摘要:为了提高弯管式汽水分离器的除湿效率,提出了2种汽水分离器改进结构,一种是弯管前加旋流装置的组合分离器,另一种是“Z”字形弯管分离器,同时对改进结构进行了数值研究。结果表明:弯管前加旋流装置的组合分离器中,汽流经过旋流叶栅后流向发生偏转,紊乱的流场持续到第一组导流除湿叶栅进口,汽流经过第二组导流除湿叶栅后流线基本与圆管的轴向一致,汽流经过旋流叶栅和导流除湿叶栅时会产生较大总压损失;“Z”字形弯管分离器管中,汽相流速比较均匀,流线分布良好,总压损失主要发生在导流除湿叶栅中。与弯管式分离器相比,弯管前加旋流装置的组合分离器的除湿效率提高了7.4%,平均总压损失系数增大了28.1%;“Z”字形弯管分离器性能最佳,除湿效率提高了11.3%,平均总压损失系数减小了37.5%。该结果可为研究和开发新型汽水分离器提供理论依据。
关键词:核电汽轮机;连通管;汽水分离器;除湿性能;数值研究
核电汽轮机需在高压缸出口布置汽水分离器,以去除高压缸出口湿度约12%~14%蒸汽中的绝大部分水分。目前常用的是波形板汽水分离器,它的低速特性决定了其尺寸庞大、系统布置复杂、造价高以及系统可靠性低等[1]。ABB公司开发出安装在高、中/低压缸连通管内的高速汽水分离器——弯管式汽水分离器(SCRUPS),并取得了满意的运行经验和效果[2-5]。这种弯管式汽水分离器的除湿效率并不比常规汽水分离器低,且尺寸小,简化了系统布置,降低了造价,提高了系统的可靠性。
图1是弯管式汽水分离器在汽轮机系统中的布置。预分离器(MOPS)先分离出沿高压缸壁流下的水分,弯管式汽水分离器(SCRUPS)去除湿蒸汽中的水分,蒸汽经再热器(Reheater)加热至一定过热度后送往中/低压缸继续膨胀做功。图2为弯管式分离器的简化结构示意。分离器内装有导流除湿叶栅,蒸汽在除湿叶栅内流动时流向发生偏转,汽流携带的大部分水滴因惯性力作用发生碰撞并沉积在带吸湿槽的除湿空心叶栅上,沉积的水分和少量蒸汽通过吸湿槽吸入叶栅内腔室并分别排出,从而达到除湿的目的。由于技术资料保密等原因,国内目前开发和应用这种分离器存在一定的难度。
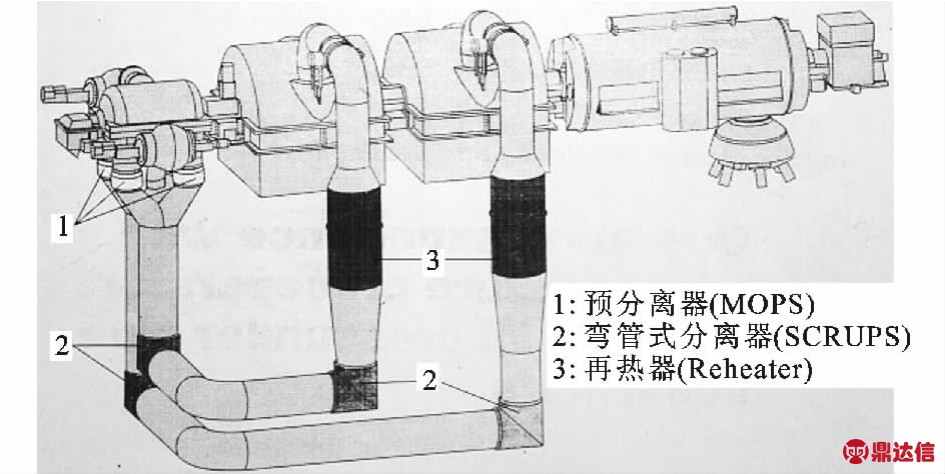
图1 弯管式汽水分离器在汽轮机系统中的布置
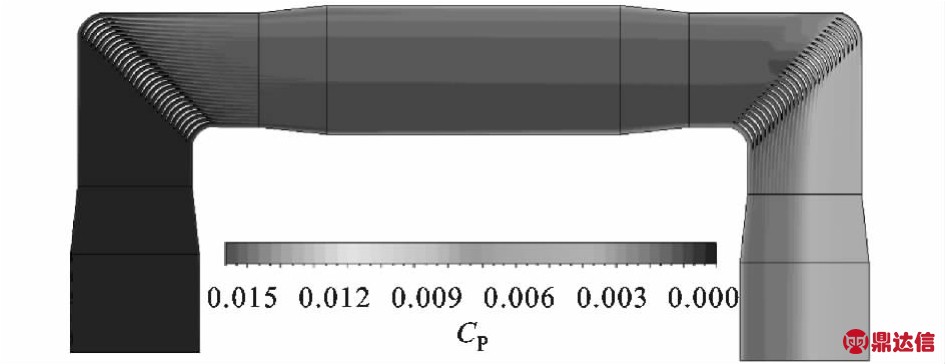
图2 弯管式汽水分离器结构简图
本文应用计算流体动力学软件ANSYS-CFX对弯管式汽水分离器和2种改进结构的除湿性能进行了数值计算与分析,揭示了“Z”字形弯管分离器具有最佳的除湿效率和最低的总压损失。
1 弯管式和2种改进结构分离器的计算模型
1.1 弯管式分离器计算模型
水滴重力忽略不计[6],模型沿叶高方向对称,取沿叶高一半进行研究能降低网格总数量,提高计算效率。
弯管式汽水分离器内水滴沉积率主要取决于导流除湿叶栅的叶宽、节距、汽流攻角[7],导流除湿叶栅的前期研究中得到了优化叶型和叶栅参数,即:叶宽为350mm,节距为60mm,冲角为10°。图3为弯管式汽水分离器结构示意。商业软件ANSYS ICEM可对分离器各部分单独进行结构化网格划分后再组合计算,根据网格无关性验证,计算时取总网格数约1 239万。
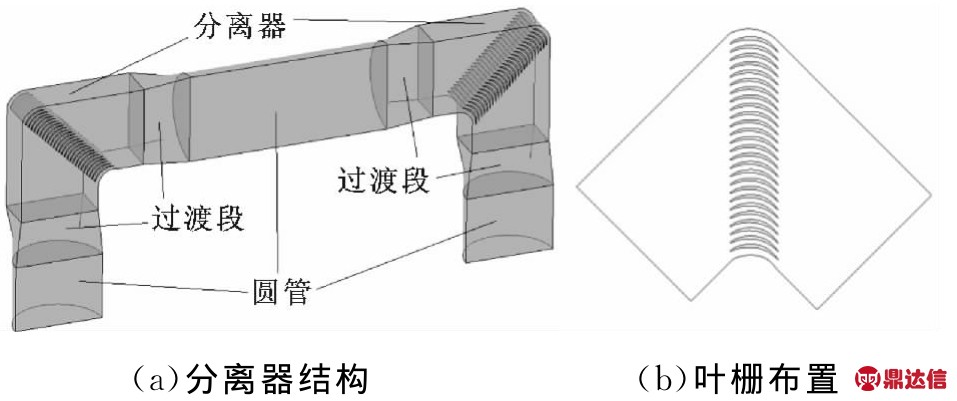
图3 弯管式汽水分离器结构
1.2 组合分离器计算模型
不同直径水滴,其沉积机理有所不同[7],大水滴沉积主要依靠惯性力,小水滴沉积受湍流效应影响很大。弯管式分离器内小水滴汽流跟随性好,沉积量低,因此本文提出了弯管前加旋流装置的组合结构(见图4),来增加汽流湍流度,以提高小水滴沉积率,旋流叶栅结构尺寸参考文献[8]。组合分离器中,旋流器为非结构化网格划分,其余为结构化网格划分,总网格数约1 450万。
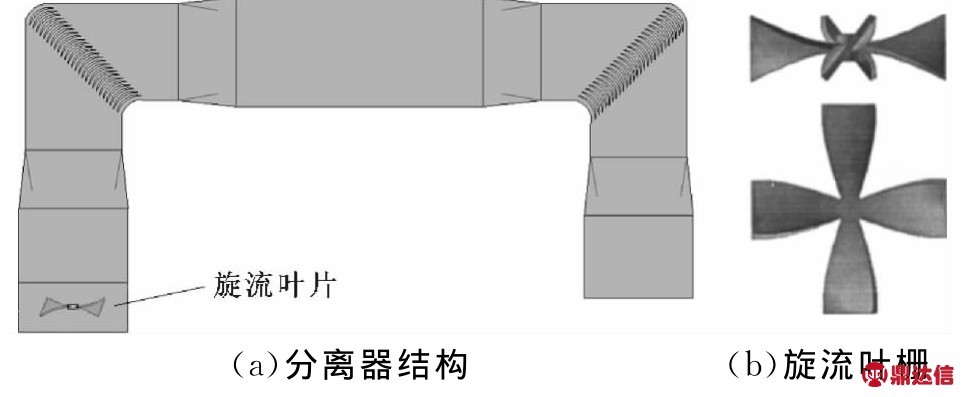
图4 组合分离器结构
1.3 “Z”字形弯管分离器计算模型
研究发现,各种直径水滴的沉积量受汽流偏转角影响很大,且随偏转角的增大而增大,为此本文提出了“Z”字形弯管分离器结构。图5为“Z”字形弯管分离器在汽轮机系统中的布置。
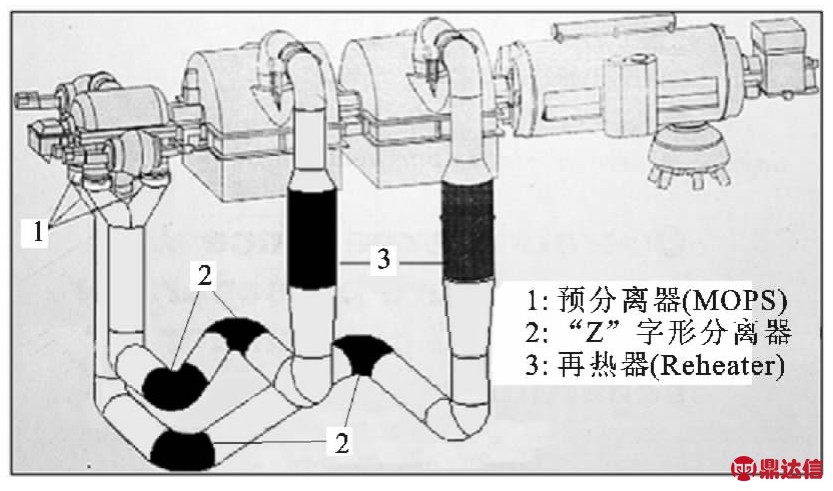
图5 “Z”字形弯管分离器在汽轮机系统中的布置
图6为“Z”字形弯管分离器结构示意,其中导流叶栅偏转角为120°,冲角为0°,由90°偏转角叶型改型并用Numeca Desigh 3D叶型优化而得,为结构化网格,总网格数约1 698万。
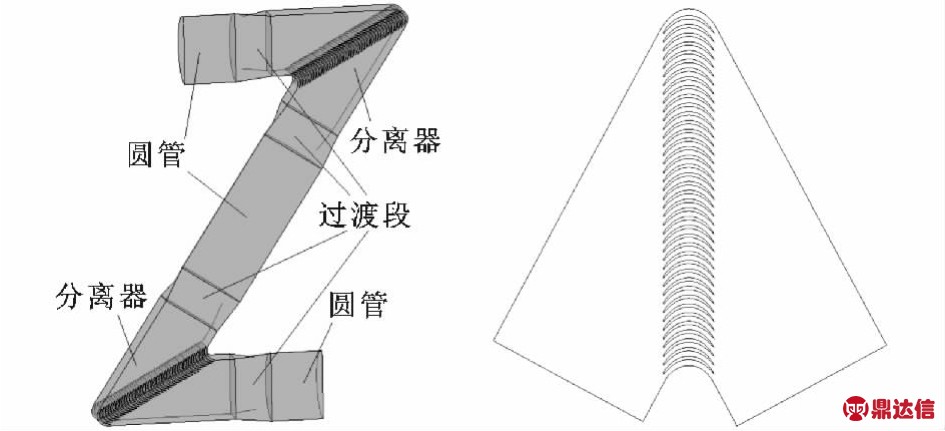
图6 “Z”字形弯管分离器结构
(a)分离器结构 (b)叶栅布置
2 数值计算方法与验证
2.1 蒸汽流场求解
采用商业软件CFX求解定常三维黏性雷诺平均N-S方程,湍流模型为壁面函数修正的标准k-ε模型。采用IAPWS-IF97标准给定蒸汽的热物理参数。
2.2 水滴输运模型
假定水滴碰撞到叶栅表面时未发生反弹,且被直接捕获,所以采用Lagrangian方法追踪水滴的运动轨迹,采用随机轨道模型修正Lagrangian方法在描述水滴运动上的误差,在运动方程的速度项中通过添加随机速度分量来考虑湍流的影响。
2.3 计算方法验证
根据Parker等人在平面叶栅上进行的小微粒沉积实验数据[9],来验证本文计算方法的适用性。采用25万、50万、100万、150万4种网格进行网格无关性验证,计算边界条件按照实验条件给定。
总压损失系数定义为

式中:P*0为进口总压;P*2为当地总压。由于文献[9]中未给出总压损失系数,所以引入外推法[10]来获得CP的精确解,即

式中:f1、f2为2种网格密度时获得的总压损失系数的计算结果;p为方程截差阶数;r为网格细化比。
沉积率为撞在实验叶栅上的粒子质量与加入的粒子总质量之比。表1为平均总压损失系数和沉积率。由表1可以看出,网格数为100万时,平均总压损失系数¯Cf的相对偏差Δ¯Cf和沉积率η的相对偏差Δη明显减小,网格数增加到150万时,平均总压损失系数的相对偏差仅减小了0.5%,沉积率的相对偏差仅减小了0.4%。因此,采用100万~150万网格比较合理,既可保证计算的准确性,也能适当减少计算量。
表1 平均总压损失系数和沉积率
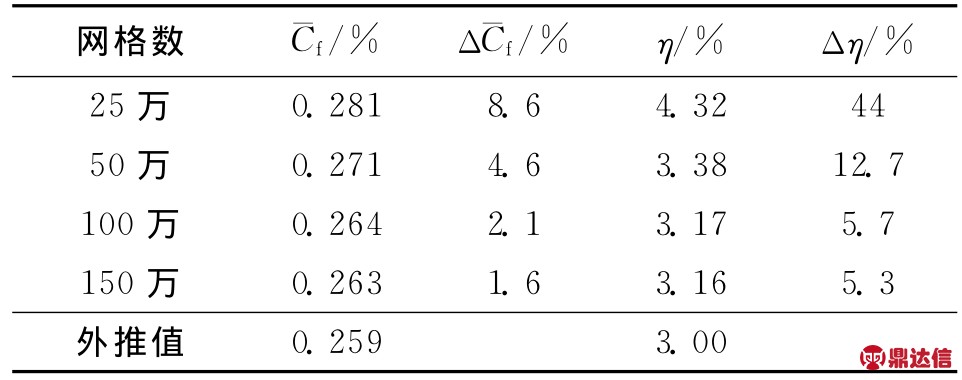
3 水滴尺寸与分布估算
核电汽轮机高压缸出口蒸汽所含水分中二次水滴不足5%[11],根据临界韦伯数计算,高压缸二次水滴的尺寸与一次水滴相差不大。为简化计算,本文将少部分的二次水滴并入一次水滴。根据文献[12]的试验资料,汽轮机一次水滴群中直径为di的水滴群质量mi与直径等于平均直径dm的水滴群质量mm之比近似服从正态分布,即

计算出水滴平均直径后,可求出各种直径水滴的质量及相应的水滴数。
根据1 750MW核电汽轮机的相关参数,按文献[11]的方法确定水滴的平均直径为10μm。本文将水滴分为5种直径范围来考核水滴的运动沉积特性,每种范围取其平均值进行计算。水滴的质量流量为37 731.1g/s,每秒有1.657 42×1015个水滴进入计算区域,该数目过于庞大,按1∶1010比例缩小水滴数目,即取165 742个水滴进行计算。表2为水滴平均直径为10μm时不同水滴直径范围内的水滴数目。
表2 水滴平均直径为10μm时不同水滴直径范围的水滴数目
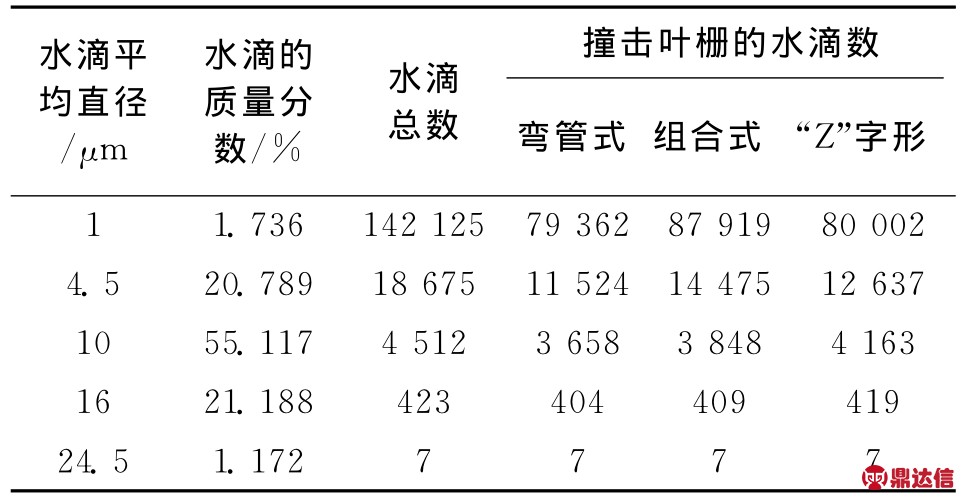
4 计算结果与分析
汽相进口给定总压1 234.5kPa、总温463.3K、汽流方向、湍流强度及长度;出口给定质量流量424.29kg/s;叶高方向上端面为对称面,其余为壁面;水滴从进口均匀加入,速度为汽相进口速度的80%[7]。
4.1 弯管式汽水分离器的计算结果
图7为弯管式汽水分离器(简称弯管式分离器)内汽相流线分布。由图7可见,分离器内流速分布较为均匀且在50m/s左右,流线分布良好,汽流沿着圆管轴向流动。
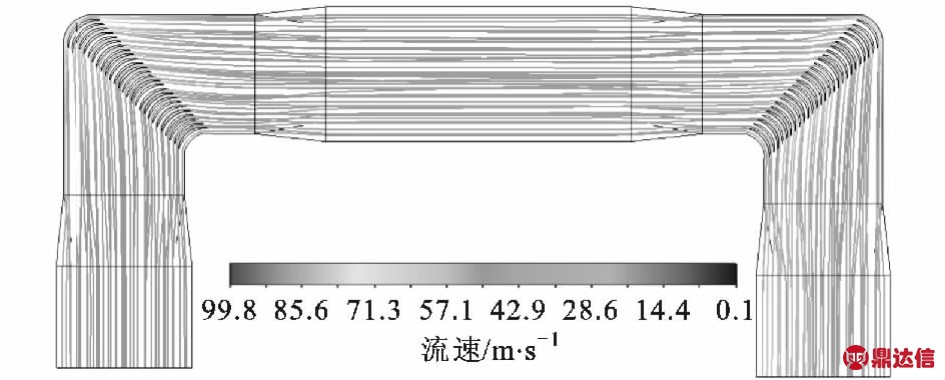
图7 弯管式分离器内汽相流线分布
图8为弯管式分离器叶栅中间截面的总压损失系数分布。由图8可见,汽流总压损失主要发生在两组导流除湿叶栅中,对应总压损失系数增大,在圆管和过渡段中汽流总压损失系数基本不变。
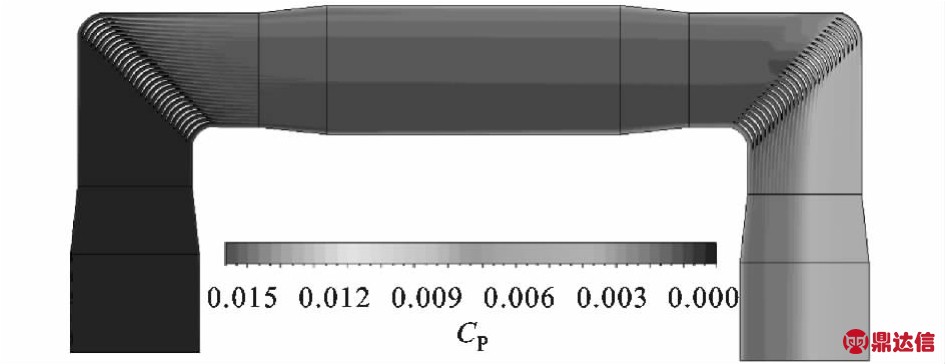
图8 弯管式分离器叶栅中间截面总压损失系数分布
图9为3种直径水滴在弯管式分离器内的运动轨迹。由图9可见,水滴在经过两组除湿叶栅时数量有所减少,水滴沉积量随着水滴直径的增大而增多。
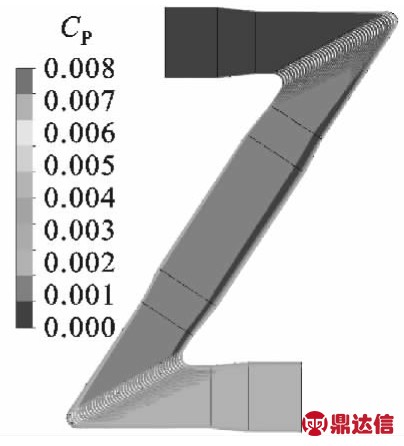
图9 3种直径水滴在弯管式分离器内的运动轨迹
4.2 组合分离器的计算结果
图10为组合分离器中汽相流线分布。由图10可见:汽流经过旋流叶栅后流线发生偏转,对应的汽流湍流度增强,紊乱的流场持续到第一组除湿叶栅进口;经过第一组除湿叶栅后,受叶栅整流的作用,流线基本均匀,经过第二组叶栅后流线与圆管轴向几乎一致。
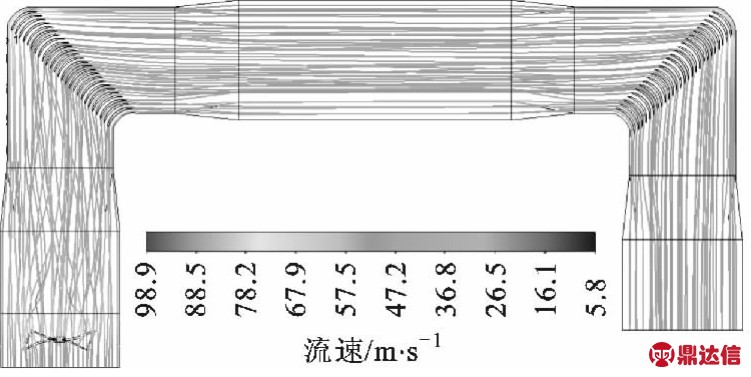
图10 组合分离器中汽相流线分布
为了定量说明汽流在两组除湿叶栅前的攻角分布,应用CFX探针功能提取计算结果中的汽流角度,并计算出沿额线分布的汽流攻角大小。图11为应用探针对两组叶栅进行数据提取的位置,图12为组合分离器中汽流攻角分布,其中横坐标相对长度l定义为探针位置距叶栅前额线端部的距离与前额线总长之比。由图11、12可以见,两组叶栅进口汽流攻角不再是设计时的10°,第一组叶栅进口汽流攻角的变化范围较大,为-4°~42°,第二组叶栅进口汽流攻角的变化范围较小,为2°~22°。
图13为组合分离器叶栅中间截面的总压损失系数分布。由图13可见,汽流在经过旋流叶栅和两组导流除湿叶栅时都会产生较大总压损失,对应的总压损失系数增大。
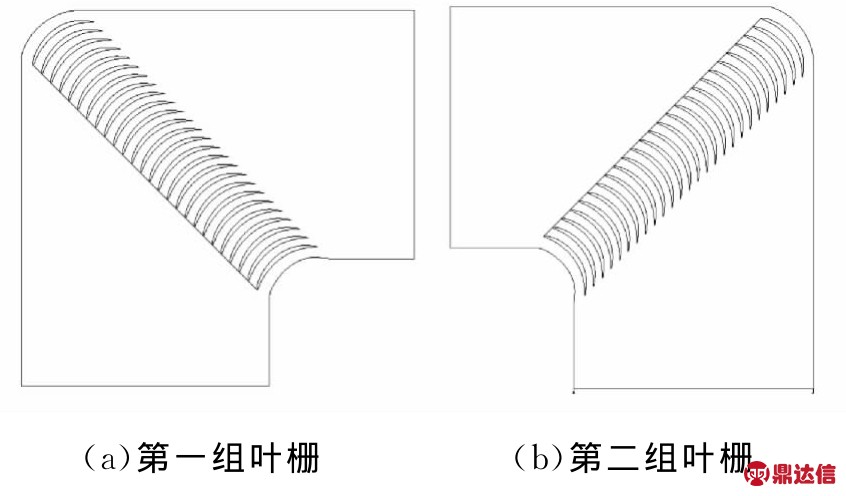
图11 探针数据提取位置示意图
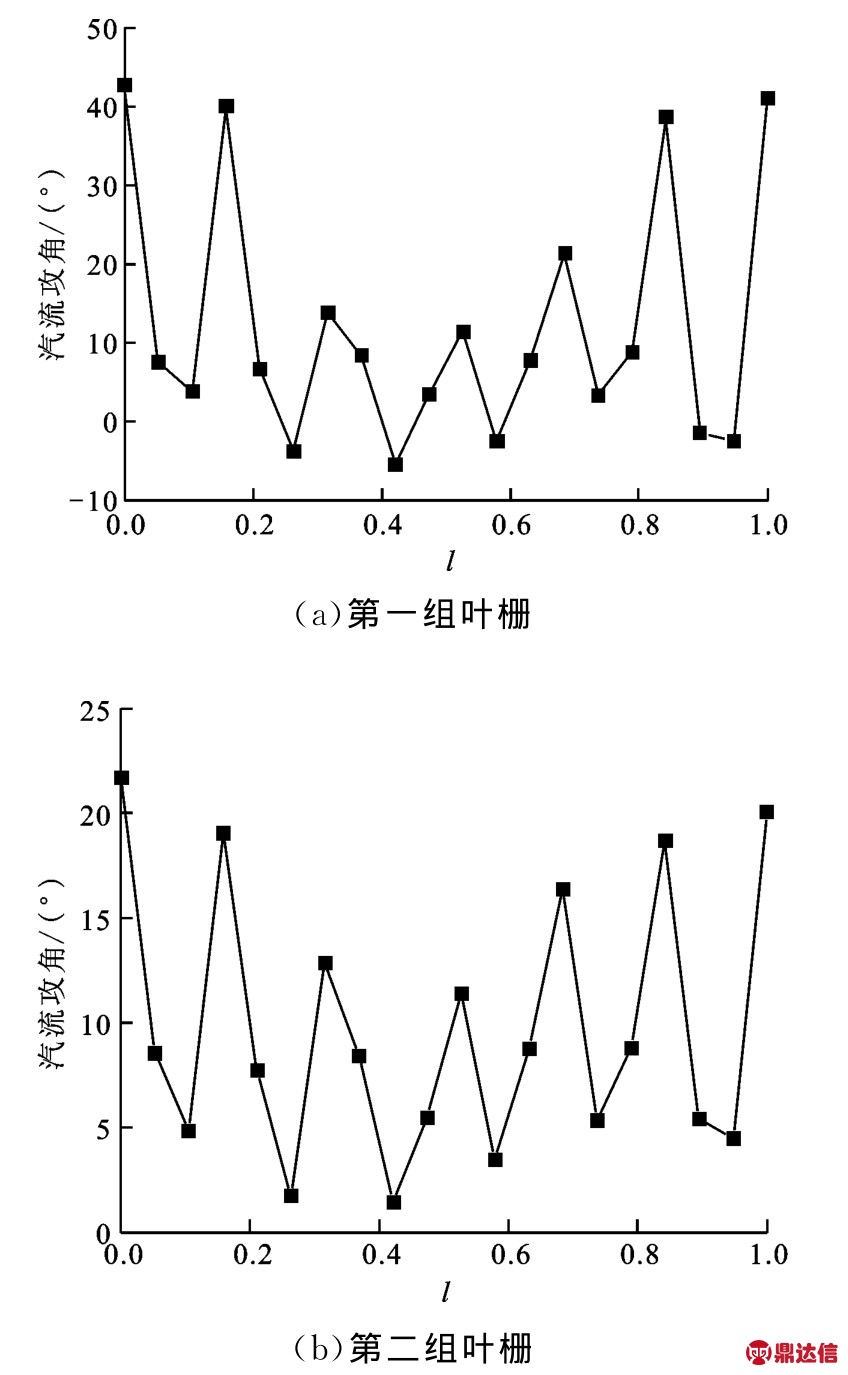
图12 组合分离器中叶栅进口汽流攻角分布
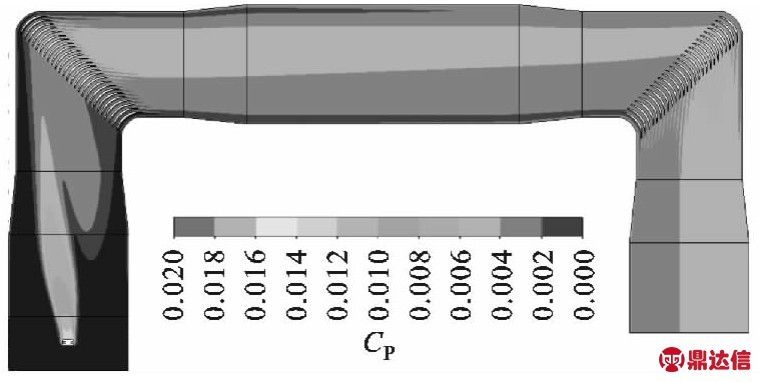
图13 组合分离器叶栅中间截面总压损失系数分布
图14为3种直径水滴在组合分离器中的运动轨迹。由图14可见,与弯管式分离器相比,组合分离器中3种直径水滴的沉积量均有所增多,尤其是直径较小的水滴沉积量增加更明显。
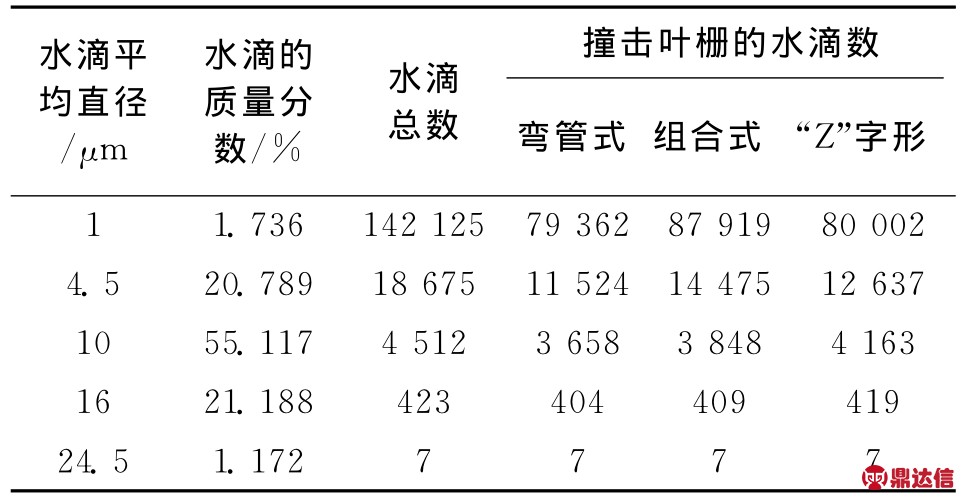
图14 3种直径水滴在组合分离器中的运动轨迹
4.3 “Z”字形弯管分离器的计算结果
图15为“Z”字形弯管分离器中汽相流线分布。由图15可见,总体上分离器中流速分布较为均匀,流线分布良好,汽流沿着圆管轴向流动。
图16为“Z”字形弯管分离器叶栅中间截面总压损失系数分布。由图16可见,汽流在经过导流除湿叶栅时总压降低明显,对应总压损失系数增大,在圆管和过渡段中汽流总压损失系数基本不变。
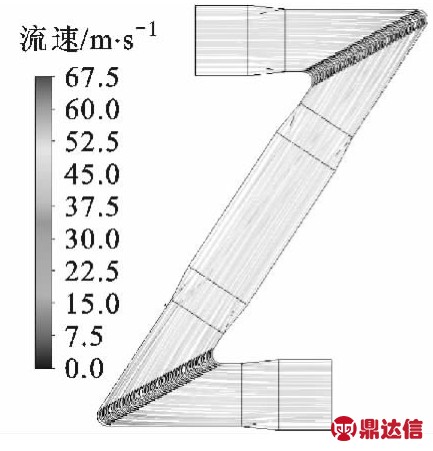
图15 “Z”字形弯管分离器中汽相流线分布
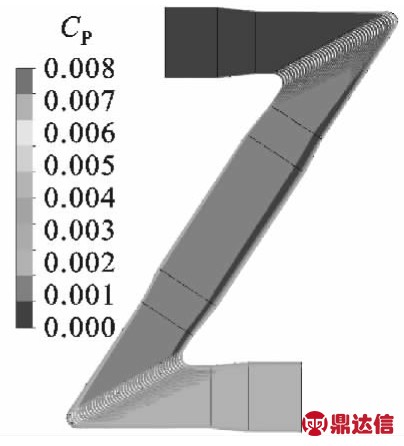
图16 “Z”字形弯管分离器叶栅中间截面总压损失系数分布
图17为3种直径水滴在“Z”字形弯管分离器中的运动轨迹。由图17可见,与弯管式分离器相比,“Z”字形弯管分离器中不同直径水滴的沉积量均有所增多,尤其是直径较大水滴沉积量增加更明显。
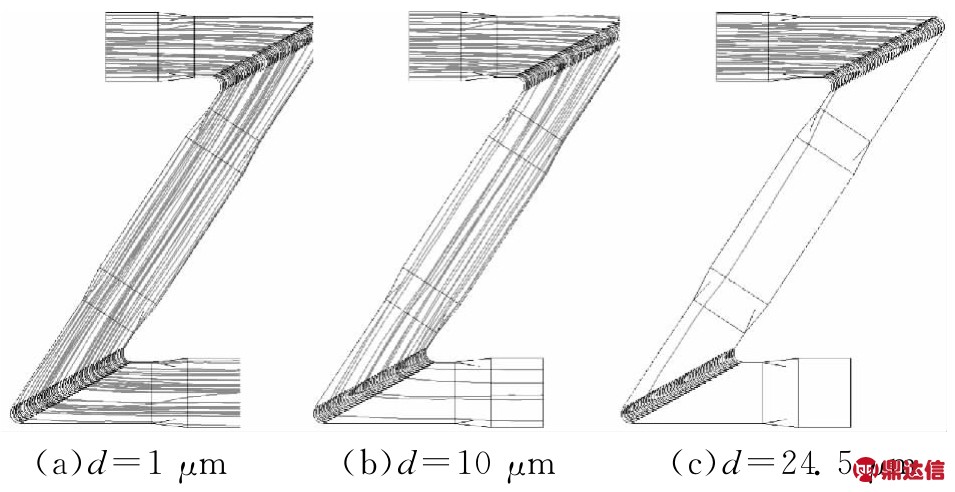
图17 3种直径水滴在“Z”字形弯管分离器中的运动轨迹
5 3种结构分离器的比较
表3为3种分离器水滴沉积数量的统计结果。由表3可见:与弯管式分离器相比,2种改进结构中各种直径水滴的沉积量均有所增多,组合分离器中直径较小水滴的沉积量增加更明显,“Z”字形弯管分离器中直径较大水滴的沉积量增加明显。根据每种直径水滴沉积率及其对应沉积量占总水滴量的质量分数,经加权求和可求得分离器的除湿效率。图18为3种分离器除湿效率和平均总压损失系数对比。由图18可见:弯管式分离器除湿效率和平均总压损失系数分别为79.9%和0.32%,组合分离器分别为85.8%和0.41%,显然在提高除湿效率的同时也增加了总压损失;“Z”字形弯管分离器除湿效率和平均总压损失系数分别为88.9%和0.20%,该分离器在提高除湿效率的同时也大大减小了总压损失。
表3 水滴沉积量统计
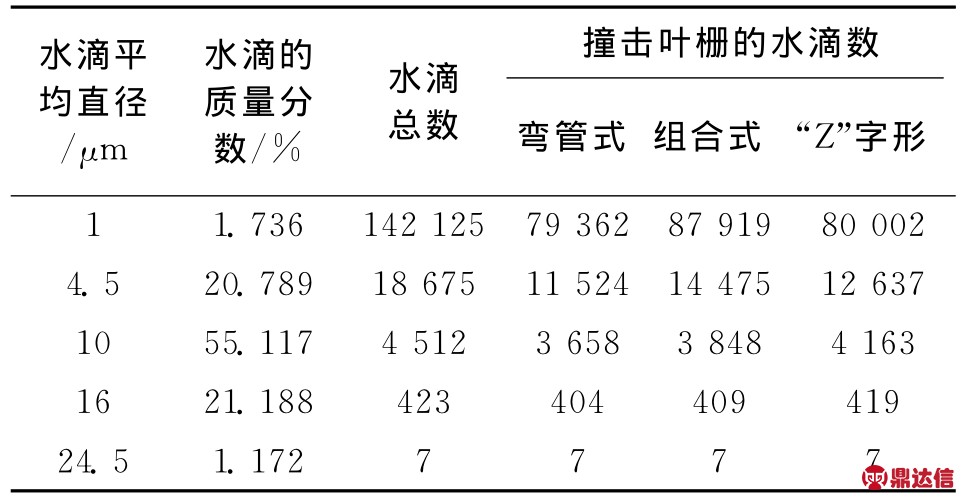
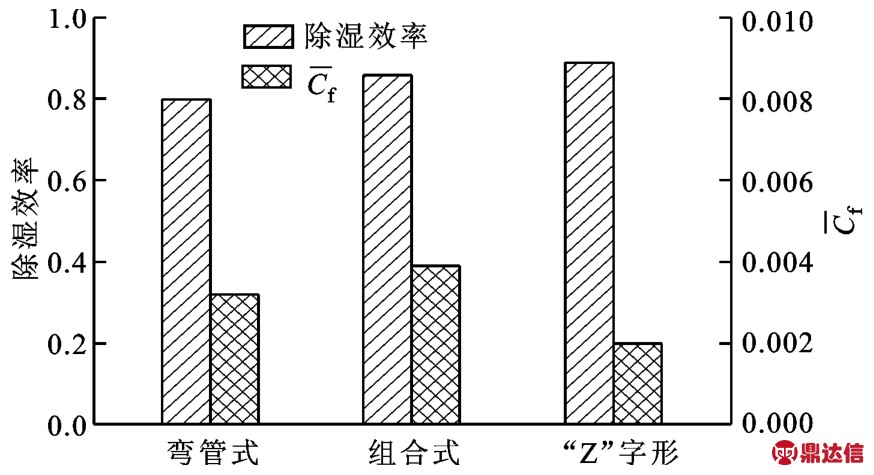
图18 3种分离器除湿效率和平均总压损失系数对比
6 结 论
(1)弯管式分离器和“Z”字形弯管分离器中汽相流速比较均匀,汽流基本沿着圆管轴向流动;汽流经过组合分离器的旋流叶栅后流线发生偏转,流场紊乱,流线经过第二组导流除湿叶栅后与圆管轴向基本一致。
(2)与弯管式分离器相比,组合分离器中直径较小水滴的沉积量增加明显,但同时也增加了总压损失;“Z”字形弯管分离器中直径较大水滴的沉积量增加明显,同时大大减小了总压损失。
(3)在除湿效率和平均总压损失系数方面,弯管式分离器分别为79.9%和0.32%,组合分离器分别为85.8%和0.41%,“Z”字形弯管分离器分别为88.9%和0.20%。显然,本文提出的“Z”字形弯管分离器具有较高的除湿效率和较低的总压损失系数,值得推荐。