摘要:分析了现有煤泥水处理工艺过程以及存在的问题,在对煤泥水特性以及现有煤泥水处理设备进行研究之后,提出将砂水分离器引入到煤泥水处理系统中,负责对高频筛筛下的矸石泥进行初步处理,将其中容易泥化的高灰矸石泥提前排出,减缓了矸石泥进入煤泥水处理系统中造成的不良影响,降低了设备故障频率,提高了煤泥水处理工作效率以及产品煤质量。
关键词:煤泥水处理;砂水分离器;优化
1 煤泥水处理工艺及其问题分析
1.1 煤泥水处理工艺分析
为了提高选煤效率,选煤厂多采用选前脱泥,以某矿为例,该矿对原煤按照其颗粒直径的大小进行分级:颗粒直径小于0.5 mm的煤泥采用板框压滤机和加压过滤机相结合的方式进行回收;直径在0.5 mm~3 mm的粗煤泥由螺旋分选机进行分选;直径在3 mm~13 mm的末煤使用中介旋流器进行分选;而对于直径在13 mm以上块煤的分选则由浅槽分选机负责。煤泥水处理的一般流程如图1所示。其中,“+”表示底流,“-”表示溢流。先由水力旋流器对原生煤泥进行分级,分级后的溢流注入浓缩池,而底流则由螺旋分选机进行分选,分选出的螺旋精矿先后由精煤旋流器和弧形筛进行分级浓缩,底流由煤泥离心机处理后形成混煤产品,精煤旋流器形成的溢流则进入浓缩池,没有通过弧形筛的煤泥则进入二次旋流桶;螺旋分选机分选出的矸石由矸石旋流器进行分级,其分级后的溢流进入浓缩池,底流进入高频筛进行筛选,筛下的煤泥送至原生煤泥桶,筛上的矸石则外排。这套生产工艺在实际生产过程中由高频筛筛出的煤泥水灰分较高,容易泥化成极为细小的煤泥,在进入浓缩池后导致沉降困难,从而影响了选煤厂的高效率运行。
1.2 煤泥水处理工艺存在的问题分析
现有选煤工艺在实际使用过程中会出现矸石进入煤泥水处理系统并泥化的现象,矸石泥在进入后只能通过浓缩池以及压滤机回收,但是矸石泥在浓缩池后容易形成悬浮层,很难沉降,并且会影响正常煤泥的沉降效率。针对这一问题,某矿启用了新的浓缩池,专门用于处理高频筛下的泥水和矸石旋流器的溢流,但是仍存在以下问题。
(1) 过滤机易损坏。如果矸石未能泥化会在加压过滤机的罐内迅速沉降,很难吸附在滤板上并会导致堆料,而泥化后的矸石由于过细会吸附在滤布上,导致卸料困难并且滤布磨损较严重;板框压滤机在进行反吹时会使矸石泥沉降在入料中心管,从而导致中心管堵塞,降低入料速度,并且还会导致滤板倾斜,存在较大的安全隐患。
(2) 循环水质量变差。矸石泥经过长时间多次的浸泡和粉碎很容易泥化,在浓缩池中很难沉降,从而需要消耗更多的药剂,使循环水的质量变差。
(3) 煤泥处理设备效率降低。矸石泥在进入系统后最终需要通过板框压滤机和加压过滤机进行处理,由于矸石泥吸附了大量水分,板框压滤机在进行处理时挤压水的效率降低,并且形成的滤饼黏度较大、卸料困难,最终导致滤饼水分难以达到要求,设备效率较低。
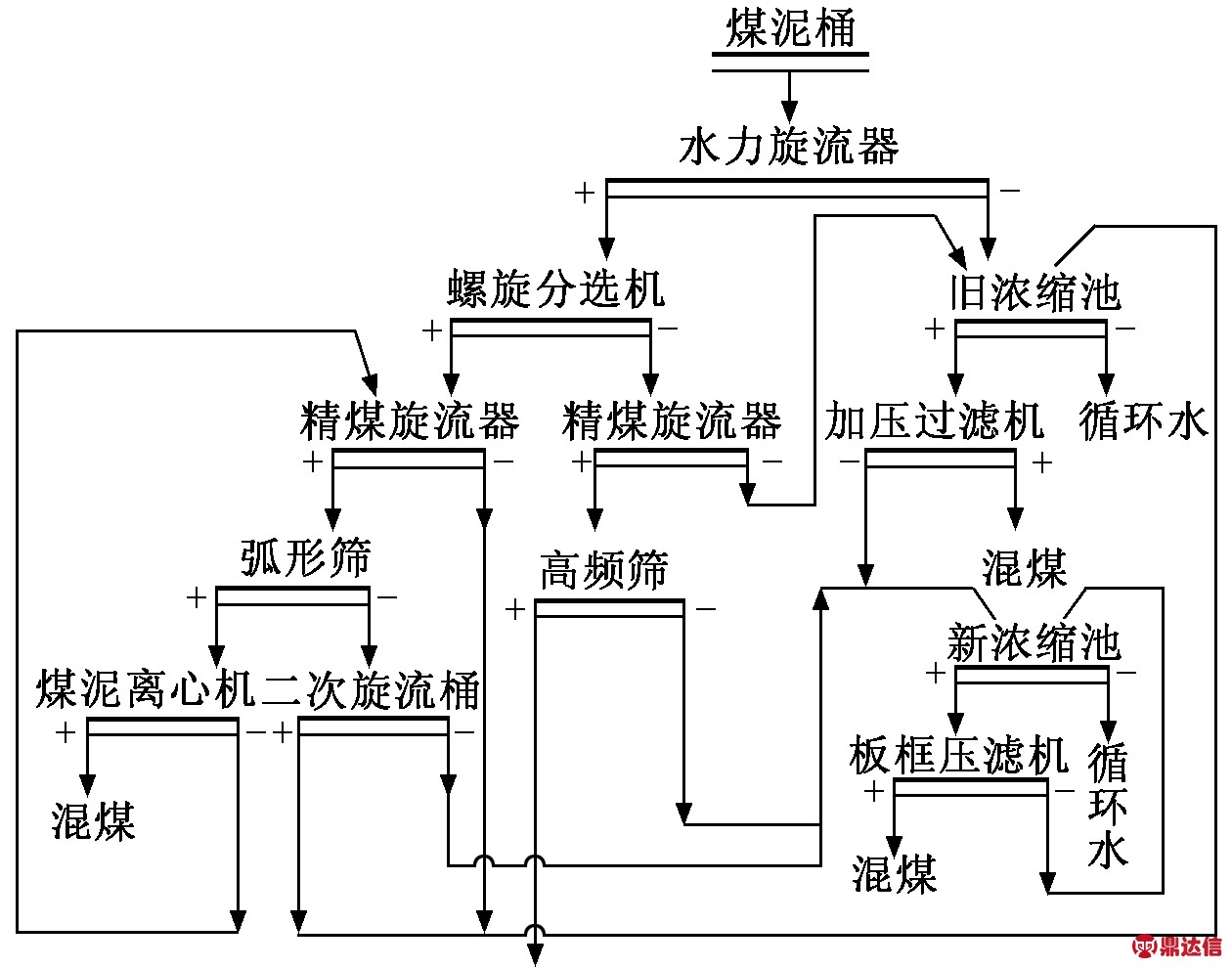
图1 现有选煤厂煤泥水处理系统工艺流程
2 煤泥水特性分析
采用X-射线对高灰极细矸石泥进行衍射物相分析,煤样衍射图谱如图2所示。样品的成分除了煤还有伊利石、高岭石、氧化矿石英、矿物方解石、伊蒙混层以及少量的硫化矿物等,煤样中脉石矿物的组成和含量如表1所示。从表1中可以看出煤样中脉石矿物主要由黏土矿物构成,占到了总量的63%,其中占到4.83%的蒙脱石很容易膨胀水化,对煤泥水的沉降和过滤效果影响较大。在洗煤过程中,矿物在水的浸泡以及机械力的作用下容易从煤样中剥落进入水中并分离成极小颗粒,这种现象在黏土矿物尤其是蒙脱石中表现得十分明显,对煤泥水处理威胁最大。
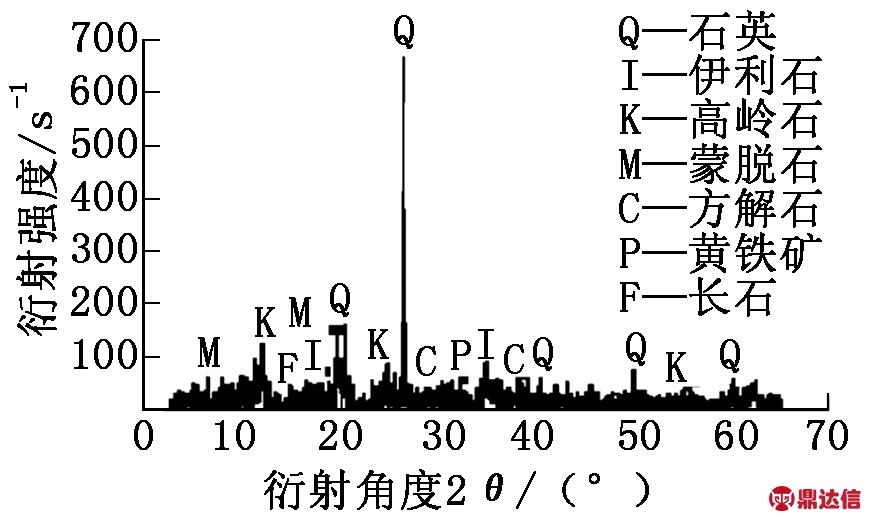
图2 煤样X-射线衍射图
表1 煤样中矿石组成及其含量(质量分数) %

经过对不同级别的矸石泥进行沉降实验后,可以得到以下结论:矸石容易泥化,且颗粒小于0.075 mm的矸石泥沉降缓慢;颗粒直径在0.075 mm~0.35 mm之间的矸石泥沉降速度最快。因此需要迅速将0.075 mm~0.35 mm之间的矸石泥从系统中排除,同时也要减少大颗粒矸石泥在系统中的存量,防止其进一步分解成更小颗粒。
3 砂水分离器研究
3.1 砂水分离器工作原理
砂水分离器的作用是对砂水混合液进行砂水分离,主要由U形槽、导流板、水箱、衬条、无轴螺旋、驱动装置等组成,如图3所示。矸石泥进入砂水分离器箱体后,体积较大的颗粒会较快地沉降在箱体以及U形槽底部,无轴螺旋负责将沉淀沿倾斜放置的U形槽提升,在保证矸石泥沉淀彻底脱水后排出箱体,剩下的煤泥水则从溢流口流出。
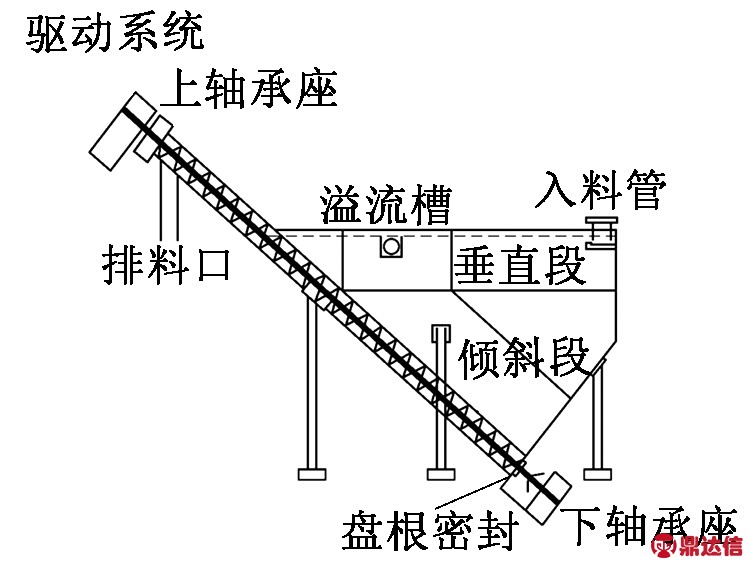
图3 砂水分离器结构示意图
3.2 砂水分离器设计
3.2.1 箱体设计
通过对高频筛筛下水的测量和统计,其煤泥水的流量大概为150 m3/h,假定煤泥水在箱体内的停留时间为50 s,那么箱体的体积应该在2.1 m3以上,考虑到矸石泥沉淀对体积的影响,箱体的体积应该适当增大,箱体的垂直段容积设定为3 m3,倾斜段体积设定为3 m3。为了保证矸石泥在沉淀后能够顺利进入U形槽进行提升,将箱体底部的倾斜板的倾斜角度设定为60°。为了在有限的空间内提升箱体容量,将U形槽的倾斜角度设定为40°,长度为5.5 m,排料口需要高出水面1 m,即箱体的总高度为2.4 m,垂直段的高度为0.6 m。
为了扩大箱体容积以及提高矸石泥在箱体中的停留时间,在上部垂直箱体的后背板下方也采用60°倾角设计。同时为了进一步达到延长沉降时间的目的,在箱体内部焊接了2块高度为500 mm的钢板,钢板沿箱体长度方向布置,其上边沿高出溢流口3 cm,从而起到导流入料的作用。
由于箱体不同位置受磨损程度不同,因此采用的钢板厚度也不同,在箱体上部由于磨损较小,采用6 mm厚的钢板焊接;而下部由于磨损较大,因此采用8 mm厚钢板焊接。考虑到U形槽对材料的耐磨程度要求最高,因此U形槽的外部采用8 mm厚钢板,其内部则粘贴有耐磨陶瓷材料。
3.2.2 传动系统设计
砂水分离器的传动系统主要是用于U形槽中螺杆的驱动,驱动电机的额定功率为11 kW,通过变比为12.56的减速器驱动螺杆旋转。螺杆的旋转速度对于矸石泥的排出质量至关重要:螺杆转速过慢会导致矸石泥排出速度过慢,如果入料浓度较大会导致矸石泥大量沉积在底部,严重时会压死螺杆,如果入料浓度较低,则会导致上料困难;螺杆转速过快会导致矸石泥不容易被压实,含水量大,浓度低。针对这一问题,电机采用变频调速的方式,根据入料浓度调整电机转速,一般将变频器的输出频率设置在50 Hz~30 Hz,通过减速器减速,将螺杆的转速维持在1 rad/s~2 rad/s。
4 使用效果
砂水分离器投入使用后平均每小时排出矸石泥10 t,从而大大降低了浓缩池的排矸压力。为具体检验砂水分离器对不同粒级的矸石泥的排矸能力,对其进行了单机实验,其实验结果如表2所示。
表2 砂水分离器单机检查结果 %
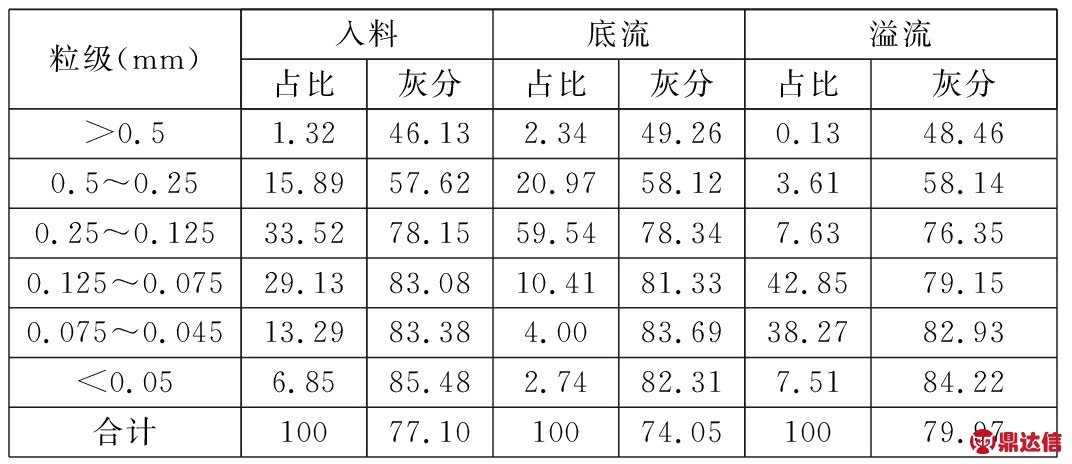
从表2中可以看出:入料中0.075 mm~0.5 mm粒级的物料比例为78.54%,在底流排料中提升到了90.92%,粒度大于0.074 mm的物料比例从入料的79.86%降低到了溢流的54.22%,这个粒级的矸石泥在浓缩池中能够实现缓慢沉降,在防止压耙事故发生的同时也缓解了矸石泥的进一步泥化。