摘 要:某高压气井特殊螺纹接头油管发生泄漏,结合油管泄漏检查结果,采用化学成分分析、力学性能试验等方法,对油管泄漏的原因进行了分析。结果表明:油管密封面泄漏主要集中在3 900~4 869.49 m井段,其中4 200~4 500 m井段油管密封面全部泄漏,油管泄漏既与弯曲载荷有关,也与油管刚度有关;天然气从接箍端面渗入的油管集中在1 800~4 869.49 m井段,其原因可能与温度升高之后螺纹脂性能发生变化有关,也可能与油管柱承受的载荷分布有关;多根油管接头泄漏,说明该种油管接头气密封性能不满足该井使用要求。
关键词:油管; 特殊螺纹接头; 接箍; 泄漏
油管柱泄漏,套压异常升高,是油田容易发生的失效事故[1-5]。一旦套压异常升高,油田必须进行修井作业,这不但会花费大量的人力和物力,而且存在很大的安全风险。如果油管柱泄漏是油管穿孔或者断裂所致,起出油管柱之后很容易找到油管柱泄漏位置;如果油管螺纹接头泄漏导致套压异常升高,现场作业人员要确定油管泄漏位置及泄漏接头数量是相当困难的。由于没有找到油管接头泄漏的真正原因,虽然油田花费大量资金进行了修井作业,但却没有一个有效的预防措施,此类事故仍然会不断发生。
2015年4月18日,某井A,B,C环空压力突然升高。该井完井管柱下深5 209.9 m。其中φ88.9 mm×7.34 mm规格13Cr钢110级特殊螺纹接头油管所处井段为9.01~1 949.96 m,φ88.9 mm×6.45 mm规格13Cr钢110级特殊螺纹接头油管所处井段为1 949.96~4 640.32 m,封隔器位置井深4 640.86~4 642.66 m。为了找出该井油管接头泄漏原因,笔者对该井起出的油管螺纹接头现场端进行了多种理化检验和分析,并提出了相应的改进措施,以期避免或减小此类事故的再次发生。
1 理化检验
1.1 油管泄漏情况统计分析
油管泄漏情况检验分析结果见表1和图1,部分油管接头宏观形貌如图2~4所示。封隔器位置为4 640.32~4 642.66 m,封隔器以下到井底4 655.10~4 869.49 m井段有20根油管,其中密封面泄漏的油管有13根,占65%;接箍端面渗入的油管有7根,占35%。
表1 油管外螺纹接头泄漏及接箍端面气体渗入数量统计
Tab.1 Statistics of leakage of outer threaded joints and gas penetration from the end of the coupling surface
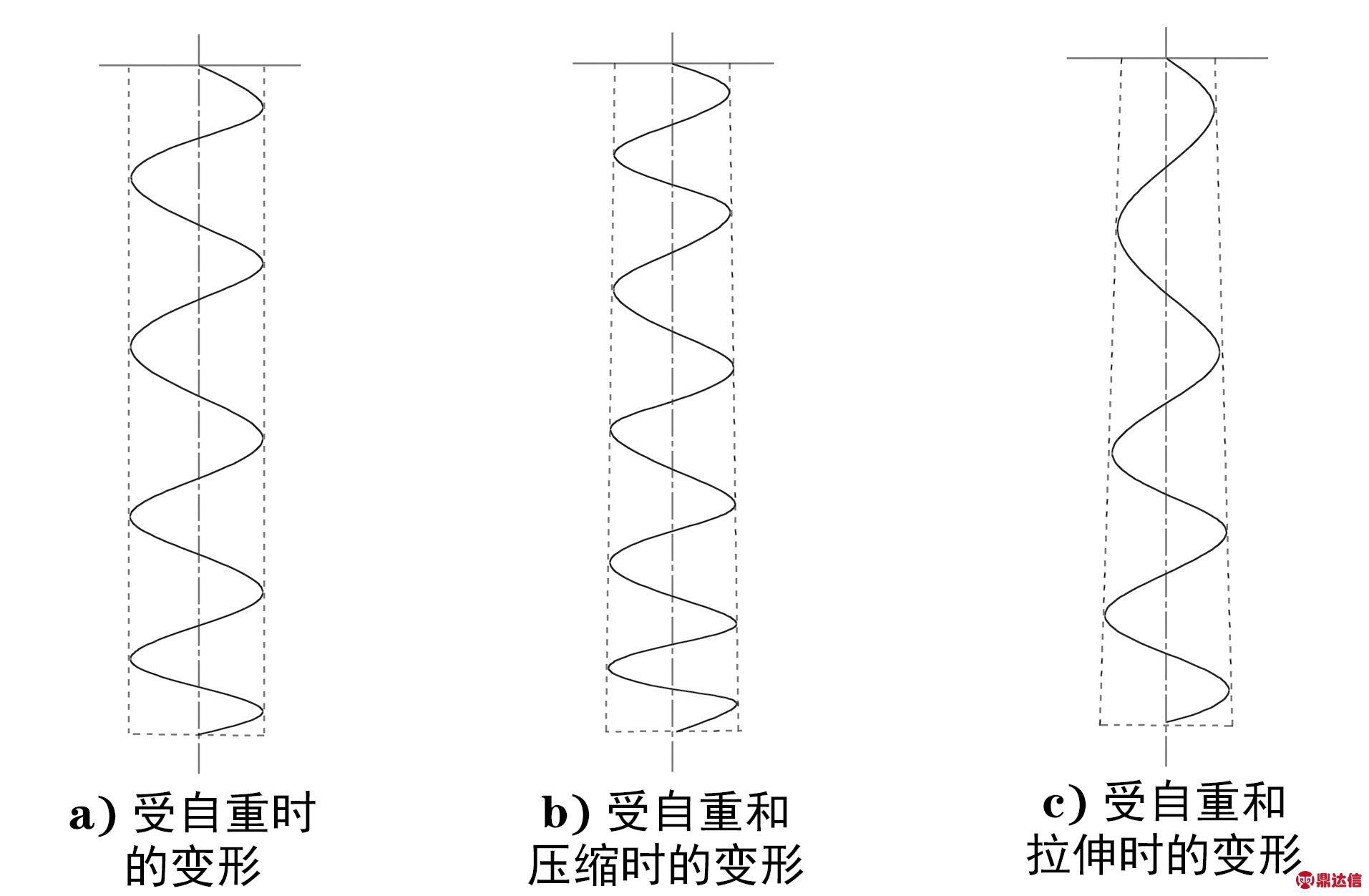
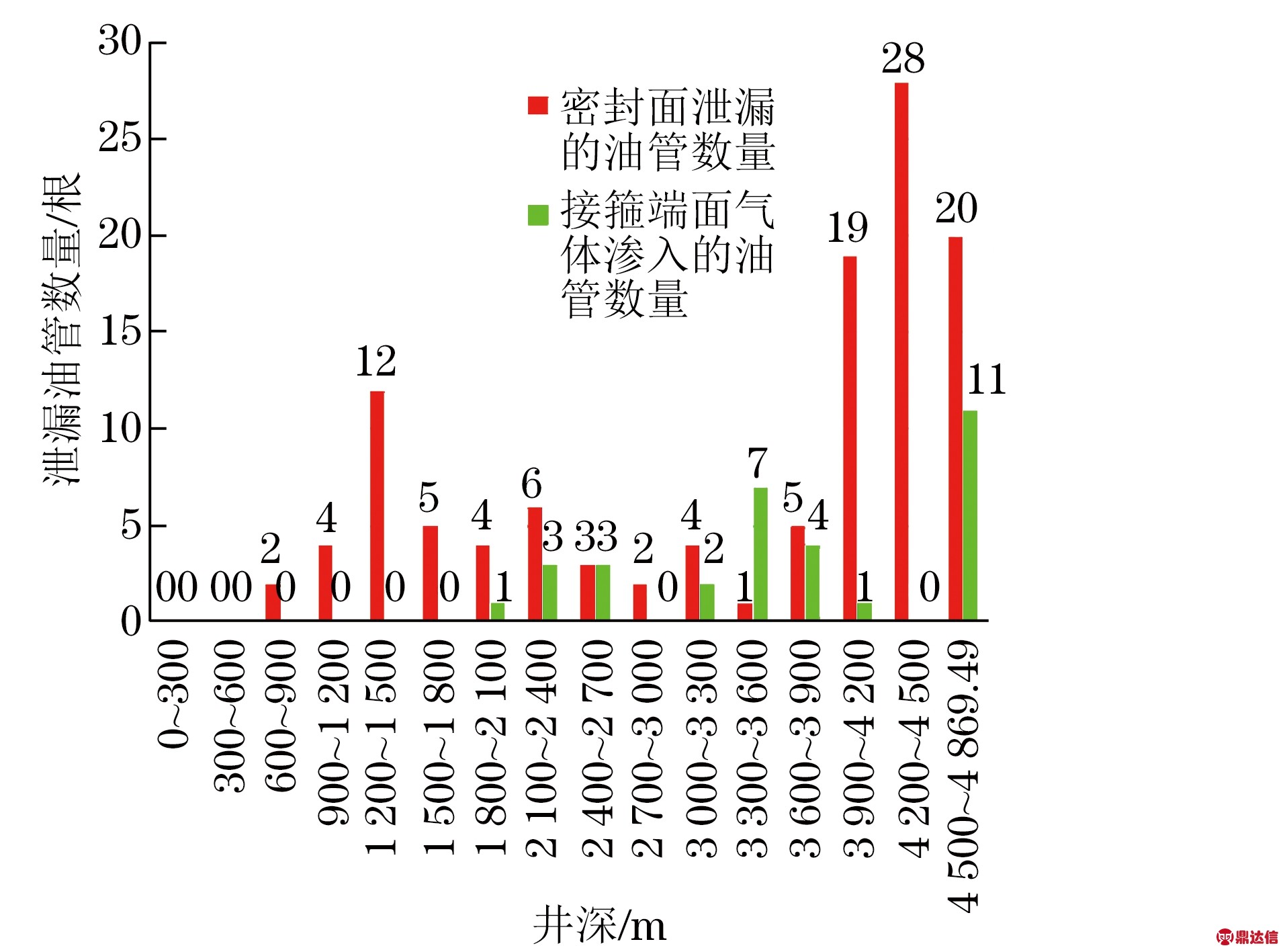
图1 油管泄漏统计分析结果
Fig.1 Statistical analysis results of the oil tube leakage
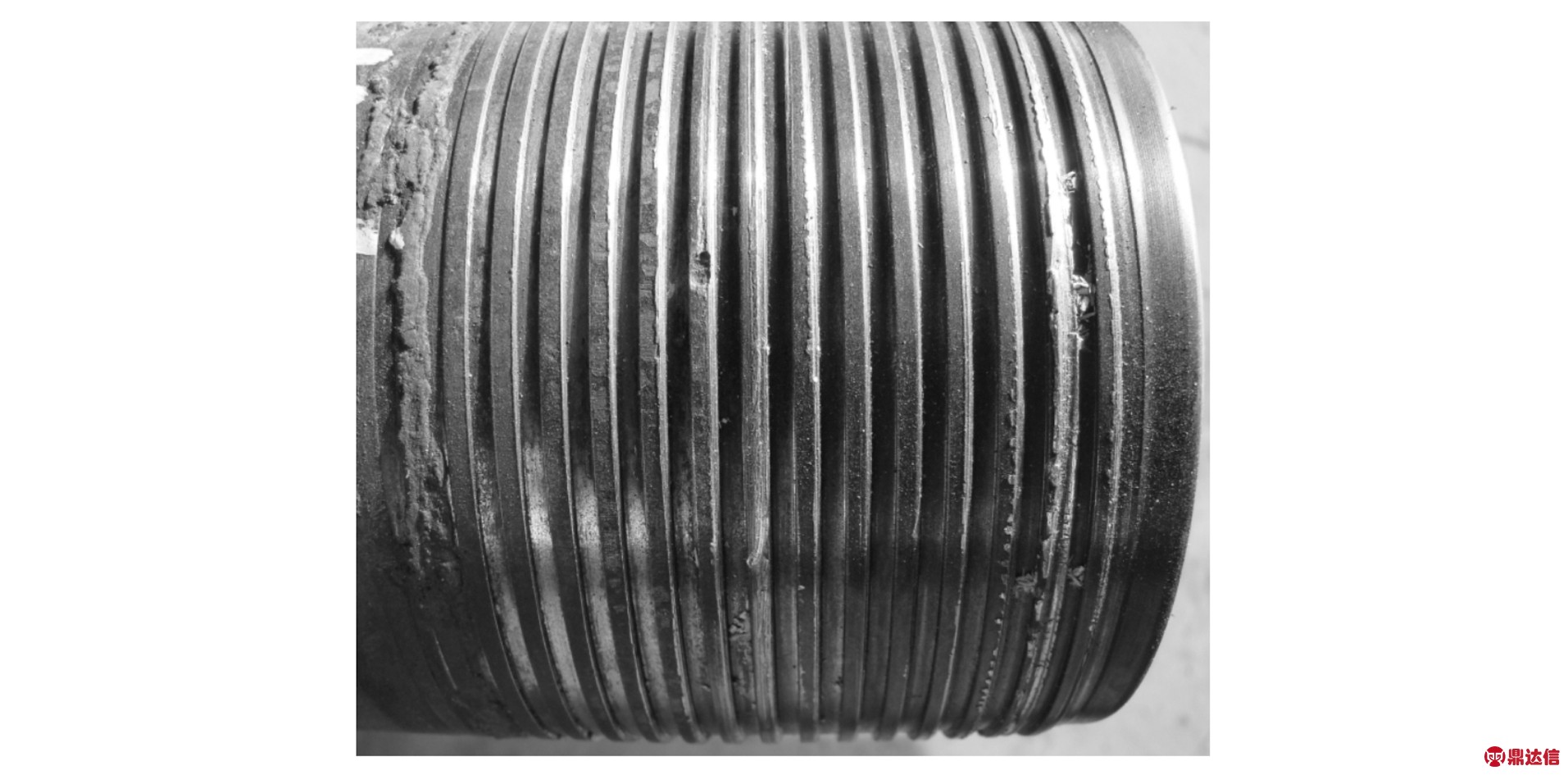
图2 441号油管泄漏外螺纹接头宏观形貌
Fig.2 Macro morphology of the leakage outer thread joint of
No. 441 oil tube
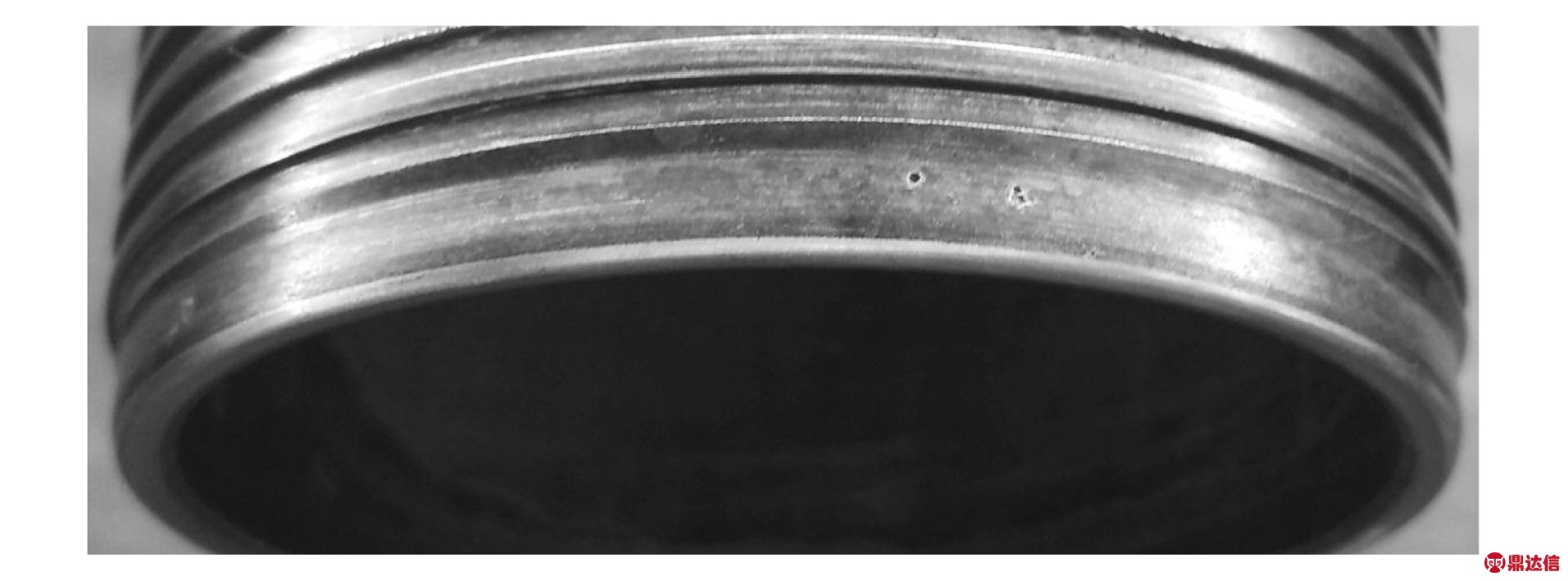
图3 266号油管泄漏外螺纹接头及密封面点蚀宏观形貌
Fig.3 Macro morphology of the leakage outer thread joint and sealing surface corrosion of No. 266 oil tube
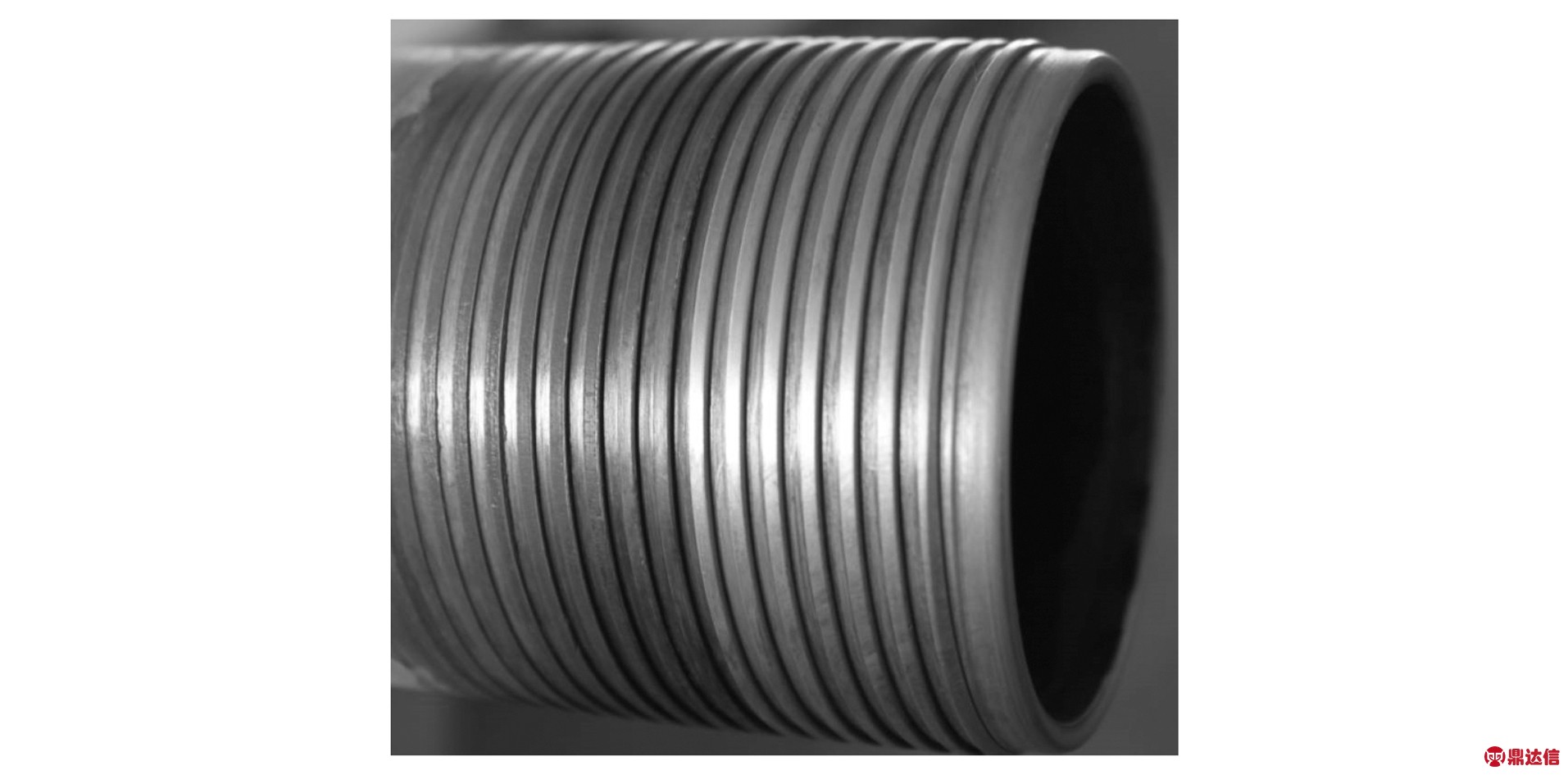
图4 343号油管接箍端面气体渗入后外螺纹接头宏观形貌
Fig.4 Macro morphology of the outer thread joint of No.343 oil tube after gas permeating from coupling end face
1.2 化学成分分析
采用ARL 4460直读光谱仪对油管试样进行化学成分分析,结果见表2。根据化学成分分析结果判断,油管试样的化学成分满足用户要求。
1.3 力学性能试验
沿油管管体纵向取19.1 mm×50 mm板状拉伸试样,沿接箍纵向取φ6.25 mm×25 mm棒状拉伸试样,沿管体纵向取55 mm×10 mm×5 mm夏比V型缺口冲击试样,沿接箍纵向取55 mm×10 mm×7.5 mm夏比V型缺口冲击试样。拉伸和冲击试验结果见表3,可见管体屈服强度、抗拉强度、断后伸长率和纵向冲击吸收能量均满足用户要求。
表2 油管的化学成分(质量分数)
Tab.2 Chemical compositions of the oil tube (mass fraction) %

表3 油管力学性能试验结果
Tab.3 Mechanical property test results of the oil tube
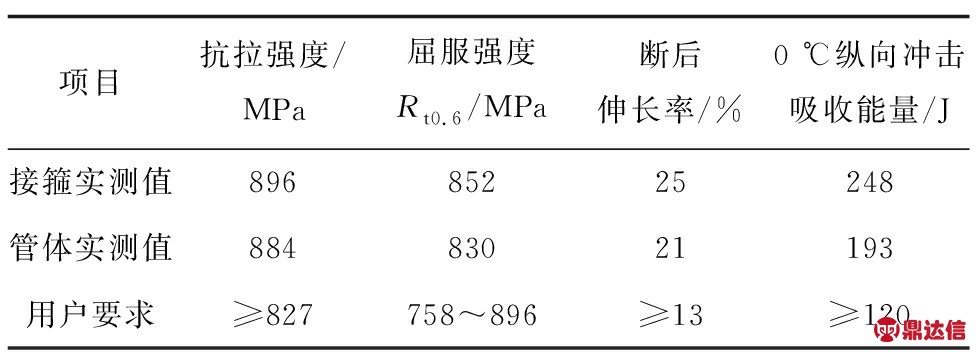
2 分析与讨论
2.1 密封面泄漏及天然气从接箍端面渗入的油管接头判定
油管柱泄漏之后会导致套压异常升高。如果是油管穿孔或者断裂导致油管柱泄漏,起出油管柱之后很容易找到油管柱穿孔或者断裂位置[6-10];如果是螺纹接头泄漏,一般不会使螺纹接头几何形状发生改变,但是天然气流过螺纹接头表面后会使整个螺纹接头表面颜色发生变化,如图2所示,甚至发生局部腐蚀,如图3所示。螺纹接头表面颜色发生变化的原因是天然气流过螺纹接头表面后天然气中的部分碳原子沉积在螺纹接头表面,螺纹接头表面发生局部腐蚀的介质是天然气中所含的CO2和凝析水[11-13]。依据螺纹接头表面颜色特征及腐蚀形貌最终确定了该井油管螺纹接头的泄漏数量。
天然气从接箍端面渗入同样不会使螺纹接头几何形状发生改变,天然气从接箍端面渗入并没有导致螺纹接头泄漏,因此只有与天然气接触的螺纹接头大端局部区域表面变色,如图4所示。螺纹接头局部表面变色原因也是天然气中的部分碳原子沉积的结果,如果天然气从接箍端面渗入和油管接头泄漏同时存在,用肉眼只能判定油管接头泄漏,而无法判定是否天然气从接箍端面渗入。依据螺纹接头变色特征最终确定了该井天然气从接箍端面渗入的油管接头数量。
2.2 油管泄漏规律及原因分析
靠近井口油管受拉伸载荷最大,油管容易发生泄漏事故。该井0~600 m井段却没有泄漏,说明拉伸载荷不是导致该井油管密封面泄漏的主要原因。图5为油管柱受不同载荷时弹性变形示意图,油管泄漏最集中的井段在3 900~4 869.49 m井段,其中4 200~4 500 m井段油管密封面全部泄漏,越靠近井底,油管柱所受的弯曲载荷越大,这说明导致油管泄漏的载荷与弯曲载荷有关。油管泄漏最严重的油管为φ88.9 mm×6.45 mm规格13Cr钢110级特殊螺纹接头油管,该油管柱刚度最弱,这说明油管泄漏也与油管的刚度有关。
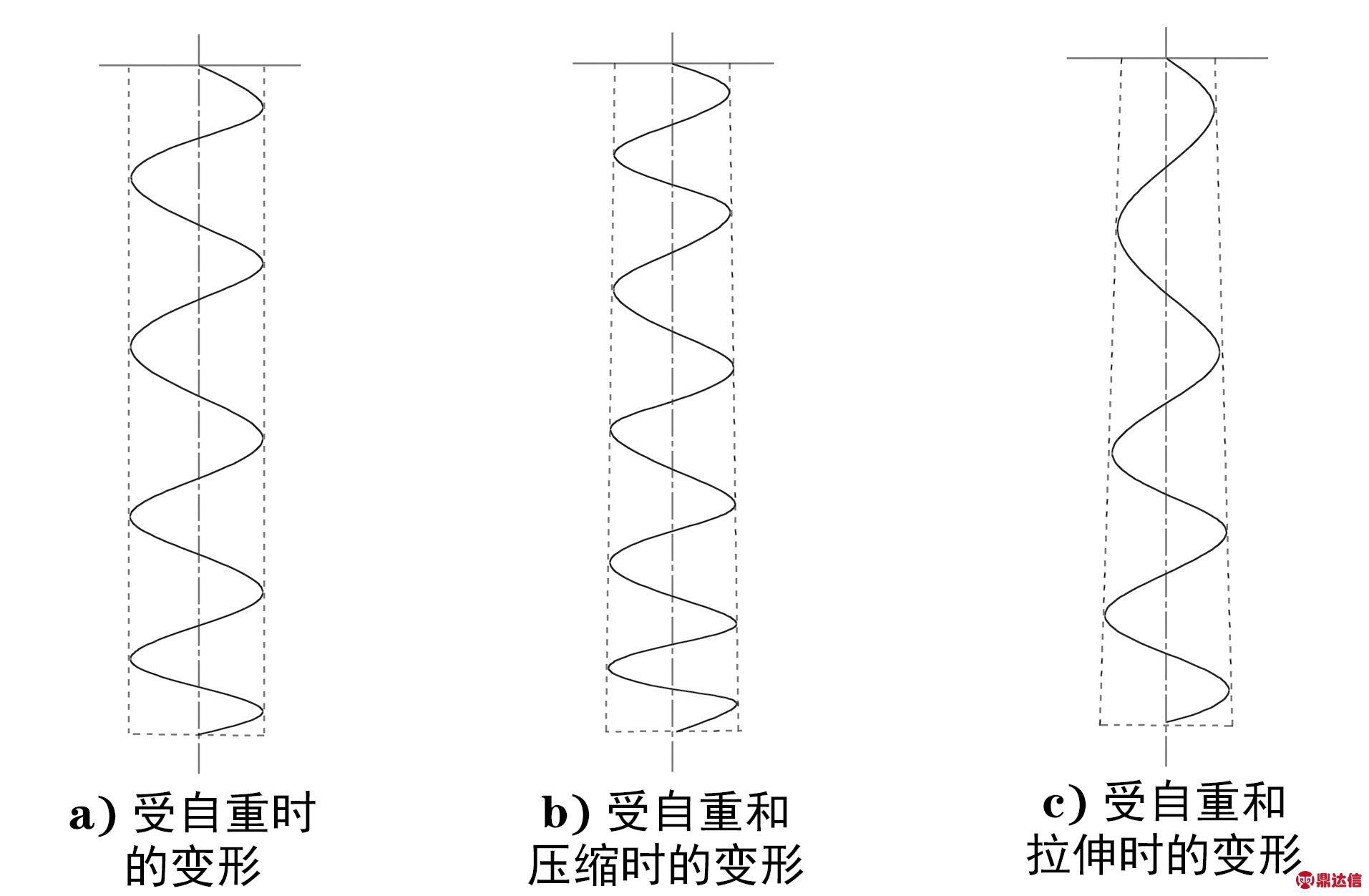
图5 油管柱受不同载荷时弹性变形示意图
Fig.5 Schematic diagram of the elastic deformation of the oil tube string under different loads:
a) deformation of self weight;b) deformation of self weight and compression;c)deformation of self weight and tension
2.3 天然气从接箍端面渗入规律及原因分析
全井接箍端面气体渗入的油管共有32根,占总油管数的6.5%。在0~1 800 m井段没有接箍端面气体渗入的油管。接箍端面气体渗入的油管集中在1 800~4 869.49 m井段,其中4 500~4 869.49 m井段接箍端面气体渗入的油管有11根,占该井段油管总量的36.7%;3 300~3 600 m井段接箍端面气体渗入的油管有7根,占该井段油管总量的22.6%。4 200~4 500 m井段没有发现接箍端面气体渗入的油管,其痕迹可能被密封面泄漏的痕迹掩盖。
接箍端面气体渗入的油管集中在1 800~4 869.49 m井段,该井段温度范围为109~128 ℃;在4 500~4 869.49 m井段接箍端面气体渗入的油管比例最高,其温度范围为128~132 ℃;而在0~1 800 m井段却没有接箍端面气体渗入的油管,其温度范围为79~109 ℃。油管接箍端面渗入可能与温度升高之后螺纹脂性能发生变化有关,也可能与油管柱承受的载荷分布有关[14]。当温度升高之后,螺纹脂中的油脂会老化,失去原有的附着能力,天然气容易渗入。在交变载荷作用下,内、外螺纹接头大端接触应力较大部位温度升高致使螺纹脂老化,螺纹脂在螺纹表面的结合力降低,天然气容易渗入。
2.4 油管接头密封性能分析
特殊螺纹接头油管应当具有气密封性能,该井虽然采用了特殊螺纹接头油管,但多根油管接头泄漏,说明该种油管接头气密封性能不足,不满足该井使用要求。
3 结论及建议
油管泄漏主要集中在3 900~4 869.49 m井段,其中4 200~4 500 m井段油管密封面全部泄漏,导致油管柱泄漏的原因既与弯曲载荷有关,也与油管刚度有关。天然气从接箍端面渗入的油管集中在1 800~4 869.49 m井段,其原因可能与温度升高之后螺纹脂性能发生变化有关,也可能与油管柱承受的载荷分布有关。其中多根油管接头泄漏,说明该种油管接头的气密封性能不满足该井使用要求。
建议在完井管柱设计时增加失效井段油管的刚度,同时在油管使用前进行油管接头气密封性能检验。