摘要:硅热法是目前工业产镁的主要技术手段,但由于该过程涉及高温化学反应及复杂传热机理,鲜有报道对此技术进行详细动力学及数值计算研究。本工作采用实验的方法获得皮江法炼镁化学反应动力学数据,根据数据分析确定了分段动力学模型,并转化为精确的数学模型。然后建立了耦合数学模型、辐射模型和导热模型的三维非稳态数值计算模型,并通过数值模拟计算,获得工业产镁过程中球团反应转化率和温度随生产时间的分布规律。计算结果表明,生产时间2h后球团最低温度已达1203K,4h后物料平均还原率已达66%。该技术改进方向主要为增加外层球团数量并提高还原罐中心区域传热效率。本工作可以用于指导强化传热设备的设计,预测实际生产效果,节省大量试验投资。
关键词:镁;生产;反应动力学;动力学模型;传热;数值模拟
随着国际上铁、铝、铜等传统金属材料的应用发展趋势变缓,镁及镁合金作为最轻的金属结构材料以每年20%的持续增长速度异军突起,依靠其优越特性被称为21 世纪的绿色工程材料并在国际上得到了越来越广泛的应用[1-12]。世界各国高度重视镁及镁合金材料的研究开发应用,拓宽了其在各个深加工领域的应用范围,尤其是近年来镁及镁合金材料在汽车零部件[13-15]和轨道交通[16-18]上的应用潜力使其成为科学家、企业家、军事家甚至各国政府关注的焦点。世界镁及镁合金材料产业的迅速发展带动了金属镁冶炼工业生产的急剧增长,最具代表性的中国原镁产量由1991 年的1 万吨猛增为2000 年的20 万吨,并一直处于逐年升高的趋势。目前我国是世界第一大原镁生产大国和出口大国。然而我国在原镁冶炼生产领域取得如此大的成绩依靠的不是国际领先的镁冶炼生产技术,而是国外因资源匮乏和劳动力成本过高放弃了这一高能耗、高污染行业,使我国在特定环境下发展起来具有中国特色的皮江法镁冶炼生产工业。
由于皮江法镁冶炼属于高耗能、高污染行业,资源匮乏和对污染排放要求较高的发达国家基本已经放弃原镁的生产,所以国际上对该领域的基础研究较少。目前,国内研究较多集中在对生产设备的改造,而对皮江法炼镁过程中的传热机理和化学反应动力学机理研究较少。固固反应的复杂多样性使得获取准确的动力学机理较为困难,基于动力学机理的数值模拟计算更鲜有研究。1981年Wynnyckyj等[18]首次考虑到硅热法炼镁过程发生的化学反应,并将化学反应与传热联系起来后提出了收缩核反应模型。虽然此模型并非纯正的化学反应动力学模型,但却是热法炼镁化学反应动力学机理研究的一个里程碑。1991年徐日瑶等[19]以收缩性未反应核模型为基础提出了一个描述还原过程的综合速率公式,但只适用于描述部分还原过程。2002 年,埃及科学家Morsi 等[20]通过实验研究获得了在最佳工艺条件下硅热法炼镁过程的部分化学反应动力学数据,认为在还原率低于85%的情况下,扩散模型可以较好地描述此化学反应过程,并计算出了该反应的表观活化能为306kJ/mol。刘宏专和徐日瑶[21]于1995 年率先将数值计算的方法引入硅热法炼镁领域,在不考虑化学反应和采用球团填充层等效热导率的前提下,用数值计算的方法求解导热微分方程,研究了球团在加热过程中的传热特性和温度分布,认为球团内部温度只是球团半径和反应时间的函数。夏德宏等[22]使用CFX软件对金属镁冶炼工艺中单根还原罐内外的传热进行了数值模拟,将球团的化学反应吸热简化为恒定数值的吸热源,得到了还原罐内部温度变化规律,发现了提高传热效率的制约因素。加拿大Yu 等[23]在对其发明的竖式还原罐内部传热过程进行数值模拟时将化学反应吸热项做成温度的一次函数,取得了较好效果。清华大学杨康定等[24]于2009 年在数值模拟皮江法炼镁过程中首次将化学反应动力学模型考虑入内,计算比较了化学反应对内部温度场的影响。但其采用的化学反应动力学模型是收缩性未反应核模型,用此模型描述整个还原过程时会有部分偏差。
鉴于目前所用化学反应动力学模型无法完全准确描述整个硅热法炼镁过程,寻求可靠精确的化学反应动力学模型并转化为相应的数学模型是本文的研究重点。在此基础上将数学模型嵌入数值计算模型,可以精确预测各种工业条件下硅热法炼镁过程中的产镁速率,为节能减排探索过程中减少实验设备投资。
本文首先采用实验的方法获取皮江法炼镁过程的化学反应动力学基础数据,根据数据分析确定该过程准确的化学反应动力学模型,然后将动力学模型转化为数学模型,最后将此数学模型应用至数值模拟计算模型中,获得工业产镁过程中球团在传热和化学反应耦合作用下反应转化率和温度分布规律,以期为皮江法炼镁工艺技术的进一步开发及强化传热设备的改善设计提供指导。
1 实验材料和方法
1.1 材料
本实验所用主要原料均由镁冶炼公司提供,包括白云石、硅铁合金和氟化钙。
本实验采用白云石原料由辽宁大石桥所产,成分分析结果如表1所示。
表1 白云石化学组成成分
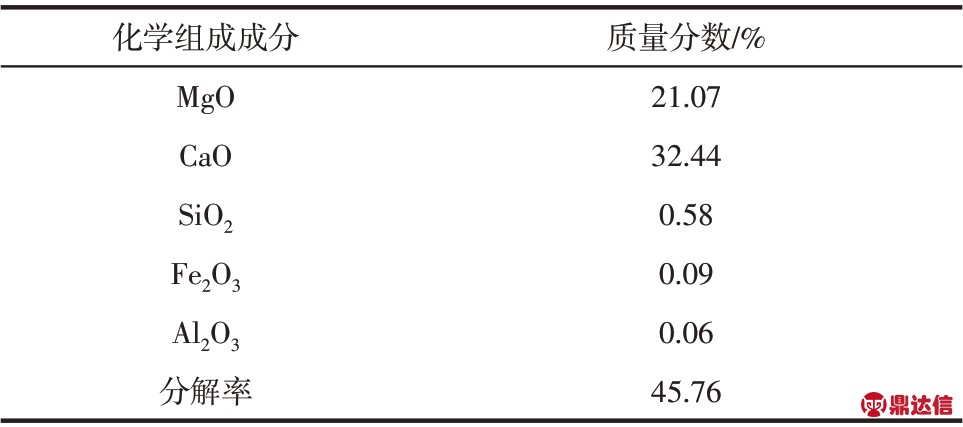
在金属镁冶炼工业生产中一般采用含硅75%左右的硅铁合金作还原剂,以达到使用最少的成本产出最高的还原率。本实验所用工业纯75%硅铁合金成分组成见表2。
表2 工业纯75%硅铁合金化学组成成分
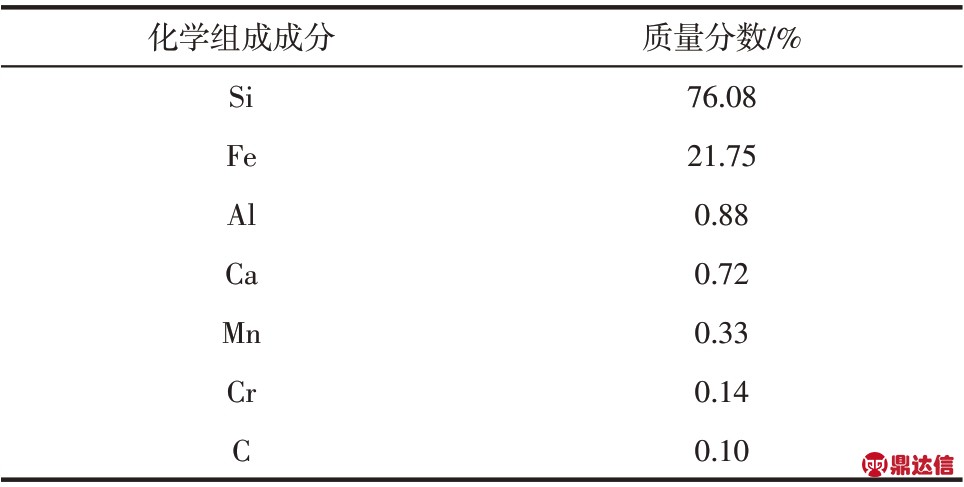
皮江法炼镁过程的还原反应属于颗粒间的固固反应,添加表面活性较高的催化剂萤石氟化钙用来加速还原过程的进行,提高生产效率,因此本实验选用分析纯氟化钙作为还原反应的催化剂。
1.2 实验装置与分析仪器
本套实验装置由压球系统、反应釜及真空系统组成。压球系统包括QHPE50x80 颚式破碎机,实验用行星球磨机以及自制压球机(油压千斤顶及直径25mm 成型模具)。反应釜系统由马弗炉、高温管式真空炉、热电偶、冷却器、流量计及压力真空计等组成。高温管式真空炉以硅钼棒为加热元件,自带温度控制系统(精度±1℃)。反应釜由99刚玉管组成,一端通过不锈钢法兰接入真空系统,另一端可自由取、放料。真空系统主要由真空管路、真空阀、ZX-15型旋片式真空泵等组成。实验装置的主要设备结构示意图如图1所示。
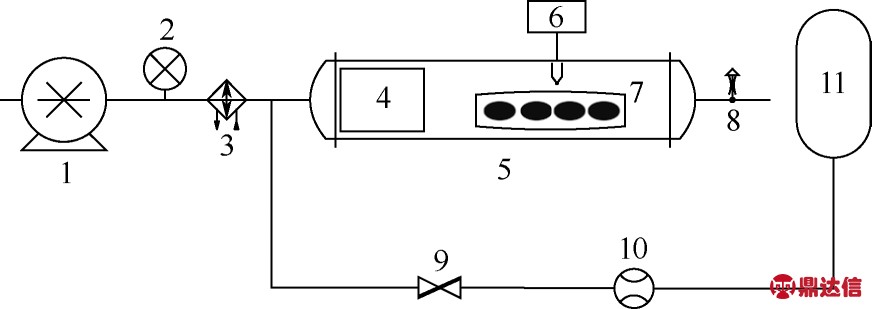
图1 实验装置主要设备结构示意图
1—真空泵;2—真空表;3—换热器;4—结晶器;5—还原罐体;6—温度控制;7—球团及坩埚;8—放气阀;9—阀门;10—流量计;11—氩气瓶
本实验的真空加热设备是核心部件,不仅要保证精确的温度控制,还要达到要求的真空条件,因此本实验还原反应发生的场所为高温管式真空炉设备中的刚玉真空管内。实验装置的主要设备实物图如图2所示。
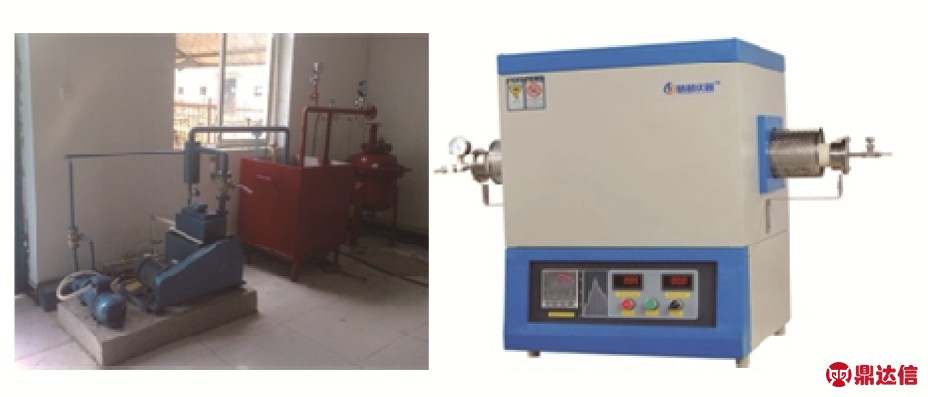
图2 实验装置主要设备实物图
1.3 实验方法
球团制备方法采用一般金属镁冶炼厂家使用的典型工艺,即配硅比1.2、成型压力150MPa和催化剂质量分数3%。将化验合格的白云石煅烧后得到水化活性和酌减合格的煅白细磨,过100目筛后与75%硅铁、萤石粉末按质量比80∶17∶3混合均匀压块。成型压力为150MPa,球团形状为厚度小于1mm 的圆柱状。为了确保传热因素对本实验结果准确性的影响降至最低,盛装实验对象的坩埚采用高温下不会被氧化增重的310S 特种不锈钢材料制备或者高纯度刚玉坩埚,且实验之前预先放入管式真空炉内,保证实验开始时坩埚温度已达到实验所需温度。
管式真空炉用氩气进行两次置换后,取一定量实验对象迅速放入质量一定、在管式真空炉预先加热至实验温度的坩埚内,然后迅速放回管式真空炉的恒温段并抽真空至10Pa 以下后开始计时,经过设定的实验时间后,迅速将坩埚拿出称量,根据球团质量的减少计算得到球团在此实验时间内的反应转化率。
2 实验结果与讨论
2.1 皮江法炼镁化学反应动力学数据
现有金属镁冶炼厂家一般选取配硅比1.2、成型压力150MPa、催化剂CaF2质量分数3%、煅白水化活性33%作为最佳生产条件。实验所测皮江法炼镁化学反应速率在不同反应温度下随反应时间变化规律如图3所示。所有实验数据均由不同实验人员重复3 次以上计算平均值所得,具有可重复性。称量球团所用电子精密天平的精度为0.01g,根据该精度及每个实验点的测量数值可以计算每个实验点的不确定度。因所测实验数据较多,不在文中一一列出,根据计算结果可得还原率最大不确定度为0.008。
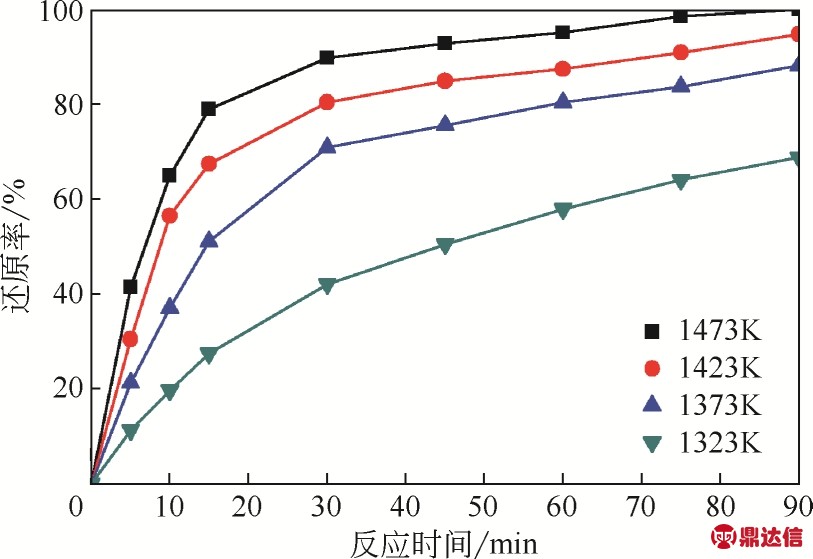
图3 皮江法炼镁化学反应动力学数据
分析图3可知,任意时间点还原率随还原温度的升高而增加。当还原温度由1323K 提高到1373K、1423K、1473K 时,15min 的 还 原 率 由27.5%分别上升至51.1%、67.4%、78.9%。值得注意的是,在还原温度增幅相同的条件下,还原率在低温区的增幅明显高于高温区,因此在工业生产中为了达到最高生产效率,还原温度必须在某一临界值之上。分析此图明显发现,还原率在1323K 和1373K 之间有一个较大阶跃,还原温度超过1373K时还原率的增幅则急速变缓,所以在进行工业生产时应该尽可能保证还原温度不低于1373K。根据还原率随反应温度变化的趋势可推算,当还原温度超过1473K时可以得到更高还原率。但在工业生产中还原反应发生在耐热合金制成的还原罐内,当温度超过1473K时还原罐的耗损非常严重,极大地增加了生产成本,所以考虑到经济效益,还原温度一般设定在1473K以下。由此可知,皮江法炼镁工艺技术的最佳还原温度是1373~1473K。
由图3可知,在给定的还原温度下,还原率随着反应时间的增加而升高。在1373K下,反应时间由15min 增加至30min、60min、90min 时,还原率由51.1%分别升高至70.9%、80.4%、88.2%。分析此图还可以发现在任意还原温度下,还原率的增长速率在开始阶段较大,随后逐渐下降直至趋近于零。随着还原温度的升高,还原率快速增长阶段所占时间在减少,在1473K反应15min还原率即可接近80%,而在1373K若要达到相同还原率则所需反应时间超过60min。因此,在工业生产时应该特别关注还原反应的开始阶段,此阶段产镁速率较快,在镁蒸气冷凝端应该适当提高降温效率以保障产生的镁蒸气全部冷凝,避免因冷却不及时而造成的生产效率下降。
2.2 皮江法炼镁化学反应动力学模型分析
皮江法炼镁过程发生的化学还原反应属于固固反应,一般固固反应主要具备以下特点[25]:①反应物颗粒之间的空间因素经常为控制因素;②不同形态的固相反应物往往具有不同的反应机理和不同的动力学方程;③同一反应的速率方程在反应的初期与后期经常不同。
固固反应的上述特点使其出现了3 种反应模型:扩散模型、相界面模型和核晶增长模型。常用描述扩散过程的模型有Jander 方程和Ginstling 方程;描述相界面的模型有表面反应模型和1st Avrami 化学反应模型;描述核晶增长的模型有Erofeev方程。各模型方程见表3。
表3 固固化学反应动力学模型及相应方程
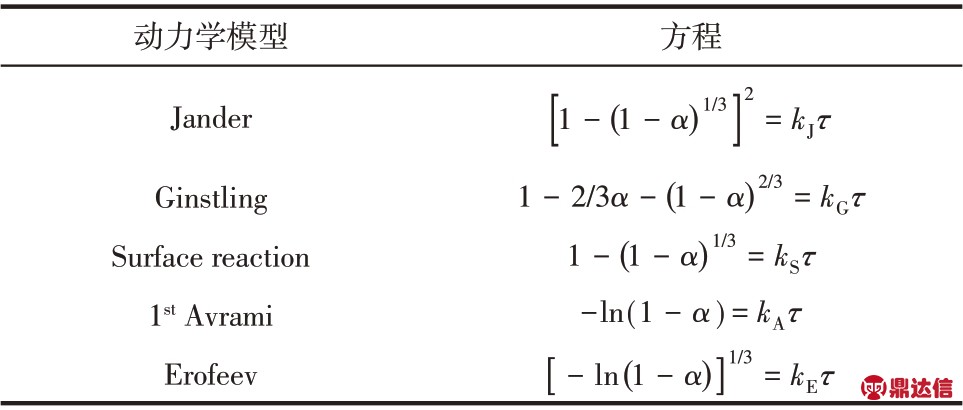
根据本文已取得皮江法炼镁的化学反应动力学数据,研究该过程的化学反应动力学模型归属。首先采用表3中的各个动力学模型分别描述皮江法炼镁的化学反应过程,并与图3中的动力学实验数据进行对比,发现单一的动力学模型无法准确描述完整的化学反应过程。因此,采用分段模型对完整的化学反应进行描述,并根据实验数据在反应初期采用1st Avrami化学反应模型,在反应后期使用Jander扩散模型分段拟合,比较准确地描述了整个化学反应过程,如图4所示。
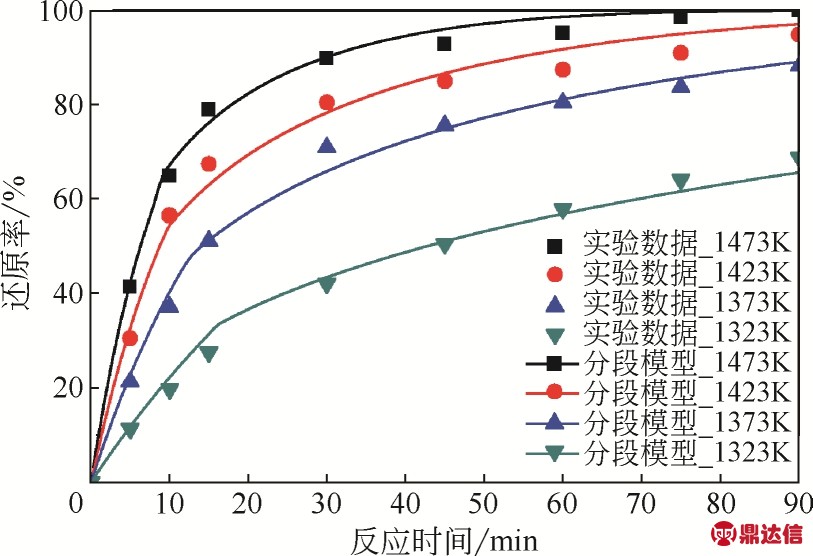
图4 皮江法炼镁化学反应动力学分段模型曲线与实验数据对比图
由图4可以发现,用1st Avrami化学反应模型和Jander扩散模型分段描述皮江法炼镁化学反应过程是比较准确的。在反应初期,化学反应发生在固体颗粒接触面上,属于相界面模型;在反应中后期,因产生的大量镁蒸气向外扩散环节受到了限制,化学反应模型转变为扩散模型。在动力学分段节点处可以观察到还原率增长速率出现明显下降的现象,两种模型转变的时间节点则是由反应温度决定。该分段动力学模型适用温度范围为1323~1473K。
采用分段模型得到反应温度为1323K、1373K、1423K、1473K 下的皮江法炼镁化学反应动力学方程见式(1)。
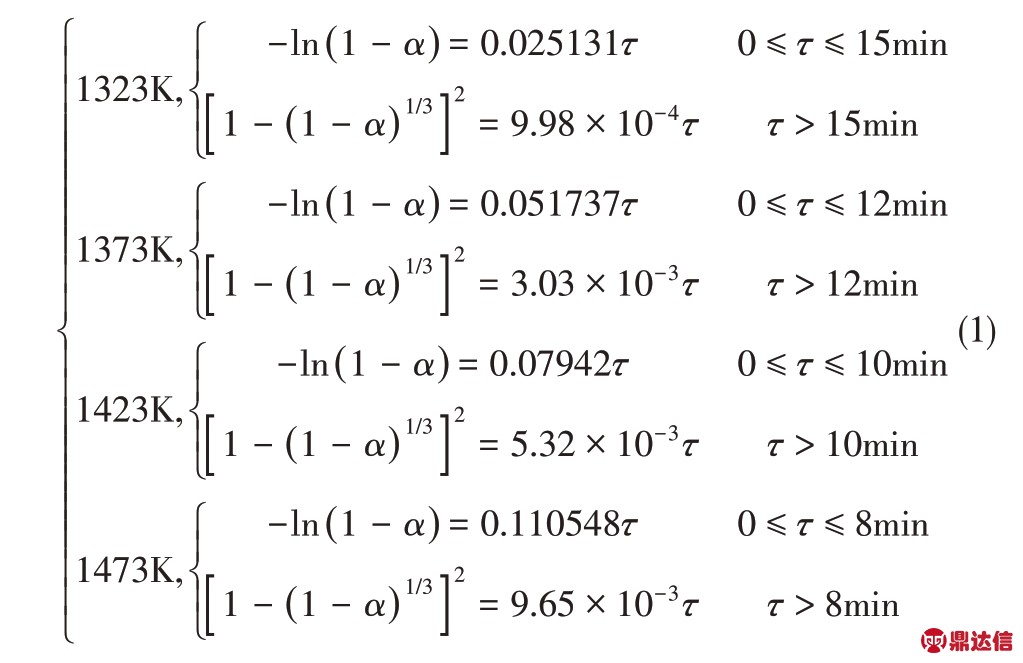
2.3 皮江法炼镁化学反应动力学数学模型的分析与转化
采用分段模型可以准确解释皮江法炼镁化学反应动力学机理,但实验温度选取的是特定若干代表性反应温度,并不能涵盖到每一个温度点和时间点。由于皮江法炼镁是一个基于化学反应动力学模型的非稳态升温过程,对该过程的数值模拟计算工作涉及反应温度区间内任一温度下任一时间的化学反应动力学数据,且必须将全部数据用C语言编程后加载至数值计算软件,所以仅有若干代表性反应温度下的动力学数据远远不能满足随后的数值模拟计算工作需要。为此,对皮江法炼镁化学反应动力学数据进行分析并转化为一种准确且简便的数学模型是非常有必要的。
使用Origin软件对动力学数据进行多种数学函数形式的拟合和精度对比,确定精度最高的数学函数为多项式和指数混合型函数,得到皮江法炼镁化学反应动力学的数学模型,如式(2)所示。
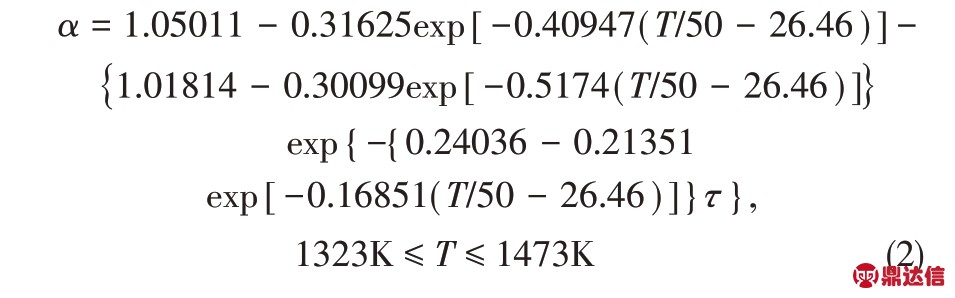
式中,T为温度,K。
为了验证该数学模型在预测非代表性反应温度下动力学数据的准确性,用此数学模型计算反应温度1348K、1398K、1448K 下还原率随反应时间的变化曲线并与实验结果作对比,如图5所示。

图5 皮江法炼镁化学反应动力学数学模型实验验证
由图5可知,皮江法炼镁化学反应动力学数学模型预测不同温度下各实验点的还原率与实验值相差全部控制在5个百分点以内,且预测值与实验值的偏差均低于3%。因此采用本文得到的皮江法炼镁化学反应动力学数学模型描述整个炼镁过程的化学反应是非常准确的,可以方便高效地应用于后续的数值模拟计算工作。
3 数值模拟计算
皮江法炼镁是一个涉及传热传质和化学反应的复杂热力学过程,对该过程进行数值计算的难点在于准确确定全部反应区域内瞬时化学反应吸热速率,精确计算各点反应转化率及平均产镁速率。为此,需将本文得到的皮江法炼镁化学反应动力学数学模型用用户自定义函数加载至数值计算软件Fluent,建立相应的传热传质与化学反应综合数值计算模型。
3.1 皮江法工业炼镁物理模型及计算区域
皮江法炼镁过程是在耐热合金钢制还原罐内完成,还原罐形状一般为外径330mm,壁厚30mm,长度约为3000mm的圆筒,内部填满核桃状或椭球状球团。为了便于计算,可将球团处理为球形球团。因球团的体积决定了炼镁过程中的化学反应吸热量,所以必须采用等效体积法简化球团形状以保证传热计算结果的准确性。根据分析计算,球团的等效直径为22mm。在实际工业生产中,球团在还原罐内属于非规矩整齐式排布,而且是随机“见缝插针”式排列,如图6所示。
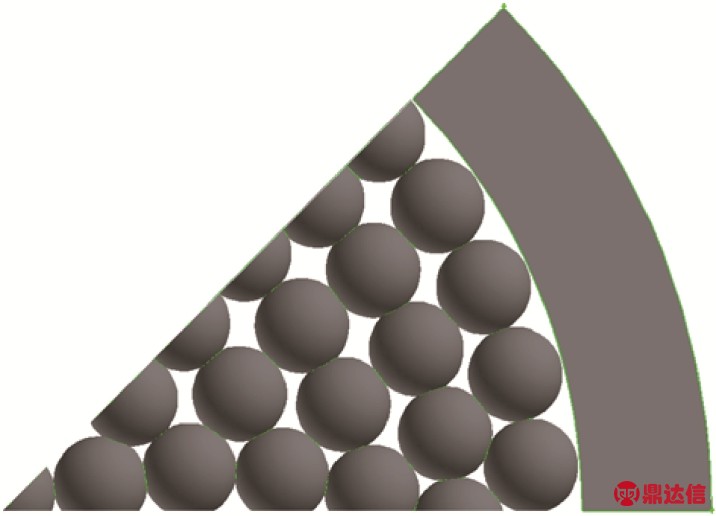
图6 球团在还原罐内无规律“见缝插针”式排布
还原罐轴向长度较大,可在轴向取单层球团厚度建立三维立体物理模型。由于球团在还原罐内的传热过程主要是沿径向由外而内逐层进行,可将物理模型近似按几何对称性取1/8几何体作为计算区域。使用Gambit 软件进行网格划分,逐渐加密网格并使其满足网格无关性条件。在此基础上,为提高后续计算过程中辐射传热模型的计算精度,最终加密网格数量至75 万左右。计算区域及网格示意图如图7所示。
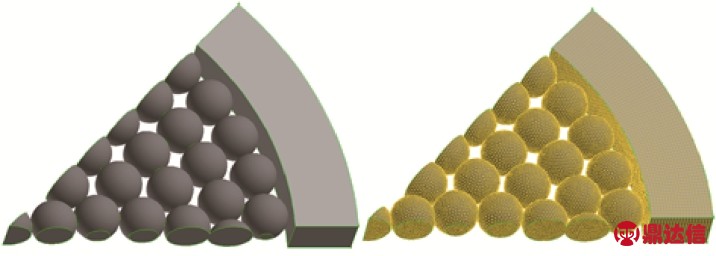
图7 三维计算区域及其网格系统
3.2 控制方程、物性参数及求解条件
3.2.1 控制方程
皮江法镁冶炼工业生产的步骤是将球团填充至还原罐内被加热升温,迅速将还原罐密封后抽真空进行镁蒸气的生产和冷凝。还原罐外侧壁温为还原炉的炉温,在此炉温加热下依次进行如下传热过程:①还原罐外侧向内侧的导热过程;②还原罐内壁与球团表面间及不同球团表面间的辐射传热;③球团内部的导热过程;④球团发生还原反应时进行的化学吸热过程。
由还原罐外侧向内侧的导热过程属于恒壁温条件下无内热源的三维非稳态导热过程,其控制方程[26]见式(3)。

式中,ρs 为还原罐材料的密度,取常数7850kg/m3;cs 为还原罐材料的比热容,取常数460J/(kg·K);λs为还原罐材料的热导率,虽此数值随温度有变动,但因变化幅度较小,可视为常数,取平均值35W/(m·K)。
由于球团内部的导热过程导致球团温度升高至足以发生还原反应,此时球团内部开始进行化学吸热过程,因此球团内部导热过程与还原反应中进行的化学吸热过程相伴相随,可将球团内部进行还原反应的吸热量处理成源项代入球团内部导热微分方程,得到球团导热过程的控制方程[26]如式(4)所示。

式中,ρb为球团的密度,kg/m3;cb为球团的比热容,J/(kg·K);λb为球团的热导率,W/(m·K);Sb为还原反应吸热源项,W/m3。
3.2.2 物性参数
在皮江法炼镁还原过程中球团会因内部镁蒸气的产生扩散而发生质量变化,所以在数值模拟计算过程中必须考虑煅白、硅铁和萤石按比例混合料球的密度变化问题。经过测量,大部分皮江法镁冶炼工业生产厂家所用由煅白、硅铁和萤石按比例混合的料球的初始密度约为1720kg/m3,随着还原反应的进行,球团密度随还原率变化的计算见式(5)。

由于球团是按质量比80%煅白、17%硅铁和3%萤石混合而制,所以球团的比热容也是由三者的比热容按相同比例混合而得。球团比热容随温度变化较大,而还原反应一般在温度超过1050℃才明显进行,可以忽略高温段因产镁造成球团组分变化而产生的球团比热容变化。查文献可得煅白随温度变化的比热容按式(6)计算。

硅铁随温度变化的比热容按式(7)计算。

萤石随温度变化的比热容计算如式(8)。

混合球团的比热容计算如式(9)。

用瞬态热丝法测量煅白、硅铁和萤石按比例混合球团在常温下的热导率为0.7W/(m·K),随着还原反应的进行,球团产生镁蒸气后会变成渣球,热导率会发生降低,当还原率为1即球团发生还原反应完全后热导率约为0.55W/(m·K),故可视球团热导率随还原率呈线性变化,计算公式为式(10)。

球团内部化学反应吸热可以当作源项处理,吸热量计算如式(11)。

式中,Hb为生成每摩尔镁蒸气所需热量,J/mol;ωb为单位体积球团平均产镁速率,mol/(m3·min)。
根据皮江法炼镁热力学原理查资料可知,生成每摩尔镁蒸气所需热量计算如式(12)。

单位体积球团平均产镁速率计算如式(13)。

式中,Mb为单位体积球团最大产镁量,根据球团质量配比计算得12587.9mol/m3;dα/dτ 为还原率在单位时间内的变化,min-1,可根据本文所得皮江法炼镁化学反应动力学数学模型进行计算。
3.2.3 求解条件
皮江法炼镁属于周期性生产过程,每个周期由常温球团装入恒温还原罐开始,在球团传热升温过程中完成镁蒸气的生产。由于在实际工业生产过程中,还原罐外侧炉温较难维持在恒定温度,可能会在一定范围内波动。为简化计算,选取炉温波动范围内若干代表性数值作为恒壁温边界条件分别进行计算分析,此时边界条件为还原罐外壁温T=T设定。球团在常温条件下装入还原罐,故初始条件为T =298.15K。
3.3 数值模拟计算结果与讨论
3.3.1 模型验证及物料平均还原率随时间变化规律
物料平均还原率的定义为某一时刻还原罐内全部物料已经产生的镁蒸气质量与理论产镁质量之比。在皮江法镁冶炼工业生产中比较关心的是还原罐内物料平均还原率随反应时间的变化规律,根据物料平均还原率确定生产周期对生产厂家非常重要。采用所建数值计算模型对还原罐内升温及还原反应情况进行模拟,得到不同壁温下物料平均还原率随时间的变化规律,如图8所示。在镁冶炼工业生产过程中,虽然炉内温度要求尽可能接近1473K,但因还原炉温度会出现波动,所以本文选取1423K、1448K 和1473K 3 个代表性炉温分别作为还原罐恒温外壁面温度。
由图8可以发现,在恒定壁温下还原罐内物料平均还原率随反应时间的增加而上升,且上升幅度随时间的增加逐渐减小;在相同反应时间下,温度的增加可以明显改善还原反应效率。与实际工业生产数据对比,发现温度为1448~1473K时数值计算结果较好,据此判定皮江法金属镁冶炼厂家所使用的还原温度大多数处于1448~1473K范围,符合工业生产实际情况,也反向证明了所建数值计算模型的正确性。
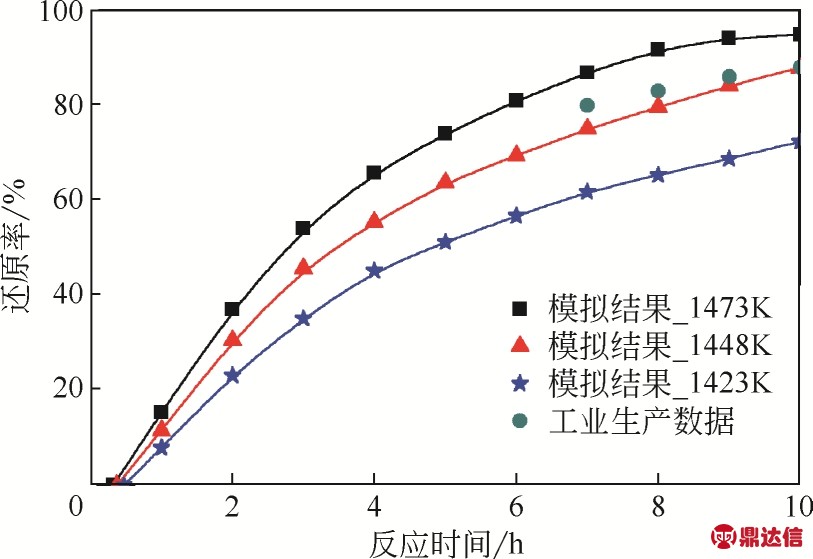
图8 还原罐不同壁温下物料平均还原率随时间变化规律
由图8可知,壁温1473K还原时间4h时物料平均还原率为66%,而8h 时为92%,即物料在一个生产周期的前半段生产的镁蒸气量远大于后半段。造成此种现象的原因并不是在生产周期前半段球团还原反应速率大于后半段,而是由于由罐壁向罐中心方向的环形截面积逐步降低,外层球团数量大于内层球团数量。因此皮江法镁冶炼生产厂家需注意,在生产周期前半段镁蒸气的冷凝收集速度要高于后半段,涉及的随镁蒸气冷凝放热量变化而负载变化的冷却系统亦需配备准确。
3.3.2 还原罐内球团瞬时还原率分布规律
根据本文计算分析可知,皮江法金属镁冶炼厂家所使用的还原温度在1448~1473K范围,以最佳温度1473K作为还原罐外壁温度,球团瞬时还原率随反应时间分布规律如图9所示。
由图9可知,传统还原罐内任一球团的瞬时还原率都随反应时间的增加而上升,总体呈现由靠近外壁处向中心区域逐层减小的规律,符合实际生产情况。根据此图可发现,增加单位反应时间还原罐内球团还原反应由外而内的推进层数基本相同,与之前所得物料平均还原率随反应时间增速减缓的现象矛盾,出现这种矛盾的原因是还原罐外层排布球团数量大于内层,每层球团所含镁蒸气的总质量呈现由外而内下降的趋势。因此可推断,相比靠近还原罐壁面的外层球团,靠近还原罐中心区域的球团进行还原反应过程时耗费相同时间产生的镁蒸气质量较少,对还原罐进行技术改造时则可考虑减少球团在还原罐中心区域的排布。
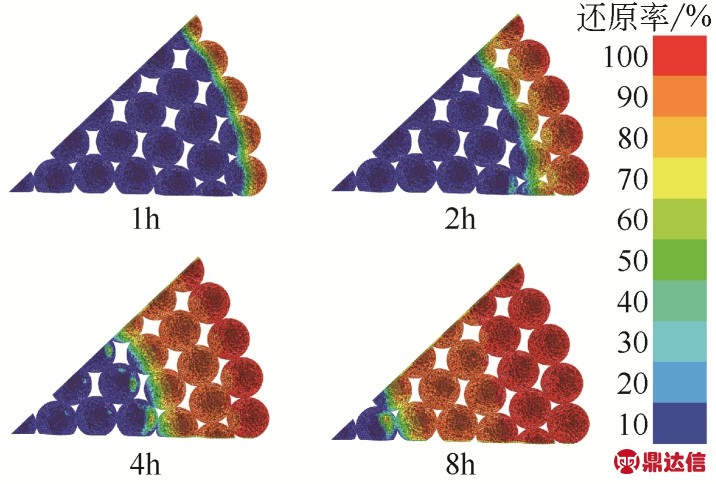
图9 还原罐内物料平均还原率随反应时间分布规律
3.3.3 还原罐内球团温度分布规律
球团温度随反应时间分布规律如图10所示。
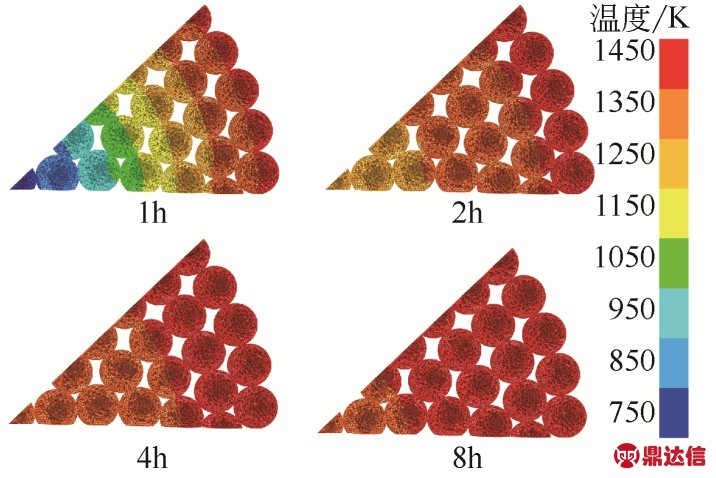
图10 还原罐内球团温度随反应时间分布规律
由图10 可知,还原罐内球团温度分布规律与瞬时还原率分布规律相似,任一球团的瞬时温度都随反应时间的增加而上升,总体呈现由靠近外壁处向中心区域逐层降低的规律。不同于球团瞬时还原率在单位反应时间还原反应由外而内的推进程度基本一致,球团温度在还原反应初期上升非常迅速,之后呈现缓慢增长的趋势。根据计算结果,在还原反应进行2h 后,球团最低温度已达1203K,大部分球团温度处于1273K以上。造成这种现象的原因是在还原反应的初始阶段,常温球团受高温壁面辐射传热和接触导热影响迅速升温,且此时球团因没有达到还原反应起始反应温度而不会出现吸热源,球团接收到的热量全部用于自身温度的提升导致球团在反应初始阶段升温速率很大。当反应过程进行2h 后,还原罐内大部分球团已经达到还原反应的起始温度,此时球团内部开始进行还原反应需要吸收大量热量,且因温度梯度的降低高温壁面向球团的辐射热量和导热量也随之降低,所以用于球团升温的热量迅速减少,导致此后球团温度的升温速率明显下降。
4 结论
(1)分段动力学模型可以准确描述温度区间为1323~1473K的皮江法炼镁化学反应动力学机理。
(2)皮江法炼镁化学反应动力学模型转化为数学模型可以精确且方便地用于数值模拟计算。
(3)本文所建包含传热模型和化学反应动力学数学模型的数值计算模型可以准确模拟皮江法镁冶炼工业生产过程,预测任意时刻球团反应还原率及温度分布。
(4)皮江法镁冶炼过程在前半周期的产镁量远大于后半周期,原因主要是由外而内每层排布球团数量的减少和还原罐中心区域的低传热效率。
本文所建数值计算模型不仅为现有皮江法炼镁工艺技术改进指明了方向,即增加外层球团数量并提高了还原罐中心区域传热效率。而且可以用于指导强化传热设备的设计,节省大量试验投资。
符号说明
cb,cs—— 分别为球团和还原罐比热容,J/(kg·K)
Hb—— 生产每摩尔镁蒸气所需热量,J/mol
Mb—— 单位体积球团最大产镁量,mol/m3
Sb—— 球团化学反应吸热量,J/m3
α—— 反应还原率,%
λb,λs—— 分别为球团和还原罐的热导率,W/(m·K)
ρb,ρs—— 分别为球团和还原罐的密度,kg/m3
τ—— 反应时间,min
ωb—— 单位体积球团平均产镁速率,mol/(m3·min)