摘要:芳烃中的苯、甲苯、二甲苯是石化行业很重要的基本有机原料,煤基甲醇制芳烃工艺极受关注。基于循环流化床甲醇制芳烃技术,对其分离工艺建立了全流程模拟模型。对甲烷吸收塔吸收剂用量进行灵敏度分析,优化后的吸收剂用量减少了27.7%。对流程中的换热网络进行热集成,使得冷、热公用工程消耗量分别减少了16.75%和11.89%,达到了提高能量回收、降低能耗的目的。
关键词:芳烃;模拟分析;换热网络
芳烃中的苯、甲苯、二甲苯在工业上有重要的应用价值,是石化行业很重要的基本有机原料,可用来生产合成橡胶、合成树脂及多种精细化工产品,且可以作为高辛烷值汽油的调和成分。因此近年来,世界各国对芳烃的需求量越来越高。工业上,BTX芳烃主要来自于催化重整油和裂解汽油,但我国原油资源短缺,2014年我国原油表观消费量5.18亿吨,对外依存度接近60%,预计2020年,我国原油对外依存度将达到69%[1]。因此,以煤合成的甲醇为原料,开发基本有机化工原料的新生产工艺路线,是当下亟待发展的方向,也是实现煤化工向石油化工延伸的有效途径[2]。
Garwood等[3]研究出了一种通过煤气化合成含碳氧化物、氢气和甲烷气体并进一步转化成高辛烷值汽油的整合工艺。Quignard等[4]发现将煤和其他原料共处理,便可获得芳烃族化合物。Hershkowitz等[5]提供了一种高度不饱和脂肪族原料和甲醇共同合成芳香族化合物的方法。Imai等[6]给出了利用芳香族化合物与烷基化剂在烷基化条件下合成苯的同系物的方法。Berger[7]给出了流化床条件下煤制挥发性烃(包括芳族化合物和烯烃)的可能方法。
我国在煤基甲醇制芳烃工艺方面也有很多相关研究。其中,华电榆横作为全球首个煤制芳烃项目已完成工业化试验[8],采用的是清华大学循环流化床甲醇制芳烃专利技术。黄格省等[9]分析了我国煤制芳烃技术的现状,提出应重视煤制芳烃的技术攻关,以达到降低成本、清洁高效的目的。葛志颖等[10]指出放大试验所达到的效果往往不如小型试验结果。目前研究主要停留在理论层面上,离真正实现工业化还有一定距离,煤基甲醇制芳烃工艺还处在工业化初期,因此仍需要确定更优的操作参数并对流程进一步优化。
本文基于循环流化床甲醇制芳烃技术,对其分离工艺采用Aspen HYSYS软件建立模型进行全流程模拟,并考虑改进流程以达到降低能耗的目的。
1 分离工艺模拟模型及模拟结果
1.1 分离工艺简介
由于甲醇芳构化反应是强放热过程,副反应很多,因此其反应产物比较复杂。参考清华大学的相关专利[11],并结合本文分离工艺的目标是H2/CO、CH4、低碳烃类(作为液化石油气,简称LPG)、苯和甲苯、C9+芳烃(C9及以上芳烃)均作为副产物排出系统,混合C8芳烃(主要为对二甲苯、邻二甲苯和间二甲苯,并含有少量乙苯)作为产品采出,建立分离工艺流程图如图1所示,其中,E101、E102、E103和E105为换
热器;C105为三相分离器,Q501为热负荷;C107、C108、C108´、C109和 C110为分离塔设备。
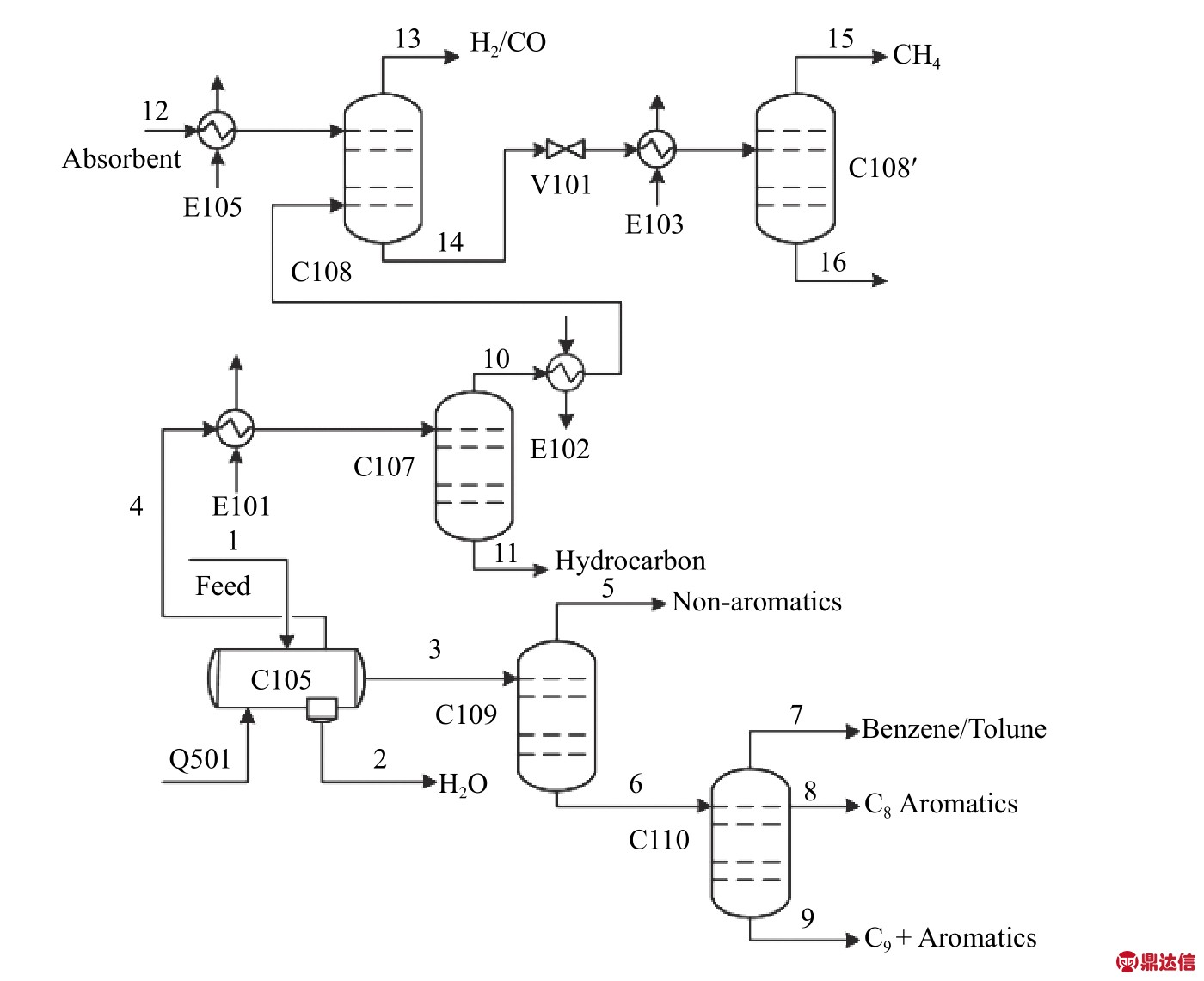
图1 分离工艺简易流程图
Fig.1 Simplified flow diagram of the separation process
1.1.1 三相分离器 从甲醇芳构化反应单元出来的高温气体(含芳烃、干气、液化气和水)回收部分热量后,经冷却冷凝进入三相分离器进一步分离。本文的研究不考虑反应器,直接从分离工艺开始模拟分析。假设从反应单元出来的高温气体(流股1)被冷却至常温再输入三相分离器C105。
采用卧式三相分离器,原料气混合物进入三相分离器进行基本相分离后,气体(流股4)从气口流出,油相(流股3)从顶部的油口流出,而水(流股2)则从下面的水槽流出。
1.1.2 油相产物分离部分 经过三相分离器简单的相分离后,反应产物被分为三相。其中油相产物主要是BTX、三甲苯以及少量的非芳烃,因此油相的分离对整个甲醇制芳烃工艺的品质有着极大的影响。这一部分主要包括两个精馏塔。
在该流程中,油相产物(流股3)首先进入芳烃-非芳烃分离器C109,经过精馏之后,油相产物中的少量非芳烃(流股5)从塔顶排出,芳烃产物(流股6)从塔底排出并进入芳烃分离器C110进一步分离,芳烃分离器C110为带侧线采出的精馏塔,可进一步将芳烃细分为苯和甲苯(流股7)、混合C8芳烃(流股8)以及C9+芳烃(流股9)分别从塔顶、侧线和塔底排出。
由于此部分的分离均是以芳烃为主体,各组分的挥发度差异不大,因此这两个精馏塔均在1~2个大气压下进行,并进行常温操作。
1.1.3 气相产物分离部分 由三相分离器分离出的气相产物(流股4)经过冷却器E101冷却后进入气相分离器C107,气相分离器的主要目的是分离甲烷及H2、CO,分离过程在高压条件下操作。气相产物中的低碳烃类(流股11)由塔底排出后进一步反应,而分离出的甲烷、H2及CO(流股10)则由塔顶排出,经预热器E102预热后从塔底进入吸收塔C108,吸收剂(流股12)经E105预热后从塔顶进入。该吸收塔选取的是Absorber模块,吸收过程在高压下进行,主要是为了分离提纯气体中的甲烷。本文中的吸收剂选用芳烃分离器C110侧线采出的C8芳烃产物(流股8)。完成吸收操作后,H2及CO由塔顶排出,吸收液(流股14)(甲烷和吸收剂的混合物)则由塔底排出,依次经真空阀V101、冷却器E103减压冷却后进入解析塔C108´,解析塔采用精馏模块,甲烷(流股15)从塔顶排出,吸收剂(流股16)由塔底排出回收利用。
1.1.4 主要操作参数及工业指标 从参考文献[12-15]得到各塔的塔压,并通过Aspen HYSYS中精馏塔的简捷计算模块 Short Cut Distillation,根据各塔的塔压计算出最小回流比,再根据实际回流比是最小回流比的1.1~2倍,输入实际回流比从而得到各塔的塔温、塔板数及进料位置等操作参数,具体如表1所示。
表1 各塔的操作参数
Table1 Operating parameters of each column
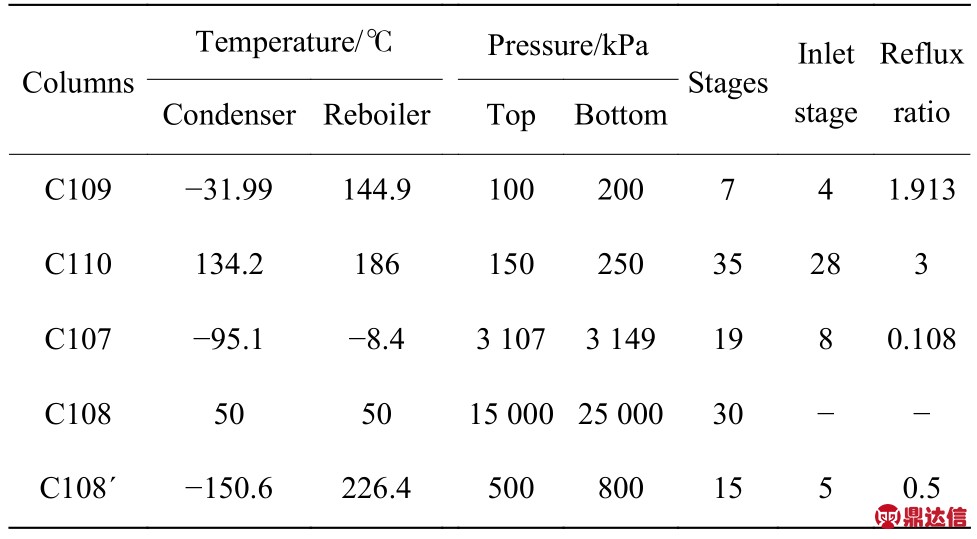
1.2 分离工艺简化模型建立及模拟结果
本文使用Aspen HYSYS流程模拟软件进行模拟。将甲醇芳构化反应器作为黑箱处理,且所有的精馏塔都是先使用简捷计算模块Short Cut Distillation进行简捷模拟,再进行严格精馏模拟。
根据本文的分离目标,在Aspen HYSYS化工模拟软件中构建如图1所示的模拟模型。
1.2.1 进料组成输入 根据 Wang等[16]通过实验分析得到清华大学循环流化床甲醇制芳烃的芳构化反应器出口产物的组成,分离工艺进料Feed的组成如表2所示(与输出结果一起)。为使模拟更符合工业化过程,本文假设分离工艺原料进料质量流率为293450kg/h。
1.2.2 塔模拟结果 利用 Aspen HYSYS 软件对建立的流程进行模拟,进料组成和各塔的操作参数如前所述,得到各塔的输出(各塔输出物流的名称见图1)如表2和表3所示。
由输出数据可以看到,各塔都具有良好的分离效果,基本均已达到分离要求。因为循环流化床甲醇制芳烃仍处在工业化初级阶段,因此要想尽快在工业上普及,仍需要进一步对流程进行改进,以便更大程度地达到节能、高效的目的。
表2 油相产物分离塔系产物组成
Table2 Product compositions of oil product separation columns
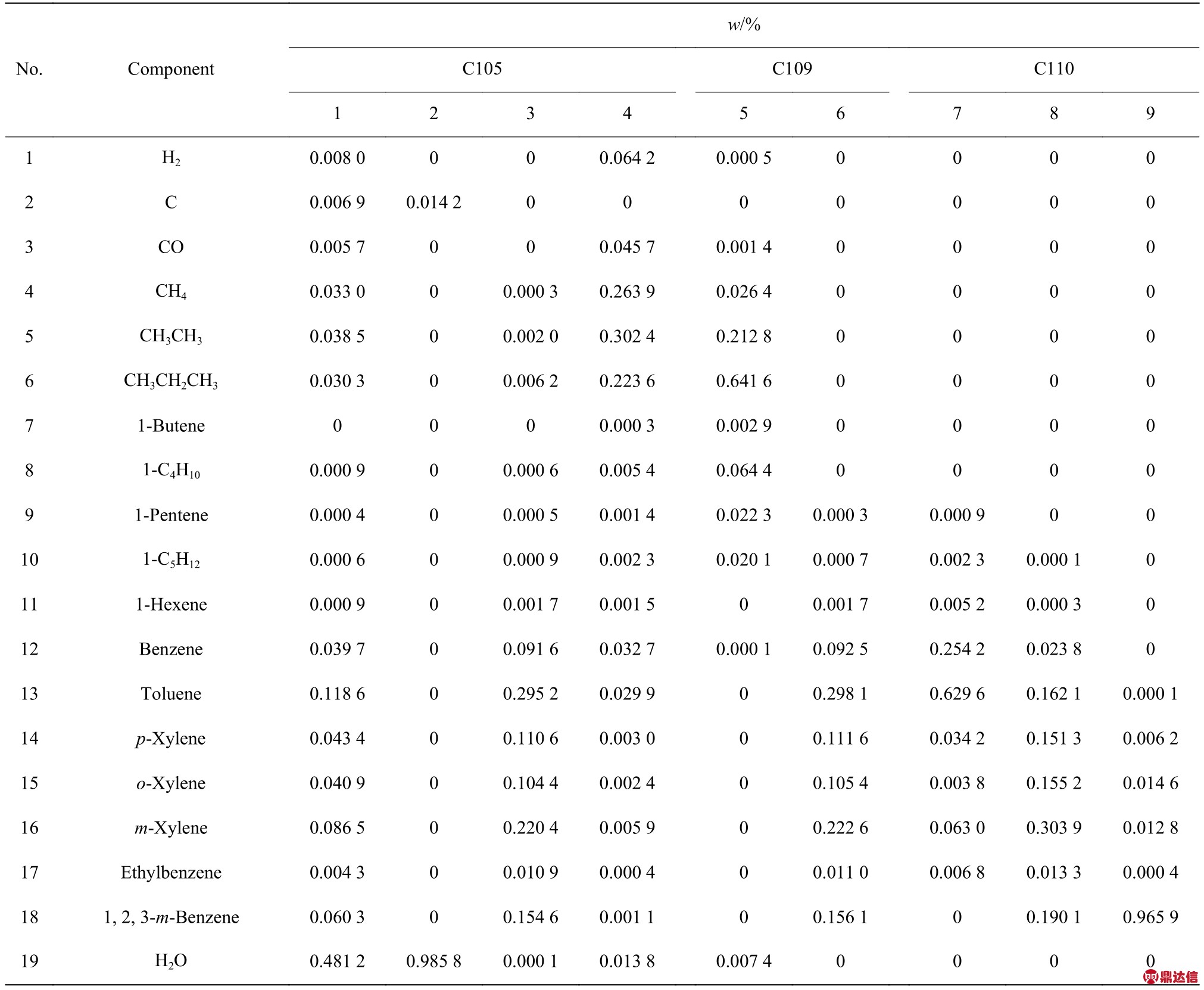
表3 气相产物分离塔系产物组成
Table3 Product compositions of gas product separation columns
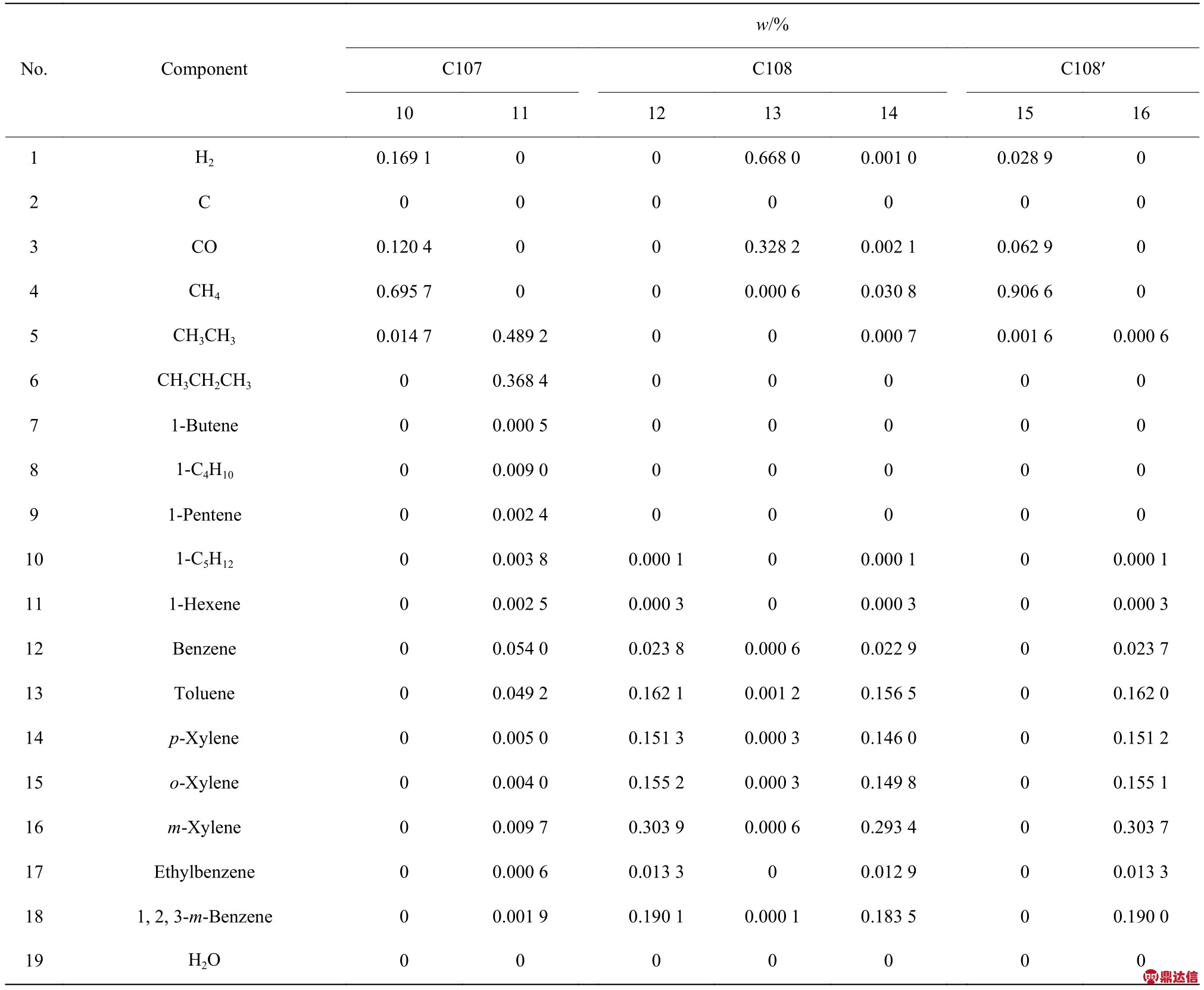
2 分离工艺的优化分析
在上述模拟过程中,我们可以看到尽管各个塔的输出都基本符合分离要求,但仍有需要改进之处。在实际生产过程中,除了要考虑分离要求之外,还需要权衡经济性、节能等各个方面的因素。本文对吸收塔中吸收剂用量进行灵敏度分析,并对塔系的换热网络进行热集成,以达到降低能耗、使流程更具有经济性的目的。
2.1 吸收塔中吸收剂用量的优化
在模拟过程中,对于吸收塔C108,若使甲烷吸收得较为彻底,则吸收剂的用量应是吸收塔原料总量的29倍,因此本文将针对吸收剂用量对吸收效果的影响进行灵敏度分析。
对吸收剂用量(自变量)与吸收液中甲烷的质量流率(因变量)进行工况分析,可以得到吸收剂用量对吸收液中甲烷质量流率的影响,如图2所示。
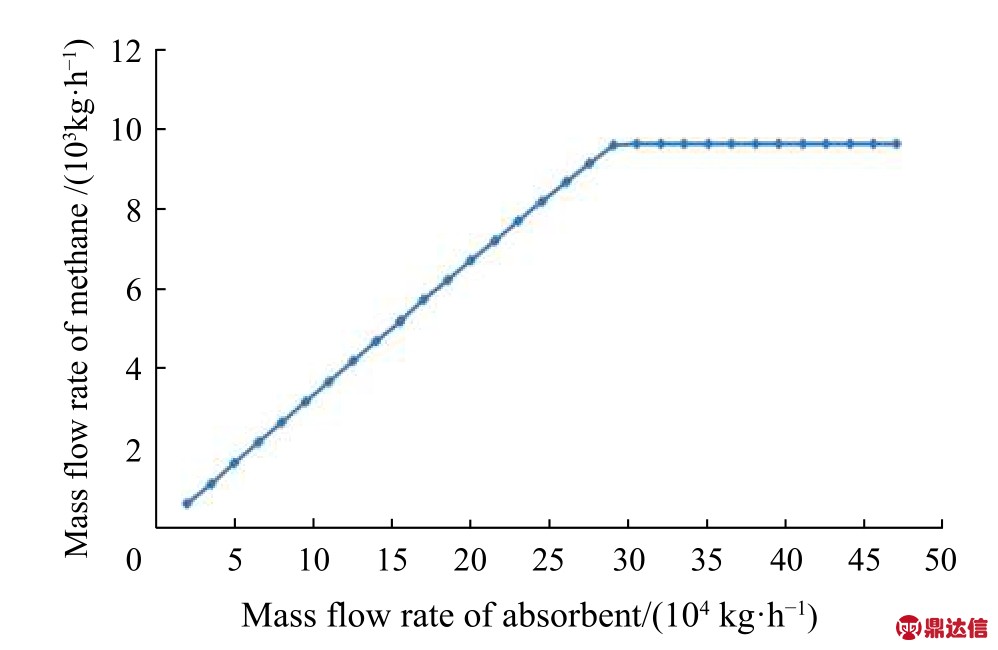
图2 吸收剂用量对吸收液中甲烷质量流率的影响
Fig.2 Effect of absorbent dosage on the mass flow rate of methane in the absorption solution
从图2中曲线可以看到,当吸收剂质量流率达到291400kg/h之后,吸收剂用量对甲烷的吸收效果影响就很小了。因此通过将吸收剂质量流率从403200kg/h 调整为 291400kg/h,使吸收甲烷的质量流率从 9654kg/h 变为 9619kg/h,几乎没有降低甲烷的吸收效果,但吸收剂用量节省了27.7%。
2.2 换热网络的热集成
在分离工艺的模拟过程中,共用到了4个换热器、4个冷凝器以及4个再沸器,这些换热设备的热量和冷量都来自公用工程,此时热公用工程消耗量为 2.86×108kJ/h,冷公用工程消耗量为 2.03×108kJ/h。如果这些冷、热流股可以互相匹配,进行系统内部换热,即可大大减少公用工程用量,降低能耗。
各冷、热物流的温度、热容流率等相关参数见表4(其中,第1列数字为物流序号,与图3中的物流序号相对应,Tin表示物流的供应温度,Tout表示物流的目标温度,Cp表示冷热物流的热容流率)。根据各冷、热物流的供应和目标温度、热容流率等相关数据,使用 Aspen Energy Analyzer软件得到物流的热夹点温度为139.2℃,冷夹点温度为134.7℃。进而采用夹点分析法,基于夹点设计3条准则[17](此准则中,N表示物流数目,下标H表示热物流,下标C表示冷物流):
(1)物流数目准则
①夹点之上:NH≤NC。这是因为夹点之上不能有冷却公用工程,因此其热物流要达到目标温度必须要通过冷物流的冷却来实现。
表4 冷、热物流参数
Table4 Data of cold and hot streams

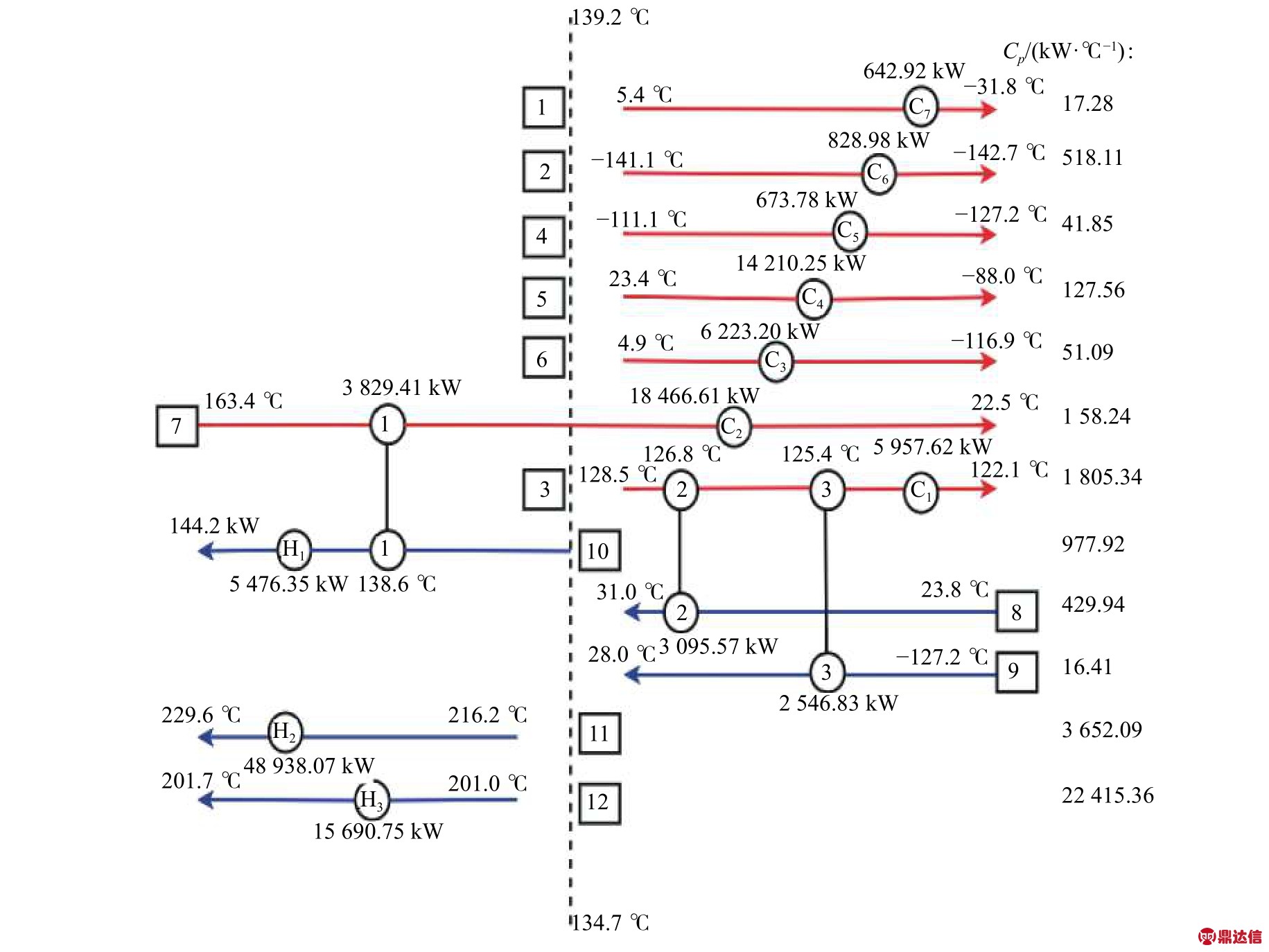
图3 热集成后的换热网络
Fig.3 Heat exchanger network considering heat integration
②夹点之下:NH≥NC。这是因为夹点之下不能有加热公用工程,因此其冷物流要达到目标温度必须要通过热物流的加热来实现。
(2)热容流率准则(适用于夹点处的匹配)
①夹点之上:CpH≤CpC。
②夹点之下:CpH≥CpC。
(3)最大换热负荷准则
每一次进行物流匹配时,应使两股换热物流中的一股达到目标温度,以此来达到最小数目换热单元的目的。
对该换热网络进行基于冷热物流匹配的换热网络热集成,最终得到集成后的换热网络如图3所示(其中,H1、H2、…表示加热器,C1、C2、…表示冷却器)。
通过冷、热物流匹配,进行换热网络热集成后,结合图3计算得出热集成后的热公用工程消耗量为2.52×108kJ/h,相比热集成前减少了 3.40×107kJ/h,即减少了11.89%;热集成后的冷公用工程消耗量为1.69×108kJ/h,相比热集成前减少了 3.40×107kJ/h,即减少了16.75%。可见,改进后的工艺流程显著降低了冷、热公用工程消耗量。
3 结 论
(1)对清华大学循环流化床甲醇制芳烃的分离工艺进行了模拟,可以看到在现有的可行条件下可以实现比较理想的分离效果。
(2)针对吸收塔C108中吸收剂的用量对吸收效果进行了灵敏度分析,得到了更优的吸收剂用量。在几乎没有降低甲烷吸收效果的情况下,使得吸收剂用量减少了27.7%。
(3)对换热网络进行了集成优化,优化后的分离工艺热公用工程消耗量从 2.86×108kJ/h降低为2.52×108kJ/h,冷公用工程消耗量从 2.03×108kJ/h 降低为 1.69×108kJ/h,冷、热公用工程消耗量均减少3.40×107kJ/h。