摘要: 为探索轴流泵机组起动过程中外特性参数和机组流道内流态的瞬变特性,建立了包括肘型进水流道、转轮、导叶、虹吸式出水流道与出水池等部件的轴流泵机组三维几何模型,采用VOF气液两相流模型与Realizable k-ε湍流模型相结合的方法,对预开启真空破坏阀及真空破坏阀保持关闭这2种起动方式下的轴流泵机组起动过程进行了三维数值模拟.数值模拟结果显示,水流翻越驼峰之后,出水流道内的空气不断被卷入水中并由下降段流道内的水流旋涡携带排出,出水流道内空气囊体积逐渐减小,从而最终形成虹吸;初始空气囊大小是影响起动过程中排气时间长短的关键因素之一,初始空气囊体积越大,排出气囊所需时间越长,而采用真空破坏阀保持关闭的起动方式会产生较大的初始空气囊,因而起动时间较长;与真空破坏阀保持关闭的起动方法相比,采用预开启真空破坏阀的方法使最大起动扬程下降了30%,起动时间缩短了64%.
关键词: 轴流泵机组;虹吸式出水流道;起动过程;VOF 模型;三维数值模拟
周大庆, 刘跃飞. 基于VOF模型的轴流泵机组起动过程数值模拟[J]. 排灌机械工程学报,2016,34(4):307-312.
ZHOU Daqing, LIU Yuefei. Numerical simulation of axial pump unit startup process using VOF model[J]. Journal of drainage and irrigation machinery engineering(JDIME), 2016,34(4):307-312.(in Chinese)
three-dimensional numerical simulation
虹吸式出水流道以其停机断流方便可靠的优点广泛应用于各类轴流泵机组[1],但是采用这类流道轴流泵机组起动时,由于需要下游水位翻过虹吸管驼峰才能形成虹吸抽水,因而起动扬程高,起动时间长,若虹吸出水流道设计不合理,易引起机组的剧烈振动,甚至导致机组起动失败[2].通常此类轴流泵机组开机前需要预抽真空从而减小起动扬程,但是,抽真空装置造价较高,在实际应用中对减小扬程和振动的效果并不理想[3].现在有不少轴流泵机组在起动过程中采用预开启真空破坏阀的方式:起动水泵前,预先打开真空破坏阀,在水流翻过驼峰后,再手动关闭真空破坏阀,通过降低虹吸管内空气受压缩程度,较大幅度地降低了最大起动扬程.
目前常用的针对泵机组的数值模拟研究较多,主要集中在:针对轴流泵机组结构构建数学模型和数学方程式求解轴流泵机组起动过程中流量、扬程、气压等数据[4-5];对虹吸管及带虹吸式出水流道轴流泵机组稳态工况水力特性进行三维数值模拟并进行分析[6-8];考虑重力影响,对抽蓄机组全过流系统开展泵工况三维计算[9];利用欧拉多相流模型针对虹吸式出水管对虹吸形成过程进行三维气液两相数值模拟[10];针对离心泵的起动过程作气液两相流的三维数值模拟[11-12];而对具有虹吸式出水流道轴流泵整体机组起动过程进行的三维数值模拟却鲜见报道.
文中在前人研究的基础上利用适合追踪气液自由表面的VOF多相流模型对预开启真空破坏阀及真空破坏阀保持关闭的轴流泵机组起动过程进行三维数值模拟,获得虹吸式出水流道中气囊的演变过程和轴流泵机组的各项参数,并针对转轮叶片压力变化及气囊的排出机理进行分析.
1 数值计算模型
1.1 模型参数
文中计算模型基于某抽水站轴流泵机组.机组参数为转轮直径3.1 m,转动惯量J=2 330.42 kg·m2,转轮叶片数4,导叶数5,单机流量30 m3/s,设计扬程4.15 m,配套电动机额定功率为2 000 kW,额定转速为125 r/min.计算模型与轴流泵机组实际尺寸比例为1 ∶1,包含肘型进水流道、转轮区、导叶区、虹吸式出水流道、出水池等部件,结构如图1所示,真空破坏阀布置在虹吸式出水流道顶部.为监测出水流道虹顶处压力,设置压力测点,测点位于真空破坏阀出口下方0.6 m处.
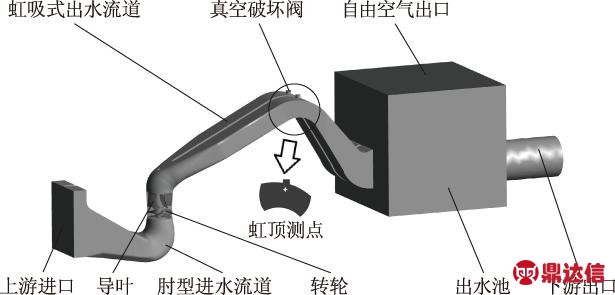
图1 轴流泵机组几何模型
Fig.1 Geometrical model of axial pump unit
1.2 网格
采用非结构化网格来划分进水流道、转轮、导叶和出水流道;采用局部函数方法对出水池进行网格划分以减少网格数量;由于转轮区和导叶区流态复杂,对其进行网格加密.不同网格划分方案如表1所示.经网格无关性验证计算,发现网格超过一定数量后计算结果对机组性能影响很小,最终选择方案3来划分计算模型.
表1 不同网格划分方案
Tab.1 Results of different meshing programs

2 三维过渡过程计算方法
2.1 控制方程与湍流模型
在VOF模型中,通过求解水和空气的体积分数连续方程追踪虹吸管内空气囊与水的界面,求解控制方程获得的速度场由各相共享,本次模拟中水为主相.
体积分数连续方程
α1=0,
(1)
α2=0,
(2)
连续性方程
·(ρu)=0,
(3)
动量方程
)u=-
p+
·[μ(
u+
uT)]+ρg+F,
(4)式中:α1和α2分别为水和空气的体积分数,α1+α2=1;ρ为密度;μ为动力黏度系数;t为时间;u为速度;为哈密顿算子;p为静压强;g为重力加速度;F为表面张力的等价体积力形式.
等物质属性参数是由控制体积中的分相决定的,其表达式分别为
ρ=α1ρ1+α2ρ2,
(5)
μ=α1μ1+α2μ2,
(6)
式中:ρ1和ρ2分别为水和空气的密度;μ1和μ2分别为水和空气的动力黏度系数.
Realizable k-ε模型由于采用了新的湍流黏度公式,使其满足对雷诺应力的约束条件,因此在雷诺应力上保持与真实湍流一致,因此已被有效地应用于各种不同类型的流动模拟,包括旋转均匀剪切流、包含有射流和混合流的自由流动、管道流动、边界层流动和带有分离的流动等[13].轴流泵机组起动过程中气液两相的运动规律变化剧烈,因此文中选用Realizable k-ε湍流模型封闭控制方程组.
2.2 离散格式及定解条件
本次数值计算利用Fluent 6.3软件完成,用有限体积法对上述数学模型进行离散,压力项采用PRESTO格式,体积分数项采用Geo-Reconstruct格式,湍动能和对流项采用一阶迎风格式,采用适合瞬态计算的PISO算法对流场速度压力进行求解,数值计算时间步长为0.01 s,初始时间为0.
定解条件为上游进口采用压力进口条件,压力值由进口水位确定,下游出口均采用速度入口条件,随机组的流量变化以保持出水池水面稳定;出水池水面采用压力出口条件,压力值为0;初始时刻,出水流道与出水池上部为空气(水面位置由上下游水位决定),故初始条件设出水流道和出水池上部区域空气体积分数为1,其他区域空气体积分数为0.出水流道内的气体采用Ideal-gas模型,遵循理想气体状态方程.
2.3 转轮转速控制及真空破坏阀边界条件
利用滑移网格技术实现转轮的旋转,通过编制用户自定义程序(UDF)控制转速为根据现场实测资料,转速从0开始按如图2所示规律上升,用时5 s至额定转速125 r/min.图中Fz为转轮叶片轴向力,M为转轮叶片转矩,p为虹顶测点压强,s为转轮转速与额定转速比值.在水泵起动之前,真空破坏阀处于开启状态,设置为压力出口,压力为0.当水流充满出水流道上升段翻过驼峰时,真空破坏阀关闭,设置真空破坏阀出口处边界条件为壁面,一直保持至起动过程结束.
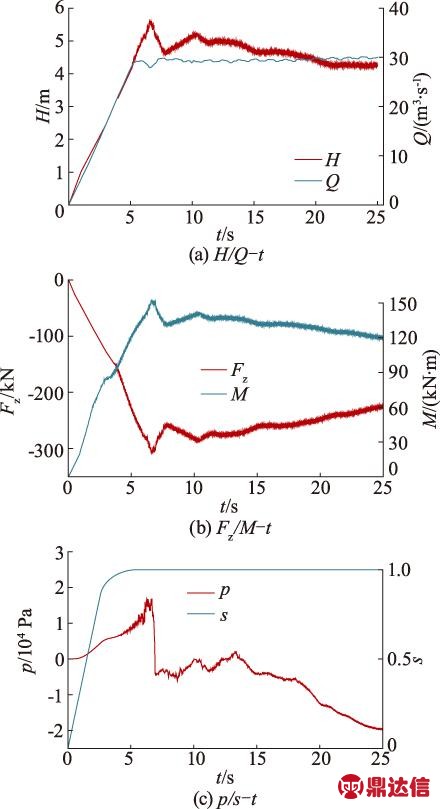
图2 起动过程各参数随时间变化曲线
Fig.2 Variations of typical parameters during
start-up process
3 预开启真空破坏阀起动过程
3.1 起动过程分析
真空破坏阀初始状态为开启,在6 s时,水流翻过驼峰,真空破坏阀关闭.整个起动过程的气液两相分布状态如图3所示,图中δ为空气体积分数.

图3 预开启真空破坏阀起动过程流态图
Fig.3 Profiles of pump with vacuum breaker valve
open in advance during start-up process
机组转速在5 s内增大至额定转速,前5 s内,水面平稳上升,出水流道内空气被压缩,因真空破坏阀为开启状态,空气从真空破坏阀排出,出水流道下降段水位仍由于空气压力增大而略有降低.在6 s时水流越过驼峰与出水流道下降段内水流交汇,此时真空破坏阀关闭.真空破坏阀关闭之后空气无法从真空破坏阀排出,如图3中t=10 s所示,空气在水流的作用下在出水流道下降段上部聚集,形成空气囊.在气囊形成之后,起动过程进入排除气囊阶段,气囊分离出大量气泡,通过水流作用将气泡从出水流道排至出水池.从图3可见,在这一阶段,出水流道下降段后端出现大量气泡从气囊分离出来,且随着排气过程的进行,气囊的体积逐渐缩小,气囊位置逐渐下移,且气囊后气泡数量逐渐减少直至气囊完全排出.在25 s时,空气囊完全排出,虹吸式出水流道形成满管流,虹吸效应完全形成,起动过程结束,机组进入正常运行阶段.
由图2可知,机组起动之后,转速在5 s内逐步升高至额定转速,流量和扬程逐步增大,叶片轴向力和转矩的大小随之增大.同时,出水流道上升段水面逐步升高,压缩虹顶空气,空气压力随之上升.6 s时真空破坏阀关闭,由于虹吸效应的作用,出水流道虹顶处迅速从正压变为负压,如图2c所示,水泵的工作扬程迅速下降,流量增加,叶片轴向力和转矩的大小也随之降低.真空破坏阀关闭之后,6-25 s为排出气囊阶段,大量气泡产生,随着气泡在出水流道内运输、溃灭,各参数出现明显波动.随着排气过程的进行,气囊体积变小,气泡数量减少,各参数波动幅度随之减小.
本次数值模拟,机组在25 s进入正常运行工况,此时机组的流量、扬程、出力与抽水站额定工况下的运行参数吻合较好.刘梅清等[1]利用数学模型计算得到最大起动扬程为额定扬程的1.25倍,虹顶最大压强为1.8×104 Pa水柱,而本次数值模拟中,最大起动扬程为5.54 m,是额定扬程的1.31倍,虹顶最大压强为1.47×104 Pa,因水泵装置不同与该文献数据有所差异,但结果具有一定可比性.可见文中的数值模拟方法具有较高的准确性,可为具有虹吸式出水流道的轴流泵机组的起动过程分析提供参考.
3.2 起动过程中转轮叶片表面压力变化
转轮转速在0-5 s内逐步上升至额定转速,随着转轮转速的升高,转轮叶片进口圆周速度增加,图4a和图4b显示转速的升高加剧了吸力面进水侧叶缘处水流的撞击和压力面进水侧叶缘处的脱流,撞击形成的高压区域和脱流产生的低压区域在0-3 s时间段内逐步变大.3-6 s时,转轮转速变化较小,出水流道上升段水面不断上升,出水流道内空气被压缩导致上升段水面压力增大,因而转轮叶片处压力增大.6-25 s为空气囊排出阶段,随着气囊的排出,出水流道的虹吸效应逐渐显现,虹顶测点压力迅速降为负值并逐渐减小,如图3c所示,因而转轮叶片压力受到气囊排出、虹吸效应影响逐渐减小.
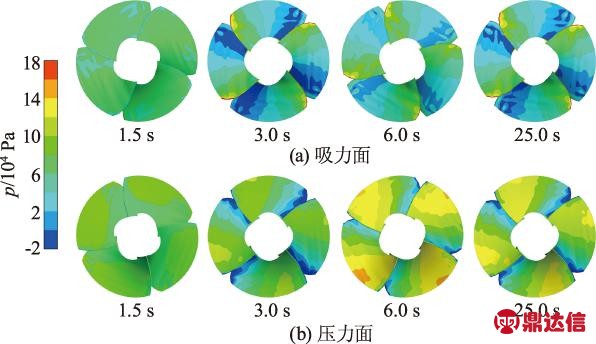
图4 起动过程叶片表面压力随时间变化
Fig.4 Variations of pressure distribution on blades
during start-up process
3.3 空气囊排出过程分析
为更为细致地分析轴流泵机组起动过程中出水流道空气囊的排出过程,对虹吸式出水流道下降段做流线图.如图5所示,在空气囊后端与出水流道出口之间形成一个具有挟气能力的旋转旋涡,将从空气囊中分离出的气泡卷入旋涡,利用旋涡的旋转流场将气泡运至出水流道出口再从出水池排出.随着空气囊中气泡的分离,空气囊体积逐渐缩小,位置向虹吸管出口移动,旋涡强度也逐渐减弱,影响范围逐渐缩小.
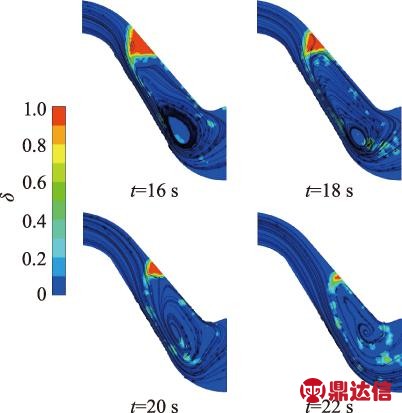
图5 出水流道下降段流态随时间变化图
Fig.5 Variations of flow state of descent part of
outlet passage
气泡和旋涡是产生机组振动的原因之一[2,14].在排气阀关闭,空气囊形成之后,气泡大量从空气囊中分离并通过旋涡运输,在传递过程中气泡溃灭不断发生,压力和力矩等动态参数也不断波动,易诱发机组振动,这也验证了已运行的某虹吸式抽水泵起动过程的监测结论:水泵的强烈振动不产生于最大起动扬程处,而产生于起动扬程下降过程中[15].
4 真空破坏阀保持关闭的起动过程
对真空破坏阀保持关闭的起动过程进行数值模拟,参数设置与预开启真空破坏阀起动过程相同.图6为起动过程流态图,过程总耗时70 s.起动开始后,出水流道上升段水面逐步上升,流道内空气被压缩,下降段水面于5 s时下降至出水流道出口处.与预开启真空破坏阀起动不同的是,预开启真空破坏阀起动时部分空气从真空破坏阀排除,空气受压缩程度小,下降段水面降低较小,而真空破坏阀保持关闭的起动过程中出水流道内气压更高,起动所需最大起动扬程更大.5 s后,流道内空气以分离气囊的方式流入出水池.随着气囊的分离,下降段水面维持在出水流道出口处上下波动,出水池内流态大幅度波动.10 s时出水流道内空气囊已经形成,但气囊明显大于同时刻预开启真空破坏阀起动中的气囊,这导致排出气囊阶段需要更长时间,之后经历60 s的排出气囊阶段形成满管流,虹吸效应完全形成,起动过程结束.对比图3与图6可知,真空破坏阀保持关闭的起动过程中,出水流道内气囊体积更大,排除气囊的时间更长,气囊下方旋涡区内气泡数量也更多.表2为不同起动过程的参数对比,表中tstart为起动时间,Hmax为最大扬程,pmax为虹顶测点最大压强.由表2数据对比可见,预开启真空破坏阀的起动方式可以缩短64%起动时间,最大起动扬程减小30%以及出水流道内空气压力下降67%.

图6 真空破坏阀保持关闭起动过程流态图
Fig.6 Profiles of pump with vacuum breaker valve
closed during start-up process
表2 不同起动过程的参数对比
Tab.2 Comparison of parameters in different start-up
processes
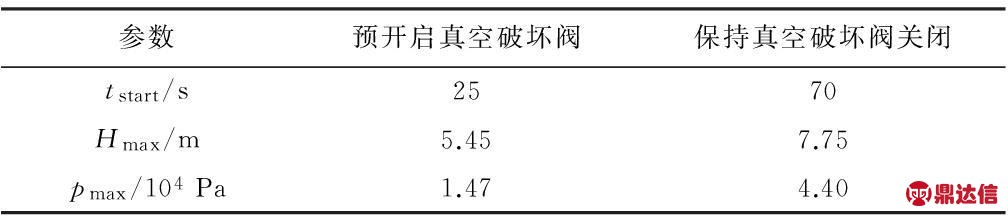
5 结 论
1) 利用VOF多相流模型能够较为准确地模拟具有虹吸式出水流道轴流泵机组的起动过程,不仅能够定量分析泵机组动态参数的瞬变特性,还能直观清晰地显示出水流道内空气囊排出演化过程.
2) 出水流道中虹吸的形成是利用出水流道内的旋涡不断将从空气囊中分离出的气泡携带排出,空气囊大小是影响排气时间长短的关键因素之一.
3) 相较于真空破坏阀保持关闭的起动过程,预开启真空破坏阀的方法可以降低出水流道中空气的压缩程度,可有效减少起动时间,降低最大起动扬程,起动过程流态也更加平稳.