摘 要:利用流体计算软件,对两级串联旋风分离器内部流场分布及不同操作参数下旋风分离器的分离性能进行了数值模拟,并将CFD仿真结果与经验模型结果进行了对比分析。结果表明,CFD预测值与经验模型计算结果分布趋势相同;在入口浓度一定时,随入口风速的增大,旋风分离器分离效率提高,压降增加;相同入口速度下,分离效率随入口浓度的增加而降低,压降升高。
关键词:旋风分离器;数值模拟;多相流;分离效率;压降
旋风分离器是一种分离非均相流体混合物的设备,工作介质为空气,利用设备结构形状和流体自身动力,促使气固、气液两相或气液固三相流体高速旋转,产生不同大小的离心力,从而实现气固、气液及气液固分离[1]。其结构主要由旋风筒体、集灰斗和蜗壳三部分组成。由于分离器具有结构简单,没有运动部件,且造价低等优点,广泛应用于石油、化工、冶金等行业。随着能源形式的日益紧张,褐煤干燥提质一体化越来越受到人们的重视[2]。旋风分离器作为褐煤干燥提质设备,其相关性能的研究具有重要的现实意义。在褐煤干燥提质过程中,由于对旋风分离器的分离效率要求较高,使用一台旋风分离器完成分离任务往往不能满足生产需要,这种情况下,多级串联旋风分离器的应用越来越普遍[3]。
本文采用混合多相流模型(Mixture),以山西省辛安煤矿中应用的煤泥干燥系统中的旋风分离器设备为研究对象,对其进行了数值模拟研究,主要分析了串联旋风分离器内流场分布情况,将CFD计算值与经验模型结果进行了对比,并对不同入口速度和颗粒浓度下分离器的分离性能进行了对比分析。
1 计算模型
1.1 物理模型和计算网格
串联旋风分离器结构模型如图1所示,两级入口都为180°蜗壳。旋风分离器的网格划分利用ICEM中自动影射技术,对计算域进行分块,生成六面体网格,网格总数156000,网格划分结果如图2所示。
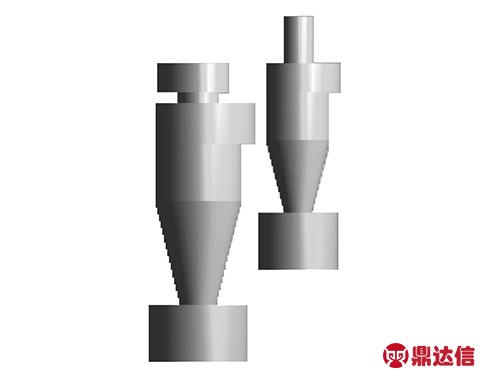
图1 物理模型
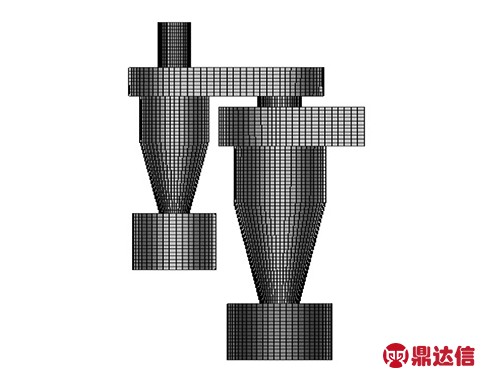
图2 有限元模型
1.2 数学模型
旋风分离器内部为高度复杂的三维、非稳态、带旋转的湍流流动,因此计算中湍流模型选取RSM湍流模型,考虑了湍流的各向异性。
混合相模型可以模拟n相,通过求解混合相的动量、连续性和能量方程,第二相的Volume Fraction方程,以及相对速度的代数表示[4]。控制方程如下:
质量守恒方程:
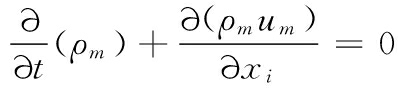
(1)
动量守恒方程:
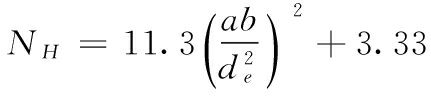

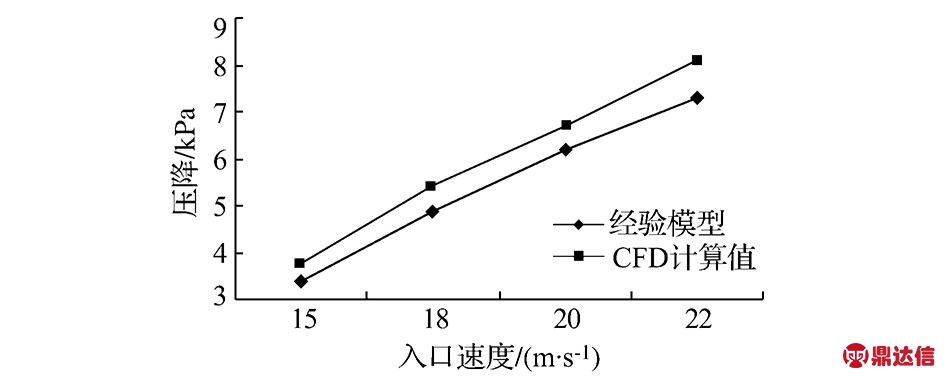
(2)
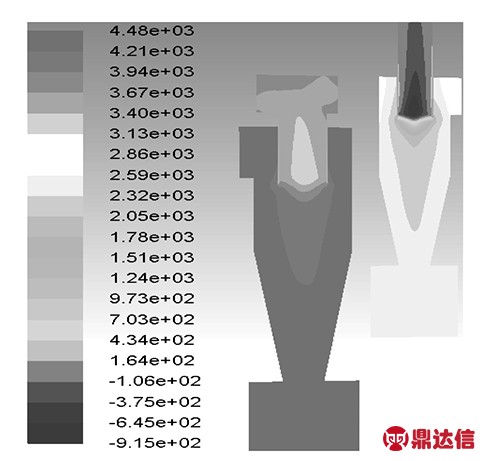
式中,g为重力加速度;umi为平均质量速度;ρm为混合相密度;μm为混合相粘度。
第二相体积分数方程:
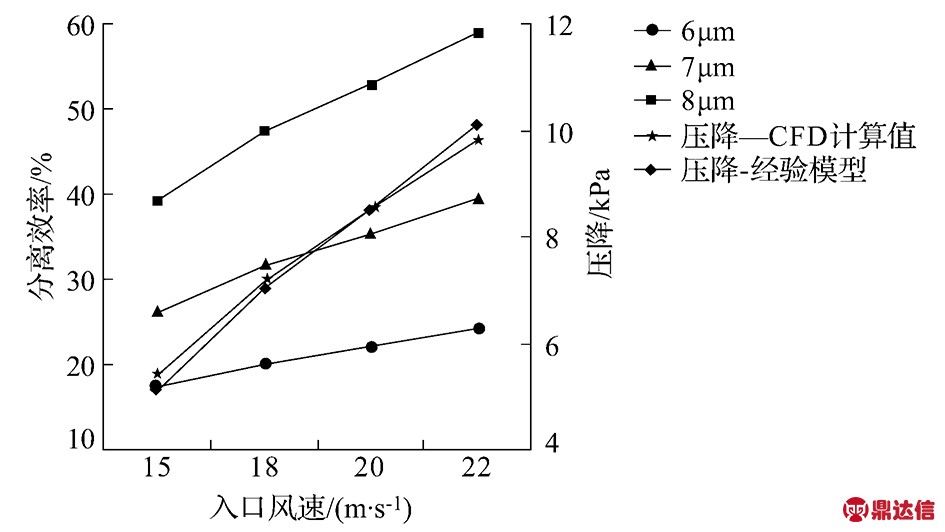
(3)
Reynolds应力输运方程:

(4)
式中,Dij为扩散项;Pij为产生项;Πij为压力应变项;εij为耗散项。
在Reynolds应力输运方程中,包含有湍动能k和耗散率ε,k和ε方程如式(5)、式(6):
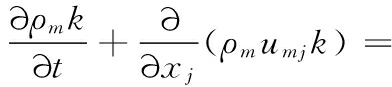

(5)
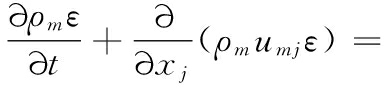

(6)
1.3 边界条件
入口条件:入口采用速度入口,入口速度20m/s。进口湍动能和水力直径分别为3%和420mm。
出口条件:出口采用压强出口,出口压强为0Pa。
壁面条件:固体壁面采用无滑移边界,近壁采用标准壁面函数。
计算用煤粉颗粒,密度为1500kg/m3。
2 计算结果与分析
2.1 气相流场分析
2.1.1 流场分布分析
经计算,在给定边界条件下,两级串联旋风分离器的总压降为6012Pa。两级分离器纵截面静压分布如图3所示。从图中3可看出,两级内静压分布趋势相同,沿径向由外向内静压值递减,到达中心轴线排气管底端处压强最低,这样的分布有利于颗粒的分离。切向速度分布如图4所示,旋风分离器速度分布场中起主导作用的就是切向速度,粉尘在切向速度的带动下高速旋转,因离心力作用被甩向器壁而分离,切向速度越大,离心力越大,分离效率越高。从图4看,切向速度具有很好的轴对称性,排气管半径位置切向速度最大,此处是内部强制涡和外部自由涡的分界处。
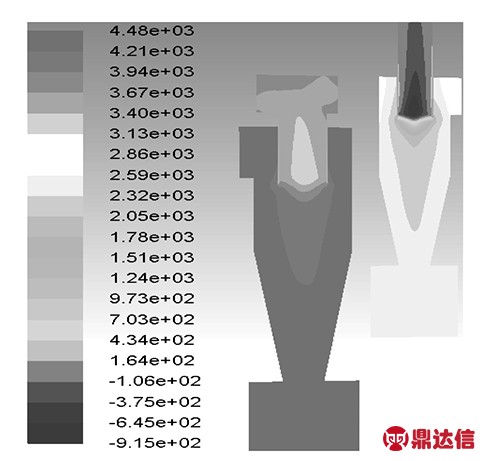
图3 静压分布云图

图4 切向速度分布云图
2.1.2 压力损失计算结果与分析
压力损失修正公式为[5]:

(7)
式中,C为入口型式阻力系数,180°蜗壳入口取C=0.4;NH为进口速度水头。
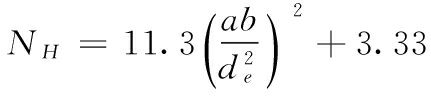
(8)
不同入口速度下,纯气相流场旋风分离器压力损失CFD计算值与经验模型结果的对比如图5所示。
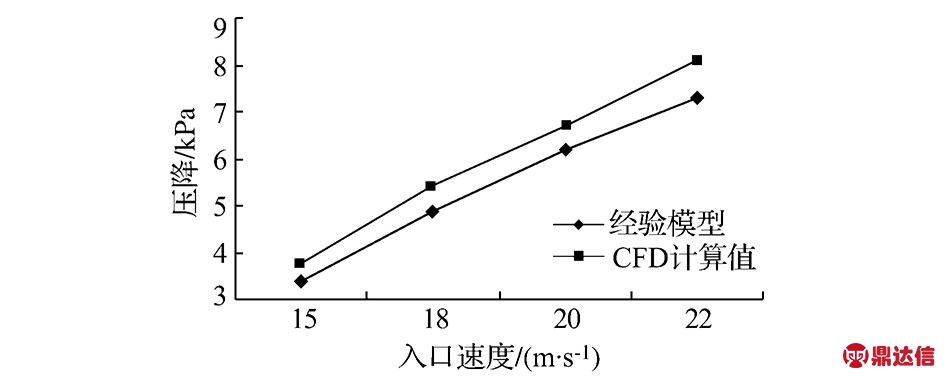
图5 不同入口风速下压力损失比较
由对比结果可知,不同入口风速下的压力损失分布趋势大体一致,但二者之间存在一定的差距。这主要是由于经验模型的局限性及仿真计算中对模型的一些理想化处理所致。图5也表明了CFD可以用于旋风分离器压力损失的预测。
2.2 操作参数对分离性能的影响
2.2.1 入口速度对分离性能的影响
两级串联旋风分离器在不同入口速度下,6μm、7μm、8μm三种粒径颗粒的分离效率以及分离器的总压降如图6所示。由图6可知,在相同入口浓度下,随入口风速的增大,分离效率提高。这是由于入口风速增大,增加了离心力,最终分离效率提高。随颗粒粒径的增大,效率提高的幅度越大,即入口风速对大粒径颗粒的分离影响较明显。
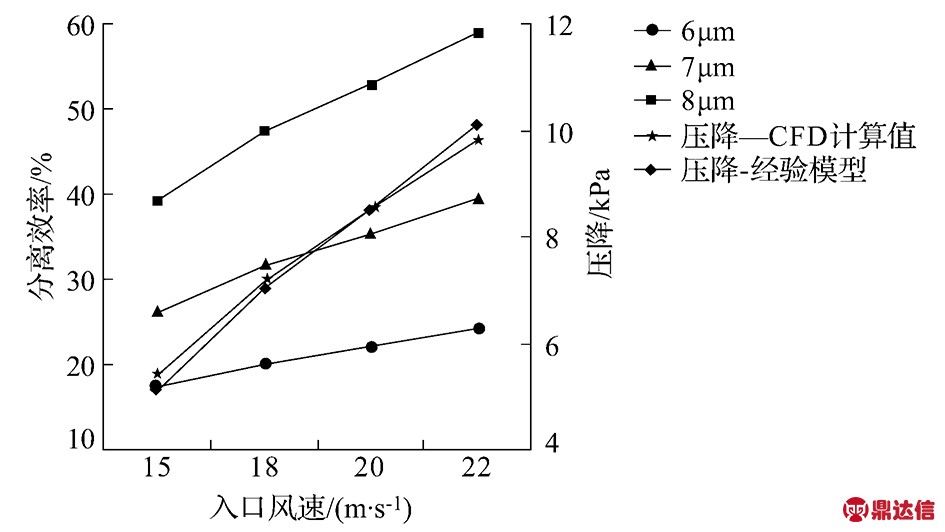
图6 不同入口速度下分离效率和压降
入口风速增大,有利于颗粒的分离,但同时也会导致压降的增加,通过CFD预测和经验模型计算,两种情况下得到的不同入口风速下的压降变化分布趋势一致,随入口风速的增大,压降升高。由Stairmand压降理论计算公式可知,压降与入口速度的平方呈正比[3]。可见,入口速度的改变对压降的影响非常显著。因此,若要通过提高风速来提升分离效率,具有一定的局限性,而且Svarovsky曾指出当入口风速(压降)非常高时,旋风分离器的分离效率反而会逐渐降低[3]。文献[1]也通过实验得到了相同的结论,这是由于返混和颗粒反弹的影响,导致的分离效率的降低。
2.2.2 入口浓度对分离性能的影响
不同入口浓度下,串联旋风分离器的分离效率和压降的变化如图7所示,将CFD预测压力损失值与经验模型计算得到的压力损失值进行了对比,两者分布趋势一致,曲线大体吻合。从图7中可看出,随入口浓度的增大,分离器的分离效率降低。这是由于在相同入口气速下,颗粒入口浓度升高,降低了旋风筒内的流速,导致离心力降低。另外,固体颗粒的增多导致了粒子间的相互干扰的增加,使煤粉颗粒分离困难。
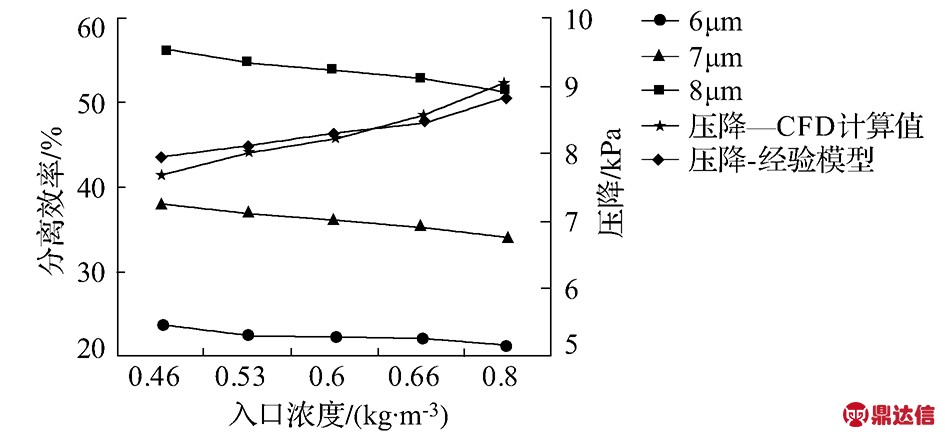
图7 不同入口浓度下分离效率和压降
由图7可知,压降随入口浓度的升高而增加,因为当入口颗粒浓度增加时,一方面因离心力被甩向器壁的颗粒会降低气流边界与器壁的摩擦损失、湍流损耗;另一方面进、出口处局部流动损失因气固两相混合物密度增大而增加。当后者造成的结果显著于前者时,压降升高。
3 结 论
1)CFD仿真计算得到的压降值与经验模型结果分布趋势一致,两者之间具有一定差距,CFD可用于旋风分离器压力损失的预测。
2)相同入口浓度下,随入口速度的增加,两级分离器的总分离效率升高,压降随之增加。
3)相同入口速度下,随入口浓度的增加,分离效率降低,压降升高。