摘 要:以API标准P110钢级材质为基体材料,采用喷涂方法制备自润滑涂层。自润滑涂层以聚酰胺酰亚胺-环氧树脂为黏结剂,添加固体润滑剂二硫化钼和聚四氟乙烯。利用涂层附着力测定仪、摩擦磨损试验机,研究二硫化钼和聚四氟乙烯含量对涂层附着力、摩擦学特性的影响。试验结果表明:当聚酰胺酰亚胺-环氧树脂中改性二硫化钼的含量为30%(质量分数)、聚四氟乙烯含量为7%(质量分数)时,固化温度为280~300℃,保温时间为10~15 min,自润滑涂层具有良好的附着力、摩擦磨损性能,可满足油套管特殊螺纹接头的抗粘扣性能。
关键词:油套管;特殊螺纹接头;粘扣;自润滑涂层;二硫化钼;聚四氟乙烯
石油天然气勘探开发必须使用油套管产品,套管用螺纹连接成套管柱,形成采油通道,油管用螺纹连接成油管柱进行采油。油套管接头由内螺纹和外螺纹组成,使用过程通过上扣和卸扣进行螺纹的拧紧和松开。油套管接头重复上卸扣不发生粘扣是其重要性能指标之一,评价试验标准规定,油管和套管接头上卸扣次数需分别达到9次上卸和2次上卸不粘扣失效[1]。为了克服油套管螺纹接头的粘扣失效,现有技术采用对螺纹接头连接表面进行磷化、电镀铜锡合金等表面处理 [2-5],上扣时,再在螺纹接头连接处涂覆螺纹脂,确保螺纹接头连接处不发生粘扣失效。但螺纹脂中含有以铅、锌为主的重金属粉末[6-7],这些重金属粉末对环境会造成严重污染,不能满足环保的要求。因此,开发一种不使用螺纹脂的自润滑涂层,既保证接头上卸扣不发生粘扣,又满足环保要求。固体自润滑材料是一类概念上与传统润滑材料完全不同的新型润滑材料。传统润滑材料在摩擦界面上形成某种形式的流体或半流体膜,从而起到有效的润滑作用;而固体润滑材料则主要是依靠材料本身或其转移膜的低剪切特性而具有优良的抗磨和减摩的作用。通常固体自润滑材料是以粉末、薄膜、表面涂层、整体材料或复合材料的形式使用。随着科学技术的发展,无环境污染、耐磨寿命长、低摩擦因数、自修复能力强的固体润滑材料在电子、生物、通信、航天及航空等高科技领域应用得越来越广泛,而高分子涂层作为固体润滑涂层的主要类型之一,已成为摩擦学领域(摩擦、磨损与润滑)重要的研究课题之一[8-12]。石油天然气开采所用的油套管螺纹接头上扣过程具有滑动接触面承受载荷大的特点,目前固体润滑涂层应用研究主要集中于中、小载荷的场合[13-14],而大载荷应用研究方面的报道较少。本文结合油套管接头使用特点,研发了一种固体自润滑涂层,并进行上卸扣试验,以研究其实物性能。
1 试验方法
1.1 试验用试样
试样有两种:一种为检测涂层性能用试样,尺寸为120 mm×50 mm×1.5 mm;另一种为工业试验用实物试样,尺寸为Φ73.02 mm×5.51 mm油管。试样的主要化学成分见表1。
表1 试样的主要化学成分(质量分数) %

1.2 试验用药品
聚酰胺酰亚胺(PAI)为分散液,固体含量40%,外观为红棕色液体,25℃下的黏度为1 500~2 500 mPa·S;环氧树脂(EP)为固体粉末;经硅烷偶联剂处理过的改性二硫化钼(MoS2)粉体;聚四氟乙烯(PTFE)微粉;N-甲基吡咯烷酮、二甲基甲酰胺、乙酸乙酯和丙酮。
1.3 基材处理
试样采用喷砂处理。选用棱角多、硬度适中、80目的石英砂磨料;以0.5~0.6 MPa干燥洁净的压缩空气为动力,喷距为150 mm,喷射角为30°~75°;将磨料高速喷射至试样表面去氧化皮,并使其粗糙化。
1.4 涂料制备
取一定量的改性MoS2粉体和PTFE粉体,在SFM-1行星式球磨机的球磨罐中,以280 r/min的速度球磨6 h,然后加入一定量的PAI和经丙酮溶解的EP树脂,以及由N-甲基吡咯烷酮、二甲基甲酰胺、乙酸乙酯按一定比例混合的溶剂,再次球磨6 h后,过300目不锈钢筛网即得PAI-EP固体润滑涂料。
1.5 涂层制备
用喷枪沿试样表面来回均匀喷涂,喷涂压力为0.3~0.4 MPa,喷枪嘴与试样的距离为 100~150 mm,涂层厚度控制在10~15 μm。将喷涂后的试样放入电热鼓风干燥箱中,于280℃烧结10 min,随炉冷却,即得PAI-EP固体润滑涂层。
1.6 性能测试
按GB 1720—1989《漆膜附着力测定法》测定涂层的附着力。
用MRH-3G摩擦磨损试验机,以环-块摩擦副的形式来做自润滑涂层的摩擦特性试验。试验机有自动加载装置,可灵活施加所需载荷。试验时试样固定,对偶件按设定速度做回转运动。对偶材料为45钢,经淬火处理后硬度为50~53 HRC。试验时的摩擦力和摩擦因数由测量装置自动采集和计算。
2 试验结果及分析
2.1 固化温度和时间对涂层附着力的影响
测定同一涂层配方、不同固化工艺(温度、时间)对涂层附着力的影响,具体见表2。
表2 不同固化温度和时间对涂层附着力的影响
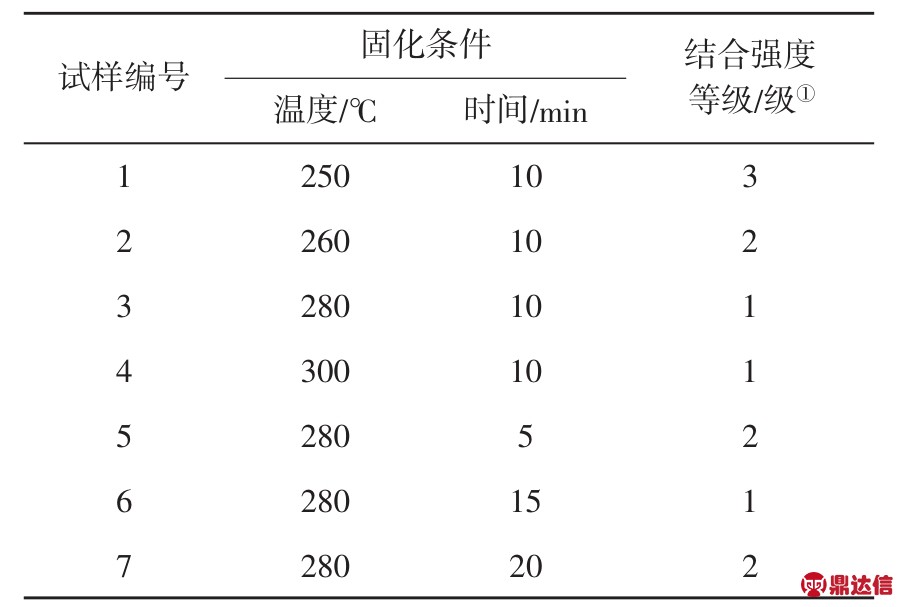
注:①用划圈法测定。
从表2可看出,PAI-EP基固体自润滑涂层的最佳固化温度为280~300℃,时间为10~15 min。固化温度低,则涂层熔融黏度高,流动性差,影响涂料的流平,进而影响涂层与金属基体的充分粘扣,降低了涂层的附着力;固化温度过高,涂层中的树脂将发生变质甚至分解,使涂层与底材的附着力下降。固化温度一定时,适当延长固化时间可提高涂层的附着力,这是因为PAI-EP树脂交联需要一定的时间,但固化时间过长,PAI-EP树脂过度交联,反而影响涂层与底材间的附着力。
2.2 改性MoS2含量对摩擦特性的影响
涂料中加入不同含量的改性MoS2,MoS2含量对涂层摩擦因数的影响如图1所示。由图1可见,改性MoS2含量对涂层的摩擦因数有重要的影响,涂层摩擦因数随着涂料中改性MoS2含量的增加而降低。这是由于涂层的润滑特性随改性MoS2含量增加而得到提高,MoS2润滑功能的实现是一个润滑膜转移的过程。在摩擦起始阶段,涂层在摩擦界面中被剪切时,剪切主要发生在膜内的MoS2润滑粒子上,对偶件间的摩擦转变为涂层的内摩擦。涂层完全隔开了两个对磨金属表面,金属之间没有接触,也即没有磨损。随着摩擦过程的进行,被剪切掉的部分润滑微粒在压力作用下,黏附在原先没有涂膜的表面,形成了一层润滑转移膜,此时摩擦效果最佳。MoS2具有较低的层间剪切强度,且其与金属基体有较强的附着力,故摩擦因数随其含量的增加而减小。但若MoS2含量过多,会使涂层的韧性和结合强度降低,使得摩擦过程中涂层更容易撕裂和剥落,润滑膜过早失效而造成金属间对磨。考虑到PAI-EP基固体自润滑涂层的实际工作条件,要求涂层与金属基体间的附着力大,确定涂料中添加的MoS2含量最高为30%。
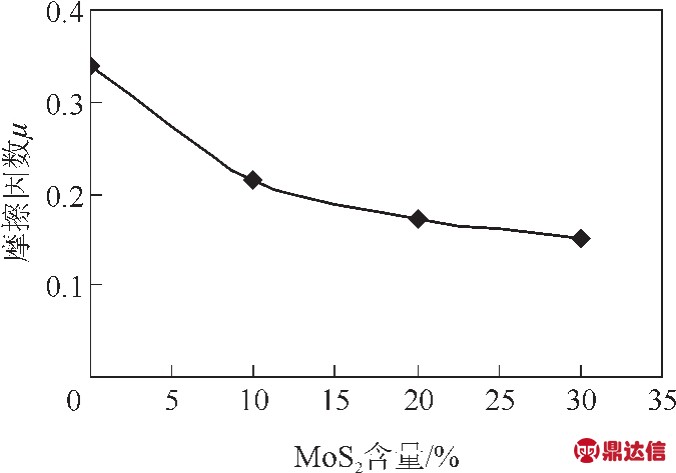
图1 涂料中MoS2含量对涂层摩擦因数的影响
载荷与摩擦因数的关系如图2所示。从图2可以看出,涂层的摩擦因数随载荷的增大而减小,随着涂料中改性MoS2含量的增加而减小;MoS2含量为30%的涂料,在较高载荷(300 N)下的摩擦因数接近0.1,具有优良的减摩性能。在试验载荷范围内,涂料中添加30%改性MoS2的减摩性能明显优于其他涂料。
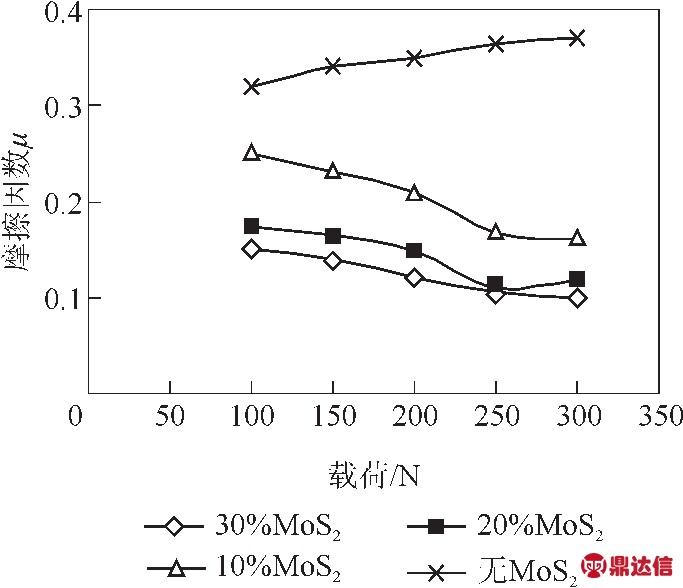
图2 载荷与摩擦因数的关系
载荷与磨损率的关系如图3所示。从图3可以看出,磨损率随载荷的增加而减少,随涂层中改性MoS2含量增加而减少。这说明在偶件表面,仅PAI-EP树脂难以形成均匀的转移膜,故磨损率和摩擦因数均较大。MoS2是各向异性的层状化合物,在平行于基础面方向的硬度为800~1 000 VPN,而在垂直于基础面方向的硬度只有20~80 VPN[15]。MoS2是机械地转移到对摩表面而形成固体润滑膜,从而将对摩表面间的摩擦转变为MoS2间的摩擦。PAI-EP改性MoS2涂层在偶件表面形成了转移膜,该转移膜可有效阻止摩擦副表面材料的相互转移及涂层同偶件表面的直接接触;因此,涂层表现出良好的抗磨和减摩性能。
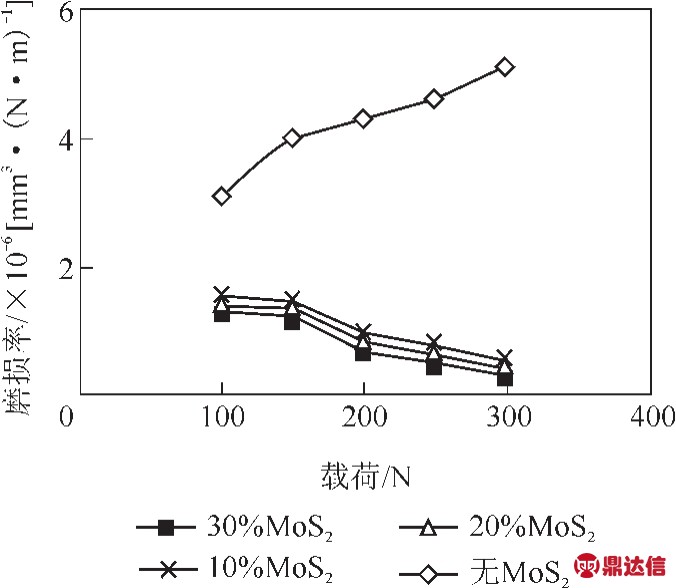
图3 载荷与磨损率的关系
2.3 PTFE含量对涂层摩擦性能的影响
涂料中PTFE含量与涂层摩擦因数的关系如图4所示,发现涂层的摩擦因数随着涂料中PTFE含量的增加而降低。
对比图1和图4可以看出:添加不同含量的PTFE和改性MoS2均可降低涂层的摩擦因数,其中添加30%改性MoS2的减摩性能最佳,其摩擦因数同PAI-EP相比降低了约56%。

图4 涂料中PTFE含量与涂层摩擦因数的关系
涂料中PTFE含量与涂层磨损率的关系如图5所示。从图5可见,PAI-EP中加入PTFE后能降低涂层的磨损率,提高涂层的耐磨性能。
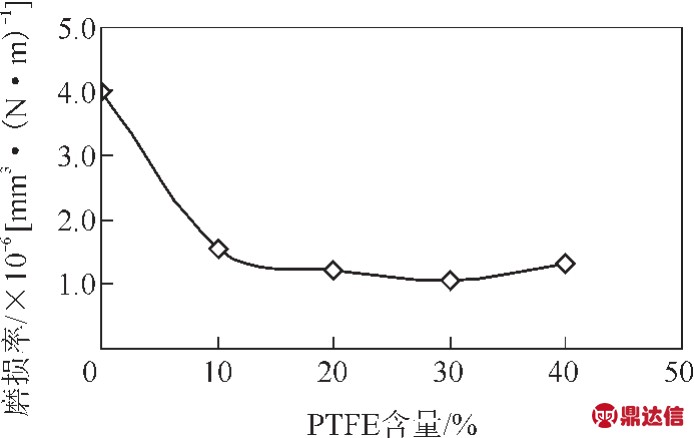
图5 涂料中PTFE含量与涂层磨损率的关系(载荷为200 N)
2.4 改性MoS2和PTFE对涂层摩擦性能的影响
涂料中固定改性MoS2含量为30%,改变PTFE添加量时,涂层的摩擦因数变化如图6所示。从图6可知,涂料中加入PTFE可降低摩擦因数,当PTFE含量超过7%,涂层的摩擦因数降幅趋缓。
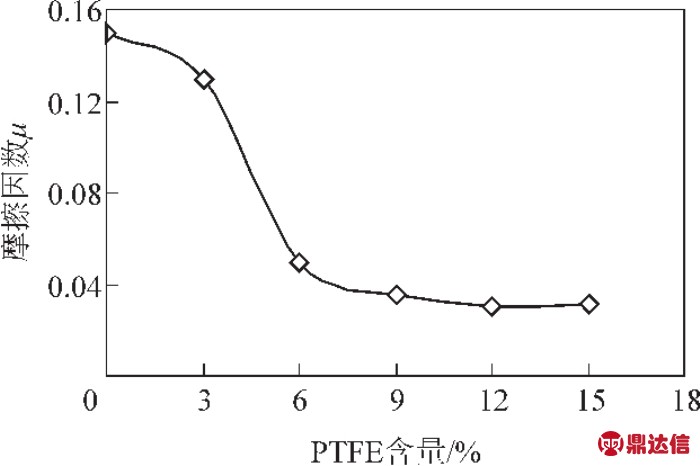
图6 含30%MoS2涂料中加入PTFE后对涂层摩擦因数的影响
当涂层中同时加入改性MoS2和PTFE,比单独加改性MoS2或PTFE具有更低的摩擦因数。由于PTFE与PAI-EP表面能不同,把含有这两种固体润滑剂的树脂涂料涂装在金属基材上时,各聚合物与金属基材的界面张力的差异,造成一种聚合物对基材润湿性能好,成为底漆;另一种对基材润湿性差,成为面漆。产生所谓“自分层效应”。PTFE与金属基材的表面张力差值大,PTFE与PAI-EP混合均匀后涂覆在工件表面,使得PTFE富集于表面,PAI-EP富集于涂层底部,进一步降低了涂层的摩擦因数,发挥了涂料中改性MoS2和PTFE的协同效应。
2.5 实物试验
添加30%(质量分数)改性MoS2和7%(质量分数)PTFE的涂料,对Φ73.02 mm×5.51 mm规格P110特殊螺纹接头油管接箍进行了表面喷涂处理,完成实物上卸扣试验研究。特殊螺纹接头油管上卸扣试验结果见表3,11次卸扣后油管管体、接箍实物如图7~8所示,产品上卸扣性能超出了API RP 5C5—2017 标准[1]9 次上卸扣要求。
表3 特殊螺纹接头油管上卸扣试验结果
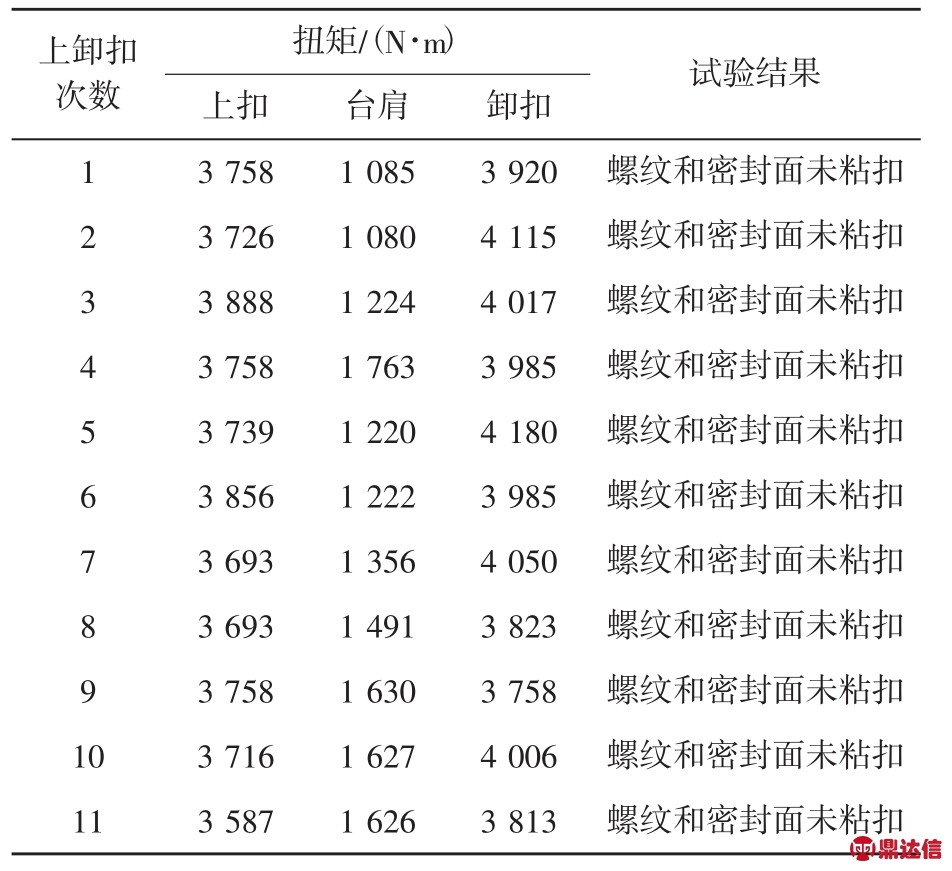

图7 上卸扣试验用油管管体实物
3 结 论
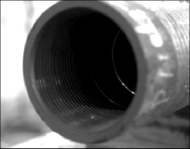
图8 上卸扣试验用油管接箍实物
3.1 摸清果园土壤养分状况 根据2017年对彬州市果园土壤检测,0~50 cm土层养分总体状况如下:有机质平均含量10.15 g/kg,与陕西省果园土壤养分含量分级指标数值10.1~13 g/kg对比,偏低;碱解氮平均含量42.6 mg/kg,与陕西省果园土壤养分含量分级指标数值35~55 mg/kg对比,较低;磷平均含量33.2 mg/kg,与陕西省果园土壤养分含量分级指标数值≥30 mg/kg对比,丰富;钾平均含量198.1 mg/kg,与陕西省果园土壤养分含量分级指标数值160~200 mg/kg对比,适宜。
(2)涂层的摩擦因数随载荷的增大而减小,随涂料中改性MoS2含量的增加而减小;改性MoS2含量为30%的涂料,表现出优良的减摩性能。
(3)涂料中同时加入改性MoS2和PTFE,具有协同效应。
(4)添加30%改性MoS2和7%PTFE的涂料,喷涂Φ73.02 mm×5.51 mm P110特殊螺纹接头油管,油管的上卸扣性能超出了API RP 5C5—2017标准9次上卸扣要求。