摘 要:针对目前铅酸蓄电池刀切装置通用性差且自动化程度低等问题,设计出一款新型铅酸蓄电池刀切分离器。阐述了刀切分离器的工作原理,分析其结构特点及动作过程,设计液压、气动系统并甄选系统元件,对重要回路进行仿真校核。该装置体积小,自动化程度高,安装在现有铅酸蓄电池回收预处理生产线上,用于多种规格的铅酸蓄电池的切割。
关键词:铅酸蓄电池;液压系统设计;气动系统设计
引言
国内铅酸蓄电池回收预处理工艺中的“逐步分离法”工艺,采用刀切装置将回收的铅酸蓄电池从汇流条根部(极群组与汇流条连接部分)刀切成上盖和下槽体,再通过振动分离以及运输集中等方式,分别对这两部分进行分类回收[1]。
铅酸蓄电池汇流条根部高度不一,导致某一型号刀切装置只能切割一种规格的铅酸蓄电池,需人工送料,劳动强度大,导致无法安装在现有的预处理生产线上[2]。制约 “逐步分离法”工艺推广使用。
为解决上述问题,设计出一款铅酸蓄电池刀切分离器。该装置通过改变刀片高度,刀切多种规格的铅酸蓄电池。采用气动系统以及液压系统实现自动化作业。
1 刀切分离器结构设计
1.1 刀切分离器工作原理
设计的铅酸蓄电池刀切分离器通过调节刀片高度、侧压、下压、推送刀切等四步完成对多种规格蓄电池的切割。刀切过程中, 通过升降装置中的液压缸调节刀片高度,使刀片与待切割蓄电池汇流条根部高度相适应。侧压动作将蓄电池从辊子运输线上推入刀切分离装置中,并压紧蓄电池。蓄电池被下压以及侧压压紧后,由推送装置推送蓄电池经过刀片升降装置刀切,直至上盖与下槽体完全分离。此后,下槽体继续被推入回收预处理工艺的振动分离器中。
1.2 刀切分离器主体结构设计
铅酸蓄电池刀切分离器主体结构由侧压装置、下压装置、刀片升降装置及推送装置组成,如图1所示。
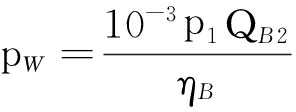
1.刀片升降装置 2.下压装置 3.推送装置 4.侧压装置
图1 铅酸蓄电池刀切分离器主体结构
下压装置与侧压装置采用气动系统,执行元件为单杆双作用气缸。推送装置与刀片升降装置则采用液压系统,使用单杆双作用液压缸作为执行元件。刀切时,下压装置与侧压装置始终压紧工作台上的蓄电池。此时,装置中的两个气缸活塞杆均受径向作用力,为避免气缸过早损坏,采用双导杆机构保护气缸活塞杆。滑块机构保证推送装置中的液压缸活塞杆不受重力产生的径向作用力,如图2所示。
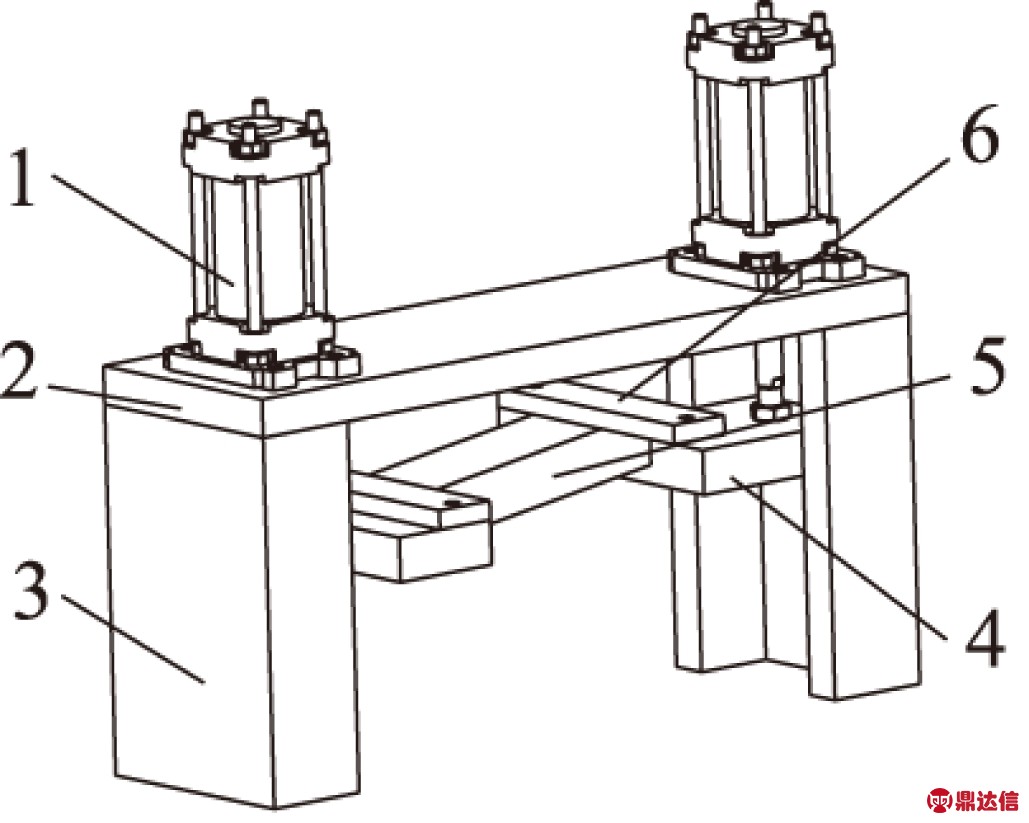
1.液压缸 2.连接板 3.立柱 4.升降块 5.刀片 6.压板
图2 刀片升降装置
刀片升降装置的立柱为方形凹槽,上端通过连接板连接,液压缸安装在连接板上。采用双液压缸同时升降的方式带动刀片升降,活塞杆端部通过升降块以及压板连接刀片。升降块位于凹槽内,凹槽对活塞杆的运动起导向作用的同时,保护活塞杆不受径向作用力。采用斜切的方式刀切蓄电池,即刀片在水平面内倾斜安装于升降块上。升降装置整体安装在刀切分离器的底板上,与后续的振动分离器衔接。
2 液压、气动系统设计
2.1 液压系统设计
推送装置以及刀片升降装置液压系统原理图如图3所示。该液压系统由电机、电磁换向阀、液压泵、分流集流阀、电磁溢流阀、调速阀、过滤器等构成。
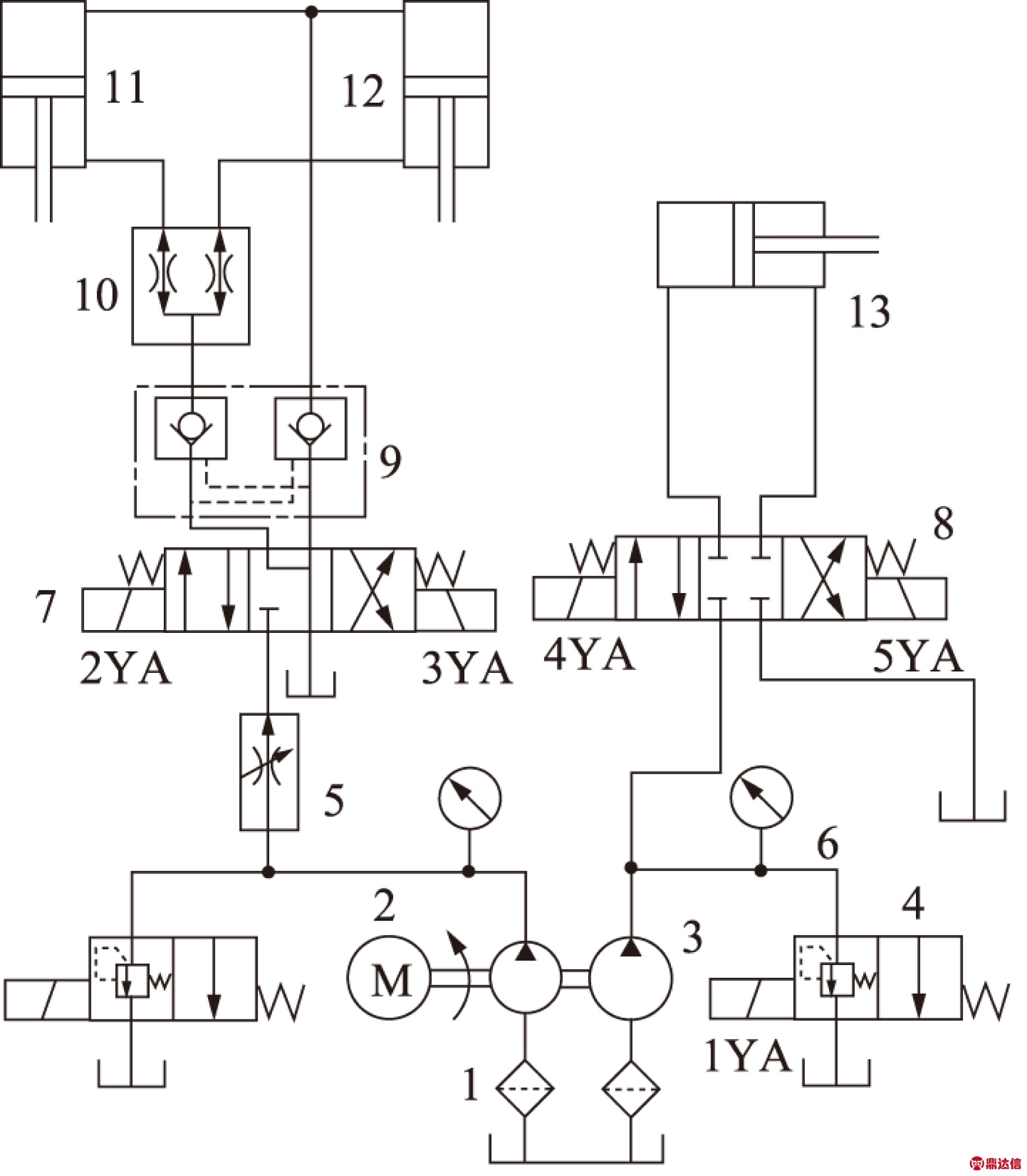
1.过滤器 2.电机 3.双联叶片泵 4.电磁溢流阀 5.调速阀 6.压力表 7.三位四通电磁Y形换向阀 8.三位四通O形电磁换向阀 9.液压锁 10.分流集流阀 11~13.液压缸
图3 液压系统原理图
该液压系统采用电磁溢流阀作为完成刀切后的卸荷以及液压系统保护元件。升降回路中,分流集流阀保证2个液压缸运动同步,避免2个液压缸的流量不一,影响升降精度。刀切时三位四通Y型电磁换向阀处于中位,液压锁锁紧同步油缸来抗拒刀切过程中受到的外力干扰[3],调速阀起到稳定刀片升降速度的作用。每完成一次刀切,将活塞杆完全缩回,再调定下一次刀片升降高度,消除分流集流阀的累积误差。
2.2 液压元件选型
1) 推送装置液压缸选型
切割铅酸蓄电池时最大负载15000 N。根据液压与负载的关系以及液压缸的行程需求,初选液压缸的工作压力p1=2.2 MPa,液压缸行程L1=700 mm。本系统未在回油路中采用节流阀,且暂不考虑回油管路以及换向阀带来的压降,故背压p2=0。根据工作压力选择速比φ=1.33,即无杆腔面积A1与有杆腔面积A2的比值为4∶3,液压缸效率:ηcm=0.9[4-6]。
根据公式:

(1)
得出:A1=0.0076 m2 ,液压缸直径D=98 mm。
取标准缸径100 mm,杆径为50 mm。则液压缸无杆腔有效面积A1=78.5 cm2,有杆腔有效面积A2=58.9 cm2。
该液压缸工进速度V=100 mm/s。根据流量公式:
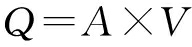
(2)
得出所需泵的流量Q为47.1 L/min。
2) 升降装置液压缸选型
刀片升降装置中,最大负载为250 N,平均每个液压缸承受负载125 N。初选升降液压缸行程L2=75 mm,直径D2=63 mm,无杆腔与有杆腔面积比为2∶1,活塞杆下降速度为10 mm/s。根据流量公式(2),可知每个液压缸工作所需要的流量为1.87 L/min。
3) 液压泵选型
考虑系统泄漏的影响,取泄漏系数K=1.2,根据公式:
QB=Q×K
得出,升降回路中液压泵的流量为两个液压缸作业时的流量之和,即QB1为4.5 L/min。在推送回路中,液压泵的流量QB2为56.52 L/min。
4) 电动机选型
叶片泵总效率ηB为0.8,选取进油路压力总损失约为1 MPa。泵的最大驱动功率:
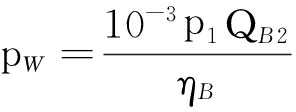
(3)
求得, pW=3.8 kW。因此,选取电机功率4 kW满足泵的驱动功率。
2.3 气动系统设计
气动系统原理图如图4所示,由单向节流阀、气缸、三联件、截止阀等气动元件构成。
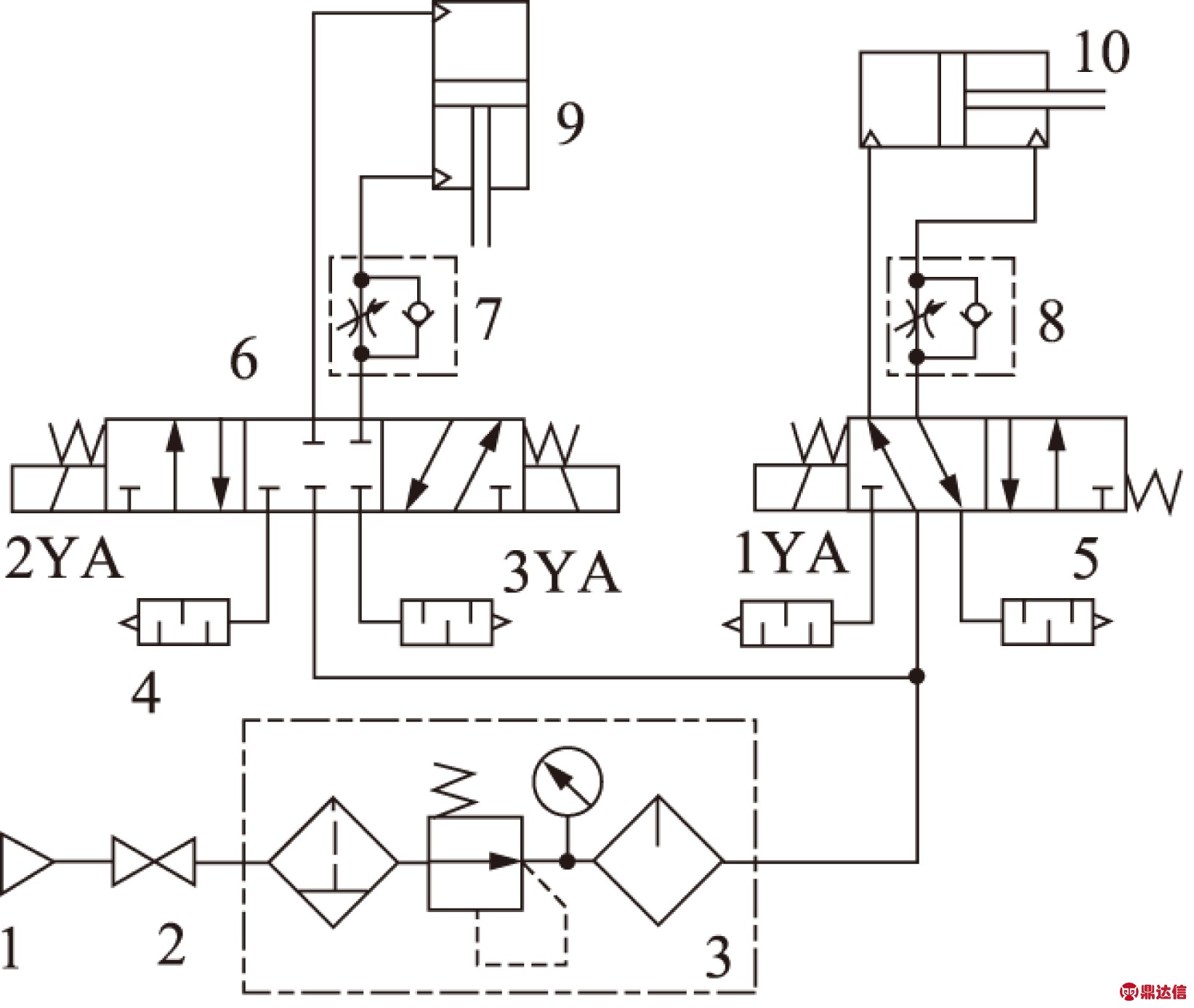
1.气源 2.截止阀 3.三联件 4.消声器 5.二位五通电磁换向阀 6.三位五通电磁换向阀 7、8.单向节流阀 9、10.气缸
图4 气压系统原理图
下压装置采用三位五通电磁换向阀控制气缸运动方向,侧压装置采用二位五通电磁换向阀控制气缸运动方向,在各个排气口使用消声器改善高速排气时产生的噪声。单向节流调速阀保证气缸的下压以及侧压时速度稳定[3-7]。蓄电池被下压装置压紧后,换向阀处于中位,保证在刀切完成后,活塞杆不会因突然失去下压反作用力而下冲并撞击液压缸活塞杆。
侧压装置中气缸活塞杆的最大负载约为200 N,下压装置中气缸最大负载约为180 N。初选气源气压0.6 MPa。所切割蓄电池最大高度差46 mm,最大宽度差42 mm。侧压装置被安装在宽度为440 mm的辊子输送线的另一端。因此,侧压装置选择长500 mm,直径50 mm的气缸,下压装置采用长100 mm,直径50 mm 的气缸。
3 推送液压缸仿真
刀切分离器液压系统开始刀切时压力瞬间升至15000 N以及在刀切完成时降至300 N,液压系统的瞬间加载荷及卸载荷使下槽体在被推入振动分离器时产生冲击,若选型不当,将严重影响刀切装置的使用寿命。为得到该系统在推送刀切时刻以及刀切完成时刻活塞杆的运动状态,油缸内压力的变化情况,避免因错误的选型导致刀切分离器设计失败,需进行仿真研究。
利用AMESim软件对推送液压缸的部分工进时间段进行仿真,即蓄电池刚开始刀切直至刀切完时间段[7]。采用长为200 mm的蓄电池作为仿真对象,将系统流量的泄漏折算至液压泵中,即液压泵的排量为47.1 mL/r,电机转速为1000 r/min。仿真系统中使用的D1VW系列换向阀,通过流量为50 L/min 时,压降为0.9 MPa。将液压缸因存在工作效率而产生的压力损失折算至负载处,即刀切时的负载为16667 N[8],刀切完成后的负载为334 N。压力管道直径为16 mm。在1 s时刻,换向阀4YA通电,液压缸开始推送蓄电池做刀切分离,在第3 s时刀切完成。
由图5、图6以及图7可以看出,液压缸活塞杆稳定时速度为10 cm/s。此时,换向阀回油通道产生0.44 MPa左右的背压。当负载为16667 N时,无杆腔压力为2.5 MPa,仿真结果与通过液压元件计算选型得出结果基本一致。
液压缸开始刀切瞬间,无杆腔的压力、速度均有较大幅度波动,但速度很快稳定在0.1 m/s,压力则稳定在2.5 MPa左右。铅酸蓄电池刀切完成时刻,压力从16667 N瞬间降至334 N,导致了该液压缸的无杆腔内压力与活塞杆速度大幅度变化。但经过小于1 s的时间后,压力与速度均达到稳定状态。由以上分析可知,该液压回路中液压油与活塞杆随着工况的变化产生波动后迅速稳定,说明液压元件选型的正确性,保证下槽体能够被平稳推送入后续振动分离器。同时,避免系统压力持续大范围变化对液压元件造成损伤。
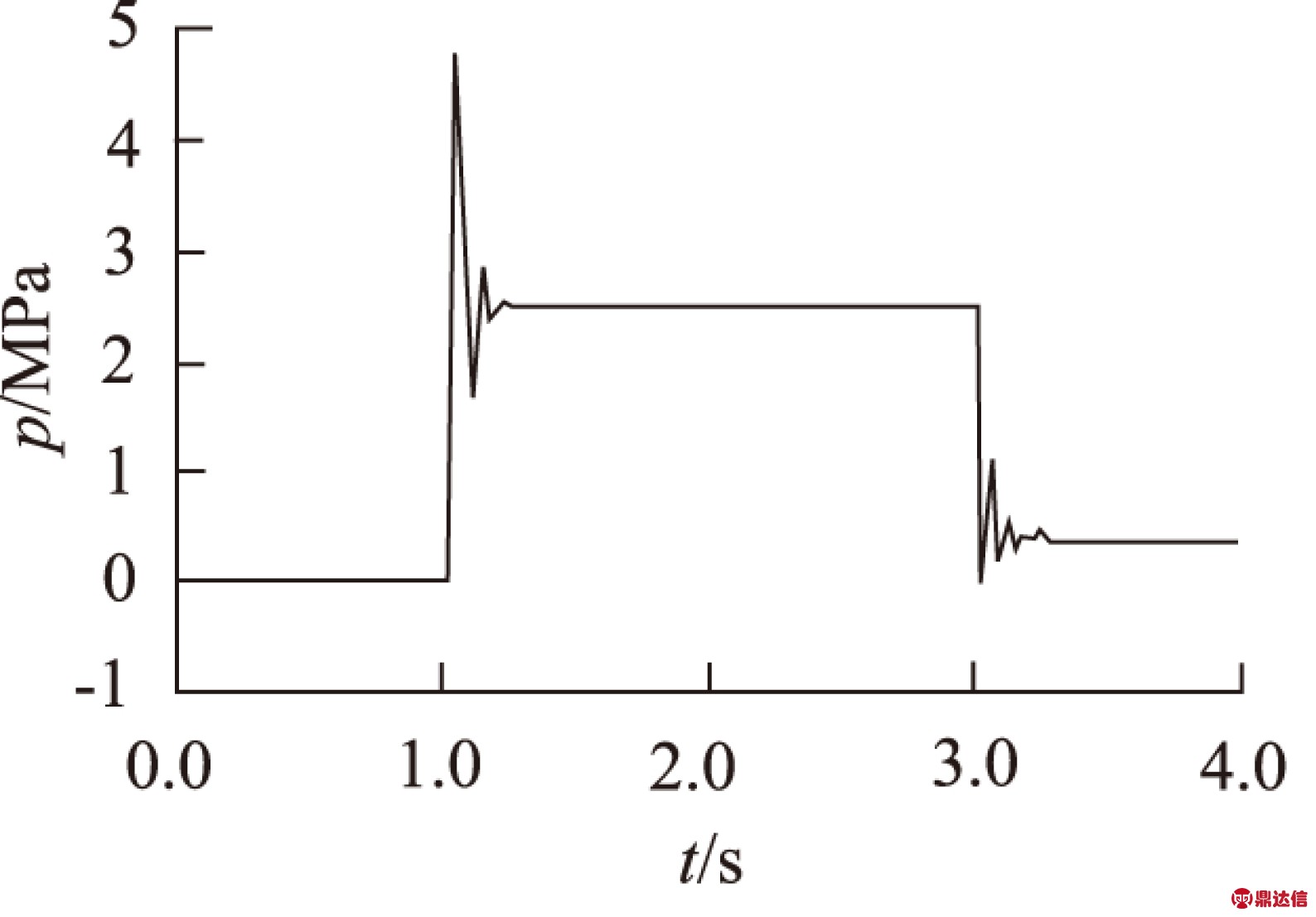
图5 液压缸无杆腔压力变化
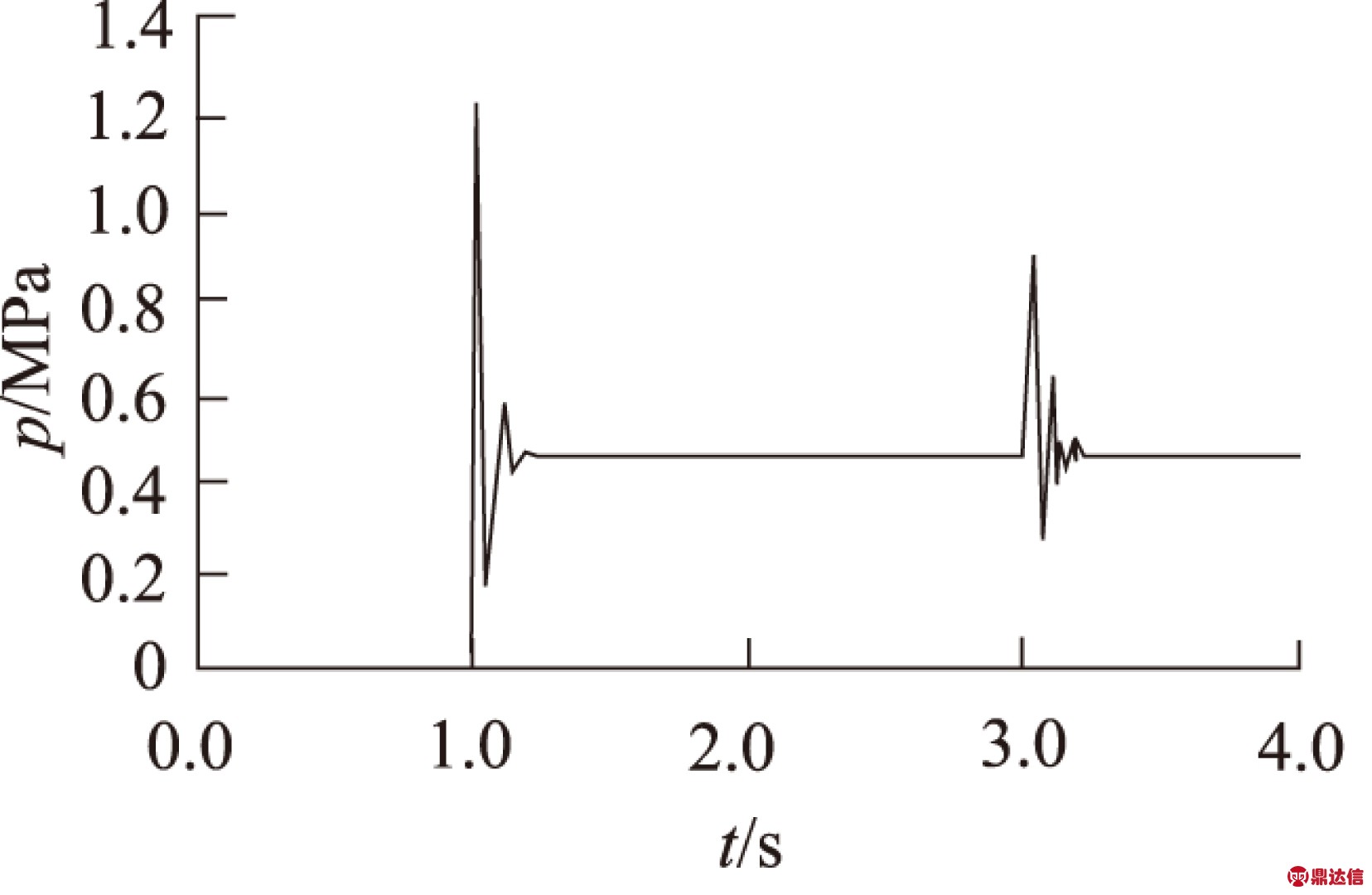
图6 换向阀回油通道压力变化
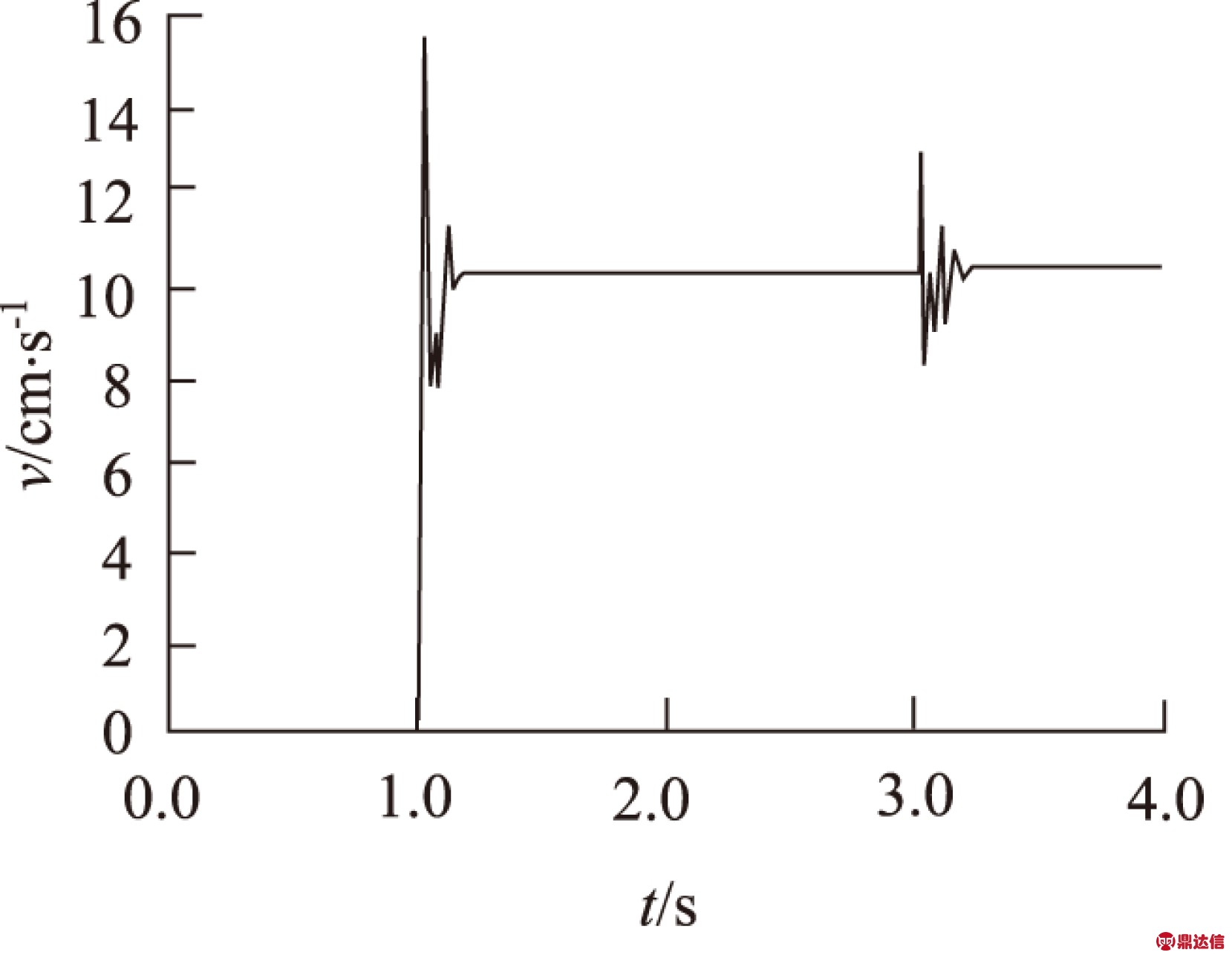
图7 液压缸活塞杆速度变化
4 结论
通过对铅酸蓄电池刀切分离器的重新设计,依靠液压系统以及气动系统,实现新型刀切分离器对不同规格型号铅酸蓄电池的切割及作业自动化,并对重要液压回路进行仿真,确定液压元件选择的正确性。该分离器扩大了“逐步分离法”应用范围,提高回收效率,且结构简单,易于维护,具有较高的应用价值。