【摘 要】通过对真空调节阀控制精度和高温工况问题的引入和讨论,展开了基于步进电动机驱动控制系统的真空调节阀的设计和实现方法的研究。介绍了真空调节阀的工况及设计要求。并通过详细的结构设计和驱动装置的软硬件开发,实现了步进电动机在真空调节阀领域中的应用,解决了控制精度和高温工况的问题。
【关键字】真空阀 调节阀 步进电动机 机电一体化
一、前言
步进电动机广泛应用于数控机床、航空航天、工业机器人等对工况要求较高的场合,是一种专门用于速度和位置精确控制的特种电动机。由于步进电动机不需要位置传感器或速度传感器便可以在开环状态定位或同步运行,因而在众多领域得到广泛的应用。
立足于DN65真空调节阀的设计与实现,通过引入步进电动机驱动控制系统作为这类真空调节阀的驱动装置,详细阐述阀门和步进电动机驱动控制系统的一体化设计研究,提供这类精密控制用耐温真空调节阀的解决方案。
二、设计背景
DN65真空调节阀是主要应用于铀浓缩厂供料系统中的压力调节阀。在供料系统管路中,工作物质通过供料装置加热蒸发后,经过调节阀的减压、调节,使调节阀后气体保持恒力,从而达到控制物料流量为恒定的目的。
在控制回路中,DN65真空调节阀处于一个单回路反馈控制系统,它是执行元件,又是自控系统中的控制元件,同时也是工艺管路系统中的阀门。测量仪表测定出阀后压力的变化ym,将测量值与要求设定值ysp进行比较,得出偏差值ε=ym-ysp,将偏差值送给系统调节器,调节器根据此偏差和预先给定的控制规律决定控制变化的应调量,送到调节阀执行机构,使调节阀开关,控制流经阀体的工作介质流量,达到稳定供料压力的作用。而在特定情况下,真空调节阀收到系统的紧急关闭信号在2s内执行紧急关闭功能,即为一个切断阀。
DN65真空调节阀主要设计要求如下:工作介质为UF气体和微量HF,工作压力为0.02~0.095MPa,工作温度为50~100℃,环境温度为100℃,具有调节功能和切断功能,阀体最大漏率≤1×10-7Pa·L/s,阀杆最大漏率≤1×10-6Pa·L/s,阀座最大漏率≤1×10-4Pa·L/s,紧急关闭时间1~2s,流量系数Kv为0.087~1.75,流量特性为等百分比,基本误差限为±4%,死区为1%,回差为3%,额定行程偏差为2.5%,整机寿命为20 000次,阀体结构为直角式、法兰连接,控制信号为DC0~10V。
为避免物料冷凝固化,整个真空工艺管线都处在80~100℃保温环境内。对于传统的电动调节阀,其控制单元的电子元件无法适应长时间在此环境温度下工作。同时,既要保持控制精度达到1%的同时,又要满足1~2s内快速关闭阀门作为切断阀功能,传统电动调节阀不能适应这类控制阀的精密控制。
因此,引入步进电动机控制驱动技术,选用耐温步进电动机与阀门一起安装在保温箱内,将其控制驱动器置于保温箱外,实现驱动机构的分体设计,满足高环境温度的工况要求。同时,步进电动机的步距角细分控制,可保证阀门控制精度的要求。通过阀杆的力矩控制可以保证切断功能阀座的密封性能。
三、阀门结构设计
1.阀门机构原理
由于步进电动机输出轴只做旋转运动,同时需要符合调节功能和快关功能,因此,在机构设计上利用螺纹副将角位移转换为直行程位移,同时设置调节阀座和切断阀芯双阀座阀芯形式将功能分隔。
如图1所示,DN65真空调节阀门顶部安装步进电动机,电动机通过联轴器与行程套相连,行程套与阀杆传动轴通过螺纹副连接,将角位移转换为直行程。阀杆传动轴推动阀芯相对与阀座运动,调节介质流量和阀后压力,形成阀门的调节和切断功能。其中,行程套、弹簧和行程开关组成力矩控制部件,用于精确控制阀门启闭过程中的力矩范围。
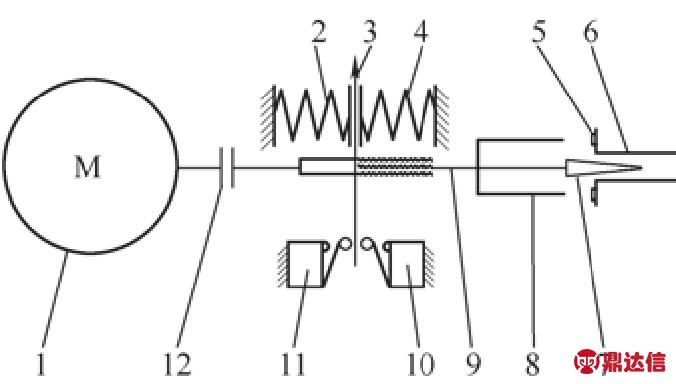
图1 阀门机构原理
1.电动机 2.弹簧1 3.行程套 4.弹簧2 5.切断阀座 6.调节阀座7.调节阀芯 8.切断阀芯 9.阀杆传动轴 10.行程开关2 11.行程开关1 12.联轴器
2.总体结构
DN65真空调节阀在正常工况中仅为调节作用,而在系统发生紧急工况下或检修要求时需要执行快速切断功能,并保证阀座密封。
该阀是一种角式真空耐压波纹管调节阀。它包括阀体,阀体上设有阀的下盖和上盖,步进电动机在上盖的顶部。阀体的内部设有阀座、密封圈、波纹管组件、阀杆和阀芯。阀体和波纹管组件之间设有垫片,形成一个承压结构。阀杆和波纹管组件的下接环通过螺纹连接后推动阀芯运动,并通过弹簧复位,阀芯是调节阀的功能组件,直接决定了阀门的工作性能。上盖和下盖的内部是行程套组件,当阀门内件运动到极限位置产生的反力可以克服弹簧预紧力,即可触动行程开关,向控制器反馈信号。
3.双阀座阀芯结构
DN65真空调节阀采用密封、节流功能分离式的设计。阀杆驱动轴推动调节阀芯和切断阀芯向调节阀座和切断阀座运动过程中,切断密封行程大于调节功能的行程,在调节阀芯和调节阀座节流行程内,阀门将执行正常调节功能。当阀杆驱动轴进一步推动双阀芯向双阀座移动时,调节阀芯离开调节阀位,切断阀芯接触到切断阀座时,此时阀门执行切断功能。
节流功能由调节阀芯和调节阀座的节流面实现,可通过对调节阀芯节流型面的调整来获得流量特性曲线,满足不同工艺系统对阀门调节的要求。
密封功能由切断阀芯和切断阀座来实现。对于真空工况下的气体密封,采用刀口密封形式,切断阀座采用软垫片(PTFE材料),切断阀芯形式为刀口密封形式,控制密封比压,实现优异的密封性能和高寿命。
4.力矩控制
DN65真空调节阀调节过程中阻力低,阀杆传动轴力矩低,而切断功能又要求控制精确的力矩既提供预设的密封比压,又控制力矩不宜过大造成密封面压溃。在阀门传动机构中设计了力矩控制单元。力矩控制单元由行程套、两个行程开关和两组弹簧组成。
因此将阀杆全行程分解为三段:调节阶段、阀门关闭阶段和全开阶段。
阀杆力矩计算式为:

式中d2——外螺纹中径;
F——阀杆上的总作用力;
λ——螺纹螺旋升角;
ρ′——当量摩擦角。
对于已确定的阀杆直径和螺纹尺寸,d2、λ和ρ′都是常量,那么要求得三个阶段的阀杆力矩,即需分别求得各个阶段的阀杆总轴向力。
(1)调节阶段的阀杆力矩 在调节阶段,总轴向力可表达为:

式中Fs——阀芯弹簧作用力;
Fb——波纹管作用力;
fo——O形圈摩擦力;
fk——键摩擦力;
f——阀芯动作摩擦力,可忽略。
带入式(1)即可求得调节阶段的阀杆总力矩:

(2)关闭阶段的阀杆力矩 在关闭阶段,总轴向力可表达为:

式中Fmf——阀座密封力;
Fs——阀芯弹簧作用力;
Fb——波纹管作用力;
fo——O形圈摩擦力;
fk——键摩擦力;
f——阀芯动作摩擦力,可忽略。
刀口密封阀座密封力可由下式确定:
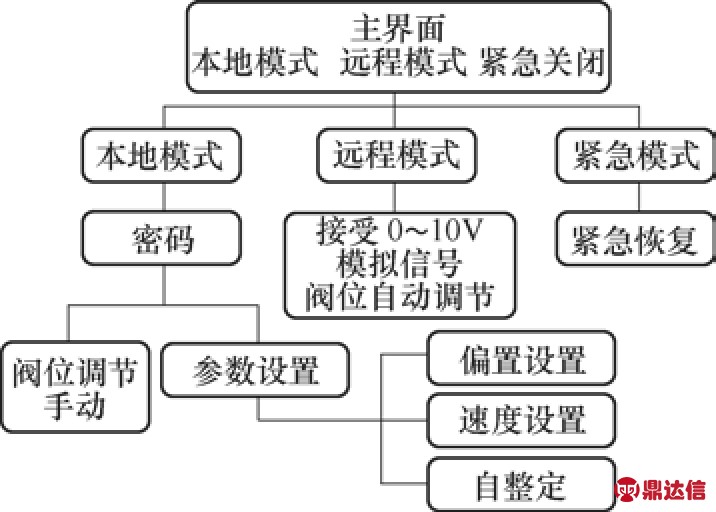
式中 D——阀座刀口密封圆直径;
q——垫片线密封比压。
带入式(1)即可求得关闭阶段的阀杆总力矩:

(3)全开阶段的力矩 全开后阀芯受到限位而使阀杆力矩逐渐增大,但没有限制要求,因此为简化设计,将全开位置阀杆力矩等同于关闭位置的阀杆力矩,即全开位置的阀杆力矩为:

(4)力矩控制的实现
1)力矩控制机理。阀门上下盖内设计了行程套组件,用于反馈行程力矩。行程套受到两端弹簧预压力保持平衡。当阀门处于关闭阶段或全开阶段时,由于两端限位,电动机继续运转会使阀杆力矩不断增加,力矩通过螺纹副装换为行程套上的推力。推力增加到一定程度时,克服弹簧阻力压缩对应的弹簧,行程套发生位移并触发相应的行程开关,反馈信号停止电动机,力矩被限制。通过设定弹簧压缩量使阀杆力矩能够控制在一个预定的设计范围内,实现阀门力矩的精确控制。
2)弹簧的设计。通过上述分析,弹簧的压缩力应根据三个阶段的阀杆总轴向力进行划分。由于关闭和全开阶段的阀杆力矩值相等,则上下两个弹簧可以等价的设计。
设计应满足如下要求:①弹簧应进行预压xmm,保证没有行程间隙,这可以控制阀门死区和回差。②弹簧预压xmm产生的力≥调节阶段的阀杆总轴向力。③弹簧压缩ymm产生的力=关闭阶段或全开阶段的阀杆总轴向力(y为触发限位开关的移动距离)。
由此,可得出关于弹簧刚度k的方程组:

由此可解出弹簧的设计刚度k,根据k可进行弹簧的设计。
3)力矩设置方法。通过上述理论分析和计算,确定了阀门各个阶段的力矩值以及弹簧的压缩量和行程开关的动作位移。为避免实际和理论误差造成力矩控制的不精确,在控制程序中设置了用户接口进行弹簧压缩量的调整。在实际制造中,阀门总成后,用力矩扳手根据值进行阀杆力矩加载,然后测量行程套指示板的位移,将此位移输入到程序“偏置”设置中即可。
四、驱动装置
1.驱动装置分体式设计
真空调节阀门工作环境温度在80~100℃,一般的工业用电动调节阀一体式执行机构会随着时间的推移,其内部大部分芯片和电子元件因高温老化而失效,因此不能适应长期在此温度下的正常工作。真空调节阀采用分体式设计,将电动机和控制器分开:选择耐温电动机保留在阀门本体上,而控制器通过电缆放置在远端常温环境内。
行程开关选择耐温、触感灵敏的单刀双掷机械开关。电缆使用耐高温聚四氟乙烯电缆。
2.控制精度
引入步进电动机用于控制阀门的好处在于其可控的开环高精度。步进电动机的角位移量和输入脉冲的个数严格成正比,在时间上与输入脉冲同步,因此只要控制输入脉冲的数量、频率及电动机绕组通电顺序,便可获得所需的转角、转速及转动方向。无脉冲输入时,在绕组电源的激励下,磁场使转子保持原有定位状态。步进电动机驱动原理如图2所示。
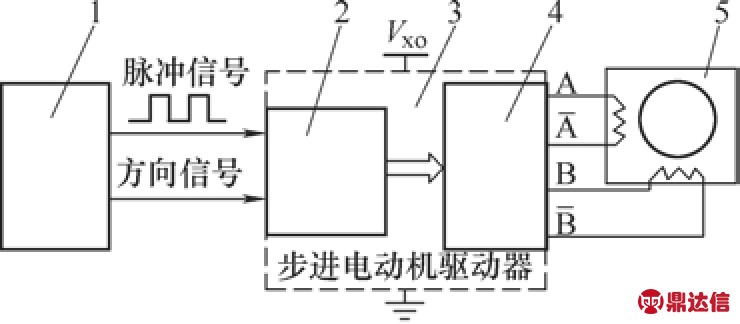
图2 步进电动机驱动原理
1.控制器 2.环形分配器细分电路 3.步进电动机驱动器4.功率放大器 5.步进电动机
一般电动机步距角为1.8°,而如果选用驱动控制器可达到最小细分角度为0.007°,对于阀门应用这个精度已经远远高于要求。因此,引入步进电动机可以实现精确的开环控制,弥补并解决了因精简阀门自身控制元件而导致控制精度降低的不利因素。
2.软硬件开发
(1)控制逻辑与功能设置 真空调节阀处于一个单回路反馈控制系统,在控制系统中它是执行元件,又是自控系统中的控制件,同时也是工艺管路系统中的阀门。控制上提供就地操作和远程操作。就地操作提供操作员对阀门的调试、诊断和紧急关闭的功能;远程操作提供系统4~20mA/0~10V标准信号的输入和输出对阀位进行控制。
主要功能划分如下:
1)本地模式(就地手动操作方式,调节阀位)。
2)远程模式(系统自动控制方式,调节阀位)。
3)紧急关闭功能(该功能为2s内切断阀门)。
4)基本设定功能(提供控制器基本参数设定)。
根据上述阀门结构和力矩单元的设计,同时又考虑到阀位控制本身为一个开环控制,长期工作可能会因为步进电动机的失步或过冲导致位置不精确。所以设计在开机或触发全开和全关限位开关时都执行自整定功能。自整定功能是根据产品出厂时根据力矩单元弹簧预压缩量而进行的阀位自动找零的功能。
控制逻辑与功能设置如图3所示。
(2)软硬件开发 一般选购步进电动机时,厂商会同时推荐一款驱动器用于脉冲信号的细分和功率放大。为真空调节阀选择步进电动机时,考虑电动机的耐温性、步距角、矩频特性、起动转矩、驱动器的升降调速功能以及细分功能等。
在进行控制驱动器硬件选型时,CPU有许多选择,单片机、PLC等都是广泛应用的低成本硬件。A/D和D/ A转换器精度的选择,影响了模拟信号和数字信号的转换精度,直接影响步进电动机作为数字化电动机的最小转角和运行稳定性。I/O接口、人机界面可以根据不同的需求进行选择。光电隔离模块可以有效避免干扰,增强系统的稳定性。
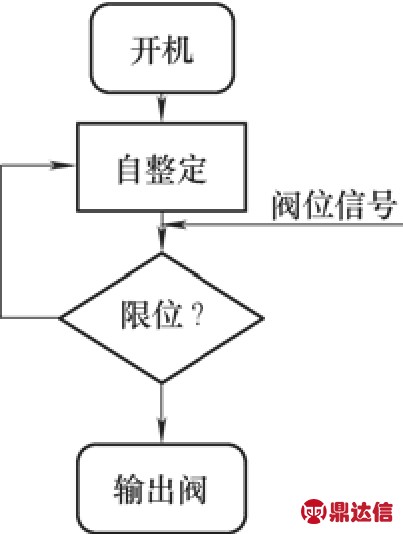
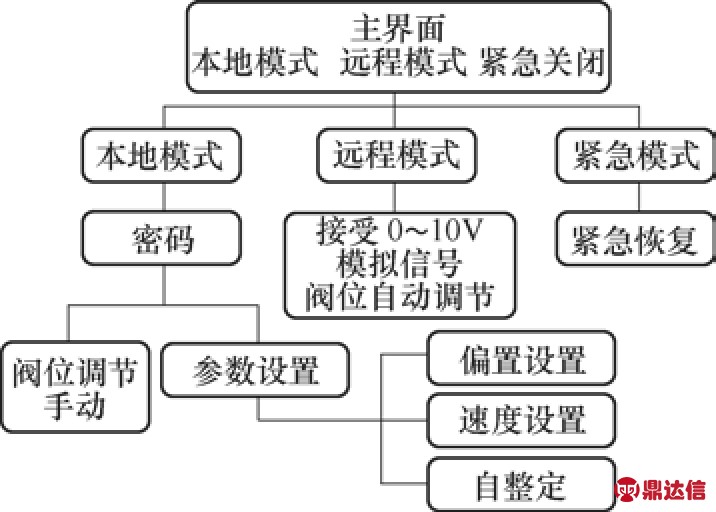
图3 控制逻辑与功能设置
本项目中进行硬件选型如图4所示:Phytron公司的耐温步进电动机、Trinamic驱动控制器、Baldor公司集成控制卡和Eview触摸屏作为主要硬件。Baldor公司的集成控制卡集成了驱动器、A/D或D/A、开关以及触摸屏等接口,和Eview触摸屏也已自带了通信协议,减少了接口匹配的工作量。
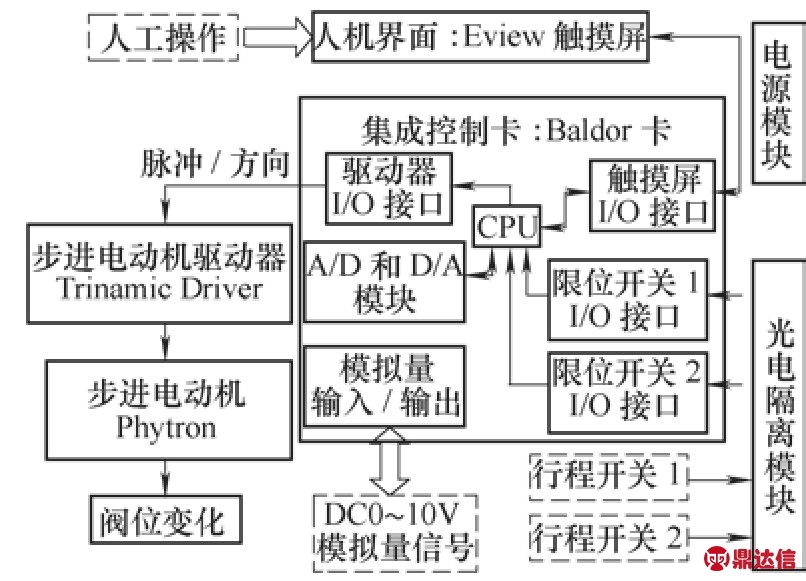
图4 步进电动机驱动原理
软件开发方面,Baldor卡基于C++的主程序开发,由于采样频率为2kHz,为了避免步进电动机来回振荡,在主程序中可采取必要的软件滤波方式进行平均化和延时处理。同时,软件开发给用户留有设置接口,包括电动机的运行速度、自整定的设置等。Eview触摸屏提供良好的人机交互平台,可视化的操作以及密码权限的分配可避免现场的误操作,保证运行安全。
五、产品试验
通过设计样机的制造,并完成对样机的系列试验,包括性能试验、流量特性试验、静特性试验、寿命试验、耐温试验以及工况试验等,该基于步进电动机驱动控制系统的真空调节阀表现出稳定优异的性能,能够完全满足使用工况的要求。
其中阀门静特性试验结果:基本误差1.67%,回差0.83%,死区1.00%,额定行程偏差1.67%。在20 000次寿命试验后,样机仍可以保持良好的精度控制。同时,在热态环境试验中,样机在精确力矩控制下保持了良好的密封性能,关闭状态真空密封试验漏率为3×10-5Pa·L/s,各项试验参数都满足工况要求。
六、结语
通过对真空调节阀控制精度和耐温工况的问题引入,展开了基于步进电动机驱动控制系统的真空调节阀的研究。并通过详细结构设计和软硬件的开发,实现了步进电动机在真空调节阀领域中的应用。最后通过样机的制造,完成系列试验,验证了真空调节阀能够满足工况的使用要求。
充分运用了数字化精密控制的概念,提供了步进电动机驱动阀门产品的原型,今后通过二次开发,可广泛应用于其他各类控制阀和切断类阀门,拓展阀门机电一体化的应用领域。