摘 要:叶片式分离器是一种较新颖的气液两相流设备的入口分离及布气装置。为了给设计提供指导,本文采用离散相模型对其中的气液两相流动过程进行模拟,并通过分离效率测试对计算模型进行了验证;在此基础上研究了气速、液滴粒径、叶片倾角及流道入口宽度对分离性能的影响。结果表明:叶片式分离器具有良好的气液分离性能,对于粒径大于50μm的液滴分离效率能够达到85%以上,增大气速和液滴粒径有利于提高叶片式入口装置的分离效率;综合考虑分离效率和压降,叶片倾角宜设置为5~8°;在现有流道宽度设计建议的范围内,减小流道宽度可显著提高小液滴分离效率,但阻力也将增加。
关键词:气液分离;叶片式分离器;气液两相流;分离性能;数值模拟
气液两相流设备广泛见诸于石油、化工等过程工业领域,为有利于设备内部气液两相的操作过程,通常都需要设置入口装置以实现气液预分离或气体均匀分布[1,2]。叶片式分离器作为一种较新颖的入口装置,原理上具有良好的分离性能和布气性能,在气液分离器、传质分离塔等设备中得到越来越广泛的应用[3,4]。目前,叶片式入口装置的研究多集中于塔器布气方面[5-7],如李旭光等人[8,9]通过实验和数值模拟的方法研究了填料塔中叶片结构参数对布气性能的影响,进而优化结构。相对来说,叶片式入口装置的气液分离性能及其与影响因素的关系研究甚少,Qaroot等人[10]使用离散相模型(DPM)对设置有叶片式入口装置及多种强化元件的分离器整体进行模拟,研究表明,叶片式入口装置能够有效的将小液滴聚并成大液滴促进分离;Kharoua等人[11]通过模拟发现用叶片式入口装置代替原先碰撞式入口装置,能够有效改善分离效果。鉴于此,本文采用计算流体动力学方法模拟了叶片式入口分离器内的气液两相流动过程,并通过气液分离实验验证了数值模拟方法的有效性,在此基础上,进一步研究了气液操作条件以及结构参数对分离性能的影响,为叶片式入口分离器结构设计提供理论指导。
1 数值模拟
1.1 几何模型与网格划分
为了切合实际,选用某油气田所用三相分离器中的7流道叶片式入口装置作为模拟对象,其结构图1。
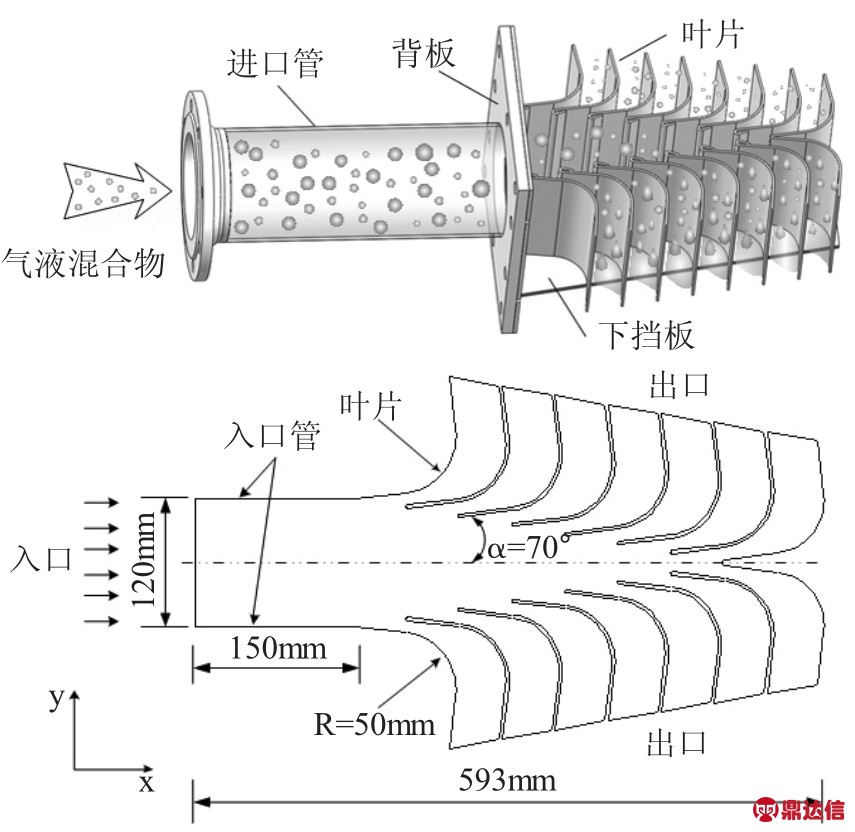
图1 叶片式入口分离器结构及几何模型
Fig.1 Structure and geometry model of vane inlet separator
由于在流道中旋流作用强,液滴受到的曳力远大于重力的影响,而且叶片流道不同高度的截面相同,其高度远大于流道宽度,因此本文不考虑重力的影响,将问题简化成二维流场进行后续的模拟计算。二维计算模型见图1,入口直径为d=120mm,入口管长150mm,入口装置每列分别由7个流道组成,叶片由两个长度为50mm的直边段和半径为R=50mm、夹角为90°的圆弧段组成,叶片倾角α=7°。为了使网格更加贴合叶片弯曲的流道,本模型采用非结构化四边形网格,并在叶片附近加密网格,叶片附近局部网格见图2。
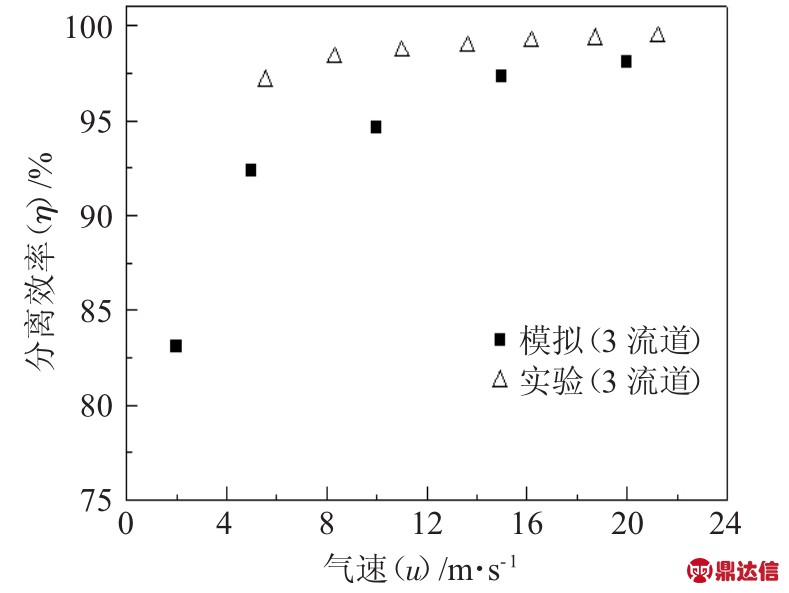
图2 叶片附近局部网格
Fig.2 Mesh near vane
1.2 计算模型及方法
经过大量的研究表明,离散相(液相)体积分数小于10%时,采用DPM模型能够很好地追踪液滴在连续相中的流动,模拟气液分离过程[12,13]。本文为研究气液分离过程中液滴的分离行为,选择使用DPM模型,并采用随机轨道模型对离散颗粒湍流运动进行计算。先计算连续相流场至收敛后,加入离散相进行耦合计算。对于连续相,选择能较好地处理旋转流动、流动分离和二次流的Realizable k-ε湍流模型,并对近壁面采用标准壁面函数处理[14]。通过对拉式坐标下的颗粒作用力微分方程积分求解运动轨迹:

其中FD(u-up)为颗粒的单位质量曳力。

式中 u、up分别是气相和液滴的速度;ρ,ρp分别是气相和液滴的密度;μ:液滴动力粘度;dp:液滴粒径;Re:液滴的相对雷诺数;CD:曳力系数;Fx:其他附加力。
由于整个过程压力变化不大,将气相视为不可压流体来处理。选用压力基求解器,压力速度耦合方法采用PISO算法,压力插值采用Standard格式,动量方程、湍动能方程和湍流耗散率方程均选用精度较高的二阶离散格式,时间选用一阶隐式离散格式求解,各方程的收敛残差设置为1×10-5,时间步长取 1×10-3s。
1.3 边界条件
模拟介质选用常温下的水和空气,空气为连续相,离散相水以液滴的形式注入连续相中。对于连续相,入口采用速度入口边界条件,出口采用压力出口边界条件,并将出口压力设置为大气压。对于离散相,进口采用面注射,使液滴均匀分布在进口截面上,速度与连续相相同。进口和出口对液滴均设置为逃逸(escape),叶片壁面设置为捕集(trap)。
在本文中离散相液滴入口条件考虑了均一和非均一粒径两种情况,均一粒径便于考察其他参数影响,而非均一粒径更接近现实工况,研究表明,Rosin-Rammler粒径分布符合现实工况的粒径分布[12,15]:

式中 Yd:粒径大于d的液滴所占的质量分数,选取J sang等人 [16]气液分离实验测得粒径参数,即d=60μm,dmin=20μm,dmax=140μm,分布系数 n=2.25。
1.4 网格无关性验证
叶片式入口装置的分离效率是指通过叶片捕集的液滴质量与进入入口装置总的液滴质量之比,可以通过监测进出口液滴质量来计算,如式(4)[12]:

式中 η:分离效率;m:入口液滴质量,kg;m1:叶片捕获液滴质量,kg;m2:出口液滴质量,kg。
为确定合适的网格数量,分别划分了4不同数量的网格,计算结果见表1。
表1 不同数量网格计算结果比较(u=2m/s,dp=40μm)
Tab.1 Results dependent on different number of grid
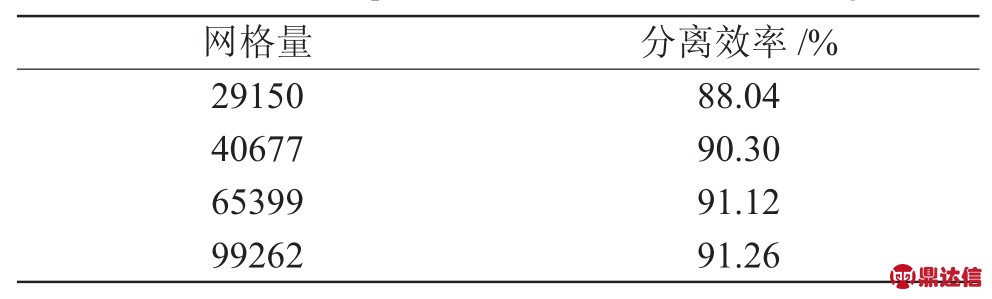
可以看出,当网格数量由65399增加到99262,分离效率仅变化0.15%,此时可认为计算结果与网格数量无关,因此,选择数量为65399网格进行后续的计算。
2 实验部分
由于通过实验单独测量叶片式入口装置的分离效率存在一定困难,本文通过测量仅设有叶片式入口装置的气液分离器的整体分离效率,验证数值计算模型。实验在一个长宽高尺寸为1500mm×305mm×350mm的气液分离器中进行,入口装置采用3流道叶片式入口装置,入口直径为d=25mm,叶片由两个长度为30mm的直边段和半径为R=30mm、夹角为90°的圆弧段组成,叶片倾角α=7°。分离器和入口装置均采用有机玻璃制造,图3为实验流程图。
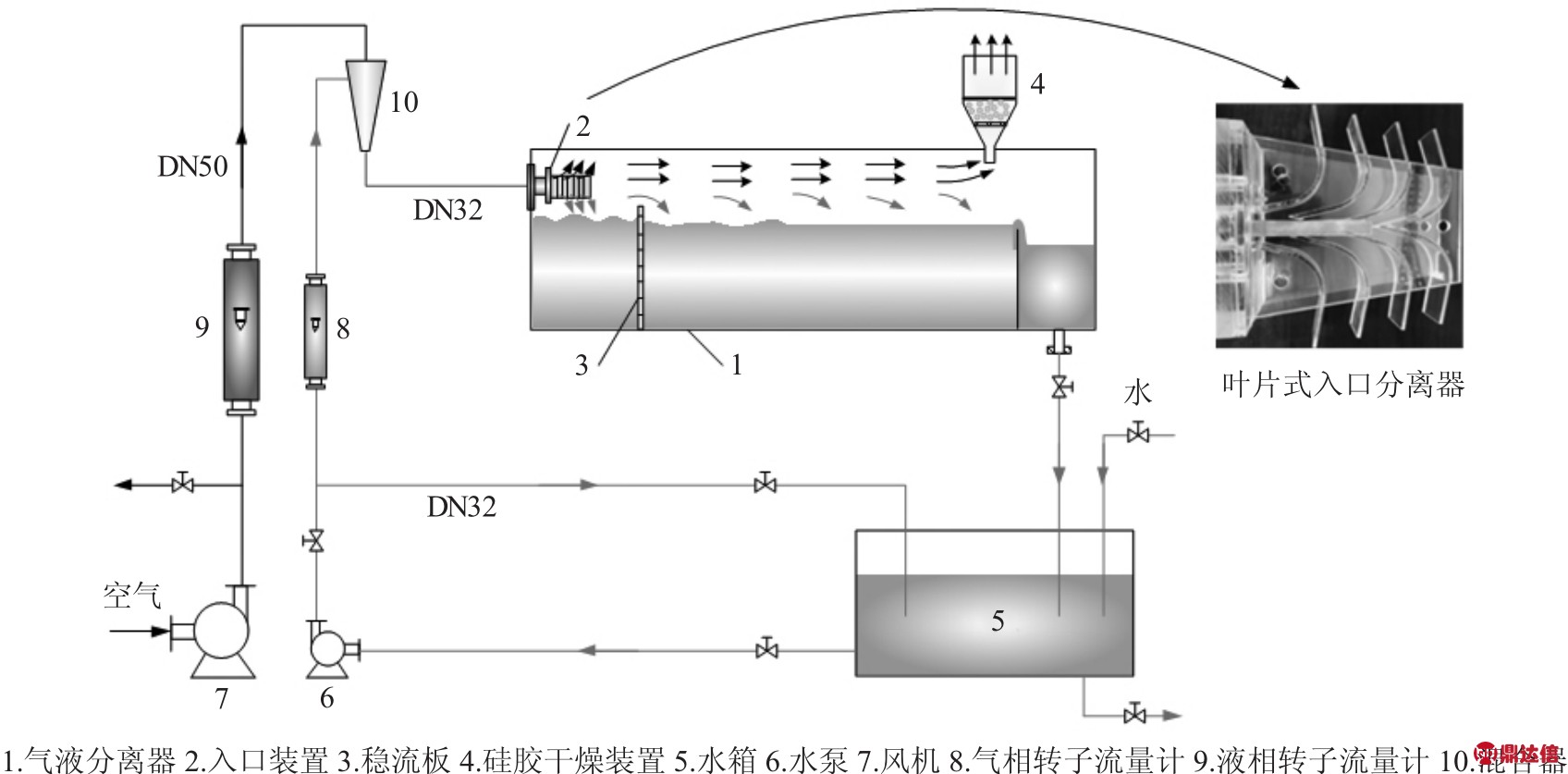
图3 气水分离实验流程图
Fig.3 Flow scheme of gas-liquid separation experiment
采用空气-水体系,空气和水通过混合器混合后通过入口装置进行预分离,然后通过分离器沉降段后,分别从水相、气相出口流出。在气相出口设置硅胶干燥装置来收集气相中夹带的液滴,通过称重法测量干燥硅胶的实验前后的增重量,进而计算分离器整体分离效率:

式中 η:分离效率;Δm:硅胶吸水量,kg;Δt:测试时间,s;m&:入口处夹带在气相中的水相质量流量,kg·s-1。
根据工程实际设计了本实验工艺参数,保持水相体积流量为400L·h-1不变,通过改变气量进行实验,共设定了 7 组气相流量,分别为 10,15,20,25,30,35,40 Nm3·h-1,对应的进料速度为5.9~22.9m·s-1。
3 结果与讨论
3.1 模型有效性验证
为了验证模拟有效性,根据实验中使用的叶片式入口装置原型重新建立3流道叶片入口装置计算模型,并按照上述模拟方法进行模拟计算。由于单独测量叶片式入口装置的分离效率有一定难度,这里将模拟结果与分离器整体分离效率进行比较,如图4。
实验得到的整体分离效率包含叶片式入口装置的分离效率与后续沉降段的沉降分离效率,所以模拟结果要低于实验结果。随着气速增加,液滴停留时间缩短,沉降段分离作用弱,两者差值也在逐渐缩小,符合物理规律,因此,模拟结果具有较高的可靠性。后续采用同种模拟策略对7流道叶片式入口装置进行模拟计算,进一步研究气液操作条件与结构参数对分离性能的影响。
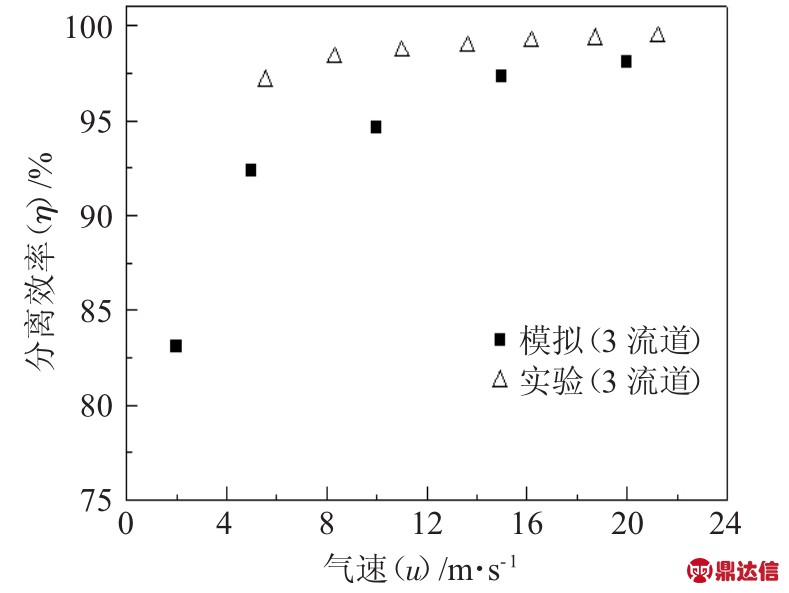
图4 实验结果与模拟结果对比
Fig.4 Comparison of experimental results and simulation results
3.2 气速u对分离性能的影响
入口液滴采用Rosin-Rammler粒径分布,在不同进气速度下进行模拟计算,得到叶片式入口装置分离性能随气速的变化见图5。
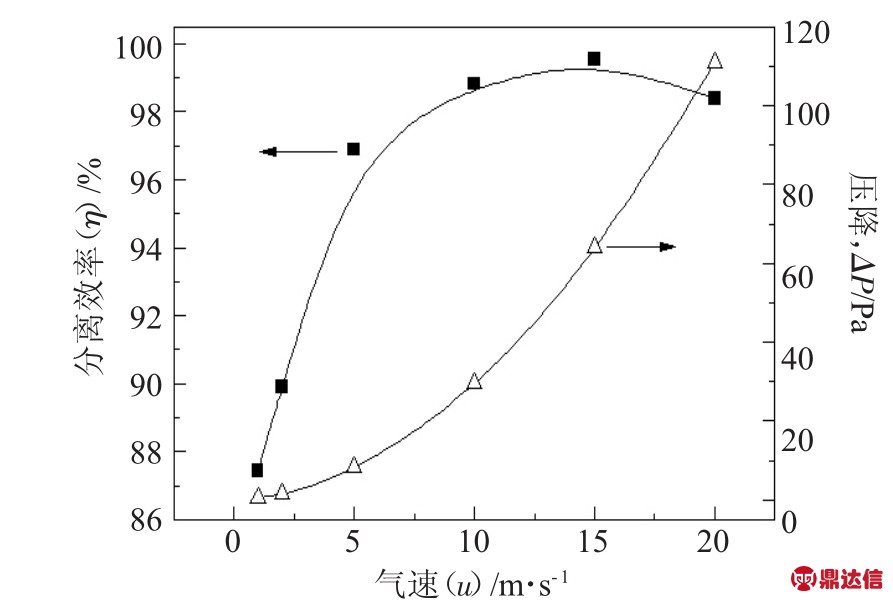
图5 进气速度对分离性能的影响
Fig.5 Effect of velocity on separation performance
可以看出,分离效率均在85%以上,并且随着气速增加,分离效率也在不断增加。因为液滴受到的惯性离心力和质量、速度有关,当气速增加时,液滴受到的惯性离心力也相应增加[17],因此,液滴在叶片流道中流动时更容易偏向叶片壁面被捕集。
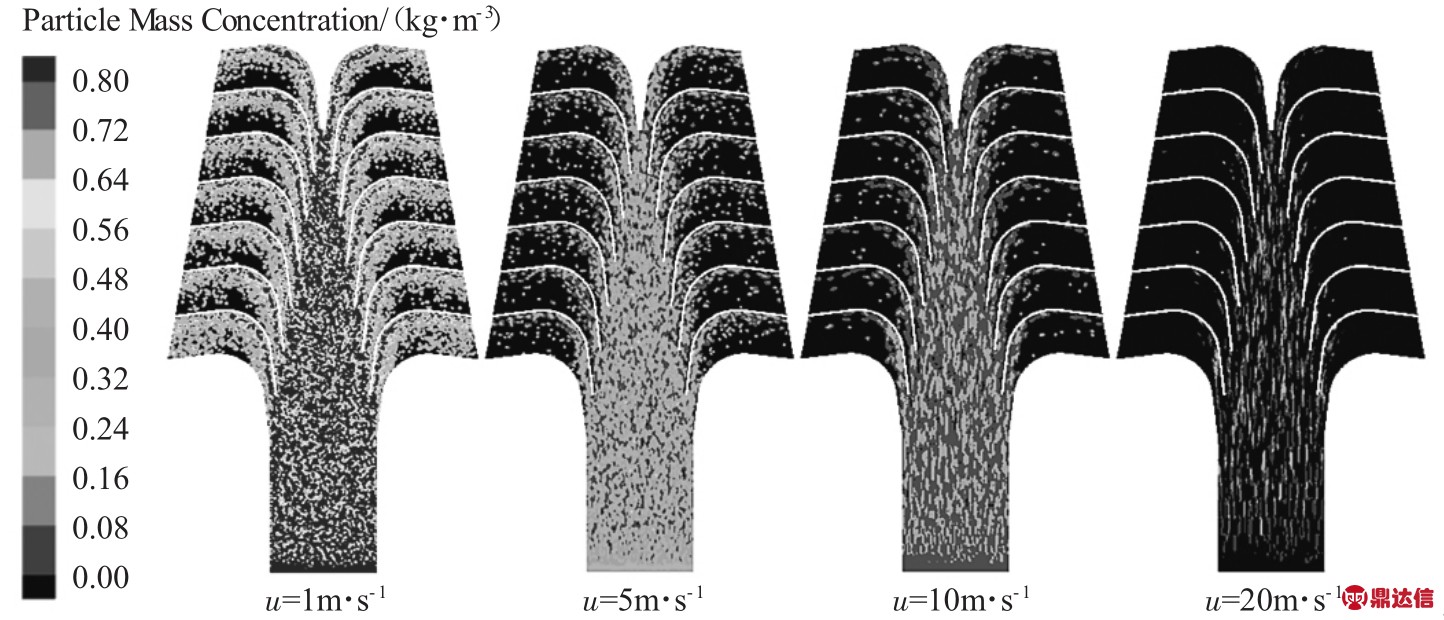
图6 不同速度下液滴浓度图
Fig.6 Particle mass concentration of different velocities
从图6液滴浓度分布图可知,随着气速增加,越来越多的液滴在叶片圆弧段就被捕集分离,剩下一些粒径较小、跟随性较好的液滴从叶片流道逃逸。但是速度对于分离效率的影响大小也视液滴粒径而定。
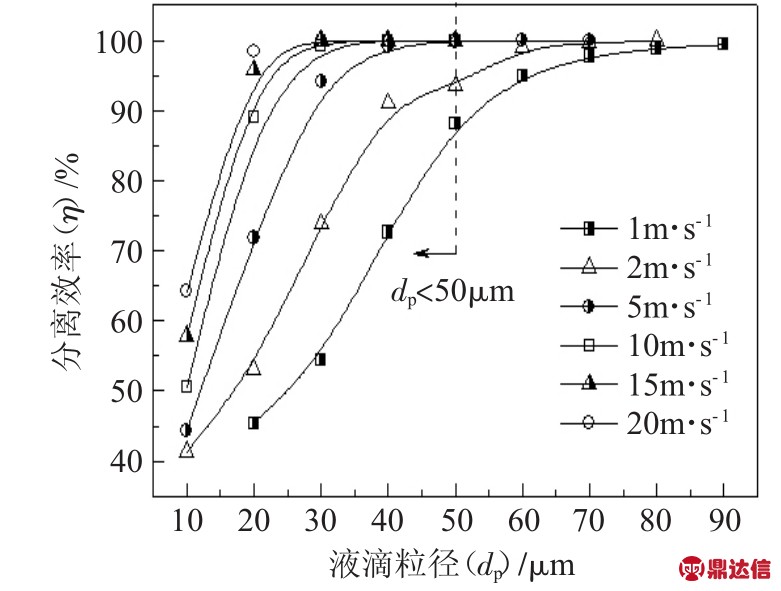
图7 液滴粒径对分离效率的影响
Fig.7 Effect of droplet diameter on separation efficiency
从图7可以看出,粒径小于50μm的液滴对气速较为敏感,增加气速时,效率有极大的提升。另一方面,在气速增加时,气流在叶片流道内的湍流扰动越强烈,进出口压降也随之增大(图5)。因此,在实际工况中,应结合压降与效率综合考虑,设计合适的进气速度。
3.3 液滴粒径dp对分离性能的影响
图7为不同进气速度下液滴粒径与分离效率的关系曲线图,可以看出对于粒径大于50μm的液滴分离效率能够达到85%以上,并且随着液滴粒径增大,分离效率总体上呈上升趋势,增速由大到缓。因为随着液滴粒径增大,受到的惯性离心力越大,跟随性随之变差,难以跟随气流沿着叶片流道流动,从而脱离气流撞击叶片壁面被捕集分离。
由上述分析可知,叶片式入口装置的分离原理如图8所示。
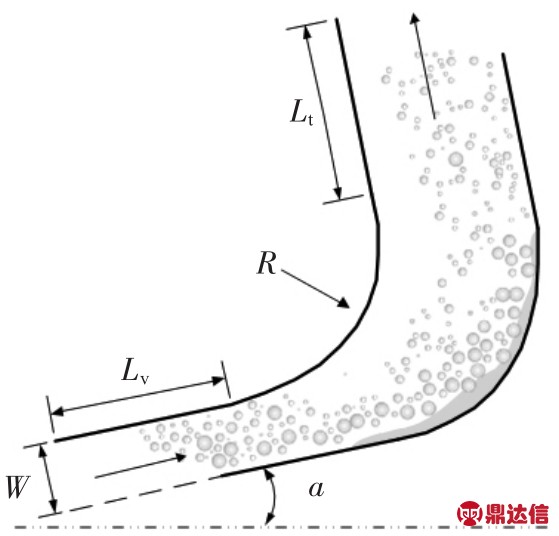
图8 叶片流道结构及工作原理
Fig.8 Structure and separation principle of vane passage
当气体携带液滴在叶片流道中流动时,由于流动方向和流通截面的不断变化,而液滴的惯性比气体的大,气体很容易改变方向,而液滴由于惯性大保持原来的运动方向,从而与气流分离并撞向叶片壁面被捕集[18]。后续撞击叶片壁面的液滴与前诉液滴聚并融合,从而在叶片壁面上形成液膜,然后通过重力作用沿着叶片壁面向下沉降分离。增大气速或者粒径都会使液滴受到的惯性离心力增大,从而导致分离效率增加。
3.4 叶片倾角α对分离性能的影响
由叶片流道结构图8可知,叶片倾角α即为叶片直边段与水平中心线夹角。图9为速度为5m·s-1,不同叶片倾角下分离效率图。
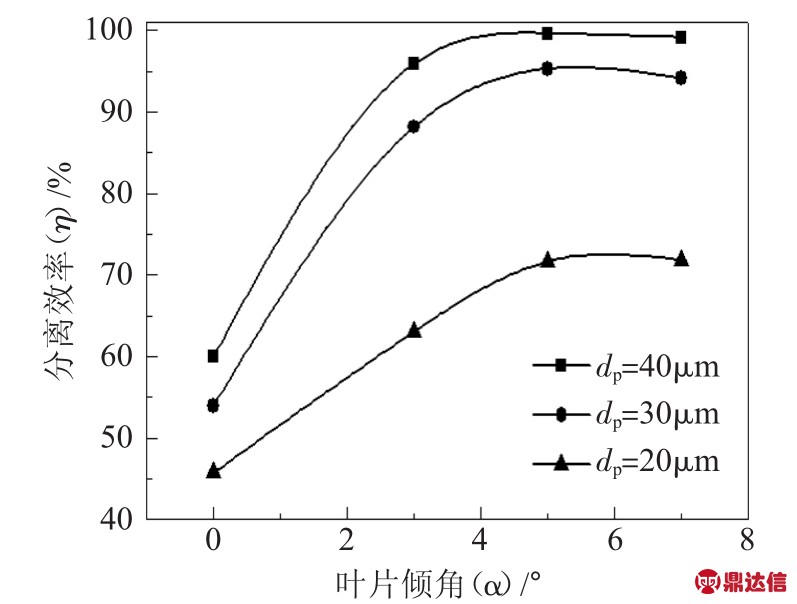
图9 叶片倾角对分离效率的影响
Fig.9 Effect of vane angle on separation efficiency
由图9可见,对于入口液滴粒径为20、30、40μm,均表现出相同的规律:随着叶片倾角增大,分离效率开始呈现出逐步上升的趋势,然后趋于平缓。这是因为当叶片倾角不断增大时,气流在叶片流道中流动时流动方向改变得越大,那么液滴就更容易在惯性离心力的作用下冲向叶片壁面被捕集分离,从而导致分离效率增大。但是随着倾角进一步增大,气流在叶片流道内受到湍流扰动也越发强烈,因此,气流会将叶片壁面粘附的液滴再次卷入气流中,最终在两者的作用下,分离效率不再继续增加。
叶片倾角对压降的影响曲线见图10。
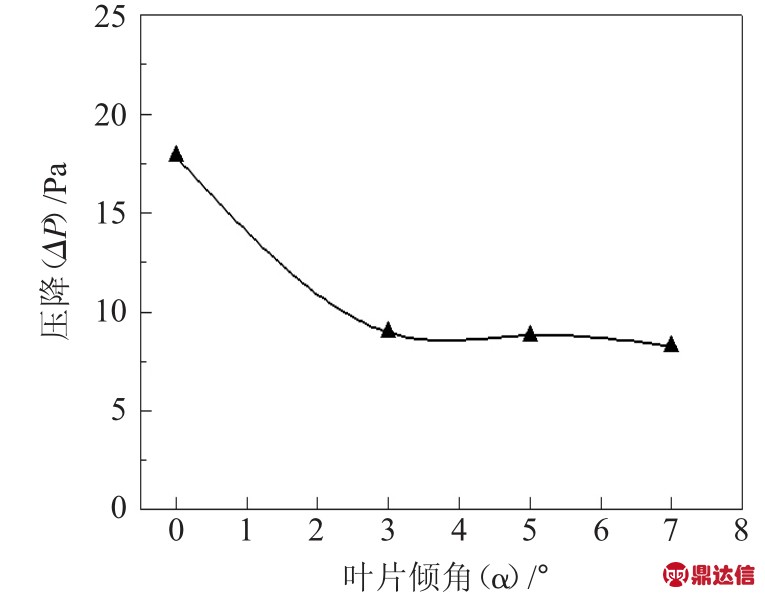
图10 叶片倾角对压降的影响
Fig.10 Effect of vane angle on pressure drop
由图10可见,叶片倾角从0°增大到7°的过程中,开始下降一小段后,其后基本保持不变。随着倾角增大,一方面流动方向变化越大,流体撞击叶片越强烈,导致压降增大;另一方面叶片流道在靠近中心主体流动一侧的开口(入口宽度)增大,流体在流道中流动速度减缓,导致压降减小,由于倾角整体变化很小,后者对压降的作用大于前者,从而导致了图10的变化趋势。因此,综合考虑分离效率与压降两个评价指标,在设计叶片式入口装置结构时,叶片倾角设置在5~8°性能最优。
3.5 叶片流道入口宽度W对分离性能的影响
由结构图8可知,叶片流道宽度W控制着流体在流道中的流速,因此,确定合适的叶片流道宽度对提高分离效率尤为重要。入口装置总长一定时,通过改变流道数量,进而改变叶片流道入口宽度。本文模拟了流道宽度为11.6、14.0、17.4及22.6mm 4种情况,5m·s-1气速下,分离效率随叶片流道入口宽度变化曲线见图11。
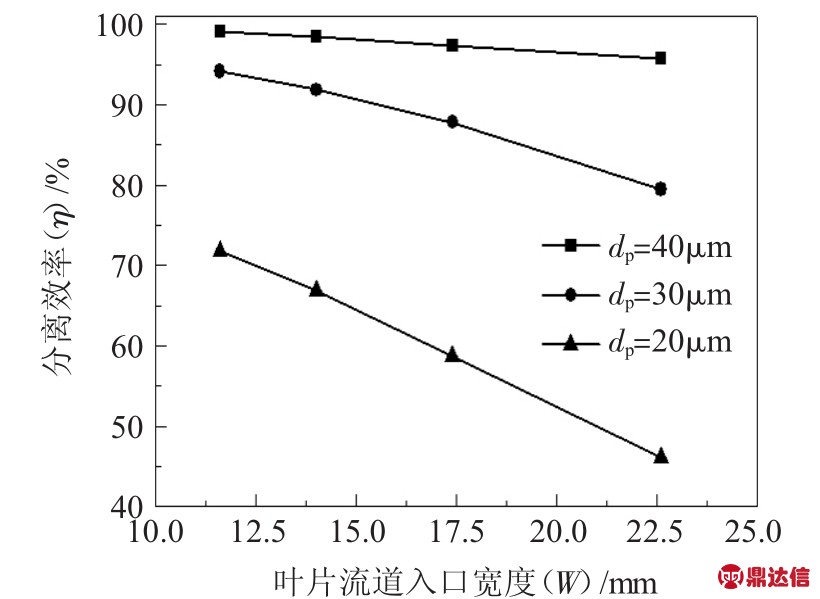
图11 叶片流道入口宽度对分离效率的影响
Fig.11 Effect of width of vane passage on separation efficiency
由图11可以看出,当叶片流道入口宽度减小时,分离效率也在不断增大,有逐渐趋于平缓的趋势,而且粒径越小的液滴效率增幅越大。因为随着叶片流道的宽度不断减小,气流速度增大,液滴受到的惯性离心力就越大,就越容易碰撞叶片壁面被捕集,与此同时增加流道数也为液滴提供了更多的附着面,因此液滴碰撞叶片壁面的机率就越大,所以分离效率不断增加。但是,随着流道宽度减小,在流道中气速增加,阻力也会相应增大。因此,在保持入口装置总长不变的情况下,适当减小流道入口宽度,是有利于强化叶片入口装置的分离性能的。
4 结论
本文通过数值模拟的方法研究了叶片式入口分离器内气液两相流动过程,并进一步深入研究了气液操作条件和结构参数对分离性能的影响,主要结论如下:
(1)叶片式入口分离器是通过多个弯曲的叶片流道分散进料流体、改变气流方向和速度,依靠气液两相惯性差进行气液分离,因此,气液操作条件、结构参数对分离效率影响较大。
(2)随着进气速度增大、入口液滴粒径增大,分离效率也不断增加。并且增加气速,能够极大地提高粒径小于50μm液滴的分离效率;粒径偏大(dp≥50μm)的液滴惯性离心力大,更容易被叶片壁面捕集分离,其分离效率在85%以上。
(3)设计叶片式入口分离器结构时,应综合考虑分离效率与压降两个指标,叶片倾角为5~8°时分离性能较好;在现有流道宽度研究范围内,减小流道宽度能够有效地提高叶片式入口装置的分离性能,对分离粒径较小的液滴(dp≤30μm)效果更加明显,但同时阻力也会相应增大。