摘 要:考虑到混相输送极易在管道的立管段形成严重段塞流,影响管道和下游油气水处理设备的正常工作,造成巨大的经济损失,利用OLGA多相流瞬态模拟软件对海底管道进行段塞流预测,并通过OLGA软件模拟PID控制器对严重段塞流的自动控制。结果表明,利用PID控制器能够有效进行严重段塞流的控制,推荐在管道设计时应用OLGA软件先进行段塞流的预测,再通过OLGA软件进行PID控制系统的参数设计。
关键词:严重段塞流 分离器 PID控制器 OLGA软件
海洋地理环境特殊,通常利用采油平台进行海底油气资源的开发。对于采用全海式集输方式的海上油气田,从卫星平台或是水下井口采出的油气通常采用混相方式经海底管道输送到中心平台,统一进行油气水处理。混相输送方式在中心平台立管段极易出现严重段塞流。混相输送管道中出现段塞流,会恶化管道的运行条件。由于其流动的间歇性,会引起管道中持液率和压力急剧波动,并使得运行在该流型下的管道以及油气水处理设备内部构件承受间歇性应力冲击,从而影响设备的性能[1]。胜利油田海洋采油厂中心二号平台三相分离器运行中发现段塞流对油气处理设备造成巨大危害[2],主要包括:①瞬间液量超过分离器处理量;②分离器油水界面不稳定,直接影响分水量;③对油气水处理设备内构件产生较大的冲击力,造成焊缝疲劳而产生裂纹,最终导致管束疲劳失效,缩短了设备的使用寿命。因此有必要进行严重段塞流的预测与控制,以保证下游油气水处理设备稳定高效地工作。
1 严重段塞流形成机理及模拟
1.1 严重段塞流形成机理
通常海底管道立管部分较长(固定式平台一般为几十m到一百多m),当混相输送的流体到达立管底部时,在气体压力不足和重力回流的双重作用下,便会引发严重段塞流,严重段塞流的形成包含4个阶段[3],见图1。
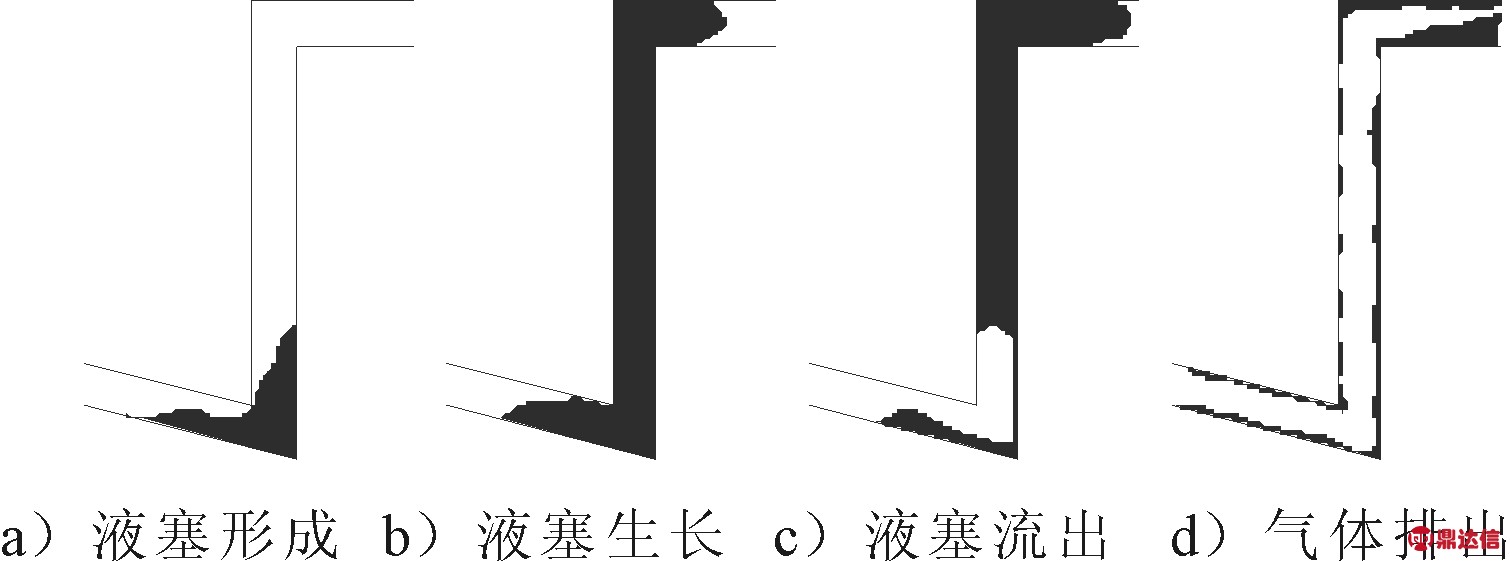
图1 严重段塞流形成过程
1)由于流量小,气体速度低,不足以将液体举升到立管顶部,外加重力作用下的回流,液体不断滑落,聚集在立管底部,液塞开始形成。该阶段明显的特征是立管底部的压力开始上升,并且几乎没有液体流入分离器内。
2)液塞完全将管线堵塞后,立管基部的压力升高,立管内的液柱也不断地增高,依然没有液体流入分离器。
3)当压力高到足以克服液塞所受的重力和阻力时,立管内的液柱在气体压力推动下开始上升,液塞后的气泡也随着液体上升。该阶段压力缓慢下降,主要是由于随着液体的不断排出,所需的压力会相应减小。
4)当气泡上升到立管顶部,管道恢复畅通,压力迅速降低,出口液体瞬时流量激增,立管底部的液体又开始聚集,下一周期的液塞开始形成,如此反复。
1.2 严重段塞流的模拟
对于段塞流的预测和模拟通常有两种方法,一种是根据经验公式进行计算,另一种是利用商业软件进行模拟。商业软件较之经验公式具有普适性好,精度高等优点。OLGA是当今最为成熟的通用多相流瞬态模拟软件,具有段塞跟踪功能,其严重段塞数据已经获得了SINTEF实验室数据以及Schmidt数据的双重验证,很多学者认为使用OLGA软件能够对严重段塞进行有效预测[3]。本文采用OLGA软件进行严重段塞流的模拟。
模拟工况:海底管道的高程剖面见图2所示。管道直径0.228 m,壁厚9 mm,外加一层厚度为20 mm的保温层,管道出口压力设定为5 MPa,空气温度为22 ℃,海水温度为6 ℃,输送流体的温度为65 ℃,流体经立管输送到平台之后,直接进入平台分离器,分离器为卧式三相分离器,直径为2 m,长度为6 m,在分离器前端装有阀门,阀门直径为0.2 m,流体流量为8 kg/s。在阀门全开的情况下,进行5 h模拟,结果见图3~5。
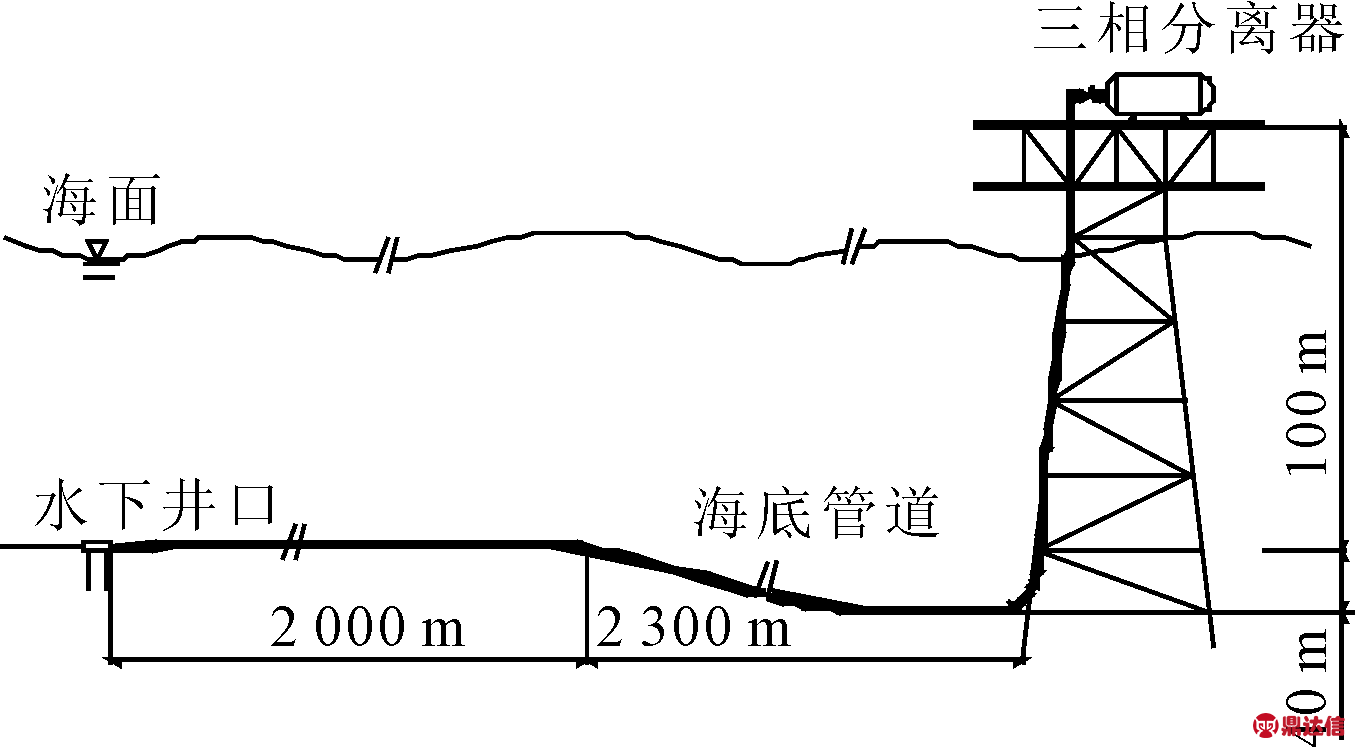
图2 海底管道布置示意
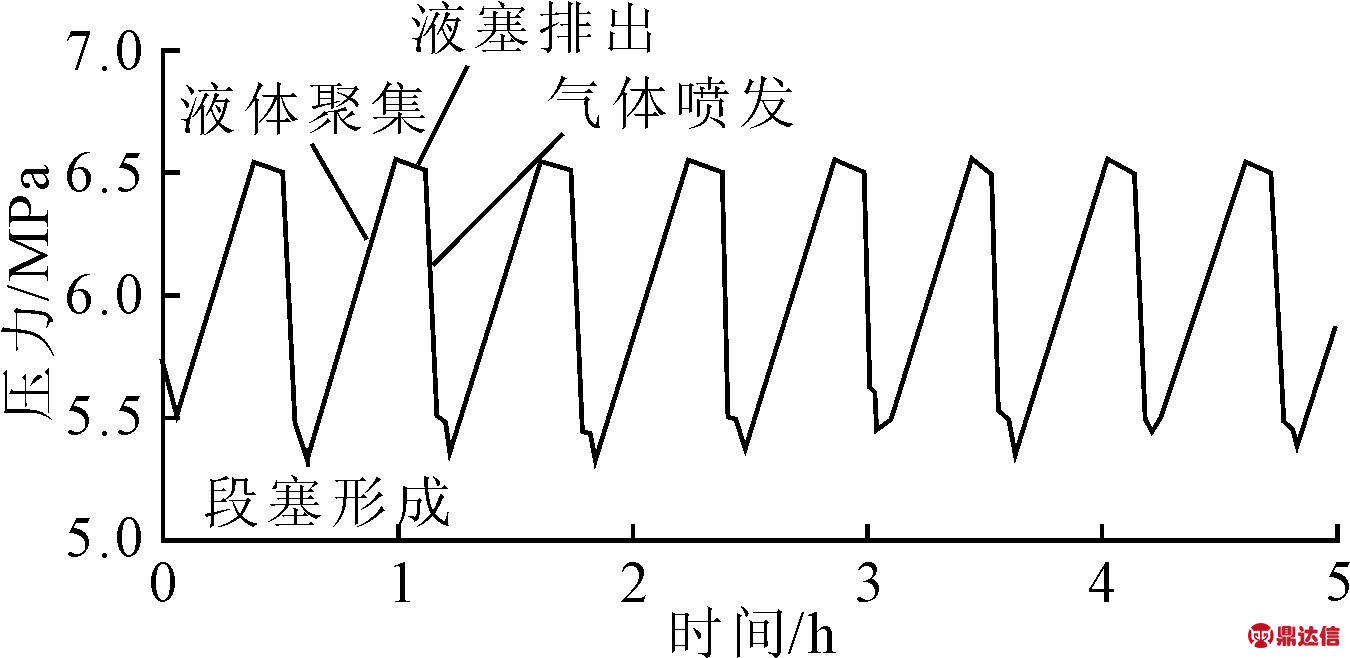
图3 立管底部压力变化
从图3可以明显看出立管底部压力变化完全符合严重段塞流周期中压力的变化趋势,表明立管段形成了严重段塞流。
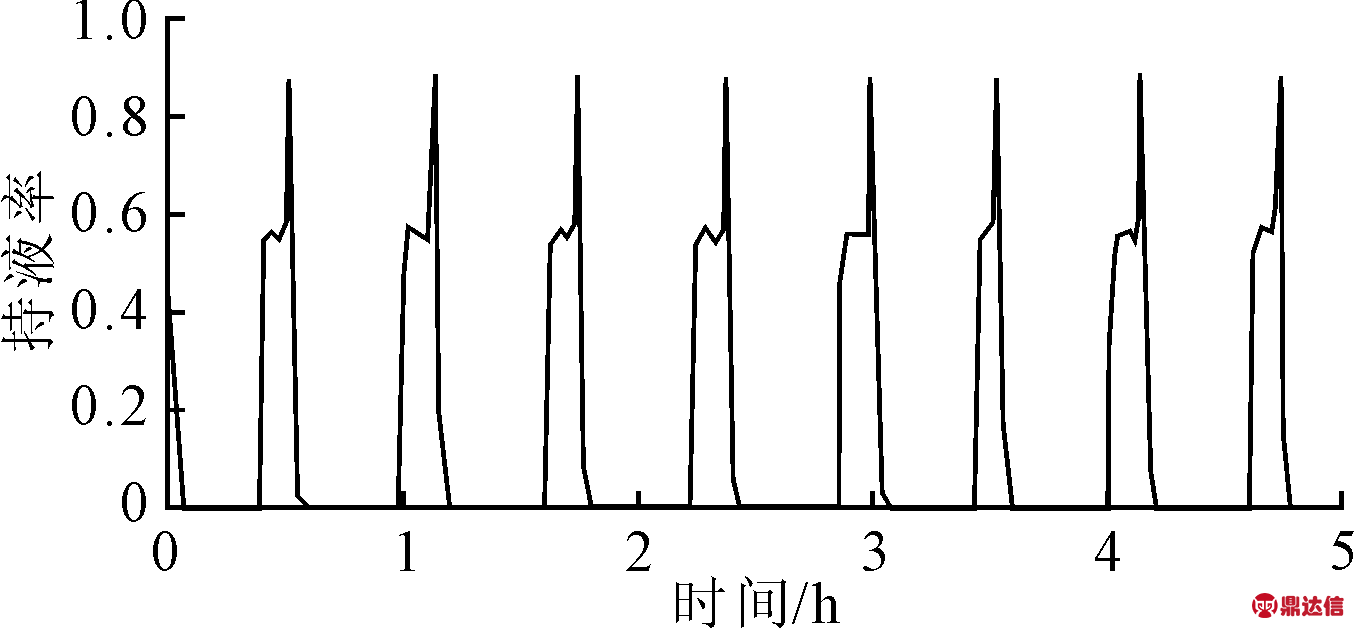
图4 分离器入口处管道持液率的变化
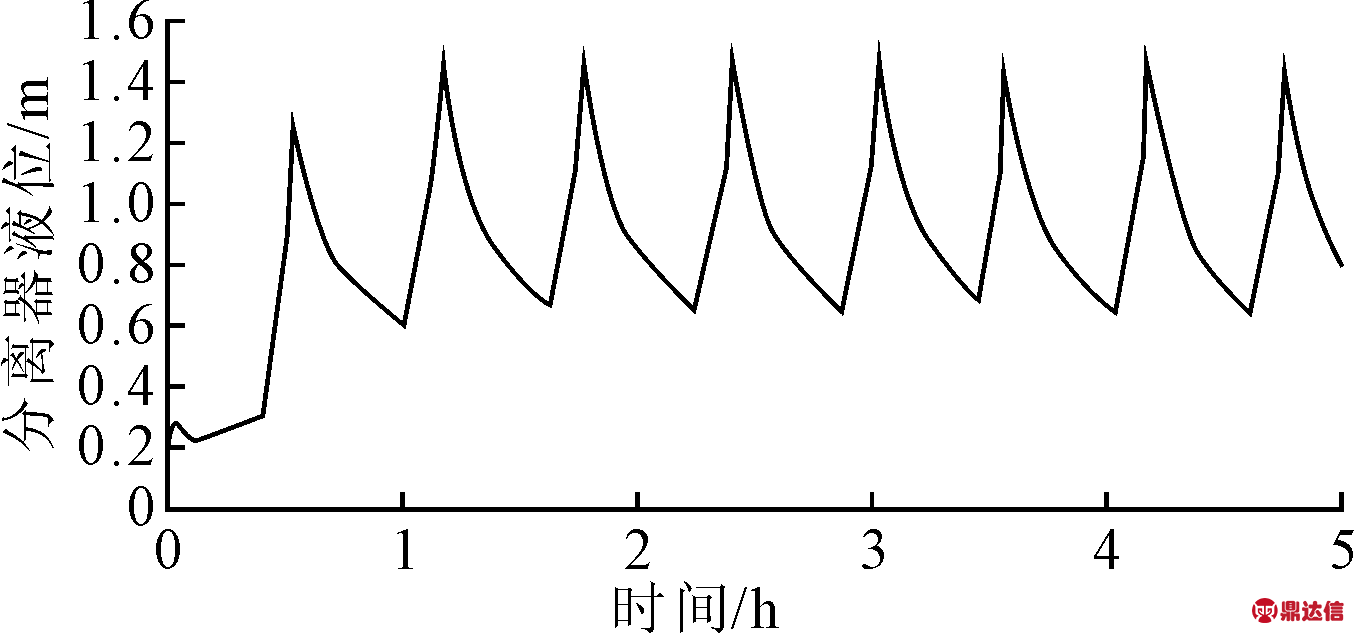
图5 分离器液位变化
与管压力变化相对应的是分离器入口处管道持液率的变化,见图4。在段塞形成的过程中持液率为0,而当段塞排出过程中,分离器入口管道持液率迅速增大,并在气体喷发时达到峰值,持液率超过0.9。持液率的这种变化必然会导致分离器内部液面的大幅波动,如图5所示,严重影响分离器的处理效果和使用寿命。
2 模拟PID控制器对严重段塞流的抑制
对于严重段塞流的控制,国内外学者提出了很多种方法,如增加回压、泵控制、声波检测与控制、气液分离、段塞捕集器等[4-6]。然而其中很多方法适用性不高,存在操作麻烦、效率不高、施工繁琐、控制不精确、占地面积大等限制。
节流法比起上述方法限制较小,并且效果明显[7]。国外在Dunbar油田16″送管线上利用自动控制方案来解决严重段塞问题。通过分离器上游的控制阀保证立管基部的压力恒定。油田使用结果表明,该种方法非常有效[8]。
自动控制方案能够根据混输管线的实时情况进行阀门的自动调节,这一点是传统节流法所不具备的。然而国内海上油气田很少见到有利用自动控制方案来进行严重段塞流控制的实例。
2.1 PID控制理论
控制系统对于维持系统的稳定有着重要作用,比如将一个系统的压力、温度、流量保持在一个容许的范围内波动。常见的一种系统为闭环控制系统,即被控制量的变化反过来会影响到控制器的输出,对于这种系统通常采用反馈控制系统来进行控制[9]。当被控对象的结构和参数不能完全掌握,或得不到精确的数学模型,控制理论的其他技术难以采用时,系统控制器的结构和参数必须依靠经验和现场调试来确定,这时应用PID控制技术最为方便。
PID控制器就是根据系统的误差,利用比例、积分、微分计算出控制量进行控制的。PID控制器的算法[10]见式(1)。


(1)
式中:Kp——放大因子; x——输入参数,如压力、液面等; τ——时间常数; u——控制器的输出信号; t——系统运行时间; ubias——控制器初始输出信号。
从PID控制器的算法可以看出,PID控制器控制主要包括三个环节。
比例(P)环节。一旦系统产生偏差信号e,比例控制立即进行调节,此时控制器的输出与输入误差信号成比例关系。如果仅有比例控制时系统输出存在稳态误差。
积分(I)环节。由于比例控制之后会存在稳态误差,即系统参数在设定值上下波动,积分控制便可消除该误差,积分作用的强弱取决于积分常数的大小,越小,积分作用越大,反之越小。
微分(D)环节。对于控制总是落后于误差的系统,微分控制可以实现“超前”控制,即在误差变得较大之前预先施加一个修正信号,从而保证控制器迅速高效地做出反应。
随着现代科技的发展,以最优控制、自适应控制、预测控制为目标,出现了大量的更为智能、高效、稳定的现代PID控制器[11]。本文使用传统的PID控制器。
2.2 PID控制阀进行段塞流的控制
节流法从本质上来讲,是通过减小阀门开度,从而减小过流面积来将立管底部的压力保持在一个较高的值。这个压力足以将流体从立管底部举升到平台上部,从而保证不会再立管底部形成液体聚集,出现严重段塞流。阀门开度如何取合适的值是比较困难的问题。开度过小,井口压力过大,影响产量;开度过大,又不能有效地将段塞排出。PID控制器有效地解决了这个问题,只需要设定想要保持的压力值,通过压力传感器实时测量立管底部压力,并将其值传递给PID控制器,PID控制器便可通过其控制算法轻松地将阀门的开度自动调节到一个合适的值。
立管底部恒定压力的选取原则是保证能够顺利地将段塞举升至平台,本文根据图3选取压力值为6.5 MPa。严重段塞流自动控制系统布置如图6所示。通过反复调节PID控制器的控制参数,最终实现了立管底部压力的控制,模拟结果见图7~10。PID控制器控制参数的最终取值为比例系数Kp=0.5,积分常数=1 000 s,微分常数为τd=0,可见实际为一个PI控制器。
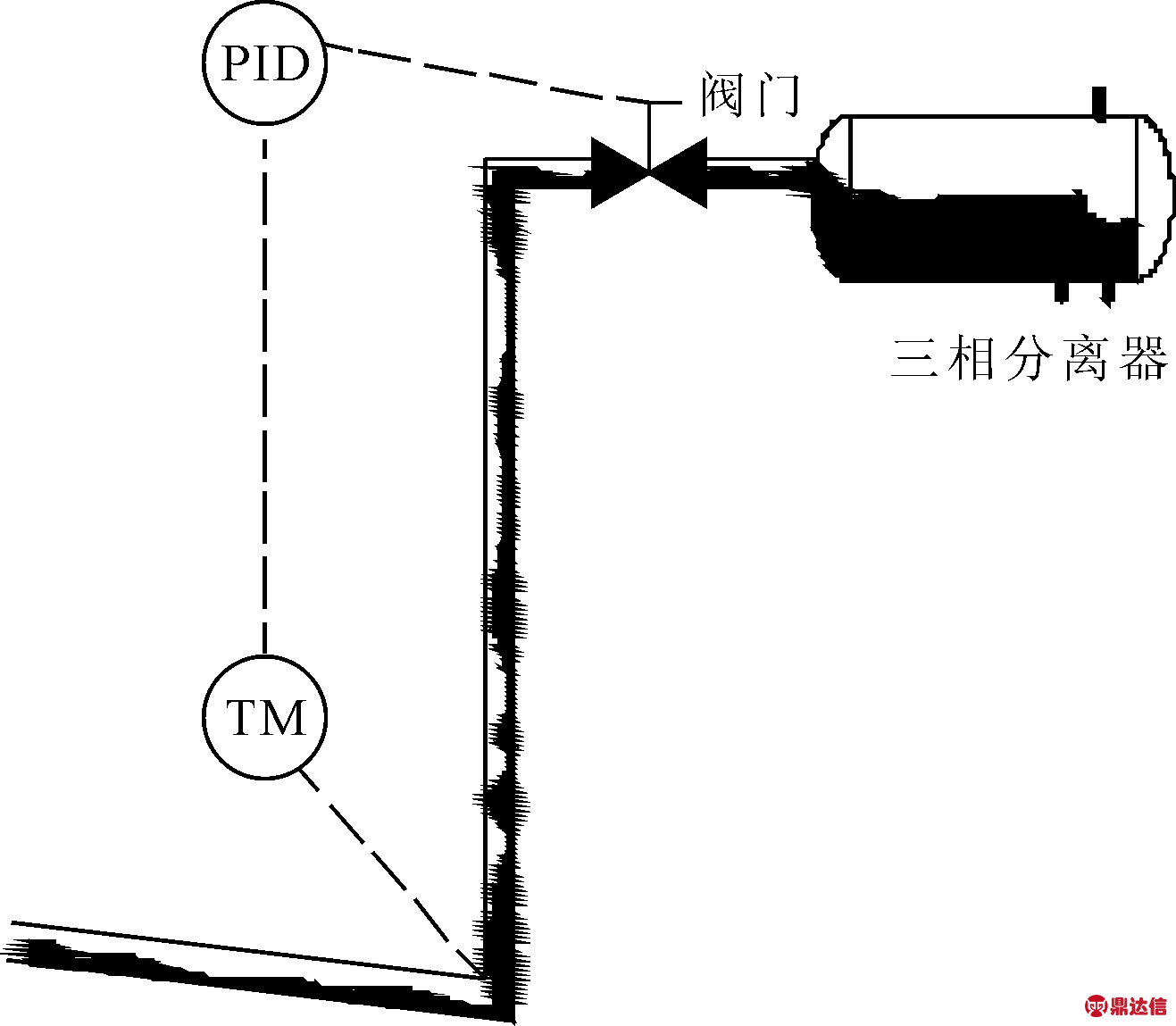
图6 严重段塞流自动控制系统布置示意
图7-9给出了利用PID控制器进行控制之后的管道系统参数的变化趋势。可见控制之后立管底部压力维持在6.5 MPa,分离器入口处的管道持液率维持在0.292,并且分离器的液位也稳定在0.882 m。有力地证明了PID控制器能够有效地实现对平台分离器入口段塞流的控制。
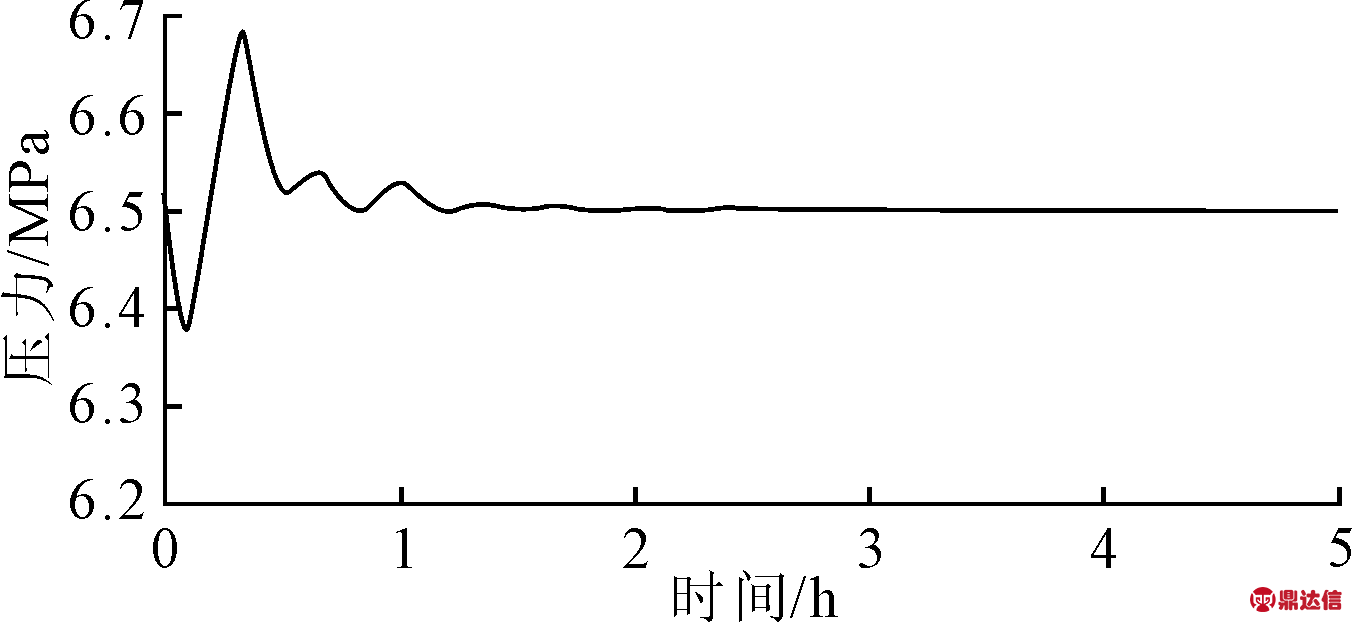
图7 PID控制后立管底部压力变化
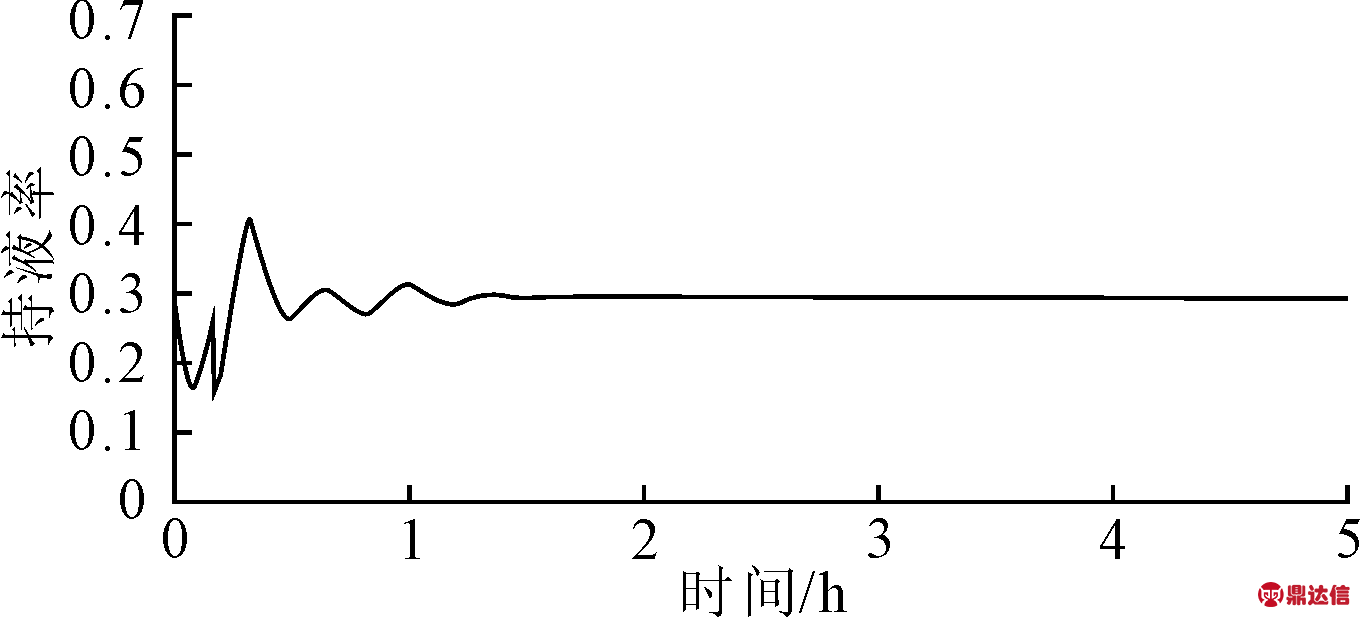
图8 PID控制后分离器入口管道持液率
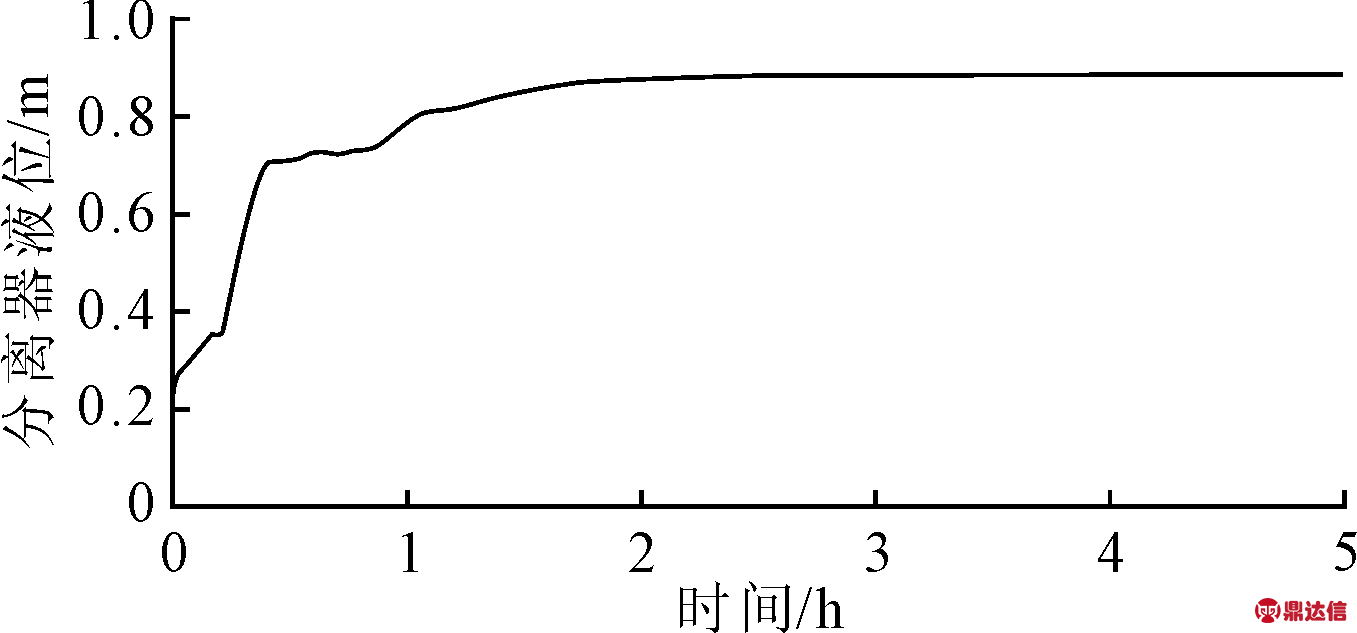
图9 PID控制后分离器液位变化
图10为阀门开度的变化,阀门开度最终保持在0.11,采用PID控制器调节阀门开度,保证了精确、及时地对严重段塞流进行控制。
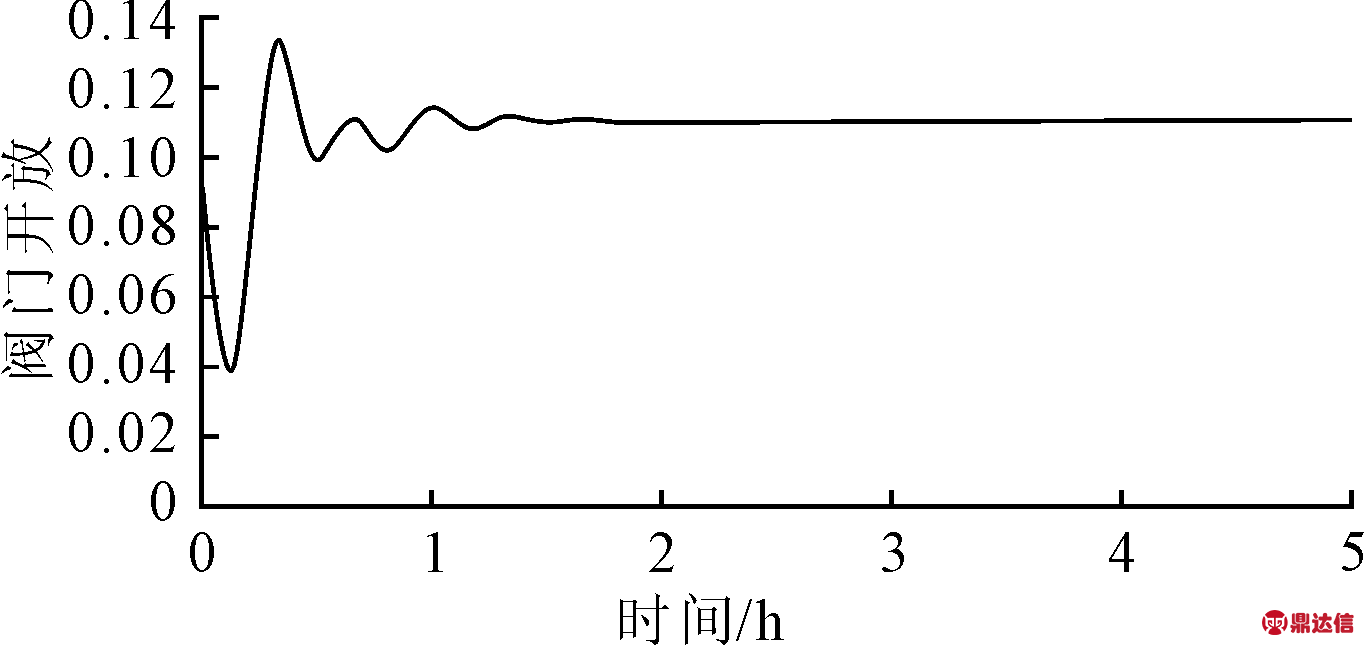
图10 PID控制后阀门开度随时间的变化
通过PID对阀门开度进行自动控制,可以得到最终阀门开度的稳定值,因此考虑可以直接将阀门开度设定为模拟结果值,也可以达到同样的效果。将阀门开度设为0.11,去掉PID控制器,模拟结果见图11。与利用PID控制器相比,压力稳定所需时间较长,但最后仍然维持在6.5 MPa。这样做有利于减少水下压力传感器的使用,减少施工量,现场适用性有待于进一步验证。
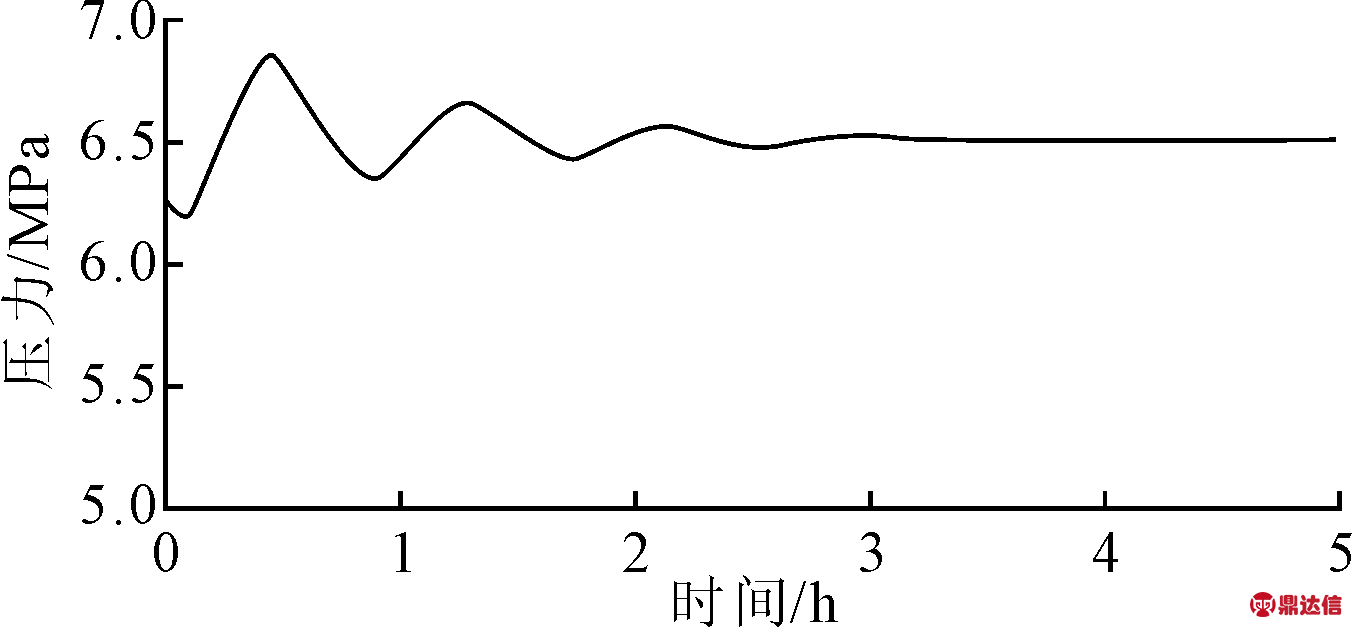
图11 开度为0.11时的立管底部压力变化
3 结论
1)利用OLGA软件能够有效预测严重段塞流,为管道及下游油气水处理设备设计提供依据。
2)利用PID控制器可以实现对平台分离器严重段塞流的自动控制,控制更为精确,效果更为明显,操作更为便捷,消除了阀门开度过大或过小对油气生产的影响,适于海上油气田严重段塞流的控制。
3)建议在实际应用PID的参数整定之前,利用OLGA软件预先对PID参数进行整定,节省现场操作时间。