摘 要 Shell石油公司研发的SM系列分离器是一种高效的脱水、脱烃设备,对其发展历程、结构组成和工作原理进行了系统的总结,结果表明,采用重力分离与高效内构件相结合的SM系列分离器具有分离效率高、构件模块化等优点,适用于天然气脱水、脱烃装置。针对SM系列分离器开展的气-液分离应用基础研究,有助于了解其内构件工作情况及分离器内液滴平均尺寸分布情况,可为分离器内构件的结构优化设计和分离器性能的进一步提升提供参考。
关键词 天然气 脱水 脱烃 气-液分离器 SM系列分离器
天然气中常含有饱和水、H2S和凝析油等,集输时需进行脱硫及脱水脱烃等处理,脱水脱烃效果决定了外输天然气的品质。脱水脱烃的实质是气液分离,要用到气-液分离设备。除重力分离器、叶片分离器等常规设备外,一些新型设备也逐渐得到推广,如GLCC、超音速分离器(3S)、SM系列分离器及内联脱气器、脱液器等[1-2]。其中,Shell石油公司的SM系列分离器由于分离效率高、处理量大等优点得到广泛应用,安装量已超过600台。国内自长北合作区成立以来,长北、榆林、格里木等气田陆续引进该类设备,推动了国内天然气处理装备的进步,但迄今为止,国内鲜有研究人员对其进行深入研究。以下在查阅相关资料的基础上,对SM系列分离器的发展历程、结构组成、工作原理、工程应用及研发过程中相关的应用基础研究进行介绍,以期为同类应用提供参考。
1 SM系列分离器的发展历程、结构及工作原理
1.1 发展历程
20世纪80年代,Shell石油公司的Stephanus Paardekooper等针对气-液分离器尺寸大、处理量小的不足,将捕雾器和旋流管塔盘组合安装在立式罐中,研发了新式气-液分离器,提高了处理量[3]。随着天然气产量的增加和分离器处理量的增大,Malconlm W McEwan等优化上述分离器的内构件布置,进一步提高了处理量和分离效率。从其所申请的专利来看,该分离器的内构件包括进料分布器、液滴聚结器和管式离心分离器,如图1(a)所示[4]。该分离器处理量大、效率高,符合天然气工业气体流量大、流速波动大的特点。因此,Shell石油公司决定将其产品化。
在产品化的过程中,Shell石油公司自主研发了进料分布器和管式离心分离器,并分别命名为入口分布器(Schoepentoeter)、涡流板(Swirldeck)。捕雾器选用Sulzer Chemtech公司的KnitMesh除沫器(Mistmat)。各内部件按图1(b)所示的顺序组装,选取各名称首字母进行命名,即SMS分离器。
SMS分离器推出后凭借高效、处理量大等优势得到迅速推广,随着部分油气田进入开采中后期,气体含液量升高,SMS分离器暴露出处理后气体达不到管输要求的问题。于是,Shell石油公司在其基础上增加除沫器的数量并合理布置,推出了更高效的SMSM分离器(见图1(c))和SMMSM分离器,从而形成了SM系列分离器。
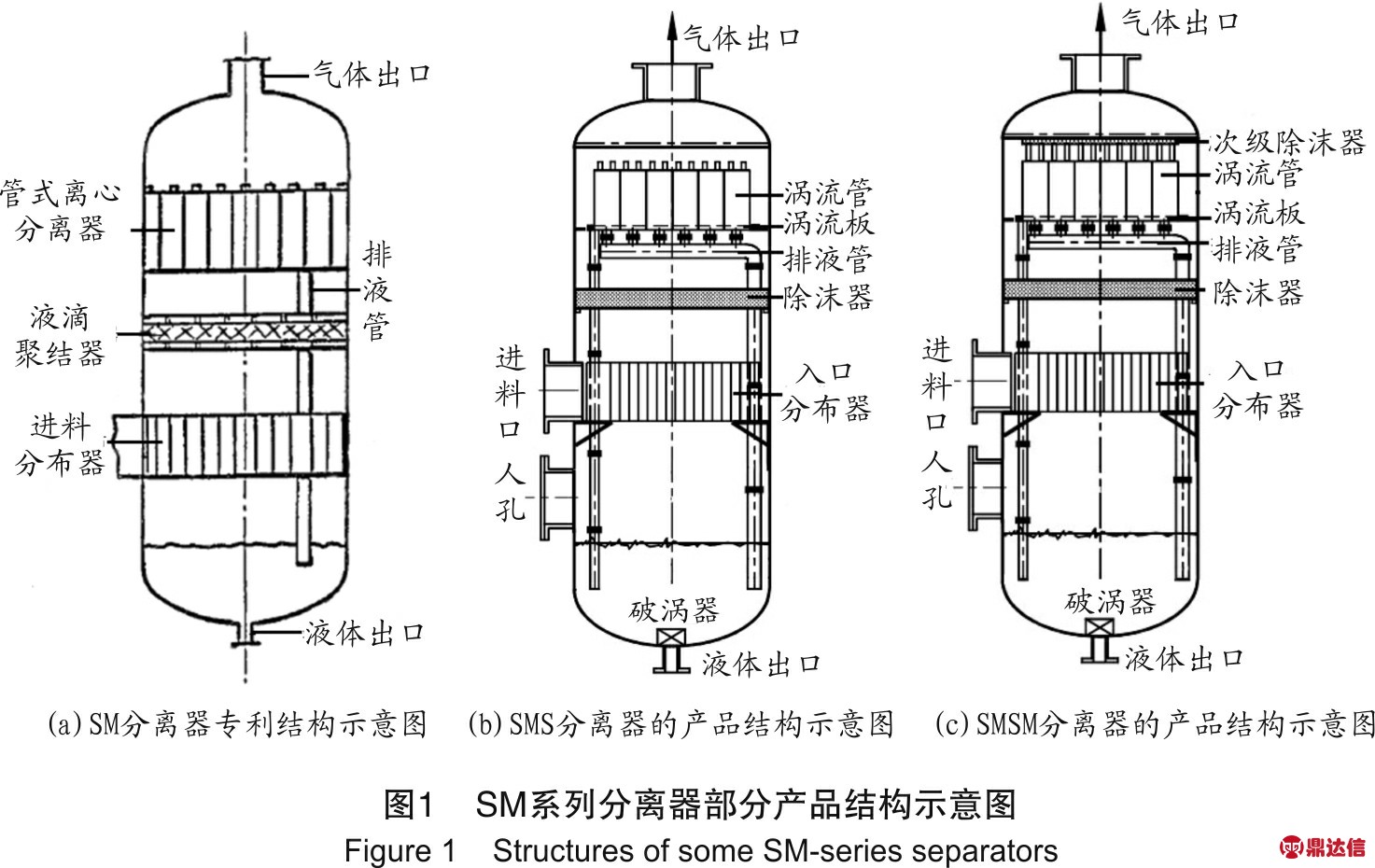
1.2 结构和工作原理
SM系列分离器的主体结构相似,区别在于除沫器的数量及布置方式,以SMSM分离器为代表,介绍SM系列分离器的主要结构及工作原理。
1.2.1 入口分布器
入口分布器是由均布叶片组成的进料通道。如图2(a)所示,叶片前半部分与气流方向平行,起引导、分割气流的作用;后半部分与前半部分垂直,改变气流流向,实现气-液初步分离,实验表明,竖直线状叶片入口分布器可分离50%~70%的液滴。Shell石油公司借助CFD软件对叶片结构进行优化,发现将叶片后半部分由竖直线状改为斜向卷曲状(如图2(b)、(c)所示),可将液滴夹带量降至原来的1/3,据此推出了仅改进叶片结构的新型入口分布器Schoepentoeter Plus [5]。
1.2.2 初级除沫器
SMSM分离器选用Sulzer Chemtech公司的KnitMesh V-Mister作为初级除沫器,其底部安装有如图3所示的V形集液槽。除沫器捕集的液滴聚结落到V形集液槽形成稳定液流后,从两端沿器壁流入集液区,该设计有效降低了二次夹带,使除沫器可在气体流量较大的工况下工作。实验表明,气速达0.15 m/s时该除沫器的压降小于0.25 kPa,而相同压降下的普通除沫器所能达到的最大气速仅为0.107 m/s[6]。
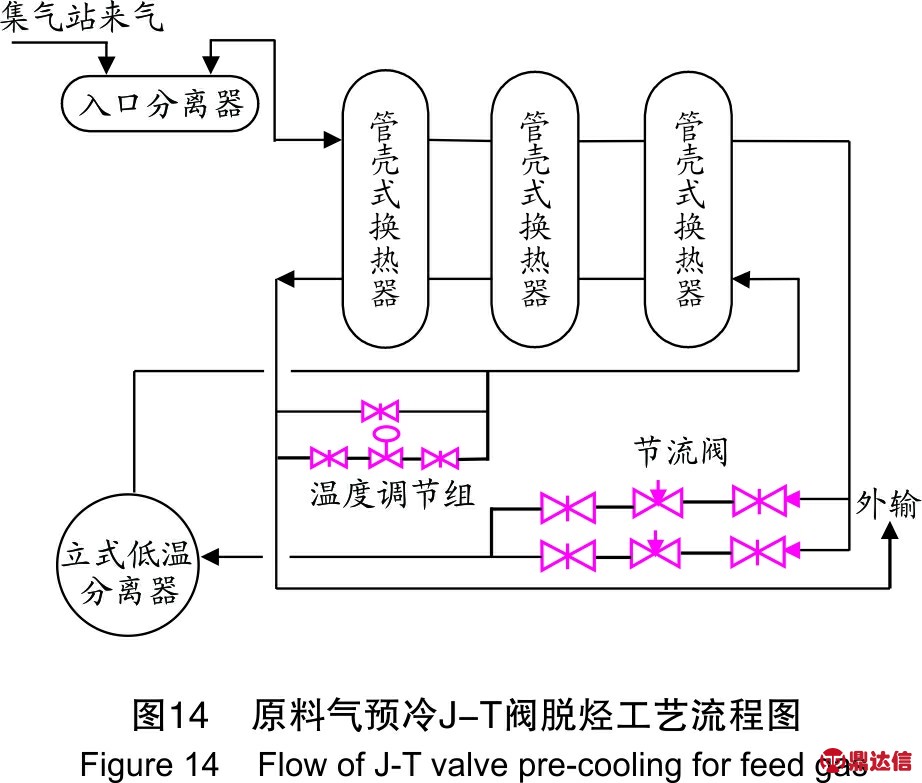
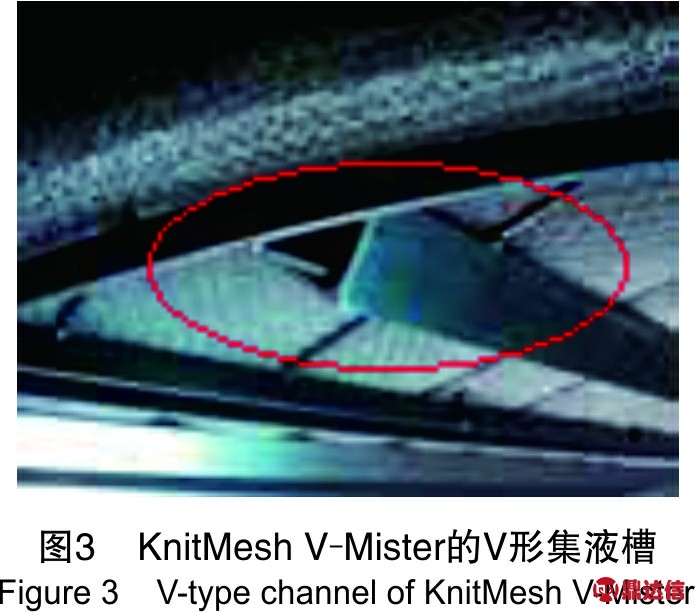
1.2.3 涡流板
涡流板是SMSM分离器的核心部件,用于除去直径约10 μm的小液滴。图4为涡流板横截面图,由图4可知,涡流板由多个接液盒紧密排列而成的涡流盘组成,接液盒内有4~6根涡流管及1根排液管[7]。涡流管结构及与次级除沫器组装示意图如图5所示,涡流管进口端装有旋流器,管壁开有若干排液切口,每个涡流管有1个初级气体出口及4个次级气体出口。
气流进入涡流盘后分散进入各涡流管,在入口旋流器作用下产生旋流。液滴被甩到管壁形成薄液层并向上运动,从管壁切口排出;气体从中心向上运动,经初级气体出口排出。涡流管正常运行时,少量气体会从管壁切口逸出,夹带的液体在重力作用下落入接液盒,从底部的排水管流到集液区;切口逸出的气体从次级气体出口离开接液盒,经涡流管上方的次级除沫器处理后与气体主体部分汇合并排出。
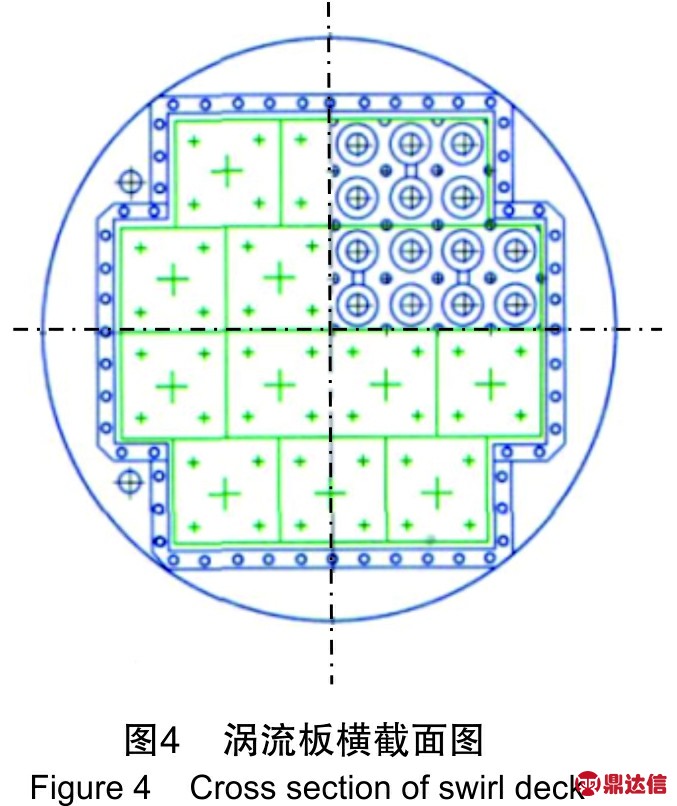
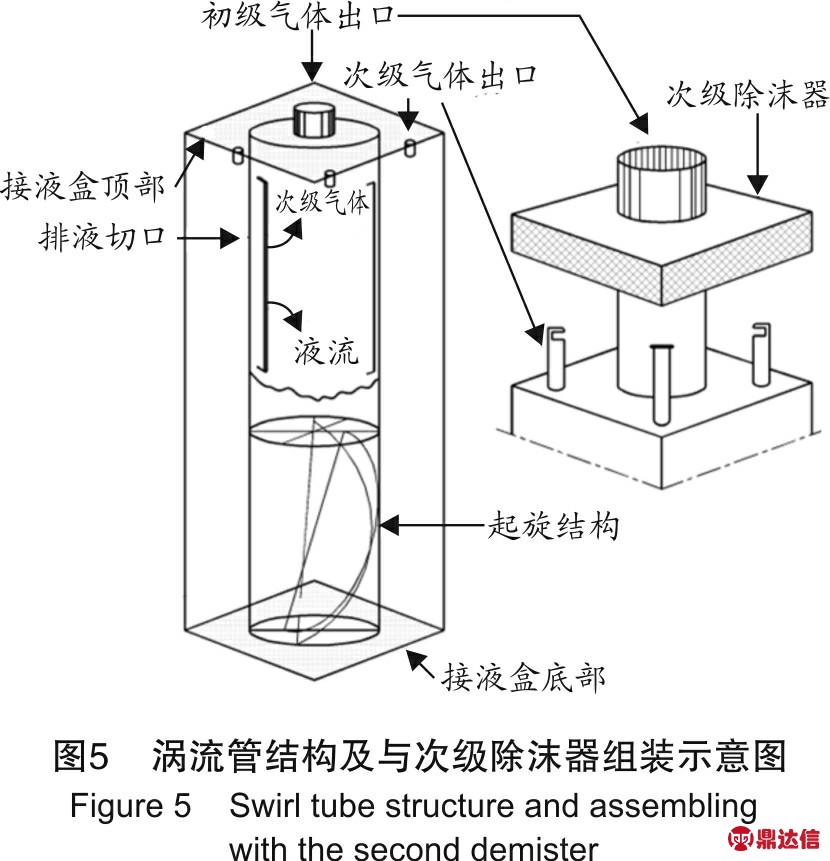
1.2.4 次级除沫器
次级除沫器用于除去次级气体中含有的少量液滴,SMSM分离器选用KnitMesh除沫器作为次级除沫器,可分离最小粒径为2~5 μm的液滴。
2 围绕SM系列分离器的应用基础研究
在SM系列分离器的发展过程中,Shell石油公司与挪威科技大学(NTNU)就气-液分离理论研究展开了密切合作,通过实验研究了丝网除沫器的工作情况,掌握了高压条件下发生液滴夹带时分离器内液滴平均尺寸的分布情况,可为分离器设计过程中相关参数的选取提供依据。
2.1 分离器内丝网除沫器的实验研究
实验装置如图6所示。首先进行常压实验,所用除沫器高为0.1 m、孔隙度为98.06%,介质为含液量0.02%(φ)的水/空气混合物,气速K的范围为0.05~0.17 m/s,待测参数为持液量、压降及液滴尺寸分布[8]。实验时按从下到上的顺序分别选取1 mm、21 mm、41 mm、61 mm、76 mm共5个位置作为测量点,测得的压降和持液量变化如图7所示。
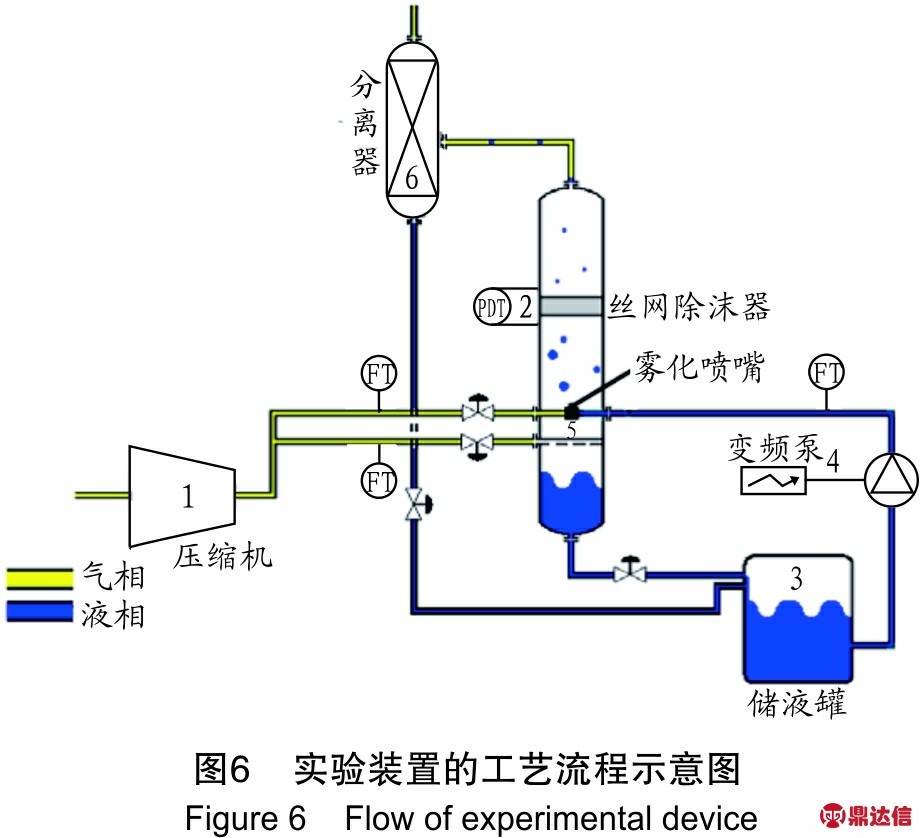
由图可知,当K值小于0.1 m/s时,压降及持液量随K值的增大而增加,所有液滴可被除去;当K值达到0.11~0.12 m/s时,压降及持液量突然增加,除沫器内发生液泛;随着K值继续增大,压降缓慢增加,持液量下降,这可能是由于除沫器内部液滴夹带所致。综合压降及持液量的变化,得出图8所示的分离效率变化趋势,即随着气速的增加,分离效率下降。此外,还测量了K值分别为0.05、0.12、0.13时除沫器下游液滴尺寸的分布情况,见图9[9]。结合分离效率的变化和液滴尺寸分布情况可知,即使发生了夹带,除沫器依然高效,且在满足下游分离单元液相载荷的前提下,工作在液泛模式是较为理想的选择。
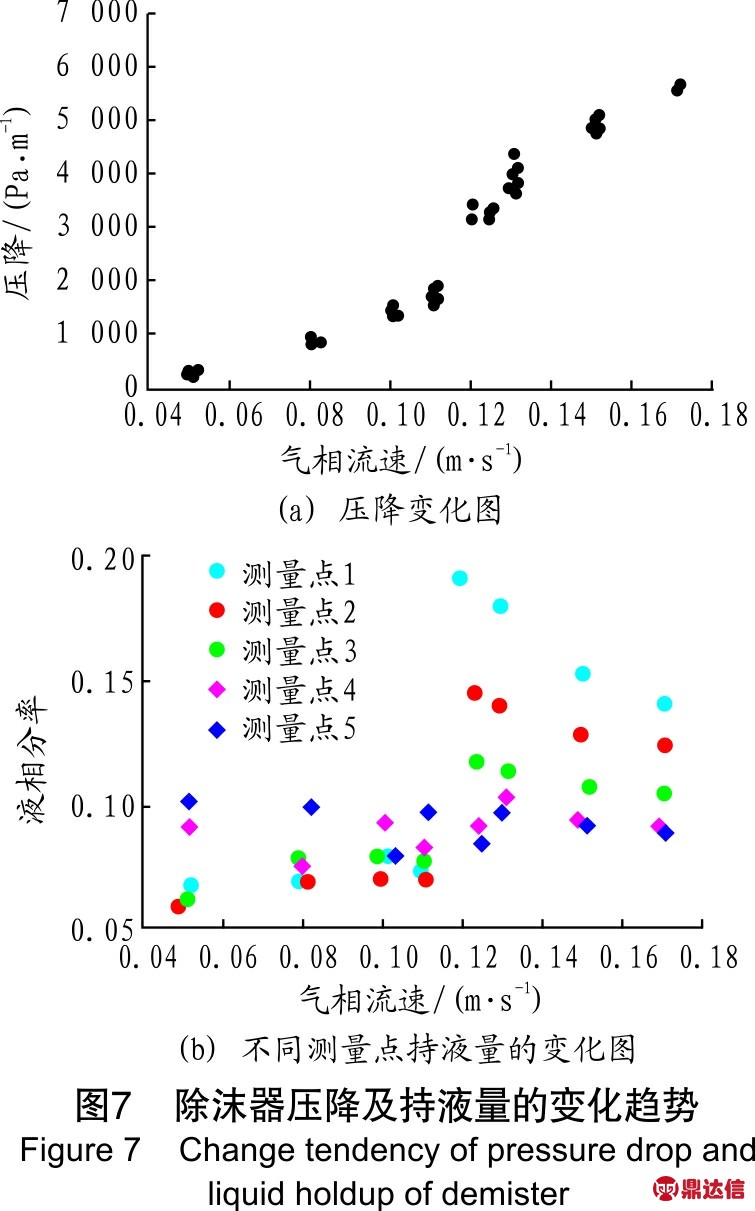
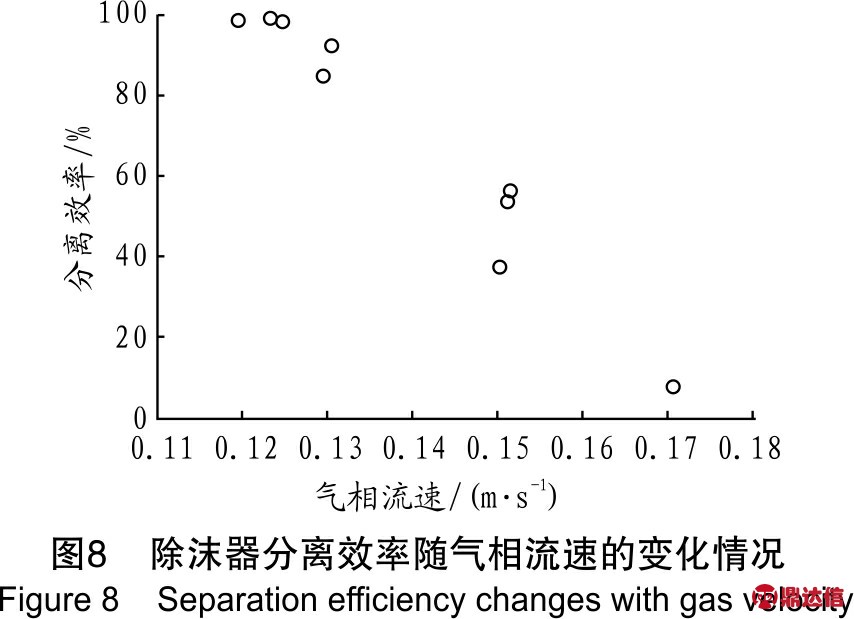
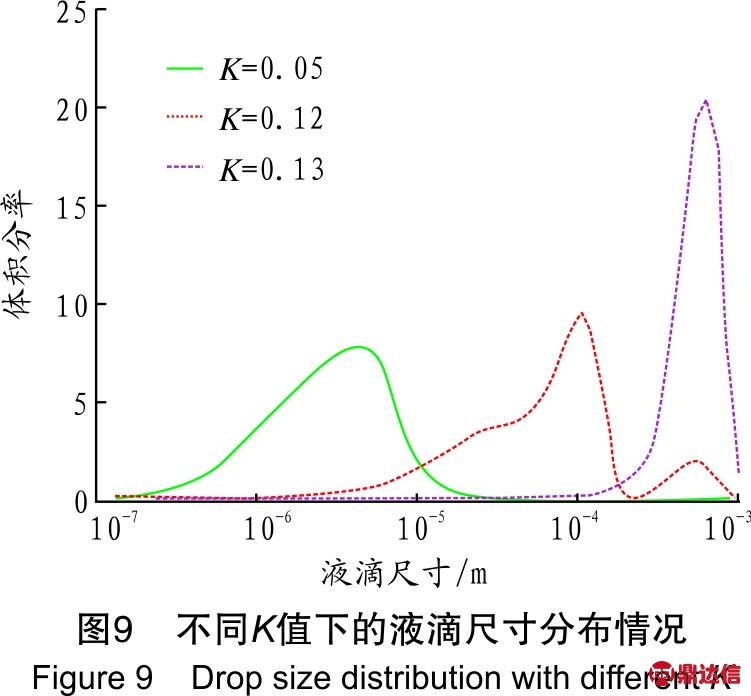
为验证上述结论在实际工况下的准确性,随后进行了高压实验。实验流程不变,仅改用高0.15 m、开孔率为98%的除沫器。分别用含液量为0.2%(φ)的N2/Exxsol和天然气/戊烷作为介质,气速范围为0.07~0.26 m/s,压力范围为2.0~9.2 MPa,待测参数仅为压降。结果均表明,高压下除沫器的工作状况及效率变化趋势与常压相同,即常压实验得出的结论适用于实际工况。
2.2 分离器内不同流态下液滴平均尺寸分布情况的理论预测研究
分离器内液滴尺寸的分布决定了分离效果,由Souders-Brown方程知,已知液滴尺寸时即可进行工艺设计[10]。因此,研究人员研究了高压液滴夹带时,层状流(对应于旋流分离)和线状流(对应丝网除沫器内的流动)对应的液滴尺寸分布,并基于已有研究提出了更准确的计算式。
实验流程如图10所示。层状流实验中用轻烃、氮气作为液相、气相,压力范围为900~1 600 kPa,气速范围为55~120 L/min(标准状况下),液相流率为0.1 L/min,液滴表面张力为24 mN/m;线状流实验中,气、液相为N2、C10H22,压力范围为600~1 600 kPa,气相流量范围为30~100 L/min,液相流量为0.3 L/min,液滴表面张力为23 mN/m。结合实验数据及已有研究发现,用Kataoka等提出的计算式得到的液滴尺寸分布结果误差较大。经过无量纲分析,加入黏度无量纲对其修正,修正前后的表达式见式(1)、式(2)[11]。
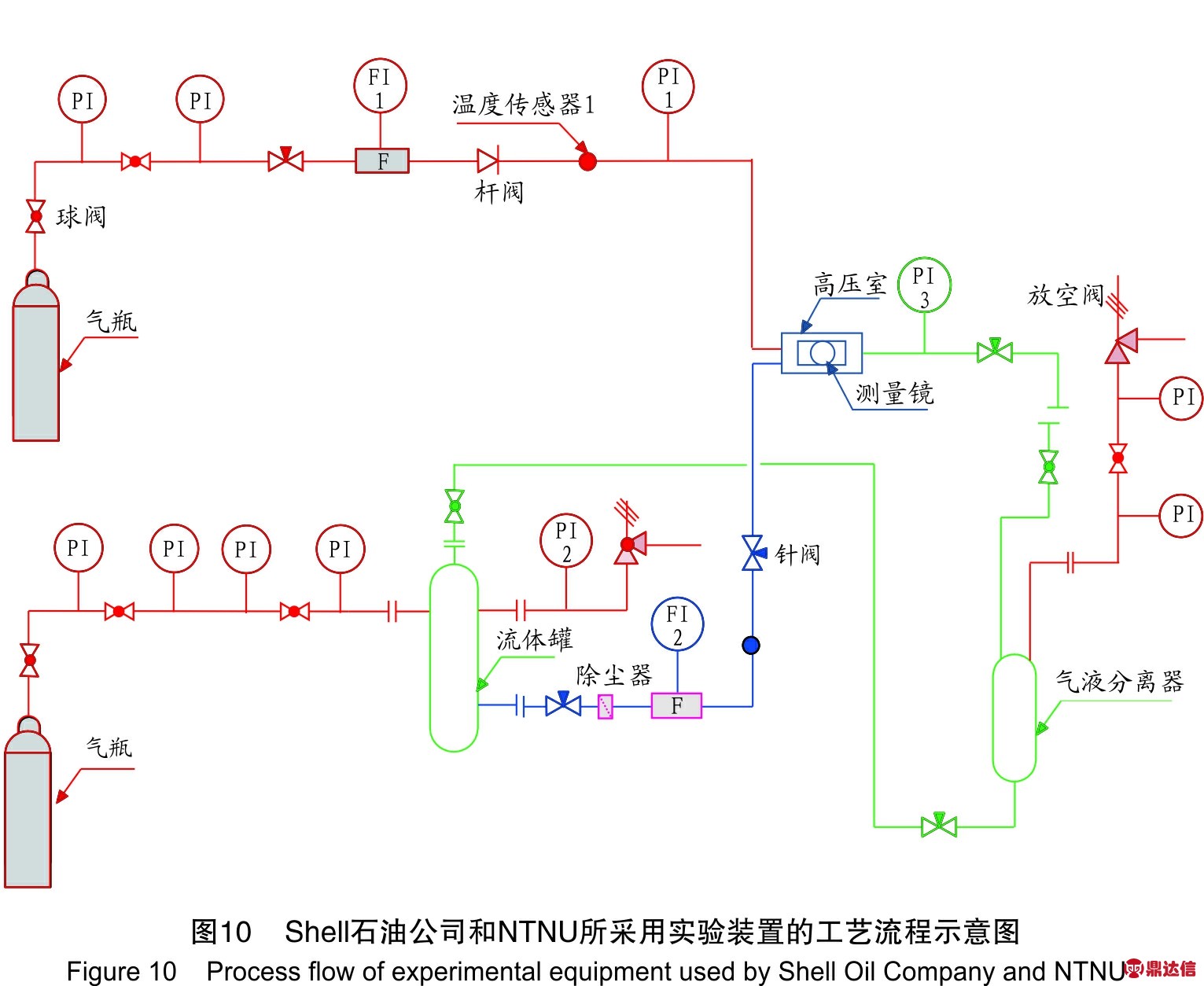
ξr/dCH=0.028WR
R
(ρg/ρl)-0.333(μg/μl)0.667
(1)
ξr/dCH=

(2)
式中,ξr为液滴平均尺寸,μm;dCH为试验装置中的流道直径,dCH=5.66 mm;Weg为气相韦伯数,Weg=;Rel、Reg分别为液相雷诺数和气相雷诺数,Rel=
,Reg=
;CW为黏度系数
为黏度,无量纲,其计算方法见式(3)。
Nμ=
(3)
式中,ρg、ρl分别为气体和液体的密度,kg/m3;ug、ul分别为气体和液体的流速,m/s;σ为液滴间的表面张力,mN/m;μg、μl分别为气体和液体的黏度,cp。
用式(2)计算得到的液滴平均尺寸分布结果与实验数据对比误差较小(如图11所示),可较好地反映液滴平均尺寸的分布规律。
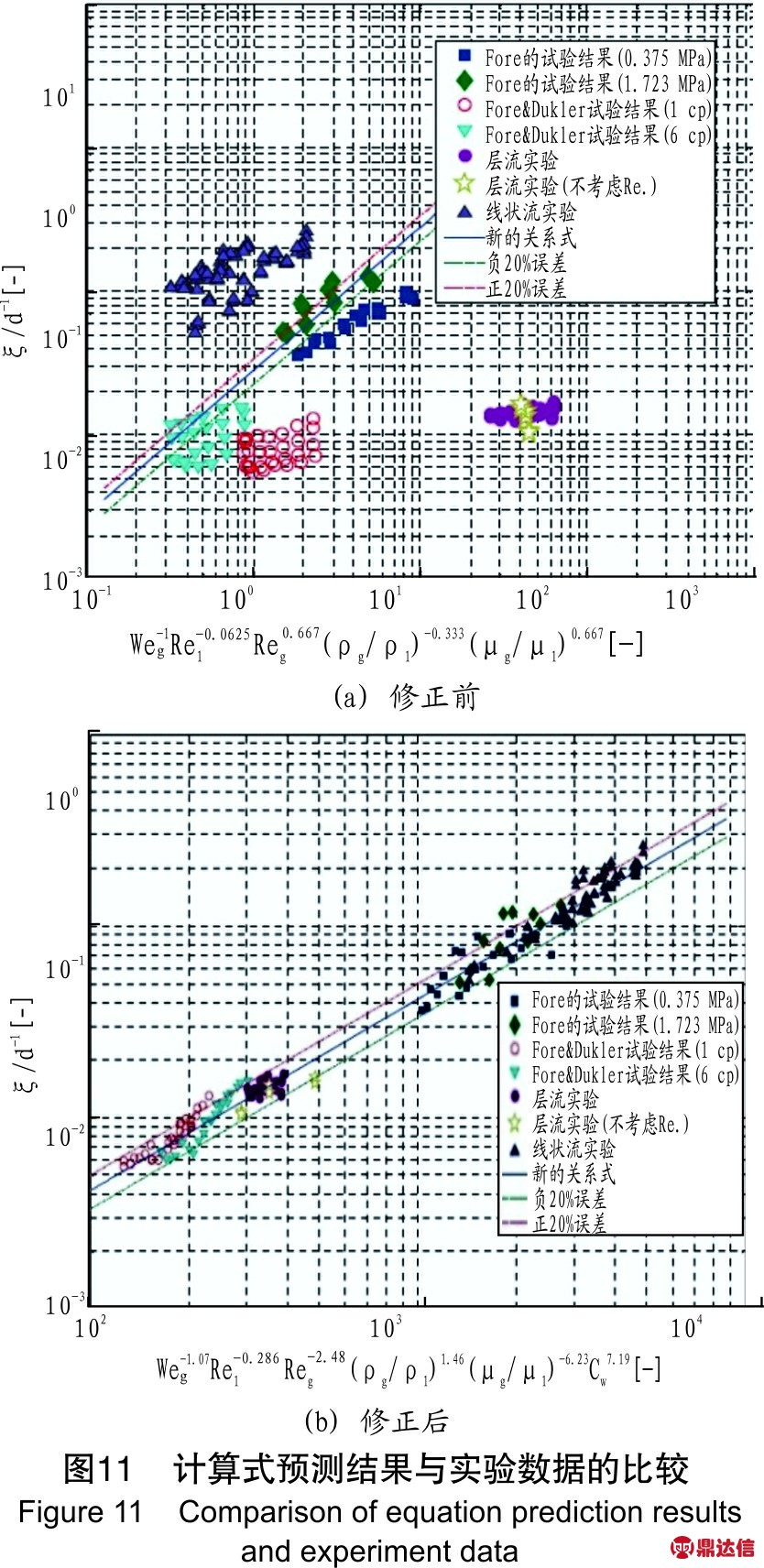
需要指出的是,除了基于实验开展应用基础研究之外,利用CFD软件进行内部流场的模拟也有力地推动了应用基础研究的进行,加快了产品的研发改进,Schoepentoeter Plus即是基于数值模拟结果设计出的产品。
3 SM系列分离器的典型工程应用案例
自SMS分离器投入使用以来,SM系列分离器即受到业内关注,许多油气公司在气体处理系统中安装了此类设备。如荷兰NAM公司的L9油气田、Shell石油公司的海鸥油气田及中国石油长北气田、榆林气田等。以下介绍国内外的2个典型工程案例。
3.1 SMS分离器在海鸥油气开采平台改造中的应用
海鸥油气田采出气经海上平台处理后直接输至英国天然气管网,因此采出气需在平台上完成甘醇脱水、脱H2S、涡轮膨胀机脱烃等操作,以满足水露点、烃露点、H2S含量等要求[12]。平台设计日处理量为1.16×107 m3(410 MMSCF),自2000年9月运行以来,实际处理量始终停留在0.88×107 m3 (310 MMSCF)。经检查发现,在8.3 MPa的操作压力下,TEG吸收塔涤气系统的叶片分离器不足以除去气体中夹带的全部凝析液,部分凝析液进入下游的甘醇再生系统,增加再生系统的发泡倾向,影响重沸器的再生效果,增加重沸器热负荷,降低TEG贫液浓度,进而导致回收系统难以正常运行,最终限制了整个处理系统的生产能力。
为解决该问题,Shell石油公司对涤气系统进行了改造,用丝网除沫器或旋流分离器代替叶片分离器。为选择合适的设备,Shell石油公司对上述3种分离设备进行了实验比较,图12所示结果表明,旋流分离器是最好的选择,因此,Shell石油公司决定在涤气系统使用SMS分离器。
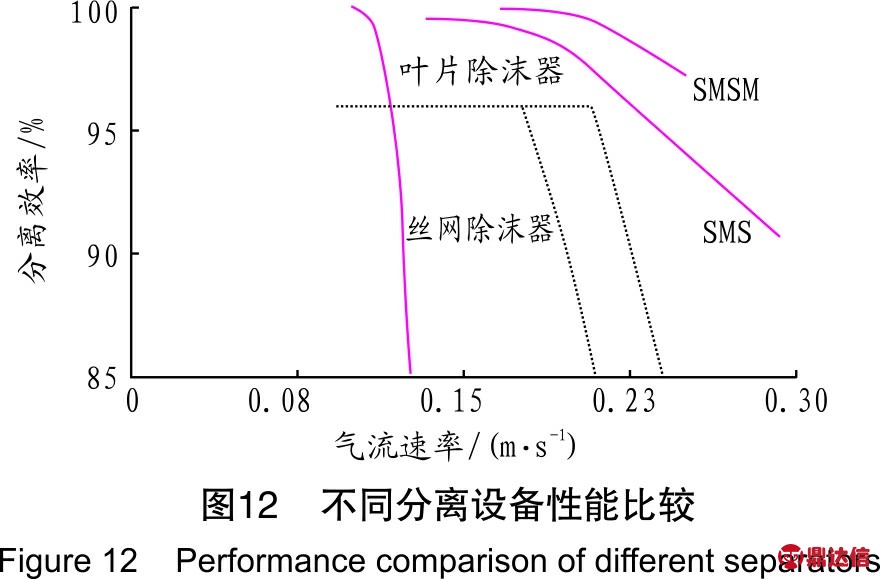
吸收塔主要内构件包括:高为0.6 m的规整填料、升气塔盘、液体分布器和涤气系统(由入口分布器和叶片式除沫器组成)。改造方案要求保留入口分布器,仅将叶片除沫器更换为丝网除沫器和涡流板。改造时发现,叶片除沫器移除后的空间小于1 m,而涡流管高0.5 m,除沫器厚度为0.1 m,支撑件高0.03 m,考虑部件间的安装间隙,1 m的空间无法满足安装要求。为此,Shell石油公司用高0.4 m的高性能涡流管(HPST)代替原涡流管,成功地将涤气系统改造为SMS分离器,改造前后涤气系统的结构对比如图13所示。改造后平台的日处理量增至1.16×107 m3(410 MMSCF),取得了预期效果。
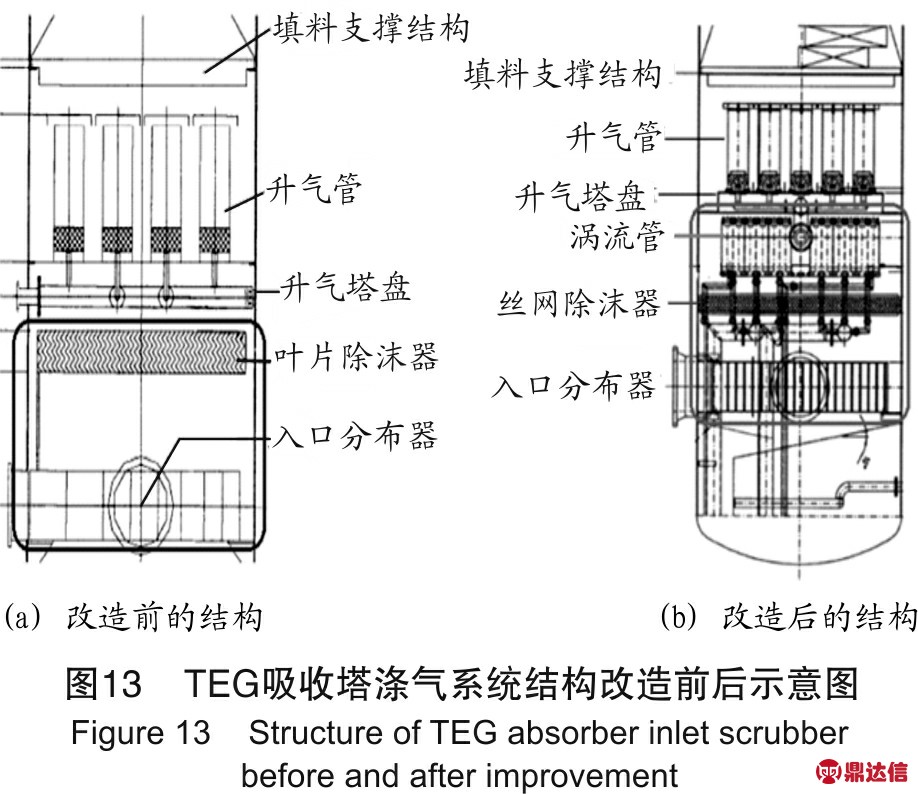
3.2 SMSM分离器在长北气田的应用
长北气田采出气中不含H2S、只含微量CO2,经脱水、脱烃处理后即可输至榆林压气站。气田地面处理工程采用分散脱水、集中脱烃的工艺,即先在各集气站将气体的水露点降至-13 ℃,然后在配气总站集中脱烃,待烃露点达标后外输[13]。配气总站进气温度在2~10 ℃,可利用的剩余压力能为1 MPa,采用图14所示的原料气预冷J-T阀脱烃工艺,利用脱烃后低温产品气换热预冷及J-T阀节流,形成稳定低温,然后借助高效分离器将析出的凝析油分离出来。2003年5月,该工艺投入应用,并选用板翅式换热器作为换热设备,选用卧式重力分离器、颇尔预过滤器和气液聚结器作为三级低温分离设备。实际应用时发现,板翅式换热器易结垢并出现液堵,达不到预期换热效果,影响产品气的烃露点指标;三级分离器处理后的产品天然气烃露点比制冷温度高4 ℃,无法满足生产要求。
2005年,配气总站用管壳式换热器、SMSM低温分离器替换原来的换热设备和三级分离设备,并对SMSM低温分离器和管壳换热器进行了实验。结果表明,SMSM低温分离器平均压差0.32 MPa,满足配气总站的工况要求,分离器出口气体烃露点为-12 ℃,可分离出大部分小液滴,效果较好。换热器换热温差较小(约为1.8 ℃),平均换热效率96%,取得了较好的换热效果。该装置投入使用后运行稳定,无需注甲醇,降低了生产成本;单位压降产生的温降大、运行压差小,减小了上游集气管线运行压力,达到了改造的目的。
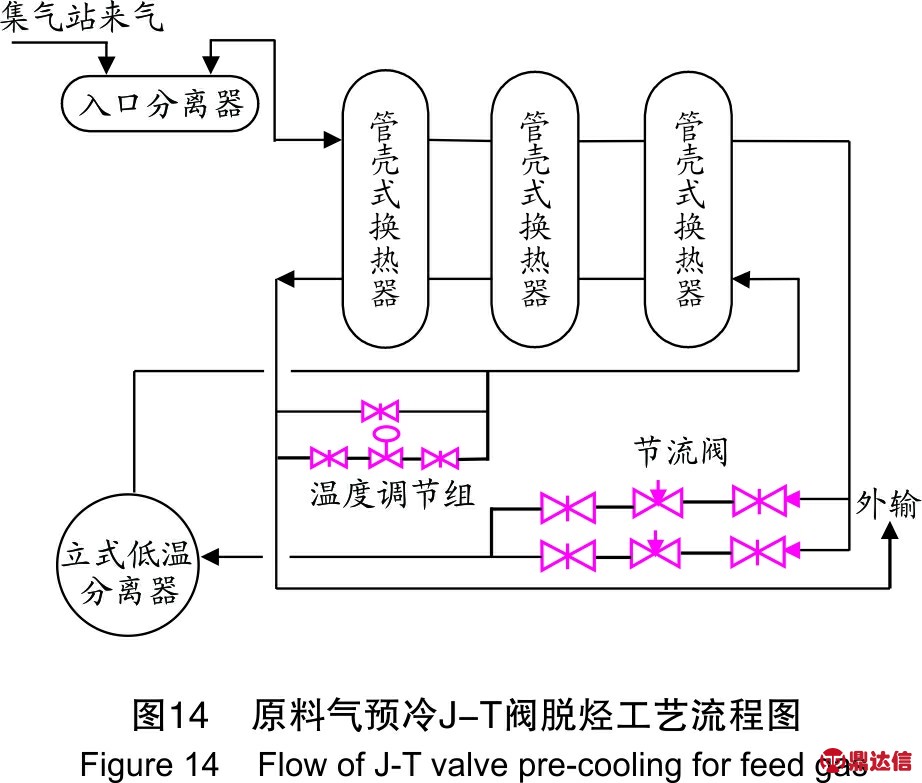
由于SMSM分离器在配气总站取得了良好的工程效果,2006年投产的苏里格气田第一天然气处理厂、2007年投产的长北气田中央处理厂均使用SMSM分离器作为低温脱烃设备,并取得满意的效果[7,14]。
4 结论与建议
(1) SM系列分离器采用重力分离与高效分离元件相结合的设计方法,可灵活地适应不同生产区域和阶段的情况,经过多年的研究和改进,目前已形成了分离效率高、处理量大、调节比高(可达到10,一般的气-液分离器仅为2~4)等技术优势。
(2) 围绕气-液分离过程中液滴平均尺寸分布的应用基础研究,促进了SM系列分离器的研发和分离性能的提高,使分离效率提高到98%~99%;借助CFD软件进行的数值模拟研究,促使相关内构件往紧凑、高效方向发展,体积更小、运行稳定的新型入口分布器Schoepentoeter Plus即为数值模拟研究的产物。
(3) 从SM系列分离器的应用情况可以看出,该系列分离器用于海上平台时主要起涤气器的作用,多用于气体处理系统的改造升级,可使处理量增加20%~30%;用于陆上处理厂时,主要用于低温冷凝脱水处理系统,控制气体的水露点和烃露点,从而在相同的温降条件下获得更低的水露点和烃露点。