摘 要: 以去离子水为工质,探究了不同孔密度泡沫铜在不同压力下的沸腾换热性能.实验结果表明:泡沫铜表面生成汽泡的总体积大于光滑表面生成汽泡的总体积.孔密度对泡沫铜的沸腾换热性能有很大影响,在试验参数测试范围內,泡沫铜的沸腾换热性能随孔密度的增加先增强后减弱,70PPI为最佳孔密度.相对于光滑表面,压力越大,高孔密度金属泡沫的强化沸腾换热能力减弱.
关键词: 金属泡沫;孔密度;压力;沸腾汽泡;沸腾换热性能
由于工质相变换热系数比较大,并具有高热流密度和低温差的优点.因此,为解决电子器件高热流密度散热问题,目前通过改造蒸发面结构来强化沸腾换热越来越受到更多学者的关注[1-4].由于金属泡沫的优异性能,其强化沸腾换热的作用已得到众多研究者的关注.文献[5]研究了泡沫铜孔密度和厚度对沸腾换热的影响,结果表明泡沫铜孔密度和厚度之间有合理的匹配.文献[6]以丙酮为工质研究了泡沫铜孔密度对汽泡生长过程的影响,发现90PPi泡沫铜在较低的过热度下就发生了汽泡合并,在较高过热度下,低孔密度泡沫铜的沸腾换热性能优于高孔密度泡沫铜.随后分别以光滑表面、微槽道表面和多孔涂层表面为蒸发壁面进行沸腾换热实验研究[7-8],实验结果表明:微槽道表面和多孔涂层表面的沸腾换热性能均优于光滑表面,在低过热度下多孔涂层表面的沸腾换热性能优于微槽道表面,在高过热度下微槽道表面的沸腾换热性能优于多孔涂层表面.并且三维多孔涂层表面的临界热流密度为普通表面的3.7倍.文献[9]中研究了金属泡沫的材质和厚度对沸腾换热的影响,相比于光滑表面,金属泡沫延迟了沸腾危机点,随着金属泡沫厚度的减少,泡沫铜的沸腾传热能力先减小后增强,而泡沫镍的沸腾传热能力增强.随后又研究了梯度孔金属泡沫对沸腾换热的影响[10-11],实验结果显示相对于单一孔径的金属泡沫,梯度孔金属泡沫显示出更好的沸腾换热性能.从已有的研究看,对金属泡沫沸腾换热的研究多集中于池沸腾换热,进一步考虑蒸发腔内在不同压力下金属泡沫沸腾换热性能的研究还未见报道.文中在不同压力下对不同孔密度泡沫铜的沸腾换热性能进行试验研究,考察泡沫铜孔密度及不同压力对泡沫铜沸腾换热性能的影响.
1 试验装置和数据处理
图1为实验装置示意图,包括电加热系统、冷却系统、抽真空系统、数据采集系统.加热系统是由加热铜块、功率仪、智能电量测量仪PF9901和5根额定功率为250W加热棒组成,加热铜块的上表面为直径30 mm的圆,其余面采用导热系数为0.25W/(m·K)的PEEK板进行保温,以减少漏热量.冷却系统主要是冷却蒸发腔受热产生的水蒸汽,并通过调节冷却水流量来调节蒸发腔内的压力.抽真空系统主要由真空阀和真空泵FY-1C-N组成,用于实验前对系统抽真空.数据采集系统由6个热电偶、1个压力传感器、温度巡检仪NPXJ-C4000TD0、 MCGS组态软件和高速摄像仪组成.热电偶T1,T2和T3依次放在加热铜块轴心线处,间距为18 mm,用来测量热流密度,T4放置在加热铜块上表面中心上方3 mm处,用于测量沸腾容器内工质的温度,T5 和T6分别放置在蒸汽出口位置和液体回流位置,用于测量沸腾容器出口处蒸汽温度和回流液体的温度,压力传感器放置在沸腾容器上盖处,用于测量系统内的压力.沸腾容器的3面共有3块石英玻璃,高速摄像仪通过石英玻璃捕捉汽泡的动态图像,试验高速摄像仪的拍摄速度为1 000帧/秒,分辨率为640×480像素.
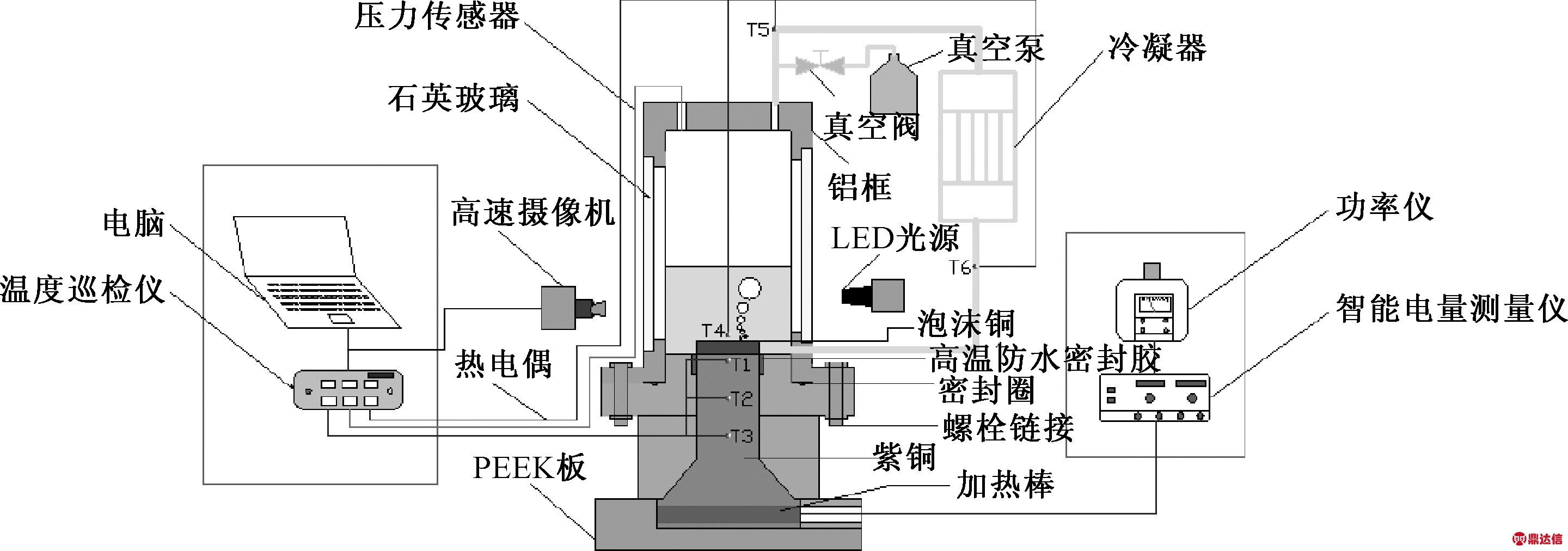
图1 实验装置示意
Fig.1 Schematic of the experimental steup
试验中所用的泡沫铜采用电沉积法制备,实验前泡沫铜和加热铜块之间通过铜基板连接,先把泡沫铜和2 mm厚的铜基板在高温炉中烧结成一体,然后通过线切割加工直径为30 mm的圆柱,再通过锡粉把铜基板焊接在加热铜块上,加热铜块和铜基板之间的焊锡厚度约为0.03 mm, 约为热电偶T1测温点到铜基板上表面距离的1.0%,其热阻可忽略不计.试验中共用4种不同孔密度泡沫铜样品,参数如表1.金属泡沫的结构如图2.
表1 金属泡沫的构造参数
Table 1 Structure parameters of metallic foam
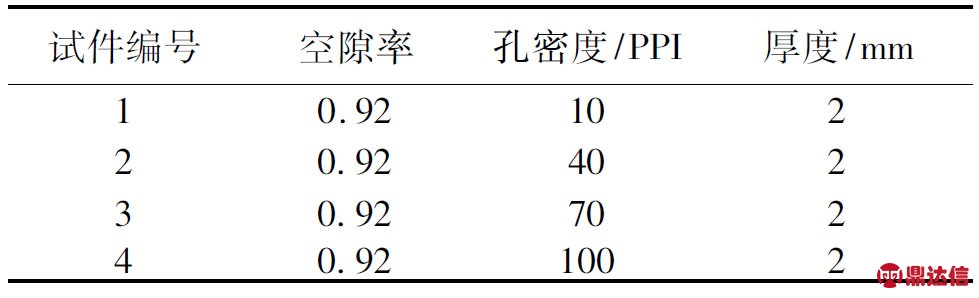
图2 通孔金属铜泡沫(放大10倍)
Fig.2 Copper foam (magnifying 10 times)
试验步骤:① 按照图1完成实验装置的连接,打开真空泵和真空阀对试验系统进行抽真空至系统内压力为2Pa,然后通过该真空阀向系统内充入去离子水,不同压力下去离子水的物理性质如表2,文中实验充液率为40%(工质体积占沸腾容器内腔体积的40%);② 实验时首先接通加热棒电源,通过调节功率仪控制加热棒的总输入功率,同时打开冷却水泵,通过调节水的流速来维持系统内压力为某一恒定值,当热电偶的波动范围小于0.3 K/20min时,用电脑记录各个传感器的数值和汽泡生长图像;③ 将加热功率依次按照2%增加,重复前述实验步骤②,直至加热表面沸腾换热性能突然恶化(热电偶的读数急剧增大),此时加热表面热流密度达到临界热流密度,试验结束.更换实验测试样品,重复步骤①、②、③.
表2 不同压力下去离子水的物理性质
Table 2 Physical properties of deionized water under different pressures

由于紫铜的导热系数远大于PEEK板的导热系数,因此可以把紫铜的导热视为一维导热,根据T1,T2,T3的值可以计算出加热表面的热流密度:

(1)

(2)
式中:ξ0为T1位置点到铜基板上表面的距离;ξ1为T1和T2位置点之间的距离;ξ2为T2和T3位置点之间的距离;q为热流密度;λ为导热系数;Tw为铜基板上表面的温度.
传热面的壁面过热度为:
ΔT=Tw-Ts
(3)
式中,Ts为工质的饱和温度.
因此加热表面的沸腾换热系数h为:
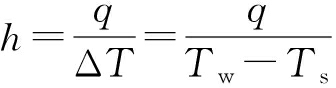
(4)
在数据处理中,为保证测量精度,随温度变化对加热铜块的导热系数进行了温度修正.根据加热铜块的牌号具体拟合得到其导热系数为:
λ=-0.068T+410.9
(5)
式中:T=(T1+T2+T3)/3
在计算试验系统热流密度误差和换热系数误差时,按照标准的误差分析,误差的主要来源为:经标定后的热电偶测量误差0.5%,热电偶间距误差0.4%,经温度修正后的加热铜块导热系数误差1%
热流密度的不确定度为:

(6)
沸腾换热系数的不确定度为:

(7)
式中,L为相邻热电偶之间的距离.按照标准误差分析计算出热流密度的最大不确定度为1.9%,沸腾换热系数的最大不确定度为9.15%.
2 结果与分析
2.1 孔密度对沸腾换热性能的影响
图3为在101 kPa下,孔密度为10PPI、40PPI、70PPI和100PPI的4种泡沫铜表面和光滑表面的沸腾传热曲线.从图3中可以看出,在低热流密度下泡沫铜的沸腾换热性能明显好于光滑表面,并且起始沸腾点的过热度比光滑表面低3~4℃.
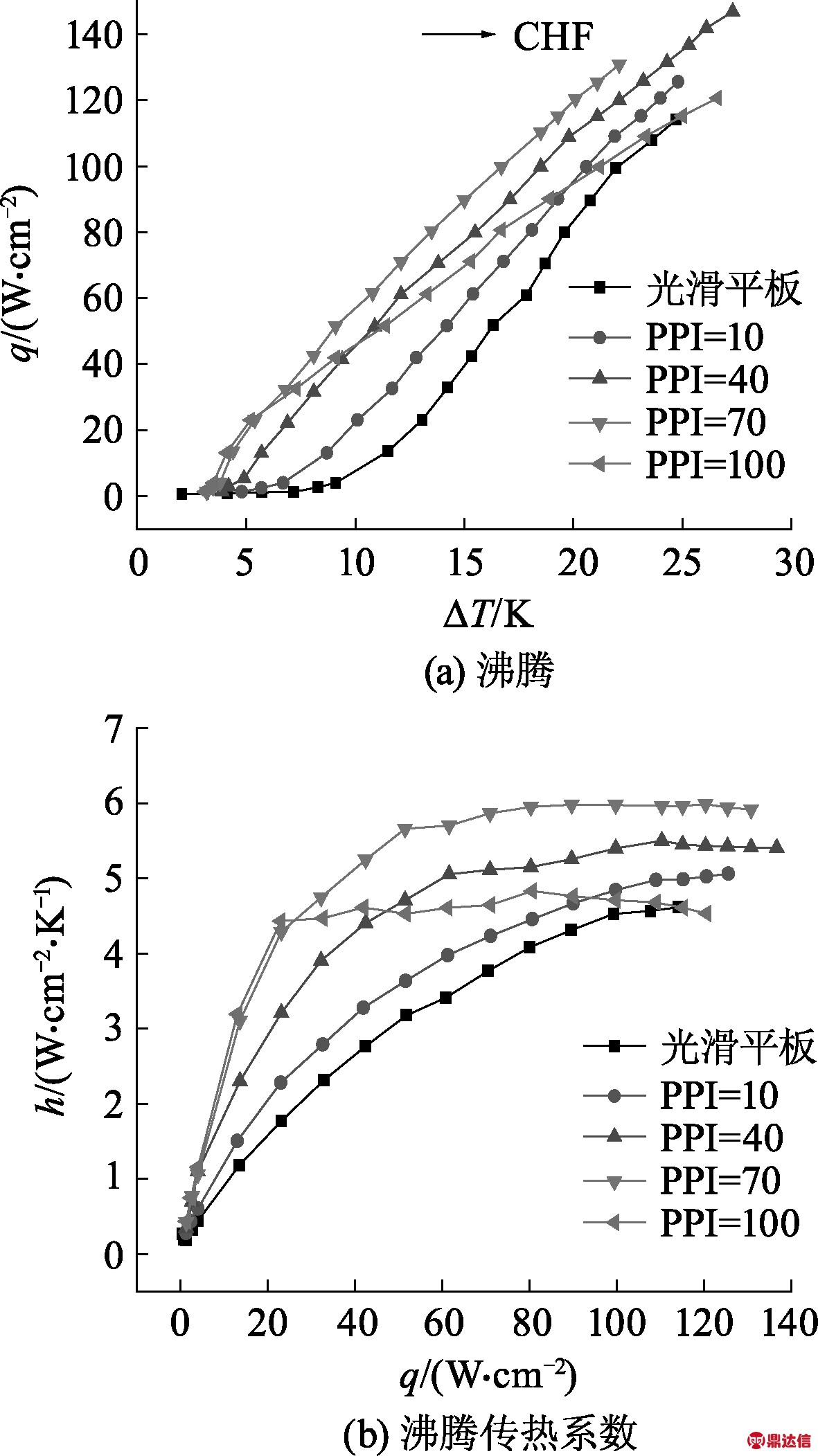
图3 金属泡沫的沸腾传热曲线
Fig.3 Boiling curves of copper foam
在同样厚度和孔隙率下,泡沫铜的整体沸腾换热性能随孔密度的增加先提高后降低.主要是由于随着孔密度的增大,泡沫铜的比表面积增大,并且单位表面积上的汽化核心点数目增加,这有利于强化换热.100PPI的沸腾换热性能却低于70PPI的沸腾换热性能,这表明虽然100PPI的比表面积和汽化核心点数目明显高于70PPI,但是孔密度越高,孔径越小,汽泡上升过程中所受的阻力相应增加,此时汽泡上升过程中所受阻力带来的负面作用大于汽化核心点数目增多带来的正面作用.
从图3(b)中可以看出:当热流密度处于0~94 W/cm2区域,100PPI的沸腾换热性能明显高于10PPI,当热流密度大于94 W/cm2,100PPI的沸腾换热性能明显低于10PPI,主要因为在低热流密度区,100PPI泡沫铜骨架内部没有出现汽泡拥挤现象,汽化核心点数目多占主导作用,当热流密度高于94 W/cm2,100PPI泡沫铜骨架内部发生了汽泡拥挤现象,因此恶化了传热.相对于光滑表面,高孔密度泡沫铜在低热流密度区沸腾换热能力优势明显,其中当热流密度为13.1 W/cm2时,100PPI的换热系数是光滑表面的2.7倍,但在高热流密度区,其强化沸腾换热性能优势并不明显.相对于光滑表面,泡沫铜在一定程度上提高了临界热流密度,其中40PPI的临界热流密度是光滑表面的1.28倍,这主要是因为泡沫铜的毛细力,使新鲜的液体及时补充到汽化区,延迟了沸腾危机点.
2.2 汽泡行为的可视化分析
通过可视化观察发现,随着热流密度的增大,光滑表面和泡沫铜表面的汽化核心点数逐渐增加,汽泡生成的周期缩短.在101 kPa下,光滑表面核态沸腾过程中汽泡的形态如图4,40PPI泡沫铜的汽泡形态如图5.
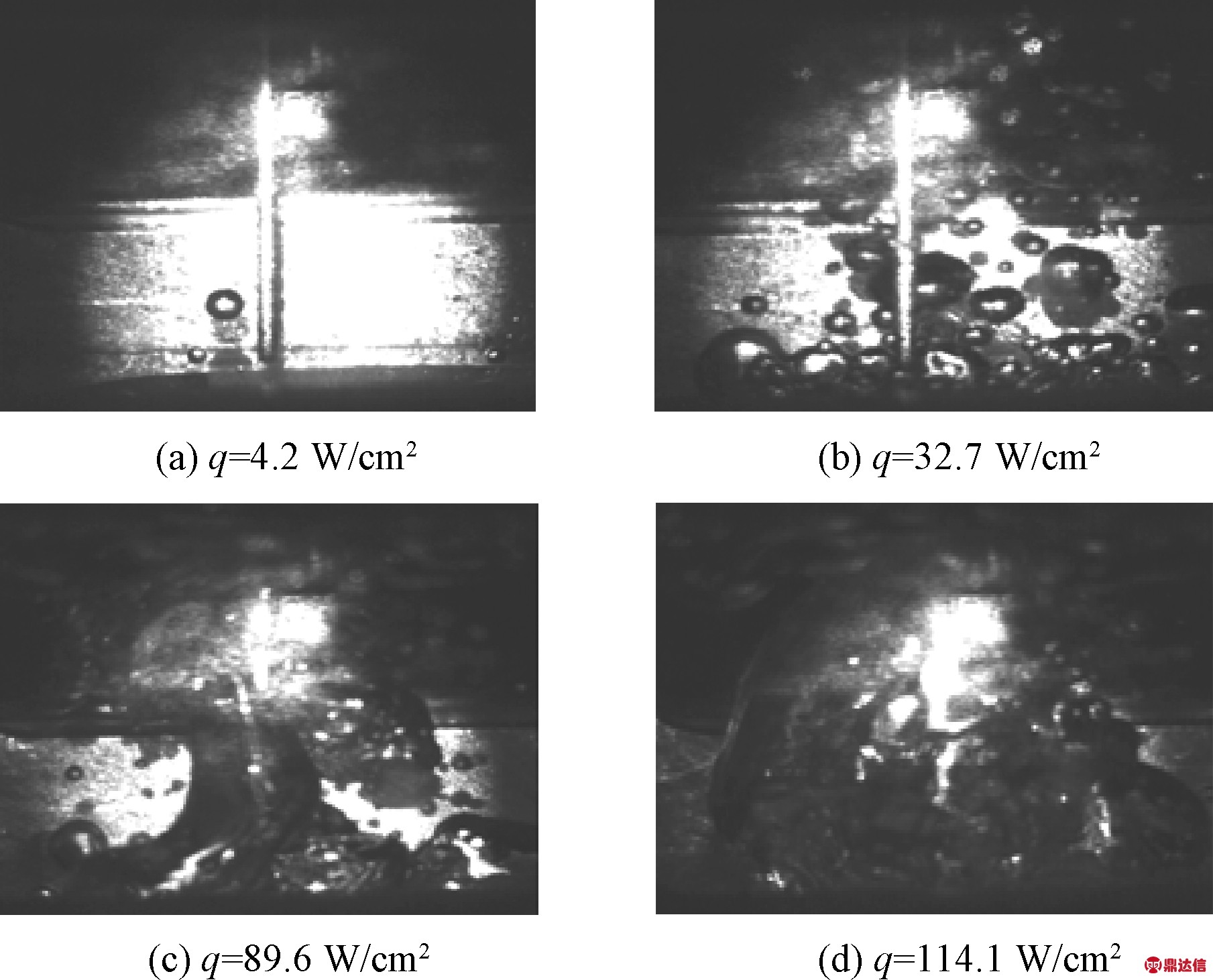
图4 光滑表面汽泡生长图像
Fig.4 Boiling patterns on the smooth surface
起始沸腾点:当热流密度约为4.2W/cm2时,光滑表面温度约为108℃时,光滑表面某些位置上有汽泡产生,并且有些汽泡向加热面中心方向稍微滑移后才离开加热表面.此时泡沫铜表面的温度约为105℃,并且汽泡的数量多,分布较密集,因此出现了图3(a)40PPI沸腾曲线的起始点左移的现象.
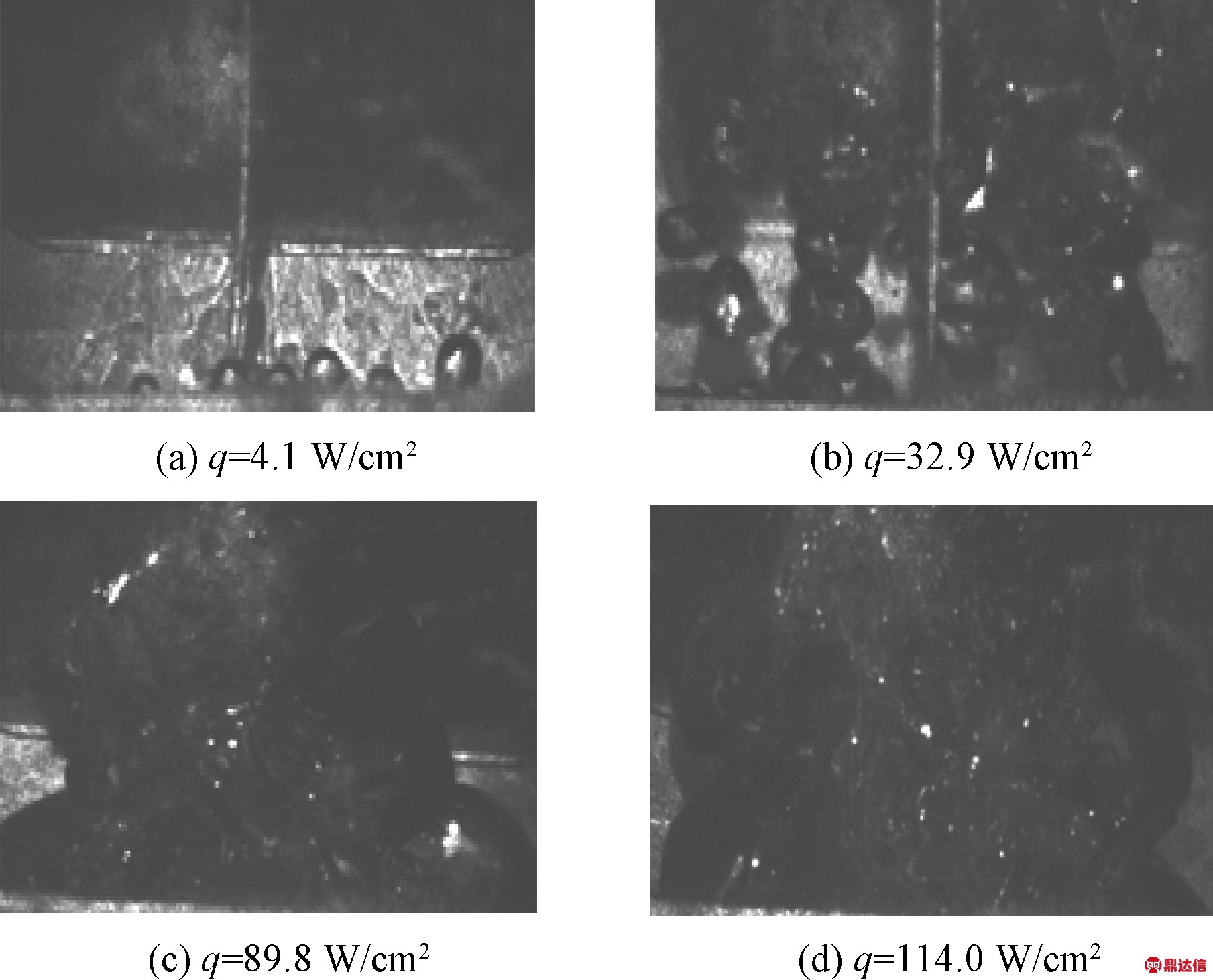
图5 40PPI泡沫铜汽泡生长图像
Fig.5 Boiling patterns on the 40PPI copper foam surface
孤立汽泡阶段:当热流密度达到32.7W/cm2时,光滑表面上出现了大量汽泡,但是汽泡的位置点杂乱无章.泡沫铜在此热流密度下生成的汽泡相对规则,主要由于汽泡在泡沫铜内部生成并向上移动的过程中,汽泡不断的接收能量,直径不断增加,但是不断的被金属骨架粉碎,因此金属孔径的大小限制了汽泡的大小,并且汽泡从泡沫铜某些汽化核心点像火焰一样喷发而出,汽泡的脱离频率远远大于光滑表面,汽泡的总体积远远大于光滑表面汽泡的总体积,这很好地解释了图3(b)中该阶段泡沫铜的沸腾换热系数远远大于光滑表面的换热系数.
汽泡合并阶段:当热流密度达到89.6 W/cm2时,汽泡在上升的过程中扰动剧烈,导致汽泡的脱离频率变快,加热壁面上的小汽泡横向合并成大汽泡,光滑表面出现了比较明显的蘑菇状蒸汽泡,而泡沫铜表面出现的是蒸汽块.当热流密度达到114.1 W/cm2时,光滑表面上的汽泡在上升的过程中也出现合并,逐渐在加热面上形成蒸汽柱.而泡沫铜表面上是大量的蒸汽块,并且在上升过程中有少量合并.通过图4、5发现在汽泡合并阶段,相对于光滑表面,金属铜泡沫表面汽泡的总体积大的优势越来越不明显,这很好的解释了图3(b)中:在高热流密度下,泡沫铜的强化沸腾换热性能并不明显.由于泡沫铜表面产生的汽泡较多,为了拍摄泡沫铜表面汽泡的全景图,激光的照射范围调大了,所以出现了泡沫铜表面汽泡图像偏暗.
2.3 压力对泡沫铜表面沸腾换热性能的影响
图6分别给出了光滑表面和不同孔密度泡沫铜在压力70、101、143 kPa下的沸腾换热系数曲线,图6表明光滑表面的换热系数和临界热流密度均随压力的增大而提高,其中光滑壁面在143 kPa和70 kPa下的临界热流密度比值为1.20,换热系数的比值在热流密度为13.1W/cm2达到最大值1.31.但泡沫铜的沸腾换热性能并不是单一的随压力变化而变化,不同孔密度泡沫铜对压力变化的敏感程度是不一样的,在试验参数测试范围内,10PPI的泡沫铜的沸腾换热性能随压力变化而变化的趋势和光滑表面比较接近,40PPI的泡沫铜对压力的变化表现不敏感,但是70PPI的泡沫铜沸腾换热性能随压力变化而变化的趋势和光滑表面相反,压力越高,70PPI的泡沫铜在热流密度超过20 W/cm2时,沸腾换热性能反而下降,相对于70PPI,100PPI泡沫铜沸腾换热性能下降趋势更为明显,其中100PPI泡沫铜在70、143 kPa下的临界热流密度比值为1.14,换热系数的比值在热流密度为109.0W/cm2达到最大值1.32,对于这种现象的原因可能是:随着压力的提高,一些潜在的汽化核心点被激化,因此光滑表面的换热系数和临界热流密度均随压力的增大而提高.而对于孔径比较小的泡沫铜,当汽化核心点数目增加到一定数量时,汽泡容易在金属骨架内堵塞,新鲜的液体不能及时补充到金属骨架内部,因此恶化了其沸腾换热性能.
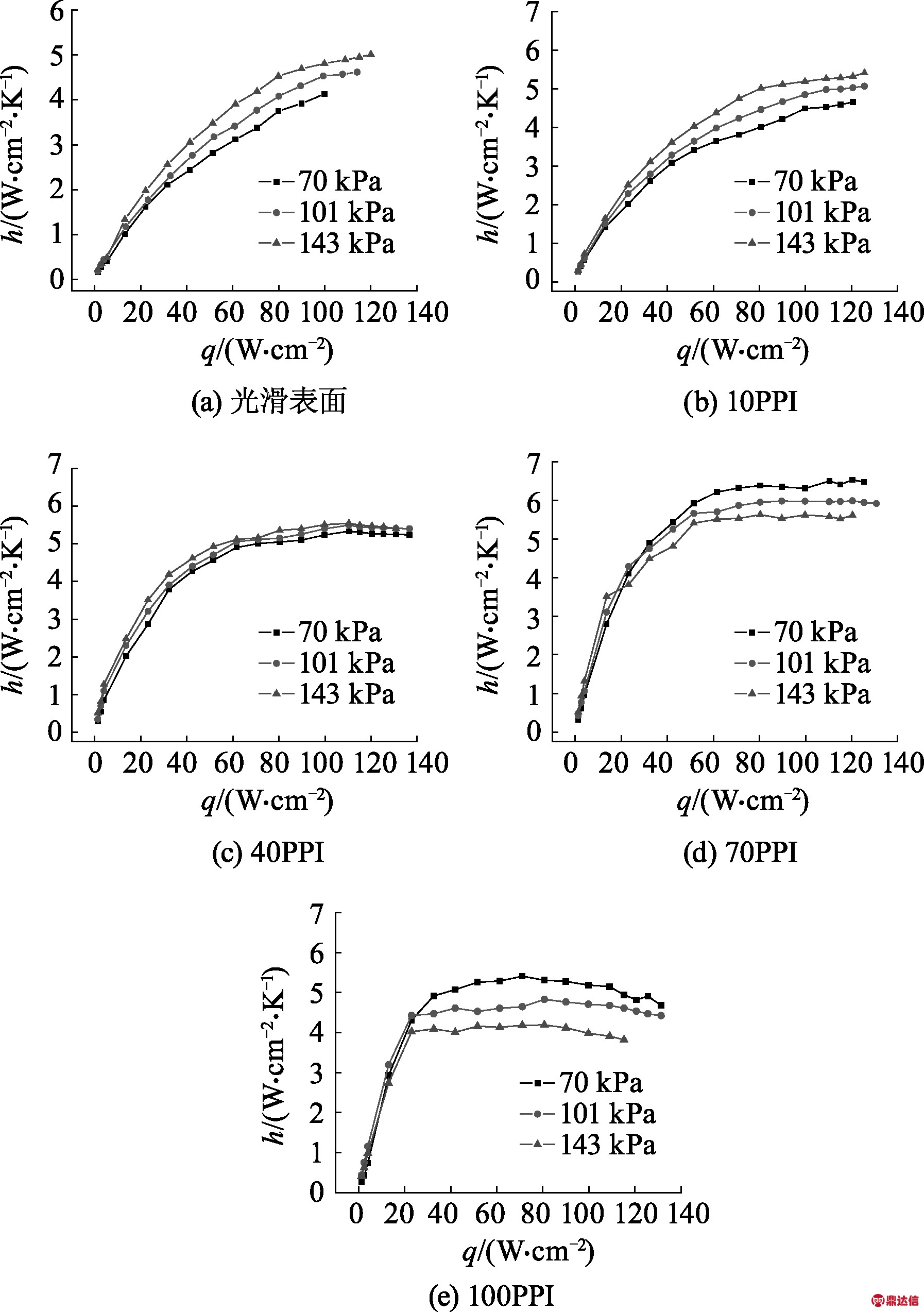
图6 不同压力下泡沫铜的沸腾换热系数曲线
Fig.6 Boiling heat transfer coefficient curves of copper foams under different pressures
2.4 文中试验结果与其他文献的比较
图7为光滑表面试验结果与前人的实验结果对比的折线,从图中可以看出文中的试验数据与文献[12-13]的试验数据比较相近,尤其当热流密度处于40~100W/cm2,文中的试验曲线几乎和文献[12]中的曲线重合,但是在高热流密度时,稍有不同,并且临界热流密度低于文献[12-13]中临界热流密度.文献[12-13]中所用的加热表面都小于文中试验所用的加热表面,因此文中试验测定的临界热流密度小于他们测定的临界热流密度是合理的.
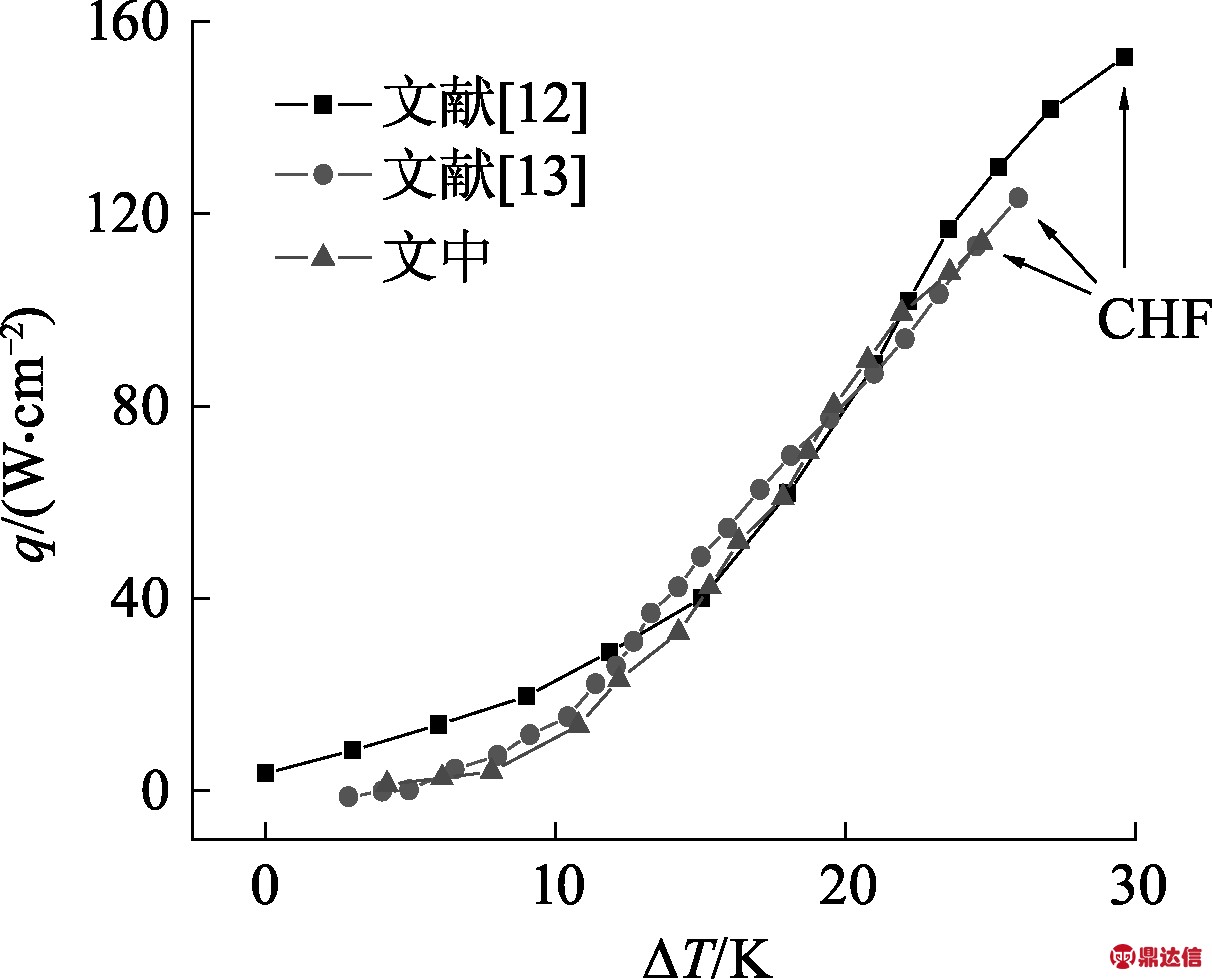
图7 光滑表面沸腾换热曲线
Fig.7 Boiling curves of smooth surface
其次是加热表面的特性(材质,粗糙度和润湿性)的不同;再次是试验台架的其他因素(如工质中的含气量、系统内压力和加热铜柱的取值等)的不同,热电偶的布置位置和精度的不同.
文献[5]中在一个大气压下探究了孔密度分别为30PPI、60PPI和90PPI的泡沫铜在不同过冷度下的沸腾换热性能,当过冷度为0时,在试验参数范围内,泡沫铜的沸腾换热性能随孔密度的增加先增大后减小,与本文的试验结果相同,并且文中试验100PPI的泡沫铜在高热流密度区沸腾换热能力恶化,文献[5]中90PPI泡沫铜的沸腾换热性能在高热流密度区也出现恶化现象.
3 结论
(1) 泡沫铜在低热流密度区强化沸腾换热显著,并且起始沸腾点所需的过热度比光滑表面低3~4℃,在较高热流密度下,泡沫铜强化沸腾换热的能力并不明显.在试验参数范围内,泡沫铜的沸腾换热能力随孔密度的增大先增强后减弱.
(2) 高孔密度泡沫铜的沸腾换热性能随压力的升高而降低,低孔密度泡沫铜的沸腾换热性能随压力的变化和光滑表面比较接近.
(3) 在一定热流密度下,泡沫铜表面的汽泡像火焰喷出,呈串珠状,而光滑表面的汽泡是杂乱无章的.单从泡沫铜表面无法看出泡沫铜表面汽泡之间明显的区别,需进一步探究泡沫铜内部汽泡的成长模式.