摘 要:对某新型六缸天然气气体机的油气分离器进行了试验研究,初步探索了运行参数对分离器内部温度、压力损失和分离效率的影响。试验结果表明,窜气量的变化会对油气分离器的内部温度、压力损失、分离效率产生影响:在不同的窜气量条件下,迷宫式油气分离器内部的温度变化趋势基本一致。随着窜气量的增大,油气分离器内部的整体温度升高;精滤孔板处的压力损失量最大,且随着窜气量的增大而增大;分离效率随窜气量的增大而不断提高。
关键词:气体机;迷宫式油气分离器;运行参数;窜气量;分离性能
油气分离器是曲轴箱通风系统的重要部分[1],其性能直接关系到发动机的污染物排放水平。为衡量迷宫式油气分离器的分离性能,本文研究运行参数(窜气量)对油气分离性能的影响,进行了气体机油气分离器性能台架试验。
1 迷宫式油气分离器结构
迷宫式分离器外部结构如图1所示,主要由缸盖罩箱体、进出气口、入口挡板、粗滤和精滤盖板、回油槽、粗滤和精滤回油管组成。粗精滤盖板与回油槽为一体结构,用于收集分离的机油,其结构如图2所示。曲轴箱窜气从迷宫入口进入,入口挡板与进气入口平面呈一定角度,可初步阻拦部分从摇臂、弹簧等处飞溅起来的大颗粒油滴。
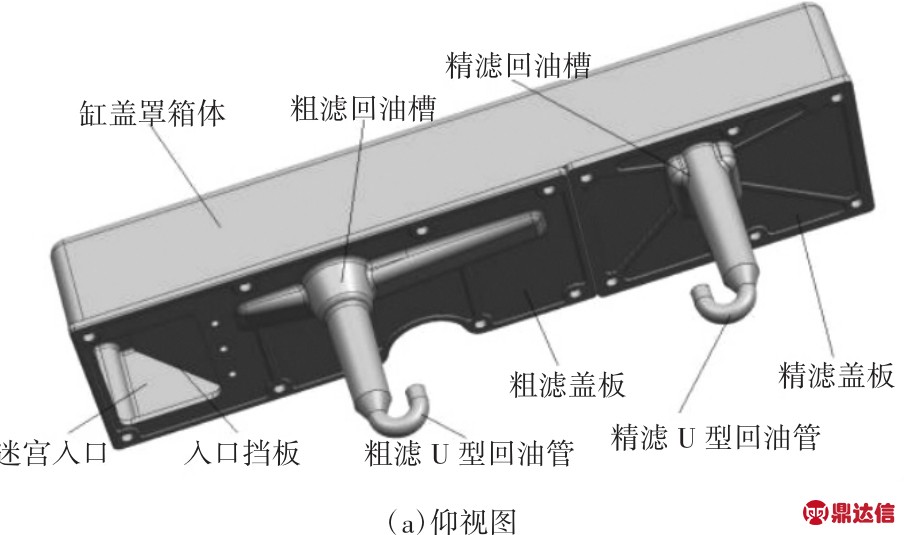
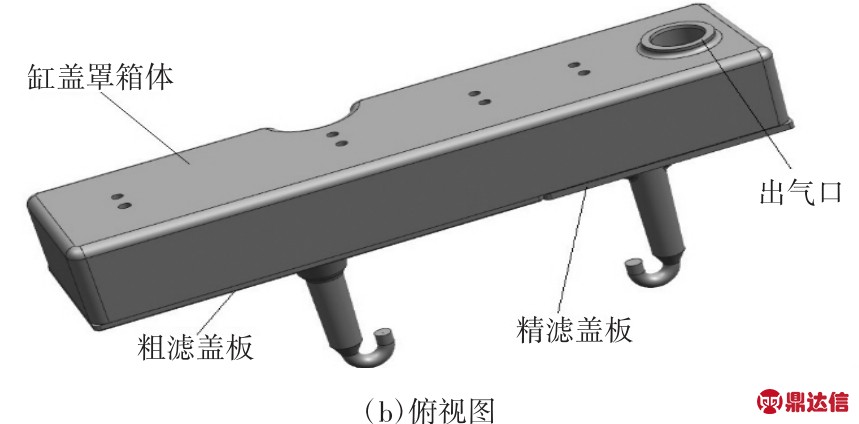
图1 油气分离器外部结构
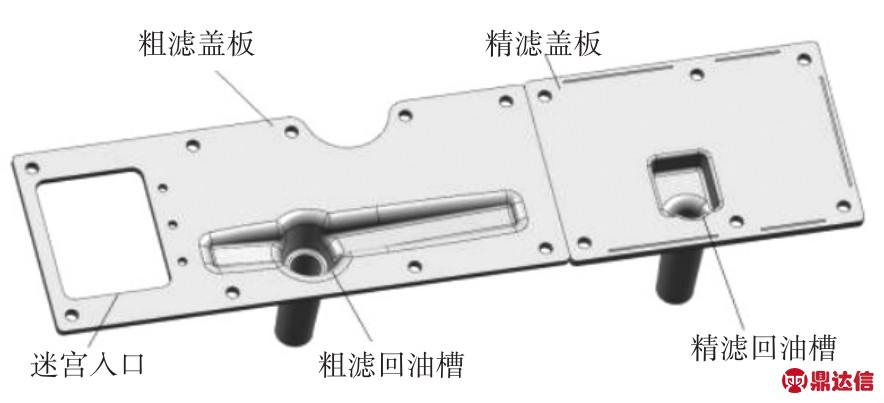
图2 粗滤和精滤盖板及回油槽的结构
图3 为油气分离器箱体的内部结构。箱体内不同侧面设置有多道挡板,插入孔板与挡板相配合形成迷宫式结构。当曲轴箱窜气从进气口进入油气分离器后,在内部挡板的引导下,呈蛇形曲线流动。通过孔板处气流加速和挡板的阻拦,使得部分油滴撞击到挡板上,从而实现油滴与气体的分离。通过两个粗滤孔板、1个精滤孔板与挡板的多次作用,多数大颗粒和部分小颗粒油滴即可与气体实现分离。分离出的机油回流并聚集在粗滤和精滤盖板上,在重力作用下沿回油槽斜面向回油管流动。回油管设计成U型,机油进入U型管道形成油封,可以防止曲轴箱气体从回油孔流出,保证油气分离器的密封性。分离器顶部布置温度和压力传感器,分别监测油气分离器内部不同位置(迷宫入口、粗滤板后、精滤板后)的温度和压力,位置如图2所示。
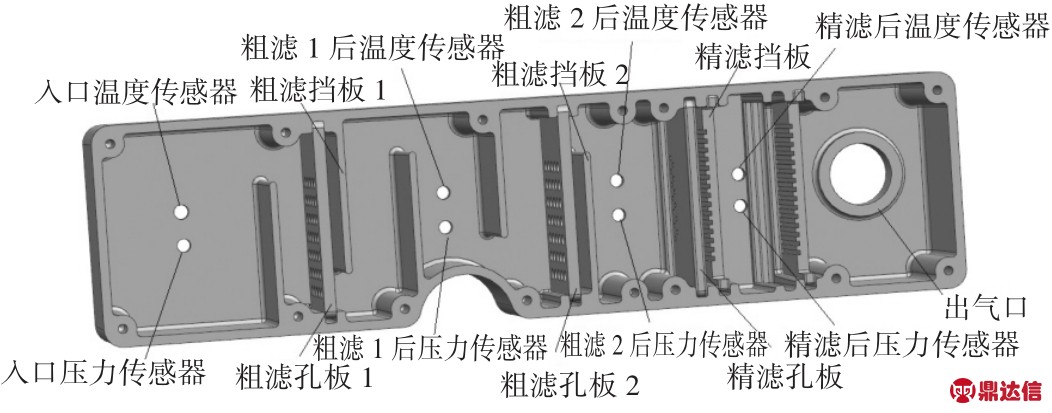
图3 油气分离器内部结构
2 试验方案
2.1 试验台架
试验采用一台六缸直列式压缩天然气发动机,缸径120 mm,压缩比为11,标定功率250 kW.采用闭式油气分离通风系统进行试验研究。闭式油气分离通风系统实验台架如图4所示。闭式通风系统的迷宫式油气分离装置的出气口处接上油气收集工装后,还需将收集工装的出口与膜式燃气表进气口相接,膜式燃气表的出气口接入压力控制阀(PCV),再接到空气滤清器后方的进气管。PCV的作用是阻止发动机的回火,即避免引起曲轴箱爆炸[2]。PCV通过曲轴箱与进气管之间的压力差来调节窜气流量,使曲轴箱压力稳定在一个合适的范围内。一般情况下,曲轴箱压力必须保证在-2.5~1 kPa[3]。
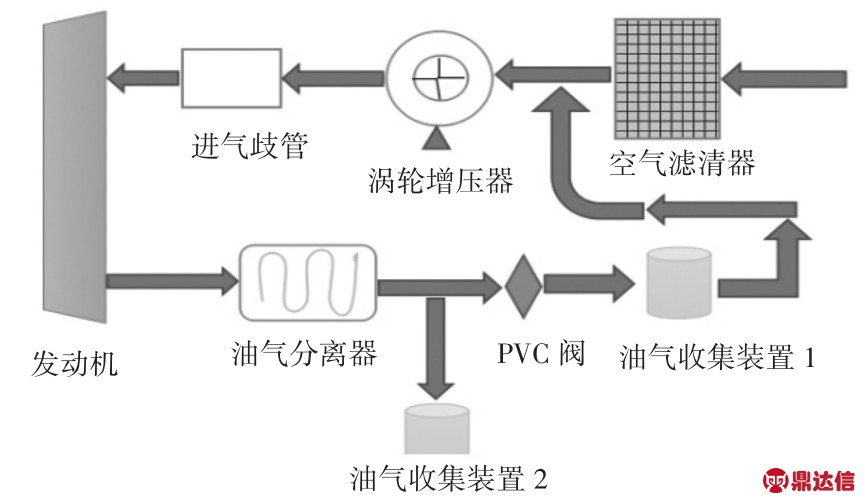
图4 试验台架示意图
曲轴箱中的窜气流经迷宫式油气分离器,一部分窜气中的机油液滴被分离器分离并由收集装置2所收集,这部分机油的量称为回油量。未被分离出来的机油液滴则被收集装置1所收集,此部分机油的量称为窜油量。收集装置由外壳与滤芯组成,有入口与出口两端,窜气经工装流过时,未被分离的机油便由滤芯吸收。分别测量油气收集装置1、2试验前后的质量变化,即可得出窜油量、回油量。油气分离效率即为回油量与总油量的比值,其中总油量为回油量与窜油量之和。
2.2 试验方法
选择全负荷、标定转速(2 100 r/min)的运行工况研究窜气量对油气分离器性能的影响。为了实现不同的窜气量,采用不同的活塞环,通过活塞环间隙的变化间接调节活塞窜气量的大小。首先,采用活塞漏气量仪AVL442测量发动机在此工况下的曲轴箱窜气量,然后使用油气收集装置测量窜气量不同时的回油量、窜油量,计算得到不同窜气量下的油气分离效率。试验过程中,每隔10 min进行一次测量,共进行6次,最终测量值采用加权平均计算得到。温度、压力的分布则通过布置在油气分离器上的温度、压力传感器测量得到。
3 试验结果与分析
3.1 窜气量对温度的影响
温度是油气分离器分离性能实验中监测的重要指标之一。如果油气分离器内部的温度过低,水蒸气容易凝结成液滴通过回油管回流到油底壳中,造成机油乳化变质,造成零部件之间磨损加剧,使用寿命降低。因此,控制好油气分离器内部的温度高于水蒸气冷凝温度很有必要。
由图5可知,在不同的窜气量条件下,迷宫式油气分离器内部的温度变化趋势基本一致。总体上看,从迷宫入口到精滤孔板后呈下降趋势,只是在经过粗滤孔板1后略有上升,只有1℃左右。其中,温度降幅最大发生在粗滤孔板2之间,降幅达到了3~4℃左右。随着窜气量的增大,油气分离器内部的温度也越高:窜气量为180 L/min时,粗滤孔板1、2后以及精滤孔板后的温度都是最高的。原因在于随着窜气量的增大,随气体进入油气分离器内部的热量也越多,因而温度也越高。
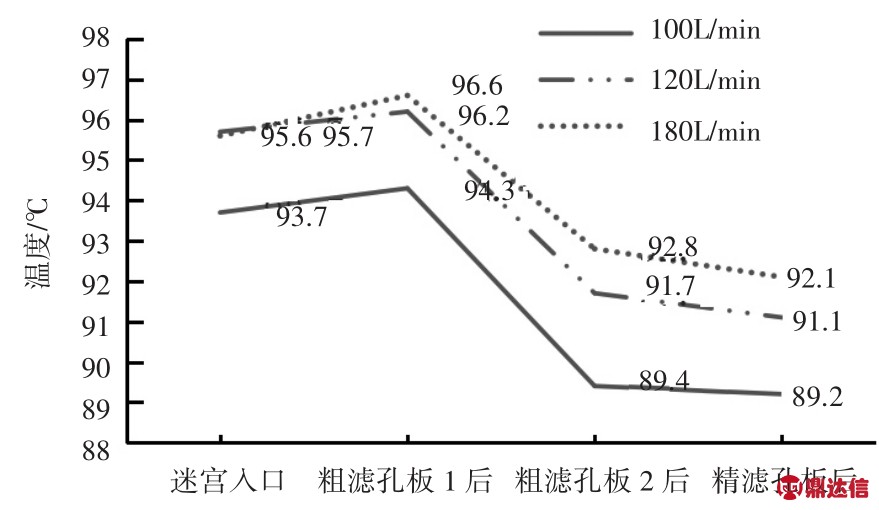
图5 窜气量对油气分离器内部温度的影响
3.2 窜气量对压力的影响
油气分离器内部的压力分布情况也是监测的重要指标,通常用压力损失来衡量。如果油气分离器内的压力损失过大,说明气流在流经迷宫时受到的阻力过大,曲轴箱内压力可能超过许用压力。同时,压力损失也从侧面衡量了气流动能损失的程度。压力损失过大,气流动能损失过多,通过过滤孔板时速度太低,对分离效率显然是不利的。此外,压力损失过大,气流流出分离器后无法有效地被压力控制阀(PCV)吸入进气管[4]。因此,应保证分离效率的同时尽可能减小压力损失。
图6、7为不同窜气量下的油气分离器内部的压力变化和压力损失情况。压力损失为测量点处压力与迷宫入口处的压力之差。从图中可知,粗滤孔板1、2前后压力损失不大。当气流流经粗滤孔板1后,窜气量为180 L/min时无损失,100 L/min、120 L/min时也只损失了0.1~0.2 kPa;当气流流经粗滤孔板2后,窜气量为100 L/min、120 L/min时无损失,180 L/min时只损失了0.1 kPa.压力损失较大的地方是在精滤孔板处:三种窜气量下,压力都发生了不同程度的下降。随着窜气流量的增大,压力损失也随之增大。180 L/min时,压力损失达到了1 kPa.原因在于精滤孔板处孔径较小,孔数也较少,总的流通面积较小,气流流速较快,与孔壁的摩擦阻力增大,能量损耗增加,压力损失也较大。从中可以看出,提高分离效率与降低压力损失之间是矛盾的关系:经过通孔气流的流速增加,使得液滴被挡板拦截的概率增加,一般会使分离效率提高;但同时又会使节流作用增强,增加与通孔的摩擦阻力,造成压力损失增大。所以,如何寻求最优的结构组合,使得两目标都达到可以接受的范围,还需要进一步的研究。
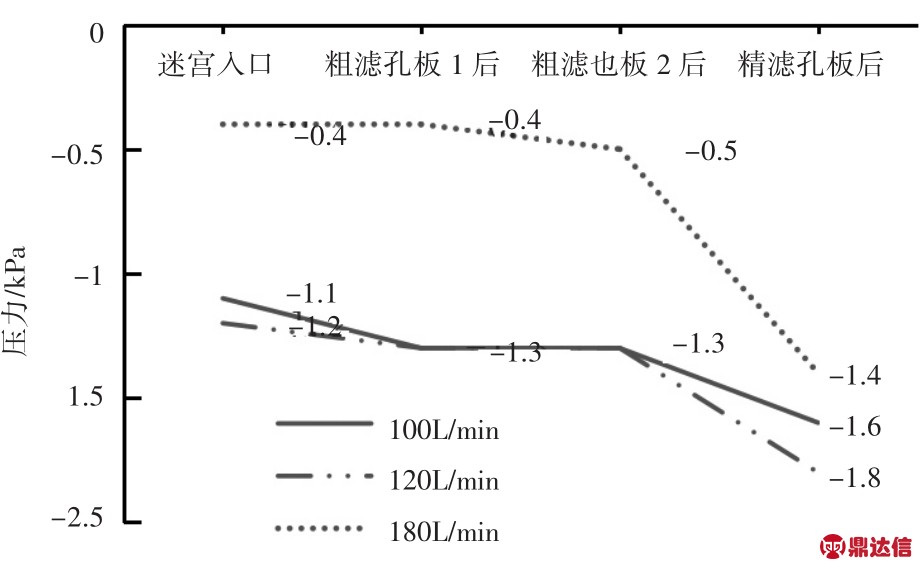
图6 窜气量对油气分离器压力分布的影响
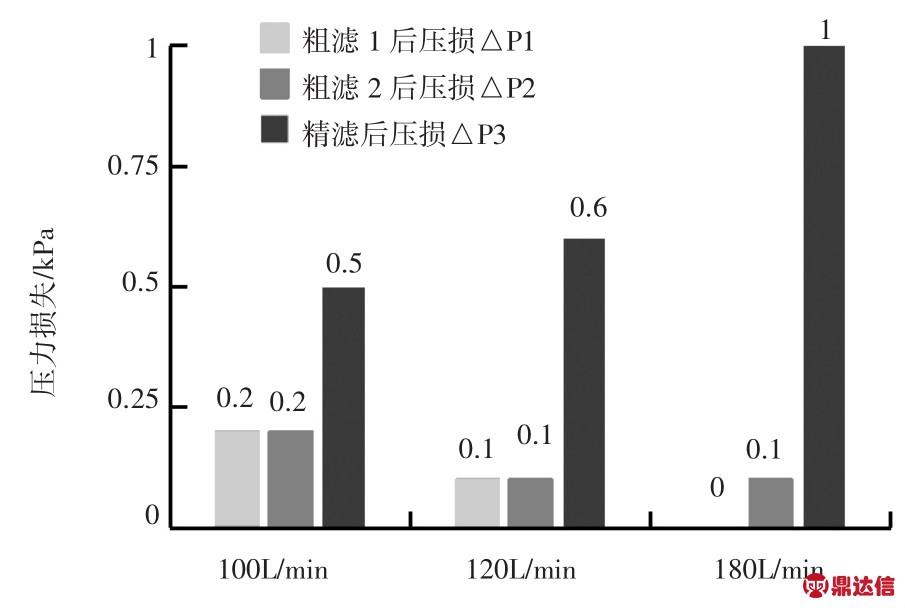
图7 窜气量对压力损失的影响
3.3 窜气量对分离效率的影响
分离效率是油气分离器结构设计的关键目标,也是衡量油气分离器性能最重要的指标。分离效率越高,经过油气分离器分离后的窜气中机油液滴越少,进入燃烧室参与燃烧的机油液滴则越少,排放性能改善。
图7为不同窜气量下窜油量、回油量及其所占百分比的变化。从图中可以看出,随着窜气量的增大,窜油量和回油量均增加,且增加的幅度随窜气量的增大而明显提升:窜气量从100 L/min增加到120 L/min时,回油量只增加了3.7 g;从120 L/min增加到180 L/min时,回油量就增加了13.4 g,约为之前的3倍多。尽管窜油量也有所增加,但回油量的增加量明显大于窜油量的增加量,使得回油量占总油量的比例上升更快。回油量占总油量的比例越高,则说明被窜气中被分离出的机油液滴越多,分离效率也越高。图9反映了比例变化的结果:随着窜气量的增大,分离效率不断升高。当窜气量从100 L/min增加到180 L/min时,分离效率提升了6.9%.
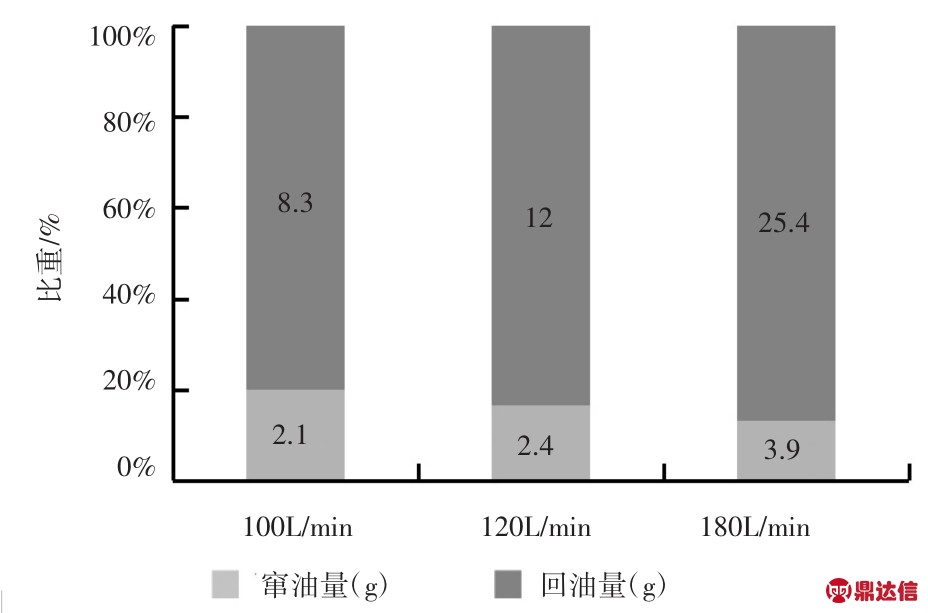
图8 窜气量对窜油量、回油量及其比重的影响
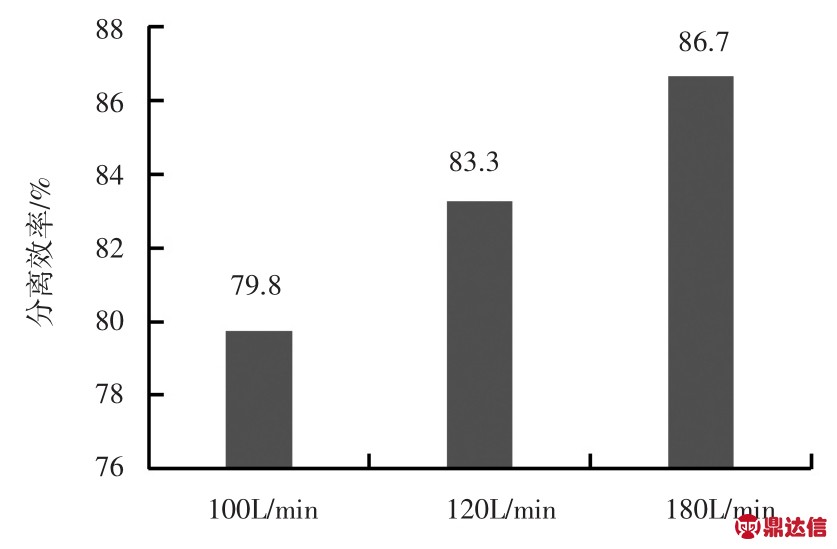
图9 窜气量对分离效率的影响
4 结论
(1)在不同的窜气量条件下,迷宫式油气分离器内部的温度变化趋势基本一致。随着窜气量的增大,油气分离器内部的温度越高,这与窜气携带进入油气分离器的热量增加有关。总体上看,温度从迷宫入口到精滤孔板后呈下降趋势,粗滤孔板后略有上升1℃左右。温度降幅最大发生在粗滤孔板2前后,3~4℃左右。
(2)不同的窜气量条件下,粗滤孔板1、2前后压力损失不大。压力损失较大的地方是在精滤孔板处:三种窜气量下,压力都发生了不同程度的下降。随着窜气流量的增大,压力损失也随之增大。180 L/min时,压力损失达到了1 kPa.
(3)随着窜气量的增大,窜油量和回油量均增加,且增加的幅度随窜气量的增大而明显提升。回油量的增加量明显大于窜油量的增加量,使得回油量占总油量的比例上升更快,因此分离效率随窜气量的增大而增大。当窜气量从100 L/min增加到180 L/min时,分离效率提升了6.9%.