摘要:通过建立机紧状态下的扭矩方程,应用MATLAB软件对P110油井钢管圆螺纹接头在正常机紧、过机紧和欠机紧状态下的扭矩进行仿真,并借助ANSYS软件分析了圆螺纹接头在不同机紧状态下的力学状态。研究结果表明:油管和接箍啮合的开始部位存在明显的应力集中区,在过机紧(2.5圈)状态下,应力集中区将超过规定值而增大螺纹接头粘扣的趋向。
关键词:油井钢管;圆螺纹;粘扣;受力分析;仿真
随着井深增加,油井钢管的工况条件变恶劣,粘扣、刺扣、泄漏、滑脱掉井、挤毁、疲劳断裂、腐蚀等失效事故时有发生,且造成巨大的经济损失。在诸多失效形式中,油管螺纹的粘扣占较大比例[1-11],轻者表现为损伤螺纹表面,影响油管的反复上卸扣能力和上扣扭矩,严重时降低油管的密封性及连接强度,使之在螺纹连接处发生泄漏或掉井事故。通过油井钢管圆螺纹接头受力过程的分析,借助计算机仿真技术,研究油井P110钢管圆螺纹接头在不同机紧状态下的力学状态,从而为现场实际操作提供理论指导。
1 齿面接触力扭矩方程分析
油管在服役中螺纹接头部位要经历反复上卸扣的扭矩作用,是整个油管中最脆弱、最容易损坏的部分,油管上卸扣时横截面如图1所示。

图1 上卸扣时油管和接箍的横截面
上卸扣扭矩为

式中,Fx为轴向拉伸应力。
上扣接触应力为

径向过盈量δ,经换算得

式中,R为啮合处公称节圆半径,mm;L为轴向啮合长度,mm;μ为摩擦因数;a为油套管内半径,mm;b为螺纹中径,mm;c为接箍外半径,mm。
可见,锥管螺纹上扣位置与扭矩及过盈量成正比,旋扣位置越长(啮合螺纹越多),上扣扭矩越大。采用带钳或B型大钳操作,管材夹持部位有适量的夹持力作用,接头螺纹旋接同样形成齿面接触应力与扭矩引起的径向、环向应力,上扣扭矩越大,齿面接触应力与复合应力越大。在上扣过程中,随着啮合螺纹的增加,螺纹之间的复合应力和齿面接触应力越来越大,螺纹之间的摩擦力也随之增加。
P110油井管基本参数:
油套管内半径 38 mm
接箍外半径 56 mm
油管螺纹端半径 45.80 mm
轴向啮合长度 54.36 mm
油管螺纹锥度 50.825 mm/m
螺纹齿顶高 1.226 mm
每英寸螺纹牙数 8牙
有效螺纹长度内的螺纹圈数 17.12圈
根据API RP 5CI标准[12],API圆螺纹接头在使用时,需要施加一定的扭矩使其达到合理的上扣位置(机紧圈数)。标准机紧状态下«88.9 mm× 6.45 mm的P110油管在使用时要求有2圈的机紧圈数,欠机紧状态下为1.5圈的机紧圈数,过机紧状态下为2.5圈的机紧圈数。选取单元距油管螺纹端长度为x(mm),则得到标准机紧、欠机紧、过机紧3种状态下相关的参数如表1。
表1 3种机紧状态下螺纹啮合相关参数

应用MATLAB 6.01软件编程、计算和仿真,得到如图2所示的3种机紧状态下上扣所需扭矩曲线。由图2可以看出,在过机紧0.5圈状态下,上扣扭矩将达到3 020 N·m,已经超过P110油管规定扭矩范围(1 750~2 930 N·m)。由于过机紧状态下的有效螺纹长度增大,使上扣扭矩增加,齿面接触应力增高,塑性应变的变形增大,螺纹粘扣倾向随之增大。欠机紧状态下0.5圈上扣,所需扭矩比标准机紧状态所需扭矩小,但是欠机紧状态是内、外螺纹配合公差形成“小脑袋带大帽子”的情况,将影响螺纹接头的抗滑脱能力。在标准机紧状态下,上扣所需扭矩在规定的扭矩范围内,同时有利于油管密封及防止接头滑脱。分析认为:过扭矩情况下油管所受的轴向外力最大,也最容易发生粘扣。

图2 3种机紧状态下上扣扭矩
2 上卸扣扭矩和齿面接触应力仿真
考虑到油套管上卸扣和拉伸过程中加载荷是对称于其中心轴线的,而且在旋合过程中螺纹升角< 2°,力学分析模型可做轴对称处理。本研究中使用ANSYS5.7有限元分析仿真软件,在Windows环境下进行分析仿真。
首先对几何模型进行网状有限元模型的划分,以油管的轴线为x轴,油管螺纹小端面为 y轴建立笛卡尔坐标系。所研究的油管为P110«88.9 mm× 6.45 mm加厚油管,其中接箍外径«112.0 mm,管体外径«88.9 mm,管体壁厚«6.45 mm。为了研究轴向力的影响,对接箍的一端施加全约束,左边施加x方向的约束,对油管内壁施加 y方向的约束。分别在正常扭矩、过扭矩、欠扭矩3种情况下对油管接头施加800 kN的轴向载荷,根据所加的约束和载荷以及指定的关键路径绘出相应的仿真图形。标准扭矩机紧状态、过扭矩机紧状态和欠扭矩机紧状态的仿真结果分别如图3~5所示。
由图3可以看出:啮合螺纹两端接触应力非常高,最大值出现在油管螺纹啮合的第 1牙,为946.015 MPa,接箍最外端的螺纹扣受力达到756.816 MPa,而且外螺纹顶端有效螺纹长度范围内承载面接触力比较大,导向面接触应力几乎为零;但在外螺纹小端8~9牙以内,承载面与导向面上接触应力都很小,这种接触应力分布特征显然与轴向力有关。从外螺纹有效螺纹开始,接触力骤然变大,即在开始的一两处存在着明显的应力集中。此后,接触力逐渐变小,从第5牙起至第12牙,接触应力小到几乎为零,至于从第13牙起至大端应力又升高,显然与上扣机紧扭矩有关。分析结果表明:油套管在上扣过程中,螺纹粘扣在螺纹的2个面均可发生,而且啮合螺纹两端粘扣倾向严重。有轴向力作用后,承载面容易产生粘扣,而且螺纹顶端接触应力较大处的粘扣倾向严重。
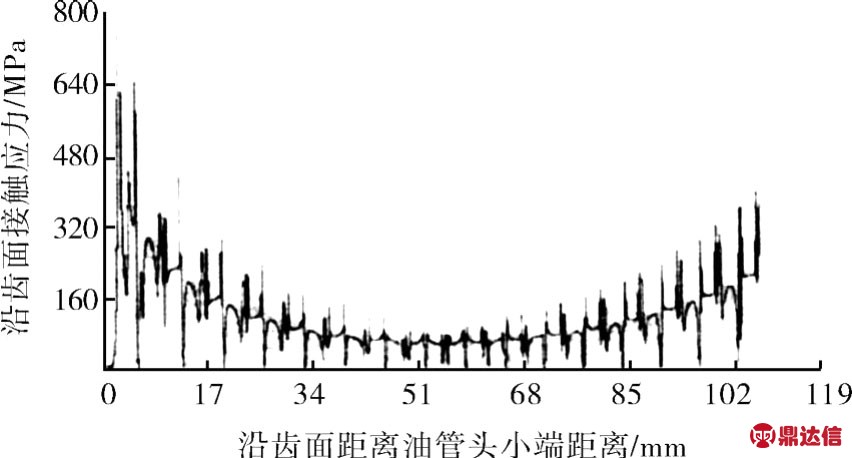
图3 标准扭矩机紧状态仿真结果
图4为螺纹机紧2.5圈时800 kN轴向拉力条件下沿齿面的齿面接触力图形,可以看出,沿螺纹牙侧面(包括承载面和导向面)接触应力分布规律与图3基本一致,但是最大接触应力值达到 978.408 MPa,比标准扭矩机紧状态下的最大值高3.42%。所以,随着上扣扭矩增加,齿面接触应力增高,塑性变形倾向增大,导致螺纹粘扣倾向随之增大。
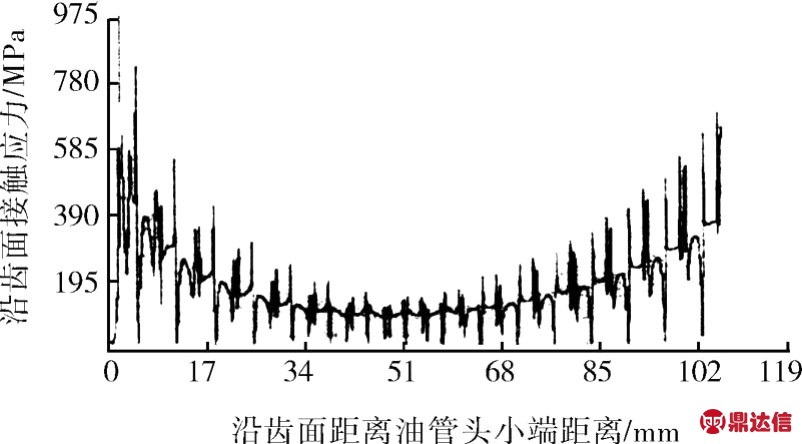
图4 过扭矩机紧状态仿真结果
由图5可以看出,欠扭矩时螺纹的齿面接触力分布也和标准扭矩以及过扭矩的齿面接触力分布趋势基本一致。机紧1.5圈时,接触应力的最大值为807.344 MPa,分别比标准扭矩机紧状态下低14.66%,这说明欠扭距时齿面接触力有所下降。从力学方面看,欠扭矩上扣可以缓解螺纹粘扣。但是机紧不到位使内外螺纹啮合的齿数少,且各牙齿啮合的深度浅,即内外螺纹之间在径向有很大的间隙。当吊起试样时,内外螺纹会形成偏心,外螺纹接头端面尖角就会与内螺纹相撞,从而在上扣过程中也有可能发生粘扣现象。另外,机紧不到位直接影响油管的密封性和螺纹接头的抗滑脱强度。
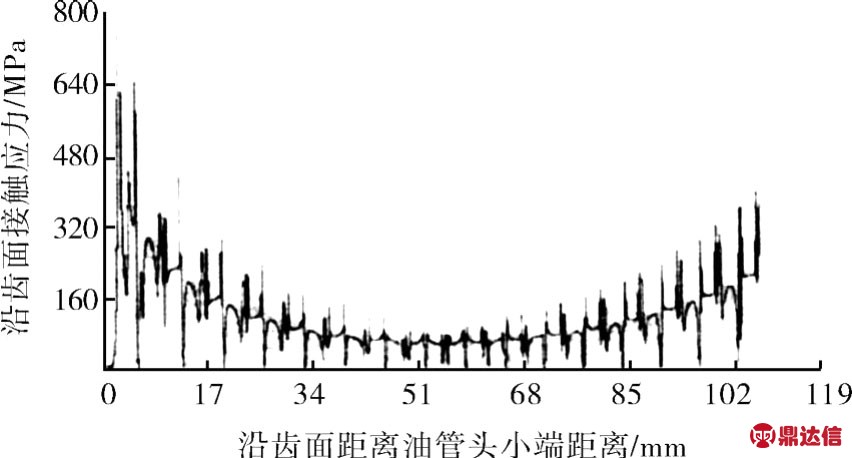
图5 欠扭矩机紧状态仿真结果
3 结语
通过MA TLAB对扭矩的仿真结果可知,机紧圈数直接决定着上卸扣扭矩,当上卸扣圈数超过规定的圈数时,上卸扣扭矩会明显增大。通过ANSYS分析和仿真的结果可知,齿面接触力的最大值总是出现在油管螺纹接头的第1~2有效螺纹啮合处,且随机紧圈数增加,齿面接触力增大。API圆螺纹接头在正常机紧、过扭矩机紧、欠扭矩机紧3种情况下,啮合螺纹两端都存在较大的接触应力,产生较大的塑性变形,一旦发生粘扣首先产生于啮合螺纹两端,特别是倒角面上的起始牙,然后向中间发展。这和油管实际失效情况基本吻合。上扣机紧扭矩低可以减轻粘扣倾向,却使螺纹接头滑脱强度降低,在一定范围内过扭矩机紧可以提高螺纹接头抗滑脱强度,但却存在粘扣加重的倾向。