摘 要 为解决含气率达到80%的井况下,单级气液分离器无法将气体全部有效分离的问题,创新使用了双级气液分离器,减少了油井含气量,提高了采油效率。通过Fluent软件对单双级气液分离器的分离效率进行数值模拟,优化双级气液分离器结构,得到分离效果更好、更适应实际井况的结构参数。
关键词 重力式气液分离器 单双级 Fluent 数值模拟
重力式气液分离器利用重力沉降的分离原理解决油井开采中的油气混合问题。它结构简单、无能耗、处理钻井液能力高、安全可靠,适用于含气量高的油井[1]。油气比较高时,油气两相同时进泵,影响抽油泵的泵效,气体含量达到一定程度时会使抽油泵产生“气锁”,严重影响生产[2]。
实际生产作业中,因在防气方面效果显著,工作人员会首选重力式气液分离器。安装位置多为泵的入口处,这样布置使得自由气体在油液中分离出来,不会进入到泵体内,之后自由气体进入布置在油套外的环形空间,直接排到地面[3]。
对一些含气80%的油井,由于单级气液分离器的结构限制,无法将气体全部有效分离,笔者创新的串联两个单级气液分离器,使它成为双级气液分离器而使油气完全分离。
1 单双级气液分离器结构对比
单双级气液分离器结构如图1所示,图1a为单级气液分离器结构平面图,图1b为单级气液分离器三维结构图,图1c为单级气液分离器流体区域模型图,图1d为双级气液分离器三维结构图,从图1d中可以知道双级气液分离器即为两个单级气液分离器串联而成。
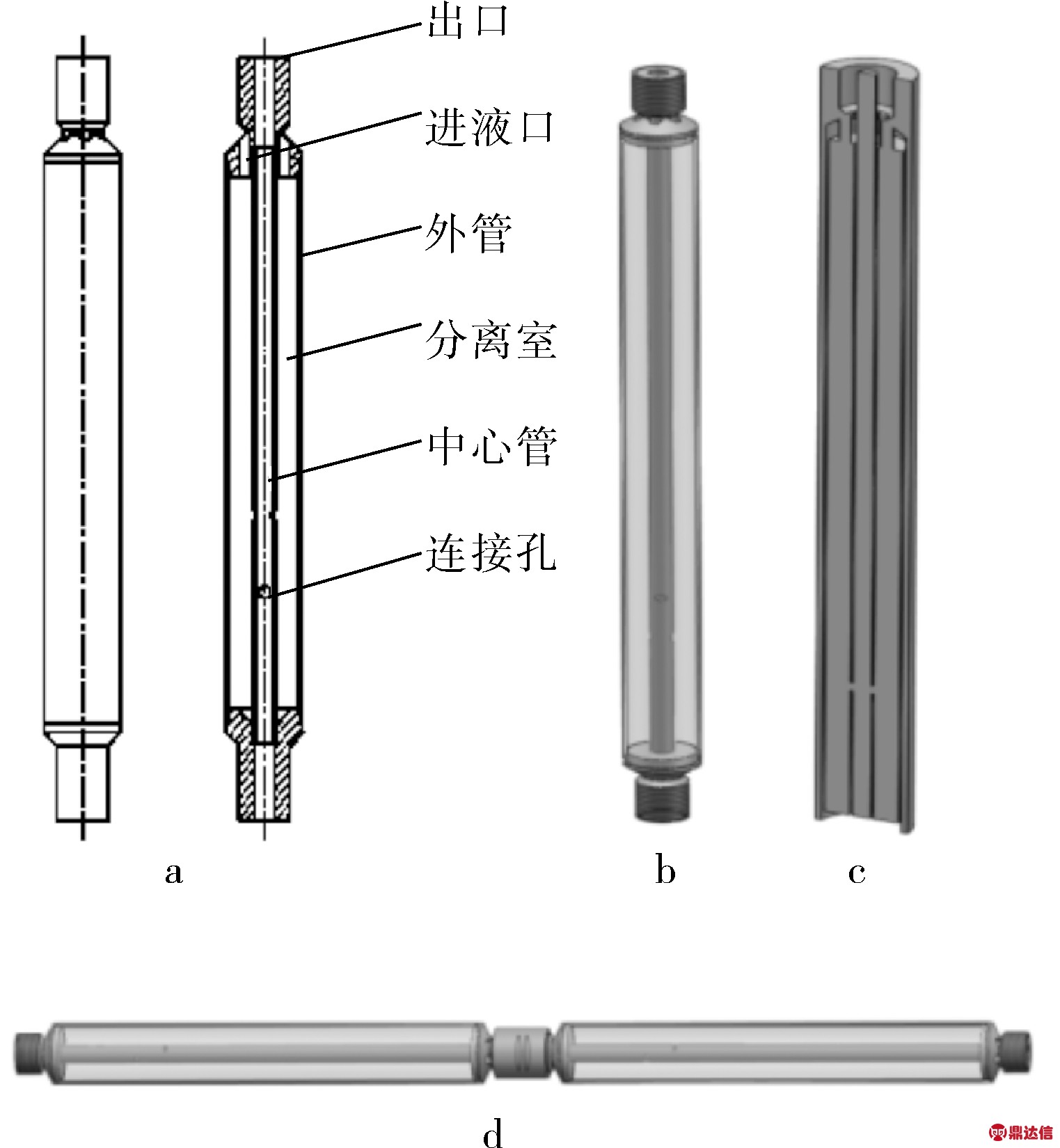
图1 单双级气液分离器结构
根据油田实际井况[4],选定单双级气液分离器基本结构尺寸为:外管内径98mm,中心管外径32mm,φ16mm的进液口6个,φ16mm的外管和中心管连接孔4个。单级分离室长度1 460mm,双级为两个单级串联而成。
2 单双级气液分离器分离效率对比
对单级气液分离器和双级气液分离器的分离效率进行数值模拟[5]。从图2对比结果可以看出,双级气液分离器分离效果与单级气液分离器相当,分离效率不但没有提高,反而有些下降。
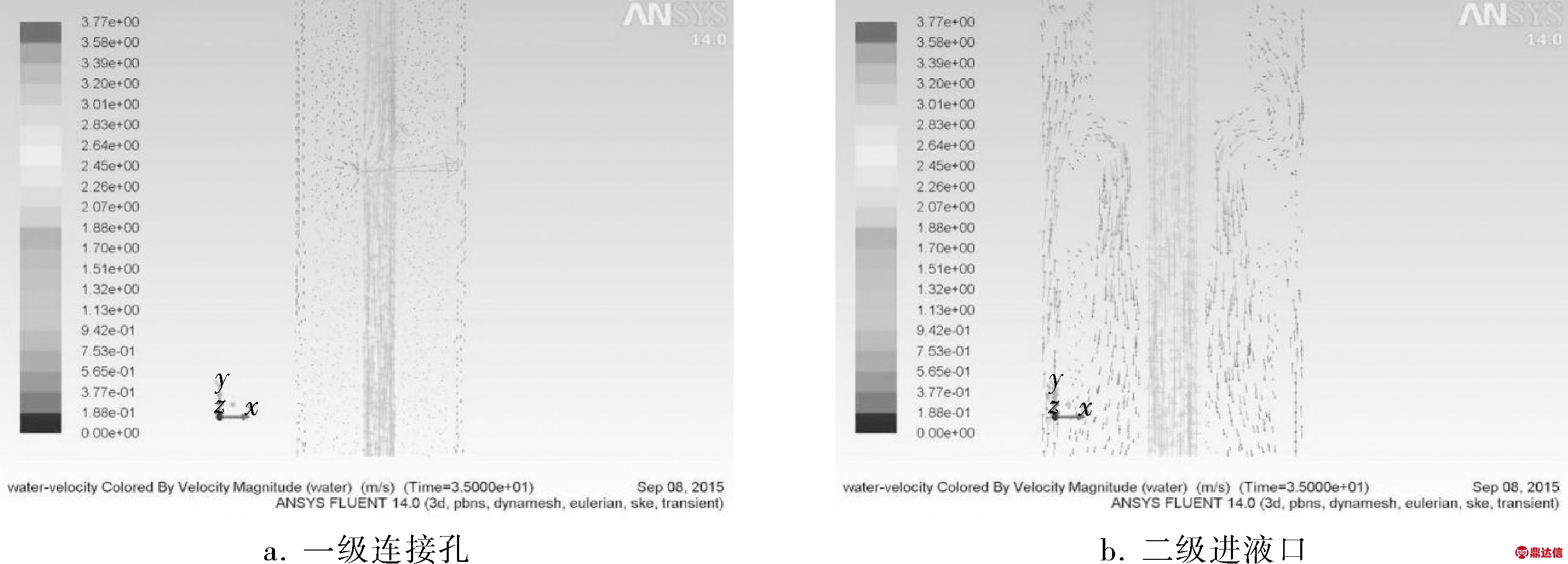
图2 单级和双级气液分离器液相含量分离效果对比
从双级气液分离器模拟云图(图3)分析原因发现,在串联的两级气液分离器中,由于上一级气液分离器距离抽油泵吸入口更近、阻力更小,因此大部分的介质通过上面一级气液分离器进入抽油泵里,只有少量的介质通过下面一级气液分离器进入抽油泵,因此两级气液分离器的分离效果没有完全发挥出来。
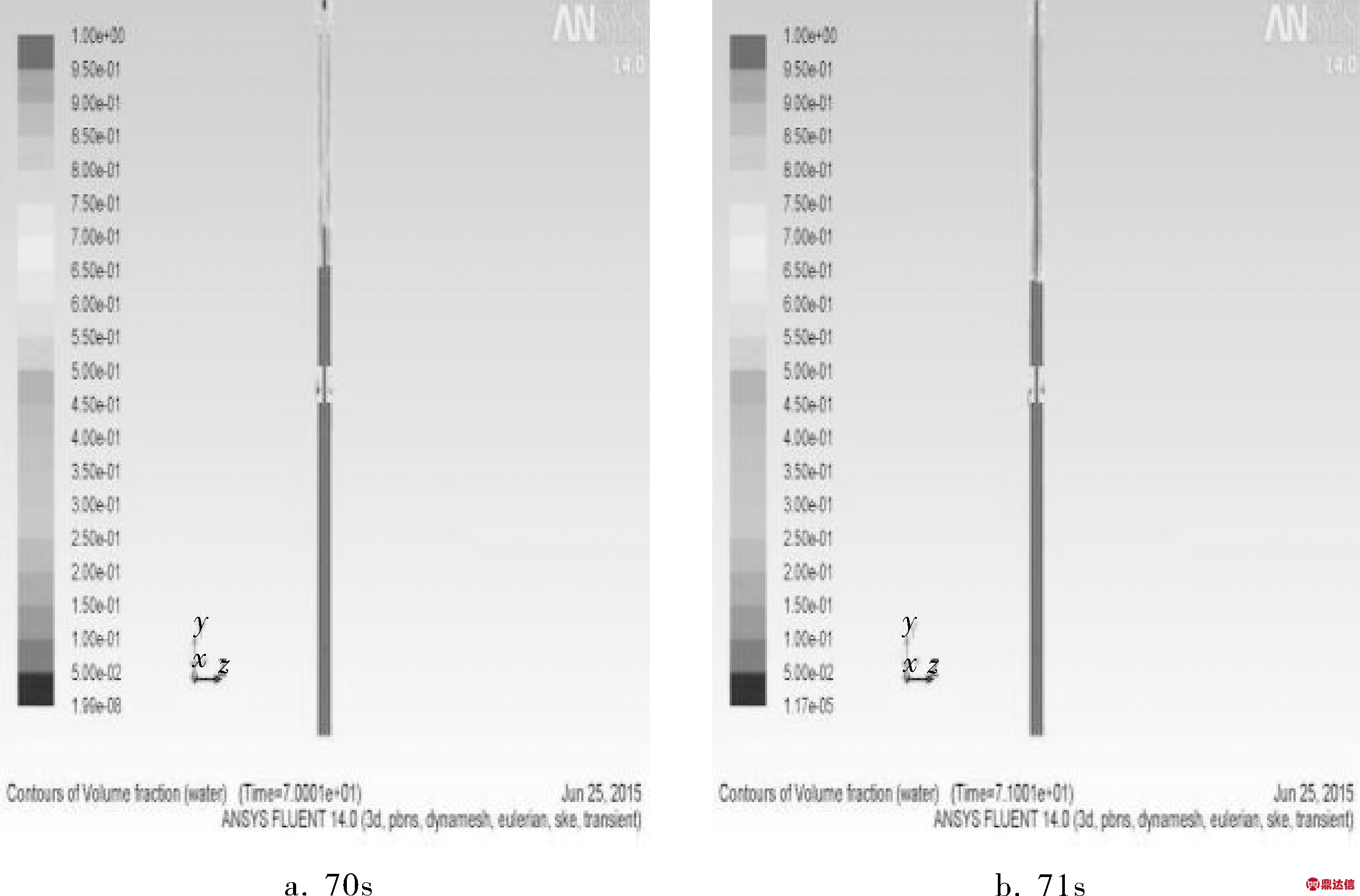
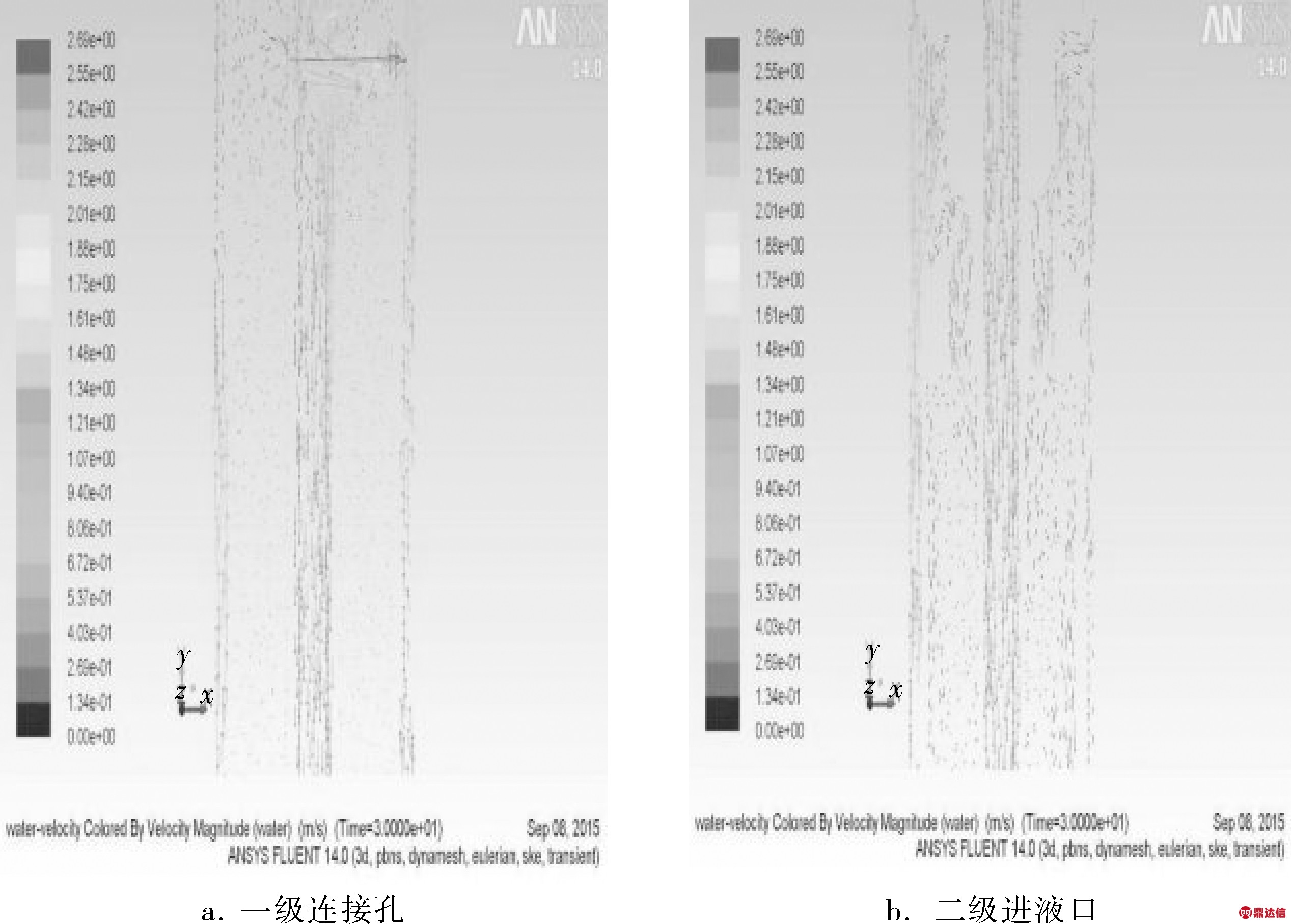
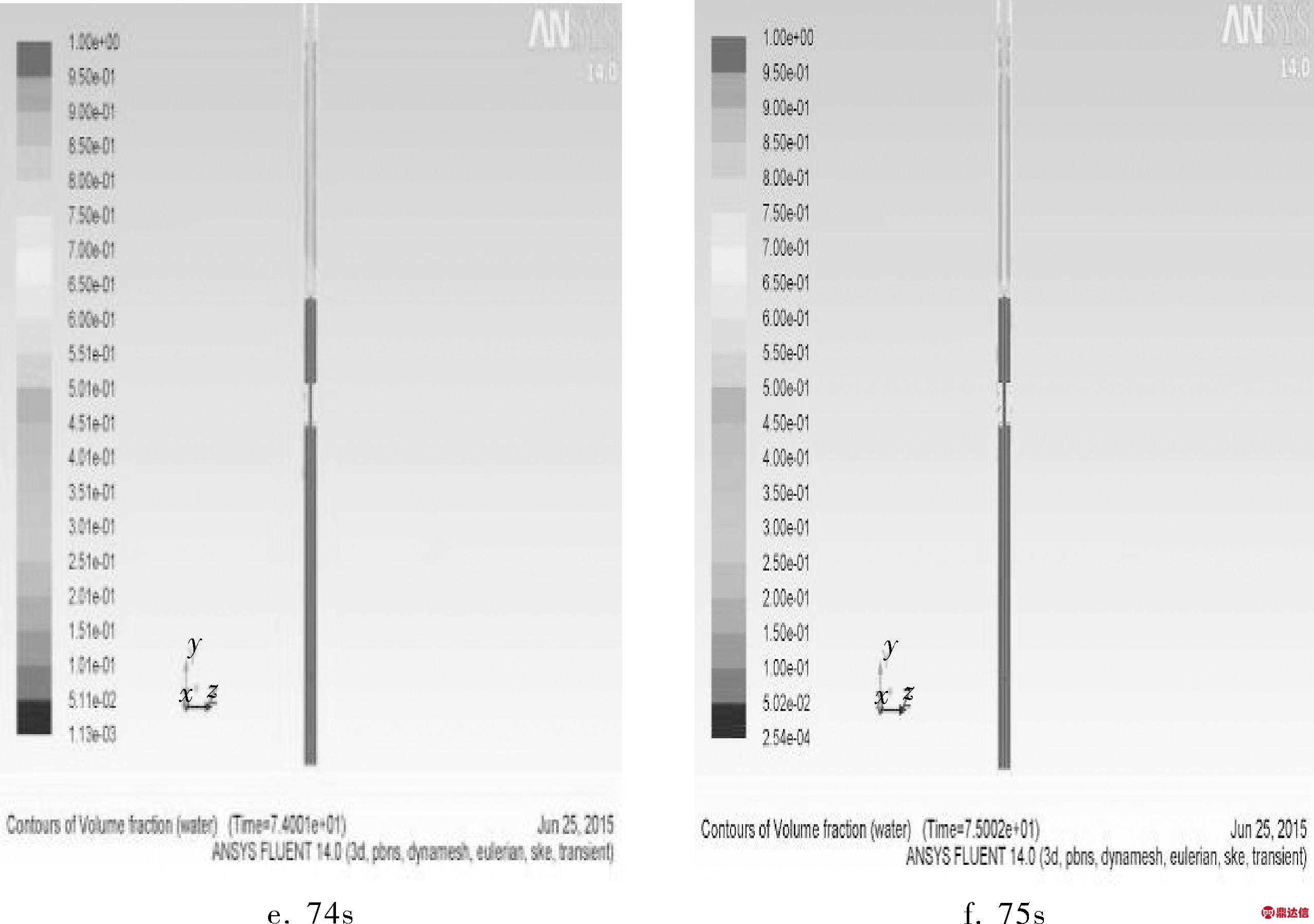
图3 不同时刻双级气液分离器液相含量云图
从双级气液分离器70s(下冲程)时一二级连接处的液相流场图(图4a)可以看到,中心管流体向下流动,即一级气液分离器分离的水流到了二级气液分离器中;二级气液分离器进液口处的流体是从气液分离器向套管流动,即二级气液分离器分离的水流回到套管中。由此可见,在抽油机下冲程时,一级气液分离器分离出的水进入了二级气液分离器,然后通过二级气液分离器又进入了套管中,因此影响了双级气液分离器的分离效率。从双级气液分离器75s(上冲程)时二级进液口液相流场图(图4b)可以看到,中心管流体向上流动,即二级气液分离器分离的水流到了抽油泵中;二级气液分离器进液口处的流体是从套管向气液分离器流动,即将套管介质吸入到二级气液分离器中。从双级气液分离器75s(上冲程)时一级外管和中心管连接孔流场图(图4c)可以看到,抽油泵吸入的介质来源于3个部分,即一级气液分离器的上部连接孔、一级气液分离器的下部连接孔、二级气液分离器中心管。从各部分流量来看,主要来源于一级气液分离器的上部连接孔。
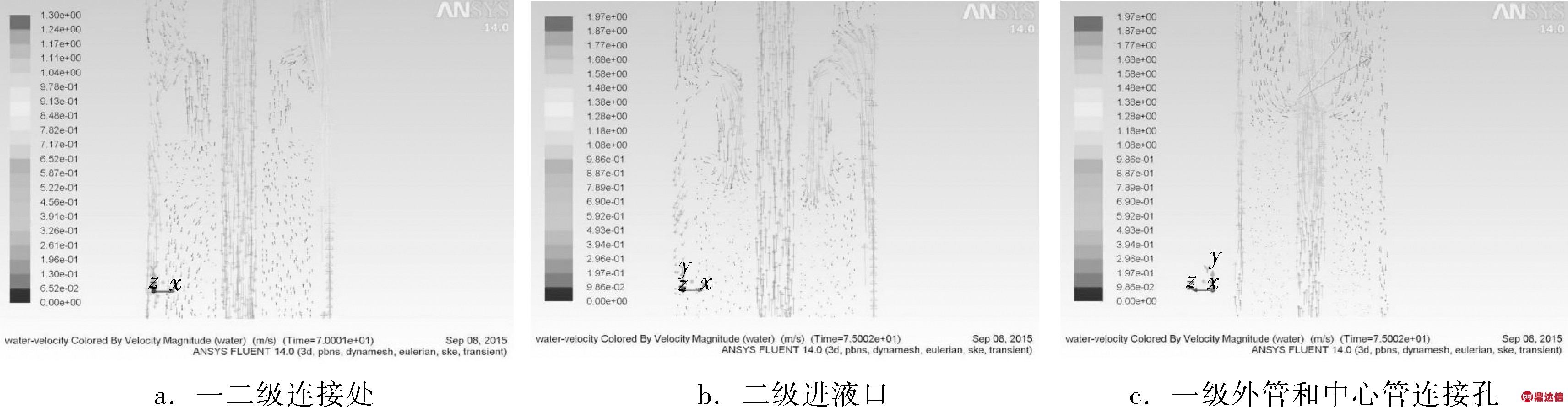
图4 双级气液分离器中不同部分的液相流场图
从图5也可以看到,一级气液分离器的上部连接口以下几乎全是水,但却没有被抽入抽油泵中。
图6是一级和二级气液分离器各自出口流量和气液分离器总流量。从图中可以看到,气液分离器总流量为7.00×10-4m3/s,一级气液离装置平均流量是5.32×10-4m3/s,二级气液分离装置平均流量是1.68×10-4m3/s。实际上二级气液分离器内液相含量更大,应该使二级气液分离器流量更大。
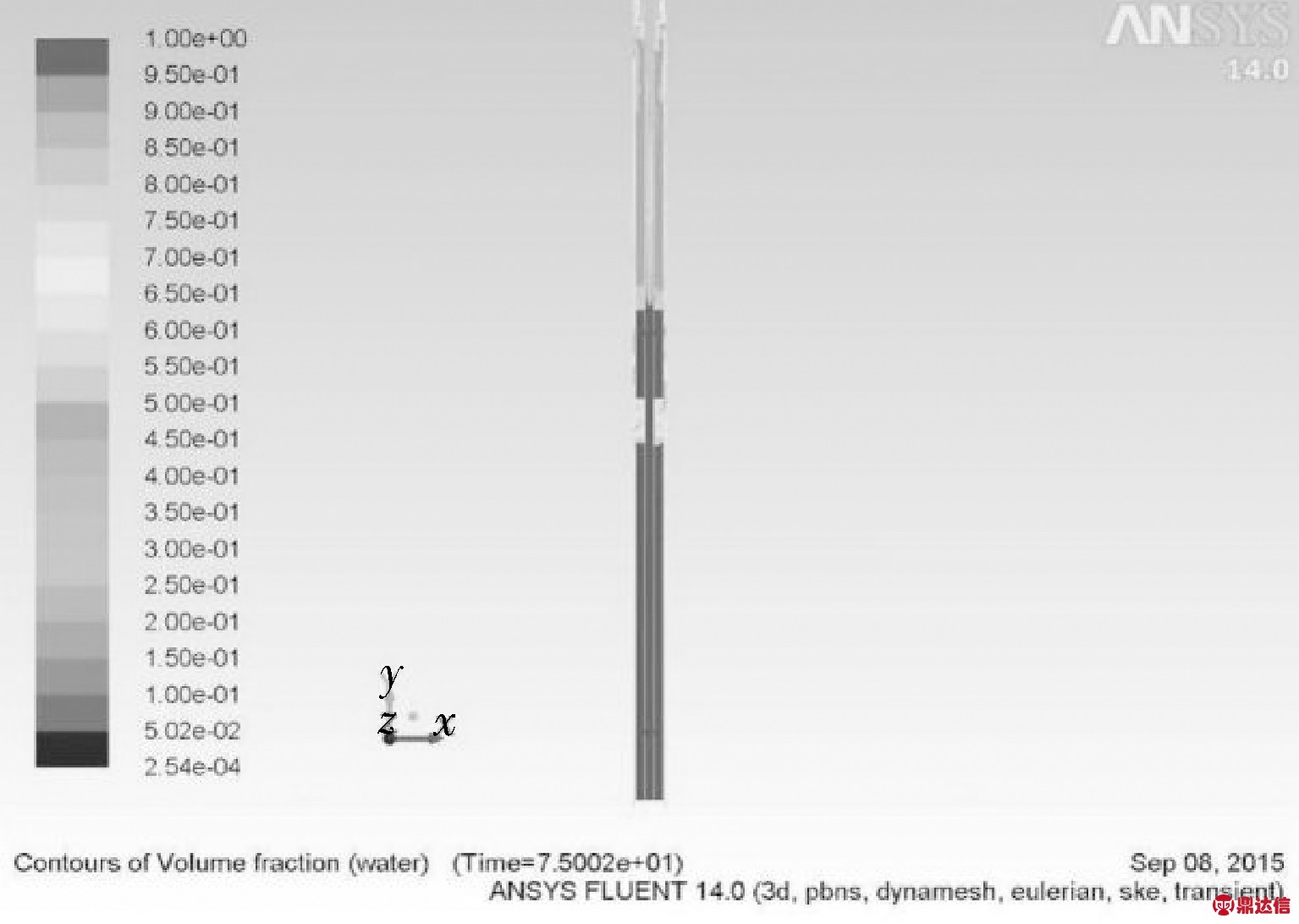
图5 双级气液分离器75s(上冲程)时液相含量
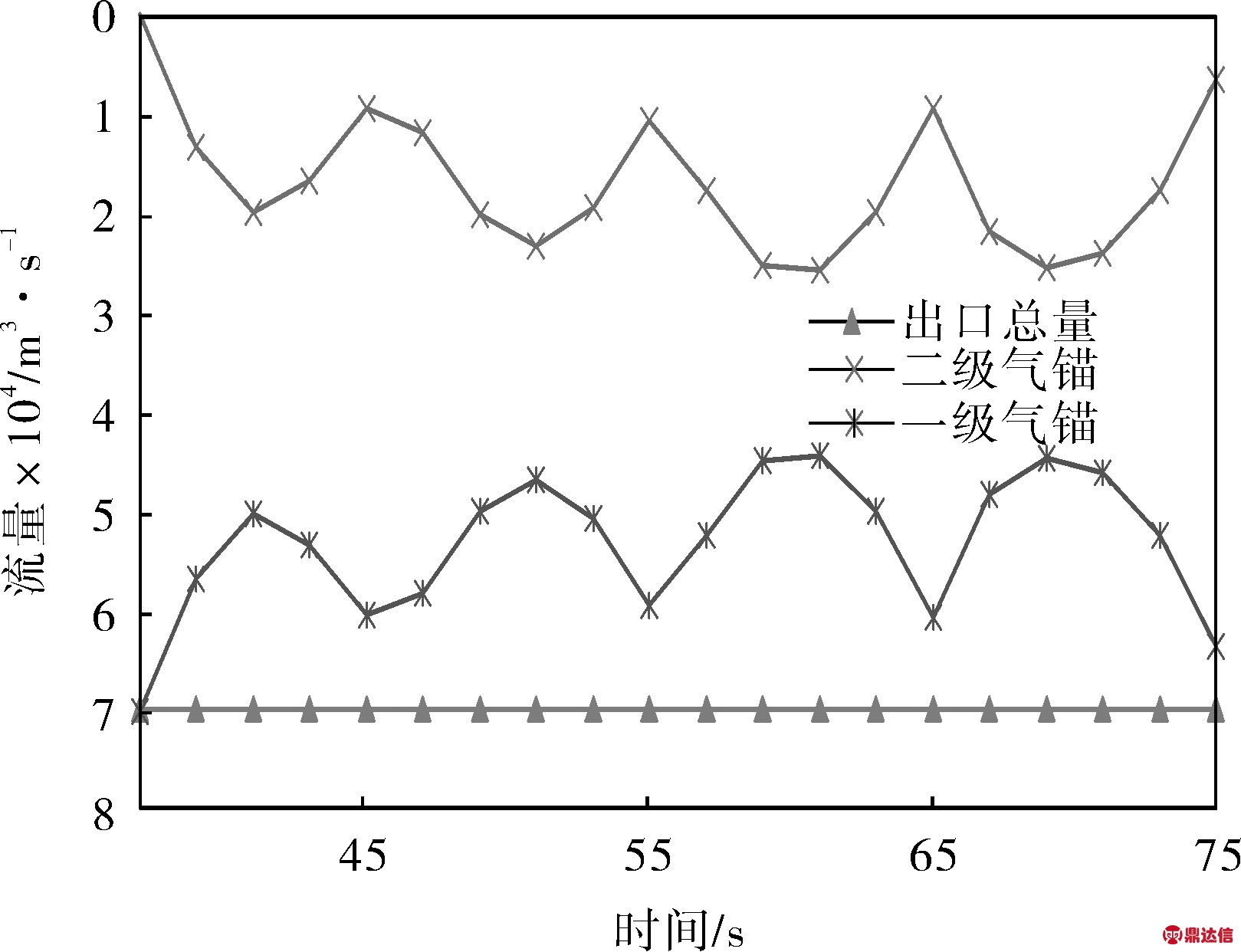
图6 双级气液分离器中各级气液分离器流量随时间变化曲线
从以上分析来看,由于一级气液分离器距离抽油泵吸入口距离更近,吸入阻力更小,因此在上冲程时吸入抽油泵的介质大部分来自于一级气液分离器,少量来自二级气液分离器。但二级气液分离器分离出的水更多而没有能够被吸入。
3 双级气液分离器结构优化和分离效率
为了提高双级气液分离器的分离效率,需要增加进入二级气液分离器的流量。这就要求上冲程时一二级气液分离器流入到抽油泵的介质量基本相同,从流体力学方面考虑需要增大上面一级气液分离器的阻力[6~9],解决办法就是减小上一级气液分离器外管和内管之间的连接孔直径和数量。
从如图7所示的模拟结果来看,将双级气液分离器上一级气液分离器外管和中心管之间的连接管孔从原来的4个φ16mm减少到1个φ10mm,就可以使出口含气量从原来的10%下降到0%。
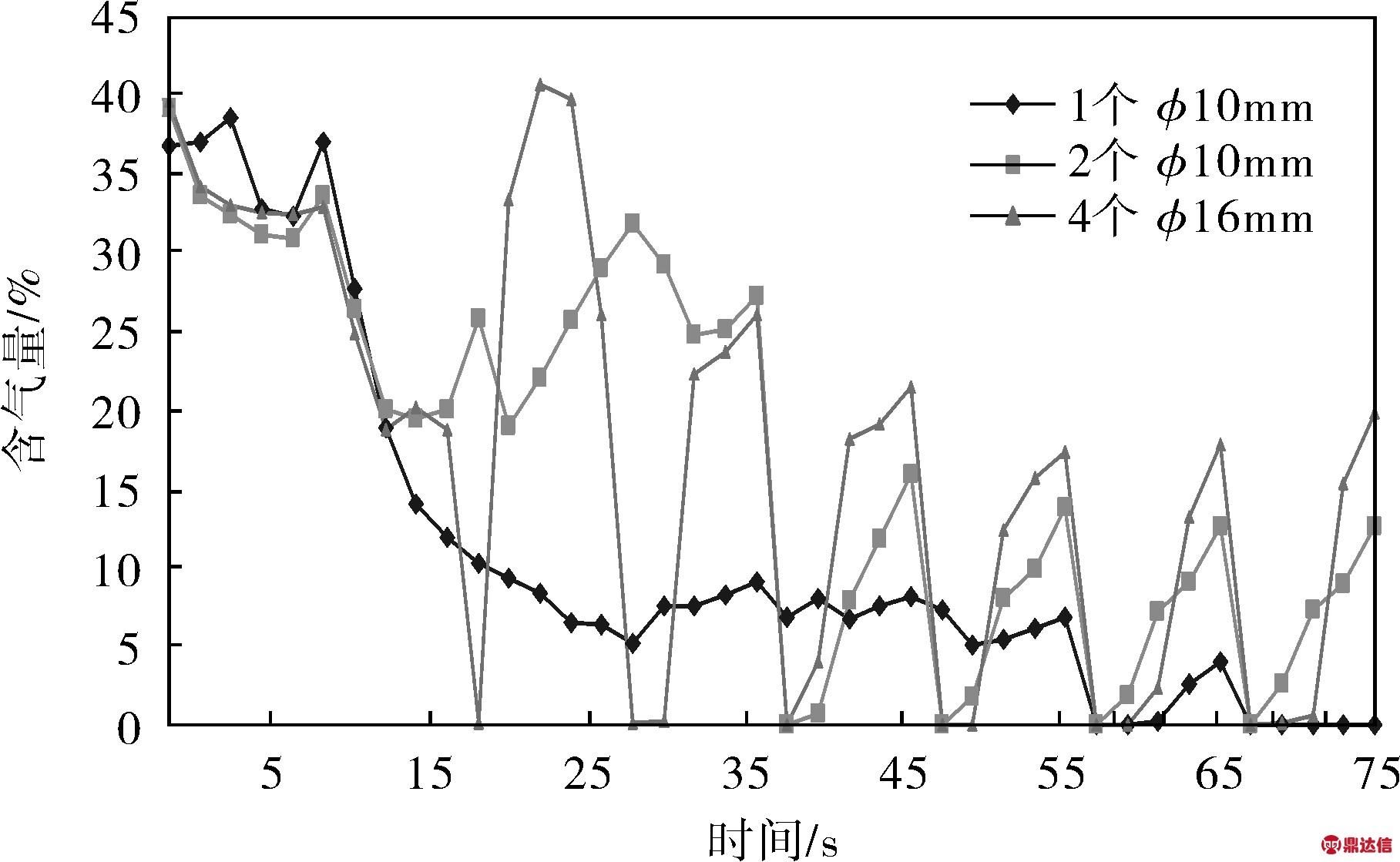
图7 双级气液分离器不同内外管连接孔分离效果对比
图8是结构优化后双级气液分离器30s(下冲程)时一二级气液分离器不同部分流场图。从图8a、b可以看到,中心管流体向下流动,即一级气液分离器分离的水流到了二级气液分离器中;二级气液分离器进液口处的流体是从气液分离器向套管流动,即二级气液分离器分离出的气从二级气液分离器流回到套管中。
由此可见,在抽油机下冲程时,一级气液分离器分离出的水进入了二级气液分离器,二级气液分离器分离的气进入了套管中[10]。
图9是结构优化后双级气液分离器35s(上冲程)时一二级气液分离器不同部分流场图。从一级气液分离器外管与中心管连接孔流场(图9a)可以看到,抽油泵吸入的介质来源于两个部分,即一级气液分离器的连接孔、二级气液分离器中心管。从二级气液分离器进液口流场(图9b)可以看到,中心管流体向上流动,即二级气液分离器分离的水流到了抽油泵中;二级气液分离器进液口处的流体从套管向气液分离器流动,即将套管介质吸入到二级气液分离器中。
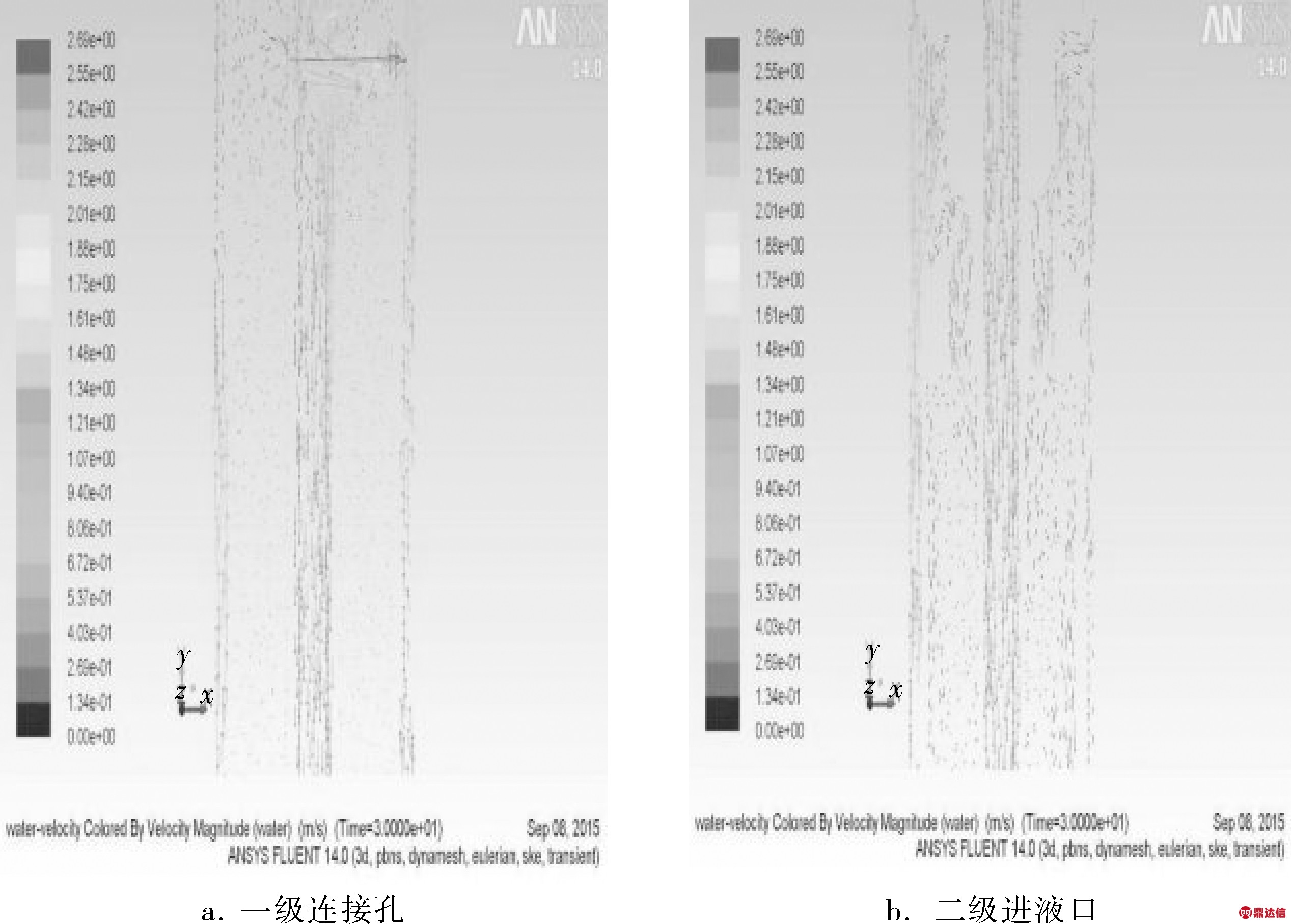
图8 结构优化后一二级气液分离器30s(下冲程)时流场图
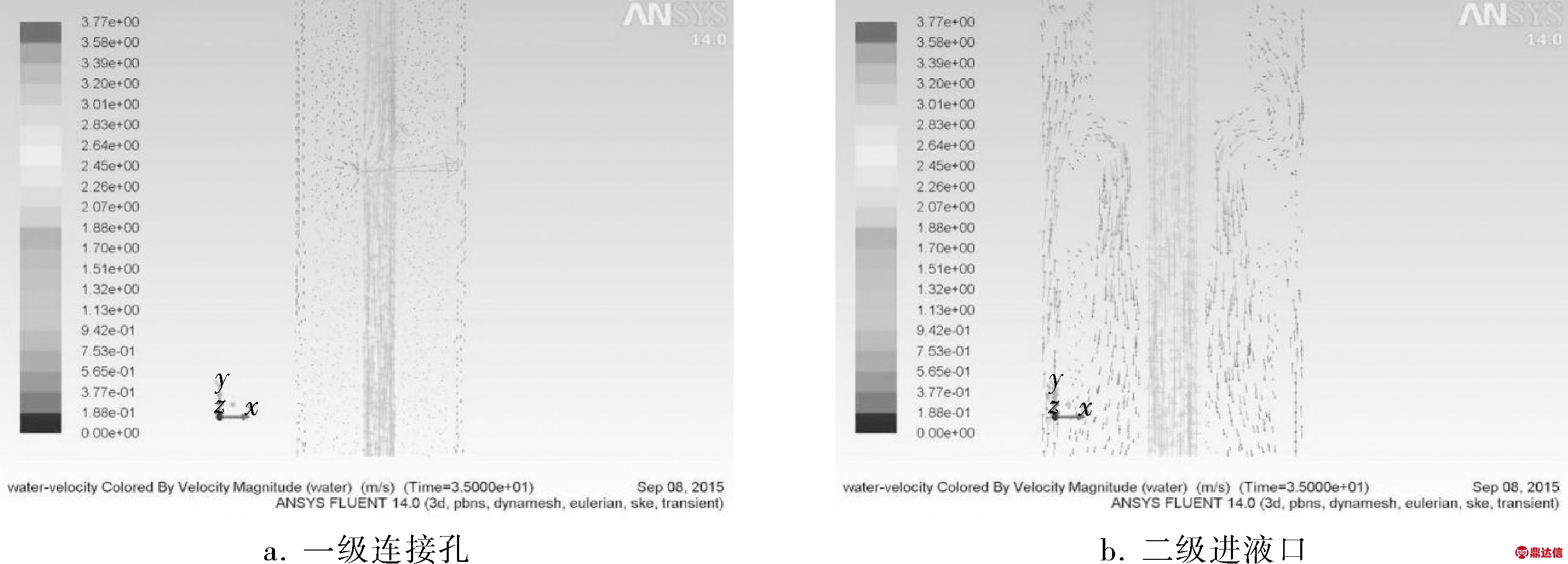
图9 结构优化后一二级气液分离器35s(上冲程)时流场图
图10是结构优化后一、二级气液分离器各自出口流量和气液分离器总流量,从各部分流量来看,一二级气液分离器流入抽油泵的量相差不大,气液分离器总流量为7.00×10-4m3/s,一级气液分离器平均流量是2.57×10-4m3/s,二级气液分离器平均流量是4.43×10-4m3/s。由于一级气液分离器在抽油机下冲程时分离出的液相会流到二级气液分离器中,因此使得二级气液分离器流量大,更能有效发挥双级气液分离器的作用。
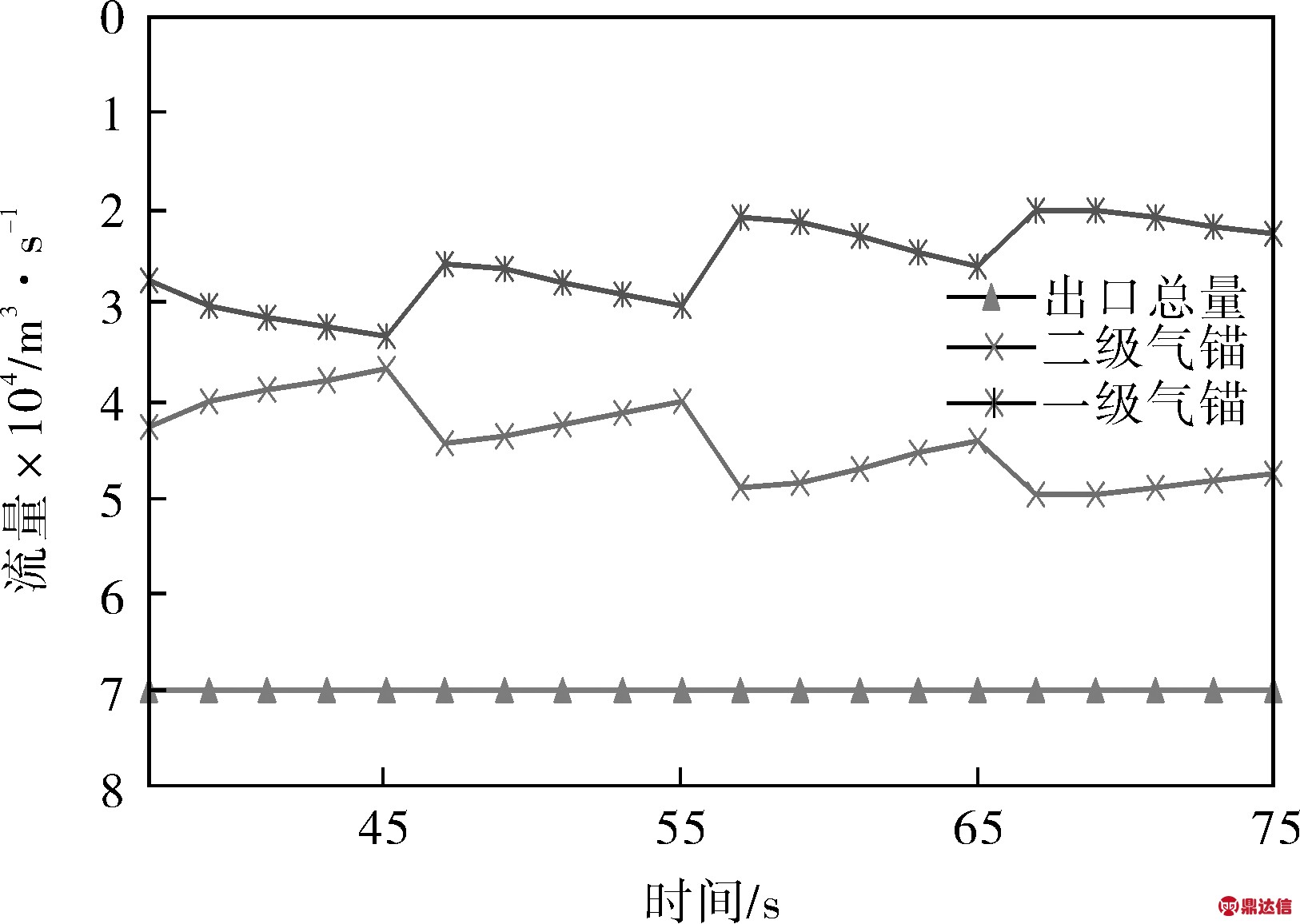
图10 改进后双级气液分离器各级气液分离器流量随时间的变化曲线
4 结论
4.1 对一级和二级外管与中心管连接孔都是4个φ16mm的气液分离器进行数值模拟分析,单级气液分离器工作时下冲程分离出的水完全进入抽油泵,而双级气液分离器工作时下冲程一级气液分离器分离的水进入了二级气液分离器中最终流入了套管中,而在上冲程时二级气液分离器又没有将水流入抽油泵,因此双级气液分离器分离效果不如单级气液分离器。
4.2 通过将一级气液分离器的外管与中心管连接孔由 4个φ16mm减少到1个φ10mm,二级气液分离器的外管与中心管连接孔4个φ16mm不变,结构优化后下冲程一级气液分离器分离的水部分进入了二级气液分离器,二级气液分离器分离的气流入套管中,而在上冲程时二级气液分离器分离出的水流入抽油泵,因此双级气液分离器分离效果高于单级气液分离器。