摘 要 海上风机导管架结构在使用期限内容易受到船只的侧向撞击。针对圆柱形导管架构件受到撞击后及碳纤维修复后的轴向承载能力进行了相关的研究,探讨了同一凹痕尺寸下修复方式对圆管构件承载能力的影响以及凹痕尺寸对圆管构件承载能力的影响。设计了3 根未加固柱和6 根CFRP 加固柱开展了轴压试验研究,并与有限元所得破坏模式进行对比。静力试验结果与有限元破坏模式十分接近,这为后续的导管架结构的设计及维护提供了一定的参考意义。
关键词 凹痕尺寸,碳纤维修复,静力试验,有限元
0 引 言
随着海上工程的迅猛发展,海上风电场支撑结构的使用需求渐渐变大,由于导管架结构具有经济性好、建造施工快、整体性强等特点,是目前海上风电场支撑结构的主流形式。
针对钢管在侧向撞击下的变形机理,许多学者对此都有一系列的研究。国内外的研究多集中于钢管双向挤压形成凹痕的研究。其中Gupta等[1]对不同尺寸和不同材料制成的钢管在双向挤压下的变形机理进行了研究;Cho等[2]通过实际试验结合有限元模拟的方法,研究了在低温条件下钢管在双向挤压下的变形机理。
单向挤压变形的研究成果相对于双向挤压来说相对较少。研究成果较完整的有Amdahl[3]以及Wierzbicki 和Suh[4]的 理 论 推 导 及 试 验 研 究。Amdahl[3]针对侧向平面载荷作用下的钢管构件研究其变形机理;Wierzbicki 和Suh[4]则对侧向线载荷作用下的钢管构件研究其变形机理。Pacheco和Durkin[5]与Maalim 等[6]分别使用了不同的方法制造钢管凹痕,其中Pacheco 和Durkin[5]在试验中使用了尖锐的刀片模拟了线载荷对钢管进行的制造凹痕的过程,试验所得凹痕与Wierzbicki 和Suh[4]所推导得出变形机理吻合。邵炎林和何炎平[7]在Pacheco 和Durkin[5]的凹痕试验基础上,对其进行了有限元模拟,模拟结果也与试验所得结果近似吻合。此外,在线荷载作用下钢管凹痕两侧为三维曲面,这增加了有限元建模的困难,邵炎林和何炎平[7]也对凹痕区域进行了理想化建模研究,这种简化建模所得到的极限受压强度与实际结果相近。
CFRP 加固技术始于20 世纪80 年代,目前为止,许多学者都对CFRP 加固有一定的研究。Ghazijahani 等[8]研究了轴向压力作用下CFRP 结合内部支撑木条的加固空心圆钢管的破坏模式及其承载能力提高情况。Huang 等[9]研究了CFRP以及灌浆加固下的有环向壁损缺陷的空心圆钢管在轴向压力作用下的破坏模式及其承载能力提高情况。两位学者的试验结果都表明了CFRP 能有效提高受损构件的轴向承载能力。CFRP 加固成型工艺众多,常见的有手糊成型、真空袋压成型、模压成型、RTM 成型、热压罐成型等工艺,伍文艳等[10]针对其中的手糊、真空袋压、模压三种加固工艺下的构件进行了相关的力学性能规律研究,得出了加固成型工艺对于CFRP 加固效果具有显著的影响的结论,且一般来说,在拉伸强度、拉伸模量、弯曲强度、弯曲模量上,模压高于真空袋压高于手糊。
本文对试验结果数据进行处理,得到荷载-位移曲线以及荷载-应变曲线。通过荷载-位移曲线来比较CFRP 的不同修复方式对钢管轴向承载能力的影响,通过荷载-应变曲线来比较钢管、CFRP不同区域在轴向加载不同阶段的局部变形,从而分析加载不同阶段CFRP 与钢管的协同变形作用并和有限元结果进行分析比较。
1 试验概况
1.1 试件设计与试验分组
钢管试件设计尺寸参考了学者邵炎林和何炎平[7]文献中尺寸。试件分为9 根钢管短柱,包括3根未补强钢管以及6 根CFRP 补强钢管。试验变量包括凹痕深度hd和不同的CFRP 加固方式,凹痕深度的选取参考了前人的研究[5],具体的试件分组见表1。试件的尺寸如图1所示。

图1 钢管尺寸(单位:mm)
Fig.1 Steel tube sizes(Unit:mm)
表1 试件主要参数
Table 1 Main parameters of specimens
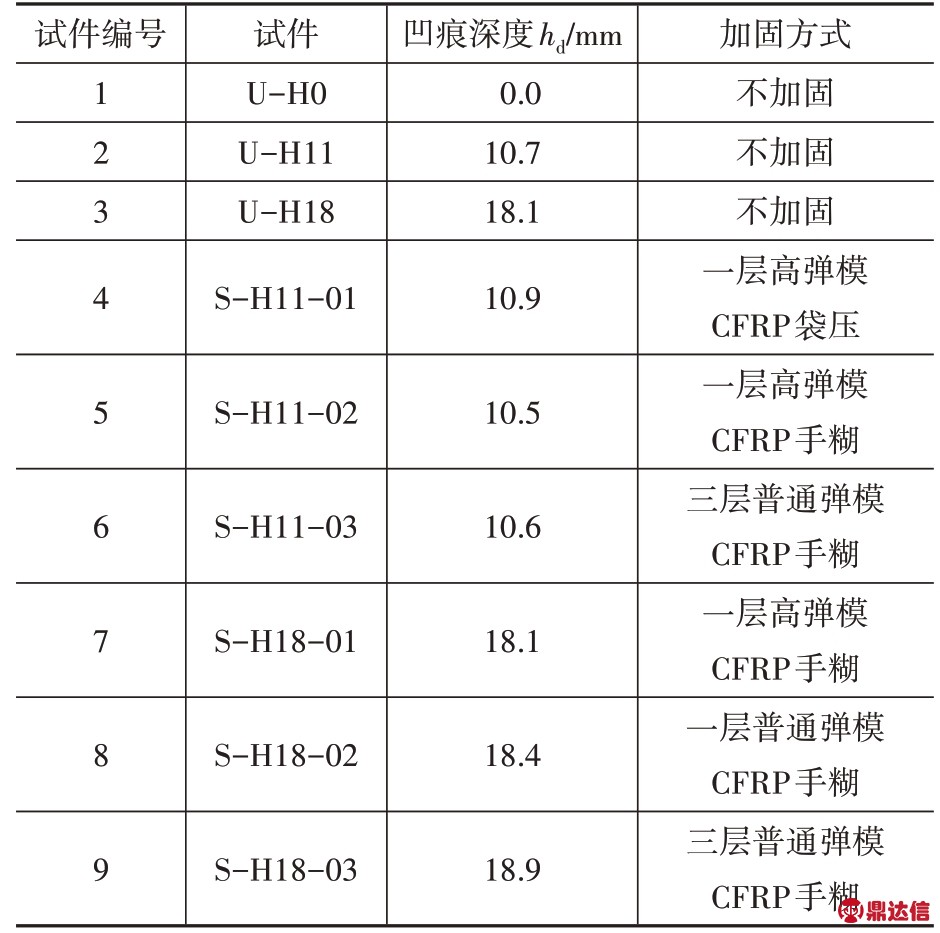
1.2 材料属性
试验中材料的材性如表2 所示。钢材材性通过在试验用钢材上切割4 根材性试件后根据《金属材料室内拉伸试验方法》(GB/T 228—2010)进行静力拉伸试验得到[11]。据生产厂家提供的数据资料,普通弹模CFRP 的杨氏模量为230 GPa,拉伸强度为3 400 MPa,每层厚度为0.167 mm;高弹模CFRP 的杨氏模量为681.3 GPa,拉伸强度为1 967 MPa,每层厚度为0.143 mm,两者的泊松比均为0.3。试验采用了Araldite420 胶水作为黏结剂,相关材性数据由生产厂家所提供。
表2 材料属性
Table 2 Material properties
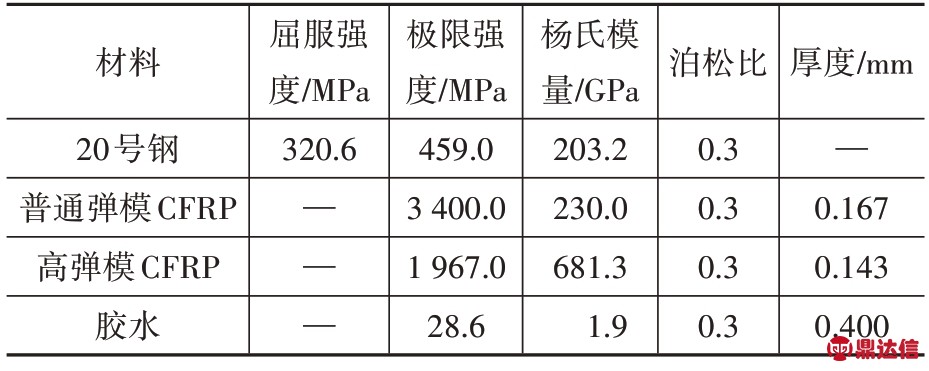
1.3 真空袋压工艺介绍
真空袋压的目的是均匀施压、赶出气泡。本次试验中4 号试件采用了真空袋压工艺。首先需要按加固区域的大小剪制4 种真空辅材,如图2所示。
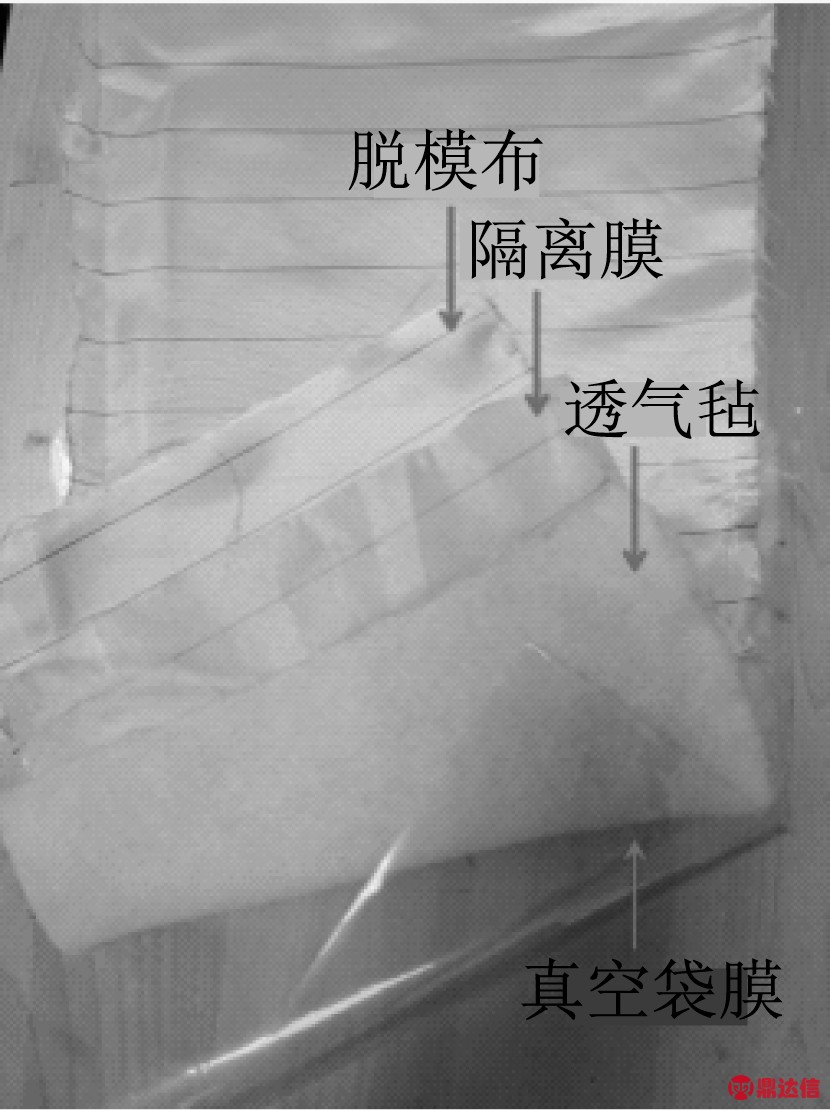
图2 真空辅材
Fig.2 Vacuum auxiliary material
之后将真空辅材(脱模布、隔离膜、透气毡、真空袋膜)由内而外按顺序黏贴,在真空袋膜上穿一个恰能通过真空阀的小孔并安装真空阀,之后通过接头与树脂管将真空泵与真空阀连接,启动真空泵,直至透气毡表面吸出胶水,如图3所示。
1.4 试件加载前的准备流程
CFRP 修复的钢管试件制作流程包含以下几个步骤:①用车削等精加工方式制作符合试验要求尺寸的圆形钢管和辅助制造凹痕的钝头以及钢板支座。②将钢管放置在特制支座中,将特制钝头固定在静力装置上以2 mm/min 的速率下降对钢管施加凹痕,之后用游标卡尺测量凹痕深度。③施加凹痕后的钢管,用原子灰涂抹凹痕区域使其表面平整。④把用胶水浸润过的CFRP 布缠绕在钢管的凹痕受损区域,CFRP 环向缠绕于钢管凹痕区域中心,轴向长度为200 mm。本次黏贴CFRP 时用到了真空袋压和手糊两种工艺。具体的准备流程如图4所示。
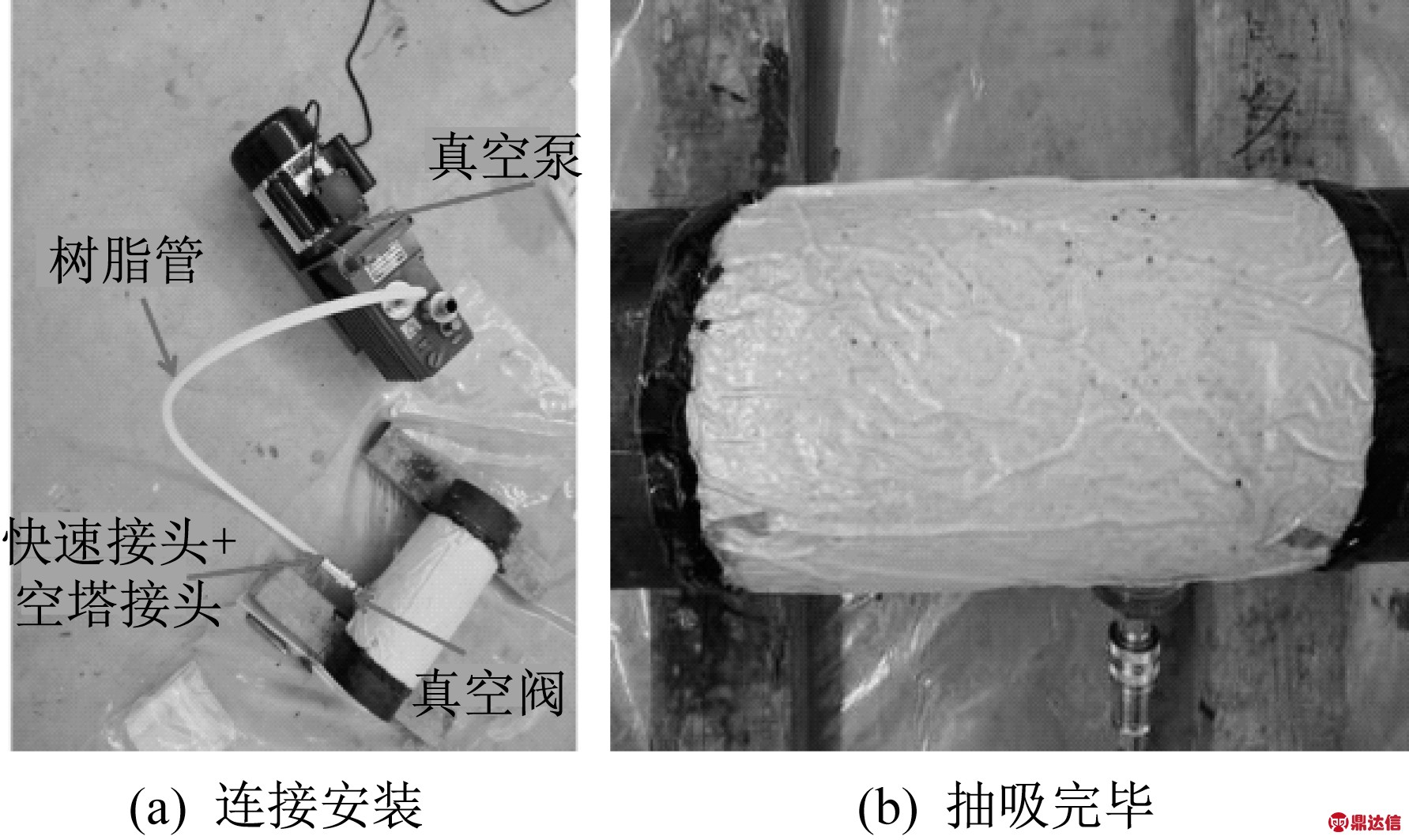
图3 真空袋压工艺
Fig.3 Vacuum bag pressing process
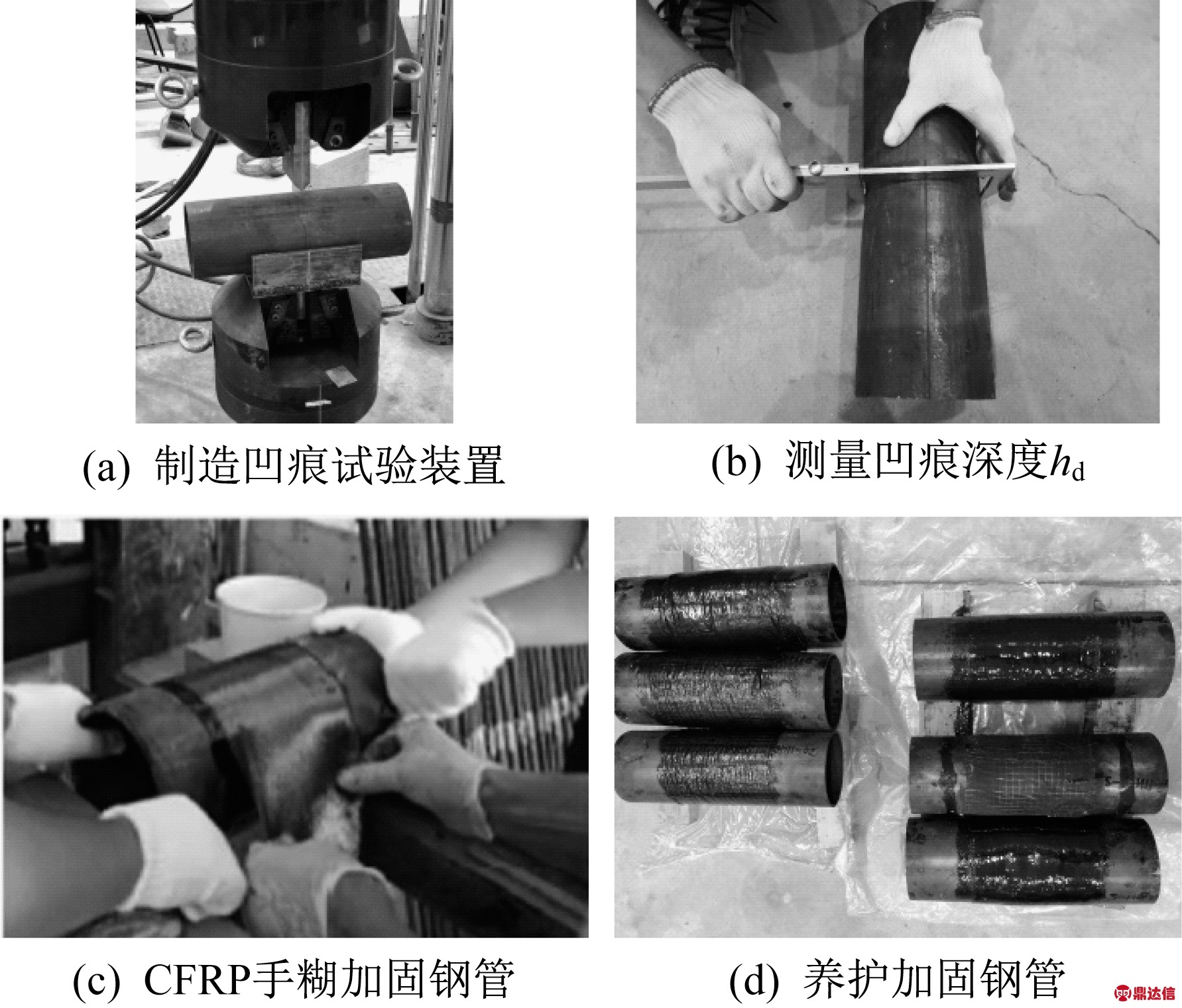
图4 试件准备流程
Fig.4 Preparation of specimens
1.5 试验装置和试验流程
钢管试件修复完成后,在同济大学工程结构性能演化与控制试验室进行了轴向压缩试验。对6 个补强试件、2 个未补强试件以及1 个无损伤试件先后进行了轴压加载,加载试验装置为3 000 kN高刚度液压试验机,如图5所示。
应变片的布置如图6所示。其中,不加固的圆管试件仅在内壁中间高度处布置2 个轴向应变片D_I_V、I_V,CFRP 补强钢管试件在内壁中间高度处布置2个轴向应变片,在CFRP外侧中间高度处隔120°布置3个轴向应变片和3个环向应变片。
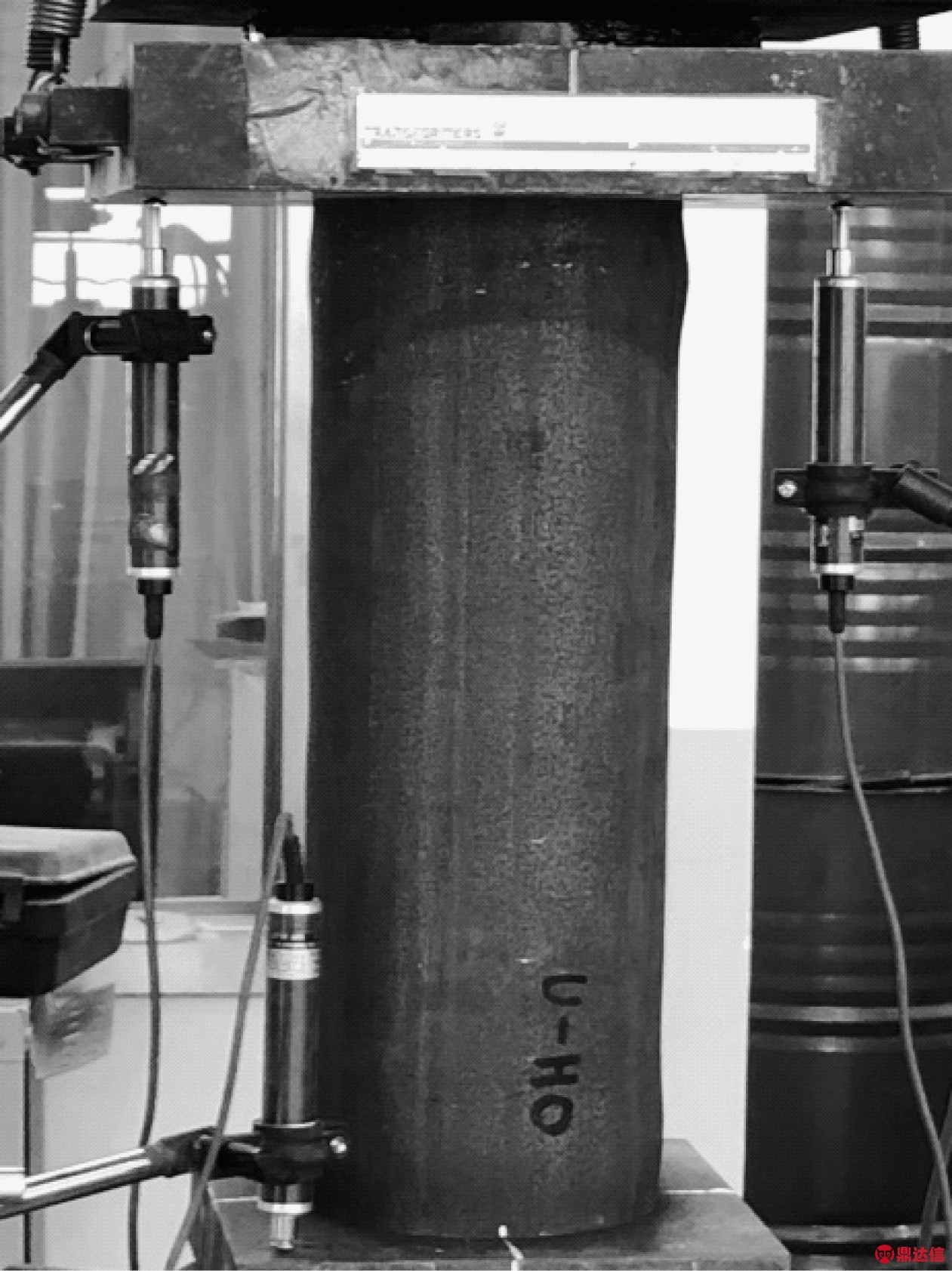
图5 试验加载装置
Fig.5 Test set-up
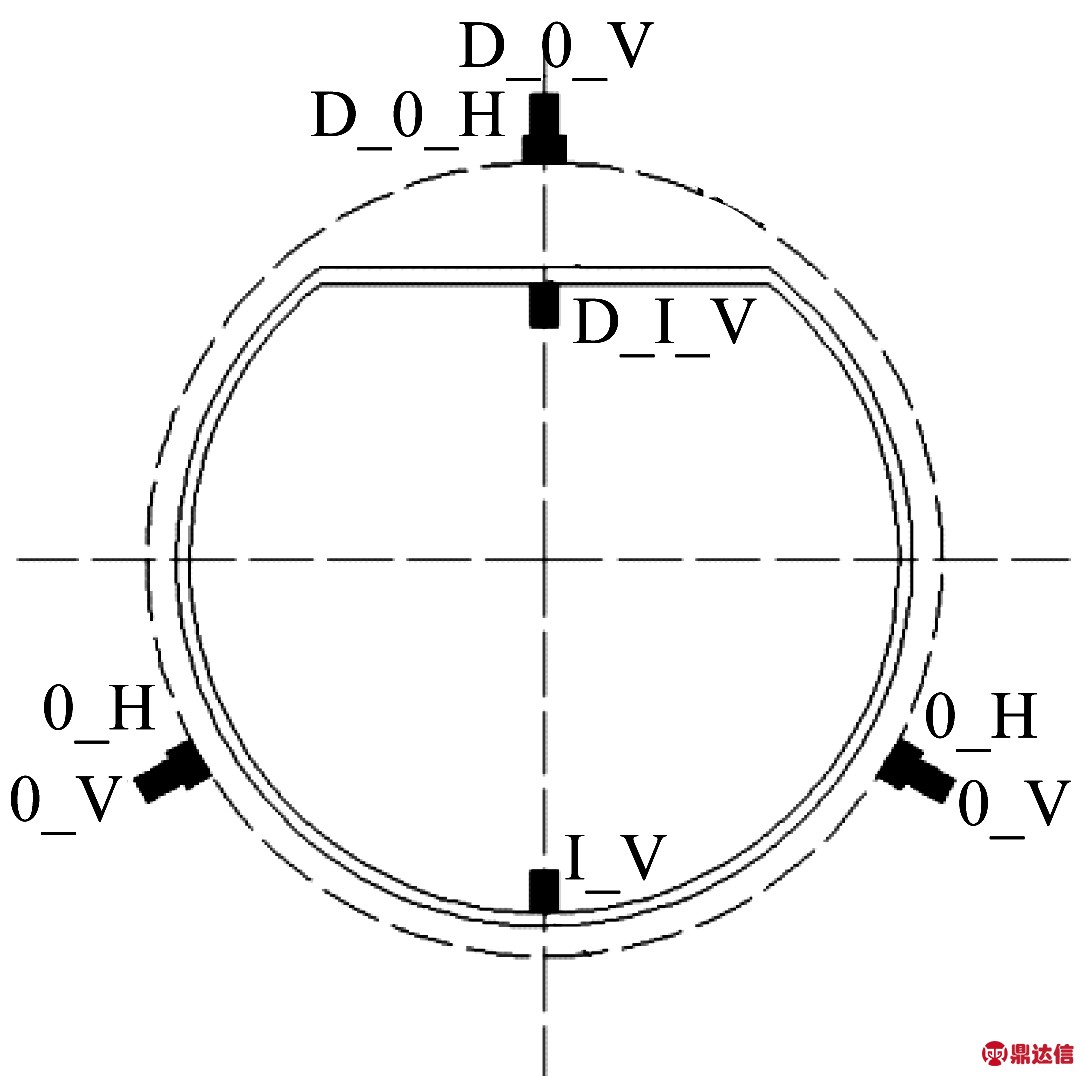
图6 应变片布置
Fig.6 Strain gauge layout
此外,使用3 个测量范围为25 mm 的线性位移可变传感器(LVDT)来对每个试件整个高度区域范围内的轴向位移进行测量,其中2 个位移传感器顶住上部加压板,1 个位移传感器顶住下部板,如图5所示。
正式加载时,所有试件均以0.4 mm/min 的速度进行加载,采用这种缓慢的加载速率,可以完整地观察试件的局部屈曲过程。
2 有限元模型
通过ABAQUS 6.14-4有限元软件模拟钢管的轴向加载试验。其中未补强钢管试件定义了刚体钝头并完整地模拟了制造凹痕后进行轴向加压的过程,补强试件则采用了邵炎林和何炎平[7]提出的对凹坑区域的几何尺寸理想化的方法进行建模后轴向加压的方法来进行研究。有限元模型中,钢管和CFRP 采用S4R 单元,原子灰采用C3D8R单元,制造凹痕的刚体钝头采用R3D4 单元,其中CFRP 层采用复合层的方式定义为CFRP-胶水复合层。根据表2 中试验材料的材性数据,各修复材料定义了弹性,钢管根据材性试验数据定义了非线性。钢管、原子灰、CFRP复合层之间采用Tie的方式连接。
未补强试件中,模拟凹痕的制造过程时,定义了接触的法向行为与切向行为来有效地模拟钝头尖端与钢管的接触。通过刚体约束控制钝头参考点的位移来控制钝头下降来制造凹痕。
试件加载时的边界条件中,除了加载端的轴向位移,试件两端的各个自由度均受到约束。加载端横截面的中心参考点通过耦合约束整个截面,同时控制该中心参考点的位移进行轴向位移加载。
3 试验结果及分析
3.1 破坏模式
第一组试件是未补强的三个试件,破坏模式如图7 所示,并与有限元模拟的破坏图进行了对比。无凹痕的对照试件U-H0 呈现了一个经典的破坏模式,与之前学者们做的试验结果表现出了良好的一致性[12],在靠近试件纵向两端的部位出现了向外的局部屈曲,其中凸出的局部屈曲部分被称为象脚。试件U-H11、U-H18 则均表现出了凹痕损伤区域随着加载的进行,凹痕处的深度逐渐增大的现象,并且试件随着加载的进行出现了整体屈曲。
第二组是有凹痕缺陷的各补强试件,破坏模式如图8 所示。在第二组试验中,当加载进行到一定程度时,单层高弹模CFRP 加固的各试件均发出了清脆的响声,且最后均发生了高弹模CFRP 的撕裂现象,而普通弹模CFRP 加固试件加载时无明显声音且最后也无撕裂现象。声音是由于高弹模CFRP 的部分塑料丝发生了崩裂引起的,且CFRP 层在加载时受到环向的拉伸应力,由于高弹模CFRP 的极限强度小于普通弹模CFRP的极限强度,因此前者撕裂而后者未撕裂。此外,单层CFRP 手糊加固试件发生了CFRP 搭接处的脱落,而真空袋压加固试件则并无此现象发生,这是由于真空袋压加固后可以使得CFRP 层与层之间的黏结变得更加可靠。这些补强试件与未补强试件的失效模式相似,均发生了向凹痕侧弯曲的整体屈曲现象。
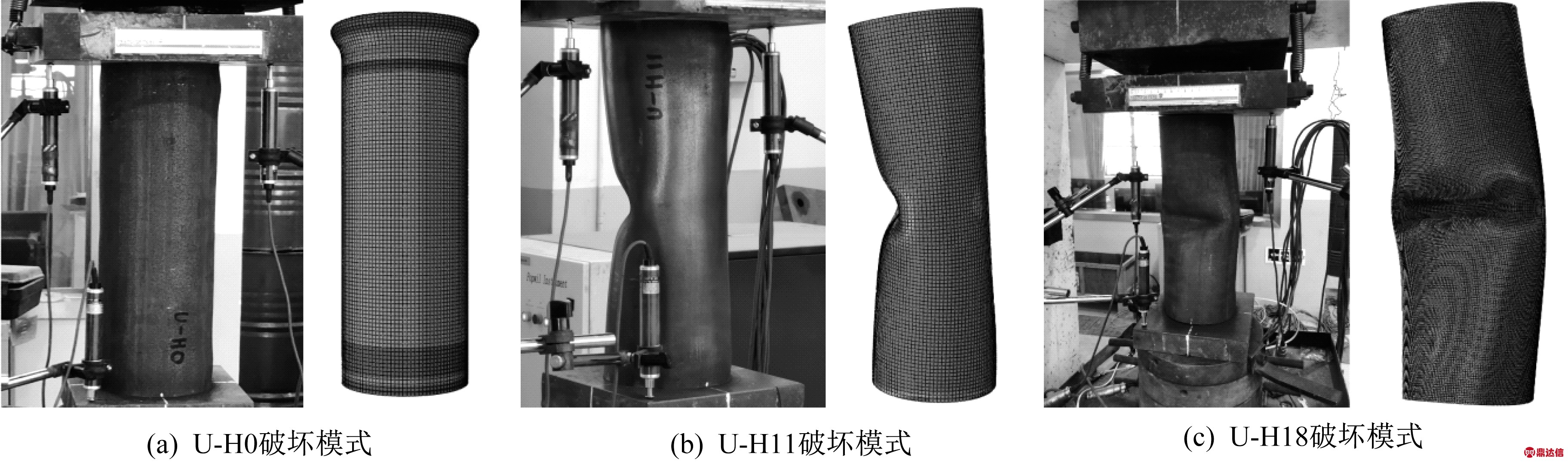
图7 未补强试件典型破坏模式
Fig.7 Typical failure modes observed for unpaired specimens
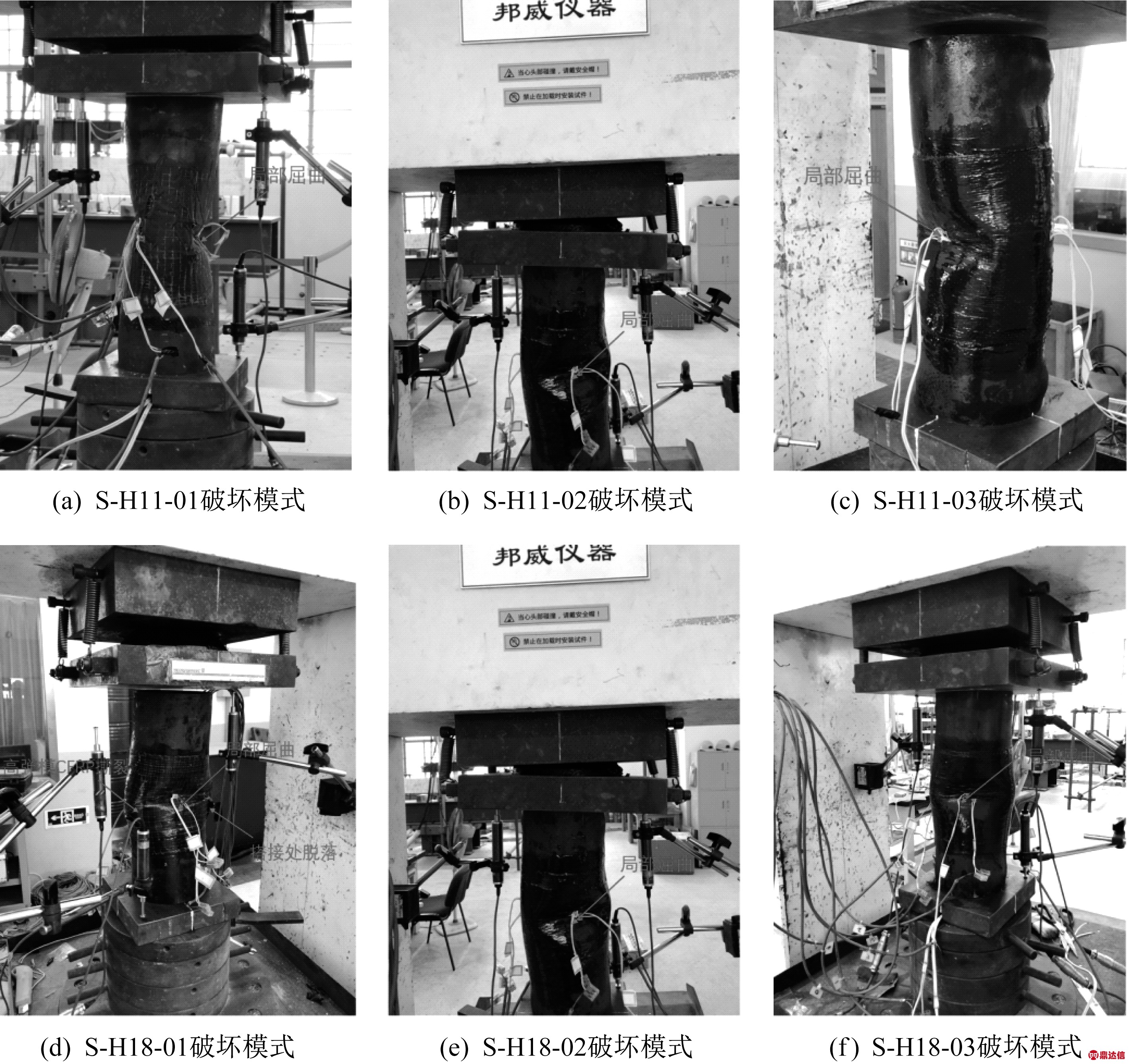
图8 补强试件典型破坏模式
Fig.8 Typical failure modes observed for repaired specimens
3.2 荷载-位移曲线
根据试验的设计参数,试件分为3 组进行讨论,每个试件都能与表1 中一一对应。每个组的荷载-位移曲线如图9 所示,展现了不同试件在轴压性能上的比较。位移由底板LVDT 示数减去顶板两个LVDT的平均示数得到。
从各钢管的荷载-位移曲线上,很容易观察到,直到屈服荷载之前,荷载是线性上升的,达到有限塑性平台后,荷载呈现出非线性上升。比较不同试件可以发现,随着凹痕深度的增大,极限位移减小,同时极限承载力也减小,如图9(a)所示。相比手糊加固试件S-H11-02,真空袋压加固试件S-H11-01 可以很明显地提高极限位移,分别对应5.37 mm 和14.09 mm 的极限位移,如图9(b)所示。同时发现,相比未修复的钢管试件,单层高弹模CFRP 修复的试件极限承载力均略有降低,但普通弹模CFRP 修复的试件极限承载力均有所提高,且随着普通弹模CFRP 的层数增加而提高得更多,如图9(b)和图9(c)所示。

图9 荷载-位移曲线对比
Fig.9 The comparison of the load-displacement curves
可以从各荷载-位移曲线图中发现,普通弹模CFRP 相比起高弹模CFRP 更能提高试件的极限承载力,且层数增加提高效果更好。真空袋压加固比起手糊加固能显著提高试件的极限位移。
3.3 荷载-应变曲线
各应变片的标号如图6 所示。在处理应变数据时,将补强试件未受损区外壁的两个轴向应变O_V 和两个环向应变O_H 都采用平均值作为代表值。图10 分别显示了无损伤、未补强、补强试件的荷载-应变曲线。
对于无损伤试件U-H0来说,两个应变片的数值随荷载的上升几乎相同表明试件处于轴心受压状态。
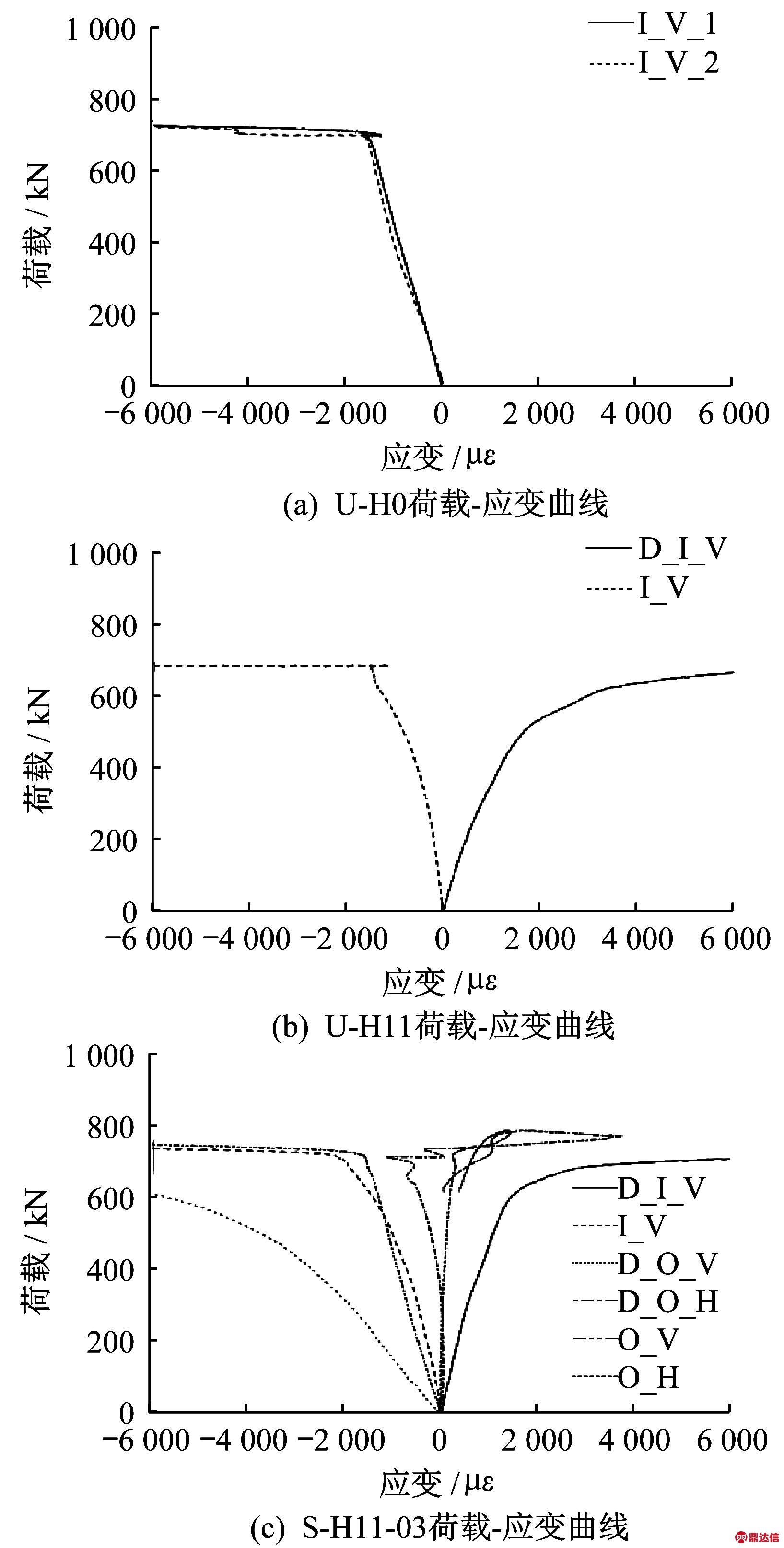
图10 无缺陷、未补强、补强试件的荷载-应变曲线
Fig.10 Load-strain curves of undamaged,unrepaired and repaired specimens
对于未补强试件U-H11 来说,凹痕区内壁纵向应变片(D_I_V)受拉,凹痕区正对180°方向的内壁应变片(I_V)受压,对应了圆管在加载过程中发生的向凹痕区所在侧的整体弯曲,且这种弯曲并不是突然发生的,从加载初期程度逐渐加大。
对于补强试件S-H11-03 来说,可以发现这种整体弯曲现象依然发生。凹痕区外部环向应变片(D_O_H)在加载初期的应变较小可以忽略不计,但随着加载的进行,可以看到当接近极限荷载时,D_O_H 突然出现了很大的拉应变,这主要是由于在这时,钢管凹痕区发生了一个突然的向内局部屈曲,而CFRP 为了抑制这样的屈曲起到了一定的环箍作用所致。而无损伤区的外部环向应变片(O_H)在加载过程中始终受拉,这是由于CFRP抑制着圆管的整体弯曲发生所致。
如图11 所示,比较18 mm 凹痕深度下的各试件D_I_V(凹痕区内壁处轴向)的应变数值,相比未修复试件U-H18,单层高弹模CFRP加固会使得该处拉应变增大,而普通弹模CFRP 会抑制该处的拉应变增大,且该抑制效果由单层变为三层时,抑制更为明显,这与最后的轴向承载能力修复结果有了很好的对应。
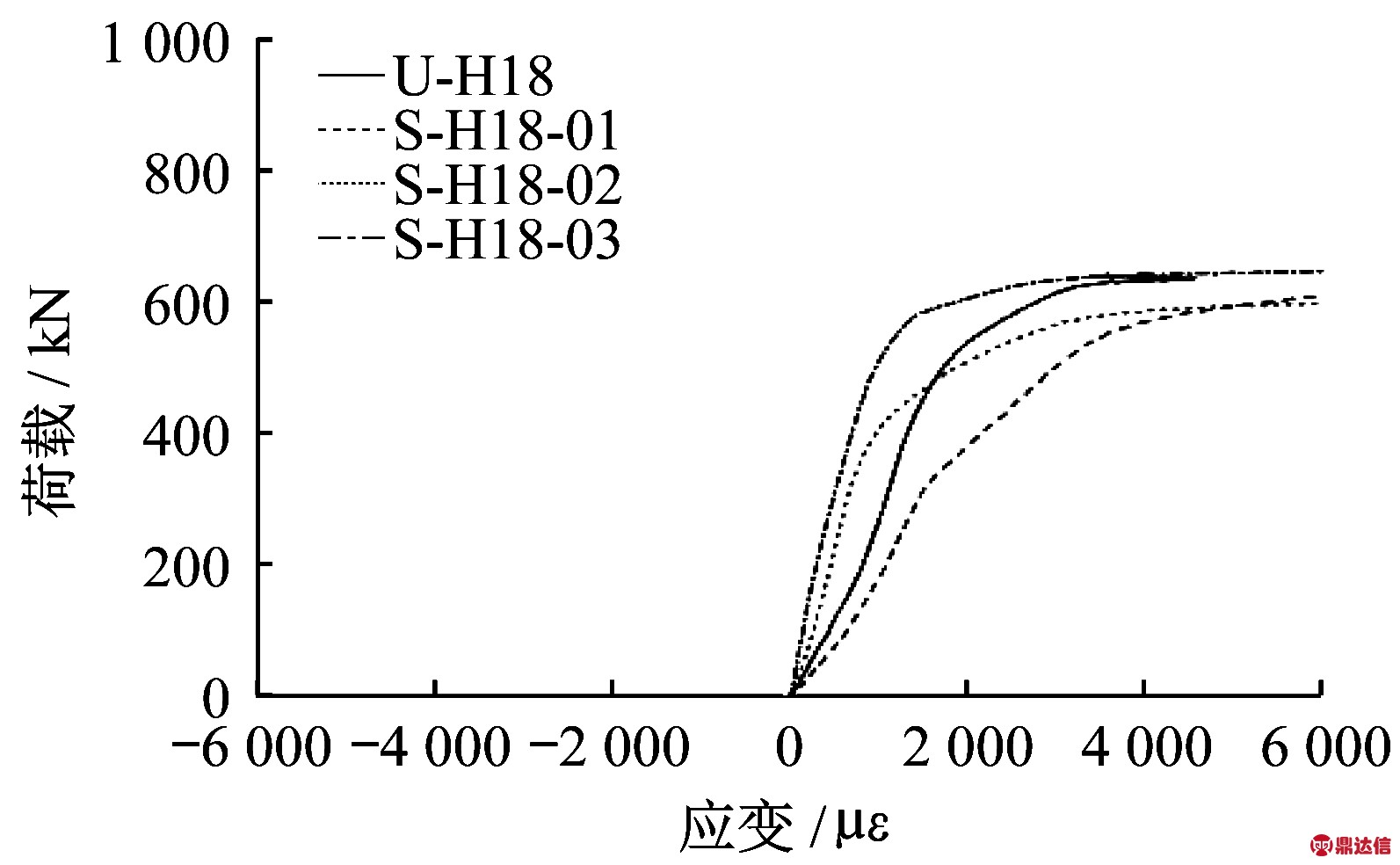
图11 D_I_V处的荷载-应变曲线比较
Fig.11 Comparison of load-strain curves at D_I_V
4 影响轴向承载力参数分析
各试件的轴向承载力及极限位移如表3所示。
表3 试件结果统计表
Table 3 Results of specimens
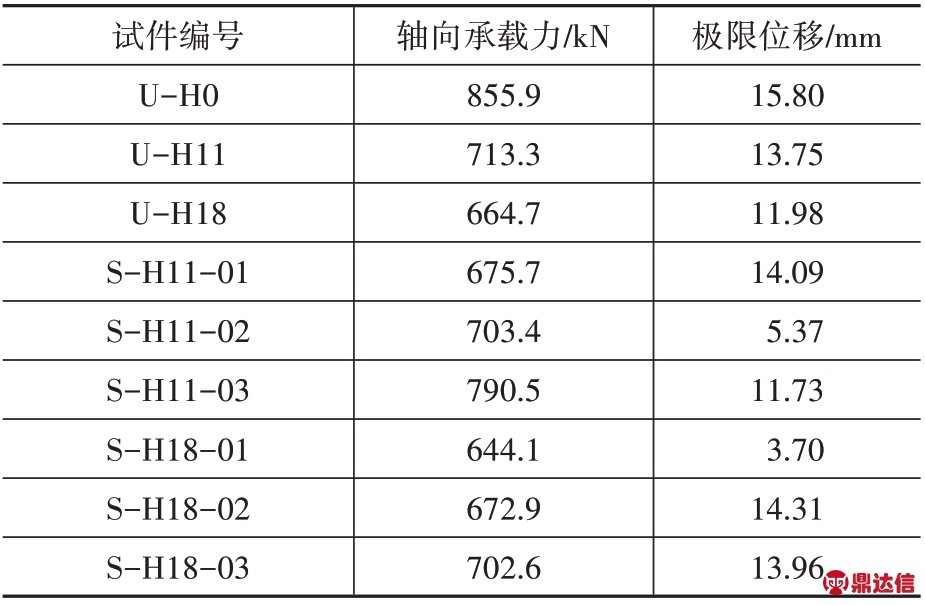
4.1 凹痕深度hd的影响
由未补强试件U-H0、U-H11、U-H18 的荷载-位移曲线可知,凹痕深度越大,试件的轴向承载能力越低,且峰值承载力对应的位移也越低,塑性平台阶段不明显且流幅越小,进入塑性后承载力的提高幅度也越小,并且进入塑性时对应的位移和承载力也越低。对照U-H0试件,试件U-H11的极限承载力降低了16.7%,对应的位移减小了13%;U-H18 的极限承载力降低了22.3%,对应的位移减小了24.2%。综上所述,随着试件的凹痕深度加大,试件的受压性能发生了不同程度的退化。
4.2 修复方式的影响
由11 mm 凹痕深度下的各试件的荷载-位移曲线对比,如图9(b)所示,S-H11-01、S-H11-02 与U-H11相比,极限承载力略有降低,可以认为是一层高弹模CFRP 加固的效果不明显,试件的极限承载力差异主要由安装误差以及材料的离散性决定。对比S-H11-01 和S-H11-02,可发现试件的峰值承载力对应的位移大大提高了,这种现象与真空袋压加固可以加强胶水的黏结程度,使得在加载过程中保证CFRP 与钢管间不发生脱落有关。对比S-H11-03 与U-H11,极限轴向承载力获得了一定程度的提升,极限轴向承载力由713.3 kN 提高到了790.5 kN,约提高了11%。
18 mm 凹痕深度下的各试件,S-H18-01 与UH18相比,轴向承载力略有降低。试件S-H18-02、S-H18-03与U-H18相比,承载力均略有上升,其中试件S-H18-03相比U-H18轴向承载力由664.7 kN提高到了702.6 kN,约提高了5.7%。
5 结 论
在这项试验研究中,用不同弹性模量的碳纤维布以及不同的工艺对凹痕钢管进行加固,以评估加固对局部损伤和柱承载力的影响。同时,比较了不同凹痕深度下的钢管极限承载力。本研究得出以下结论:
(1)凹痕深度越大,钢管的轴向承载力越低,受压性能越差。
(2)普通弹模CFRP 加固可以提高凹痕钢管的轴向承载力,且其提高程度随层数增加而上升,随钢管凹痕深度增大而有一定的减小。
(3)单层高弹模CFRP 加固对于钢管的轴向承载力几乎无提高。
(4)对于凹痕钢管构件,真空袋压加固相比于手糊加固,并没有明显地提高承载力,但能一定程度上增强构件的延性。
(5)由于高弹模CFRP 极限强度小于普通弹模CFRP,在钢管向凹痕侧屈曲时会发生撕裂从而提前退出工作,无法对钢管产生有效的环箍约束,因此高弹模CFRP 加固效果没有普通弹模CFRP效果好。