摘 要:针对纤维复合材料真空辅助成型工艺中模具制造周期较长的问题,提出一种三维打印与真空辅助融合的纤维复合材料成型技术。将数字化设计方法与三维打印技术应用于成型模具的设计制造,极大地缩短了模具的设计制造时间,特别是复杂模具的快速制造。通过流道与模具的一体化设计制造,简化传统真空辅助成型工艺中流道优化布置工序,无需额外配置真空阀及快速接头等部件,节约生产成本。以熔融沉积成型三维打印工艺为例,采用单向连续碳纤维与碳纤维布为增强材料、双组份环氧树脂胶为复合材料基体、聚乳酸为模具材料,对上述方法进行实验验证。结果表明,所提方法可实现复合材料成型模具的快速制造,有效缩短纤维复合材料产品的成型制造周期。
关键词:三维打印;真空辅助成型;复合材料;碳纤维;模具
0 引 言
随着社会经济的迅猛发展和科学技术的不断进步,复合材料在日常生活与国防工业领域中的应用日益增加,结构也越来越复杂[1-2]。而复合材料成型工艺是复合材料得以广泛应用的基础,对复合材料最终性能具有重要影响。目前常见复合材料成型工艺主要包括手糊成型[3]、真空辅助成型[4]、缠绕成型[5]、拉挤成型[6]等,每种工艺都具有各自的优缺点,适用于不同性能与批量的产品制造。真空辅助树脂传递模塑成型工艺因其成本低、污染小、效率高等优点而得到广泛的应用[7]。
模具是真空辅助树脂传递模塑成型过程的必需工艺装备,决定着最终成型产品的结构复杂度及表面质量[8]。而当前众多复合材料成型模具尚处于经验设计阶段,依赖于设计人员所掌握的知识和经验,严重制约了成型模具的设计效率,极大延长了产品的生产准备周期[9]。模具的快速设计制造是提高复合材料成型工艺生产效率的一大关键举措,而数字化设计和快速制造是决定模具制造周期和成本的两大核心技术[10]。探索开发模具快速设计制造与真空辅助融合的复合材料成型工艺对于提高复合材料生产效率具有重要意义。
蓬勃发展的三维打印技术融合数字化设计方法,可实现复杂结构的快速制造,为复合材料构件成型模具的快速设计制造提供了一种可行的技术手段。三维打印技术以CAD数据为基础,采用材料逐层叠加的方法实现实体零件的直接制造[11],在随形冷却注塑模具[12]、构件铸型[13]、射孔模具[14]等方面逐步展开应用。目前较为成熟的用于模具直接制造的三维打印技术主要包括选择性激光烧结、选择性激光融化、电子束选区融化等[15],但上述技术具有投资高、专业性强等特点,不适合高校内大范围的本科生教学实训。
作为低成本、易操作的熔融层积成型技术在复合材料成型模具中的应用鲜有报道,本文探索尝试将熔融层积成型技术运用到复合材料构件成型模具的设计制造,并与真空辅助树脂传递模塑成型工艺结合,开发三维打印与真空辅助融合的复合材料成型实验具有重要的工程应用价值和实践教学意义。
1 工艺流程
三维打印与真空辅助融合的复合材料成型整个工艺流程如图1所示,主要包括基于三维打印的模具设计制造一体化过程和纤维复合材料真空辅助成型过程,前者主要实现模具的快速设计制造;而后者主要实现纤维复合材料构件的成型。

图1 三维打印与真空辅助融合的复合材料成型工艺流程
1.1 设计制造一体化过程
(1)模具设计。采用三维建模软件(如SolidWorks、CATIA、UG)构建成型模具数字化三维模型,更进一步地,可结合复合材料工艺仿真软件(如PAM-RTM)对模具表面或内部的流道进行优化再设计。
(2)模具制造。将设计好的三维模型转化成三维打印设备可识别的控制代码(如G代码),并传输给打印设备,实现模具的快速制造。
1.2 纤维复合材料真空辅助成型过程
(1)材料准备。包括纤维增强体(如碳纤维束/布、玻璃纤维束/布)、树脂胶(如环氧树脂+固化剂);脱模布、脱模剂、导流网、真空膜、真空泵、密封胶带等。
(2)材料铺放。按照一定的顺序将密封胶带、脱模剂、纤维增强体、脱模布、导流网等铺放在模具表面。
(3)封装和抽真空。将真空袋覆盖已铺放的材料表面,形成真空环境并用真空泵检查气密性。
(4)注胶和固化。通过真空泵将树脂液通过模具中的流道导入复合材料构件内部,随后进行固化。
(5)脱模和修整。将前述带有模具的已固化好的复合材料结构件中的模具移除,并进一步修整获得最终所需结构。
2 实验验证
以熔融沉积成型三维打印工艺为例,采用连续碳纤维束与碳纤维布为增强体材料、双组分环氧树脂胶为复合材料基体材料、聚乳酸为模具材料,设计制造碳纤维复合材料壳体进行所提出方案可行性验证。
2.1 芯模一体化设计制造
采用三维设计软件Solidworks设计如图2所示的芯模。芯模直径d1=50.0 mm,厚度t=3.0 mm,高度h=80.0 mm,流道直径d2=4.0 mm。
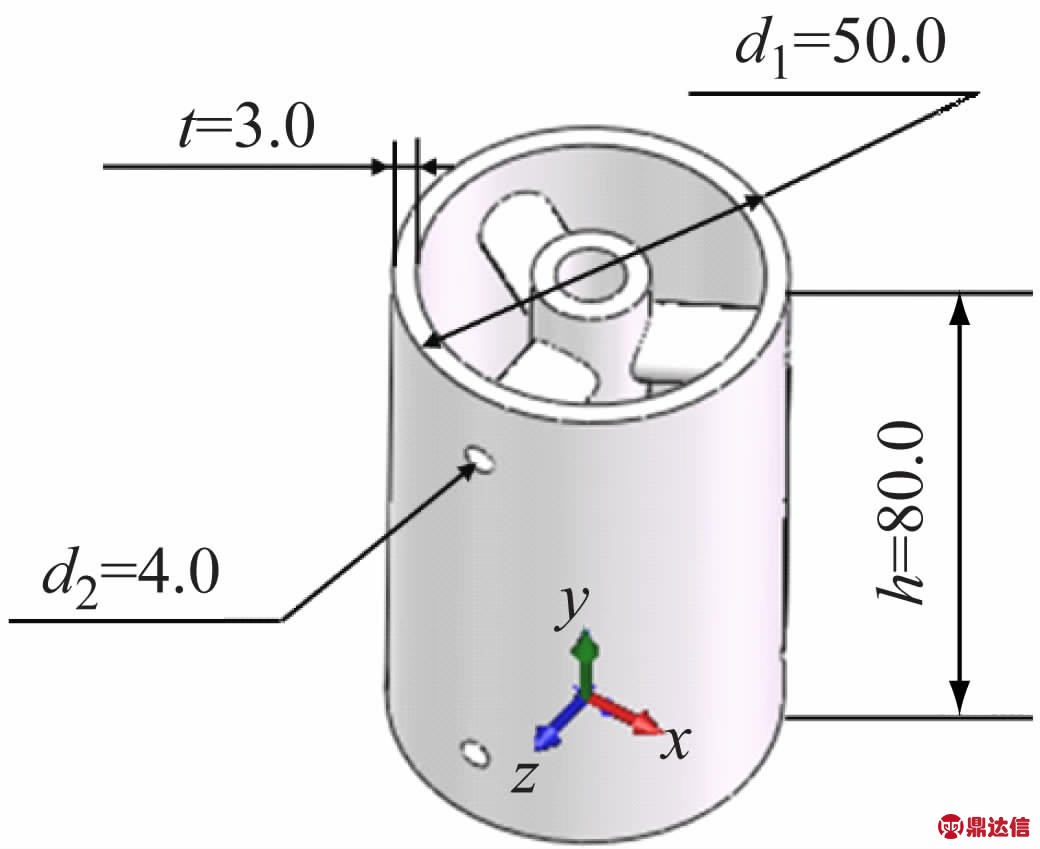
图2 芯模结构数字化设计(mm)
将设计好的芯模导出STL格式文件并采用三维切片软件Cura进行切片生成打印机可识别的G代码,将G代码传输给打印机实现芯模的制造,具体过程如图3所示。
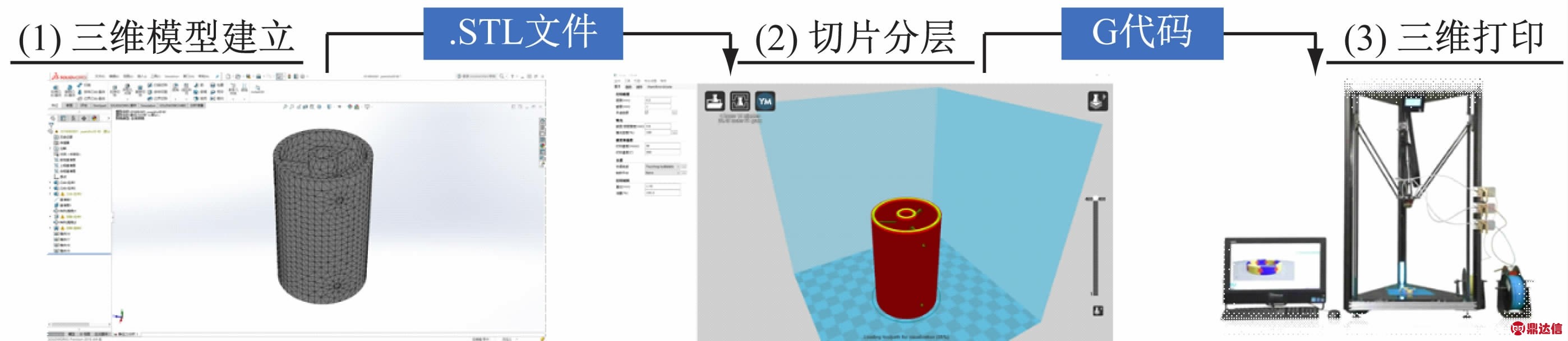
图3 从数字化设计模型到实体三维打印过程
打印工艺参数对结构件力学性能具有重要影响,考虑真空辅助成型对气密性要求,而三维打印层层叠加的特性可能因层间界面黏结不足而导致气密性下降,实验中通过增加结构件壁厚与填充率的方法确保满足真空气密性要求。具体打印工艺参数:壁厚1.0 mm,层高0.2 mm,填充率100%,打印速度50 mm/s,打印温度200℃。采用上述参数制造的芯模见图4。
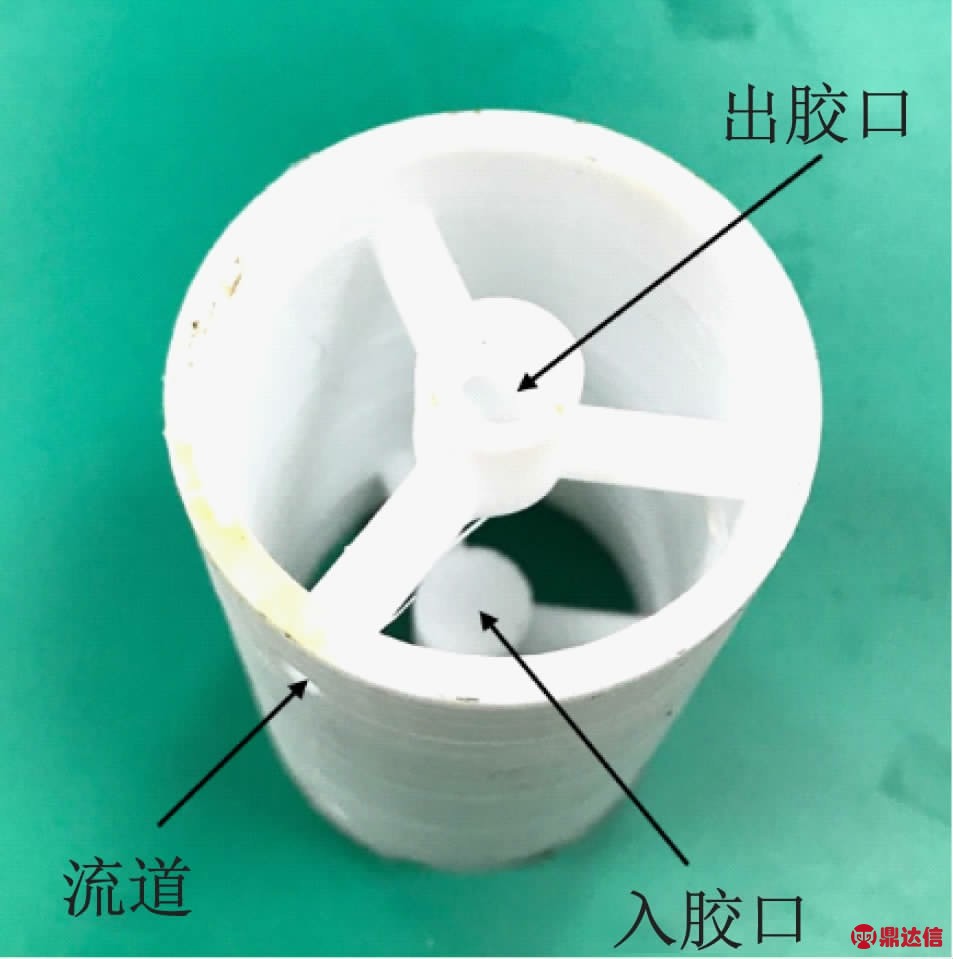
图4 三维打印芯模制造结果
2.2 纤维复合材料真空辅助成型
根据芯模尺寸裁剪合适尺寸的碳纤维布、脱模布、导流网等材料;以环氧树脂与固化剂比例1∶1配置环氧树脂胶;将打印好的芯模表面进行打磨并涂敷凡士林,并将裁剪好的碳纤维布、脱模布、导流网等依次铺放在模具表面,最后包覆真空膜;将塑料软管分别与芯模的入胶口和出胶口连接,其中与出胶口连接的塑料软管另一端与树脂收集器连接,树脂收集器通过另一塑料软管与真空泵连接。采用扳机式快速夹夹紧与芯模入胶口连接的塑料软管的另一端,开启真空泵进行气密性检查。确认密封性完好后取下扳机式快速夹并将塑料软管与环氧树脂胶连接,再次启动真空泵进行注胶直至整个碳纤维布被环氧树脂胶浸润;重新将扳机式快速夹夹紧与入胶口连接的塑料软管以及与出胶口连接的塑料管,进行常温固化。实验装置如图5所示。
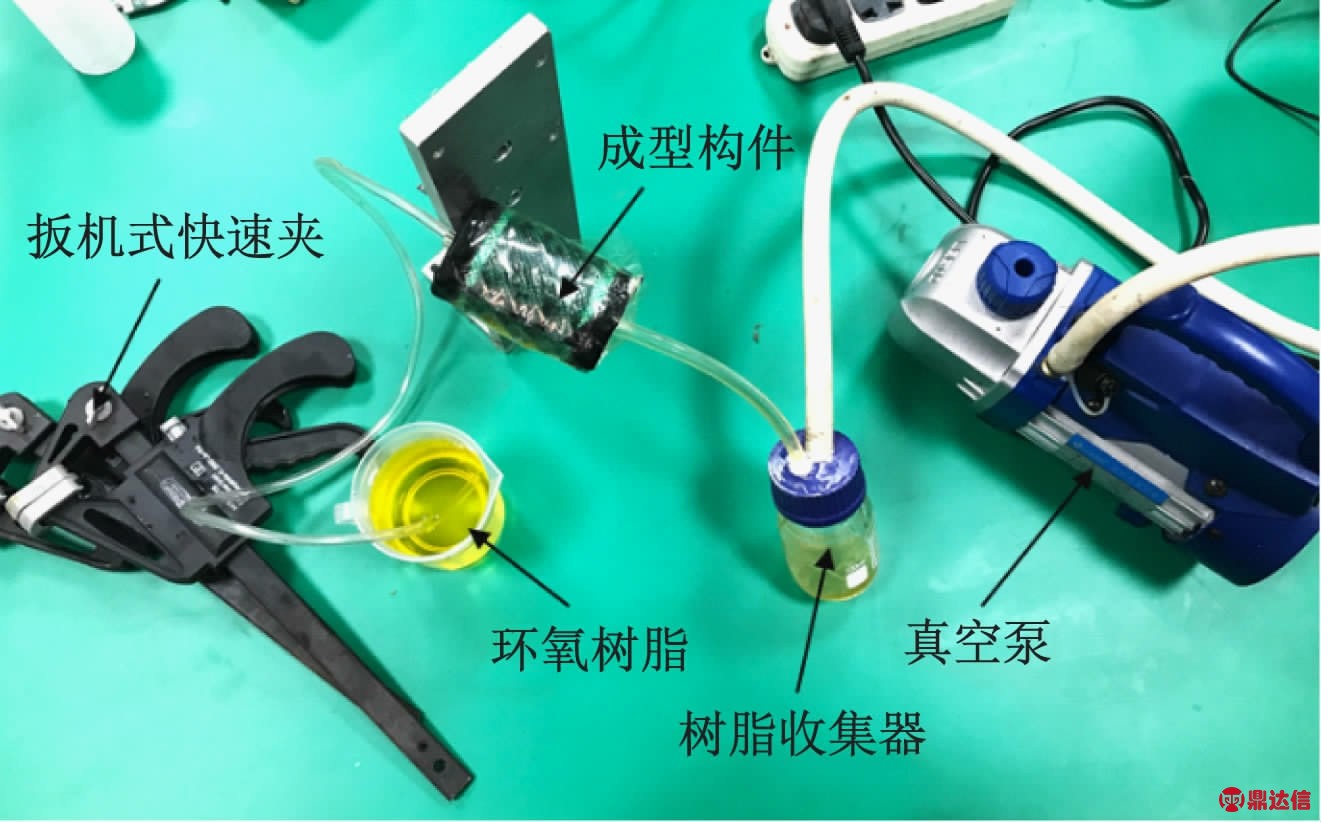
图5 纤维复合材料真空辅助成型系统
将固化好的成型构件芯模去除,获得所需的纤维复合材料结构,如图6所示分别为单向连续碳纤维丝增强结构与碳纤维布增强结构,两种结构均具有良好的成型效果,均可实现良好的浸润,没有出现未浸润区。
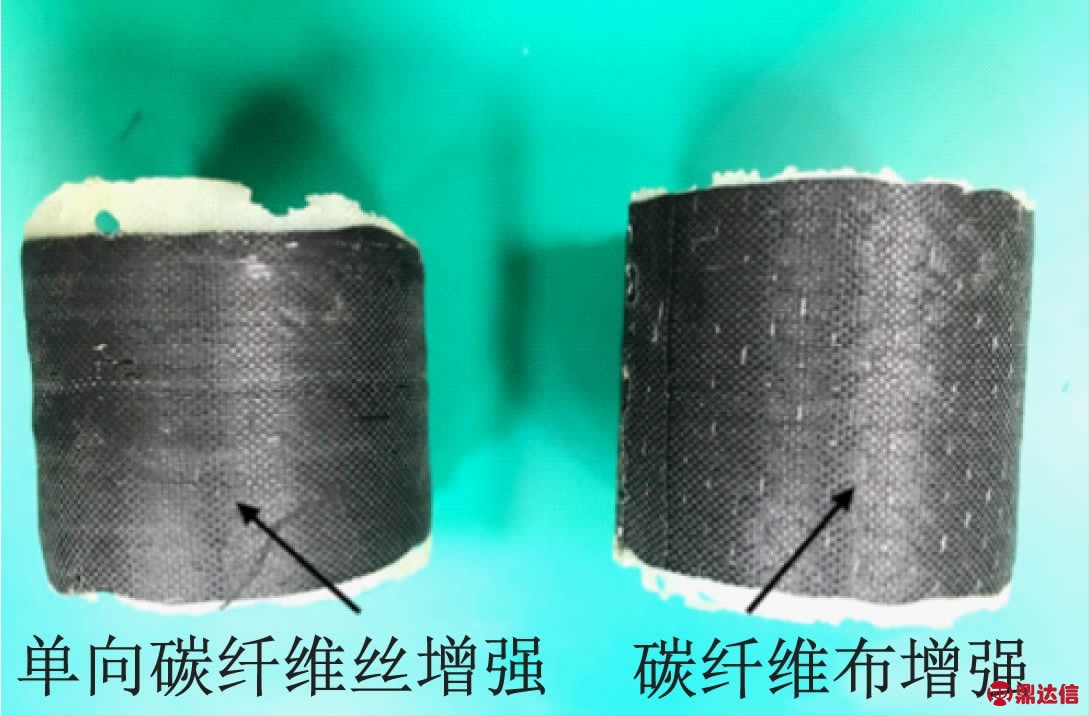
图6 碳纤维增强复合材料结构件
3 结 语
三维打印为复合材料成型模具的高效准备提供了可行思路,采用数字化设计与三维打印增材制造相结合的方法,可显著提高复合材料成型模具的开发效率,缩短模具准备周期,特别是在小批量、个性化复合材料构件制备方面具有突出的优势。提出了三维打印与真空辅助融合的复合材料成型工艺,并以单向连续碳纤维丝与碳纤维布为增强材料、双组分环氧树脂胶为基体进行实验验证,结果表明所提方法具有良好的可行性。未来将尝试把三维打印与真空辅助融合的复合材料成型实验推广至学生实验教学,培养学生创新性思维与工程化能力。