摘 要:应用数值模拟技术,从气相体积分数、速度大小和总压分布等方面对气液旋流分离器轴向截面流场进行分析。通过对4个不同截面的数值分析,将溢流管气相出口作为气相分离的通道,流场分布较稳定,各因素波动较为平缓。分析结果显示,筒体和锥部中各因素变化趋势较为明显;尤其是筒体部分,内外旋流交错,与器壁发生激烈碰撞,大量动能被消耗,速度迅速下降。
关键词:气液旋流分离器; 数值模拟; 流场
旋流分离器在工业生产中的应用相当普遍,因其操作简便、经济实用的优点而受到诸多青睐。虽然旋流分离器结构简单,但其内部的流场分布非常复杂,直接影响到最终的分离效果。对于内部流场的分析,单纯依靠实验研究难以完成,需耗费大量的人力、物力和时间成本。数值模拟技术具有经济省时的优越性,则很好地弥补了此缺陷;同时,通过数值模拟可全面分析旋流分离器内部流场的分布情况,有助于旋流分离器分离性能提高研究[1-7]。
1 模型的建立
应用Fluent软件进行模拟计算,所采用的气液旋流分离器结构如图1所示。气液旋流分离器的尺寸大小、计算模型及边界条件等参照文献[8]进行设计。各计算参数的残差值数量级设置为10-3,迭代计算进行到2 000步收敛。
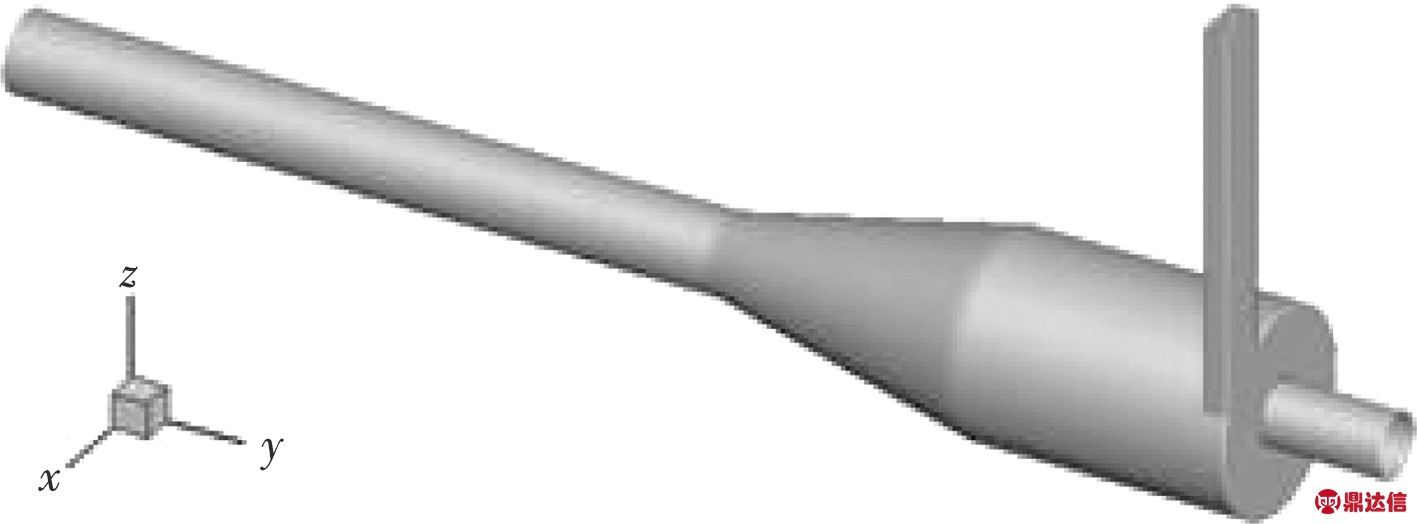
图1 气液旋流分离器结构示意图
2 内部流场分析
为了更好地展现气液旋流分离器的内部流场情况,除了分析整体轴向截面流场情况之外,还在旋流分离器轴向截面沿y轴方向自上而下截取了4个截面, 分别对其气相体积分数、速度大小和总压分布进行分析。这4个截面所处的位置,分别表示为y=25 mm,y=-16 mm,y=-50 mm,y=-90 mm。
2.1 气相体积分布
观察气液旋流分离器轴向截面的气相分布云图(见图2),可明显看出,气液旋流分离器的气相体积分数在经过分离之后,大体沿中心轴线对称分布;同时,气相体积分布由溢流管向下逐渐减小。图标上颜色的深浅对应表示所在区域的气相体积分数:颜色深,表示气相体积分数越大;颜色浅,表示气相体积分数小。其中,作为旋流分离主要场所的圆柱形筒体,气相体积分数较大,气相物质含量整体较高。
经过筒体到达锥部这一段,随着旋流分离的持续进行,图中深色区域逐渐减退,表明气相物质的含量逐渐下降;最后剩下的液相物质经由锥部下面所连接的底流管分离出去,至此旋流分离操作即完成。溢流管口的气相体积分数为92%左右,表明大部分气相物质是经由溢流管口离开操作体系。
根据气液旋流分离器各截面的气相体积分布(见图3),4个截面上的气相体积分布曲线大致上呈对称分布。
y=25 mm截面位于溢流管的上半部分,由于大部分的气相通过此位置分离出去,因此,截面上的气相体积分数总体保持较高水平。在横向坐标x=3.5 mm 附近,气相体积分数达到峰值。
y=-16 mm截面位于入口管附近,气液两相混合物从这里进入旋流分离器。密度较小的气相往内旋流形成内旋流,而液相则形成外旋流,因此大体上筒体边缘部分的气相体积分数低于中间部分。此处是旋流分离的主要场所,气液两相所形成的旋流在这里交汇分离。
y=-50 mm截面位于圆柱形筒体临近锥部的位置,气液两相在这里继续完成分离。随着旋流分离的不断进行,筒体内部的流场逐渐趋于稳定,绝大部分气相往筒体中间的溢流管位置汇拢并分离出去。
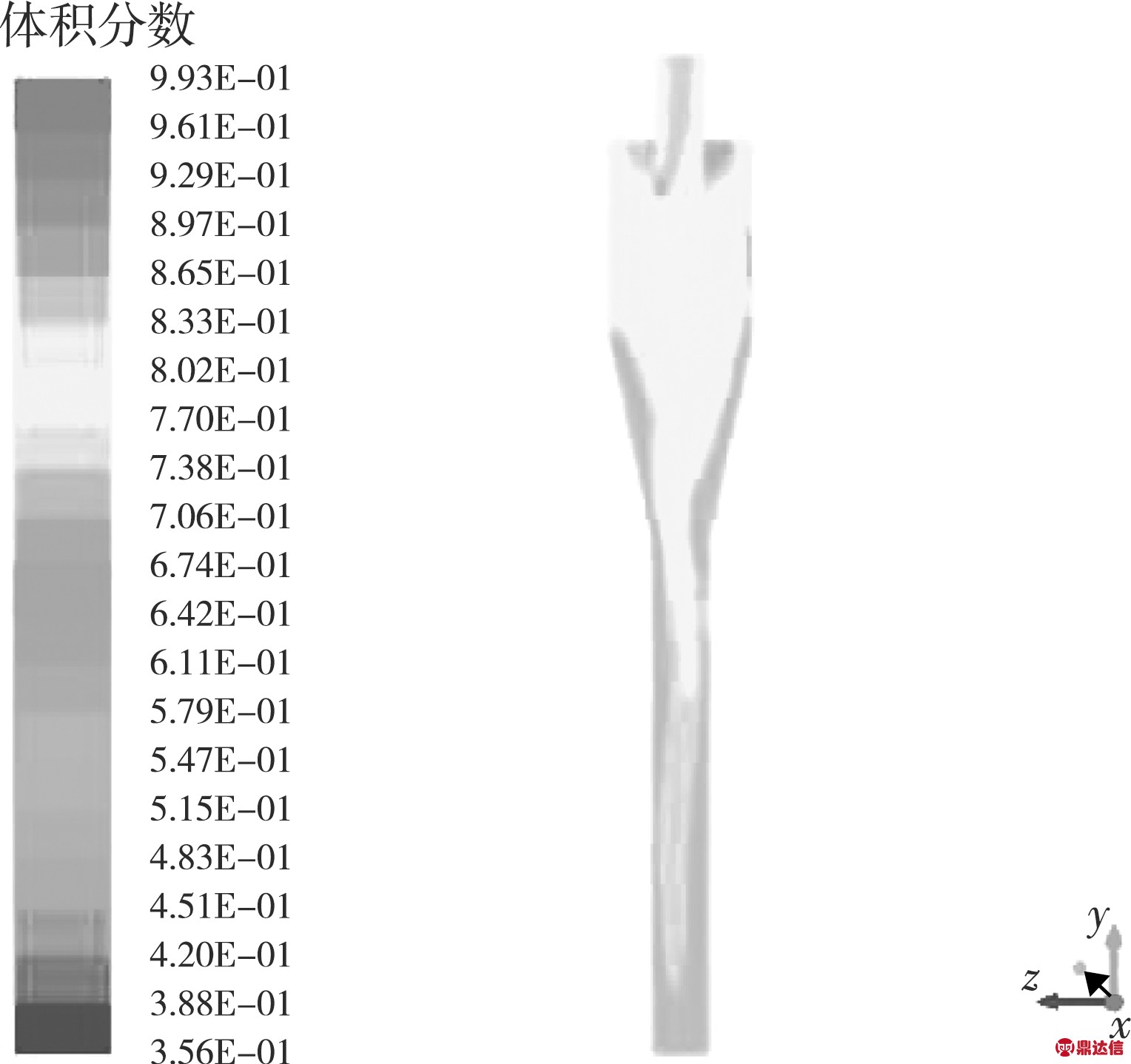
图2 气液旋流分离器轴向截面的气相分布云图
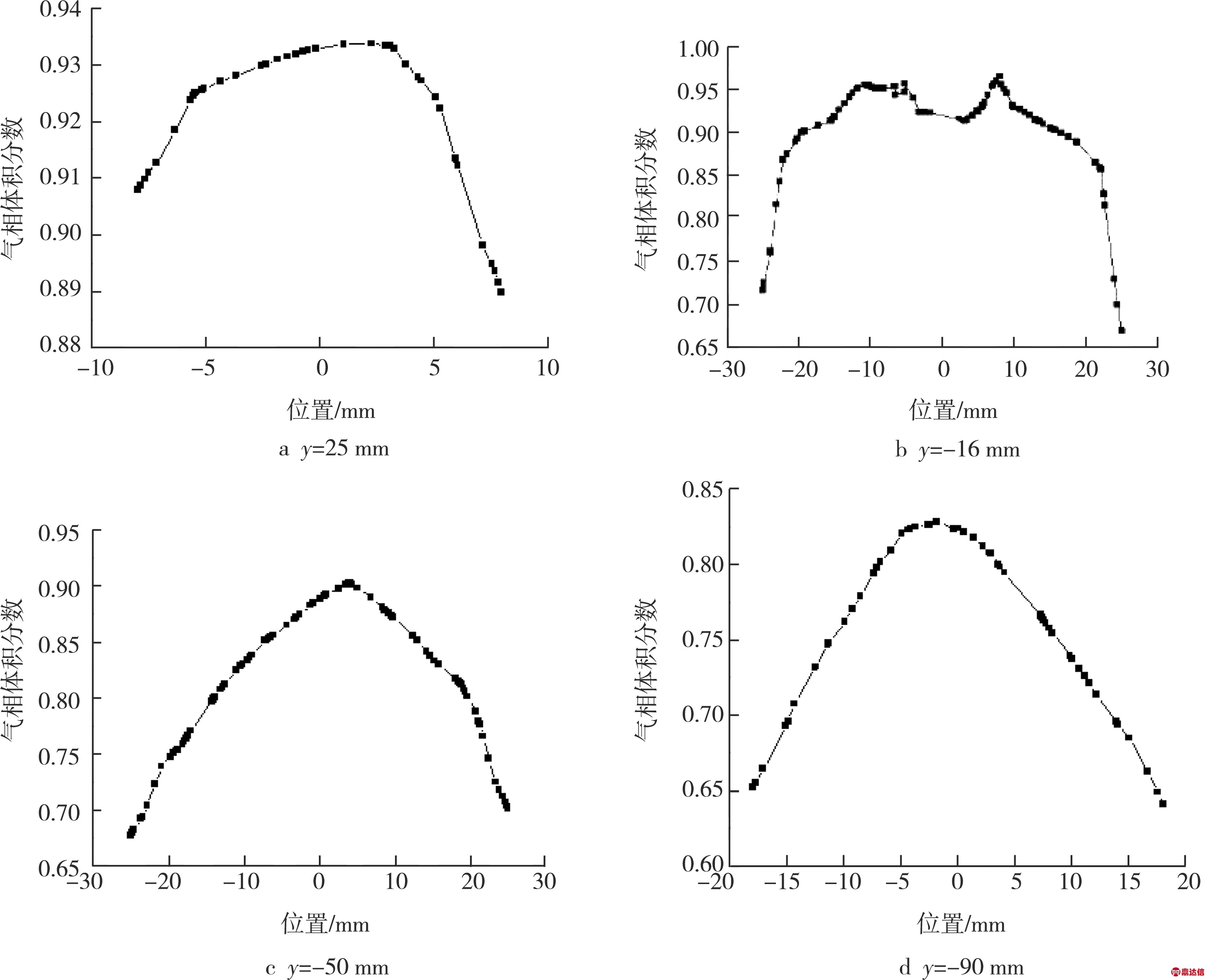
图3 气液旋流分离器各截面的气相体积分布曲线图
y=-90 mm截面靠近锥部的中间部分,经过前面筒体内的旋流分离之后,余下的部分混合物将在这里完成分离。此时,大部分的气相已经通过溢流管离开操作体系。通过曲线图观察可知,气相体积分数的分布具有较好的对称性,截面所处的流场趋于稳定。
2.2 速度分布
图4所示气液旋流分离器轴向截面的速度分布云图,展现了旋流分离器轴向截面的速度分布情况。可以看出,入口管与筒体连接部分处的速度最大。图上,颜色深,表示速度值大;颜色浅,表示速度值小。相对器壁而言,旋流分离器中间段区域的速度值较小,筒体两侧的内壁都各有一个速度较大值的分布区。
两相混合物在离心力的影响下,均以6 ms的速度切向进入分离器中,两者分内外旋流在分离的过程中与筒体和锥部的器壁不断产生摩擦碰撞,使得大部分的动能被损耗,流动速度变慢。因此,气液旋流分离器各截面的速度分布曲线上(见图5),在y=-16 mm和y=-50 mm截面,速度曲线波动程度较大,曲线形状大体呈倒U形分布。此时,截面所在流场变化也较为激烈,湍流强度较大。
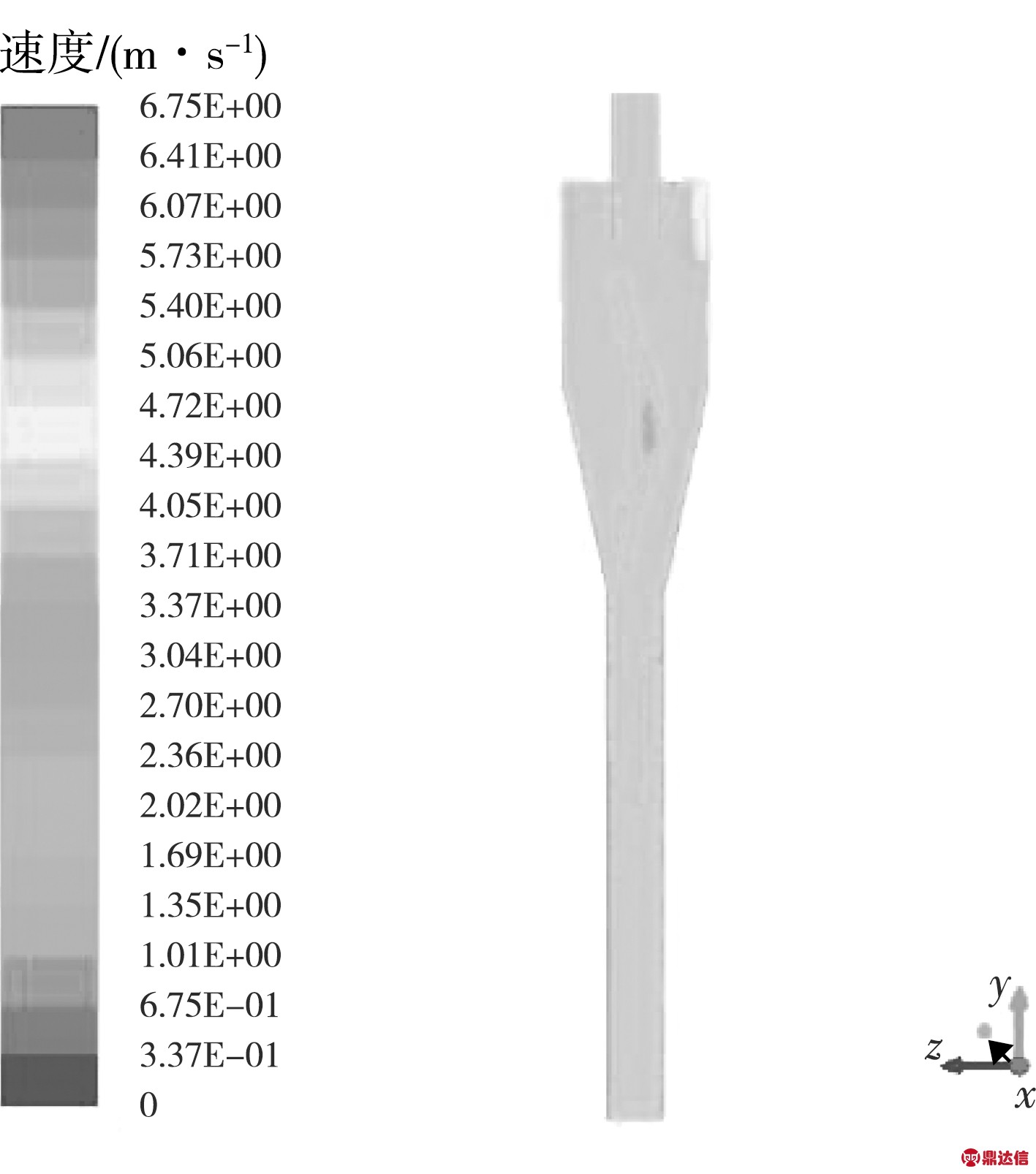
图4 气液旋流分离器轴向截面的速度分布云图
y=25mm截面临近溢流管的气相出口处,经过旋流分离出来的气相借助内旋流的推动,已经从溢流管口离开了操作体系,此时速度的变化不大,并趋向稳定。
y=-16 mm截面正好包括了进口管与筒体的接口以及溢流管深入筒体内部的部分,位置比较特殊。外旋流往器壁方向运动,与器壁的摩擦碰撞程度较严重,所损耗的动能也多,速度曲线两端的变化较为显著。相比之下,内旋流的带动使得大部分气相往溢流管位置靠拢,与器壁的摩擦碰撞程度较轻,所损耗的动能较少,速度曲线中间部分较为平稳,变化较小。
y=-50 mm截面在筒体的下部,没有了溢流管的影响,并且经过上一截面位置的旋流分离,多数气相已被带离分离器,余下的混合物在旋流的过程中与器壁继续发生碰撞,速度继续下降,变化已没有上面的位置明显。
y =-90 mm截面临近锥部的中间部分。此时,大部分气液混合物已通过旋流分离出去,同时也损耗掉了大部分动能;余下的混合物旋流趋缓,速度变化减小。
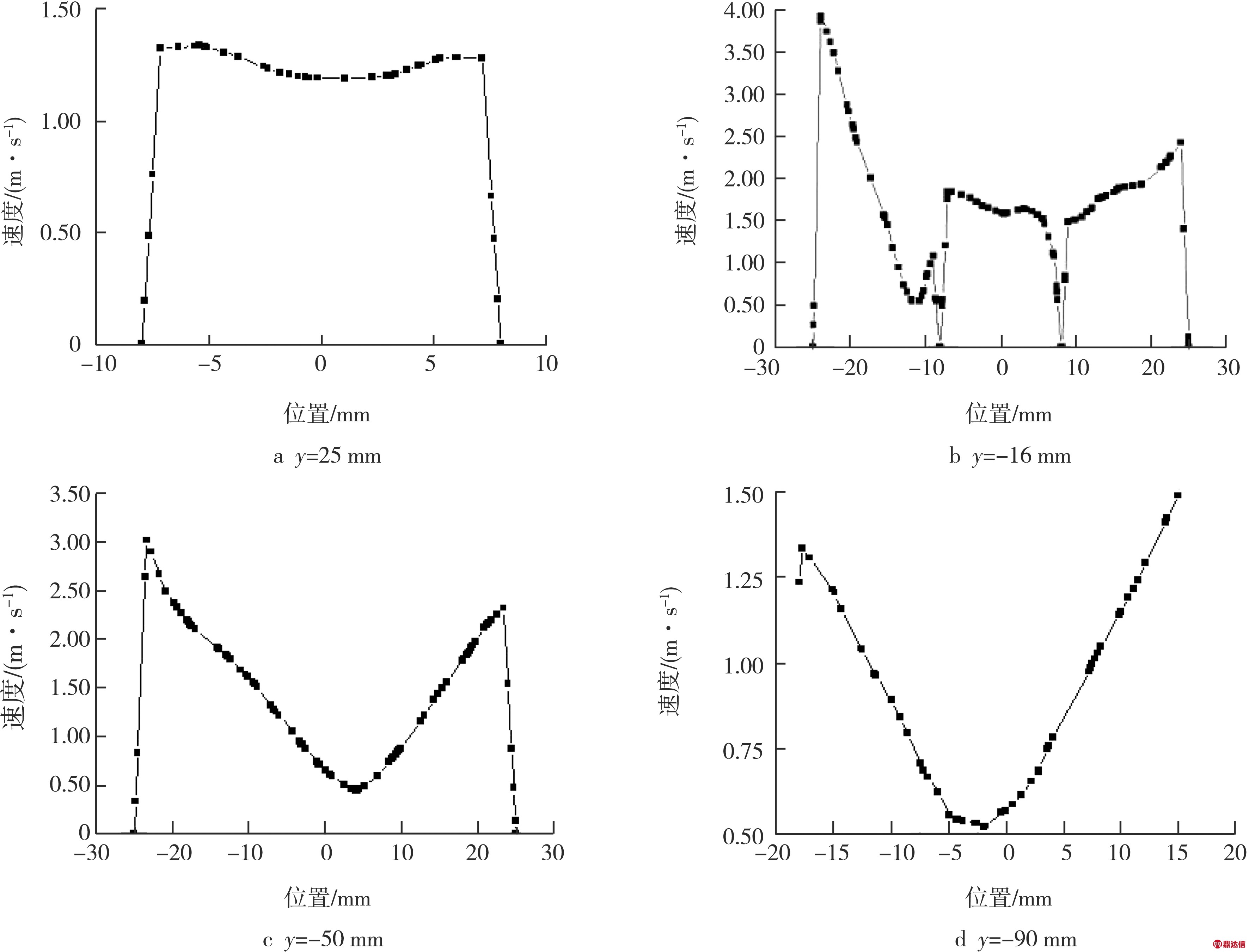
图5 气液旋流分离器各截面的速度分布曲线图
2.3 总压分布
观察气液旋流分离器轴向截面的总压分布云图(见图6),可以看出,分离器内中心区的总压低于壁面处的总压,这主要由旋流产生的离心作用力所引起。
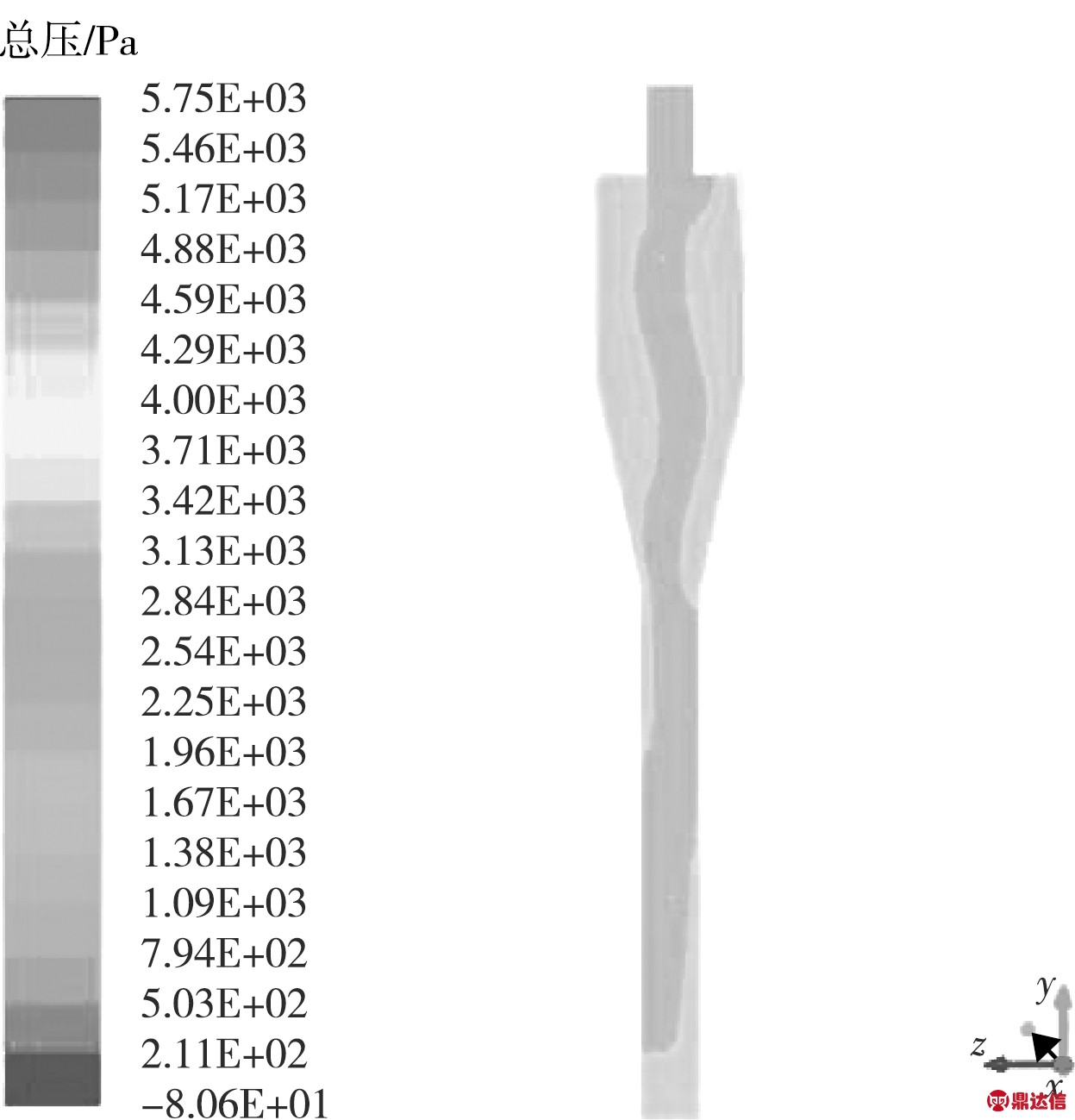
图6 气液旋流分离器轴向截面的总压分布云图
观察气液旋流分离器各截面的总压分布(见图7),可看出内部总压整体上呈对称分布,入口处最大。
在y=25 mm截面,由于靠近溢流管的气相出口处,大部分的气相由此分离出去,导致此处截面相比于其他3个截面,整体总压较低。
在y=-16 mm和y=-50 mm截面,压力震荡程度较明显。外旋流所在的圆柱形筒体和锥部的器壁两侧区域,压力较高;中心内旋流所在区域压力较低,并且整个旋流分离器中心区域的总压均为最低。而且,在y=-16 mm截面,经过旋流分离之后,其溢流管中心处集聚了绝大部分气相,此时压力变化趋于稳定。有少部分液相被内旋流夹带上去,集中在溢流管的外部,因而两侧压力稍高于中间。
在y=-90 mm截面,仍有一部分混合物在进行分离。此时压力震荡幅度减缓,流场波动也没有之前剧烈。大部分液相在这里汇集,并经由锥部下方的底流管分离出去。
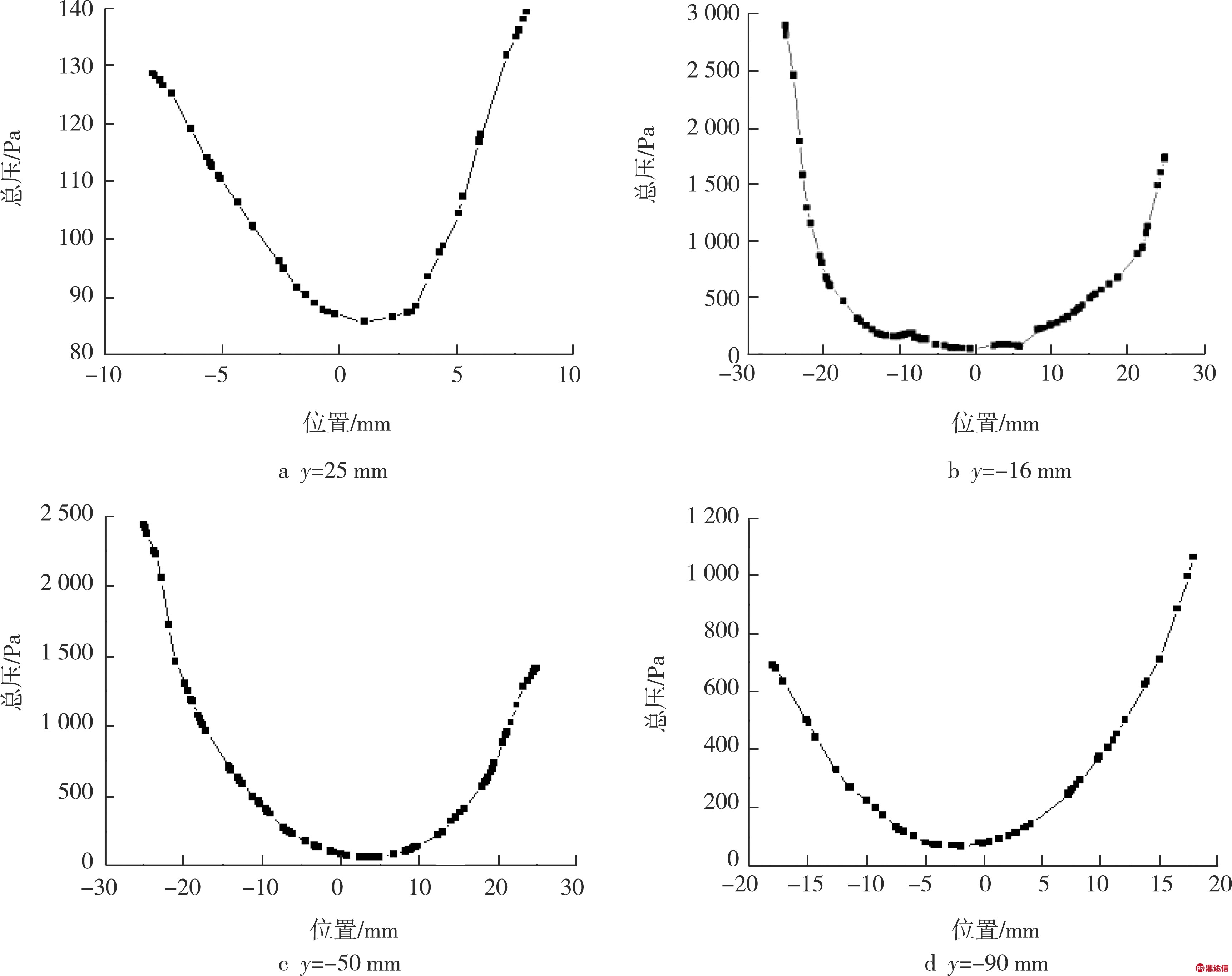
图7 气液旋流分离器各截面的总压分布曲线图
3 结 语
筒体作为主要的旋流区域,气液混合物从入口管切向进入后,筒体与入口管的连接处形成了一个不稳定的流场。此位置的湍流强度较大,压强也大于分离器内部其他部位。由于此时旋流分离尚未充分进行,混合物与器壁的碰撞接触较少,因此出现了速度最大值。
从4个不同截面的曲线图来看,溢流管气相出口处(y=25 mm截面)作为气相分离的通道,流场分布较稳定,各因素的波动较为平缓。筒体(y=-16 mm和y=-50 mm截面)和锥部(y=-90 mm截面)的各因素变化趋势较为明显。尤其是筒体部分,内外旋流在这里交错,与器壁发生激烈的碰撞,混合物的大量动能都被消耗掉,速度迅速下降。