摘要:以应用中最为常见的筒锥型切流返转式旋风分离器为对象,考察了旋风分离器各结构尺寸及入口气速对压力降的影响,评价了若干压力降模型的适用性。结果表明,Stairmand压力降计算模型的均方差最小,但由于其忽略了几何放大对压力降系数的影响,限制了该压力降模型的适用性。利用相似与模化的分析方法,在对文献给出的实验数据进行回归分析的基础上,修正了Stairmand压力降计算模型,并将修正式的计算结果与实验测量值及另外多篇文献中给出的切流返转式旋风分离器在不同结构尺寸及操作气速共计150种工况下的实验数据进行对比,结果表明,修正式的精度更高,适用范围更广,可以满足旋风分离器设计计算的要求。
关键词:旋风分离器 压力降模型 适用性 回归分析
旋风分离器是气固分离过程中一种常用的设备,因其结构简单,无运转部件,适用于高温高压等条件,目前在石油、化工、冶金、能源、环境等诸多领域得到广泛应用。压力降是旋风分离器的主要性能指标之一,直接关系到能量消耗和风机的合理选择。国内外学者对它进行了许多研究,提出了很多计算方法和计算公式,这些压力降模型为旋风分离器的工程应用提供了必要的设计依据,但不同压力降模型间的计算结果差异较大。
Linden,Alexander,Shepherd,First,Casal,Coker等认为,阻力系数主要取决于进出口尺寸,且可表示为进口面积和排气管直径的函数[1-6]。时铭显认为除了进口面积和排气管直径,分离器直径对阻力系数的影响也不容忽视[7]。Dirgo研究结果表明旋风分离器的8个基本尺寸均会影响压力降,并归纳了经验计算公式[8]。
随着计算机技术的发展,人工神经网络、支持向量机、响应曲面法等手段也被用于寻找阻力系数与各个结构尺寸间的函数关系,虽然研究手段更先进,但本质上还属于经验方法。与经验方法不同,Stairmand,Barth,Muschelknautz等对压力降形成机理进行了一些探讨,并在此基础上建立和发展了基于旋转动能耗散的压力降计算方法[9-11]。
该文在前人的研究基础上,探究了筒锥型切流返转式旋风分离器的8个主要结构尺寸及操作变量对压力降的影响,评价了若干压力降模型的适用性;并引入相似与模化的分析方法,对已有的模型进行优化,以寻找具有较强适用性的压力降计算式,期望为工程设计和应用提供指导。
1 旋风分离器的基本结构和预测模型
一个典型的切流返转式旋风分离器主要包括图1所示的8个结构参数。
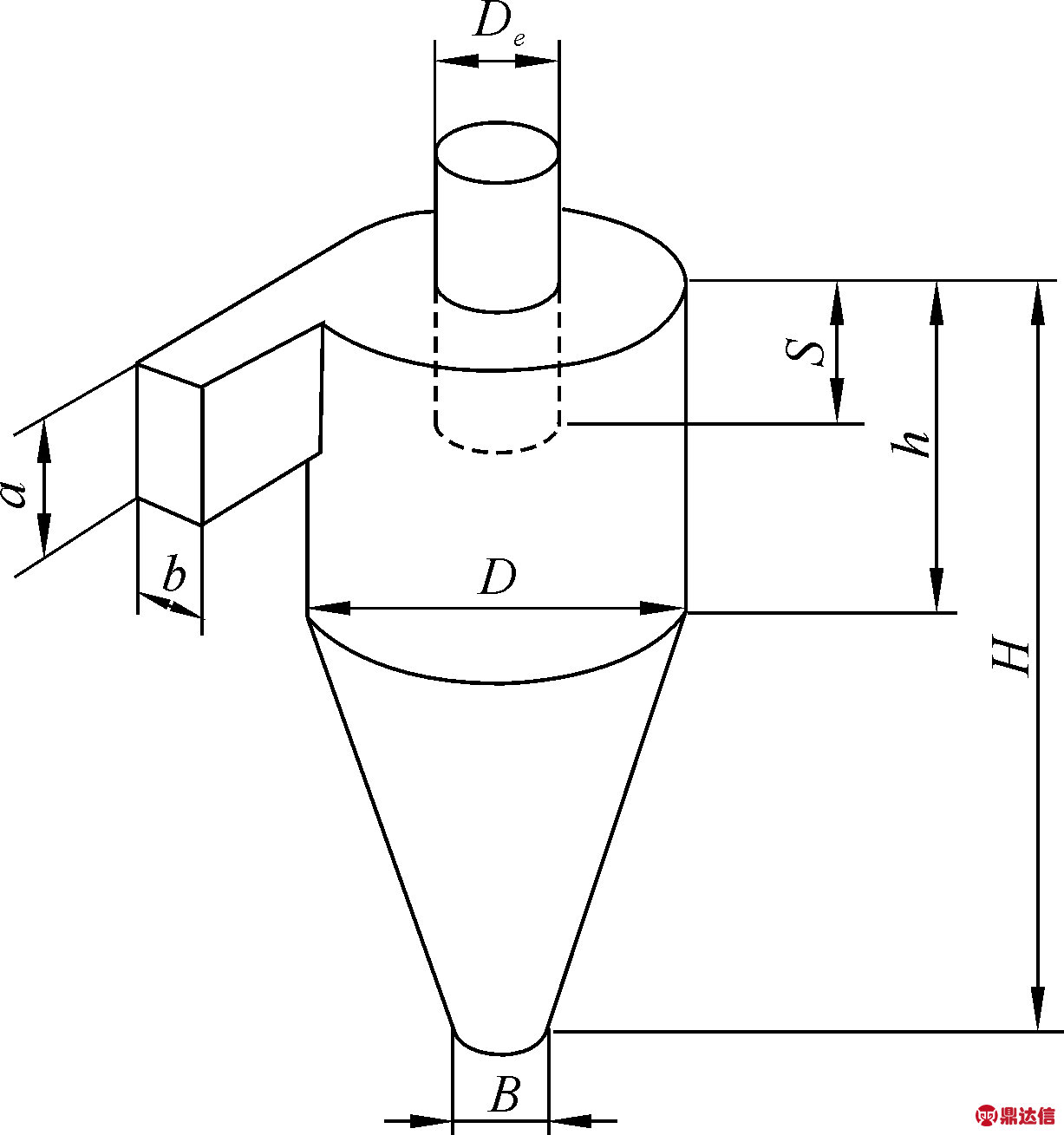
图1 切流返转式旋风分离器结构示意
Fig.1 Structural diagram of tangential reverse cyclone m 注:a—入口高度;De—排气管直径;S—排气管插入深度;h—筒体高度;H—总高度;D—筒体直径;B—排尘口直径;b—入口宽度
旋风分离器的结构参数对压力降有着较大影响,Hsiao通过实验测量的手段,较为全面地考察了筒锥型切流返转式旋风分离器的纵向和径向尺寸对压力降的影响;方麒先对不同筒径下的筒锥型切流返转式旋风分离器的压力降进行了实验研究。为了校验压力降模型在不同结构参数下的适用情况,按照单因素变量原则,依次改变旋风分离器内的几何结构尺寸,其变化范围如表1所示,将Hsiao和方麒先压力降实验值与模型的计算值对比分析,如图2所示。
图2(a)~(h)分别为筒锥型切流返转式旋风分离器在不同结构参数及入口气速下的压力降实验值与模型预测值的对比结果,从中可以看出,Stairmand模型能很好地预测压力降变化的趋势,且与实验数据吻合较好。为了更直观的比较以上不同模型的预测性能,定义旋风分离器实验压力降系数与模型计算压力降系数间的均方误差(MSE)如下:

(1)
式中,n为实验次数;ξi为模型计算压力降系数;i为实验压力降系数。
表1 旋风分离器的几何尺寸及操作条件
Table 1 Dimensional ratios of cyclone and operating conditions

根据Hsiao和方麒先给出的筒锥型切流返转式旋风分离器在不同结构尺寸及入口气速共计100种工况下的阻力系数实验值,计算了不同模型预测值与其相同工况下实验值的均方误差(MSE)大小,见表2。从对比结果可以看出,总体上目前还没一个模型的预测结果与实验值能够很好地吻合,这是因为机理性模型多是基于各自的认识和假设,与实际过程相比,仍存在一定的局限性;而依据实验数据回归的纯经验压力降模型,由于过多依赖实验数据,缺乏合理的旋风分离器内压力降形成机理的分析,耗时长且通用性较差。
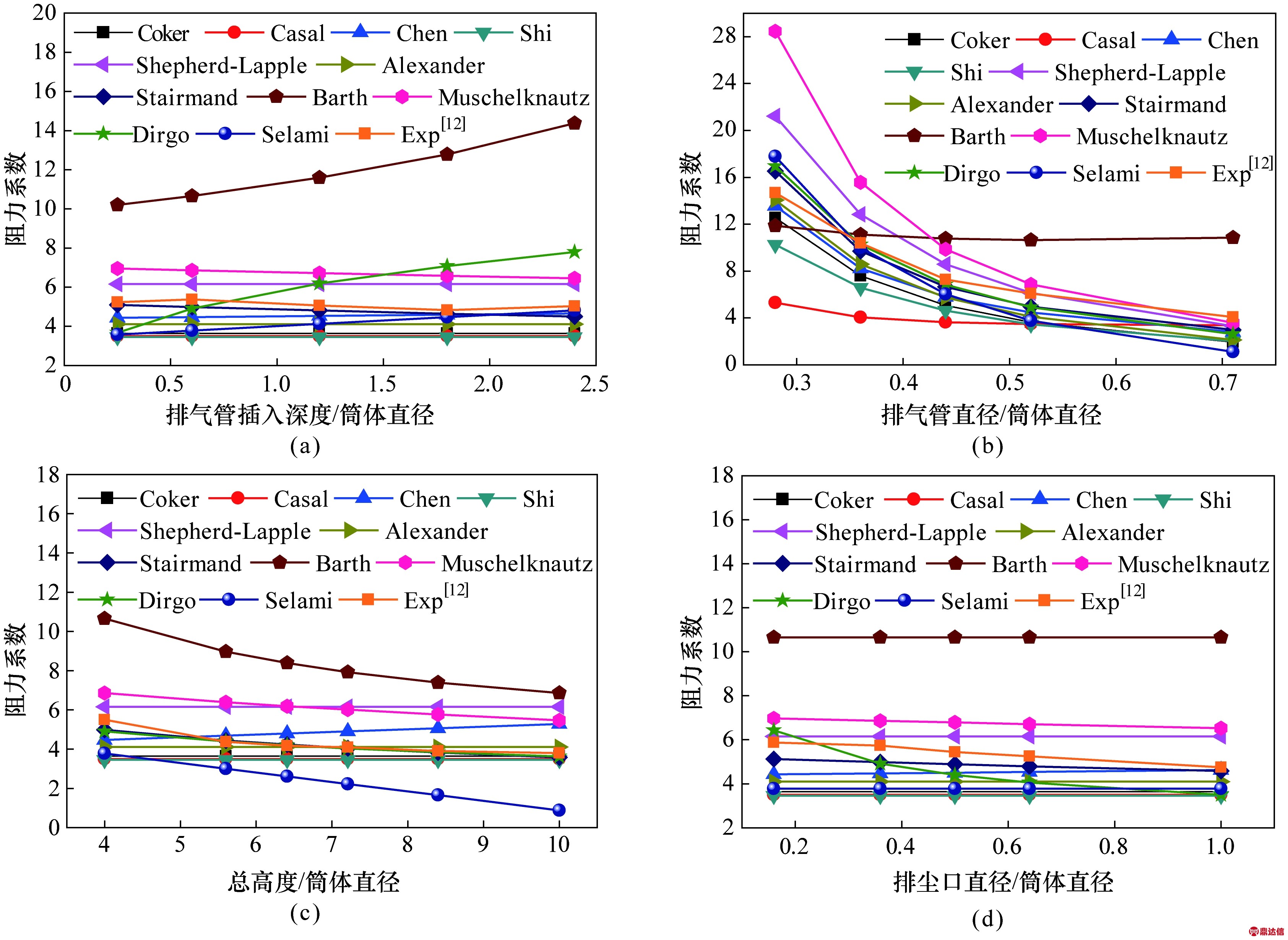
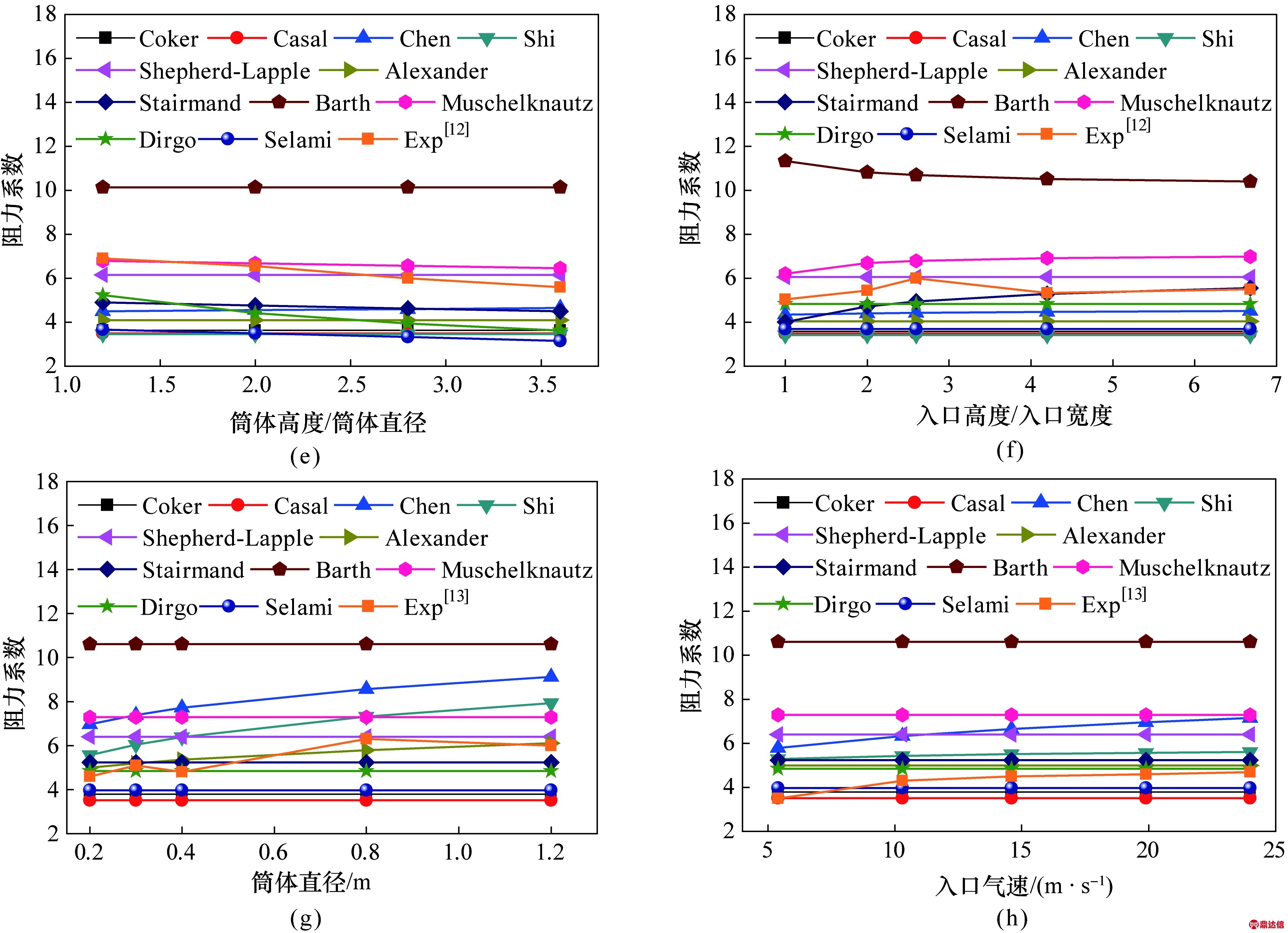
图2 模型阻力系数计算值与实验值对比
Fig.2 Comparison of several models with experimental data from Hsiao and Fang
表2 对比不同模型预测值与实验值的均方误差(MSE)
Table 2 Comparison of mean squared error(MSE) of pressure drop coefficient between models and experimental data

从图2和表2也能看出,Stairmand模型与实验数据吻合较好,即均方误差最小,且能很好地预测压力降随结构参数变化的趋势。
2 模型修正
2.1 Stairmand压力降模型理论
旋风分离器的压力降可以认为是由以下四个部分组成,即:①气流进入旋风分离器时因通流截面突然扩大而造成的膨胀损失;②形成旋涡流动而消耗的能量,也称旋流损失,其内容包含平衡离心效应所需的能量损失以及存在速度梯度而引起的气流内摩擦损失以及气流与器壁摩擦的能量损失;③气流进入排气管时因通流截面突然收缩而造成的损失,也称出口损失;④排气管入口至测压点之间气流动能的耗散损失。Stairmand从动量矩平衡计算了旋风分离器中的速度分布,然后结合进出口的静压损失与旋流中的静压损失估算了压力降,见表1。他假设压力降是由进口损失、出口损失和旋转动能损失构成的,排气管内气流的旋转动能损失很少能再转化为静压能而重新加以利用,可以认为耗散损失掉了[14]。
2.2 相似与模化
无量纲压力降系数ξ,其主要与旋风分离器几何结构、进口弗劳徳数Frc、进口粉料质量浓度Ci、进口雷诺数Rec和固气密度比ρc/ρg相关。根据相似及模化分析方法,即
ξ=f (geometry, Frc, Ci, Rec, ρc/ρg)
(2)
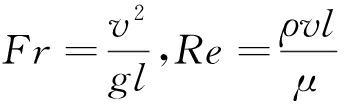
在旋风分离器的实际运行中,特别是单一气相时,重力不是主要因素,Fr,ρc/ρg及Ci可以忽略不计。故旋风分离器的压力降关系式表示为:
ξ=f(geometry,Re)
(3)
2.3 模型修正
Stairmand假设压力降是由进口损失、出口损失和旋转动能损失构成的。他认为排气管内气流的旋转动能损失占支配地位,且很少能再转化为静压能而重新加以利用。根据Stairmand压力降系数公式,其中已经考虑到旋风分离器的8个主要尺寸因素,但未体现出ξ与Re之间的关系,通过前文研究分析,Re对ξ有一定的影响,将ξ与Re之间呈现的关系处理为自然对数函数。此外,Stairmand模型计算的压力降系数也不能反映筒体直径的影响,见图2(g),这与实验结果矛盾,故还需要对筒径加以修正。可设为:
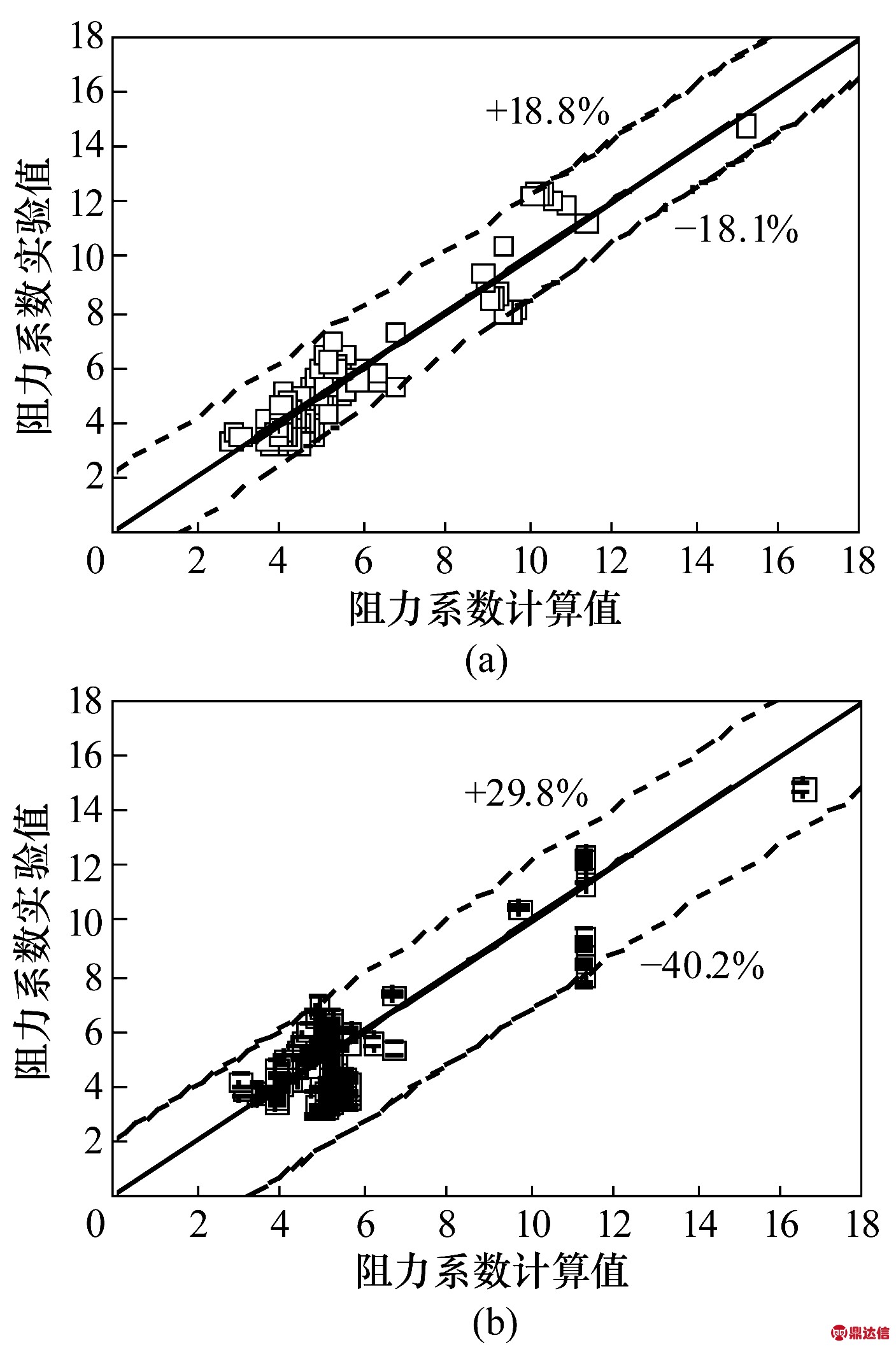
(4)
仍然根据Hsiao和方麒先等人给出的55组实验值ξ与Re,D及ξst关系,利用多元线性拟合得到压力降系数的回归系数,其部分结果见表3。
表3 压力降系数ξ 的回归系数
Table 3 Regression coefficients of pressure drop coefficient ξ

对于表3中所列出的回归系数,得到基于Stairmand旋风分离器压力降系数公式的修正计算式:

(5)
其中:

,
f0=0.005

表4为压力降系数二阶模型的方差分析,可以看出,决定系数为0.918,说明拟合效果较好,此修正模型能较为准确地预测旋风分离器的压力降。
表4 压力降系数ξ 二阶模型的方差分析
Table 4 Variance analysis of pressure drop coefficient ξ second-order model

注:R2(Adj) = 0.918。
2.4 模型验证
为验证式(5)的准确性,进一步以实验测量了不同筒体直径及气速下的分离器压力降大小。采用Stairmand型高效旋风分离器为基准,筒径分别为D=200,300,400 mm,筒体高度为1.5D,总高度为4D,排尘口直径为0.4D,升气管直径为0.5D,下接1 500 mm的料腿,料腿末端封闭,用有机玻璃制造。实验介质为常温空气,在吸风负压状态下操作,入口气速由标准毕托管在旋风分离器的入口水平圆管上测得;分离器压力降用U形管测量。式(5)的计算值和中试装置旋风分离器压力降的测量值比较见表5。从表5可以看出,式(5)计算值与实验测量值趋势一致,且吻合很好,误差都在10%以内,表现出较高的准确性。
3 修正模型的误差分析
根据上述分析和回归,式(5)所表示的旋风分离器的压力降表达式实际上已考虑了旋风器内的流场特性、结构参数和运行参数的影响。分别对通过式(5)和Stairmand压力降公式计算得到的结果与Demir,Xiang,Lim,Iozia等人给出的切流返转式旋风分离器在不同排气管直径、排气管插入深度、筒体高度、总高度及操作气速共计150种工况下的阻力系数实验值比较,结果如图3所示[15-18]。从图3(a)中可以看到数据点都密集在两条20%的误差线以内,这表明式(5)拟合较好;并且由图3(a)和图3(b)对比发现,压力降修正式(5)计算的精度明显更高。
表5 旋风分离器压力降系数计算值与实验值对比
Table 5 Comparison between pressure drop coefficients from experimental data and modified Stairmand model
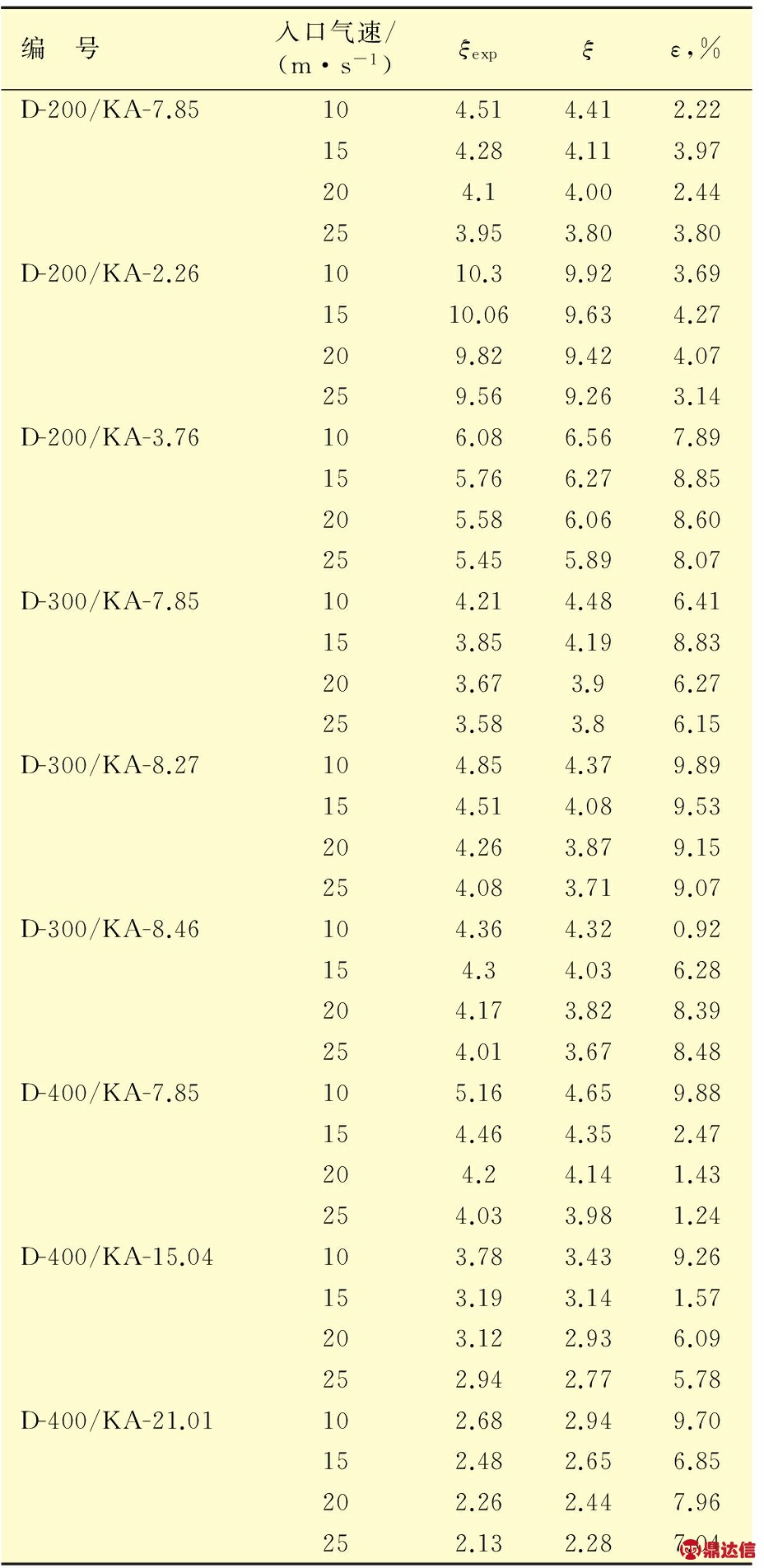
注:ξexp—实验值,ξ—修正式计算值,ε—修正式计算值与实验值误差。
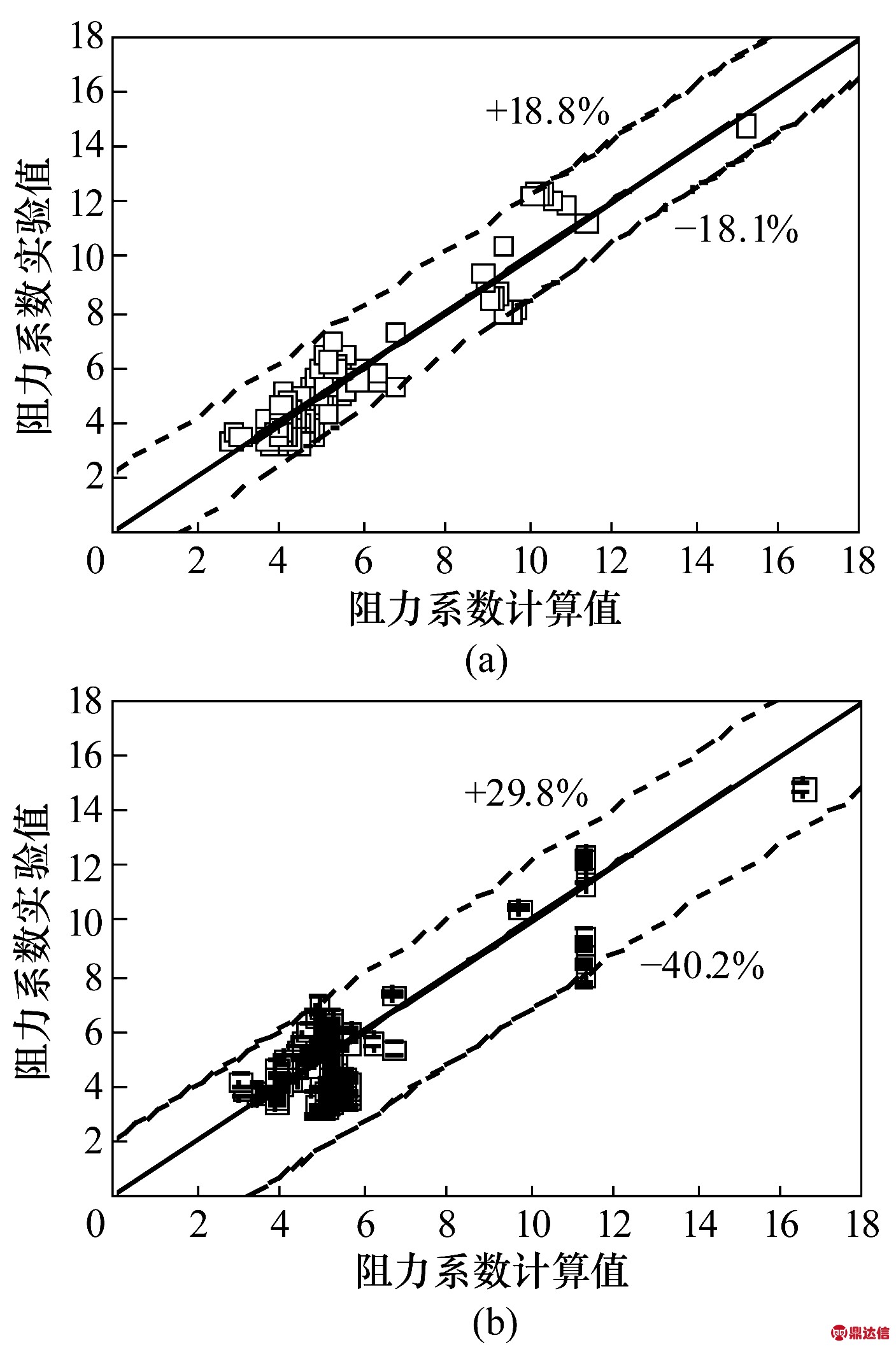
图3 阻力系数计算值与实验值的比较
Fig.3 Comparison of present model with experimental data and Stairmand model
4 结 论
(1)在前人的研究基础上,按照单因数变量原则,探究了旋风分离器的8个主要结构尺寸及操作变量对压力降的影响,评价了若干压力降模型的适用性,对比发现Stairmand模型与实验数据吻合较好。
(2)利用相似与模化的分析方法,将旋风分离器阻力系数ξ与Re的关系处理为对数函数,引入修正系数,得到一个基于Stairmand压力降模型的计算修正式。将修正式的预测结果与实验测量值及前人多组实验数据进行对比,验证了计算修正式不仅精度高而且适用性较好,基本可以满足旋风分离器设计计算的要求。
这段话中,作者借助律师之口有意突出了男孩的个人历险与古老的史诗之间的联系;并且强调这部个人史诗应该用一种“更有力度的语言”,事实上是帝国的语言——拉丁语——讲出来,明显表现了一种帝国的怀旧情结和强烈的叙事冲动。
符号说明
f——含尘气流与壁面摩擦系数;
Fs——旋风分离器器壁的总面积,m2;
f0——纯净气流与壁面摩擦系数;
n——旋流的旋涡指数;
Re——气体雷诺数;
ReR——旋风分离器雷诺数(Muschelknautz模型);
φ——惯性碰撞系数;
ζe——器内旋流损失;
ρg——气体密度,kg/m3;
ρp——颗粒密度,kg/m3;
ρstr——灰带密度,kg/m3;
μ——气体黏度,Pa·s;
ξ——纯气流阻力系数;
v——入口气速,m/s;
l——特征长度,m;
ρ——气体密度,kg/m3;
μ——气体黏度,Pa·s;
g——气体重力加速度,m/s2;
ki(i=1,2,3,4)——修正系数;
ξst——Stairmand模型计算值。