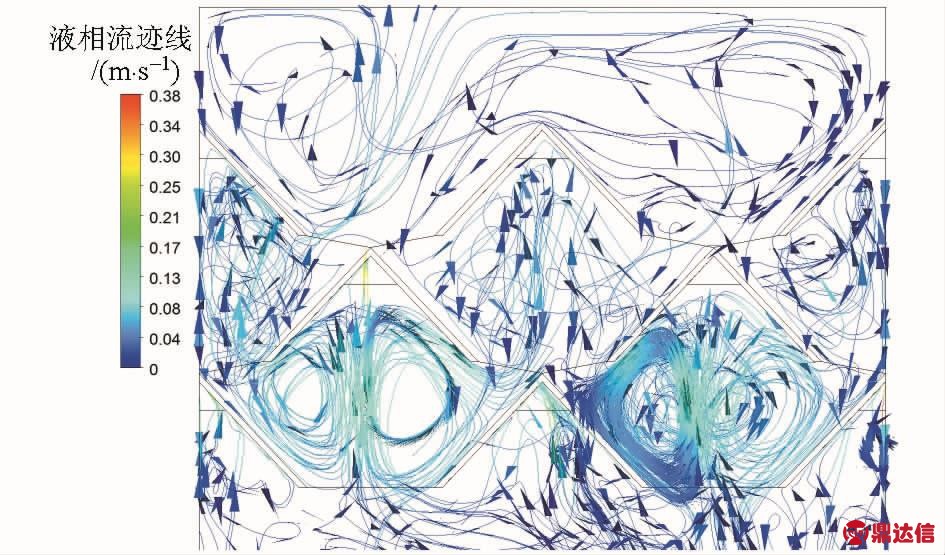
图3 三相分离器部分的液相流迹线模拟(回流缝宽度95 mm,中纵截面)
Fig.3 Liquid velocity stream line simulation of TS
相比之下,图4所示固相的流场较简单,以向下沉淀的固体颗粒运动为主,流速变化平缓,在角形挡板下部向上流动的固体颗粒所在区域,液相(图3)向上流动且流速较高,对固相形成夹带,导致一些回流运动,对挡板表面固相颗粒的沉降有所影响。从一个方面说明按沉淀理论设计挡板角度的同时,也要结合气、液相的流动特点。另外,在运动方程的描述上,固体颗粒获得的动力来自于液相和固相的夹带与推动,这在液固相流速相对固相较高且三相基本同向流动时可能比较符合,但从本例固相流线轨迹来看,固相基本以向下沉降的运动为主,与气相的上向流动不同,同时,文中采用的1.0 m/h液相设计上升流速并不是导致反应器内理想的液流均匀上升流态,模拟结果显示为较无规律的杂乱流动。
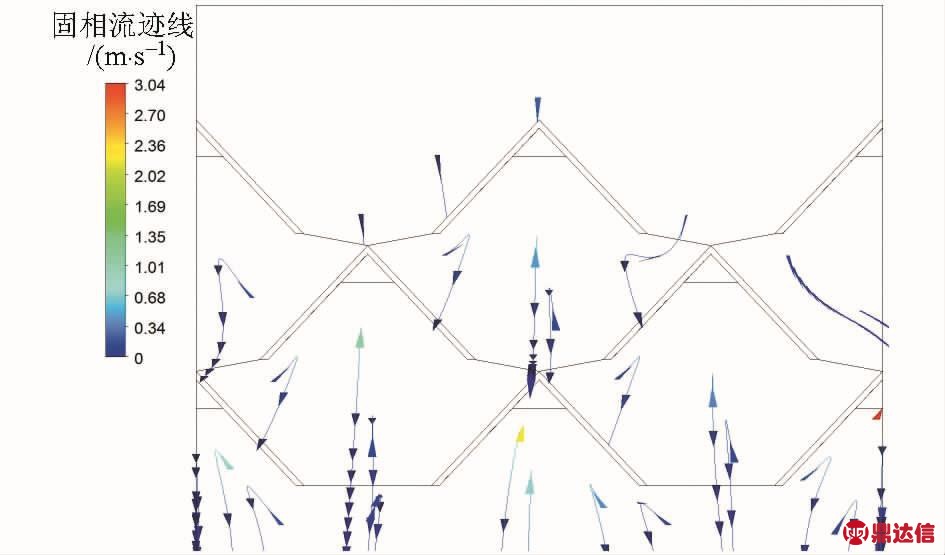
图4 三相分离器部分的固相流迹线模拟(回流缝宽度95 mm,中纵截面)
Fig.4 Solid velocity stream line simulation of TS
4 结论
(1)三相分离器内部的三相流速大大高于反应器的设计上升流速,其中气、液两流动相平均流速接近,固相平均流速相对较高。在5种回流缝宽度情况下,固相比气、液两相平均流速高1个数量级。三相分离器内部流场不规则、较为混乱,尤其是液相,以环流为主,与理想的推流反应器设计气流差异大,需要进一步研究。
(2)5种污泥回流缝宽度对三相分离器内各相平均流速的影响不大,1~2层挡板之间区域的平均流速要高于2~3层挡板之间的区域。回流缝宽度不同,速度差异也不同,总体上表现为回流缝宽度越窄,差异越明显,在2倍左右。回流缝宽度对气、液流动相影响小,对固相影响相对较大,增大回流缝宽度时,固相平均流速变大,而后基本维持在某一水平。
(3)三相分离器对固相的分离效率较高,本例的5种回流缝宽度情况下经过首层挡板的固相分离率均大于87%,多为90%以上,而相同条件下,气相的分离率最低在60%,经过两层分离器挡板后,固相分离率大于95%,气相分离率大于89%;污泥回流缝宽度越宽,各单层的气、固相分离效率下降,但对固相影响不如对气相的影响明显,通过三相分离器最上层沉淀区域的设计补充,混合液中的固相基本上可完全分离,而气相在回流缝宽度为95 mm左右时分离效率最高。